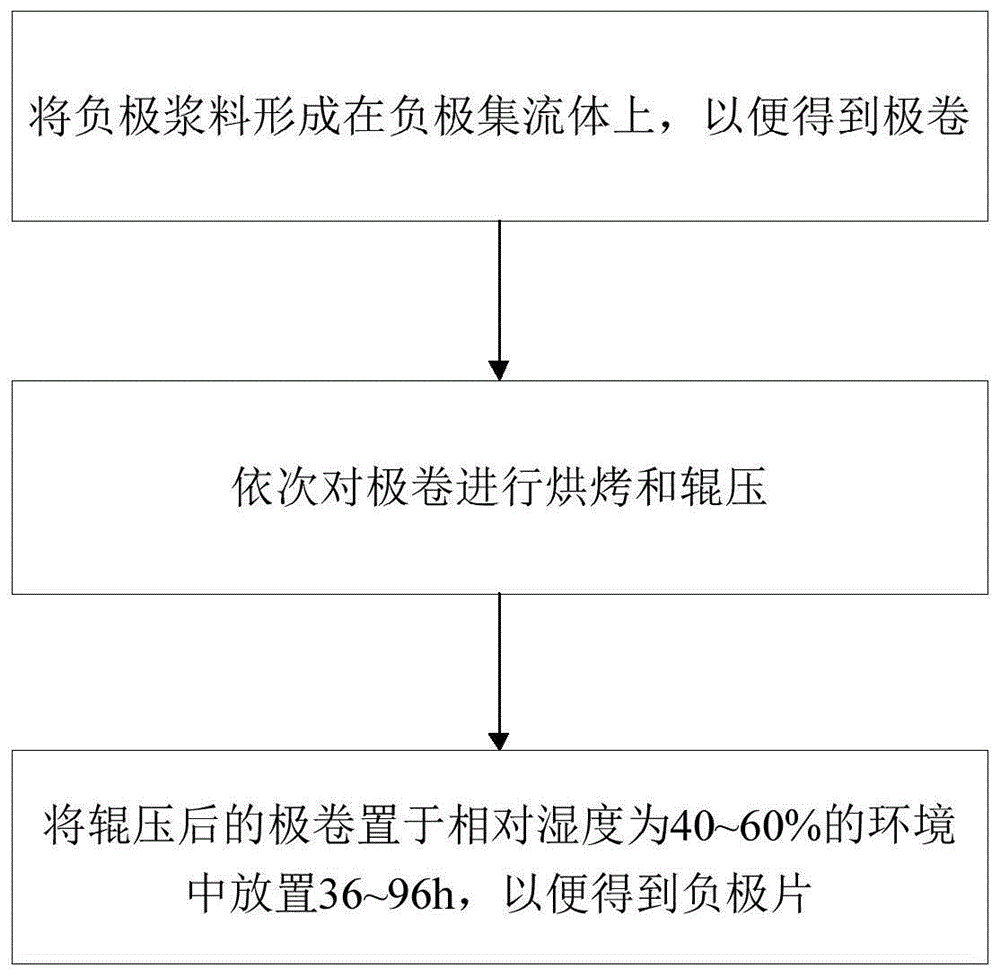
本发明属于电池领域,具体而言,涉及负极浆料、负极片及其制备方法和应用。
背景技术:
:发展新能源汽车已成为国家战略,是我国由汽车大国走向汽车强国的必由之路,电动汽车是新能源汽车的重要组成部分,汽车电动化也是目前车企的转折之路。目前,动力电池在近几年得到较快发展,电池能量密度在近两年快速提高。磷酸铁锂电池单体比能量平均达到160wh/kg,系统140wh/kg左右,三元电池单体比能量在220-240wh/kg左右,系统能量密度在140-160wh/kg左右。在2019年,动力电池能量密度有进一步上升趋势。量产的磷酸铁锂电池有望达到190wh/kg,系统160wh/kg;高比能三元电池单体达260wh/kg,系统达180wh/kg以上。目前,提升电池能量密度方法主要是使用克容量更高的三元高镍材料,减少结构件重量,减少箔材厚度,减少隔膜的厚度。但是使用容量更高的三元高镍材料时,由于高镍材料的热稳定性较差,使用时具有一定的安全隐患,例如热失控;而减少结构件重量,减少箔材和隔膜重量更容易带来安全问题。技术实现要素:本发明旨在至少在一定程度上解决相关技术中的技术问题之一。为此,本发明的一个目的在于提出负极浆料、负极片及其制备方法和应用。该负极浆料稳定性好,可以在不减少极片结构件重量、不减少箔材厚度和隔膜厚度的前提下提高电池能量密度,并降低电池内阻。根据本发明的第一个方面,本发明提出了一种负极浆料。根据本发明的实施例,该负极浆料包括:96~98.5重量份的负极活性物质、0.05~1.3重量份的导电剂和0.85~3.2重量份的粘结剂,其中,所述负极活性物质为石墨,所述导电剂为超导炭黑和/或碳纳米管,所述粘结剂为聚丙烯腈类粘结剂、聚丙烯腈类粘结剂和丁苯橡胶的混合物或者羧甲基纤维素钠和丁苯橡胶的混合物。根据本发明上述实施例的负极浆料,发明人发现,当采用石墨作为负极活性物质时,通过控制石墨、导电剂和粘结剂为上述原料组成及配比,不仅可以使负极浆料具有较好的稳定性,进而改善负极片的加工性能,而且还能提高负极片中的活性物质占比,在不减少极片结构件重量、不减少箔材厚度和隔膜厚度的前提下提高电池能量密度,并降低电池内阻,从而有效避免现有技术中因减少结构件重量、减少箔材和隔膜重量所带来的安全隐患。另外,根据本发明上述实施例的负极浆料还可以具有如下附加的技术特征:在本发明的一些实施例中,所述负极浆料包括:96~98.5重量份的石墨、0.5~1重量份的超导炭黑、0.05~0.3重量份的碳纳米管、1.1~1.3重量份的羧甲基纤维素钠和0.85~1.4重量份的丁苯橡胶;或者,所述负极浆料包括:96~98.5重量份的石墨、0.5~1重量份的超导炭黑、0.05~0.3重量份的碳纳米管、1.45~3.0重量份的聚丙烯腈类粘结剂;或者,所述负极浆料包括:96~98.5重量份的石墨、0.5~1重量份的超导炭黑、0.05~0.3重量份的碳纳米管、0.7~1.5重量份的聚丙烯腈类粘结剂和0.4~1重量份的丁苯橡胶。在本发明的一些实施例中,所述碳纳米管为单壁碳纳米管,所述负极浆料包括:96~98.5重量份的石墨、0.05~0.3重量份的碳纳米管、1.1~1.3重量份的羧甲基纤维素钠和0.85~1.4重量份的丁苯橡胶;或者,所述负极浆料包括:96~98.5重量份的石墨、0.05~0.3重量份的碳纳米管、1.45~3.0重量份的聚丙烯腈类粘结剂;或者,所述负极浆料包括:96~98.5重量份的石墨、0.05~0.3重量份的碳纳米管、0.7~1.5重量份的聚丙烯腈类粘结剂和0.4~1重量份的丁苯橡胶。在本发明的一些实施例中,所述负极浆料包括:97~98.5重量份的石墨。根据本发明的第二个方面,本发明提出了一种负极片。根据本发明的实施例,该负极片采用上述负极浆料制备得到。与现有技术相比,该负极片的加工性能较好,且活性物质占比高,将其用于电池中可以进一步提高电池的能量密度,同时降低电池内阻。根据本发明的第三方面,本发明提出了一种制备负极片的方法。根据本发明的实施例,该方法包括:(1)将权利要求1~4中任一项所述的负极浆料形成在负极集流体上,以便得到极卷;(2)依次对所述极卷进行烘烤和辊压;(3)将辊压后的极卷置于相对湿度为40~60%的环境中放置36~96h,以便得到负极片。根据本发明上述实施例的制备负极片的方法,发明人发现,辊压后的极卷在放置过程中,环境相对湿度过低或过高均不利于负极片中粘结剂的结构恢复,影响负极片的结构稳定性;并且,虽然随着放置时间的延长可以提高电池的循环稳定性,但当放置时间过长时,反而会导致电池循环稳定性下降。而当将辊压后的极卷置于相对湿度为40~60%的环境中放置36~96h再用于制备电池时,可以使电池具有更高的循环稳定性,例如在常温下和1c/1c的充放电倍率下循环500周后电池的循环容量保持率可达到95%以上。综上,该制备方法工艺简单,不仅可以改善负极片的加工性能并提高电池的能量密度、降低电池内阻,还能在不增加额外成本的前提下显著改善电池的循环性能。在本发明的一些实施例中,所述负极浆料采用如下方法制备得到:(i)将一部分的所述粘结剂和去离子水混合打胶,以便得到胶液;(ii)将所述导电剂与所述胶液混合,以便得到导电胶液;(iii)将所述负极活性物质与所述导电胶液混合,以便得到所述混合浆料;(iv)将剩余部分的所述粘结剂与所述混合浆料混合,以便得到负极浆料。或者,所述负极浆料采用如下方法制备得到:(i)将所述粘结剂和去离子水混合打胶,以便得到胶液;(ii)将所述导电剂与所述胶液混合,以便得到导电胶液;(iii)将所述负极活性物质与所述导电胶液混合,以便得到所述负极浆料。在本发明的一些实施例中,制备所述负极浆料时至少满足以下条件之一:步骤(i)中,将羧甲基纤维素钠或聚丙烯腈类粘结剂与去离子水按照质量比为(1~1.5):100混合并搅拌1~4h,以便得到所述胶液;步骤(ii)中,预先将超导炭黑与所述胶液混合并搅拌1~3h,然后再混入碳纳米管搅拌1~3h,以便得到所述导电胶液;步骤(ii)中,将单壁碳纳米管与所述胶液混合并搅拌1~3h,以便得到所述导电胶液;步骤(iii)中,将石墨与所述导电胶液混合并搅拌3~7h,以便得到所述混合浆料;步骤(iv)中,将丁苯橡胶与所述混合浆料混合并搅拌0.5~1h,以便得到所述负极浆料。步骤(i)中,将聚丙烯腈类粘结剂与去离子水按照质量比为(1~1.5):100混合并搅拌1~4h,以便得到所述胶液;步骤(ii)中,预先将超导炭黑与所述胶液混合并搅拌1~3h,然后再混入碳纳米管搅拌1~3h,以便得到所述导电胶液;步骤(ii)中,将单壁碳纳米管与所述胶液混合并搅拌1~3h,以便得到所述导电胶液;步骤(iii)中,将所述负极活性物质与所述导电胶液混合,以便得到所述负极浆料。在本发明的一些实施例中,制备负极片的方法至少满足以下条件之一:步骤(2)中,所述烘烤的时间为10~14h;步骤(3)中,将混压后的极片置于相对湿度为40~60%的环境中放置48~72h。根据本发明的第四个方面,本发明提出了一种电池。根据本发明的实施例,该电池具有上述负极片或采用上述制备方法得到的负极片。与现有技术相比,该负极片不仅能量密度高,还具有较好的循环性能和安全性能。本发明的附加方面和优点将在下面的描述中部分给出,部分将从下面的描述中变得明显,或通过本发明的实践了解到。附图说明本发明的上述和/或附加的方面和优点从结合下面附图对实施例的描述中将变得明显和容易理解,其中:图1是根据本发明一个实施例的制备负极片的方法流程图。图2是根据本发明几个实施例的负极浆料的粘度随时间变化的对比图。具体实施方式下面详细描述本发明的实施例,所述实施例的示例在附图中示出,其中自始至终相同或类似的标号表示相同或类似的元件或具有相同或类似功能的元件。下面通过参考附图描述的实施例是示例性的,旨在用于解释本发明,而不能理解为对本发明的限制。根据本发明的第一个方面,本发明提出了一种负极浆料。根据本发明的实施例,该负极浆料包括:96~98.5重量份的负极活性物质、0.05~1.3重量份的导电剂和0.85~3.2重量份的粘结剂,其中,负极活性物质为石墨,导电剂为超导炭黑和/或碳纳米管,粘结剂为聚丙烯腈类粘结剂、聚丙烯腈类粘结剂和丁苯橡胶的混合物或者羧甲基纤维素钠和丁苯橡胶的混合物。发明人发现,当采用石墨作为负极活性物质时,通过控制石墨、导电剂和粘结剂为上述原料组成及配比,不仅可以使负极浆料具有较好的稳定性,进而改善负极片的加工性能,而且还能提高负极片中的活性物质占比,在不减少极片结构件重量、不减少箔材厚度和隔膜厚度的前提下提高电池能量密度,并降低电池内阻,从而有效避免现有技术中因减少结构件重量、减少箔材和隔膜重量所带来的安全隐患。下面对本发明上述实施例的负极浆料进行详细描述。根据本发明的实施例,本发明通过优化导电剂和粘结剂组合方式及负极浆料的配比从而提高负极活性物质的占比,与常规配方相比,在不降低电池dcr的情况下,最高活性物质占比达98.5%。根据本发明的一个具体实施例,负极浆料可以包括:96~98.5重量份的石墨、0.5~1重量份的超导炭黑(sp)、0.05~0.3重量份的碳纳米管、1.1~1.3重量份的羧甲基纤维素钠(cmc)和0.85~1.4重量份的丁苯橡胶(sbr),例如石墨的重量份数可以为96、96.5、97、97.5、98或98.5等;超导炭黑的重量份数可以为0.5、0.6、0.7、0.8、0.9或1等;碳纳米管的重量份数可以为0.05、0.1、0.15、0.2、0.25或0.3等;羧甲基纤维素钠的重量份数可以为1.1、1.14、1.18、1.22、1.26或1.3等;丁苯橡胶的重量份数可以为0.85、0.9、0.95、1、1.05、1.1、1.15、1.2、1.25、1.3、1.35、或1.4等。发明人发现,当采用石墨作为活性物质并以sp和碳纳米管作为导电剂、以cmc和sbr作为粘结剂时,通过控制各组分为上述配比,不仅可以进一步提高负极浆料的稳定性,进而改善负极片的加工性能,还能提高负极片的结构稳定性和活性物质占比,在不减少极片结构件重量、不减少箔材厚度和隔膜厚度的前提下提高电池能量密度,并降低电池内阻。需要说明的是,该负极浆料中,碳纳米管可以为多壁碳纳米管和/或单壁碳纳米管。根据本发明的再一个具体实施例,负极浆料可以包括:96~98.5重量份的石墨、0.5~1重量份的超导炭黑(sp)、0.05~0.3重量份的碳纳米管、1.45~3.0重量份的聚丙烯腈类粘结剂,例如石墨的重量份数可以为96、96.5、97、97.5、98或98.5等;超导炭黑的重量份数可以为0.5、0.6、0.7、0.8、0.9或1等;碳纳米管的重量份数可以为0.05、0.1、0.15、0.2、0.25或0.3等;聚丙烯腈类粘结剂的重量份数可以为1.45、1.55、1.65、1.75、1.95、2.05、2.25、2.5、2.75或3等,优选1.45~2.5。发明人发现,当采用石墨作为活性物质并以sp和碳纳米管作为导电剂时,相对于以cmc和sbr作为粘结剂,当选择聚丙烯腈类粘结剂时,可以进一步降低粘结剂的用量,从而提高活性物质的占比;进一步地,通过控制各组分为上述配比,可以进一步提高负极浆料的稳定性,进而改善负极片的加工性能,同时提高负极片的结构稳定性和活性物质占比,在不减少极片结构件重量、不减少箔材厚度和隔膜厚度的前提下提高电池能量密度,并降低电池内阻。需要说明的是,该负极浆料中,碳纳米管可以为多壁碳纳米管和/或单壁碳纳米管。根据本发明的又一个具体实施例,负极浆料可以包括:96~98.5重量份的石墨、0.5~1重量份的超导炭黑(sp)、0.05~0.3重量份的碳纳米管、0.7~1.5重量份的聚丙烯腈类粘结剂和0.4~1重量份的丁苯橡胶(sbr),例如石墨的重量份数可以为96、96.5、97、97.5、98或98.5等;超导炭黑的重量份数可以为0.5、0.6、0.7、0.8、0.9或1等;碳纳米管的重量份数可以为0.05、0.1、0.15、0.2、0.25或0.3等;聚丙烯腈类粘结剂的重量份数可以为0.7、0.8、0.9、1.0、1.1、1.2、1.3、1.4或1.5等;丁苯橡胶的重量份数可以为0.4、0.5、0.6、0.7、0.8、0.9或1等。发明人发现,当采用石墨作为活性物质并以sp和碳纳米管作为导电剂时,以聚丙烯腈类粘结剂和sbr作为粘结剂可以进一步提高负极浆料的稳定性以及制备得到负极片的结构稳定性;进一步地,通过控制各组分为上述配比,可以进一步提高负极浆料的稳定性,进而改善负极片的加工性能,同时提高负极片的结构稳定性和活性物质占比,在不减少极片结构件重量、不减少箔材厚度和隔膜厚度的前提下提高电池能量密度,并降低电池内阻。需要说明的是,该负极浆料中,碳纳米管可以为多壁碳纳米管和/或单壁碳纳米管。根据本发明的又一个具体实施例,负极浆料可以包括:96~98.5重量份的石墨、0.05~0.3重量份的单壁碳纳米管、1.1~1.3重量份的羧甲基纤维素钠(cmc)和0.85~1.4重量份的丁苯橡胶(sbr),例如石墨的重量份数可以为96、96.5、97、97.5、98或98.5等;单壁碳纳米管的重量份数可以为0.05、0.1、0.15、0.2、0.25或0.3等;羧甲基纤维素钠的重量份数可以为1.1、1.14、1.18、1.22、1.26或1.3等;丁苯橡胶的重量份数可以为0.85、0.9、0.95、1、1.05、1.1、1.15、1.2、1.25、1.3、1.35、或1.4等。发明人发现,超导炭黑实际上是通过点与点接触实现导电的,而单壁碳纳米管缺陷较少,一致性更好,且呈束状结构,具有完整的导电网络,可以大大提高导电性能,因此,若选用单壁碳纳米管作为导电剂,即便不采用超导炭黑,也可以显著提高制备得到的负极片的导电性,同时,导电剂总量的降低还有利于进一步提高活性物质占比;进一步地,通过控制各组分为上述配比,可以进一步提高负极浆料的稳定性,进而改善负极片的加工性能,同时提高负极片的结构稳定性和活性物质占比,在不减少极片结构件重量、不减少箔材厚度和隔膜厚度的前提下提高电池能量密度,并降低电池内阻。根据本发明的又一个具体实施例,负极浆料可以包括:负极浆料包括:96~98.5重量份的石墨、0.05~0.3重量份的单壁碳纳米管、1.45~3.0重量份的聚丙烯腈类粘结剂,例如石墨的重量份数可以为96、96.5、97、97.5、98或98.5等;超导炭黑的重量份数可以为0.5、0.6、0.7、0.8、0.9或1等;单壁碳纳米管的重量份数可以为0.05、0.1、0.15、0.2、0.25或0.3等;聚丙烯腈类粘结剂的重量份数可以为1.45、1.55、1.65、1.75、1.95、2.05、2.25、2.5、2.75或3等,优选1.45~2.5。由此可以进一步提高负极浆料的稳定性,进而改善负极片的加工性能,同时提高负极片的结构稳定性和活性物质占比,在不减少极片结构件重量、不减少箔材厚度和隔膜厚度的前提下提高电池能量密度,并降低电池内阻。根据本发明的又一个具体实施例,负极浆料可以包括:96~98.5重量份的石墨、0.05~0.3重量份的单壁碳纳米管、0.7~1.5重量份的聚丙烯腈类粘结剂和0.4~1重量份的丁苯橡胶(sbr),例如石墨的重量份数可以为96、96.5、97、97.5、98或98.5等;单壁碳纳米管的重量份数可以为0.05、0.1、0.15、0.2、0.25或0.3等;聚丙烯腈类粘结剂的重量份数可以为0.7、0.8、0.9、1.0、1.1、1.2、1.3、1.4或1.5等;丁苯橡胶的重量份数可以为0.4、0.5、0.6、0.7、0.8、0.9或1等。由此可以进一步提高负极浆料的稳定性,进而改善负极片的加工性能,同时提高负极片的结构稳定性和活性物质占比,在不减少极片结构件重量、不减少箔材厚度和隔膜厚度的前提下提高电池能量密度,并降低电池内阻。根据本发明的又一个具体实施例,基于上述负极浆料的组成,为进一步提高负极片活性物质占比,可以将石墨含量提升至97~98.5重量份,由此可以在不影响负极浆料稳定性和负极片导电性的前提下进一步提高活性物质占比,从而更有利于提高电池的能量密度。根据本发明的又一个具体实施例,本发明中采用的聚丙烯腈类粘结剂的分子量不低于30万。由此可以进一步提高负极浆料的稳定性和负极片的结构稳定性。根据本发明的又一个具体实施例,本发明中石墨、导电炭黑和碳纳米管的尺寸并不受特别限制,本领域技术人员可以根据实际需要进行选择,例如石墨和碳纳米管的尺寸可以为微纳米级,再例如,石墨d50尺寸范围可以为13~28微米,导电炭黑的粒径可以为9~17纳米,多壁碳纳米管的管径可为2~100纳米,单壁碳纳米管的管径可以为0.6~2纳米,由此可以进一步提高负极浆料的稳定性。综上所述,根据本发明上述实施例的负极浆料,当采用石墨作为负极活性物质时,通过控制石墨、导电剂和粘结剂为上述原料组成及配比,不仅可以使负极浆料具有较好的稳定性,进而改善负极片的加工性能,而且还能提高负极片中的活性物质占比,在不减少极片结构件重量、不减少箔材厚度和隔膜厚度的前提下提高电池能量密度,并降低电池内阻,从而有效避免现有技术中因减少结构件重量、减少箔材和隔膜重量所带来的安全隐患。具体地,可以在不降低电池dcr的情况下,使负极片最高活性物质占比达98.5%。根据本发明的第二个方面,本发明提出了一种负极片。根据本发明的实施例,该负极片采用上述负极浆料制备得到。与现有技术相比,该负极片的加工性能较好,且活性物质占比高,将其用于电池中可以进一步提高电池的能量密度,同时降低电池内阻。需要说明的是,针对上述负极浆料所描述的特征及效果同样适用于该负极片,此处不再一一赘述。根据本发明的第三方面,本发明提出了一种制备负极片的方法。根据本发明的实施例,参考图1,该方法包括:(1)将权利要求1~4中任一项的负极浆料形成在负极集流体上,以便得到极卷;(2)依次对极卷进行烘烤和辊压;(3)将辊压后的极卷置于相对湿度为40~60%的环境中放置36~96h,以便得到负极片。需要说明的是,制备得到的该负极片直接用于制备电池,不再继续放置。该制备方法工艺简单,不仅可以改善负极片的加工性能并提高电池的能量密度、降低电池内阻,还能在不增加额外成本的前提下显著改善电池的循环性能。下面对本发明上述实施例的制备负极片的方法进行详细描述。根据本发明的实施例,本发明中通过控制极片的放置环境以及放置时间来使负极片中粘结剂发生迁移重新建立连接,从而使极片微观结构发生变化,使负极片的机械稳定性更加稳定,从而具有更好的循环稳定性。发明人发现,辊压后的极卷在放置过程中,环境相对湿度过低或过高均不利于负极片中粘结剂的结构恢复,影响负极片的结构稳定性;并且,虽然随着放置时间的延长可以提高电池的循环稳定性,但当放置时间过长时,反而会导致电池循环稳定性下降。而当将辊压后的极卷置于相对湿度为40~60%的环境中放置36~96h再用于制备电池时,可以使电池具有更高的循环稳定性,例如在常温下和1c/1c的充放电倍率下循环500周后电池的循环容量保持率可达到95%以上。根据本发明的一个具体实施例,负极浆料可以采用如下方法制备得到:(i)将一部分的粘结剂和去离子水混合打胶,以便得到胶液;(ii)将导电剂与胶液混合,以便得到导电胶液;(iii)将负极活性物质与导电胶液混合,以便得到混合浆料;(iv)将剩余部分的粘结剂与混合浆料混合,以便得到负极浆料。由此可以进一步提高负极浆料的稳定性和均匀性。进一步地:步骤(i)中,可以将羧甲基纤维素钠或聚丙烯腈类粘结剂与去离子水按照质量比为(1~1.5):100混合并搅拌1~4h,以便得到胶液,发明人发现,通过控制上述混合条件不仅可以进一步提高打胶效率,还更有利于胶液与其它组分均匀混合。步骤(ii)中,可以预先将超导炭黑与胶液混合并搅拌1~3h,然后再混入碳纳米管搅拌1~3h,以便得到导电胶液;也可以单独将单壁碳纳米管与胶液混合并搅拌1~3h,以便得到导电胶液。步骤(iii)中,可以将石墨与导电胶液混合并搅拌3~7h,以便得到混合浆料。步骤(iv)中,可以将丁苯橡胶与混合浆料混合并搅拌0.5~1h,以便得到负极浆料,由此可以进一步提高负极浆料的均匀性和稳定性。需要说明的是,制备负极片时,均按照上述负极浆料的预定比例来配制负极浆料。根据本发明的再一个具体实施例,负极浆料可以采用如下方法制备得到:(i)将粘结剂和去离子水混合打胶,以便得到胶液;(ii)将导电剂与胶液混合,以便得到导电胶液;(iii)将负极活性物质与所述导电胶液混合,以便得到负极浆料。进一步地,步骤(i)中,将聚丙烯腈类粘结剂与去离子水按照质量比为(1~1.5):100混合并搅拌1~4h,以便得到胶液;步骤(ii)中,可以预先将超导炭黑与胶液混合并搅拌1~3h,然后再混入碳纳米管搅拌1~3h,以便得到导电胶液,也可以将单壁碳纳米管与胶液混合并搅拌1~3h,以便得到导电胶液;步骤(iii)中,将负极活性物质与所述导电胶液混合,以便得到负极浆料。由此可以进一步简化负极浆料的制备工艺。根据本发明的再一个具体实施例,制备负极片时,步骤(2)中的烘烤的时间可以为10~14h,例如可以为10h、11h、12h、13h或14h等,优选12h左右。根据本发明的又一个具体实施例,制备负极片时,步骤(3)中,可以将混压后的极片置于相对湿度为40~60%的环境中放置48~72h,例如可以在相对湿度为40%、43%、46%、50%、53%、56%或60%等的环境中放置48h、52h、56h、60h、64h、68h或72h等,由此可以进一步有利于提高电池具有更高的循环稳定性,使电池在常温下和1c/1c的充放电倍率下循环500周后电池的循环容量保持率达到95%以上。根据本发明的又一个具体实施例,负极片的制备方法可以包括:1)配制负极浆料,先将cmc放入去离子水中,搅拌1~4h使粉状cmc充分溶解形成均匀性较好的胶液,再将导电剂sp加入到打好的胶液中搅拌1~3h使导电剂均匀分散,然后再加入碳纳米管,再搅拌1~3h,使碳纳米管与sp导电浆料充分混合,加入石墨粉搅拌3~7h,最后加入sbr,搅拌0.5~1.0h,制得最终浆料,其中石墨:导电剂sp:碳纳米管:粘结剂cmc:粘结剂sbr质量比可以为(96~98.5):(0.5~1):(0.05~0.3):(1.1~1.3):(0.85~1.4);2)将制得的浆料涂布在负极集流体上并烘烤12h,然后辊压;将辊压后的极卷置于相对湿度为40~60%的环境中放置48~96h。根据本发明的又一个具体实施例,本发明中负极集流体的类型并不受特别限制,本领域技术人员可以根据实际需要进行选择,例如负极集流体可以为铜箔。根据本发明的又一个具体实施例,采用将辊压后的极卷置于相对湿度为40~60%的环境中放置36~96h得到的负极片组装电池时,电池的组装流程并不受特别限制,本领域技术人员可以根据实际需要进行选择。综上所述,根据本发明上述实施例的制备负极片的方法,辊压后的极卷在放置过程中,环境相对湿度过低或过高均不利于负极片中粘结剂的结构恢复,影响负极片的结构稳定性;并且,虽然随着放置时间的延长可以提高电池的循环稳定性,但当放置时间过长时,反而会导致电池循环稳定性下降。而当将辊压后的极卷置于相对湿度为40~60%的环境中放置36~96h再用于制备电池时,可以使电池具有更高的循环稳定性,例如在常温下和1c/1c的充放电倍率下循环500周后电池的循环容量保持率可达到95%以上。综上,该制备方法工艺简单,不仅可以改善负极片的加工性能并提高电池的能量密度、降低电池内阻,还能在不增加额外成本的前提下显著改善电池的循环性能。需要说明的是,针对上述负极浆料所描述的特征及效果同样适用于该制备负极片的方法,此处不再一一赘述。根据本发明的第四个方面,本发明提出了一种电池。根据本发明的实施例,该电池具有上述负极片或采用上述制备方法得到的负极片。与现有技术相比,该负极片不仅能量密度高,还具有较好的循环性能和安全性能。需要说明的是,本发明中电池的类型并不受特别限制,本领域技术人员可以根据实际需要进行选择,例如该电池可以为液态电池、全固态电池或准固态电池。另外,还需要说明的是,针对上述负极片和制备负极片的方法所描述的特征及效果同样适用于该电池,此处不再一一赘述。下面将结合实施例对本发明的方案进行解释。本领域技术人员将会理解,下面的实施例仅用于说明本发明,而不应视为限定本发明的范围。实施例中未注明具体技术或条件的,按照本领域内的文献所描述的技术或条件或者按照产品说明书进行。所用试剂或仪器未注明生产厂商者,均为可以通过市购获得的常规产品。实施例11)负极浆料的制备:石墨、导电剂sp、碳纳米管(包括多壁碳纳米管)、粘结剂cmc、粘结剂sbr的质量比为96:0.5:0.3:1.3:1.9,先将粘结剂cmc放入去离子水中,搅拌2h使粉状cmc充分溶解形成均匀性较好的胶液,再将导电剂sp加入到打好的胶液中搅拌1h使导电剂均匀分散,然后再加入碳纳米管,再搅拌2h,使碳纳米管与sp导电浆料充分混合,加入石墨粉搅拌3h,最好加入粘结剂sbr,搅拌0.5h,制得最终浆料。2)涂布:将上述制得的浆料在8微米双面光铜箔上进行涂布,将涂布后的极卷烘烤12h。3)辊压:将烘烤的极片进行辊压。4)将辊压后的极片放置在相对湿度为40%的环境下,放置48h。5)按照常规流程将极片制作成电池。实施例21)负极浆料的制备:石墨、导电剂sp、单壁碳纳米管、粘结剂cmc、粘结剂sbr的质量比为97:0.5:0.05:1.1:1.35,先将粘结剂cmc放入去离子水中,搅拌2h使粉状cmc充分溶解形成均匀性较好的胶液,再将导电剂sp加入到打好的胶液中搅拌1h使导电剂均匀分散,然后再加入单壁碳纳米管,再搅拌2h,使碳纳米管与sp导电浆料充分混合,加入石墨粉搅拌3h,最好加入粘结剂sbr,搅拌0.5h,制得最终浆料。2)涂布:将上述制得的浆料在8微米双面光铜箔上进行涂布,将涂布后的极卷烘烤12h。3)辊压:将烘烤的极片进行辊压。4)将辊压后的极片放置在相对湿度为40%的环境下,放置48h。5)按照常规流程将极片制作成电池。实施例31)负极浆料的制备:石墨、单壁碳纳米管、粘结剂cmc、粘结剂sbr的质量比为98:0.05:1.1:0.85,先将粘结剂cmc放入去离子水中,搅拌2h使粉状cmc充分溶解形成均匀性较好的胶液,再将单壁碳纳米管加入到打好的胶液中搅拌2h使导电剂均匀分散,然后加入石墨粉搅拌3h,最好加入粘结剂sbr,搅拌0.5h,制得最终浆料。2)涂布:将上述制得的浆料在8微米双面光铜箔上进行涂布,将涂布后的极卷烘烤12h。3)辊压:将烘烤的极片进行辊压。4)将辊压后的极片放置在相对湿度为40%的环境下,放置48h。5)按照常规流程将极片制作成电池。实施例41)负极浆料的制备:石墨、单壁碳纳米管、聚丙烯腈类粘结剂的质量比为98.5:0.05:1.45,将单壁碳纳米管加入聚丙烯腈类粘结剂胶液中搅拌2h使导电剂均匀分散,然后加入石墨粉搅拌3h,制得最终浆料。2)涂布:将上述制得的浆料在8微米双面光铜箔上进行涂布,将涂布后的极卷烘烤12h。3)辊压:将烘烤的极片进行辊压。4)将辊压后的极片放置在相对湿度为40%的环境下,放置48h。5)按照常规流程将极片制作成电池。对实施例1~4中负极浆料稳定性和制备得到的电池进行测试,测试结果见图2和表1~2。其中,实施例1中活性物质占比为96wt%,实施例2~4中,负极配方中的活性物质占比分别为97wt%、98wt%和98.5wt%。从表1和图2中可以看出实施例1~4的稳定性均较好,且实施例3和4的浆料稳定性更佳,加工性能更好。且实施例1~4中50%soc的放电18s放电dcr分别为15.47mω、12.40mω、12.31mω和12.24mω,可以看出,采用单壁碳纳米管作为导电剂,即便提高活性物质含量提高,电池50%soc的放电18s放电dcr也有所降低,也就是说,可以在提高电池能量密度的基础上进一步降低电池内阻,这是由于单壁碳纳米管的束状结构和高导电性使负极具有较低的内阻,较小的极化,电池dcr表现为较低的直流内阻。实施例5与实施4区别在于:4)将辊压后的极片放置在相对湿度为60%的环境下,放置48h。对比例1与实施4区别在于:不进行步骤4)。对比例2与实施4区别在于:4)将辊压后的极片放置在相对湿度为20%的环境下,放置48h。对比例3与实施4区别在于:4)将辊压后的极片放置在相对湿度为80%的环境下,放置48h。测试实施例4~5和对比例1~3制备得到的电池的循环性能,测试结果见表3。其中,循环测试条件为25℃,测试充放电电流1c/1c。从表3中可以看出,步骤4)中的相对湿度为40%和60%时,其对应常温循环500周对应的循环保持率分别为95.15%和94.67%,具有更好的循环性能。而极片辊压后不在一定相对湿度下搁置一段时间,直接流转到电池组装工序制备的电池对应500周对应的循环保持率为92.05%,循环性能相对较差;而在相对湿度为20%和80%的环境中搁置时,得到的电池对应常温循环500周对应的循环保持率分别为91.9%和89.6%,可以看出,最优的放置环境相对湿度为40%~60%。这是由于在该湿度条件下能够更好的恢复负极片中粘结剂的结构,从而提升辊压后负极片的结构稳定性,改善电池的循环性能。实施例6与实施4区别在于:4)将辊压后的极片放置在相对湿度为60%的环境下,放置72h。对比例4与实施4区别在于:4)将辊压后的极片放置在相对湿度为60%的环境下,放置24h。对比例5与实施4区别在于:4)将辊压后的极片放置在相对湿度为60%的环境下,放置96h。测试实施例5~6和对比例4~5制备得到的电池的循环性能,测试结果见表4。其中,循环测试条件为25℃,测试充放电电流1c/1c。从表4中可以看出,步骤4)中的搁置时间为24h、48h、72h、96h时,其对应常温循环500周对应的循环保持率分别为93.05%、95.15%、95.03%和91.6%,搁置时间为48h和72h时,其具有更好的循环性能。而搁置时间为24h时,由于时间较短,循环容量保持率不是最优,而当搁置时间为4d时,由于时间搁置时间太长导致循环性能下降,由此说明制备得到的负极片搁置时间过长会导致电池循环性能恶化。表1浆料性能表2加工性能及dcr测试的结果表3循环性能对比实验相对湿度搁置时间充放电循环500周后容量保持率实施例440%48h95.15%实施例560%48h94.67%对比例1--92.05%对比例220%48h91.90%对比例380%48h89.60%表4循环性能对比实验相对湿度搁置时间充放电循环500周后容量保持率实施例440%48h95.15%实施例640%72h95.03%对比例440%24h93.05%对比例540%96h91.60%在本说明书的描述中,参考术语“一个实施例”、“一些实施例”、“示例”、“具体示例”、或“一些示例”等的描述意指结合该实施例或示例描述的具体特征、结构、材料或者特点包含于本发明的至少一个实施例或示例中。在本说明书中,对上述术语的示意性表述不必针对的是相同的实施例或示例。而且,描述的具体特征、结构、材料或者特点可以在任一个或多个实施例或示例中以合适的方式结合。此外,在不相互矛盾的情况下,本领域的技术人员可以将本说明书中描述的不同实施例或示例以及不同实施例或示例的特征进行结合和组合。尽管上面已经示出和描述了本发明的实施例,可以理解的是,上述实施例是示例性的,不能理解为对本发明的限制,本领域的普通技术人员在本发明的范围内可以对上述实施例进行变化、修改、替换和变型。当前第1页12