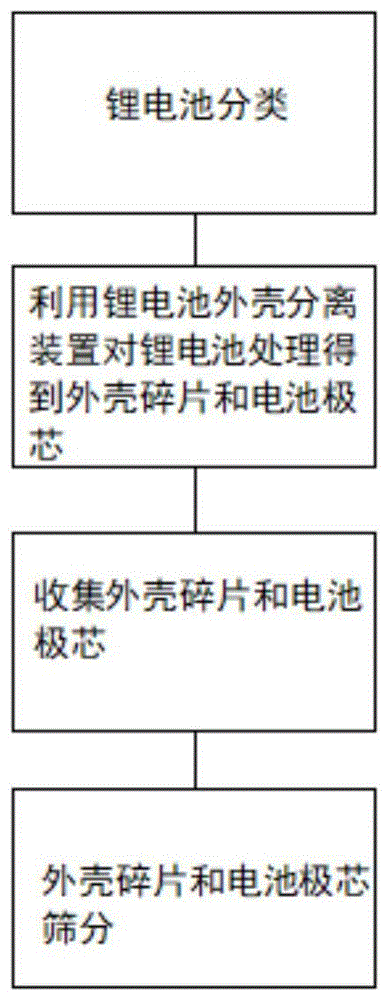
本发明涉及锂电池技术领域,更具体地说,本发明涉及一种锂电池高效分离回收工艺。
背景技术:
随着电子技术和新能源技术的发展,数码电子产品和新能源汽车的应用也越来越普遍,锂电池是数码电子产品和新能源汽车重要的供能部件,需求量非常大,而使用后废弃的锂电池也越来越多。这些废弃的锂电池对环保的压力越来越大,怎样快速合理地对废弃锂电池回收利用成为一个亟需解决的问题。
锂电池一般包括外壳和电池极芯,其中电池极芯是正极材料、负极材料和隔膜组合卷绕形成。传统的锂电池回收工艺是将锂电池放电后直接连同外壳材料一起破碎成颗粒然后在分筛出各种材料,这种方法简单粗暴,外壳材料与电极材料混合后,分离较为困难,降低了分离回收的效率。
因此,亟需设计一种锂电池高效分离回收工艺。
技术实现要素:
本发明的一个目的是解决至少上述缺陷,并提供至少后面将说明的优点。
本发明的另一个目的是提供一种能够快速将外壳材料与电池极芯分离的锂电池高效分离回收工艺。
为了实现本发明的这些目的和其它优点,本发明提供一种锂电池高效分离回收工艺,其中,包括:
步骤一、对收集的废弃锂电池进行形状分类,分类出圆柱形锂电池,同时对圆柱形锂电池按直径大小分类;
步骤二、根据圆柱形直径设计对应的锂电池外壳分离装置去除锂电池的外壳,所述锂电池外壳分离装置包括:
锥形的料仓,其用于接收圆柱形的废弃锂电池,所述料仓具有圆筒状下端;
下料机构,其包括适配部、下料部、导料部和驱动部;所述适配部为锥形筒结构,且大小刚好适配至料仓圆筒状下端的内壁,并与料仓圆筒状下端的内壁滑动贴合;所述下料部连接在适配部下端,下料部为筒状结构,内部具有竖直向下的多个圆孔,圆孔与锂电池外形相适配以允许锂电池向下通过,所述下料部下端设置有管状伸长部,每个圆孔对应设置一个管状伸长部,且圆孔的孔径和管状伸长部的孔径相同;所述导料部为锥形凸起结构,所述导料部设置在圆孔的周边用以将锂电池向下引导至圆孔;所述驱动部驱动下料机构相对料仓竖直上下往复运动;
竖切机构,其内设置多个竖直下的直管,所述直管上下开口,每个直管分别对应一个管状伸长部,所述管状伸长部活动套入所述直管内部以将锂电池导入到直管内;所述直管的内壁设置有多个竖直的切刀以分别至少从四个方向对锂电池的外壁竖直切割,多个切刀中至少有两个切刀的刀刃切割方向与锂电池的下落方向相同,至少有一个切刀的刀刃切割方向与锂电池的下落方向相反,所述切刀的刀刃凸出直管内壁的深度与锂电池外壳的厚度相等;
斜切机构,其设置在所述直管的下开口处,所述斜切机构至少设置一个倾斜刀片以对锂电池侧部斜切,且所述倾斜刀片的切割深度与锂电池外壳厚度相等以刚好将锂电池外壳切碎形成外壳碎片;
步骤三、使用收集器收集从锂电池外壳分离装置掉落的外壳碎片和电池极芯;
步骤四、使用振筛装置将外壳碎片和电池极芯过滤即完成外壳材料和电池极芯的分离回收。
上述技术方案中,首先对收集的废弃锂电池进行形状分类,分类出圆柱形锂电池,对圆柱形锂电池进行专项分离,提高分离回收效率。
其次,废弃的锂电池被投入到锂电池外壳分离装置的料仓内,在驱动部驱动下料结构上下移动的过程中,成堆的锂电池一个个排列地进入到下料部的圆孔内,并通过管道伸长部进入到竖切机构的直管中,切刀从多个方位对通过的锂电池进行竖向切割,使得锂电池的外壳形成条状,然后再经过直管下开口处的倾斜刀片斜切,使得锂电池的外壳形成片状,进而从锂电池上掉落,完成锂电池外壳和电池极芯的分离,降低后期回收的难度,提高分离回收的效率。
再次,锂电池外壳分离装置的适配部为锥形筒结构,且大小刚好适配至料仓的内壁,并与料仓内壁滑动贴合能够防止锂电池卡入到适配部与料仓内壁之间的间隙内,同时使得下料机构的上下往复运动更加稳定。
再次,锂电池外壳分离装置的驱动部可以驱动下料机构上下移动,防止锂电池在料仓内堆积无法松动下落至下料部,同时导料部为锥形的凸起机构,能够在下料机构上下移动的过程中将锂电池导入到圆孔中。
再次,锂电池外壳分离装置的竖切机构和斜切结构分别将锂电池的外壳切条和切段,使得外壳形成碎片从锂电池上脱离,完成外壳的分离回收。
还有,锂电池外壳分离装置中多个切刀中至少有两个切刀的刀刃切割方向与锂电池的下落方向相同以提高给锂电池下落的推力,防止锂电池堵塞,至少有一个切刀的刀刃切割方向与锂电池的下落方向相反以给锂电池下落的阻力,保持切刀对外壳充分切割,其中下落的推力始终大于下落的阻力,保证外壳充分切割的同时,保证锂电池高效通过。
优选的是,所述的锂电池高效分离回收工艺中,所述驱动部包括:
支撑架,其位于所述料仓的上部;
电动伸缩杆,其一端固定在支撑架上,另一端竖直向下伸延至下料部;
振动部,其连接在电动伸缩杆和下料部之间。
增加振动部使得下料机构在上下移动过程中振动,促使锂电池进入圆孔中,减少堵塞的情况。
优选的是,所述的锂电池高效分离回收工艺中,所述振动部包括振动弹簧和振动电机,所述振动弹簧将电动伸缩杆和下料部弹性连接,所述振动电机设置在振动弹簧内部并驱动振动弹簧振动。
优选的是,所述的锂电池高效分离回收工艺中,还包括控制模块,所述控制模块分别与电动伸缩杆和振动电机连接,并控制电动伸缩杆按固定周期伸缩,控制振动电机按固定周期振动
优选的是,所述的锂电池高效分离回收工艺中,所述圆孔按照矩形阵列方式设置,每四个圆孔之间设置一个导料部,且每个导料部的底部边缘与圆孔的边缘接合使得锂电池顺畅进入到圆孔内。
优选的是,所述的锂电池高效分离回收工艺中,所述切刀为圆形切刀,部分切刀设置在相邻两个直管之间,且圆形切刀两侧的刀刃分别伸入到相邻两个直管中形成对锂电池的切割。
优选的是,所述的锂电池高效分离回收工艺中,多个切刀在直管的纵向上错开设置,且相邻切刀之间的距离相等,相邻切刀之间的距离不大于锂电池的长度,以保证至少两个切刀同时对锂电池形成切割和夹持,减少锂电池切割时松动。
本发明至少包括以下有益效果:
本发明首先对收集的废弃锂电池进行形状分类,分类出圆柱形锂电池,对圆柱形锂电池进行专项分离,提高分离回收效率。
其次,废弃的锂电池被投入到锂电池外壳分离装置的料仓内,在驱动部驱动下料结构上下移动的过程中,成堆的锂电池一个个排列地进入到下料部的圆孔内,并通过管道伸长部进入到竖切机构的直管中,切刀从多个方位对通过的锂电池进行竖向切割,使得锂电池的外壳形成条状,然后再经过直管下开口处的倾斜刀片斜切,使得锂电池的外壳形成片状,进而从锂电池上掉落,完成锂电池外壳和电池极芯的分离,降低后期回收的难度,提高分离回收的效率。
再次,锂电池外壳分离装置的适配部为锥形筒结构,且大小刚好适配至料仓的内壁,并与料仓内壁滑动贴合能够防止锂电池卡入到适配部与料仓内壁之间的间隙内,同时使得下料机构的上下往复运动更加稳定。
再次,锂电池外壳分离装置的驱动部可以驱动下料机构上下移动,防止锂电池在料仓内堆积无法松动下落至下料部,同时导料部为锥形的凸起机构,能够在下料机构上下移动的过程中将锂电池导入到圆孔中。
再次,锂电池外壳分离装置的竖切机构和斜切结构分别将锂电池的外壳切条和切段,使得外壳形成碎片从锂电池上脱离,完成外壳的分离回收。
还有,锂电池外壳分离装置中多个切刀中至少有两个切刀的刀刃切割方向与锂电池的下落方向相同以提高给锂电池下落的推力,防止锂电池堵塞,至少有一个切刀的刀刃切割方向与锂电池的下落方向相反以给锂电池下落的阻力,保持切刀对外壳充分切割,其中下落的推力始终大于下落的阻力,保证外壳充分切割的同时,保证锂电池高效通过。
本发明的其它优点、目标和特征将部分通过下面的说明体现,部分还将通过对本发明的研究和实践而为本领域的技术人员所理解。
附图说明
图1为本发明所述锂电池高效分离回收工艺的流程框架图;
图2为本发明所述所述锂电池外壳分离装置的结构示意图;
图3为本发明所述下料部的俯视结构示意图;
图4为本发明所述竖切机构的俯视结构示意图;
图5为本发明所述驱动部的结构示意图。
具体实施方式
下面结合实施例对本发明做进一步的详细说明,以令本领域技术人员参照说明书文字能够据以实施。
实施例1
如图1~4所示,一种所述锂电池外壳分离装置,其中,包括:
锥形的料仓1,其用于接收圆柱形的废弃锂电池,所述料仓1具有圆筒状下端2;
下料机构,其包括适配部3、下料部4、导料部5和驱动部;所述适配部3为锥形筒结构,且大小刚好适配至料仓圆筒状下端2的内壁,并与料仓圆筒状下端2的内壁滑动贴合;所述下料部4连接在适配部3下端,下料部4为筒状结构,内部具有竖直向下的多个圆孔401,圆孔401与锂电池外形相适配以允许锂电池向下通过,所述下料部4下端设置有管状伸长部13,每个圆孔401对应设置一个管状伸长部13,且圆孔401的孔径和管状伸长部13的孔径相同;所述导料部5为锥形凸起结构,所述导料部5设置在圆孔401的周边用以将锂电池向下引导至圆孔401;所述驱动部包括支撑架7和电动伸缩杆6,用以驱动下料机构相对料仓1竖直上下往复运动用以促使料仓中的锂电池进入到圆孔401内。
竖切机构,其内设置多个竖直下的直管8,所述直管8上下开口,每个直管8分别对应一个管状伸长部13,所述管状伸长部13活动套入所述直管8内部以将锂电池导入到直管8内;所述直管8的内壁设置有多个竖直的切刀9以分别至少从四个方向对锂电池的外壁竖直切割,所述切刀9的刀刃凸出直管8内壁的深度与锂电池外壳的厚度相等以使得切刀划开锂电池的外壳,并减少对电池极芯的伤害,保证电池极芯的完整性。
斜切机构,其设置在所述直管的下开口处,所述斜切机构至少设置一个倾斜刀片10以对锂电池侧部斜切,且所述倾斜刀片的切割深度与锂电池外壳厚度相等以刚好将锂电池外壳切碎。
上述技术方案中,废弃的锂电池首先被投入到料仓内,在驱动部驱动下料结构上下移动的过程中,成堆的锂电池一个个排列地进入到下料部的圆孔内,并通过管道伸长部进入到竖切机构的直管中,切刀从多个方位对通过的锂电池进行竖向切割,使得锂电池的外壳形成条状,然后再经过直管下开口处的倾斜刀片斜切,使得锂电池的外壳形成片状,进而从锂电池上掉落,完成锂电池外壳和电池极芯的分离。
其中,适配部为锥形筒结构,且大小刚好适配至料仓的内壁,并与料仓内壁滑动贴合能够防止锂电池卡入到适配部与料仓内壁之间的间隙内,同时使得下料机构的上下往复运动更加稳定。
驱动部可以驱动下料机构上下移动,防止锂电池在料仓内堆积无法松动下落至下料部,同时导料部为锥形的凸起机构,能够在下料机构上下移动的过程中将锂电池导入到圆孔中。
竖切机构和斜切结构分别将锂电池的外壳切条和切段,使得外壳形成碎片从锂电池上脱离,完成外壳的分离回收。
进一步,如图1和4所示,所述驱动部包括:
支撑架7,其位于所述料仓1的上部;
电动伸缩杆6,其一端固定在支撑架7上,另一端竖直向下伸延至下料部;
振动部,其连接在电动伸缩杆6和下料部之间。
增加振动部使得下料机构在上下移动过程中振动,促使锂电池进入圆孔中,减少堵塞的情况。
所述振动部包括振动弹簧11和振动电机12,所述振动弹簧11将电动伸缩杆6和下料部弹性连接,所述振动电机12设置在振动弹簧11内部并驱动振动弹簧11振动,从而使得下料部也产生振动。
还包括控制模块,所述控制模块分别与电动伸缩杆6和振动电机12连接,并控制电动伸缩杆按固定周期伸缩,控制振动电机按固定周期振动。
进一步,如图2所示,所述圆孔401按照矩形阵列方式设置,每四个圆孔401之间设置一个导料部5,且每个导料部5的底部边缘与圆孔401的边缘接合使得锂电池顺畅进入到圆孔401内而不被卡住。
进一步,如图3所示,所述切刀9为圆形切刀,部分切刀9设置在相邻两个直管8之间,且圆形切刀两侧的刀刃分别伸入到相邻两个直管8中形成对锂电池的切割。
进一步,多个切刀9中至少有两个切刀的刀刃切割方向与锂电池的下落方向相同以提高给锂电池下落的推力,防止锂电池堵塞,至少有一个切刀的刀刃切割方向与锂电池的下落方向相反以给锂电池下落的阻力,保持切刀对外壳充分切割,其中下落的推力始终大于下落的阻力,保证外壳充分切割的同时,保证锂电池高效通过。
进一步,如图1所示,多个切刀9在直管8的纵向上错开设置,且相邻切刀9之间的距离相等,相邻切刀9之间的距离不大于锂电池的长度。
实施例2
一种锂电池高效分离回收工艺,包括:
步骤一、对收集的废弃锂电池进行形状分类,分类出圆柱形锂电池,同时对圆柱形锂电池按直径大小分类。
步骤二、根据圆柱形直径设计对应的锂电池外壳分离装置去除锂电池的外壳,如图1~4所示,所述锂电池外壳分离装置包括:
锥形的料仓1,其用于接收圆柱形的废弃锂电池,所述料仓1具有圆筒状下端2;
下料机构,其包括适配部3、下料部4、导料部5和驱动部;所述适配部3为锥形筒结构,且大小刚好适配至料仓圆筒状下端2的内壁,并与料仓圆筒状下端2的内壁滑动贴合;所述下料部4连接在适配部3下端,下料部4为筒状结构,内部具有竖直向下的多个圆孔401,圆孔401与锂电池外形相适配以允许锂电池向下通过,所述下料部4下端设置有管状伸长部13,每个圆孔401对应设置一个管状伸长部13,且圆孔401的孔径和管状伸长部13的孔径相同;所述导料部5为锥形凸起结构,所述导料部5设置在圆孔401的周边用以将锂电池向下引导至圆孔401;所述驱动部包括支撑架7和电动伸缩杆6,用以驱动下料机构相对料仓1竖直上下往复运动用以促使料仓中的锂电池进入到圆孔401内。
竖切机构,其内设置多个竖直下的直管8,所述直管8上下开口,每个直管8分别对应一个管状伸长部13,所述管状伸长部13活动套入所述直管8内部以将锂电池导入到直管8内;所述直管8的内壁设置有多个竖直的切刀9以分别至少从四个方向对锂电池的外壁竖直切割,所述切刀9的刀刃凸出直管8内壁的深度与锂电池外壳的厚度相等以使得切刀划开锂电池的外壳,并减少对电池极芯的伤害,保证电池极芯的完整性。
斜切机构,其设置在所述直管的下开口处,所述斜切机构至少设置一个倾斜刀片10以对锂电池侧部斜切,且所述倾斜刀片的切割深度与锂电池外壳厚度相等以刚好将锂电池外壳切碎。
如图1和4所示,所述驱动部包括:
支撑架7,其位于所述料仓1的上部;
电动伸缩杆6,其一端固定在支撑架7上,另一端竖直向下伸延至下料部;
振动部,其连接在电动伸缩杆6和下料部之间。
增加振动部使得下料机构在上下移动过程中振动,促使锂电池进入圆孔中,减少堵塞的情况。
所述振动部包括振动弹簧11和振动电机12,所述振动弹簧11将电动伸缩杆6和下料部弹性连接,所述振动电机12设置在振动弹簧11内部并驱动振动弹簧11振动,从而使得下料部也产生振动。
还包括控制模块,所述控制模块分别与电动伸缩杆6和振动电机12连接,并控制电动伸缩杆按固定周期伸缩,控制振动电机按固定周期振动
如图2所示,所述圆孔401按照矩形阵列方式设置,每四个圆孔401之间设置一个导料部5,且每个导料部5的底部边缘与圆孔401的边缘接合使得锂电池顺畅进入到圆孔401内而不被卡住。
进一步,如图3所示,所述切刀9为圆形切刀,部分切刀9设置在相邻两个直管8之间,且圆形切刀两侧的刀刃分别伸入到相邻两个直管8中形成对锂电池的切割。
进一步,多个切刀9中至少有两个切刀的刀刃切割方向与锂电池的下落方向相同以提高给锂电池下落的推力,防止锂电池堵塞,至少有一个切刀的刀刃切割方向与锂电池的下落方向相反以给锂电池下落的阻力,保持切刀对外壳充分切割,其中下落的推力始终大于下落的阻力,保证外壳充分切割的同时,保证锂电池高效通过。
进一步,如图1所示,多个切刀9在直管8的纵向上错开设置,且相邻切刀9之间的距离相等,相邻切刀9之间的距离不大于锂电池的长度。
使用时,废弃的锂电池首先被投入到料仓内,在驱动部驱动下料结构上下移动的过程中,成堆的锂电池一个个排列地进入到下料部的圆孔内,并通过管道伸长部进入到竖切机构的直管中,切刀从多个方位对通过的锂电池进行竖向切割,使得锂电池的外壳形成条状,然后再经过直管下开口处的倾斜刀片斜切,使得锂电池的外壳形成片状的外壳碎片,进而从锂电池上掉落,完成锂电池外壳和电池极芯的分离,但是部分外壳碎片还会黏附在电池极芯上。
步骤三、使用收集器收集从锂电池外壳分离装置掉落的外壳碎片和电池极芯;
步骤四、使用振筛装置将外壳碎片和电池极芯过滤,外壳碎片通过振筛装置的网孔掉落,而电池极芯留在网上,达到分离的目的,且振筛装置振动使得黏附在电池极芯上少量的外壳碎片掉落,得到干净的电池极芯。
尽管本发明的实施方案已公开如上,但其并不仅仅限于说明书和实施方式中所列运用。它完全可以被适用于各种适合本发明的领域。对于熟悉本领域的人员而言,可容易地实现另外的修改。