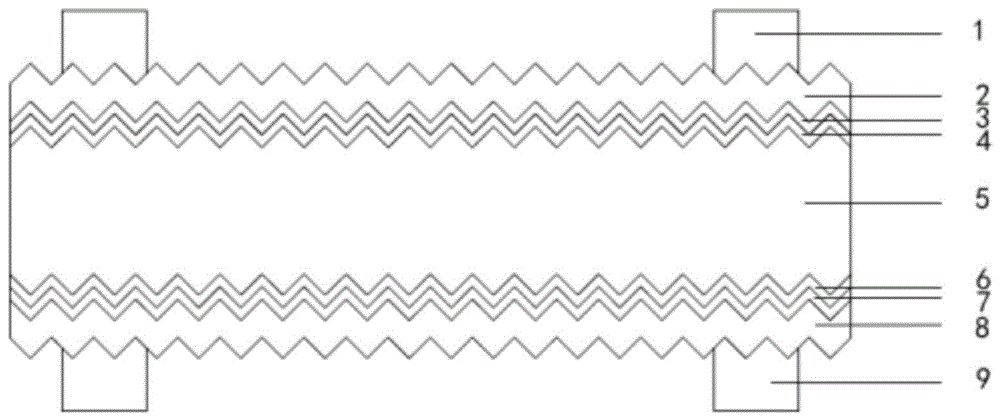
一种硅异质结shj太阳能电池及其制备方法,属于半导体光电转换技术领域,具体涉及硅异质结shj太阳能电池技术领域。
背景技术:
随着经济社会的发展,大量使用常规化石能源,导致了严重的环境污染问题,发展利用清洁能源已成为人们的共识。由于太阳能取之不尽用之不竭,清洁无污染,是未来最理想最可持续的可再生能源。太阳能电池直接将光能转变为电能,是太阳能利用的一种重要方式。太阳电池通常是由一种或者两种以上具有吸收太阳光并且转化成电能的材料结合在一起形成同质结(homojunction)或者异质结(heterojunction)半导体二极管结构。太阳电池吸收太阳光并产生电子和空穴对,通常称为光生载流子,经过二极管的内建电场分离后电子和空穴分别集聚到n型和p型半导体区形成电势。为了有效地把电子和空穴输送到外部电路,通常在前表面(第一受光面)和后表面(第二受光面)制作金属电极,金属电极与半导体材料形成良好的电学接触,把光生载流子有效地输送到外部电路。
对于硅异质结太阳电池,由于其特殊的全程低温工艺,要求金属电极制备过程中必须使用低温树脂固化型银浆料。该低温银浆料的常在180-200℃固化成型,可低温或常温保存。由于低温浆料内部含有大量有机树脂,保质期一般只有3-6个月。同时,低温银浆固化后的电阻率较高,为4-8×10-6ω·cm,约为高温浆料的2倍,导电性能较差。低温银浆料依赖于树脂粘附力粘附在电池表面,焊接拉力较差。为了弥补导电性差和焊接拉力小,需要增加单片电池的银浆使用量。
为了利用太阳电池进行大规模发电,同时增强太阳电池本身抵抗恶劣环境影响的能力,增加各种环境的使用可靠性,需要对太阳电池进行串并联组合,制备成太阳电池组件。常规太阳能电池组件是采用焊带焊接的方式,将尺寸为210cm×210cm、166cm×166cm、156.75cm×156.75cm或125cm×125cm等规格的太阳电池片正电极和负电极互连,形成具有一定电流、电压输出的发电单元。随着光伏技术的发展,组件技术也日新月异,目前市场上常见的组件技术有3主栅线(busbar-bb)、4bb、5bb、6bb、9bb和12bb的整片、半片、三分之一片焊接技术;无主栅(nonbusbar-nbb)的整片和半片封装技术;叠瓦5分片、6分片封装技术;以及采用导电胶水(eca)粘接技术、导电胶带(acf)粘接技术等各种各样的组件技术。由于组件技术多种多样,需要的太阳电池的金属电极图形也有很大区别,即使是相同的组件技术,如9bb组件,不同组件厂商所用的主栅间距也不尽相同。如此大量的太阳电池金属电极图形类型,给太阳电池生产厂家带来了很大的苦恼。通常太阳电池产生厂家只能等客户确定订单和电极图形后才能进行生产,往往会耽误大量时间和产能,造成经济损失。
技术实现要素:
本发明的目的在于:提供一种硅异质结shj太阳能电池及其制备方法,以解决上述由于太阳能电池金属电极图形类型量大,通常太阳电池产生厂家只能等客户确定订单和电极图形后才能进行生产,往往会耽误大量时间和产能,造成经济损失的缺陷。同时可减小金属电极线对光的遮挡,减少银浆耗量,提高太阳电池的光电转换效率。
本发明采用的技术方案如下:
一种硅异质结shj太阳能电池,太阳电池受光面分为第一受光面和第二受光面,第一受光面包括依次设置在单晶硅衬底一侧的第一本征非晶硅层、n型掺杂非晶硅叠层、第一tco薄膜层以及第一金属栅线电极,第二受光面包括依次设置在单晶硅衬底另一侧的第二本征非晶硅层、p型掺杂非晶硅叠层、第二tco薄膜层以及第二金属栅线电极,第一金属栅线电极和第二金属栅线电极均分别包括一组多个平行的金属细栅线和边框线,金属细栅线和/或边框线的宽度为20-100μm,金属细栅线间距为0.5-2.5mm。第一金属栅线电极和第二金属栅线电极图形只有金属细栅线,无主栅,金属细栅线和边框线组成的图形四个边角分别设置有预留定位的mark点,形成一种异质结太阳电池。
该异质结太阳电池既可以作为一种新产品满足组件制备需要,亦可根据需要将金属电极图形快速变化为常用的多种太阳电池产品金属电极图形。异质结太阳电池电极图形改变方法为:采用丝网印刷的方法,依靠mark点进行图形精确定位,在此异质结太阳电池的第一受光面和第二受光面原图形基础上,制备主栅电极、定位线、防断栅线等,完成其他所需电极图形的制备。
优选的,金属细栅线和边框线组成的图形四个边角分别设置有定位mark点。
优选的,mark点为圆形、长方形、正方形或圆形,圆形mark点的直径为0.1-1mm,长方形和正方形mark点的边长为0.1-1mm。
优选的,第一金属栅线电极和第二金属栅线电极的宽度为20-100μm。
更为优选的,第一金属栅线电极和第二金属栅线电极的宽度为55μm。
优选的,相邻金属细栅线之间的间距l为0.5-2.5mm。
优选的,在第一受光面和第二受光面的端部分别设置有垂直于金属细栅线的焊带定位线。
优选的,在第一受光面和第二受光面上垂直于细栅线方向设置有主栅线和防断栅线。
一种所述的硅异质结shj太阳能电池的制备方法,包括如下步骤:
a、以n型单晶硅作为衬底,利用碱溶液的各向异性腐蚀功能进行制绒,制作具有减反射功能的表面金字塔结构,经过sc1和sc2进行清洗,腐蚀去掉表面氧化层,得到清洁的表面;
b、利用pecvd在n型单晶硅衬底的一面制作第一本征非晶硅n型掺杂非晶硅叠层,在衬底的第二面制作第二本征非晶硅和p型掺杂非晶硅叠层,第一本征非晶硅层、第二本征非晶硅层的厚度分别为4-10nm,n型和p型掺杂非晶硅叠层的厚度分别为5-20nm;
c、分别在n型和p型掺杂非晶硅叠层分别沉积第一tco薄膜层和第二tco薄膜层,第一tco薄膜层和第二tco薄膜层的电子浓度在5x1019cm-3至5x1020cm-3之间,电阻率在1x10-4至8x10-4ω·cm之间,迁移率大于30cm2/vs,形成shj电池的第一受光面和第二受光面,在400-1100nm波长范围的光学透过率大于88%;
d、利用丝网印刷制作金属栅线电极,第一受光面和第二受光面的第一金属栅线电极和第二金属栅线电极均由一组多个平行的金属细栅线和边框线组成,金属细栅线和边框线组成的图形四个边角分别设置有预留定位的mark点,采用树脂型低温固化银浆,印刷后栅线平均宽度为20-100μm,在100-200℃条件下干燥1-20min,紧接着在150-250℃条件下固化5-60min;
e、依靠定位mark点,采用丝网印刷技术和低温导电浆料,在电池端部制备多条垂直于金属细栅线的焊带定位线,或垂直于细栅线方向制备主栅和防断栅线,焊带定位线或主栅线和防断栅线印制完成后在100-200℃条件下干燥1-20min,紧接着在150-250℃条件下固化5-60min。
更为优选的,步骤d中在150度条件下干燥10分钟,紧接着在200度条件下固化40分钟。
优选的,步骤d完成后,将低温细焊带直接垂直压在异质结太阳电池第一受光面和第二受光面,然后进行组件的加热层压,利用层压温度,使低温焊带涂层熔融,焊带直接粘合在金属细栅线上,完成组件的制备。焊带涂层为锡铅铋、锡铋银或锡铋铟低温合金。
优选的,步骤e完成后,在主栅线位置,采用焊带焊接的方式对异质结太阳电池进行串并联接,然后进行组件的加热层压,完成组件制备。
更为优选的,步骤e中焊带定位线印制完成后在150度条件下干燥10分钟,紧接着在200度条件下固化40分钟。
综上所述,由于采用了上述技术方案,本发明的有益效果是:
1、本发明中,第一金属栅线电极和第二金属栅线电极图形只有金属细栅线,无主栅,金属细栅线和边框线组成的图形四个边角分别设置有预留定位的mark点。该太阳电池细栅线的宽度在20-100μm之间,可降低银浆使用量,银耗量<150mg,同时可减小金属电极线对光的遮挡,提高太阳电池的光电转换效率和组件输出功率。
2、该异质结太阳电池可以作为一种新产品满足组件制备需要,亦可根据需要将金属电极图形快速变化为常用的多种太阳电池产品金属电极图形。在第一受光面和第二受光面,制备垂直于金属细栅线方向的主栅线、焊带定位线、防断栅线等,依靠mark点进行图形精确定位,制备成所需电极图形,可以有效提高产线利用率,缩短产品交货时间,加快满足客户需求。
附图说明
图1为本发明shj电池的断面结构图;
图2为本发明多功能金属细栅线电极结构图;
图3为本发明带焊带定位线无主栅shj太阳电池的细栅线电极结构图;
图4为本发明转换为5bb太阳电池的电极结构图。
图中标记:1-第一金属栅线电极,2-第一tco薄膜层,3-n型掺杂非晶硅叠层,4-第一本征非晶硅层,5-单晶硅衬底,6-第二本征非晶硅层,7-p型掺杂非晶硅叠层,8-第二tco薄膜层,9-第二金属栅线电极。
具体实施方式
为了使本发明的目的、技术方案及优点更加清楚明白,以下结合附图及实施例,对本发明进行进一步详细说明。应当理解,此处所描述的具体实施例仅用以解释本发明,并不用于限定本发明。
实施例1
一种硅异质结shj太阳能电池,包括依次设置在单晶硅衬底5一侧的第一本征非晶硅层4、n型掺杂非晶硅叠层3、第一tco薄膜层2以及第一金属栅线电极1,依次设置在单晶硅衬底5另一侧的第二本征非晶硅层6、p型掺杂非晶硅叠层7、第二tco薄膜层8以及第二金属栅线电极9,其特征在于:第一金属栅线电极1和第二金属栅线电极9均分别包括一组多个平行的金属细栅线和边框线,金属细栅线和/或边框线的宽度为20-100μm,金属细栅线间距为0.5-2.5mm,
如图1所示多功能金属电极shj太阳电池的基本结构,以n型单晶硅作为衬底,利用等离子体增强化学气相沉积(pecvd)或者热丝催化化学气相沉积(cat-cvd)等在n型单晶衬底的第一面制作第一本征非晶硅和n型掺杂非晶硅叠层,在n型单晶硅衬底5的第二面制作第二本征非晶硅和p型掺杂非晶硅叠层。利用磁控溅射(pvd)或者反应性等离子体沉积(rpd)分别在第一面和第二面制作具有高电导性和高透光率的透明导电第一tco薄膜层2和第二tco薄膜层8形成shj电池的第一受光面和第二受光面。第一受光面和第二受光面都不设置主栅线,仅依靠细栅线收集光生载流子,细栅线与第一tco薄膜层2及细栅线与第二tco薄膜层8之间分别形成良好的欧姆接触。多功能金属细栅线图形如图2所示。
实施例2
一种硅异质结shj太阳能电池的制备方法,包括如下步骤:
a、以n型单晶硅作为衬底,利用koh碱溶液的各向异性腐蚀功能进行制绒,制作具有减反射功能的表面金字塔结构,金字塔的平均底边尺寸为2-3微米,经过sc1和sc2进行清洗,利用hf水溶液腐蚀去掉表面氧化层,得到清洁的表面,然后利用等离子体增强化学气相沉积(pecvd)进行非晶硅薄膜沉积;
b、利用pecvd在n型单晶衬底的一面制作本征非晶硅和n型掺杂非晶硅叠层,在衬底的第二面制作本征非晶硅和p型掺杂非晶硅叠层,本征非晶硅层的厚度为4-8nm,n型和p型掺杂非晶硅层的厚度分别为5-20nm,然后传递到反应等离子体沉积(rpd)设备沉积第一tco薄膜层2和第二tco薄膜层8;
c、利用rpd设备分别在第一受光面和第二受光面分别沉积第一tco薄膜层2和第二tco薄膜层8,通过对设备和沉膜条件优化保证得到高品质第一tco薄膜层2和第二tco薄膜层8,利用霍尔效应测试仪测量第一tco薄膜层2和第二tco薄膜层8,其电子浓度在5x1019cm-3至5x1020cm-3之间,电阻率在1x10-4至8x10-4ωcm之间,迁移率大于30cm2/vs,这样形成shj电池的第一受光面和第二受光面,利用分光光度计测量第一tco薄膜层2和第二tco薄膜层8在400-1100nm波长范围的光学透过率大于88%;
d、利用丝网印刷制作金属栅线电极,第一受光面和第二受光面的第一金属栅线电极1和第二金属栅线电极9结构及分布如图2所示,第一金属栅线电极1和第二金属栅线电极9均由一组多个平行的金属细栅线和边框线组成,金属细栅线和边框线组成的图形四个边角分别设置有预留定位的mark点,网板的细栅线开口宽度为30微米,采用树脂型低温固化银浆,印刷后栅线平均宽度为65微米,在150度条件下干燥10分钟,紧接着在200度条件下固化40分钟,这样就完成了多功能shj电池的基本制作,多功能金属细栅线图形如图2所示;
e、在第四步制备完成的多功能金属电极shj太阳电池基础上,即在图2所示的多功能金属栅线结构的基础上,利用图2上的定位mark点,采用丝网印刷技术和低温导电浆料,在电池端部制备多条垂直于金属细栅线的焊带定位线,该定位线可以在后续组件制备过程中对焊带进行定位,同时可以防止焊带摆放触及不到电池边界,起到栅线互联的作用,所述导电浆料可以与第四步浆料相同或采用不同浆料,焊带定位线印制完成后在150度条件下干燥10分钟,紧接着在200度条件下固化40分钟,这样就完成了多功能shj电池转换为焊带定位线nbb电池的制作,如图3所示为带焊带定位线的nbb电极图形;
更为优选的,利用此多功能shj电池和低温焊带直接制备组件,将低温细焊带直接垂直压在shj第一受光面和第二受光面,然后进行组件的加热层压,利用层压温度,使低温焊带涂层熔融,焊带直接粘合在金属细栅线上,完成组件的制备,焊带涂层为锡铅铋、锡铋银、锡铋铟等低温合金。
更为优选的,在第四步制备完成的多功能金属电极shj太阳电池基础上,依靠定位mark点,采用丝网印刷技术和低温导电浆料制备5条主栅图形和防断栅线,所述导电浆料可以与第四步浆料相同或采用不同浆料。然后在150度条件下干燥10分钟,紧接着在200度条件下固化40分钟,这样就完成了多功能金属电极shj电池转换为5bb电池的制作。
精确定位制备主栅线形成图4所示的具有5条主栅线的5bb电极图形,采用同样方式也可以制备9bb、12bb等电极图形,不再穷举。
以上介绍金属电极的制作方法采用了丝网印刷技术,电镀铜的方法可以达到相同或更好的效果,研究结果证明,采用电镀铜金属电极技术可以提高转换效率0.3%以上,但是,考虑到原材料、工艺成本、工艺复杂性等问题,本申请专门介绍。
以上所述仅为本发明的较佳实施例而已,并不用以限制本发明,凡在本发明的精神和原则之内所作的任何修改、等同替换和改进等,均应包含在本发明的保护范围之内。