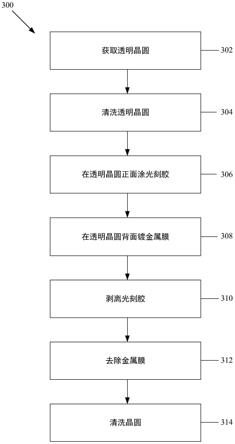
[0001]
本申请涉及表面声波滤波器制造工艺,并具体涉及一种用于表面声波滤波器的具有背面金属层的晶圆及其制造方法。
背景技术:[0002]
随着光刻技术的发展,对晶圆对准和曝光系统的精度提出更高要求。为缩短精确对准的随机搜索标记位置的时间和提高晶圆利用率,必须在精确对准之前的晶圆传输阶段增加预对准工序,才能保证在较短的时间内将晶圆精确对准。光刻机中晶圆预对准装置的主要作用是,在调平、光刻工序前,对晶圆进行预对准,尽量缩小晶圆从晶圆盒中由机械手取出再放到精对准工位的位置重复性误差。目前采用的预对准定位方法都采用线性ccd(charge coupled device,电荷耦合器件)传感器检测晶圆边缘及晶圆中心。另外,在表面声波滤波器制造工艺中,一般对晶圆进行自动抓取,可升降旋转的机械手臂将晶圆送到上料台,而后取片设备向晶圆出发射光束,并以此判断上料台上是否存在晶圆、晶圆是否放平,确定晶圆的位置和大小。然而,当前表面声波滤波器制造工艺中通常使用单面或双面抛光的、具有一定透明度的晶圆。这些透明晶圆(诸如,采用铌酸锂、钽酸锂等透明材料的单晶压电基板)无法反射光束,会导致无法进行平边检测和晶圆中心定位,造成光刻对偏和无法对准,无法进行下一步对准工艺,导致生产停机或降低产品良率。另外,由于透明晶圆无法反射光束,因此取片设备无法判断上料台上是否存在晶圆、晶圆是否放平,无法确定晶圆的位置和大小,这将导致取片设备无法取片而造成生产停机。参见图1,示出了对透明压电晶圆进行取片操作的示意图。如图1中所图示,在对透明压电晶圆进行取片操作时,取片设备中的光源102向上料台104晶圆放置处(放置有透明晶圆106,透明晶圆106具体地如图1左下角处所示)发射光束,然而,由于透明晶圆无法反射光线,因此光线会穿透该透明晶圆106到达取片设备的光线接收装置108(例如,光敏二极管),造成取片设备无法判断上料台上是否存在晶圆。
[0003]
另外,在表面声波滤波器制造工艺中,诸如压电过程之类的中间过程会在晶圆表面产生表面电荷,目前采用的制造工艺无法有效地将所产生的表面电荷传导离开晶圆,因此会引发热释电效应。
[0004]
再加上由于晶圆厚度较小、强度不高,目前采用的表面声波制造工艺中对透明晶圆进行操作的过程极易发生晶圆破裂。
技术实现要素:[0005]
在第一方面中,本发明提供一种制造用于表面声波滤波器的具有背面金属层的晶圆的方法,所述方法包括:获取透明晶圆;对所述透明晶圆进行清洗;在所述透明晶圆的正面涂光刻胶;在所述透明晶圆的背面镀金属膜;以及剥离在所述透明晶圆的所述正面涂覆的所述光刻胶,以制成所述具有背面金属层的晶圆,其中,所述金属膜在利用所述具有背面
金属层的晶圆完成相应操作之后被去除。
[0006]
进一步地,根据第一方面所述的方法可任选地包括:其中,所述光刻胶在对所述具有背面金属层的晶圆的相应操作完成之后被去除。进一步地,根据第一方面所述的方法可任选地包括:其中,所述金属膜的厚度为50纳米至200纳米。进一步地,根据第一方面所述的方法可任选地包括:其中,所述金属膜采用钛或镍制成。进一步地,根据第一方面所述的方法可任选地包括:其中,在所述晶圆的背面镀金属膜采用蒸镀或磁控溅射来实现。进一步地,根据第一方面所述的方法可任选地包括:其中,所述金属膜被去除通过反应离子刻蚀或感应耦合电浆刻蚀来实现。
[0007]
在第二方面中,本发明提供了一种用于表面声波滤波器的具有背面金属层的晶圆,所述具有背面金属层的晶圆包括:透明晶圆;以及背面金属层,所述背面金属层通过在所述透明晶圆的背面镀金属膜来形成,其中,所述背面金属层在利用所述具有背面金属层的晶圆完成相应操作之后被去除。
[0008]
进一步地,根据第二方面所述的具有背面金属层的晶圆可任选地包括:其中,所述光刻胶在对所述具有背面金属层的晶圆的相应操作完成之后被去除。进一步地,根据第一方面所述的具有背面金属层的晶圆可任选地包括:其中,所述金属膜的厚度为50纳米至200纳米。进一步地,根据第一方面所述的具有背面金属层的晶圆可任选地包括:其中,所述金属膜采用钛或镍制成。进一步地,根据第一方面所述的具有背面金属层的晶圆可任选地包括:其中,在所述晶圆的背面镀金属膜采用蒸镀或磁控溅射来实现。进一步地,根据第一方面所述的具有背面金属层的晶圆可任选地包括:其中,所述金属膜被去除通过反应离子刻蚀或感应耦合电浆刻蚀来实现。
[0009]
本发明提供了一种用于表面声波滤波器的具有背面金属层的晶圆及其制造方法。通过在透明晶圆的背面镀金属膜,可以显著提高晶圆的反光性,有利于光刻对准,提高良率;提高自动取片成功率,防止产线停机;晶圆背面存在一层金属膜,由于金属电导率较高,因此可以将表面电荷导出,抑制热释电效应;此外,通过在晶圆背面镀金属膜,提高了晶圆结构强度,防止表面声波滤波器制造过程中晶圆破裂;金属导热率较高还可以提高器件散热效果。
附图说明
[0010]
为了提供对本发明及本发明的特征和优点的更完整的理解,结合所附附图进行下列描述,其中,相同或相应的附图标记表示相同或相应的部分,其中:
[0011]
图1是对透明压电晶圆进行取片操作的示意图;
[0012]
图2是对非透明压电晶圆进行取片操作的示意图;
[0013]
图3是具有背面金属层的晶圆的制造过程及后续处理过程的示意图;
[0014]
图4是在透明晶圆正面涂光刻胶的示意图;
[0015]
图5是利用蒸镀原理在透明晶圆背面镀金属膜的示意图;
[0016]
图6是利用磁控溅射原理在透明晶圆背面镀金属膜的示意图;
[0017]
图7是利用反应离子刻蚀来去除所镀金属膜的示意图;
[0018]
图8是利用感应耦合电浆刻蚀来去除所镀金属膜的示意图;以及
[0019]
图9是湿法剥离光刻胶过程中光刻胶状态变化的示意图。
具体实施方式
[0020]
本发明提供了一种用于表面声波滤波器的具有背面金属层的晶圆。应当领会,本文所称的晶圆的“正面”指示在表面声波滤波器制造工艺中用于镀idt(叉指换能器)电极的面,相应地,本文所称的晶圆的“背面”指示与所述“正面”相对的面。本文中所称的“透明晶圆”指示当前表面声波滤波器制造工艺中通常使用的单面或双面抛光的、具有一定透明度的晶圆。
[0021]
现在参考图2,图2示意性地图示出根据本发明的具有背面金属层的晶圆取片操作。如图所示,在对具有背面金属层的晶圆进行取片时,取片设备的led光源202向上料台204的晶圆放置处(放置有具有背面金属层的晶圆206,该具有背面金属层的晶圆206具体地如图2下方所示)发射光束,由于具有背面金属层的晶圆206所镀的金属膜对光线具有反射作用,取片设备的光线接收装置208无法接收到晶圆206区域的光线,由此,取片设备能够计算出晶圆206的大小及位置从而完成取片操作。类似地,通过利用具有背面金属层的晶圆,光刻机可以进行平边检测,通过选取外周某几个点的位置计算出晶圆中心的位置,从而完成预对准准备工作。
[0022]
图3图示出根据本发明的具有背面金属层的晶圆的制造及后续处理过程300。如图3所示,具有背面金属层的晶圆的制造过程开始于框302,在框302处,获取表面声波滤波器制造工艺中使用的透明晶圆。随后,过程进行至框304,在304处,对所获取的透明晶圆进行清洗。随后,过程进行至框306,在框306处,在清洗后的透明晶圆的正面涂覆光刻胶,以防止损伤晶圆。在对透明晶圆的正面涂覆光刻胶后,过程进行至框308,在框308处,在该透明晶圆的背面镀上一层金属膜。该金属膜厚为50纳米-200纳米。优选地,金属膜的材料可以是钛(ti)、镍(ni)。作为非限制性实施例,镀金属膜可以采用蒸镀或磁控溅射等方法。此外,在透明晶圆背面形成的金属层的形状可以是任意的。在框310处,最后,对框306处所描述的在该透明晶圆的正面所涂覆的光刻胶进行剥离,从而制成具有背面金属层的晶圆。任选地,为便于利用此种具有背面金属层的晶圆进行诸如取片、光刻等之类的后续操作,在对光刻胶进行剥离之后,可进一步对该具有背面金属层的晶圆进行清洗。
[0023]
在完成上述制造过程后,可利用所获得的此种具有背面金属层的晶圆来进行取片、在此种具有背面金属层的晶圆的正面进行光刻等之类的上文所描述的表面声波滤波器制造过程。在利用具有背面金属层的晶圆完成相应的取片、光刻等操作后,如图3中的框312所描绘,需要对上文如框308处所描述的在透明晶圆的背面所镀的金属膜进行去除。作为非限制性实施例,可通过反应离子刻蚀和感应耦合电浆刻蚀等方法来完成框312所示的金属膜去除。优选地,为防止去除背面金属膜损坏晶圆正面形成的电极,可以在去除金属膜前在正面电极上涂覆光刻胶作为保护层,并在去除金属膜之后利用干法去胶剥离该光刻胶。任选地,为了方便后续表面声波滤波器的制造过程,如框314处所描绘,最后可进一步对晶圆进行清洗。
[0024]
作为非限制性实施例,图4图示出通过旋转涂胶在透明晶圆的正面涂覆光刻胶的过程。在涂胶时,如图4的(a)部分所示,首先将透明晶圆吸附在真空卡盘401上,随后将液态光刻胶滴注到该透明晶圆的中心。然后,如图4的(b)部分所示,真空卡盘401低速旋转(转速通常为200到500rpm),利用离心力使光刻胶在透明晶圆的正面扩散开。随后,如图4的(c)部分所示,真空卡盘401加速旋转(转速通常在3500到5000rpm之间),甩掉多余的光刻胶。最
后,如图4的(d)部分所示,使透明晶圆正面残余的溶剂挥发,最终得到均匀的光刻胶涂层。
[0025]
作为非限制性实施例,图5图示出通过蒸镀在透明晶圆背面镀金属膜的示意图。如图5所图示,利用真空蒸镀通过以下步骤在透明晶圆背面镀金属膜:(1)加热坩埚503,使坩埚503中的金属蒸发源由凝聚相转变为气相,并达到饱和蒸汽压;(2)金属蒸汽由坩埚503传输至载片盘501上放置的透明晶圆502(如图5中的向上箭头所示);(3)由于透明晶圆502背面的温度远低于蒸发源温度,因此金属蒸汽在透明晶圆502的背面直接由气相转变为固相,凝结成金属膜;(4)打开高真空阀505,通过高真空泵506以及机械泵507抽走工艺腔(钟罩)504中多余的金属蒸汽。
[0026]
替代地,作为非限制性实施例,图6图示出通过磁控溅射在透明晶圆背面镀金属膜的示意图。如图6所示,利用溅射现象将金属靶材601上的金属原子溅射出来,并沉积到透明晶圆602的背面形成金属膜。溅射的基本步骤如下:(1)在高真空等离子体中产生正氩离子(如图6中所示,ar
+
),并向具有负电势的金属靶材601加速;(2)在加速过程中ar
+
离子获得动能,并轰击金属靶材601;(3)通过物理轰击,ar
+
离子从金属靶材601上撞击出金属原子603(如图6中黑色圆所示);(4)被撞击出的金属原子603迁移到透明晶圆601的背面,并凝聚形成金属膜;(5)额外材料被真空泵抽走(未示出)。
[0027]
作为非限制性实施例,图7图示出利用反应离子刻蚀(reactive ion etching,rie)来去除所镀金属膜。在反应离子刻蚀中,通入气体701(如图7上方的进气箭头710所示),气体701在射频电源704的作用下放电产生的等离子体702中有大量化学活性的气体离子,这些气体离子与晶圆703背面的金属膜相互作用产生化学反应,生成可挥发产物。这些挥发产物随真空抽气系统被排走(如图7下方的排气箭头720所示)。随着金属膜表层的“反应-剥离-排放”的周期循环,该金属膜被逐层刻蚀到指定深度。除了表面化学反应外,气体701产生的带能量的离子经过电场加轰击晶圆703背面的金属膜的表面也会使其表面原子溅射,产生一定的刻蚀作用,进而使表面受损,提高被刻蚀的金属膜的表面活性,加速与气体离子的反应速度,从而获得较高的刻蚀速度。替代地,图8图示出利用感应耦合电浆(inductively coupled plasma,icp)刻蚀来去除所镀金属膜。如图8所示,反应气体801进入由射频电源802、icp线圈803、以及电浆804形成的电子区域,通过电感耦合等离子体辉光放电将反应气体801分解产生具有强化学活性的等离子或等离子体(如图8中805所示,正离子与杂散电子重组形成活化的中性粒子)。这些等离子或等离子体在电场的加速作用下移动到晶圆806的背面,既在晶圆806的背面进行化学反应生成挥发性气体,又有一定的物理刻蚀作用,由此来去除根据本发明的具有背面金属层的晶圆的金属膜。
[0028]
剥离光刻胶的方式一般有湿法去胶和干法去胶两种。干法去胶一般采用等离子体刻蚀去胶。干法去胶刻蚀时,在去胶机内通入刻蚀气体o2,等离子体的活化氧使得光刻胶很快氧化,生成co2、co、h2o等挥发性成分,达到去胶的目的。湿法去胶是目前采用的较为普遍的去胶方法。湿法去胶采用溶液浸泡的方式将光刻胶剥离。作为非限制性实施例,图9示意性地图示出湿法剥离光刻胶的过程中光刻胶的状态变化。如图9中所图示,首先将根据本发明的正面具有光刻胶的晶圆放置到剥离液中,如901所示,此时光刻胶为固态。随后,如902所示,光刻胶在剥离液中形成溶胀的胶状物,此时光刻胶为胶态。最后,如903所示,光刻胶被溶解的聚合物分子分散至剥离液中,从而使得光刻胶从晶圆被剥离,此时光刻胶为液态。