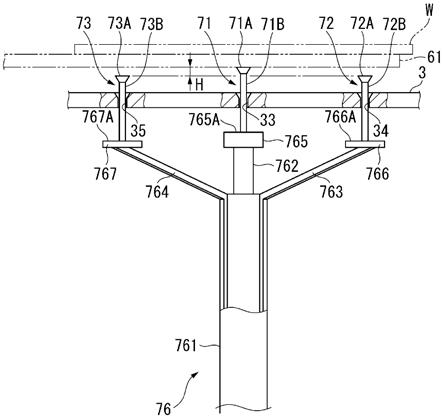
1.本发明涉及一种晶片传送装置、气相沉积装置、晶片传送方法及外延硅晶片的制造方法。
背景技术:2.气相沉积装置中,在将晶片载置至基座上的时候,首先,将以搬运叶片支承下表面的晶片搬运至基座上方时,使升降销上升,以其上端支承晶片下表面的同时,使晶片从搬运叶片分离。然后,气相沉积装置使升降销下降,将晶片载置至基座。
3.基座中设置有插入升降销的贯穿孔。为了顺利进行升降销的升降,该贯穿孔形成为在与升降销之间设置间隙。因此,升降销接触晶片时升降销倾斜,在该倾斜的状态下从搬运叶片接受晶片并载置至基座时,有晶片的载置位置偏离所期望的位置的可能性。
4.然后,进行用于抑制这种载置位置的偏离的研究(例如,参考专利文献1)。
5.专利文献1的气相沉积装置包括支承环,该支承环保持3支升降销的下端侧部分并抑制这些升降销的摇晃。支承环包括:环部;及板状部件,长度方向的一端部连接至环部的内周面,另一端部侧施力于环部侧,在板状部件与环部之间夹住并保持升降销。
6.现有技术文献专利文献专利文献1:日本特开2017
‑
135147号公报。
技术实现要素:7.发明所要解决的技术问题但是,如专利文献1的结构中,例如,当随着温度升降升降销和支承环膨胀或收缩时,有在升降销和支承环之间发生摩擦的可能性。如果发生摩擦,则产生来自升降销和支承环的灰尘,导致外延硅晶片上的微粒增加。
8.本发明的目的在于,为了不降低外延硅晶片的品质,提供能够将硅晶片载置至基座上的所期望的位置的晶片传送装置、气相沉积装置、晶片传送方法及外延硅晶片的制造方法。
9.用于解决技术问题的方案本发明的晶片传送装置是向在硅晶片上形成外延膜的气相沉积装置的基座传送所述硅晶片的晶片传送装置,所述晶片传送装置包括:搬运机构,保持所述硅晶片并将其搬运至所述基座上;及载置机构,将利用所述搬运机构搬运的所述硅晶片载置至所述基座,所述载置机构包括:多个升降销,可升降地插入于贯穿所述基座的多个贯穿孔的各自;及相对移动机构,使所述多个升降销与所述基座相对移动,所述相对移动机构使所述多个升降销相对于所述基座上升,由此以所述多个升降销支承所述硅晶片的下表面,并且,在解除利用所述搬运机构进行的所述硅晶片的保持后,使所述多个升降销相对于所述基座下降,由此
将所述硅晶片载置至所述基座,当以所述多个升降销支承所述硅晶片时,所述搬运机构与所述载置机构中至少一者的结构构成为特定的升降销最初接触所述硅晶片的下表面。
10.当以多个升降销支承硅晶片时,若只是任意的升降销最初抵接,则由于基座的贯穿孔与升降销之间的间隙的影响,在从基座中央朝向插入有该任意的升降销的贯穿孔的特定方向上,该任意的升降销的上端移动倾斜。在从该状态使多个升降销都相对于基座上升而从搬运机构接受硅晶片后,使多个升降销相对于基座下降,由此将硅晶片载置至基座上时,该载置位置从基于搬运机构的硅晶片搬运停止位置的正下方朝向上述特定方向偏离。
11.根据本发明,由于多个升降销中特定的升降销最初接触硅晶片,因此硅晶片在基座上的载置位置,从基于搬运机构的硅晶片搬运停止位置的正下方朝向上述特定方向偏离。因此,预先掌握向该特定方向的偏离量,预先将基于搬运机构的硅晶片的搬运停止位置设定至向与上述特定方向相反的方向侧仅移动上述掌握的偏离量的位置,由此能够将硅晶片载置至所期望的位置。并且,由于不使用如上述专利文献1的支承环的特殊部件,能够抑制灰尘的产生,并且能够抑制外延硅晶片的品质下降。
12.本发明的晶片传送装置中,优选在所述特定的升降销上端位于比其他升降销上端高的位置的状态下,所述相对移动机构使所述多个升降销相对于所述基座上升。
13.根据本发明,仅仅利用调整升降销的高度位置这一简单方法,就能够将硅晶片载置至所期望的位置。
14.本发明的晶片传送装置中,优选在所述特定的升降销上端位于比其他升降销上端高0.5mm以上且5mm以下的位置的状态下,所述相对移动机构使所述多个升降销相对于所述基座上升。
15.当升降销的高度差小于0.5mm时,根据硅晶片的由热引起的弯曲大小,特定的升降销无法最初接触硅晶片,有无法将硅晶片载置至所期望的位置的可能性。并且,当超过5mm时,直到特定的升降销以外的升降销接触硅晶片为止的期间,硅晶片的倾斜变大,搬运机构上硅晶片的位置偏离大,有无法将硅晶片载置至所期望的位置的可能性。
16.本发明中,由于将升降销的高度差设在0.5mm以上且5mm以下,因此能够抑制上述不良状况。
17.本发明的晶片传送装置中,优选所述多个升降销具有相同长度,所述相对移动机构包括升降销支承部件,所述升降销支承部件具有分别抵接于所述多个升降销下端的多个抵接部且相对于所述基座相对移动,抵接于所述特定的升降销的所述抵接部上端设置在比其他所述抵接部上端高的位置。
18.根据本发明,通过仅仅利用使特定的抵接部上端比其他抵接部上端高的简单方法,就能够将硅晶片载置至所期望的位置。
19.本发明的晶片传送装置中,优选所述特定的升降销形成为比其他升降销长,所述相对移动机构包括升降销支承部件,所述升降销支承部件具有分别抵接于所述多个升降销下端的多个抵接部且相对于所述基座相对移动,所述多个抵接部上端设置在相同高度的位置。
20.根据本发明,通过仅仅利用使特定的升降销比其他升降销长的简单方法,就能够将硅晶片载置至所期望的位置。
21.本发明的晶片传送装置中,优选所述搬运机构搬运所述硅晶片,以使在所述基座
上所述硅晶片中以所述特定的升降销支承的部分位于比其他部分更靠下侧。
22.根据本发明,通过仅仅设定利用搬运机构搬运的硅晶片在基座上的姿势的简单方法,就能够将硅晶片载置至所期望的位置。
23.本发明的晶片传送装置中,优选所述搬运机构包括纵长形状的支承部件,通过将载置有所述硅晶片的所述支承部件向其长度方向移动,将所述硅晶片搬运至所述基座上,所述支承部件包括从互相分离的位置沿该支承部件的长度方向延伸的一对延伸部,所述相对移动机构将所述多个升降销中位于所述一对延伸部之间的升降销作为所述特定的升降销并使其接触所述硅晶片的下表面。
24.当将硅晶片搬运至基座上时,由于容纳基座的腔室内的热,有时硅晶片下表面向下侧突出而弯曲或上表面向上侧突出而弯曲。
25.根据本发明,即使是弯曲状态不稳定的硅晶片,也能够载置至目标载置位置。
26.本发明的气相沉积装置是在硅晶片上形成外延膜的气相沉积装置,其特征在于包括:基座,载置所述硅晶片;及上述晶片传送装置,将所述硅晶片传送至所述基座。
27.本发明的晶片传送方法中,向在硅晶片上形成外延膜的气相沉积装置的基座传送所述硅晶片,所述晶片传送方法的特征在于包括如下工序:搬运工序,保持所述硅晶片并将其搬运至所述基座上;及载置工序,将通过所述搬运工序搬运的所述硅晶片载置至所述基座,所述载置工序包括相对移动工序,所述相对移动工序使可升降地插入于贯穿所述基座的多个贯穿孔的各自的多个升降销相对于所述基座上升,由此支承所述基座上的所述硅晶片的下表面,并且,在解除基于所述搬运工序的所述硅晶片的保持后,使多个升降销相对于所述基座下降,由此将所述硅晶片载置至所述基座,当以所述多个升降销支承所述硅晶片时,所述搬运工序与所述载置工序中的至少一个工序使特定的升降销最初接触所述硅晶片的下表面。
28.本发明的晶片传送方法中,优选使用具有从互相分离的位置沿所述支承部件的长度方向延伸的一对延伸部的纵长形状的支承部件,所述搬运工序通过将载置有p
‑
型的所述硅晶片的所述支承部件向其长度方向移动,将所述p
‑
型的硅晶片搬运至所述基座上,所述相对移动工序将所述多个升降销中位于所述一对延伸部之间的升降销作为所述特定的升降销并使其接触所述硅晶片的下表面。
29.本发明的外延硅晶片的制造方法中,在硅晶片上形成外延膜,所述外延硅晶片的制造方法的特征在于包括如下工序:进行所述晶片传送方法的工序,在所述晶片传送方法中将所述硅晶片传送至基座;及气相沉积工序,在传送至所述基座的所述硅晶片上形成外延膜。
附图说明
30.图1是本发明的一实施方式所涉及的气相沉积装置的从一方向观察时的示意图。
31.图2是所述气相沉积装置的从与所述一方向正交的方向观察时的示意图。
32.图3是所述气相沉积装置的基座及基座支承部件的立体图。
33.图4是所述基座的贯穿孔的剖视图。
34.图5是表示所述气相沉积装置的升降销支承部件中的升降销的支承状态的示意图。
35.图6a是使用所述气相沉积装置的外延硅晶片的制造方法说明图,是将硅晶片搬运至基座上方时的平面图。
36.图6b是使用所述气相沉积装置的外延硅晶片的制造方法说明图,是硅晶片接触升降销时的侧视图。
37.图6c是使用所述气相沉积装置的外延硅晶片的制造方法说明图,是将硅晶片载置至基座时的平面图。
38.图7a是所述外延硅晶片的制造方法说明图,是产生弯曲的p++型或p
‑
型硅晶片接触升降销时的侧视图。
39.图7b是所述外延硅晶片的制造方法说明图,是产生弯曲的p
‑
型硅晶片接触升降销时的侧视图。
40.图8a是本发明的变形例所涉及的硅晶片接触升降销时的侧视图。
41.图8b是其他变形例所涉及的硅晶片接触升降销时的侧视图。
42.图9a表示本发明的比较例中相对于硅晶片的目标载置位置的载置位置的分布。
43.图9b表示本发明的实施例1中相对于硅晶片的目标载置位置的载置位置的分布。
44.图9c表示本发明的实施例2中相对于硅晶片的目标载置位置的载置位置的分布。
45.图10a是表示根据图9b的结果调整硅晶片的搬运停止位置时相对于硅晶片的目标载置位置的实施例1的载置位置的分布。
46.图10b是表示根据图9c的结果调整硅晶片的搬运停止位置时相对于硅晶片的目标载置位置的实施例2的载置位置的分布。
具体实施方式
47.[实施方式]以下,对本发明的一实施方式进行说明。
[0048]
〔气相沉积装置的结构〕如图1所示,气相沉积装置1包括腔室2、基座3、加热部4以及晶片传送装置5。
[0049]
腔室2包括上拱顶21、下拱顶22以及固定各拱顶21、22的外缘彼此的拱顶固定体23,利用这些区划外延膜形成室20。
[0050]
由石英形成上拱顶21及下拱顶22。
[0051]
在下拱顶22的中央,向下方延伸而设置有插入后述的升降销支承部件76的支柱761的筒部221。
[0052]
拱顶固定体23包括用于进行硅晶片w对外延膜形成室20的运入及运出的晶片运入运出口24。如图2所示,拱顶固定体23包括:气体供给口25,用于向外延膜形成室20内供给气体;及气体排出口26,用于从外延膜形成室20排出气体。
[0053]
基座3以被碳化硅覆盖的碳形成为圆板状。
[0054]
在基座3的一个主面上形成有容纳硅晶片w的圆形锪孔部31。锪孔部31的直径比硅晶片w的直径大。
[0055]
如图3所示,在基座3的另一个主面的外缘附近设置有嵌入后述支承销753的3个嵌合沟32。嵌合沟32在基座3的圆周方向上以120
°
间隔设置。
[0056]
并且,在基座3中设置有贯穿两主面的第1贯穿孔33、第2贯穿孔34及第3贯穿孔35。
[0057]
各贯穿孔33、34、35,在锪孔部31内,在基座3的圆周方向上以120
°
间隔设置。如图4所示,各贯穿孔33、34、35包括:圆锥状的锥形部33a、34a、35a,随着从载置硅晶片w的锪孔部31的载置面31a朝基座3的厚度方向中心内径变小;及轴孔部33b、34b、35b,在基座3的厚度方向内径相等。
[0058]
如图1所示,加热部4包括设置在腔室2上侧的上加热器41以及设置在下侧的下加热器42。上加热器41以及下加热器42由红外线灯或卤素灯构成。
[0059]
晶片传送装置5将硅晶片w传送至基座3。晶片传送装置5包括搬运机构6以及载置机构7。
[0060]
搬运机构6保持硅晶片w并将其搬运至基座3。搬运机构6包括纵长形状的支承部件61(参考图6a)以及搬运机器人62。
[0061]
支承部件61例如以石英形成为细长长方形板状。支承部件61包括细长长方形板状的主体部61a以及从该主体部61a的末端宽度方向两端延伸的一对延伸部61b。
[0062]
搬运机器人62保持支承部件61在长度方向的一端侧。搬运机器人62通过向其长度方向移动支承部件61,将载置于支承部件61上的硅晶片w搬运至腔室2内,在基座3的锪孔部31上载置硅晶片w后,将支承部件61移动至原来的位置。搬运机器人62根据需要,在将硅晶片w搬运至腔室2内前,将支承部件61向与其长度方向正交的方向移动,调整基座3中硅晶片w的载置位置。
[0063]
载置机构7,将利用搬运机构6搬运的硅晶片w载置至基座3。如图1、图2、图3及图5所示,载置机构7包括第1升降销71、第2升降销72及第3升降销73以及相对移动机构74。
[0064]
各升降销71、72、73例如以被碳化硅覆盖的碳形成为相同形状的棒状。如图4所示,各升降销71、72、73包括圆锥台状的头部71a、72a、73a以及从该头部71a、72a、73a中直径较小的端部以圆柱状延伸的轴部71b、72b、73b。
[0065]
关于各升降销71、72、73,轴部71b、72b、73b插入于各贯穿孔33、34、35的轴孔部33b、34b、35b,并且由于其自身重量头部71a、72a、73a与锥形部33a、34a、35a抵接,由此被基座3支承。当各升降销71、72、73被基座3支承时,头部71a、72a、73a优选形成为其上端位于比锪孔部31的载置面31a更靠下方。关于轴部71b、72b、73b,其粗细形成为,当配置为其中心轴与各贯穿孔33、34、35的轴孔部33b、34b、35b的中心轴一致时,在与轴孔部33b、34b、35b之间可设置间隙c。
[0066]
相对移动机构74通过相对移动各升降销71、72、73与基座3,将利用搬运机构6搬运的硅晶片w载置至基座3。相对移动机构74包括基座支承部件75、升降销支承部件76以及驱动机构77。
[0067]
基座支承部件75以石英形成。基座支承部件75包括圆柱状的支柱751、从该支柱751的末端以放射状延伸的3支臂752以及设置在各臂752末端的支承销753。
[0068]
臂752在支柱751的圆周方向上以120
°
间隔向斜上方延伸设置。在臂752的长度方向中央设置有贯穿该臂752的贯穿孔752a。
[0069]
各支承销753以纯粹的sic形成,分别嵌入基座3的嵌合沟32内,由此支承该基座3。
[0070]
升降销支承部件76以石英形成。升降销支承部件76包括圆筒状的支柱761、从该支柱761的末端以放射状延伸的第1、第2、第3臂762、763、764以及设置在各臂762、763、764末端的第1、第2、第3抵接部765、766、767。
[0071]
各臂762、763、764在支柱761的圆周方向上以120
°
间隔向斜上方延伸设置。
[0072]
各抵接部765、766、767以各自的上端面765a、766a、767a将各升降销71、72、73从下方支承。将第1抵接部765形成为比第2抵接部766及第3抵接部767高。上端面765a与上端面766a、767a的高度差δh优选0.5mm以上且5mm以下,更优选2mm以上且3mm以下。
[0073]
在各臂762、763、764位于外延膜形成室20内的状态下,支柱761插入于下拱顶22的筒部221。在各臂762、763、764位于基座支承部件75的各臂752下方且被基座3支承的各升降销71、72、73下端可与各抵接部765、766、767的上端面765a、766a、767a抵接的状态下,在支柱761的内部插入有支柱751。
[0074]
驱动机构77又使基座支承部件75及升降销支承部件76旋转,又使升降销支承部件76升降。
[0075]
〔外延硅晶片的制造方法〕其次,对使用气相沉积装置1的外延硅晶片的制造方法进行说明。
[0076]
首先,准备p型或n型硅晶片w。当硅晶片w是p型时,添加有硼,当硅晶片w是n型时,添加有磷、砷及锑。硅晶片w的直径可以是200mm、300mm、450mm等任意大小。
[0077]
其次,配置于未图示的氮气氛的机器人室内的搬运机构6的支承部件61将硅晶片w支承为使其主面与水平面平行。然后,当配置于机器人室与腔室2之间的未图示的闸阀打门时,搬运机构6的搬运机器人62维持主面与水平面平行的状态不变将硅晶片w经由晶片运入运出口24运入至被加热部4加热的外延膜形成室20内,最后使其停止在基座3的锪孔部31上。
[0078]
此时,如图6a所示,基座3中,为了使第1贯穿孔33位于一对延伸部61b间的中心位置且比硅晶片w的中心w
c
更靠运入方向侧、使第2贯穿孔34及第3贯穿孔35位于主体部61a外侧且比中心w
c
更靠运出方向侧(机器人室侧),调整旋转方向的位置。
[0079]
其次,晶片传送装置5的驱动机构77使升降销支承部件76上升,并使被基座3支承的各升降销71、72、73上升。此时,由于第1抵接部765的上端面765a位于比第2抵接部766及第3抵接部767的上端面766a、767a更靠上方,因此各升降销71、72、73维持第1升降销71的头部71a位于比第2升降销72及第3升降销73的头部72a、73a更靠上方的状态不变而上升。因此,第1升降销71最初接触硅晶片w的下表面,然后,第2升降销72及第3升降销73接触。
[0080]
在此,假设,当将升降销支承部件76的抵接部765、766、767形成为相同高度时,各升降销71、72、73的头部71a、72a、73a维持位于相同高度的状态不变而上升。硅晶片w由于在外延膜形成室20内被加热部4加热,因此因该硅晶片w的两主面的温度差或热吸收的差产生弯曲。此时,由于硅晶片w的弯曲状态,最初接触硅晶片w的升降销或是第1升降销71,或是第2升降销72,不稳定。
[0081]
基座3的各贯穿孔33、34、35的轴孔部33b、34b、35b形成为在与各升降销71、72、73的轴部71b、72b、73b之间可设置间隙c。因此,例如,图6b中用双点划线所示的硅晶片w中,第1升降销71最初接触进而上升时,硅晶片w的重量只作用于第1升降销71,且第1升降销71的下端未固定至第1抵接部765,因此间隙c的存在导致第1升降销71倾斜。具体而言,第1升降销71以使头部71a向从基座3中心朝向第1贯穿孔33的第1方向侧d1移动的方式倾斜。
[0082]
如图6b中用实线所示,由于该第1升降销71的倾斜,硅晶片w向比基于搬运机构6的基座3上的停止位置更靠第1方向侧d1偏离。
[0083]
在该状态下,若进一步地使升降销支承部件76上升,则各升降销71、72、73全部接触硅晶片w,该硅晶片w从支承部件61被举起,但被举起时的硅晶片w的位置向比基座3上的停止位置更靠第1方向d1侧偏离。
[0084]
搬运机构6将支承部件61移动至腔室2外部,闸阀被关闭,则驱动机构77使升降销支承部件76下降,硅晶片w被载置至基座3的锪孔部31内,但如图6c所示,硅晶片w的载置位置维持比基座3上的目标载置位置p更靠第1方向d1侧偏离的状态。
[0085]
这种硅晶片w的载置位置偏离,在第2升降销72或第3升降销73最初接触硅晶片w时也同样发生。其偏离方向,在第2升降销72最初接触时,如图6a所示,成为从基座3中心朝向第2贯穿孔34的第2方向d2,在第3升降销73最初接触时,成为从基座3中心朝向第3贯穿孔35的第3方向d3。
[0086]
如此,当维持各升降销71、72、73的头部71a、72a、73a位于相同高度的状态不变并使这些上升时,不知道硅晶片w在基座3上的载置位置向哪个方向偏离。
[0087]
相对于此,本实施方式中,由于使第1升降销71最初接触硅晶片w的下表面,因此各升降销71、72、73全部接触硅晶片w时的硅晶片w的偏离方向成为第1方向d1。
[0088]
基于搬运机构6的运入的硅晶片w的停止位置,一般为基座3上的硅晶片w的目标载置位置p正上方,但本实施方式中,明白硅晶片w的载置位置以高概率从该停止位置向第1方向d1偏离。因此,预先掌握该偏离量δd,预先将基于搬运机构6的硅晶片w停止位置设定在从目标载置位置p正上方向与第1方向d1相反的方向侧仅返回δd的位置,由此能够将硅晶片w载置至基座3上的目标载置位置p上。
[0089]
并且,在以支承部件61将硅晶片w支承在基座3上的状态下,由于来自基座3的辐射热,硅晶片w下表面侧的温度比上表面侧的温度高。
[0090]
当硅晶片w是p++型时,由于硅晶片w的热吸收率高,因此容易产生由上述辐射热的影响引起的硅晶片w上下表面的温度差。因此,当将硅晶片w运入至基座3上时,如图7a所示,在短时间内下表面向下侧突出而弯曲。即,硅晶片w中,存在于支承部件61的一对延伸部61b之间的部分弯曲成比存在于主体部61a外侧的部分低。因此,如图7a中用双点划线所示,存在于一对延伸部61b之间的第1升降销71变得容易最初接触硅晶片w。
[0091]
另一方面,当硅晶片w是p
‑
型时,由于硅晶片w的热吸收率比p++型低,因此不易产生由辐射热的影响引起的硅晶片w上下表面的温度差。因此,当将硅晶片w运入至基座3上时,如图7a所示,下表面向下侧突出而弯曲,如图7b所示,上表面向上侧突出而弯曲。即,硅晶片w中,存在于一对延伸部61b之间的部分弯曲成比存在于主体部61a外侧的部分低或高。
[0092]
当硅晶片w弯曲成如图7a所示那样时,与p++型的情况相同地,第1升降销71变得容易最初接触硅晶片w。
[0093]
另一方面,当硅晶片w弯曲成如图7b所示那样时,若使各升降销71、72、73的高度位置相同,则变得容易最初接触存在于主体部61a外侧的第2升降销72或第3升降销73,而变得难以预先掌握载置位置向哪个方向偏离。结果,产生无法将硅晶片w载置至目标载置位置p上的情况。但是,本实施方式中,由于第1升降销71的高度位置比第2升降销72及第3升降销73高,因此通过使第1升降销71与第2升降销72、第3升降销73的高度差比硅晶片w的弯曲量大,如图7b的双点划线所示,变得容易使第1升降销71最初接触硅晶片w,能够预先掌握载置位置向哪个方向偏离。结果,即使是弯曲状态不稳定的p
‑
型硅晶片w,也能够将硅晶片w载置
至目标载置位置p上。
[0094]
另外,硅晶片w的弯曲量(硅晶片w的外缘与中央的差),也依赖于硅晶片w的厚度、外延膜形成室20内的温度,是1mm左右。
[0095]
在将硅晶片w载置至基座3后,从气体供给口25连续导入作为载体气体的氢气的同时,从气体排出口26将其排出,由此使外延膜形成室20内成为氢气氛。然后,使外延膜形成室20内的温度上升,与载体气体一起导入原料气体、掺杂气体至外延膜形成室20内的同时,通过驱动机构77使基座支承部件75及升降销支承部件76旋转,由此在硅晶片w上形成外延膜。
[0096]
另外,作为原料气体,例如使用sih4(甲硅烷)、sih2cl2(二氯硅烷)、sihcl3(三氯硅烷)、sicl4(四氯化硅)等。作为掺杂气体,当外延膜是p型时,使用b2h6(乙硼烷)、bcl3(三氯化硼)等硼化物,当外延膜是n型时,使用ph3(磷化氢)、ash3(砷化氢)等。
[0097]
在形成外延膜后,驱动机构77使升降销支承部件76上升,以各升降销71、72、73从基座3举起硅晶片w。然后,闸阀打开时,搬运机器人62将支承部件61移动至外延膜形成室20内部,停止在硅晶片w下方。然后,当驱动机构77使升降销支承部件76下降并将硅晶片w交接给支承部件61时,搬运机器人62将支承部件61与硅晶片w一起运出至外延膜形成室20外部,结束1片外延硅晶片的制造处理。
[0098]
〔实施方式的作用效果〕根据上述实施方式,由于使各升降销71、72、73中第1升降销71最初接触硅晶片w,因此预先掌握向第1方向d1的硅晶片w的载置位置偏离量,先设定基于搬运机构6的硅晶片w停止位置,由此能够将硅晶片w载置至所期望的位置。
[0099]
由于将第1抵接部765形成为比第2抵接部766及第3抵接部767高,因此即使使用相同形状的各升降销71、72、73,也能够将硅晶片w载置至所期望的位置。
[0100]
各升降销71、72、73中,将位于一对延伸部61b之间的第1升降销71作为特定的升降销并使其最初接触硅晶片w的下表面。因此,即使是弯曲状态不稳定的p
‑
型硅晶片w,也能够将硅晶片w载置至目标载置位置p。
[0101]
[变形例]另外,本发明不只限定于上述实施方式,在不脱离本发明的主旨的范围内,可以作各种改良及设计变更。
[0102]
例如,图8a所示,也可以使各抵接部765、766、767的高度相同,并使第1升降销71的长度比第2升降销72及第3升降销73更长,由此使第1升降销71与以主面与水平面平行的方式运入的硅晶片w最初接触。
[0103]
如图8b所示,也可以使各抵接部765、766、767的高度相同,并且使各升降销71、72、73的长度相同,利用搬运机构6的支承部件61以使其主面相对于水平面倾斜的方式运入硅晶片w,由此使第1升降销71最初接触硅晶片w。
[0104]
上述实施方式或图8a及图8b所示的变形例中,使第1升降销71最初接触硅晶片w,但也可以使第2升降销72或第3升降销73最初接触硅晶片w。当使第2升降销72或第3升降销73最初接触时,硅晶片w的载置位置向第2方向d2或第3方向d3偏离,但能够通过在将硅晶片w运入至外延膜形成室20前,根据偏离方向,向与硅晶片w的运入方向正交的方向移动支承部件61,由此将硅晶片w载置至所期望的位置。
[0105]
并且,也可以将各升降销71、72、73在基座3的圆周方向旋转180
°
的状态下进行配置。升降销的数量也可以是4个以上。
[0106]
也可以在以各升降销71、72、73全部从搬运机构6接受硅晶片w后,使各升降销71、72、73停止或者下降的同时,使基座3上升并将硅晶片w载置至基座3。
实施例
[0107]
其次,通过实施例更详细地对本发明进行说明,但本发明不受这些例子的任何限定。
[0108]
〔比较例〕首先,准备了与上述实施方式相同的气相沉积装置以及直径300mm且厚度775μm的p
‑
型硅晶片w。作为各升降销71、72、73,准备了轴部71b、72b、73b与各贯穿孔33、34、35的轴孔部33b、34b、35b的间隙c是0.25mm的升降销。
[0109]
然后,使各升降销71、72、73的高度位置相同,将外延膜形成室20内加热至700℃,进行了对基座3的硅晶片w的载置处理。利用测量装置(epicrew公司制edge zoom)从基座上方测量了被载置至基座3的硅晶片w中心与目标载置位置p中心的偏离。对100片硅晶片w进行了相同的实验。
[0110]
〔实施例1〕除了使第1升降销71的高度位置比第2升降销72及第3升降销73高1mm以外,进行了与比较例1相同的实验。
[0111]
〔实施例2〕除了使第1升降销71的高度位置比第2升降销72及第3升降销73高2mm以外,进行了与比较例1相同的实验。
[0112]
〔评价〕将比较例、实施例1、2的各测量结果示于图9a、图9b及图9c。
[0113]
另外,图9a、图9b及图9c中,纵轴y及横轴x的值,是以图1、图2、图6a~图6c、图7a、图7b的xyz轴为基准的值。即,纵轴y的正值表示向硅晶片w的运出方向的偏离,负值表示向硅晶片w的运入方向(第1方向d1)的偏离。并且,横轴x的正值表示向与运入方向正交的一方向(第3方向d3侧)的偏离,负值表示向与运入方向正交的另一方向(第2方向d2侧)的偏离。
[0114]
并且,当横轴及纵轴的位置都是0mm时,表示硅晶片w的载置位置不从目标载置位置p偏离。
[0115]
比较例中,如图9a所示,载置位置从目标载置位置p向基座3的圆周方向的各位置偏离,偏离位置波动大。
[0116]
认为其理由在于,如上所述,由于p
‑
型硅晶片w的弯曲在图7a或图7b中任一状态下发生,因此最初接触硅晶片w的升降销不是特定的。
[0117]
相对于此,实施例1中,如图9b所示,载置位置集中在从目标载置位置p偏离的特定2处,相较于比较例偏离位置的波动小。
[0118]
而且,实施例2中,如图9c所示,载置位置集中在从目标载置位置p偏离的特定1处,相较于比较例及实施例1偏离位置的波动小。
[0119]
认为其理由在于,即使是弯曲方向不稳定的p
‑
型硅晶片w,通过使第1升降销71的
高度位置比第2升降销72及第3升降销73高,第1升降销71最初接触硅晶片w的概率也变高,高度位置的差越大其概率越高。
[0120]
并且,能够推断若使第1升降销71的高度位置与第2升降销72及第3升降销73的高度位置的差大于2mm,则载置位置从目标载置位置p偏离的波动更加变小。
[0121]
通过上述内容,确认到通过使第1升降销71的高度位置比第2升降销72及第3升降销73高,能够控制硅晶片w的载置位置从目标载置位置p偏离的波动。
[0122]
尤其,确认到若第1升降销71的高度位置与第2升降销72及第3升降销73的高度位置的差在2mm以上,则能够使硅晶片w的载置位置集中在特定的1处,偏离的波动更加变小。
[0123]
根据这些结果,预先掌握与各升降销71、72、73的高度位置的设定条件相对应的硅晶片w的载置位置偏离量及偏离方向,例如,以在实施例1的条件下在图10a所示的位置上、在实施例2的条件下在图10b所示的位置上载置硅晶片w的方式,预先使基于搬运机构6的硅晶片w的搬运停止位置偏离,则能够将硅晶片w载置至所期望的位置。
[0124]
附图标记说明1
‑
气相沉积装置,3
‑
基座,5
‑
晶片传送装置,6
‑
搬运机构,7
‑
载置机构,33、34、35
‑
贯穿孔,61
‑
支承部件,71、72、73
‑
升降销,74
‑
相对移动机构,76
‑
升降销支承部件,765、766、767
‑
抵接部,w
‑
硅晶片。