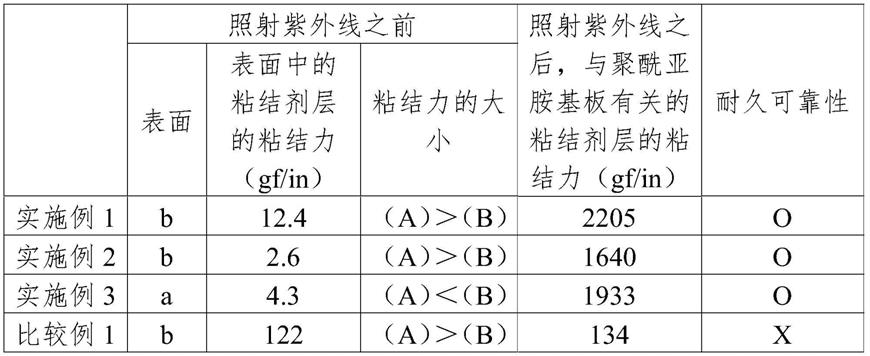
包括紫外线(uv)固化型粘结剂层的背板膜及利用其的有机发光显示装置制造方法
技术领域
[0001]
本发明涉及新有机发光显示装置制造方法及可适用于其的背板膜。
背景技术:[0002]
随着信息化技术的发达,作为用户与信息之间的连接介质的显示装置的市场正变大。由此,如液晶显示装置(liquid crystal display,lcd)、有机发光二极管显示装置(organic light emitting diode display,oled)、电泳显示装置(electro phoretic display,epd)及等离子液晶面板(plasma display panel,pdp)等的显示装置的使用增加。
[0003]
并且,最近,随着多媒体的发展,柔性(flexible)电子器件的重要性增大。由此,需在具有可挠性的基板上制造有机发光二极管(organic light emitting diode,oled)、液晶显示装置(liquid crystal display,lcd)、电泳显示装置(electrophoretic display,epd)、等离子显示面板(plasma display panel,pdp)、薄膜晶体管(thin-film transistor,tft)、微处理器(microprocessor)、随机存取存储器(random access memory,ram)、太阳能电池(solar cell)等,还需要附着于所述可挠性基板来保护及加强面板的背板膜。并且,背板膜具有防止柔性有机发光二极管面板卷曲(curl)并保护面板的功能,需要与柔性有机发光二极管面板的强粘结性。
[0004]
在以往的柔性有机发光二极管的制造工序中,使背板膜附着于有机发光二极管面板基板之后,通过利用激光雕刻工序,利用激光对背板膜进行蚀刻或利用已经图案化的背板膜的工序,来形成带隙,在此情况下,具有单元受损且制造工序的成本高的局限。
[0005]
因此,本发明人为了解决以往的问题,提供包括紫外线(uv,ultraviolet)固化型粘结剂层的背板膜及利用其的有机发光显示装置制造方法。
技术实现要素:[0006]
本发明提供节减制造费用且简化以往的工序的有机发光显示装置的制造方法。
[0007]
并且,本发明提供包括耐久可靠性优秀的紫外线(uv)固化型粘结剂层的背板膜。
[0008]
本发明的一实例提供一种背板膜(backplate),包括基材膜层及半固化(semi-cured)粘结剂层,所述基材膜层与所述半固化粘结剂层之间的粘结力a大于或小于对所述有机发光二极管面板基板的粘结剂层之间的粘结力b,粘结力a及粘结力b中的更小的粘结力为50gf/in以下。
[0009]
在本发明的一实例中,所述半固化粘结剂层附着于有机发光二极管面板基板来使得紫外线(uv)固化之后的粘结力达到1000gf/in以上。
[0010]
在本发明的一实例中,所述基材膜层选自由聚对苯二甲酸乙二醇酯(polyethylene terephthalate)、聚萘二甲酸乙二醇酯(polyethylenenaphthalate)、聚丙烯腈(polyacrylonitrile)、聚酰胺(polyamide)、聚酰胺酰亚胺(polyamideimide)、聚酰亚胺(polyimide)、聚烯烃(polyolefin)组成的组。
[0011]
在本发明的一实例中,所述有机发光二极管面板基板选自由玻璃、聚酰亚胺(polyimide)、聚醚醚酮(polyetheretherketon)、聚醚砜(polyethersulfone)、聚醚酰亚胺(polyetherimide)及聚碳酸酯(polycarbonate)组成的组。
[0012]
在本发明的一实例中,所述粘结剂层由包含橡胶类树脂、紫外线固化型低聚物以及光引发剂的粘结剂组合物制备而成。
[0013]
在本发明的一实例中,在所述粘结剂层的上部还包括离型膜层。
[0014]
本发明的另一实例提供一种有机发光显示装置制造方法,包括:步骤(a),所述背板膜内的所述半固化粘结剂层附着于包括多个单元的有机发光二极管面板基板;步骤(b),对与所述有机发光二极管面板基板的带区域的边界相对应的所述背板膜的部分进行激光切割;步骤(c),去除与所述有机发光二极管面板基板的带区域相对应的所述背板膜的一部分或全部;步骤(d),对去除与带区域相对应的所述背板膜的一部分或全部之后剩余的所述背板膜的有机发光二极管面板基板进行紫外线处理来加强粘结力;以及步骤(e),利用激光照射所述多个单元的边界,并以单元为单位来分离所述多个单元。
[0015]
在本发明的一实例中,所述步骤(b)包括以使深度达到所述基材膜层的厚度以上且小于背板膜厚度的方式对背板膜进行激光切割(laser cutting)的步骤。
[0016]
在本发明的一实例中,在所述基材膜层与所述半固化粘结剂层之间的粘结力a大于对所述有机发光二极管面板基板的粘结剂层之间的粘结力b的情况下,在所述步骤(c)中,去除与有机发光二极管面板基板的带区域相对应的整个背板膜。
[0017]
在本发明的一实例中,在所述基材膜层与所述半固化粘结剂层之间的粘结力a小于对所述有机发光二极管面板基板的粘结剂层之间的粘结力b的情况下,在所述步骤(c)中,去除与有机发光二极管面板基板的带区域相对应的背板膜的基材膜层。
[0018]
在本发明的一实例中,在所述步骤(d)中,对去除与带区域相对应的所述背板膜的一部分或全部之后剩余的所述背板膜进行紫外线处理,由此,所述粘结剂层的粘结力达到1000gf/in以上。
[0019]
其他实施例的具体事项包括于详细说明及附图。
[0020]
发明效果
[0021]
本发明的有机发光显示装置制造方法提供如下的方法,即,不使用激光雕刻,来使得单元不受损,排除不必要的工序及不使用追加的膜,来节减制造费用。
[0022]
根据本发明的方法制造的有机发光显示装置具有优秀的耐久可靠性及寿命特性。
附图说明
[0023]
图1a及图1b为用于说明本发明一实施例的背板膜的简要剖视图。
[0024]
图2a及图2b为用于说明本发明一实施例的有机发光显示装置制造方法的工序剖视图。
[0025]
图3a至图3c为用于说明本发明一实施例的有机发光显示装置制造方法的简要流程图。
[0026]
附图标记的说明
[0027]
10:背板膜
[0028]
11:粘结剂层
[0029]
12:基材膜层
[0030]
13:离型膜层
[0031]
100:有机发光二极管面板基板
[0032]
d:背板膜厚度
[0033]
d1:基材膜层的厚度
[0034]
ba:带区域
具体实施方式
[0035]
以下,详细说明本发明的实例。但是,这仅用于例示,本发明并不限定于此,本发明被发明要求保护范围定义。
[0036]
在附图中,放大厚度来示出,从而明确表达各层及区域。并且,在附图中,为了说明的便利,一部分层及区域的厚度有所夸张。
[0037]
以下,在基材的“上部(或下部)”或基材的“上(或下)”形成一个结构不仅意味着一个结构与所述基材的上面(或下面)相接触来形成,还意味着在所述记载与在基材上(或下)形成的一个结构之间还包括其他结构。
[0038]
本发明的一实例涉及包括紫外线固化型粘结剂层的背板膜及利用其的有机发光显示装置制造方法,更具体地,提供与有机发光二极管面板基板的损伤无关地形成带隙的有机发光显示装置制造方法和适合用于其的背板膜。
[0039]
在本发明的一实例中,提供一种背板膜,包括基材膜层及半固化(semi-cured)粘结剂层,所述基材膜层与所述半固化粘结剂层之间的粘结力a大于或小于对所述有机发光二极管面板基板的粘结剂层之间的粘结力b,粘结力a及粘结力b中的更小的粘结力为50gf/in以下。
[0040]
在本发明的一实例中,在半固化粘结剂层的上部还可包括离型膜层。
[0041]
图1a为本发明一实例的包括基材膜层12及半固化粘结剂层11的背板膜10的简要剖视图。
[0042]
图1b为本发明一实例的包括基材膜层12、半固化粘结剂层11及离型膜层13的背板膜10的简要剖视图。
[0043]
所述半固化粘结剂层11位于所述基材膜层12的上部,以相向的方式附着于有机发光二极管面板基板100。
[0044]
所述半固化粘结剂层11可利用包括橡胶类树脂、紫外线固化型低聚物及光引发剂的粘结剂组合物层叠于基材膜层来制备。所述半固化粘结剂层11的厚度为约5μm至约50μm。可将所述半固化粘结剂层11的厚度维持在所述范围来确保所目的的粘结力。
[0045]
所述橡胶类树脂可以为选自由苯乙烯-异丁烯-苯乙烯(sibs)类橡胶、苯乙烯-异丁烯(sib)类橡胶、苯乙烯-丁二烯-苯乙烯(sbs)类橡胶、苯乙烯-丁二烯(sb)类橡胶、苯乙烯-异戊二烯-苯乙烯(sis)类橡胶、苯乙烯-乙烯-丁烯-苯乙烯(sebs)类橡胶、丁基类橡胶、聚异丁烯(pib)类橡胶、丙烯橡胶、氨基甲酸乙酯橡胶等组成的组中的一种以上。优选地,所述橡胶类树脂为包含苯乙烯的橡胶类树脂。
[0046]
所述紫外线固化型低聚物可以为固化之后粘结力优秀的紫外线固化型树脂。例如,可选自包含丙烯酸酯树脂、甲基丙烯酸酯树脂、异氰酸酯树脂、三聚氰胺树脂、氨基甲酸
乙酯树脂、环氧树脂、酸酐、聚胺树脂及羧基的聚合物中。所述紫外线固化型低聚物可利用橡胶类树脂和微细的相分离现象,在照射紫外线之前的步骤实现低粘结力。因此,在固化之前,相对于有机发光二极管面板基板或基材膜层,包含所述紫外线固化型低聚物的半固化粘结剂层可具有低粘结力,例如,可具有50gf/in以下的粘结力。
[0047]
优选地,所述紫外线固化型低聚物可以为环氧树脂,含有2个以上的官能团,可以为环氧当量为100g/eq至1500g/eq的环氧低聚物。所述环氧树脂可在分子结构内具有环形结构,例如,可以为芳香族基(例如,苯基)、进行氢化反应的芳香族环氧化合物。在此情况下,所述构成脂环式环的氢原子可被烷基等的取代基取代。作为含有芳香族基的环氧化合物的具体例,双酚类环氧树脂(双酚a型环氧树脂、双酚f型环氧树脂、双酚ad型环氧树脂)、酯醛型环氧树脂、低聚木糖型环氧树脂、双环戊二烯型环氧树脂、萘型环氧树脂、三酚甲烷型环氧树脂及缩水甘油胺型环氧树脂等的低聚物形态,但并不限定于此。
[0048]
所述光引发剂的种类并没有特殊限制,例如,可以使用芳香族重氮盐、芳香族碘铝盐、芳香族锍盐或铁-芳烃络合物等的公知的阳离子引发剂,其中,可使用芳香族锍盐,但并不限定于此。
[0049]
所述粘结剂组合物包含所述橡胶类树脂、紫外线固化型低聚物以及光引发剂,除此之外,还可包含选自由粘结增进剂、热引发剂、多官能丙烯酸酯、防静电剂、硅烷偶联剂、防氧化剂、填充剂及可塑剂、颜料、分散剂、消泡剂、增稠剂组成的组中的一种以上。所述添加剂可在不抑制粘结剂组合物的物性的范围内适当地进行调节。
[0050]
在本发明的一实例中,所述基材膜层12与所述半固化粘结剂层11之间的粘结力a大于或小于对所述有机发光二极管面板基板100的粘结剂层11之间的粘结力b。
[0051]
在本发明的一实例中,将所述基材膜层12与所述半固化粘结剂层11之间的粘结力a及对所述有机发光二极管面板基板100的粘结剂层11之间的粘结力b的大小设置得不同,可不通过激光雕刻,去除与带区域相对应的背板膜10的全部或一部分。
[0052]
相对于所述有机发光二极管面板基板100或所述基材膜层12,所述半固化粘结剂层11可具有低粘结力,例如,可具有50gf/in以下的粘结力,优选地,可具有30gf/in以下的粘结力,更优选地,可具有20gf/in以下的粘结力。因此,在激光切割之后,当进行刮切(scrape)工序时,半固化粘结剂层11可残留于与带区域相对应的所述有机发光二极管面板基板100或者与基材膜层12一同完全去除。
[0053]
所述半固化粘结剂层11附着于有机发光二极管面板基板100来进行紫外线固化之后,可具有1000gf/in以上的粘结力,优选地,可具有1300gf/in以上的粘结力,更优选地,可具有1500gf/in以上的粘结力。
[0054]
所述基材膜层12可选自由聚对苯二甲酸乙二醇酯(polyethylene terephthalate)、聚萘二甲酸乙二醇酯(polyethylenenaphthalate)、聚丙烯腈(polyacrylonitrile)、聚酰胺(polyamide)、聚酰胺酰亚胺(polyamideimide)、聚酰亚胺(polyimide)、聚烯烃(polyolefin)组成的组中的一种以上的材料,但并不限定于此,可使用各种公知的膜层。
[0055]
所述有机发光二极管面板基板100可选自由玻璃、聚酰亚胺(polyimide)、聚醚醚酮(polyetheretherketon)、聚醚砜(polyethersulfone)、聚醚酰亚胺(polyetherimide)及聚碳酸酯(polycarbonate)组成的组,但并不限定于此,可使用各种公知的膜层。
[0056]
本发明的另一实例提供一种有机发光显示装置的制造方法,包括:步骤(a),将所述背板膜10内的所述半固化粘结剂层附着于包括多个单元的有机发光二极管面板基板100;步骤(b),对与所述有机发光二极管面板基板100的带区域ba的边界相对应的所述背板膜10的部分进行激光切割;步骤(c),去除与所述有机发光二极管面板基板100的带区域ba相对应的所述背板膜10的一部分或全部;步骤(d),对去除所述背板膜10的一部分或全部之后剩余的所述背板膜10的有机发光二极管面板基板100进行紫外线处理来加强粘结力;以及步骤(e),利用激光照射所述多个单元的边界,并以单元为单位来分离所述多个单元。
[0057]
图2a及图2b为用于说明本发明一实施例的有机发光显示装置制造方法的工序图。
[0058]
在本发明的一实例中,将背板膜10的半固化粘结剂层11以与有机发光二极管面板基板100相向的方式附着于有机发光二极管面板基板100,对与有机发光二极管面板基板100的带区域ba的边界相对应的所述背板膜10的部分进行激光切割(图2a及图2b的步骤(a))。
[0059]
在此情况下,以使深度达到所述基材膜层12的厚度d1以上且小于背板膜10厚度d的方式对背板膜10进行激光切割(步骤(b))。即,激光切割以使深度达到半固化粘结剂层11的厚度d-d1的一部分或全部的方式来进行,当进行刮切(scrape)工序时,可容易与基材膜一同掉落。并且,本发明的激光切割的深度小于背板膜10的厚度d,因此,与激光雕刻工序不同地,不使有机发光二极管面板基板100受损。在所述基材膜层12与所述半固化粘结剂层11之间的粘结力a大于对所述有机发光二极管面板基板100的半固化粘结剂层11之间的粘结力b的情况下,在所述步骤(c)中,可去除与有机发光二极管面板基板100的带区域ba相对应的整个背板膜10。
[0060]
作为一例,在刮切工序中,一同去除存在于带区域ba的半固化粘结剂层11及基材膜层12(图2a的步骤(c1))。
[0061]
作为另一例,在所述基材膜层12与所述半固化粘结剂层11之间的粘结力a小于对所述有机发光二极管面板基板100的半固化粘结剂层11之间的粘结力b的情况下,去除与有机发光二极管面板基板100的带区域ba相对应的背板膜10的基材膜层12,半固化粘结剂层11残留于有机发光二极管面板基板100的上部(图2b的步骤(c2))。
[0062]
对去除与有机发光二极管面板基板100的带区域ba相对应的背板膜10的一部分或全部之后剩余的所述背板膜10进行紫外线处理,向单元的边界照射激光,并以单元为单位来分离多个单元(图2a及图2b的步骤(d)及步骤(e))。
[0063]
以下,记载本发明的实施例及比较例。下述实施例仅为本发明的一实施例,本发明并不限定于下述实施例。
[0064]
实施例
[0065]
实施例1:制备背板膜
[0066]
配合61重量份的苯乙烯-异戊二烯-苯乙烯(sis)树脂、39重量份的脂环式环氧化合物,并添加0.5重量份的作为阳离子光引发剂的三芳基磺胺六氟锑酸盐,利用甲苯以使固体成分成为30重量百分比的方式进行稀释,从而制备了粘结剂组合物,所述苯乙烯-异戊二烯-苯乙烯(sis)树脂由苯乙烯-异戊二烯-苯乙烯嵌共聚物构成且包含19重量百分比的苯乙烯。
[0067]
将在所述内容中制备的粘结剂组合物涂敷于作为基材膜的聚对苯二甲酸乙二醇
酯(pet)上,在120℃的温度条件下的烘箱干燥3分钟,并以使粘结剂层的厚度成为25μm的方式进行涂敷之后,通过贴合离型膜来制备了背板膜,从而保护被涂敷的粘结剂面。
[0068]
实施例2:制备背板膜
[0069]
配合84重量份的苯乙烯-异丁烯-苯乙烯(sibs)树脂、16重量份的脂环式环氧化合物,添加0.5重量份的作为阳离子光引发剂的三芳基磺胺六氟锑酸盐,利用甲苯以使固体成分成为30重量百分比的方式进行稀释来制备了结剂组合物,所述苯乙烯-异丁烯-苯乙烯(sibs)树脂由苯乙烯-异丁烯-苯乙烯嵌共聚物构成且包含13重量百分比的苯乙烯。
[0070]
将在所述内容中制备的粘结剂组合物涂敷于作为基材膜的聚对苯二甲酸乙二醇酯(pet)上,在120℃的温度条件下的烘箱干燥3分钟,并以使粘结剂层的厚度成为25μm的方式进行涂敷之后,通过贴合离型膜来制备了背板膜,从而保护被涂敷的粘结剂面。
[0071]
实施例3:制备背板膜
[0072]
配合73重量份的苯乙烯-异丁烯-苯乙烯(sibs)树脂、27重量份的脂环式环氧化合物,添加0.5重量份的作为阳离子光引发剂的三芳基磺胺六氟锑酸盐、15重量份的作为增粘剂发的烃类树脂,利用甲苯以使固体成分成为30重量百分比的方式进行稀释来制备了粘结剂组合物,所述苯乙烯-异丁烯-苯乙烯(sibs)树脂由苯乙烯-异丁烯-苯乙烯嵌共聚物构成且包含13重量百分比的苯乙烯。
[0073]
将在所述内容中制备的粘结剂组合物涂敷于作为基材膜的聚对苯二甲酸乙二醇酯(pet)上,在120℃的温度条件下的烘箱干燥3分钟,并以使粘结剂层的厚度成为25μm的方式进行涂敷之后,通过贴合离型膜来制备了背板膜,从而保护被涂敷的粘结剂面。
[0074]
比较例1:制备背板膜
[0075]
相对于由98.5重量份的丙烯酸-2-乙基己酯(2-eha)及1.5重量份的甲基丙烯酸羟乙酯(2-hema)组成的100重量份的丙烯类共聚物,添加1.2重量份的交联剂(异氰酸酯类三羟甲基丙烷的甲苯二异氰酸酯加合物(tdi)),利用乙酸乙酯以使固体成分成为30重量百分比的方式进行稀释来制备了粘结剂组合物。
[0076]
将在所述内容中制备的粘结剂组合物涂敷于作为基材膜的聚对苯二甲酸乙二醇酯(pet)上,在120℃的温度条件下的烘箱干燥3分钟,并以粘结剂层的厚度成为25μm的方式进行涂敷之后,通过贴合离型膜来制备了背板膜,从而保护被涂敷的粘结剂面。
[0077]
实验例:评价背板膜的物理特性
[0078]
(1)检测照射紫外线(uv)之前的粘结力
[0079]
以使宽度成为25mm、长度成为200mm的方式对在所述实施例及比较例中制备的背板膜进行裁剪来制造了试片。在去除所述离型膜之后,经由试片的粘结剂层并利用2kg的辊附着于聚酰亚胺基板,并在常温温度条件下放置30分钟。通过使用拉力试验机以5mm/sec的剥离速度及180度的剥离角度剥开背板膜,并以如下所述的方式观察了剥离力和所分离的表面。
[0080]
(2)检测照射紫外线(uv)之后的粘结力
[0081]
以使宽度成为25mm、长度成为200mm的方式对在所述实施例及比较例中制备的背板膜进行裁剪来制造了试片。经由所述试片的粘结剂层并利用2kg的辊附着于聚酰亚胺基板,并在常温温度条件下放置30分钟。利用水银灯以使光量成为2000mj/cm
2
的方式照射紫外线,并放置2小时,通过使用拉力试验机以5mm/sec的剥离速度及180度的剥离角度剥开背
板膜并检测剥离力。
[0082]
(3)耐久可靠性
[0083]
以使宽度成为100mm、长度成为200mm的方式对在所述实施例及比较例中制备的背板膜进行裁剪来制造了试片。经由所述试片的粘结剂层并利用2kg的辊附着于聚酰亚胺基板,利用水银灯以使光量成为2000mj/cm
2
的方式照射紫外线。在85℃的温度、90%rh、500hr的条件下放置通过如上所述的内容制备的样品,并通过如下所述的方式评价了外观。
[0084]
评价基准
[0085]
o:不产生气泡、剥离、翘起等不良
[0086]
x:产生气泡、剥离、翘起等不良
[0087]
表1
[0088][0089]
*半固化粘结剂层和基材膜聚对苯二甲酸乙二醇酯(pet)的粘结力a
[0090]
*半固化粘结剂层和聚酰亚胺基板的粘结力b
[0091]
*粘结剂层和基材膜聚对苯二甲酸乙二醇酯(pet)的表面:a
[0092]
*粘结剂层和聚酰亚胺板的表面:b
[0093]
在实施例1及实施例2中,在固化之前,剥离背板膜时,粘结剂层与基材膜苯二甲酸乙二醇酯(pet)一同从聚酰亚胺基板去除。固化之前,与聚酰亚胺基板有关的半固化粘结剂层的粘结力为50gf/in以下,与基材膜苯二甲酸乙二醇酯(pet)有关的粘结剂层的粘结力a大于与聚酰亚胺基板有关的粘结剂层的粘结力b。因此,在实施例1及实施例2中,根据在本发明一实例的图2a中揭示的工序进行刮削工序时,与背板基板一同从面板基板剥离。在此情况下,当根据本发明的方法进行刮削工序时,容易去除带区域的粘结剂层,在照射紫外线之后,相对于聚酰亚胺层,粘结剂层具有1000gf/in以上的粘结力。
[0094]
在实施例3中,在固化之前,当剥离背板时,粘结剂层残留于聚酰亚胺基板。在固化之前,与基材膜苯二甲酸乙二醇酯(pet)有关的半固化粘结剂层的粘结力为50gf/in以下,与聚酰亚胺基板有关的半固化粘结剂层的粘结力b大于与基材膜苯二甲酸乙二醇酯(pet)有关的半固化粘结剂层的粘结力a,因此,当剥离背板时,粘结剂层残留于聚酰亚胺基板。因此,在实施例3中,根据本发明一实例的图2b中揭示的工序进行刮削工序之后,粘结剂层残留于面板基板,在固化之后,相对于聚酰亚胺层,具有1000gf/in以上的粘结力。
[0095]
但是,在比较例1的情况下,在照射紫外线之后,相对于聚酰亚胺层,具有远不及1000gf/in的低粘结力。因此,无法适用本发明的方法,无法提供具有优秀的耐久可靠性及
寿命特性的有机发光显示装置。
[0096]
以上,对本发明的优选实施例进行了详细说明,本发明的权利范围并不局限于此,普通技术人员利用发明要求保护范围中定义的本发明的基本概念进行的各种变形及改良形态也属于本发明的权利范围。