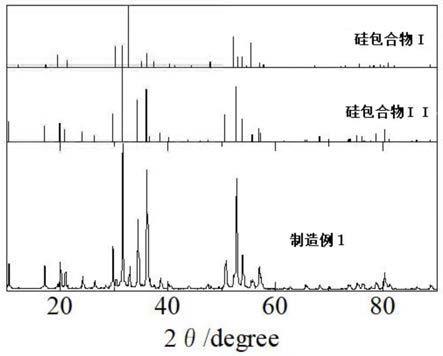
含有硅包合物ii的负极活性物质
技术领域
[0001]
本发明涉及含有硅包合物ii的负极活性物质。
背景技术:[0002]
已知在由si形成的多面体的空间中包接其它金属的被称为硅包合物的化合物。在硅包合物之中,主要报告了关于硅包合物i(silicon clathrate-i:i型硅包合物)和硅包合物ii(silicon clathrate-ii:ii型硅包合物)的研究。
[0003]
所谓硅包合物i,是以20个si原子包接1个na原子的12面体与以24个si原子包接1个na原子的14面体将面共享而成的硅包合物,用na8si
46
这一组成式表示。na存在于构成硅包合物i的所有多面体的笼(cage)中。
[0004]
所谓硅包合物ii,是si的12面体与si的16面体将面共享而成的硅包合物,用na
x
si
136
这一组成式表示。其中,x满足0≤x≤24。即,在构成硅包合物ii的多面体的笼中,既可以存在na,也可以不存在na。
[0005]
在非专利文献1中记载了从含有na及si的na-si合金制造硅包合物i及硅包合物ii的方法。若具体描述,则记载了在不到10-4
torr(即不到1.3
×
10-2
pa)的减压条件下,将na-si合金加热到400℃以上,来将na作为蒸气除去,从而制造出硅包合物i和硅包合物ii。并且,还记载了:由于加热温度的不同,硅包合物i和硅包合物ii的生成比例会发生变化;以及若加热温度变高,则na会从硅包合物i脱离,硅包合物i的结构发生变化,从而会生成一般的金刚石结构的si晶体。
[0006]
而且,关于硅包合物ii,记载有制造了na
22.56
si
136
、na
17.12
si
136
、na
18.72
si
136
、na
7.20
si
136
、na
11.04
si
136
、na
1.52
si
136
、na
23.36
si
136
、na
24.00
si
136
、na
20.48
si
136
、na
16.00
si
136
、na
14.80
si136。
[0007]
在专利文献1中也记载了硅包合物的制造方法。具体地说,记载了将使用硅晶圆和na制造的na-si合金在10-2
pa以下的减压条件下以400℃加热3小时来将na除去,从而制造出硅包合物i和硅包合物ii。
[0008]
另外,还报告了将硅包合物ii所包接的na以li、k、rb、cs或ba来置换的硅包合物ii、将硅包合物ii的si的一部分以ga或ge来置换的硅包合物ii。
[0009]
现有技术文献
[0010]
非专利文献
[0011]
非专利文献1:h.horie,t.kikudome,k.teramura,and s.yamanaka,journal of solid state chemistry,182,2009,pp.129-135
[0012]
专利文献
[0013]
专利文献1:特开2012-224488号公报
技术实现要素:[0014]
发明要解决的问题
[0015]
硅包合物ii即使是内包的na脱离,也会维持其结构。本发明的发明人着眼于这一点而想到了将内包的na脱离后的硅包合物ii用作锂离子二次电池的负极活性物质。
[0016]
本发明是鉴于这样的情况而完成的,目的在于提供一种适合于锂离子二次电池的负极的、含有硅包合物ii的负极活性物质。
[0017]
用于解决问题的方案
[0018]
本发明的负极活性物质的特征在于,包含硅材料,在上述硅材料中,含有由组成式na
x
si
136
(0≤x≤10)表示的硅包合物ii,并且直径为100nm以下的孔的体积为0.025cm3/g以上。
[0019]
发明效果
[0020]
本发明的负极活性物质抑制了充电时膨胀的程度。因此,具备本发明的负极活性物质的负极在充放电时的劣化被抑制。
附图说明
[0021]
图1是制造例1的硅材料的x射线衍射图、以及硅包合物i及硅包合物ii的x射线衍射图。
[0022]
图2是评价例1中的na吸收剂与na的反应物的x射线衍射图、以及金刚石结构的si晶体及na2sio3晶体的x射线衍射图。
[0023]
图3是制造例2、制造例3以及制造例5的硅材料的x射线衍射图。
具体实施方式
[0024]
以下说明用于实施本发明的最佳的方式。此外,只要没有特别指明,本说明书中记载的数值范围“x~y”将下限x和上限y包含在其范围中。并且,通过将包含这些上限值和下限值以及实施例中罗列的数值在内的这些数值任意组合,能构成数值范围。而且,能够将从数值范围内任意选择的数值设为上限、下限的数值。
[0025]
本发明的负极活性物质的特征在于,包含如下硅材料(以下有时称为本发明的硅材料。):含有由组成式na
x
si
136
(0≤x≤10)表示的硅包合物ii,并且直径为100nm以下的孔的体积为0.025cm3/g以上。
[0026]
在本发明的硅材料中,优选硅包合物ii中的na含量低。其原因是,锂会变得能够在na脱离后的硅包合物ii的多面体的笼内移动,其结果是,负极活性物质的膨胀的程度被抑制。
[0027]
作为na
x
si
136
中的x的范围,优选0≤x≤7,更优选0≤x≤5,进一步优选0≤x≤3,特别优选0≤x≤2,最优选0≤x≤1。
[0028]
在本发明的硅材料中,在不脱离本发明的主旨的范围内,也可以存在na及si以外的其它元素。作为其它元素,在硅包合物ii中可例示能与na置换的li、k、rb、cs及ba、以及能与si置换的ga及ge。
[0029]
在本发明的硅材料中,直径为100nm以下的孔的体积为0.025cm3/g以上。此外,与本发明的硅材料相关的孔的直径的大小及孔的体积是指使用遵循jis z 8831的气体吸附法对本发明的硅材料进行分析时算出的孔的直径的大小及孔的体积。
[0030]
在制造锂离子二次电池的负极时或者组装锂离子二次电池时,具备负极活性物质
的负极会被加压。在此,直径大的孔的强度差,因此可预见即使在负极活性物质中存在直径大的孔,由于被加压,直径的大的孔也会发生变形。
[0031]
在本发明的硅材料中,作为规定了直径为100nm以下的孔的原因之一,能够举出如下方面:若是直径为100nm以下的细孔,则不会较大地破坏强度,所以可预计即使在锂离子二次电池制造时等的加压条件下,变形也会被抑制。另外,作为上述原因中的另一个原因,还有如下方面:针对具有直径为100nm以下的细孔的硅材料,使用该细孔的体积不同的多个硅材料进行了试验,结果在该细孔的体积与负极的膨胀量(膨胀力)之间找到了相关性。
[0032]
作为本发明的硅材料中的、直径为100nm以下的孔的体积,能够例示0.025cm3/g~0.1cm3/g的范围内、0.03cm3/g~0.08cm3/g的范围内、0.035cm3/g~0.07cm3/g的范围内、0.04cm3/g~0.06cm3/g的范围内。
[0033]
那么,为了制造直径为100nm以下的孔的体积为0.025cm3/g以上的本发明的硅材料,优选尽量以低温进行使na从na-si合金脱离的na脱离反应。
[0034]
本发明的发明人关于使na作为蒸气从na-si合金脱离的硅包合物ii的高效的制造方法进行了研究,结果想到了在反应系统内捕获na的蒸气。由于在反应系统内捕获na的蒸气,所以除了可预见反应系统内的na的分压会降低而所希望的反应速度会增加以外,还可预见不需要强的减压条件。而且,可想见能够显著地削减排出到系统外的na的量,因此能够削减用于捕获na的特别装置所需的费用。
[0035]
并且,本发明的发明人在能与na发生反应的材料(本说明书中称为“na吸收剂”。)与na-si合金共存的环境下进行了试验,结果发现即使在弱的减压条件下也进行了所希望的反应、也能够削减排出到系统外的na的量、并且也能够优先制造硅包合物ii。
[0036]
在使用该na吸收剂的硅包合物ii的制造方法(以下有时简称为“本发明的制造方法”。)中,能够以比较低的温度进行所希望的反应,因此对于本发明的硅材料的制造是有利的。
[0037]
本发明的制造方法的一方案的特征在于,在含有na及si的na-si合金与na吸收剂以非接触的方式共存的反应系统内,通过加热上述na-si合金,使从上述na-si合金气化的na与上述na吸收剂反应来减少上述na-si合金中的na量。
[0038]
本发明的制造方法的技术意义在于,通过用存在于系统内的na吸收剂捕捉以下的反应式中的气体状的na(g),使以下的反应式向右侧有利地进行。另外,在本发明的制造方法中,由于在比较低的na分压条件下进行反应,因此还有硅包合物i的生成被抑制、硅包合物ii被优先制造的优点。
[0039]
na-si合金
←→
硅包合物ii+na(g)
[0040]
在na-si合金中,na及si的组成用na
y
si
136
(24<y)表示。作为na-si合金,优选使用与si相比na过度地存在的合金、即na及si的组成由na
z
si(1<z)表示的合金。
[0041]
为了制造na-si合金,只要在惰性气体气氛下将na及si熔融使其合金化即可。
[0042]
在na-si合金中,在不脱离本发明的主旨的范围内,也可以存在na及si以外的其它元素。作为其它元素,在硅包合物ii中可例示能与na置换的li、k、rb、cs及ba、以及能与si置换的ga及ge。
[0043]
na吸收剂是指能与0价的na发生反应的材料。鉴于本发明的制造方法的技术意义,na吸收剂是指能与0价的na发生反应的材料中的、与金属na的蒸气压力相比蒸气压力较低
的材料。
[0044]
通过使用易于与na发生反应的优异的na吸收剂,能够降低本发明的制造方法中的加热温度,另外,还能够使减压条件平稳。
[0045]
作为na吸收剂,能够例示碱金属及碱土类金属以外的金属氧化物、碱金属及碱土类金属以外的金属硫化物、碱金属及碱土类金属以外的金属卤化物。
[0046]
作为具体的na吸收剂,能够例示wo2、wo3、moo3、zno、feo、fe2o3、vo、v2o3、tio2、sio、sio2、al2o3、ws2、mos2、zns、fes、tis2、sis2、al2s3,其中,优选从wo3、moo3、zno、feo、v2o3、tio2、sio以及al2o3中选择的na吸收剂,更优选从wo3、moo3、feo以及tio2中选择的na吸收剂。
[0047]
优选的na吸收剂即使在na的分压低的条件下,也能与na进行反应。在将系统内的na与na吸收剂的摩尔比设为大体1:1、将系统内的温度设为350℃的条件下,将以下的反应式达到平衡状态的时点的na分压在表1中示出。
[0048]
na(g)+na吸收剂
←→
生成物
[0049]
[表1]
[0050]
na吸收剂na分压wo310-22.4
atmmoo310-26.3
atmzno10-6.5
atmfeo10-14.7
atmv2o310-10
·3atmtio210-1
5.9
atmsio10-10.5
atmal2o310-5.5
atm
[0051]
na吸收剂的使用量只要根据na-si合金所包含的na的量适当地决定即可。作为na吸收剂,既可以使用一种na吸收剂,也可以同时采用多种na吸收剂。
[0052]
在本发明的制造方法中,通过使用na吸收剂,与现有的硅包合物ii的制造方法相比,即使在弱的减压条件下也能够进行所希望的反应,另外,即使在低的加热温度下也能够进行所希望的反应。
[0053]
作为减压条件下的气压p,能够例示p<105pa、p≤104pa、p≤103pa、p≤102pa、p≤10pa。作为与现有的硅包合物ii的制造方法相比的情况下的有利的气压p,能够例示10-2
pa<p<105pa、10-1
pa≤p≤104pa、10pa<p≤102pa。
[0054]
加热温度t还由减压条件所左右,能够例示100℃≤t≤450℃、150℃≤t≤400℃、200℃≤t≤350℃、250℃≤t≤300℃。在加热温度t低的情况下,需要降低气压p。
[0055]
优选加热温度t是400℃以下。其原因是,若加热温度t是400℃以下,则不仅能够抑制金刚石结构的si晶体的生成,还能够得到优选的物理性质的硅材料。
[0056]
在本发明的制造方法中,可以将使na与na吸收剂反应来减少na-si合金中的na量这一工序作为单个工序进行实施以制造硅包合物ii,另外,也可以使在上述的工序中得到的硅包合物ii与新的na吸收剂以非接触的方式共存并加热硅包合物ii,从而制造减少了na量的硅包合物ii。
[0057]
根据以上事项,作为本发明的制造方法的另一方案,能够掌握以下的制造方法。
[0058]
本发明的制造方法的另一方案是由组成式na
x2
si
136
表示的硅包合物ii的制造方法,其特征在于,在由组成式na
x1
si
136
表示的硅包合物ii与na吸收剂以非接触的方式共存的反应系统内,通过加热上述硅包合物ii,使从上述硅包合物ii气化的na与上述na吸收剂反应来减少上述硅包合物ii中的na量。
[0059]
其中,x1及x2满足0<x1≤24、0≤x2≤10以及x2<x1。
[0060]
在含有经过本发明的制造方法制造的硅包合物ii的硅材料中,可能会附着na或naoh等,因此为了将其除去,优选实施用水清洗硅材料的清洗工序。
[0061]
通过用水清洗硅材料,还能够期待硅材料的表面被局部氧化,氧被导入硅材料中。被导入了氧的硅材料可期待其稳定性的提高、作为负极活性物质的性能的提高。
[0062]
作为在清洗工序中使用的水,从na或naoh等易于溶解的观点来看,优选使用酸性的水溶液。作为酸性的水溶液中的酸的浓度,优选0.1~10质量%,更优选0.5~5质量%,进一步优选1~4质量%。
[0063]
优选在清洗工序之后通过过滤及干燥将水从硅材料除去。
[0064]
硅材料可以经过粉碎或分级而成为一定的粒度分布的粉末。
[0065]
作为硅材料优选的平均粒径,优选1~30μm的范围内,更优选2~20μm的范围内,进一步优选3~15μm的范围内。此外,平均粒径是指用一般的激光衍射式粒度分布测定装置测定了试料的情况下的d
50
。
[0066]
锂离子二次电池具备正极、负极、电解液以及隔离物,或者具备正极、负极以及固体电解质。负极具备包含本发明的硅材料的本发明的负极活性物质。也可以采用以碳等导电性材料覆盖了表面的本发明的硅材料作为本发明的负极活性物质。
[0067]
作为本发明的负极活性物质以外的锂离子二次电池的构成要素,只要适当地采用公知的构成要素即可。
[0068]
具备本发明的负极活性物质的负极抑制了充电时膨胀的程度。因此,在具备本发明的负极活性物质的锂离子二次电池中,能够减小正极-隔离物-负极这一单元构成、或者正极-固体电解质-负极这一单元构成的厚度方向的约束压力。另外,在具备本发明的负极活性物质的锂离子二次电池中,可期待寿命的提高。
[0069]
一般地,使用固体电解质的固体型锂离子二次电池的约束压力高,因此具备本发明的负极活性物质的锂离子二次电池的约束压力减小的效果在固体型锂离子二次电池中会得到有效地发挥。
[0070]
以上,说明了本发明的实施方式,但本发明不限于上述实施方式。能够在不脱离本发明的主旨的范围内以实施了本领域技术人员能进行的变更、改良等的各种方式来实施。
[0071]
[实施例]
[0072]
以下,示出制造例、实施例及比较例等,更具体地说明本发明。此外,本发明不限于这些实施例。
[0073]
(制造例1)
[0074]
·
na-si合金的制造工序
[0075]
在惰性气体气氛下,将na及si熔融并进行冷却而制造了na-si合金。在该na-si合金中,na相对于si的组成比稍高。
[0076]
·
硅包合物ii的制造工序
[0077]
在不锈钢制的反应容器内部的底部配置了1质量份的sio粉末作为na吸收剂。在不锈钢制的反应容器内部的底部设置了台座,并在台座的上部配置了不锈钢制的坩埚。在该坩埚内配置了1质量份的na-si合金。
[0078]
对不锈钢制的反应容器加上不锈钢制的盖,将它们配置在真空炉内。此外,能够从不锈钢制的反应容器与不锈钢制的盖的间隙排出反应容器内部的气体。
[0079]
将真空炉内减压到10pa,以350℃加热12小时,从而合成了含有硅包合物ii的硅材料。
[0080]
将真空炉内冷却到室温,从坩埚回收了含有硅包合物ii的硅材料。另外,还回收了存在于反应容器内部的底部的、na吸收剂与na的反应物。此外,在真空炉内部或反应容器内部未观察到金属na的析出。
[0081]
将硅材料投入到3质量%的盐酸中并进行搅拌,从而对其进行了清洗。将清洗后的硅材料通过过滤来分离,并以80℃进行减压干燥,从而制造出含有硅包合物ii的制造例1的硅材料。
[0082]
(评价例1)
[0083]
针对含有硅包合物ii的制造例1的硅材料、以及na吸收剂与na的反应物,用粉末x射线衍射装置进行了x射线衍射测定。
[0084]
将制造例1的硅材料的x射线衍射图、以及硅包合物i及硅包合物ii的x射线衍射图在图1中示出。另外,将na吸收剂与na的反应物的x射线衍射图、以及金刚石结构的si晶体及na2sio3晶体的x射线衍射图在图2中示出。
[0085]
根据图1可知,制造例1的硅材料的主要成分是硅包合物ii。另外,根据图2可知,作为na吸收剂的sio与na反应而变为了na2sio3。
[0086]
(制造例2)
[0087]
除了将硅包合物ii的制造工序中的硅材料的合成工序如下所示设为2阶段工序以外,用与制造例1同样的方法制造了含有硅包合物ii的制造例2的硅材料。
[0088]
·
含有硅包合物ii的硅材料的合成(1阶段工序)
[0089]
在不锈钢制的反应容器内部的底部配置了1质量份的sio粉末作为na吸收剂。在不锈钢制的反应容器内部的底部设置了台座,并在台座的上部配置了不锈钢制的坩埚。在该坩埚内配置了1质量份的na-si合金。对不锈钢制的反应容器加上不锈钢制的盖,将它们配置在真空炉内。将真空炉内减压到10pa,以350℃加热12小时,从而合成了含有硅包合物ii的硅材料。
[0090]
将真空炉内冷却到室温,从坩埚回收了含有硅包合物ii的硅材料。
[0091]
·
含有硅包合物ii的硅材料的合成(2阶段工序)
[0092]
在别的不锈钢制的反应容器内部的底部配置了1质量份的sio粉末作为na吸收剂。在该不锈钢制的反应容器内部的底部设置了台座,并在台座的上部配置了不锈钢制的坩埚。在该坩埚内配置了回收后的1质量份的硅材料。对不锈钢制的反应容器加上不锈钢制的盖,将它们配置在真空炉内。将真空炉内减压到10pa,以350℃加热6小时,从而合成了含有硅包合物ii的硅材料。
[0093]
(制造例3)
[0094]
除了将硅包合物ii的制造工序中的硅材料的合成工序中的、2阶段工序的温度设
为400℃以外,通过与制造例2同样的方法制造了含有硅包合物ii的制造例3的硅材料。
[0095]
(制造例4)
[0096]
除了将硅包合物ii的制造工序中的硅材料的合成工序中的、2阶段工序的温度设为400℃、将加热时间设为12小时以外,通过与制造例2同样的方法制造了含有硅包合物ii的制造例4的硅材料。
[0097]
(制造例5)
[0098]
除了将硅包合物ii的制造工序中的硅材料的合成工序中的、2阶段工序的温度设为450℃以外,通过与制造例2同样的方法制造了含有硅包合物ii的制造例5的硅材料。
[0099]
(评价例2)
[0100]
针对含有硅包合物ii的制造例1~制造例5的硅材料,用粉末x射线衍射装置进行了x射线衍射测定。此外,制造例1的硅材料中的硅包合物ii实质上相当于通过制造例2~制造例5的硅材料的制造工序中的1阶段工序合成的硅包合物ii。
[0101]
将制造例2、制造例3及制造例5的硅材料的x射线衍射图在图3中示出。在图3中,用三角形表示的峰值出自硅包合物ii,用四边形表示的峰值出自硅包合物i,用
×
表示的峰值出自金刚石结构的si晶体。
[0102]
根据图3可知,制造例2、制造例3以及制造例5的硅材料均以硅包合物ii为主要成分。另外可知,在加热温度为450℃的制造例5的硅材料中存在金刚石结构的si晶体。
[0103]
根据以上的结果可认为,在加热温度为450℃的制造例5的硅材料的合成条件中,由于na分压比较高,因此作为中间体的硅包合物i的生成比例变得比较高。并且可认为,随着na从作为中间体的硅包合物i中被除去,硅包合物i变为了si晶体。
[0104]
另一方面可认为,在加热温度为400℃以下的制造例2及制造例3的硅材料的合成条件中,由于na分压比较低,因此作为中间体的硅包合物i的生成比例变得比较低,而优先制造了硅包合物ii。
[0105]
另外,在制造例1~制造例5的硅材料的各x射线衍射图中,根据硅包合物ii的出自(311)的峰值强度和出自(511)的峰值强度,分别算出了硅包合物ii的组成式na
x
si
136
中的x的值。此外,硅包合物ii的组成式na
x
si
136
中的x的值与出自(511)的峰值强度相对于出自(311)的峰值强度之比的值存在相关关系。
[0106]
将结果在表2中示出。
[0107]
[表2]
[0108] 合成条件x的值制造例11阶段工序22.4制造例22阶段工序:条件为350℃6小时6.8制造例32阶段工序:条件为400℃6小时1.7制造例42阶段工序:条件为400℃12小时1.5制造例52阶段工序:条件为450℃6小时0.6
[0109]
根据表2可知,加热温度越高,另外加热时间越长,则所制造的硅包合物ii的组成式na
x
si
136
中的x的值变得越低。
[0110]
(制造例6)
[0111]
除了如下所示进行了硅包合物ii的制造工序中的硅材料的合成工序以外,用与制
造例1同样的方法制造了含有硅包合物ii的制造例6的硅材料。
[0112]
在不锈钢制的反应容器内部的底部配置了moo3粉末作为na吸收剂。在不锈钢制的反应容器内部的底部设置了台座,并在台座的上部配置了不锈钢制的坩埚。在该坩埚内配置了na-si合金。na-si合金中的na的摩尔与na吸收剂的摩尔之比是4∶6。
[0113]
对不锈钢制的反应容器加上不锈钢制的盖,将它们配置在真空炉内。
[0114]
将真空炉内减压到10pa,以280℃加热40小时,从而合成了含有硅包合物ii的硅材料。
[0115]
(制造例7)
[0116]
除了将加热温度设为330℃、将加热时间设为20小时以外,用与制造例6同样的方法制造了含有硅包合物ii的制造例7的硅材料。
[0117]
(制造例8)
[0118]
除了使用feo粉末作为na吸收剂以外,用与制造例6同样的方法制造了含有硅包合物ii的制造例8的硅材料。
[0119]
(制造例9)
[0120]
除了将加热温度设为330℃、将加热时间设为20小时以外,用与制造例8同样的方法制造了含有硅包合物ii的制造例9的硅材料。
[0121]
(制造例10)
[0122]
除了将加热温度设为380℃、将加热时间设为20小时以外,用与制造例8同样的方法制造了含有硅包合物ii的制造例10的硅材料。
[0123]
(制造例11)
[0124]
除了将加热温度设为430℃、将加热时间设为6小时以外,用与制造例8同样的方法制造了含有硅包合物ii的制造例11的硅材料。
[0125]
(制造例12)
[0126]
除了使用sio粉末作为na吸收剂以外,用与制造例6同样的方法制造了含有硅包合物ii的制造例12的硅材料。
[0127]
(制造例13)
[0128]
除了将硅包合物ii的制造工序中的硅材料的合成工序如下所示设为2阶段工序以外,用与制造例12同样的方法制造了含有硅包合物ii的制造例13的硅材料。
[0129]
·
含有硅包合物ii的硅材料的合成(1阶段工序)
[0130]
在不锈钢制的反应容器内部的底部配置了sio粉末作为na吸收剂。在不锈钢制的反应容器内部的底部设置了台座,并在台座的上部配置了不锈钢制的坩埚。在该坩埚内配置了na-si合金。na-si合金中的na的摩尔与na吸收剂的摩尔之比是4∶6。
[0131]
对不锈钢制的反应容器加上不锈钢制的盖,将它们配置在真空炉内。将真空炉内减压到10pa,以280℃加热40小时,从而合成了含有硅包合物ii的硅材料。
[0132]
将真空炉内冷却到室温,从坩埚回收了含有硅包合物ii的硅材料。
[0133]
·
含有硅包合物ii的硅材料的合成(2阶段工序)
[0134]
在别的不锈钢制的反应容器内部的底部配置了sio粉末作为na吸收剂。在该不锈钢制的反应容器内部的底部设置了台座,并在台座的上部配置了不锈钢制的坩埚。在该坩埚内配置了回收后的硅材料。回收后的硅材料包含的na的摩尔与na吸收剂的摩尔之比是4∶
6。
[0135]
对不锈钢制的反应容器加上不锈钢制的盖,将它们配置在真空炉内。将真空炉内减压到10pa,以330℃加热20小时,从而合成了含有硅包合物ii的硅材料。
[0136]
(制造例14)
[0137]
除了将硅包合物ii的制造工序中的硅材料的合成工序中的、2阶段工序的温度设为380℃以外,用与制造例13同样的方法制造了含有硅包合物ii的制造例14的硅材料。
[0138]
(制造例15)
[0139]
除了将硅包合物ii的制造工序中的硅材料的合成工序中的、2阶段工序的温度设为480℃、将加热时间设为6小时以外,用与制造例13同样的方法制造了含有硅包合物ii的制造例15的硅材料。
[0140]
(比较制造例1)
[0141]
除了如下所示进行了硅包合物ii的制造工序中的硅材料的合成工序以外,用与制造例1同样的方法制造了比较制造例1的硅材料。
[0142]
在不锈钢制的反应容器内部的底部配置了na-si合金。将其配置在真空炉内。将真空炉内减压到10pa,以280℃加热40小时,从而合成了硅材料。将真空炉内冷却到室温,回收了硅材料。
[0143]
(比较制造例2)
[0144]
除了将硅材料的合成工序如下所示设为2阶段工序以外,用与比较制造例1同样的方法制造了比较制造例2的硅材料。
[0145]
·
硅材料的合成(1阶段工序)
[0146]
在不锈钢制的反应容器内部的底部配置了na-si合金。将其配置在真空炉内。将真空炉内减压到10pa,以280℃加热40小时,从而合成了硅材料。将真空炉内冷却到室温,回收了硅材料。
[0147]
·
硅材料的合成(2阶段工序)
[0148]
在别的不锈钢制的反应容器内部的底部配置了回收后的硅材料。将它们配置在真空炉内。将真空炉内减压到10pa,以380℃加热20小时,从而合成了含有硅包合物ii的硅材料。
[0149]
(比较制造例3)
[0150]
除了将硅材料的合成工序中的、2阶段工序的温度设为480℃、将加热时间设为6小时以外,用与比较制造例2同样的方法制造了比较制造例3的硅材料。
[0151]
(评价例3)
[0152]
针对含有硅包合物ii的制造例6~制造例15的硅材料和比较制造例1~比较制造例3的硅材料,用粉末x射线衍射装置进行了x射线衍射测定。
[0153]
其结果是,证实了在制造例6~制造例15的硅材料和比较制造例2~比较制造例3的硅材料中含有硅包合物ii。但是,从比较制造例1的硅材料并未检测到出自硅包合物ii的峰值。这证明了在比较制造例1的制造条件下无法制造出硅包合物ii。
[0154]
另外,在制造例6~制造例15的硅材料和比较制造例2~比较制造例3的硅材料的各x射线衍射图中,根据硅包合物ii的出自(311)的峰值强度和出自(511)的峰值强度,分别算出了硅包合物ii的组成式na
x
si
136
中的x的值。
[0155]
将以上的结果在表3中示出。
[0156]
[表3]
[0157][0158]
根据表3可以说,在使用了na吸收剂的合成条件下,会顺利地进行na从na-si合金的除去。另外可以说,由于na吸收剂的种类而会在反应速度上产生差。
[0159]
可以说通过使用na吸收剂,能够以更低的温度进行反应,并且能够以更短的时间进行反应。
[0160]
(评价例4)
[0161]
使用遵循jis z 8831的气体吸附法分析了制造例6、制造例10、制造例11以及比较制造例3的硅材料。将结果在表4中示出。表4中的空孔体积是指直径为100nm以下的孔的体积。
[0162]
[表4]
[0163]
[0164]
根据表4可以说,合成条件中的加热温度越低,则直径为100nm以下的孔的体积变得越大。为了制造本发明的硅材料,可以说加热温度低的制造方法是优选的。
[0165]
(实施例1)
[0166]
使用制造例10的硅材料如下所示制造了实施例1的固体型锂离子二次电池。
[0167]
将0.4g作为固体电解质原料的0.75li2s-0.25p2s5粒子、0.8g作为负极活性物质的平均粒径为1μm的制造例10的硅材料、0.06g作为导电材料的气相法碳纤维(vapor grown carbon fiber)、以及0.32g作为粘结剂的pvdf系树脂的5质量%丁酸丁酯溶液添加到聚丙烯制容器中。将该容器在超声波分散装置中进行30秒超声波处理后,使用振荡器进行30分钟振荡处理,从而制备了负极活性物质含有量相对多的负极复合材料用原料a。
[0168]
将0.7g作为固体电解质原料的0.75li2s-0.25p2s5粒子、0.6g作为负极活性物质原料的平均粒径为3μm的si单质粒子、0.06g作为导电材料的气相法碳纤维(vapor grown carbon fiber)以及0.24g作为粘结剂的pvdf系树脂的5质量%丁酸丁酯溶液添加到聚丙烯制容器中。将该容器在超声波分散装置中进行30秒超声波处理后,使用振荡器进行30分钟振荡处理,从而制备了负极活性物质含有量相对少的负极复合材料用原料b。
[0169]
将这样准备好的负极活性物质含有量多的负极复合材料用原料a通过使用敷料器(applicator)的刮涂法涂布到作为集电体的铜箔上,进行了60分钟自然干燥。
[0170]
接下来,通过使用敷料器的刮涂法将负极活性物质含有量少的负极复合材料用原料b涂布到自然干燥后的负极复合材料用原料a的表面,进行了60分钟自然干燥而得到了负极前体。
[0171]
将这样得到的负极前体在调整为100℃的热板上干燥30分钟而制造了负极。
[0172]
将0.3g作为固体电解质原料的0.75li2s-0.25p2s5粒子、2g作为正极活物质原料的lini
1/3
co
1/3
mn
1/3
o2粒子、0.03g作为导电材料的气相法碳纤维(vapor grown carbon fiber)、以及0.3g作为粘结剂的pvdf系树脂的5质量%丁酸丁酯溶液添加到聚丙烯制容器中。将该容器在超声波分散装置中进行30秒超声波处理后,使用振荡器进行30分钟振荡处理,从而制备了正极复合材料用原料。
[0173]
将这样准备好的正极复合材料用原料通过使用敷料器的刮涂法涂布到作为集电体的铝箔上,进行了60分钟自然干燥而得到了正极前体。
[0174]
将这样得到的正极前体在调整为100℃的热板上进行30分钟干燥而制造了正极。
[0175]
将0.4g作为固体电解质原料并且平均粒径为2μm的0.75li2s-0.25p2s5、以及0.05g作为粘结剂的abr系树脂的5质量%庚烷溶液添加到聚丙烯制容器中。将该容器在超声波分散装置中进行30秒超声波处理后,使用振荡器进行30分钟振荡处理,从而制备了固体电解质材料部用糊(paste)。
[0176]
将这样准备好的固体电解质材料部用糊通过使用敷料器的刮涂法涂布到作为基盘的al箔上,在调整为100℃的热板上进行30分钟干燥,从而得到了固体电解质层。
[0177]
将上述的负极、固体电解质层、正极以按该顺序接触的方式进行了层叠。对该负极-固体电解质层-正极层叠体以130℃施加200mpa的压力达3分钟,得到了实施例1的固体型锂离子二次电池。
[0178]
(比较例1)
[0179]
除了使用比较制造例3的硅材料作为负极活性物质以外,用与实施例1同样的方法
制造了比较例1的固体型锂离子二次电池。
[0180]
(参考例1)
[0181]
除了使用表现出金刚石结构的si晶体粉末作为负极活性物质以外,通过与实施例1同样的方法制造了参考例1的固体型锂离子二次电池。
[0182]
(评价例5)
[0183]
按规定的压力约束实施例1的固体型锂离子二次电池,以0.1c(库仑)流通恒电流至规定的电压为止而进行了初次充电。
[0184]
在初次充电中,监视了电池的约束压力,测定了充电状态下的约束压力。
[0185]
关于比较例1及参考例1的固体型锂离子二次电池,也进行了同样的试验。
[0186]
算出了以由参考例1的固体型锂离子二次电池测定出的最大约束压力为基准的、由实施例1及比较例1的固体型锂离子二次电池测定出的最大约束压力的比例。
[0187]
将结果在表5中示出。
[0188]
[表5]
[0189][0190]
根据表5可知,使用含有硅包合物ii的硅材料作为负极活性物质的实施例1及比较例1的固体型锂离子二次电池中的约束压力均较之使用si晶体粉末作为负极活性物质的参考例1的固体型锂离子二次电池中的约束压力而减小了。而且可知,在含有硅包合物ii的硅材料中,若直径为100nm以下的孔的体积大,则约束压力的减小率高。
[0191]
根据以上的结果可以说,通过将本发明的硅材料用作负极活性物质,能够有效地抑制充电时负极的膨胀。