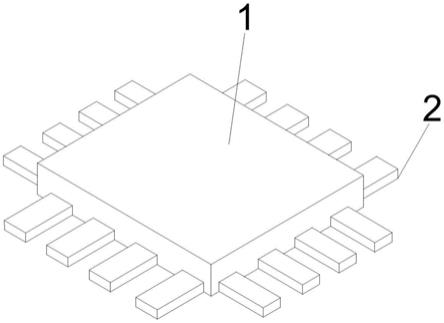
1.本发明涉及半导体复合散热材料的封装结构技术领域,具体为一种半导体复合散热材料的封装结构及其制造方法。
背景技术:2.半导体封装是指将通过测试的晶圆按照产品型号及功能需求加工得到独立芯片的过程。封装过程为:来自晶圆前道工艺的晶圆通过划片工艺后被切割为小的晶片,然后将切割好的晶片用胶水贴装到相应的基板(引线框架)架的小岛上,再利用超细的金属(金锡铜铝)导线或者导电性树脂将晶片的接合焊盘连接到基板的相应引脚,并构成所要求的电路;然后再对独立的晶片用塑料外壳加以封装保护,塑封之后还要进行一系列操作,封装完成后进行成品测试,通常经过入检。
3.现有的半导体封装由于其工艺的问题,半导体复合散热材料封装结构尺寸较大,进而导致了现有的半导体封装电阻比较大,导致了信号延迟高的问题。
技术实现要素:4.(一)解决的技术问题
5.针对现有技术的不足,本发明提供了一种半导体复合散热材料的封装结构及方法。
6.(二)技术方案
7.为实现上述目的,本发明提供如下技术方案:一种半导体复合散热材料的封装结构,包括载体,所述载体的为矩形的块,且载体的内部固定安装有芯片,所述载体的前后左右四侧外壁面上分别固定安装有引脚。
8.一种半导体复合散热材料的封装结构方法,其特征在于,包括以下步骤:第一步:对硅片减薄,然后利用切割设备对硅片切割,将硅片切割成大小合格,硅片的背面减薄需要经过有磨磨、切割、研磨、倒角、抛光(化学机械抛光以及干式抛光)、化学腐蚀(电化学腐蚀、湿法腐蚀以及等离子增强化学腐蚀)以及硅片检测,在背面磨削之前将硅片正面切割出一定深度的切口,然后再进行背面磨削。
9.第二步:芯片贴装,芯片贴装的方式四种:共晶粘贴法,焊接粘贴法,导电胶粘贴法,和玻璃胶粘贴法,共晶粘贴法:利用金-硅合金(一般是69%au,31%的si),363度时的共晶熔合反应使ic芯片粘贴固定。
10.第三步:芯片互连,打线键合,载在自动键合(tab)和倒装芯片键合,打线键合技术有,超声波键合、热压键合以及热超声波键合,打线键合(wb)是将细金属线或金属带按顺序打在芯片与引脚架或封装基板的焊垫上形成电路互连。
11.第四步:成型,塑料封装的成型技术,一、转移成型技术,二、喷射成型技术,三、预成型技术但最主要的技术是转移成型技术,转移技术使用的材料一般为热固性聚合物。
12.第五步:芯片互连:将芯片焊区与电子封装外壳的i/o或基板上的金属布线焊区相
连接,只有实现芯片与封装结构的电路连接才能发挥已有的功能。
13.优选的,所述在硅片减薄之前,先用机械或化学的方式切割处切口,然后用磨削方法减薄到一定厚度之后采用adpe腐蚀技术去除掉剩余加工量实现裸芯片的自动分离。
14.优选的,所述为了获得最佳的共晶贴装所采取的方法,ic芯片背面通常先镀上一层金的薄膜或在基板的芯片承载座上先植入预芯片。
15.优选的,所述tab是将芯片焊区与电子封装外壳的i/o或基板上的金属布线焊区用具有引线图形金属箔丝连接,其中的关键技术:1芯片凸点制作技术2tab载带制作技术3载带引线与芯片凸点的内引线焊接和载带外引线焊接技术,凸点芯片的制作工艺,形成凸点的技术:蒸发/溅射涂点制作法,电镀凸点制作法置球及模板印刷制作,焊料凸点发,化学镀涂点制作法,打球凸点制作法,激光法。
16.(三)有益效果
17.与现有技术相比,本发明提供了一种半导体复合散热材料的封装结构及方法,具备以下有益效果:该半导体复合散热材料的封装结构及其制造方法,薄的芯片更有利于散热,减小芯片封装体积,提高机械性能、硅片减薄、其柔韧性越好,受外力冲击引起的应力也越小,晶片的厚度越薄,元件之间的连线也越短,元件导通电阻将越低,信号延迟时间越短,从而实现更高的性能,减轻划片加工量减薄以后再切割,可以减小划片加工量,降低芯片崩片的发生率。
附图说明
18.图1为本发明结构立体示意图;
19.图2为本发明结构剖视示意图。
20.图中:1载体、2引脚、3芯片。
具体实施方式
21.下面将结合本发明实施例中的附图,对本发明实施例中的技术方案进行清楚、完整地描述,显然,所描述的实施例仅仅是本发明一部分实施例,而不是全部的实施例。基于本发明中的实施例,本领域普通技术人员在没有做出创造性劳动前提下所获得的所有其他实施例,都属于本发明保护的范围。
22.请参阅图1-2,一种半导体复合散热材料的封装结构,包括载体1,所述载体1的为矩形的块,且载体1的内部固定安装有芯片3,所述载体1的前后左右四侧外壁面上分别固定安装有引脚2。
23.一种半导体复合散热材料的封装结构方法,其特征在于,包括以下步骤:第一步:对硅片减薄,然后利用切割设备对硅片切割,将硅片切割成大小合格,硅片的背面减薄需要经过有磨磨、切割、研磨、倒角、抛光(化学机械抛光以及干式抛光)、化学腐蚀(电化学腐蚀、湿法腐蚀以及等离子增强化学腐蚀)以及硅片检测,在背面磨削之前将硅片正面切割出一定深度的切口,然后再进行背面磨削。
24.所述化学机械抛光技术是化学作用和机械作用相结合的技术,其过程相当复杂,影响因素很多。首先工件表面材料与抛光液中的氧化剂、催化剂等发生化学反应,生成一层相对容易去除的软质层,然后在抛光液中的磨料和抛光垫的机械作用下去除软质层,使工
件表面重新裸露出来,然后再进行化学反应,这样在化学作用过程和机械作用过程的交替进行中完成工件表面抛光。
25.所述电化学腐蚀就是金属和电解质组成两个电极,组成腐蚀原电池。例如铁和氧气,因为铁的电极电位总比氧的电极电位低,所以铁是负极,遭到腐蚀。特征是在发生氧腐蚀的表面会形成许多直径不等的小鼓包,次层是黑色粉末状溃疡腐蚀坑陷,不纯的金属跟电解质溶液接触时,会发生原电池反应,比较活泼的金属失去电子而被氧化,这种腐蚀叫做电化学腐蚀。钢铁在潮湿的空气中所发生的腐蚀是电化学腐蚀最突出的例子。钢铁在干燥的空气里长时间不易腐蚀,但潮湿的空气中却很快就会腐蚀。原来,在潮湿的空气里,钢铁的表面吸附了一层薄薄的水膜,这层水膜里含有少量的氢离子与氢氧根离子,还溶解了氧气等气体,结果在钢铁表面形成了一层电化学腐蚀电解质溶液,它跟钢铁里的铁和少量的碳恰好形成无数微小的原电池。在这些原电池里,铁是负极,碳是正极。铁失去电子而被氧化.电化学腐蚀是造成钢铁腐蚀的主要原因。
26.所述湿法化学腐蚀是最早用于微机械结构制造的加工方法。所谓湿法腐蚀,就是将晶片置于液态的化学腐蚀液中进行腐蚀,在腐蚀过程中,腐蚀液将把它所接触的材料通过化学反应逐步浸蚀溶掉。用于化学腐蚀的试剂很多,有酸性腐蚀剂,碱性腐蚀剂以及有机腐蚀剂等。根据所选择的腐蚀剂,又可分为各向同性腐蚀和各向异性腐蚀剂。各向同性腐蚀的试剂很多,包括各种盐类(如cn基、nh基等)和酸,但是由于受到能否获得高纯试剂,以及希望避免金属离子的玷污这两个因素的限制,因此广泛采用hf—hno3腐蚀系统。各向异性腐蚀是指对硅的不同晶面具有不同的腐蚀速率。基于这种腐蚀特性,可在硅衬底上加工出各种各样的微结构。各向异性腐蚀剂一般分为两类,一类是有机腐蚀剂,包括epw(乙二胺、邻苯二酚和水)和联胺等,另一类是无机腐蚀剂,包括碱性腐蚀液,如koh、naoh以及nh4oh。
27.所述化学腐蚀是指金属与外部介质直接起化学作用,引起表面的破坏。它与电化学腐蚀的区别是没有电流产生,开始时,在金属表面形成一层极薄的氧化膜,然后逐步发展成较厚的氧化膜,当形成第一层金属氧化膜后,它可以减慢金属继续腐蚀的速度,从而起到保护作用,但所形成的膜必须是完整的,才能阻止金属的继续氧化,化学腐蚀金属与空气接触生成氧化膜就是化学腐蚀的一种。金属表面与机油接触,由于机油中含有有机酸或酸性物质,使零件表面受到强烈腐蚀;燃料与润滑油中含有硫的成分.它对轴承合金的影响很大,对钢铁也有很强的腐蚀作用。金属表面的腐蚀,使金属材料的性质起了很大变化,甚至严重损坏。如有机酸把铜铅合金轴承的铅腐蚀掉,增加了轴承的负荷应力和摩擦系数,加速了磨损,常常引起合金脱落。
28.第二步:芯片贴装,芯片贴装的方式四种:共晶粘贴法,焊接粘贴法,导电胶粘贴法和玻璃胶粘贴法,共晶粘贴法:利用金-硅合金(一般是69%au,31%的si),363度时的共晶熔合反应使ic芯片粘贴固定。
29.所述焊接是金属加工的主要方法之一,它是将两个或两个以上分离的工件,按一定的形式和位置连接成一个整体的工艺过程。焊接的实质,是利用加热或其他方法,使焊料与被焊金属之间互相吸引、互相渗透,依靠原子之间的内聚力使两种金属达到永久牢固地结合。
30.第三步:芯片互连,打线键合,载在自动键合(tab)和倒装芯片键合,打线键合技术有,超声波键合、热压键合以及热超声波键合,打线键合(wb)是将细金属线或金属带按顺序
打在芯片与引脚架或封装基板的焊垫上形成电路互连。
31.第四步:成型,塑料封装的成型技术,一、转移成型技术,二、喷射成型技术,三、预成型技术但最主要的技术是转移成型技术,转移技术使用的材料一般为热固性聚合物。
32.喷射成形是用高压惰性气体将合金液流雾化成细小熔滴,在高速气流下飞行并冷却,在尚未完全凝固前沉积成坯件的一种工艺。它具有所获材料晶粒细小、组织均匀、能够抑制宏观偏析等快速凝固技术的各种优点,它是是把金属熔融、液态金属雾化、快速凝固、喷射沉积成形集成在一个冶金操作流程中制成金属材料产品的新工艺技术,对发展新材料、改革传统工艺、提升材料性能、节约能耗、减少环境污染都具有重大作用,由于快速凝固的作用,所获金属材料成分均匀、组织细化、无宏观偏析,且含氧量低。与传统的铸一锻工艺和粉末冶金工艺相比较,它流程短、工序简化、沉积效率高,不仅是一种先进的制取坯料技术,还正在发展成为直接制造金属零件的制程。现已成为世界新材料开发与应用的一个热点,和气雾化制粉法相似,先将熔融的金属或合金液体用氮气或氩气雾化为细小液滴,只是不待凝固为粉时便直接喷射沉积成预形坯,其相对密度可达96%以上,经后续热加工(锻、轧、挤或热等静压)成全致密产品。这种喷射成形产品因受快速凝固作用使其结晶结构细化,成分均匀而无宏观偏析,它几乎具有粉末冶金制品的优点,但可省去制粉、筛分、压制和烧结等工序,降低了生产成本。
33.热固性聚合物一般先形成预聚物,成型时,经加热使其中潜在的官能团继续反应成交联结构而固化。这种转变时不可逆的,只能成型一次,再加热时不能熔融塑化,也不溶于溶剂,一般是体型聚合物,如酚醛树脂以及硫化橡胶。
34.第五步:芯片互连:将芯片焊区与电子封装外壳的i/o或基板上的金属布线焊区相连接,只有实现芯片与封装结构的电路连接才能发挥已有的功能。
35.所述在硅片减薄之前,先用机械或化学的方式切割处切口,然后用磨削方法减薄到一定厚度之后采用adpe腐蚀技术去除掉剩余加工量实现裸芯片的自动分离。
36.所述为了获得最佳的共晶贴装所采取的方法,ic芯片背面通常先镀上一层金的薄膜或在基板的芯片承载座上先植入预芯片。
37.所述tab是将芯片焊区与电子封装外壳的i/o或基板上的金属布线焊区用具有引线图形金属箔丝连接,其中的关键技术:1芯片凸点制作技术2tab载带制作技术3载带引线与芯片凸点的内引线焊接和载带外引线焊接技术,凸点芯片的制作工艺,形成凸点的技术:蒸发/溅射涂点制作法,电镀凸点制作法置球及模板印刷制作,焊料凸点发,化学镀涂点制作法,打球凸点制作法,激光法。
38.所述硅片减薄需要经过滚磨:切片前先将硅单晶棒研磨成具有精确直径的单晶棒,再沿单晶棒的晶轴方向研磨出主、次参考面,用氢氟酸、硝酸和冰醋酸的混合液腐蚀研磨面,称为减径腐蚀。
39.切割:也称切片,把硅单晶棒切成所需形状的硅片(如圆片)的工艺。切割分多线切割、外圆切割、超声切割、电子束切割和普遍采用的内圆切割等。
40.研磨:也称磨片,在研磨机上,用白刚玉或金刚砂等配制的研磨液将硅片研磨成具有一定厚度和光洁度的工艺。有单面研磨和双面研磨两种方式。
41.倒角:为解决硅片边缘碎裂所引起的表面质量下降,以及光刻涂胶和外延的边缘凸起等问题的边缘弧形工艺。倒角方法有磨削、喷砂、化学腐蚀和恰当的抛光等,较普遍采
用的是用倒角机以成型的砂轮磨削硅片边缘,直到硅片边缘形状与轮的形状一致为止。
42.化学腐蚀:也称减薄腐蚀,目的是除去切磨后硅片表面的损伤层和沾污层,改善表面质量和提高表面平整度。化学腐蚀法有篮式、桶式、旋转杆式和盒式,采用氢氟酸、硝酸和冰醋酸的混合液从硅片两侧腐蚀掉一定的厚度。
43.抛光:为了制备合乎器件和集成电路制作要求的硅片表面,,以除去残留的损伤层并获得一定厚度的高平整度的镜面硅片。抛光分机械抛光、化学抛光、电子束抛光、离子束抛光,较普遍采用的是化学机械抛光。化学机械抛光是化学腐蚀和机械磨削同时进行,分为铜离子抛光、铬离子抛光和普遍采用的二氧化硅胶体抛光。二氧化硅胶体抛光是由极细的二氧化硅粉、氢氧化钠(或有机碱)和水配制成胶体抛光液。在抛光过程中,氢氧化钠与硅表面反应生成硅酸钠,通过与二氧化硅胶体的磨削,硅酸钠进入抛光液,两个过程不停顿地同时进行而达到抛光的目的。根据不同要求,可用一次抛光、二次抛光(粗抛光和精抛光)或三次抛光(粗抛光、中间抛光和精抛光)。为满足超大规模集成电路对表面质量和平整度的要求,已有无蜡抛光和无磨料抛光等新工艺。
44.硅抛光片检测:包括目检、几何尺寸检测和热氧化层错检测等。目检是在正面高强度光或大面积散射光照射下目测抛光片上的原生缺陷和二次缺陷。这些缺陷包括边缘碎裂、沾污、裂纹、弧坑、鸦爪、波纹、槽、雾、嵌入磨料颗粒、小丘、桔皮、浅坑、划道、亮点、退刀痕和杂质条纹等。几何尺寸的检测包括硅片的厚度、总厚度变化、弯曲度和平整度的检测。厚度为硅片中心上、下表面两个对应点之间的距离;总厚度变化为同一硅片上厚度最大值与最小值之差;弯曲度为硅片的中线面与参考平面之间距离的最大值与最小值之差;平整度指硅片表面上最高点与最低点的高度差,用总指示读数表征。硅片的热氧化层错检测是指硅抛光片表面的机械损伤、杂质沾污和微缺陷等在硅片热氧化过程中均会产生热氧化层错,经择优腐蚀后,在金相显微镜下观测热氧化层错的密度,以此鉴定硅片表面的质量。
45.尽管已经示出和描述了本发明的实施例,对于本领域的普通技术人员而言,可以理解在不脱离本发明的原理和精神的情况下可以对这些实施例进行多种变化、修改、替换和变型,本发明的范围由所附权利要求及其等同物限定。