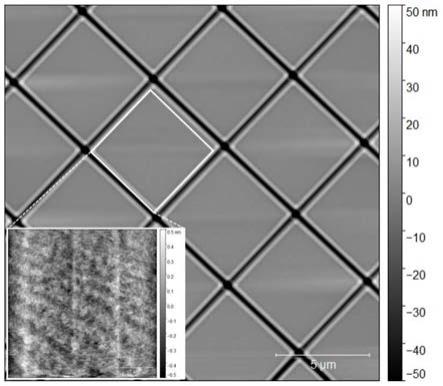
[0001]
本发明属于材料领域。具体地,本发明涉及一种图形硅衬底-硅锗薄膜复合结构及其制备方法和应用。
背景技术:[0002]
信息时代的高速发展产生了庞大的数据运算和处理需求,对能够进行数据运算和处理的微电子和光电子器件的性能提出了更高的要求。硅锗合金作为一种重要的半导体材料,已经广泛地应用于移动通信、卫星通讯、射频技术、自动化技术和光电子等领域。由于硅锗具有优于纯硅的良好特性,并且工艺上与硅工艺兼容,采用硅锗合金及si/gesi异质结所制作的器件性能优越。硅锗合金制作成器件首先需要解决材料问题,即在硅基衬底上外延生长高质量及高平整度的硅锗薄膜材料。
[0003]
现有技术中,大多使用成分渐变的方法制备硅锗薄膜材料。这种方法通过生长数微米厚的渐变层来释放硅锗合金和硅衬底之间晶格失配产生的应力。同时,生长过程产生的穿透位错在应变硅量子阱器件中对载流子形成散射,从而降低了载流子迁移率,影响器件性能。为了获得高迁移的应变硅层,需要高质量,高平整度的硅锗薄膜材料。
[0004]
日本课题组(silicon isotope technology for quantum computing s.miyamoto and k.m.itoh,2018)利用气源分子束外延生长近3μm厚的锗硅薄膜,表面粗糙度大于1nm,后续采用化学机械抛光工艺降低粗糙度到0.1nm。现有这种技术获得的硅锗薄膜材料存在以下缺点:一方面,生长获得的硅锗薄膜材料的结构复杂。常用的化学气相沉积(cvd)方法或者气源分子束外延(mbe)生长的硅锗薄膜需要控制成分渐变且外延厚度3μm以上。另一方面,生长获得的硅锗薄膜材料的平整度差,cvd生长的硅锗薄膜制作器件需要额外的化学机械抛光(cmp)工艺。
技术实现要素:[0005]
本发明的一个目的是提供一种具有高质量及高平整度的图形硅衬底-硅锗薄膜复合结构。本发明的另一目的是提供制备本发明的图形硅衬底-硅锗薄膜复合结构的方法。本发明的又一目的是提供本发明的图形硅衬底-硅锗薄膜复合结构的应用。
[0006]
本发明的上述目的是通过以下技术方案实现的。
[0007]
在本发明上下文中,术语“方块状平台”包括正方体和长方体。
[0008]
在本发明上下文中,术语“硅锗/硅超晶格层”包括交替生长的硅锗层和硅层。在本发明中,硅锗/硅超晶格层的起始层可以是硅锗层,也可以是硅层。
[0009]
第一方面,本发明提供一种图形硅衬底-硅锗薄膜复合结构,其包括具有图形结构的硅衬底、位于所述硅衬底上的硅锗缓冲层、位于所述硅锗缓冲层上的硅锗/硅超晶格层,以及位于所述硅锗/硅超晶格层上的硅锗薄膜层,其中所述硅锗/硅超晶格层包括交替生长的硅锗层和硅层。
[0010]
优选地,在本发明所述的图形硅衬底-硅锗薄膜复合结构中,所述硅衬底的晶面为
(001)晶面。
[0011]
优选地,在本发明所述的图形硅衬底-硅锗薄膜复合结构中,所述图形结构包括在平行于所述硅衬底的[110]方向上最大尺寸不大于5μm且在垂直于所述硅衬底的[110]方向上最大尺寸不大于5μm的图形。
[0012]
优选地,在本发明所述的图形硅衬底-硅锗薄膜复合结构中,所述图形结构包括在平行于所述硅衬底的[110]方向上最大尺寸为4.3μm-5μm,更优选为4.8μm-5μm,且在垂直于所述硅衬底的[110]方向上最大尺寸为4.3μm-5μm,更优选为4.8μm-5μm的图形。
[0013]
优选地,在本发明所述的图形硅衬底-硅锗薄膜复合结构中,所述图形结构包括多个相同或者不同的图形。
[0014]
优选地,在本发明所述的图形硅衬底-硅锗薄膜复合结构中,所述图形结构包括周期性排列的或者非周期性排列的多个图形。
[0015]
优选地,在本发明所述的图形硅衬底-硅锗薄膜复合结构中,所述图形结构的相邻图形之间的上表面间距不小于200nm。
[0016]
优选地,在本发明所述的图形硅衬底-硅锗薄膜复合结构中,所述图形结构中的图形是方块状平台、圆柱体平台或者截头锥体平台。
[0017]
优选地,在本发明所述的图形硅衬底-硅锗薄膜复合结构中,所述方块状平台的侧壁面的切线与水平面的夹角为80-90
°
,更优选为85-90
°
。
[0018]
优选地,在本发明所述的图形硅衬底-硅锗薄膜复合结构中,所述硅锗缓冲层的厚度为100-400nm,更优选为200-300nm。
[0019]
优选地,在本发明所述的图形硅衬底-硅锗薄膜复合结构中,所述硅锗缓冲层中锗的含量为20wt%-40wt%,更优选为25wt%-30wt%。
[0020]
优选地,在本发明所述的图形硅衬底-硅锗薄膜复合结构中,所述硅锗/硅超晶格层包括n层硅锗层、n层或n
±
1层硅层,其中n为5-40,更优选为30-40。
[0021]
优选地,在本发明所述的图形硅衬底-硅锗薄膜复合结构中,所述硅锗/硅超晶格层中硅锗层的厚度为5-10nm,更优选为8-10nm。
[0022]
优选地,在本发明所述的图形硅衬底-硅锗薄膜复合结构中,所述硅锗/硅超晶格层中硅层的厚度为5-10nm,更优选为8-9nm。
[0023]
优选地,在本发明所述的图形硅衬底-硅锗薄膜复合结构中,在所述硅锗/硅超晶格层的硅锗层中,锗的含量为20wt%-40wt%,更优选为25wt%-30wt%。
[0024]
优选地,在本发明所述的图形硅衬底-硅锗薄膜复合结构中,所述硅锗薄膜层的厚度为100-400nm,更优选为200-300nm。
[0025]
优选地,在本发明所述的图形硅衬底-硅锗薄膜复合结构中,所述硅锗薄膜层中锗的含量为20wt%-40wt%,更优选为25wt%-30wt%。
[0026]
优选地,在本发明所述的图形硅衬底-硅锗薄膜复合结构中,所述硅锗薄膜层的表面粗糙度为0.1-0.5nm,更优选为0.1-0.2nm。
[0027]
第二方面,本发明提供本发明的图形硅衬底-硅锗薄膜复合结构的制备方法,其包括以下步骤:
[0028]
(1)在硅衬底上形成图形结构;
[0029]
(2)在具有图形结构的硅衬底上外延生长硅锗缓冲层;
[0030]
(3)在所述硅锗缓冲层上交替外延生长硅锗层和硅层,以形成所述硅锗/硅超晶格层;
[0031]
(4)在所述硅锗/硅超晶格层上外延生长硅锗薄膜层。
[0032]
优选地,在本发明所述的制备方法中,所述步骤(1)中的在硅衬底上形成图形结构是通过包括以下步骤的方法进行的:
[0033]
在硅(001)衬底表面利用等离子增强化学气相沉积方法生长sio2掩模;
[0034]
利用深紫外光刻技术在所述sio2掩膜上沿着与硅衬底的[110]方向平行和垂直的两个方向上构筑凹槽结构;
[0035]
通过反应离子刻蚀技术在所述凹槽结构上制备图形结构,然后利用氢氟酸移除所述sio2掩膜。
[0036]
优选地,在本发明所述的制备方法中,所述步骤(2)中外延生长硅锗缓冲层是通过包括如下步骤的方法进行的:
[0037]
采用分子束外延生长技术在具有图形结构的硅衬底上于320-350℃外延生长硅锗缓冲层。
[0038]
优选地,在本发明所述的制备方法中,所述步骤(3)中的外延生长硅锗/硅超晶格层是通过包括如下步骤的方法进行的:
[0039]
采用分子束外延生长技术在所述硅锗缓冲层上于320-350℃外延生长硅锗/硅超晶格结构。
[0040]
优选地,在本发明所述的制备方法中,所述步骤(4)中的外延生长硅锗薄膜层是通过包括如下步骤的方法进行的:
[0041]
采用分子束外延生长技术在所述硅锗/硅超晶格层上外延生长硅锗薄膜层。
[0042]
优选地,在本发明所述的制备方法中,所述步骤(4)中的外延生长硅锗薄膜层是通过包括如下步骤的方法进行的:
[0043]
采用分子束外延生长技术在所述硅锗/硅超晶格层上于350-400℃外延生长100-150nm厚的硅锗薄膜层,然后于500-600℃外延生长50-100nm厚的硅锗薄膜层。
[0044]
第三方面,本发明提供本发明的图形硅衬底-硅锗薄膜复合结构在应变硅器件中的应用。
[0045]
本发明具有如下有益效果:
[0046]
本发明提供的图形硅衬底-硅锗薄膜复合结构,其穿透位错密度低且表面粗糙度低。基于所述硅锗薄膜层生长的应变硅器件,可有效减少缺陷对载流子的散射,从而提高载流子迁移率。
附图说明
[0047]
以下,结合附图来详细说明本发明的实施方案,其中:
[0048]
图1为本发明实施例1的步骤(1)中制备的表面具有周期性的方块状平台的硅衬底的原子力显微镜图;
[0049]
图2为本发明实施例1的步骤(1)中制备的方块状平台的侧壁截面的扫描电子显微镜图;
[0050]
图3为本发明实施例1的步骤(2)中生长的硅锗缓冲层的表面原子力显微镜图;插
图为白色方框内的方块状平台的上表面的原子力显微镜图;
[0051]
图4为本发明实施例1的步骤(3)中生长的硅锗/硅超晶格层的表面原子力显微镜图;插图为白色方框内的方块状平台的上表面的原子力显微镜图;
[0052]
图5为本发明实施例1的步骤(4)中生长的硅锗薄膜层的表面原子力显微镜图;插图为白色方框内的方块状平台的上表面的原子力显微镜图;
[0053]
图6为对比例1生长的硅锗薄膜层的表面原子力显微镜图;
[0054]
图7为对比例2生长的硅锗薄膜层的表面原子力显微镜图;
[0055]
图8为对比例3生长的硅锗薄膜层的表面原子力显微镜图;
[0056]
图9为本发明实施例1制备的图形硅衬底上的硅锗薄膜层的横截面低倍透射电子显微镜图(左)和高倍透射电子显微镜图(右)。
具体实施方式
[0057]
下面结合具体实施方式对本发明进行进一步的详细描述,给出的实施例仅为了阐明本发明,而不是为了限制本发明的范围。
[0058]
实施例1
[0059]
(1)在硅(100)衬底表面利用等离子增强化学气相沉积方法,生长sio2掩模。在所述等离子增强化学气相沉积方法中,采用sih4和n2o作为气源,并且在350℃下进行气相沉积。然后,利用深紫外光刻技术,在sio2掩膜上沿着与硅衬底的[110]方向平行和垂直的两个方向上构筑凹槽结构,以形成上表面为5μm的正方形且深度为450nm的长方体。在深紫外光刻技术中,采用的光源的波长为248nm。然后,通过反应离子刻蚀技术在所述凹槽结构上制备周期性的方块状平台。在所述反应离子刻蚀技术中,采用sf6和o2作为气源。然后利用氢氟酸移除所述sio2掩膜。
[0060]
(2)然后,采用分子束外延生长技术在具有周期性的方块状平台的硅(001)衬底上于350℃外延生长200nm硅锗缓冲层。在所述硅锗缓冲层中,锗的含量为30wt%。
[0061]
(3)接着,采用分子束外延生长技术在硅锗缓冲层上于350℃依次交替生长硅锗层和硅层,以形成硅锗/硅超晶格层。所述硅锗/硅超晶格层包括35层硅锗和35层硅层。在所述硅锗/硅超晶格层的硅锗层中,锗的含量为30wt%。硅锗层的厚度为9nm,硅层的厚度为9nm。
[0062]
(4)随后,采用分子束外延生长技术在硅锗/硅超晶格层上于350℃继续生长150nm硅锗薄膜层。在所述硅锗薄膜层中,锗的含量为30wt%。然后,采用分子束外延生长技术在150nm厚的硅锗薄膜层上于550℃继续生长50nm硅锗薄膜层。
[0063]
对比例1
[0064]
按照与上述实施例1相同的方法制备图形硅衬底-硅锗薄膜复合结构,不同之处在于没有生长硅锗/硅超晶格层。
[0065]
对比例2
[0066]
按照与上述实施例1相同的方法,不同之处在于硅衬底是不具备图形结构的平整的衬底,来制备平整硅衬底-硅锗薄膜复合结构。
[0067]
对比例3
[0068]
按照与上述实施例1相同的方法制备图形硅衬底-硅锗薄膜复合结构,不同之处在于利用深紫外光刻技术,在sio2掩膜上沿着与硅衬底的[110]方向平行和垂直的两个方向
上构筑凹槽结构,以形成上表面为10μm的正方形且深度为450nm的长方体。
[0069]
产品表征
[0070]
图1为本发明实施例1的步骤(1)中制备的表面具有周期性的方块状平台的硅衬底的原子力显微镜图。图1示出了实施例1的步骤(1)制备了具有周期性的方块状平台的硅衬底。方块状平台的上表面为正方形。正方形的边长为5000nm且方块状平台的间距为200nm。
[0071]
图2为本发明实施例1的步骤(1)中制备的方块状平台的侧壁截面的扫描电子显微镜图。图2示出了实施例1的步骤(1)制备的方块状平台的图形硅衬底的侧壁倾角为85
°
且方块状平台的深度为450nm。
[0072]
图3为本发明实施例1的步骤(2)中生长的硅锗缓冲层的表面原子力显微镜图。插图为白色方框内的方块状平台的上表面的原子力显微镜图。图3的插图示出了硅锗缓冲层的表面粗糙度为0.146nm。
[0073]
图4为本发明实施例1的步骤(3)中生长的硅锗/硅超晶格层的表面原子力显微镜图。插图为白色方框内的方块状平台的上表面的原子力显微镜图。图4的插图示出了硅锗/硅超晶格层的表面粗糙度为0.162nm。
[0074]
图5为本发明实施例1的步骤(4)中生长的硅锗薄膜层的表面原子力显微镜图。插图为白色方框内的方块状平台的上表面的原子力显微镜图。图5的插图示出了硅锗薄膜层的表面粗糙度为0.163nm,并且没有观察到穿透位错。
[0075]
图6为对比例1生长的硅锗薄膜层的表面原子力显微镜图。图6示出了对比例1制备的硅锗薄膜层的表面粗糙度为0.741nm。相对于具有硅锗/硅超晶格层的硅锗薄膜层,对比例1制备的硅锗薄膜层的表面更加粗糙。图6的白圈示出了表面存在穿透位错。图6表明生长硅锗/硅超晶格层可以降低硅锗薄膜层的表面粗糙度,同时提高硅锗薄膜层的晶体质量。
[0076]
图7为对比例2生长的硅锗薄膜层的表面原子力显微镜图。图7示出了对比例2制备的硅锗薄膜层的表面粗糙度为1.185nm。图7的白圈示出了表面存在穿透位错。图7表明具有图形的硅衬底有助于降低硅锗表面粗糙度,同时提高硅锗薄膜层的晶体质量。
[0077]
图8为对比例3生长的硅锗薄膜层的表面原子力显微镜图。图8示出了对比例3制备的硅锗薄膜层的表面粗糙度为0.945nm。图8的白圈示出了表面存在穿透位错。当硅衬底上的图形尺寸大于5μm时,在该衬底上外延生长的硅锗薄膜层会产生穿透位错,进而降低了硅锗薄膜层的晶体质量。
[0078]
图9为本发明实施例1制备的图形硅衬底上的硅锗薄膜层的横截面低倍透射电子显微镜图(左)和高倍透射电子显微镜图(右)。低倍透射电子显微镜图未观察到明显的缺陷。高倍透射电子显微镜图显示硅锗薄膜结构非常完美,没有位错或者堆垛层错等缺陷。