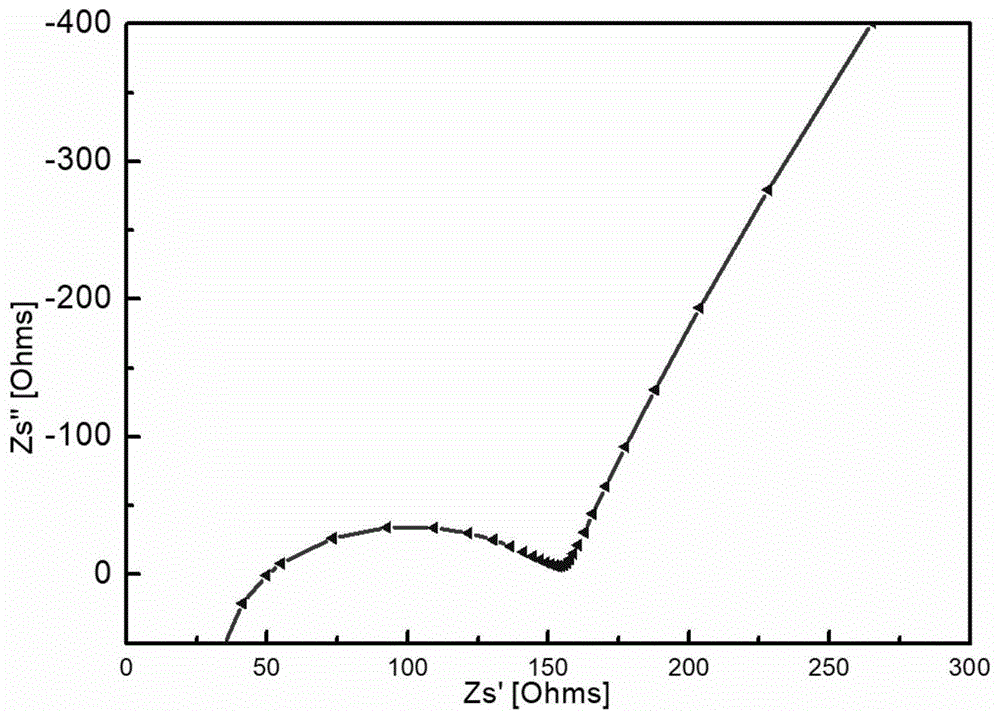
本发明涉及一种复合电解质、其应用及其制备方法,特别是涉及一种复合固态电解质其应用及其制备方法,应用于二次锂离子电池
技术领域:
。
背景技术:
:随着社会发展脚步的加快,人类对能源的需求和依赖不断加大,化石能源的使用造成的污染以及温室效应,促使着人类对清洁能源以及储存技术的发展。电池作为储存能源的装置,与人类日常生活息息相关,且广泛用于电子设备当中。由于能源紧缺和环境污染的问题的突显,可循环使用的锂离子电池吸引着更多的研究。随着新能源汽车的兴起,锂离子电池将成为未来电池发展的重点,而在电池中电解质作为电池不可或缺的一部分,影响着电池的性能,该电解质和电极材料在充放电过程中容易发生副反应,导致电池容量出现不可逆衰减,同时电池在长期服役过程中,有机液体电解质会出现挥发、干涸、泄露等现象,影响电池寿命。另一方面,传统锂电池无法使用高能量密度的金属锂作为负极材料,在电池循环中,由于金属锂表面电流密度及锂离子分布不均匀等因素,金属锂电极反复溶解、沉积容易形成不均匀的孔洞和枝晶。枝晶会刺穿隔膜,到达电池正极造成电池短路、热失控、着火爆炸等一系列安全隐患,用固态电解质代替液体电解质是获得高能量密度、安全性和长循环寿命的全固态锂电池的根本途径。全固态锂电池可以避免液体电解质带来的负效用,提高电池的安全性和服役寿命,而固态电解质与极片接触不良会导致界面电阻变大,成为固态电池发展的瓶颈,常用固态电解质的室温离子电导率为10-6scm-1,远远低于液态电解质的离子电导率。因此,固态电解质界面阻抗的降低和室温离子电导率的提高,将会促进未来固态电池的工业应用和发展。在传统固态电解质中,以高分子聚合物为基体,加入锂盐形成固态电解质,但是由于锂盐的解离度低以及高分子聚合物的结晶性高,导致锂离子在电解质中电导率较低。此外固态电解质与极片间接触不良会导致界面电阻变大。而经调研发现,聚硅氧烷具有抑制高分子聚合物的结晶性,从而提高电解质的电导率,例如以下两篇文献:1.ren等人(《solid-statesingle-ionconductingcomb-likesiloxanecopolymerelectrolytewithimprovedconductivityandelectrochemicalwindowforlithiumbatteries》j.appl.polym.sci.2018,135,45848)制备出全固态电解质的常温电导率仅为3.7×10-5scm-1,而界面阻抗却高达16000ω,电导率较低,且表面阻抗较大,稳定性较差;2.zhang等人(《advancedpolymerelectrolytewithenhancedelectrochemicalperformanceforlithium-ionbatteries:effectofnitrile-functionalizedionicliquid》acsappl.energymater.2019,2,1685-1694)制备电解质的常温电导率为3.56×10-4scm-1,界面阻抗为650ω,由于电解质中存在少量液体,导致电解质的电导率较高,但是循环稳定性低,机械稳定性低;上述文献公开的技术皆采用直接添加聚硅氧烷,通过高分子聚合物与聚硅氧烷复合,降低高分子聚合物的结晶性,提高电导率,但是由于聚硅氧烷属于高分子长链聚合物,不易溶解溶剂中,导致电解质与高分子聚合物复合程度不高,所以导致对电解质的电导率提升不太明显,另外加入聚硅氧烷,采用复合的方式,制备成膜,然后放置在电极表面,导致电极表面与电解质接触性降低,进而导致阻抗变大。在现有技术中,尽管加入聚硅氧烷使得电解质的电导率有所提高,界面阻抗有所降低,但是循环的稳定性一般,且机械性能较差,不能满足实际的生产要求,还有很大的提升空间。如何改善电极表面与电解质的接触,降低界面阻抗,同时提高电解质的机械性能以及电池的循环性能成为亟待解决的技术问题。技术实现要素:为了解决现有技术问题,本发明的目的在于克服已有技术存在的不足,提供一种聚硅氧烷复合电解质、其应用及其制备方法,采用氨基-硅氧烷单体为基础,通过氨基-硅氧烷有机单体水解缩合,在电极材料表面原位聚合生成硅氧烷链状聚合物,在加热条件下使硅氧烷链状聚合物、高分子聚合物及锂盐进行固化结合,形成复合固态电解质,从而提高高分子聚合物与聚硅氧烷的复合程度,降低高分子聚合物的结晶性,提高电解质的电导率;在电极表面原位聚合,改善电极表面与电解质的接触,降低界面阻抗,同时提高电解质的机械性能以及电池的循环性能。为达到上述发明创造目的,本发明采用如下技术方案:一种聚硅氧烷复合电解质,原料主要由氨基-硅氧烷有机单体、高分子聚合物及锂盐组分组成,按照原料组分摩尔百分比含量计算,氨基-硅氧烷有机单体组分含量为整体固态电解质的10.0~40.0mol%,高分子聚合物的组分含量为整体固态电解质的50.0~80.0mol%,锂盐的组分含量为整体固态电解质的1.0~12.5mol%;氨基-硅氧烷有机单体通过水解缩合反应,在电极材料表面原位聚合生成硅氧烷链状聚合物,并使硅氧烷链状聚合物、高分子聚合物及锂盐进行固化结合,形成复合固态电解质。作为本发明优选的技术方案,按照原料组分摩尔百分比含量计算,氨基-硅氧烷有机单体组分含量为整体固态电解质的12.90~25.00mol%,高分子聚合物的组分含量为整体固态电解质的72.73~77.42mol%,锂盐的组分含量为整体固态电解质的9.68~12.5mol%。作为本发明优选的技术方案,所述氨基-硅氧烷有机单体的化学式为:其中,r为烷基,r的碳原子数1~10;r′为—(ch2)n-nh2,4≥n≥2。作为本发明优选的技术方案,所述氨基-硅氧烷有机单体为三乙氧基-氨丙基硅烷单体和三甲氧基-氨丙基硅烷单体中的任意一种或者两种单体的混合物。作为本发明优选的技术方案,所述高分子聚合物采用如下有机物中的任意一种或者任意几种组合:聚环氧乙烷(peo)、聚丙烯腈(pan)、聚甲基丙烯酸甲酯(pmma)、聚偏氟乙烯(pvdf)、聚环氧丙烷(ppo)、聚偏氯乙烯(pvdc)、聚碳酸乙烯酯(pec)、聚三亚甲基碳酸酯(ptmc)、聚碳酸丙烯酯(ppc)。作为本发明优选的技术方案,所述锂盐采用如下锂盐中的任意一种或者任意几种组合:liclo4、lipf6、libf4、liasf6、lifsi、litfsi、licf3so3以及含氟/氮阴离子锂盐。一种本发明聚硅氧烷复合电解质的应用,在正极材料表面结合所述复合固态电解质,得到复合固态电解质膜,并结合负极材料组装二次锂离子固态电池。作为本发明优选的技术方案,所装配的固态电池的正极材料为以下的任意一种或任意几种的组合:锂钴氧化物、锂镍氧化物、锂锰氧化物、聚阴离子正极材料、三元正极材料。作为本发明优选的技术方案,所述正极材料lifepo4或limn0.8fe0.2po4。一种本发明聚硅氧烷复合电解质的制备方法,包括如下步骤:a.采用氨基-硅氧烷有机单体、高分子聚合物及锂盐作为原料,先将高分子聚合物、锂盐溶解在溶剂中,再将去离子水和氨基-硅氧烷单体依次加入,搅拌混合,获得均匀浆料;b.将在所述步骤a中得到的混合浆料涂覆在正极材料表面,形成涂覆浆料膜;c.将在所述步骤b中得到的涂覆浆料膜的正极材料加热,直至涂覆浆料膜固化成固体膜,使氨基-硅氧烷单体在正极材料表面表面进行原位聚合生成硅氧烷链状聚合物;并在加热条件下使硅氧烷链状聚合物、高分子聚合物及锂盐进行固化结合;同时除去溶剂;从而制备与正极材料表面紧密结合的复合固态电解质。本发明与现有技术相比较,具有如下显而易见的突出实质性特点和显著优点:1.本发明基于氨基-硅氧烷单体复合固态电解质,通过原位聚合,改善电解质与正极片界面接触,降低界面阻抗,有利于电池工作过程;2.本发明利用原位聚合氨基-硅氧烷单体,形成聚硅氧烷,与高分子聚合物的相互作用,降低高分子聚合物的结晶性,可以有效提高固态电解质的锂离子电导率,且制备出的电池循环稳定,性能优良;3.本发明复合固态电解质在电极表面原位聚合生成,不需要压片等工艺,具有高环保、低能耗、低成本等优势;同时制备方法简单,工艺成熟,易于操作;同时此类聚合物固态电解质体系适合工业应用;因此,在动力电池和储能电池领域具有广泛的应用前景。附图说明图1为本发明实施例一聚硅氧烷复合电解质的常温阻抗图。图2为本发明实施例二聚硅氧烷复合电解质的常温阻抗图。具体实施方式以下结合具体的实施例子对上述方案做进一步说明,本发明的优选实施例详述如下:实施例一:在本实施例中,一种聚硅氧烷复合电解质,原料主要由三乙氧基-氨丙基硅烷单体、高分子聚合物peo及锂盐liclo4组分组成,三乙氧基-氨丙基硅烷单体通过水解缩合反应,在电极材料表面原位聚合生成硅氧烷链状聚合物,并使硅氧烷链状聚合物、高分子聚合物及锂盐进行固化结合,形成复合固态电解质。在本实施例中,聚硅氧烷复合电解质的制备方法,包括如下步骤:a.采用三乙氧基-氨丙基硅烷单体、高分子聚合物peo及锂盐liclo4作为原料,摩尔比peo:li为8:1的比例和摩尔比peo:三乙氧基-氨丙基硅烷为6:1的比例取用原料,先将高分子聚合物peo、锂盐liclo4溶解在乙腈中,再将去离子水和三乙氧基-氨丙基硅烷单体依次加入,搅拌混合,获得均匀浆料;b.将在所述步骤a中得到的混合浆料涂覆在正极材料表面,形成涂覆浆料膜;c.将在所述步骤b中得到的涂覆浆料膜的正极材料加热,直至涂覆浆料膜固化成固体膜,使三乙氧基-氨丙基硅烷单体在正极材料表面表面进行原位聚合生成硅氧烷链状聚合物;并在加热条件下使硅氧烷链状聚合物、高分子聚合物peo及锂盐liclo4进行固化结合;并通过加热方式,同时除去溶剂;从而制备与正极材料表面紧密结合的复合固态电解质。实验测试分析:对本实施例制备的复合固态电解质进行测试常温阻抗实验,参见图1,本实施例制备的复合固态电解质的常温电导为6.36×10-4scm-1,界面阻抗为153.53ω。相对对比文献1中全固态电解质电导率为3.7×10-5scm-1的电导率高出10倍以上,界面阻抗相对明显降低到153.53ω;相对对比文献2中全固态电解质电导率为3.56×10-4scm-1的电导率提高78.65%,但界面阻抗相比对比文献2中全固态电解质降低了76.38%;本实施例通过原位聚合,改善电解质与正极片界面接触,降低界面阻抗,且与高分子聚合物的相互作用,降低高分子聚合物的结晶性,可以有效提高固态电解质的锂离子电导率。将本实施例复合固态电解质原位制备于lifepo4极片表面,以锂片为负极组装固态电池,室温条件下,2.5-3.7vvs.li+/li范围内0.02c循环测试,结果如下:循环1周20周50周容量(mah/g)165155149利用本实施例制备的复合固态电解质组装的二次锂离子固态电池在上述条件下循环50周,电池容量仅下降了9.7%,具有很好的电池的循环性能。实施例二:本实施例与实施例一基本相同,特别之处在于:在本实施例中,一种聚硅氧烷复合电解质,原料主要由三甲氧基-氨丙基硅烷单体、高分子聚合物pvdf及锂盐liclo4组分组成,三甲氧基-氨丙基硅烷单体通过水解缩合反应,在电极材料表面原位聚合生成硅氧烷链状聚合物,并使硅氧烷链状聚合物、高分子聚合物及锂盐进行固化结合,形成复合固态电解质。在本实施例中,聚硅氧烷复合电解质的制备方法,包括如下步骤:a.采用三甲氧基-氨丙基硅烷单体、高分子聚合物pvdf及锂盐liclo4作为原料,摩尔比pvdf:li为8:1的比例和摩尔比pvdf:三甲氧基-氨丙基硅烷为4:1的比例取用原料,先将高分子聚合物pvdf、锂盐liclo4溶解在乙腈中,再将去离子水和三甲氧基-氨丙基硅烷单体依次加入,搅拌混合,获得均匀浆料;b.将在所述步骤a中得到的混合浆料涂覆在正极材料表面,形成涂覆浆料膜;c.将在所述步骤b中得到的涂覆浆料膜的正极材料加热,直至涂覆浆料膜固化成固体膜,使三乙氧基-氨丙基硅烷单体在正极材料表面表面进行原位聚合生成硅氧烷链状聚合物;并在加热条件下使硅氧烷链状聚合物、高分子聚合物pvdf及锂盐liclo4进行固化结合;并通过加热方式,同时除去溶剂;从而制备与正极材料表面紧密结合的复合固态电解质。实验测试分析:对本实施例制备的复合固态电解质进行测试常温阻抗实验,参见图1,本实施例制备的复合固态电解质的常温电导为1.16×10-4scm-1,界面阻抗为90.63ω。相对对比文献1中全固态电解质电导率为3.7×10-5scm-1的电导率高出2倍以上,界面阻抗相对明显降低到90.63ω;相对对比文献2中全固态电解质电导率为3.56×10-4scm-1的电导率虽然略有降低,但界面阻抗相比对比文献2中全固态电解质降低了86.06%;本实施例通过原位聚合,改善电解质与正极片界面接触,降低界面阻抗,且与高分子聚合物的相互作用,降低高分子聚合物的结晶性,可以有效提高固态电解质的锂离子电导率。将本实施例复合固态电解质原位制备于limn0.8fe0.2po4极片表面,以锂片为负极组装固态电池,室温条件下,2.5-4.4vvs.li+/li范围内0.01c循环测试,结果如下:循环1周20周50周容量(mah/g)149138133利用本实施例制备的复合固态电解质组装的二次锂离子固态电池在上述条件下循环50周,电池容量仅下降了10.74%,表现出较好的电池的循环性能。综合上述实施例可知,基于氨基-硅氧烷有机单体复合固态电解质,该固态电解质体系由氨基-硅氧烷有机单体、高分子聚合物及锂盐组分,通过氨基-硅氧烷有机单体水解缩合,在电极材料表面原位聚合固化形成。本发明可使固态电解质的室温离子电导率大于1×10-4scm-1,并使其相应的固态电池可在室温下工作。本发明上述实施例复合固态电解质在电极表面原位聚合生成,不需要压片等工艺,具有高环保、低能耗、低成本等优势;本发明复合固态电解质制备方法简单,工艺成熟,易于操作。本发明上述实施例的聚合物固态电解质体系适合工业应用,在动力电池和储能电池领域具有广泛的应用前景。上面对本发明实施例结合附图进行了说明,但本发明不限于上述实施例,还可以根据本发明的发明创造的目的做出多种变化,凡依据本发明技术方案的精神实质和原理下做的改变、修饰、替代、组合或简化,均应为等效的置换方式,只要符合本发明的发明目的,只要不背离本发明聚硅氧烷复合电解质、其应用及其制备方法的技术原理和发明构思,都属于本发明的保护范围。当前第1页1 2 3