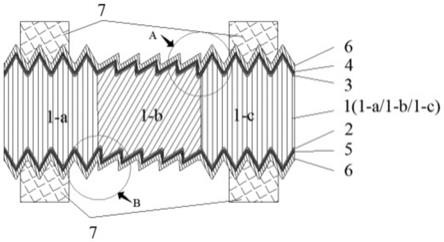
1.本发明涉及硅基异质结太阳能电池技术领域,尤其涉及以铸锭晶硅作为衬底制作硅基异质结的太阳能电池及其制作方法。
背景技术:2.能源需求日益紧张的形式下,太阳能电池行业迅猛发展。具有突出效率优势的异质结技术,量产效率已达到24%,实验室效率也达到26%以上,进一步效率提升潜力巨大,近年来备受瞩目。但异质结技术成本偏高,仍是当前大规模量产化的主要障碍。与常规晶硅太阳能电池相比,成本偏高主要体现在三大部分:设备折旧、银浆耗量、硅片成本。
3.常规的硅基异质结太阳能电池,均采用直拉单晶硅片作为衬底制作,对硅片品质有极高的要求,导致硅片成居高不下。以较低品质的铸锭单晶硅片或多晶硅片替代直拉单晶硅片制作硅基异质结太阳能电池,可以显著降低异质结太阳能电池成本。
4.然而铸锭晶硅内存在大量的杂质和缺陷,形成大量的复合中心,极大限制了载流子的迁移,导致采用铸锭单晶硅片或多晶硅片制作的异质结太阳能电池效率远低于常规直拉单晶硅片制作的异质结太阳能电池。减少和消除杂质和缺陷的影响,是铸锭单晶硅片或多晶硅片制作异质结太阳能电池的关键。其中,不同晶粒间存在的晶界缺陷是铸锭单晶硅片或多晶硅片内的主要缺陷区域,其不仅表现为大量的位错层错产生严重的复合,相邻晶粒由于生长方向不同,在制绒后,金字塔绒面生长方向有所差异,往往在相邻晶粒边界位置的金字塔容易形成较为尖锐夹角的结构。对于等离子气相沉积设备,较深的尖锐夹角区域h
+
离子和非晶硅膜层的钝化处理的效果较差,容易形成钝化缺陷而形成复合中心,影响载流子的传输。
5.因此,为了解决因晶粒生长方向不同,晶界区域的金字塔形成尖锐夹角结构导致的钝化不良缺陷,需要寻求一种制作方法,消除尖锐夹角结构,形成一种利于钝化的结构,以便对相邻晶粒边界位置进行良好的钝化。
技术实现要素:6.针对上述问题,本发明提供了一种铸锭晶硅异质结太阳能电池及其制作方法,通过消除相邻晶粒边界位置金字塔形状底部的尖锐夹角结构,形成金字塔形状底部平滑的弧形结构相连接,以改善相邻晶粒边界位置的钝化效果,以提高铸锭晶硅制作的异质结太阳能电池的转换效率。
7.本发明采用的技术方案是,提供一种铸锭晶硅异质结太阳能电池,其结构包括:铸锭晶硅衬底,所述铸锭晶硅衬底含有多个生长方向不同的晶粒;设置在铸锭晶硅衬底表面的金字塔绒面,其中,金字塔绒面底部的相邻晶粒边界位置具有平滑的弧形结构;设置在金字塔绒面表面的本征型非晶硅膜层和掺杂型的非晶硅膜层,其中,所述弧形结构上的本征型非晶硅膜层和掺杂型的非晶硅膜层的厚度比金字塔绒面的斜面上本征型非晶硅膜层和掺杂型的非晶硅膜层的厚度更厚;设置在掺杂型非晶硅膜层之上的透明导电膜层;及设置
在透明导电膜层之上的金属电极。
8.优选的,所述铸锭晶硅衬底为铸锭单晶硅片或铸锭多晶硅衬底,掺杂类型为n型或p型。
9.优选的,金字塔绒面高度为0.5-10微米;弧形结构的弧度长为0.1-1微米。
10.本发明还提供一种铸锭晶硅异质结太阳能电池的制作方法:所述方法包括步骤如下:去除铸锭晶硅衬底的杂质;对已去除杂质的铸锭晶硅衬底制作金字塔绒面;对已制作金字塔绒面的铸锭晶硅衬底进行区域圆滑处理,在金字塔绒面底部的相邻晶粒边界位置形成平滑的弧形结构;对铸锭晶硅衬底清洗并去除氧化层;对铸锭晶硅衬底两面沉积本征型非晶硅膜层和掺杂型非晶硅膜层进行钝化并形成pn结;在掺杂型非晶硅膜层上沉积透明导电膜层;及在透明导电膜层上形成金属电极。
11.优选的,所述去除铸锭晶硅衬底的杂质,为通过溶液预清洁去除有机污染和大颗粒,再表面沉积一层含磷硅氧的混合膜层后高温扩散去除杂质。
12.优选的,所述对已去除杂质的铸锭晶硅衬底制作金字塔绒面,为采用碱性蚀刻液进行各向异性的腐蚀制作金字塔绒面,所述碱性蚀刻液包含表面活性剂与抑制剂和氢氧化钠、氢氧化钾、氨水中至少一种的形成的混合溶液。
13.优选的,所述对已制作金字塔绒面的铸锭晶硅衬底进行区域圆滑处理,在金字塔绒面底部的相邻晶粒边界位置形成平滑的弧形结构,为采用酸性蚀刻液直接对金字塔绒面进行再蚀刻;或先采用酸性蚀刻液对金字塔绒面进行初步蚀刻,再用碱性微蚀液对金字塔绒面进行进一步蚀刻。
14.优选的,所述酸性蚀刻液包含表面活性剂与抑制剂,以及氢氟酸、硝酸、臭氧或双氧水中至少一种的混合溶液;所述碱性微蚀液包含表面活性剂与抑制剂和氢氧化钠、氢氧化钾、氨水中至少一种的形成的混合溶液。
15.优选的,所述碱性微蚀液的浓度低于所述碱性蚀刻液的浓度。
16.优选的,所述对铸锭晶硅衬底清洗并去除氧化层,为通过rca清洗去除表面残留的污渍和离子;再用hf的水溶液去除表面的氧化层。
17.由上述对本发明结构的描述可知,和现有技术相比,本发明具有如下优点:制作金字塔绒面后,通过先采用酸性蚀刻液进行初步蚀刻,后再用碱性微蚀液进行进一步蚀刻的圆滑处理方法,消除铸锭单晶硅片或多晶硅片衬底上因晶粒生长方向不同在相邻晶粒的边界位置的尖锐夹角结构,在金字塔绒面底部形成平滑的弧形结构;该平滑的弧形结构有利于改善后续h
+
离子的处理和非晶硅膜层的钝化效果;在上述平滑的弧形结构上沉积的本征型非晶硅层和掺杂型非晶硅膜层厚度比金字塔斜面上的本征型非晶硅膜层和掺杂型非晶硅膜层厚度更厚,进一步抑制相邻晶粒边界位置金字塔底部界面的载流子的复合,提高整体钝化水平。
附图说明
18.构成本技术的一部分的附图用来提供对本发明的进一步理解,本发明的示意性实施例及其说明用于解释本发明,并不构成对本发明的不当限定。在附图中:
19.图1为本发明一种铸锭晶硅异质结太阳能电池结构示意图;
20.图2为本发明一种铸锭晶硅异质结太阳能电池相邻晶粒边界位置金字塔底部的弧
形结构示意图;
21.图3为本发明一种铸锭晶硅异质结太阳能电池衬底金字塔形状底部的平滑弧形结构的sem图;
22.图4为本发明一种铸锭晶硅异质结太阳能电池衬底钝化后的pl图;
23.图5为对比例的结构示意图;
24.图6为对比例的金字塔绒面底部的尖锐夹角结构示意图;
25.图7为对比例金字塔绒面底部的尖锐夹角结构的sem图;
26.图8为对比例铸锭晶硅衬底钝化后的pl图。
具体实施方式
27.为了使本发明的目的、技术方案及优点更加清楚明白,以下结合附图、实施例和对比例,对本发明进行进一步详细说明。应当理解,此处所描述的具体实施例和对比例仅用以解释本发明,并不用于限定本发明。
28.实施例:
29.一种铸锭晶硅异质结太阳能电池,如图1及图2所示,其结构如下:n型掺杂的铸锭硅片衬底1内含有多个生长方向不同的晶粒(1-a/1-b/1-c),铸锭硅片衬底的表面设置有连续交替的金字塔绒面,其中,相邻晶粒1-b与晶粒1-c边界位置a的金字塔形状底部有平滑的弧形结构相连接,相邻晶粒1-a与晶粒1-b边界位置b的金字塔形状底部有平滑的弧形结构相连接(下文仅对相邻晶粒边界位置a进行结构说明);设置在金字塔绒面上的本征型非晶硅膜层2和3,其中,相邻晶粒1-b与晶粒1-c边界位置a的金字塔形状底部有平滑的弧形结构上的本征型非晶硅膜层3的厚度d1比金字塔斜面上的本征型非晶硅膜层3的厚度d2更大;设置在本征型非晶硅膜层3之上的n型掺杂型非晶硅膜层4,其中,相邻晶粒1-b与晶粒1-c边界位置a的金字塔形状底部的平滑的弧形结构上的n型掺杂型非晶硅膜层4的厚度d3比金字塔斜面上的n型掺杂型非晶硅膜层4的厚度d4更大;设置在本征型非晶硅膜层2之上的p型掺杂型非晶硅膜层5;设置在n型掺杂型非晶硅膜层4和p型掺杂型非晶硅膜层5之上的透明导电膜层6;设置在透明导电膜层6之上的金属电极7。所述铸锭晶硅衬底为铸锭单晶硅片或铸锭多晶硅衬底,掺杂类型为n型或p型。金字塔绒面高度为0.5-10微米;弧形结构的弧度长为0.1-1微米。
30.一种铸锭晶硅异质结太阳能电池的制作方法,所述方法包括步骤如下:去除铸锭晶硅衬底的杂质;对已去除杂质的铸锭晶硅衬底制作金字塔绒面;对已制作金字塔绒面的铸锭晶硅衬底进行区域圆滑处理,在金字塔绒面底部的相邻晶粒边界位置形成平滑的弧形结构;对铸锭晶硅衬底清洗并去除氧化层;对铸锭晶硅衬底两面沉积本征型非晶硅膜层和掺杂型非晶硅膜层进行钝化并形成pn结;在掺杂型非晶硅膜层上沉积透明导电膜层;及在透明导电膜层上形成金属电极。优选的,所述去除铸锭晶硅衬底的杂质,为通过溶液预清洁去除有机污染和大颗粒,再表面沉积一层含磷硅氧的混合膜层后高温扩散去除杂质。
31.所述对已去除杂质的铸锭晶硅衬底制作金字塔绒面,为采用碱性蚀刻液进行各向异性的腐蚀制作金字塔绒面,所述碱性蚀刻液包含表面活性剂与抑制剂和氢氧化钠、氢氧化钾、氨水中至少一种的形成的混合溶液。
32.所述对已制作金字塔绒面的铸锭晶硅衬底进行区域圆滑处理,在金字塔绒面底部
的相邻晶粒边界位置形成平滑的弧形结构,为采用酸性蚀刻液直接对金字塔绒面进行再蚀刻;或先采用酸性蚀刻液对金字塔绒面进行初步蚀刻,再用碱性微蚀液对金字塔绒面进行进一步蚀刻。
33.所述酸性蚀刻液包含表面活性剂与抑制剂,以及氢氟酸、硝酸、臭氧或双氧水中至少一种的混合溶液;所述碱性微蚀液包含表面活性剂与抑制剂和氢氧化钠、氢氧化钾、氨水中至少一种的形成的混合溶液。
34.所述碱性微蚀液的浓度低于所述碱性蚀刻液的浓度。
35.所述对铸锭晶硅衬底清洗并去除氧化层,为通过rca清洗去除表面残留的污渍和离子;再用hf的水溶液去除表面的氧化层。
36.具体实施例如下,步骤一,对n型掺杂的铸锭单晶硅片衬底使用氨水和双氧水的混合液在70℃以上的水溶液中浸泡清洗,以去除有机污染,烘干后采用化学气相沉积工艺(lpcvd/pecvd/hot wire cvd),在衬底表面沉积磷硅氧的混合层,并在700-1000℃的高温下退火,之后以hf溶液去除表面混合层,以去除衬底内部杂质及消除部分缺陷;步骤二,采用碱性制绒液对铸锭单晶硅片衬底进行各向异性的蚀刻,使表面产生连续接替的金字塔形状的绒面,由于铸锭单晶硅片衬底中存在不同生长方向的晶粒,相邻晶粒边界位置金字塔底部易形成尖锐的夹角结构;步骤三,采用酸性蚀刻液对表面金字塔形状进行再修饰,再表面活性剂与抑制剂的配合作用下,对金字塔斜面的蚀刻速度比金字塔底部,特别是尖锐的夹角结构区域的蚀刻速度更快,从而使底部形成平滑的弧形结构,再用碱性微蚀刻液对衬底表面进行处理,由于碱性微蚀液的工艺药剂浓度较低,可有效对金字塔顶部进行修饰以控制弧形结构的曲率和长度,使底部保持平滑的弧形结构;步骤四,采用hf溶液去除表面的氧化层;步骤五,采用pecvd对铸锭单晶衬底的表面进行h
+
处理,并沉积本征型非晶硅和掺杂型非晶硅,其中底部平滑的弧形结构与沉积方向垂直,利于增强h
+
钝化处理的效果,且该平滑的弧形结构上沉积的本征型非晶硅膜层和掺杂型非晶硅膜层的厚度会显著大于金字塔斜面上本征型非晶硅膜层和掺杂型非晶硅膜层的厚度;步骤六,采用pvd沉积透明导电膜层;步骤七,采用丝网印刷低温银浆,制作金属电极。
37.以上实施例采用所述一种铸锭晶硅异质结太阳能电池及其制作方法,制作的铸锭单晶硅片衬底圆滑处理后,金字塔形状底部的平滑弧形结构sem图像如图3所示,图中圈a内标示平滑弧形结构连接相邻的两个金字塔形状;铸锭单晶硅片衬底经pecvd钝化后的pl图像如图4所示,相邻晶粒边界位置因钝化改善后,pl图像上晶粒边界位置的黑区明显较少。
38.对比例:
39.为进一步说明本发明一种铸锭晶硅异质结太阳能电池及其制作方法的实质效果,提供一对比例未采用本发明制作的铸锭晶硅异质结太阳能电池结构如图5和图6所示,其结构如下:n型掺杂的铸锭单晶硅片衬底8内含有多个生长方向不同的晶粒(8-a/8-b/8-c),衬底的表面设置有连续交替的金字塔形状绒面,其中,相邻晶粒8-b与晶粒8-c边界位置c的金字塔形状底部有尖锐夹角结构相连,相邻晶粒1-a与晶粒1-b边界位置d的金字塔形状底部有尖锐夹角结构相连(下文仅对相邻晶粒边界位置c进行结构说明);设置在绒面上的本征型非晶硅膜层9和10,其中,相邻晶粒1-b与晶粒1-c边界位置c的金字塔形状底部的尖锐夹角结构上的本征非晶硅膜层10的厚度d5比金字塔斜面上的本征型非晶硅膜层10的厚度d6更小;设置在本征型非晶硅膜层10之上的n型掺杂非晶硅膜层11,其中,相邻晶粒8-b与晶粒
8-c边界位置c的金字塔形状底部的尖锐结构上的n型掺杂型非晶硅膜层11的厚度d7比金字塔斜面上的n型掺杂型非晶硅膜层11的厚度d8更小;设置在本征型非晶硅膜层10之上的p型掺杂的非晶硅膜层12;设置在n型掺杂型非晶硅膜层11和p型掺杂型非晶硅膜层12之上的透明导电膜层13;设置在透明导电膜层13之上的金属电极14。
40.对比例的制作方法如下:步骤一、对n型掺杂的铸锭单晶硅片衬底使用氨水和双氧水的混合液在70℃以上的水溶液中浸泡清洗,以去除有机污染,烘干后采用化学气相沉积工艺(lpcvd/pecvd/hot wire cvd),在衬底表面沉积磷硅氧的混合层,并在700-1000℃的高温下退火,之后以hf溶液去除表面混合层,以去除衬底内部杂质及消除部分缺陷;步骤二,采用碱性蚀刻液对铸锭单晶硅片衬底进行各向异性的蚀刻,使表面产生连续接替的金字塔形状的绒面,由于铸锭单晶硅片衬底中存在不同生长方向的晶粒,相邻晶粒边界位置金字塔底部易形成尖锐的夹角结构;步骤三,采用hf溶液去除表面的氧化层;步骤四,采用pecvd沉积本征型非晶硅膜层和掺杂型非晶硅膜层,其中金字塔底部尖锐夹角结构不利于h
+
离子的钝化处理和非晶硅膜层的沉积,h
+
离子的处理效果不良,且底部尖锐夹角位置沉积的本征型非晶硅膜层和掺杂型非晶硅膜层的厚度会显著小于金字塔斜面上本征型非晶硅膜层和掺杂型非晶硅膜层的厚度;步骤五,采用pvd沉积透明导电膜层;步骤六,采用丝网印刷低温银浆,制作金属电极。
41.以上对比例制作的铸锭单晶硅片衬底经制绒后,未经过圆滑处理,金字塔形状底部的尖锐夹角结构sem图像如图7所示,图中圈b内标示尖锐夹角结构连接相邻的两个金字塔形状;铸锭单晶硅片衬底经pecvd钝化后的pl图像如图8所示,相邻晶粒边界位置因钝化不良,pl图像上晶粒边界位置的黑区明显较多,且连续分布。
42.以上所述仅为本发明的较佳实施例而已,并不用以限制本发明,凡在本发明的精神和原则之内所作的任何修改、等同替换和改进等,均应包含在本发明的保护范围之内。