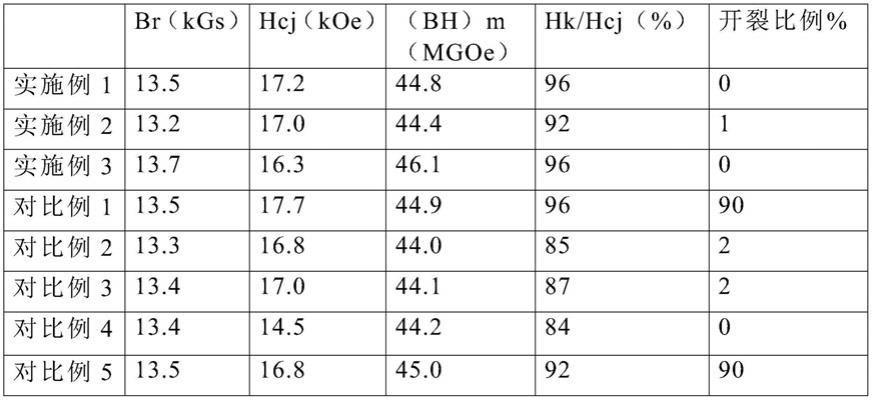
[0001]
本发明属于稀土永磁材料制备领域,涉及一种高性能磁环及其制备方法。
背景技术:[0002]
传统的永磁电机的永磁部件采用磁瓦拼接环,其采用拼装方式制备,工艺较为复杂,且存在几何中心与磁场中心不重合、表磁分布成锯齿状等缺点。磁环具有结构紧凑、装配简单、输出波形稳定等优势,显著降低电机重量和能耗,提高运行稳定性。为此,高性能永磁电机中的永磁部件正逐渐由传统的磁瓦拼接环转变为整体磁环。磁环多采用粉末冶金烧结制备而成,但是烧结磁环制备存在两个技术难点:一是磁环在烧结致密化过程中,由于磁环收缩的各向异性极易导致产品开裂;二是磁环在取向成型过程中采用辐射取向,取向磁场低,磁环磁性能要比相同粉料正常烧结磁体低很多。针对这两个技术难点,目前采用以下方法制备烧结磁环:(1)采用铸锭烧结,通过铸锭烧结可以很好地解决磁环开裂现象,但是制备的磁环磁性能较低;(2)采用铸片烧结,通过铸片烧结可以获得较高性能的磁环,但是制备的磁环易开裂,此时通过将粉末粒度磨粗的方式可以有效缓解磁环的开裂,但是该方案会使得磁粉晶粒为多晶状态,导致磁性能下降。因此,目前磁环由于易开裂以及磁性能相对较低而限制其市场应用。
技术实现要素:[0003]
本发明针对现有技术存在的不足,提供一种新型的高性能磁环的制备方法,获得的磁环具有优异的磁性能且不易开裂,可满足高端应用领域的需求。
[0004]
本发明提供的一种高性能磁环的制备方法,包括以下步骤:
[0005]
(1)按照磁环合金成分配置原料,将配置好的原料进行熔炼,浇铸甩带得平均厚度为0.2~0.4mm的速凝片;
[0006]
(2)速凝片进行高温热处理;
[0007]
(3)高温热处理后的速凝片经过氢破碎,得粗破碎粉末,再经过脱氢热处理,使得粗破碎粉末氢含量≤600ppm,然后将粗破碎粉末送入气流磨机内进行磨粉,得到气流磨磁粉;
[0008]
(4)往气流磨磁粉中添加润滑剂并搅拌2~6h,搅拌后进入磁环磁场压机进行取向成型,然后等静压处理;
[0009]
(5)高温烧结、冷却以及回火热处理。
[0010]
作为优选,所述磁环合金成分为r
x
t
y
m
z
b
(1-x-y-z)
,其中r为nd、pr、la、ce、ga、ho、dy和tb中的一种或多种,t为fe和co,fe和co的质量比为(40~100):1,m为cu、al、ga中的一种或多种以及nb、zr中的一种或两种,x为29~35wt%,y为55~70wt%,z为0.1~2wt%。
[0011]
作为优选,步骤(1)中的熔炼温度为1450~1500℃,浇铸温度为1400~1450℃,铜辊转速为1.0~1.5m/s。
[0012]
作为优选,步骤(2)中高温热处理的温度为800~1000℃,时间为20~30h。
[0013]
作为优选,经过步骤(2)的高温热处理后,速凝片的片状晶平均厚度为4~6μm。
[0014]
作为优选,步骤(3)的气流磨磁粉平均粒径与高温热处理后的速凝片的片状晶平均厚度相差0~0.5μm。
[0015]
作为优选,步骤(4)取向成型的磁场强度为0.8~1.0t,等静压处理压力为150~200mpa。
[0016]
作为优选,步骤(5)的高温烧结温度为1050~1100℃,烧结时间为4~6h。
[0017]
作为优选,步骤(5)的冷却步骤包括:先真空自冷至600~750℃,充惰性气体自冷到300~400℃,然后开风机风冷至室温。
[0018]
作为优选,所述步骤(5)的回火热处理包括:一级回火温度800~950℃,回火时间为2~4小时;二级回火温度450~580℃,回火时间为4~6小时。
[0019]
与现有技术相比,本发明具有以下有益效果:
[0020]
(1)本发明的速凝片在充氢破碎前,经过800~1000℃、时间为20~30h的高温热处理,速凝片的柱状晶长大为片状晶,控制片状晶的平均厚度为4~6μm,并在粉末破碎过程中,控制气流磨磁粉的平均粒径与速凝片的片状晶平均厚度相差0~0.5μm,制备大粒径气流磨磁粉可以降低磁环的开裂率,另一方面,气流磨磁粉的平均粒径小于或等于速凝片的片状晶平均厚度,保证气流磨磁粉为单晶颗粒,提高磁环磁性能;
[0021]
(2)本发明取向成型采用的磁场强度控制为0.8~1.0t,磁场强度不易过大,磁场强度过大导致漏磁后,部分磁粉提前被弱场取向而导致后续取向困难,降低磁体性能;
[0022]
(3)本发明高温烧结冷却采用多级冷却,多级冷却能避免快速冷却导致的材料内应力过大开裂,以及组织结构不均匀导致的性能下降。
具体实施方式
[0023]
下文将详细叙述本发明高性能磁环的制备方法,对于此时使用的技术用语或科学用语如果没有其他定义,则为本发明技术领域的技术人员通常理解的意思。
[0024]
在本文中,速凝片为本领域常规定义的速凝片,即速凝片为合金原料熔炼后浇铸到具有一定转速的铜辊上甩带获得。
[0025]
在本文中,速凝片的平均厚度定义为任意100片速凝片测量数据的平均值,测量工具可用游标卡尺或螺旋测微器等。
[0026]
在本文中,速凝片的片状晶的平均厚度定义为显微结构图中拉固定距离直线穿过片状晶个数的算术平均值:直线距离/片状晶个数。
[0027]
在本文中,气流磨磁粉的平均粒径定义为采用激光衍射散射法测得的体积基准的粒径分布的中值粒径。
[0028]
本发明实施例提供了一种高性能磁环的制备方法,包括以下步骤:
[0029]
(1)按照磁环合金成分配置原料,将配置好的原料进行熔炼,浇铸甩带得平均厚度为0.2~0.4mm的速凝片;
[0030]
(2)速凝片进行高温热处理;
[0031]
(3)高温热处理后的速凝片经过氢破碎,得粗破碎粉末,再经过脱氢热处理,使得粗破碎粉末氢含量≤600ppm,然后将粗破碎粉末送入气流磨机内进行磨粉,得到气流磨磁粉;
[0032]
(4)往气流磨磁粉中添加润滑剂并搅拌2~6h,搅拌后进入磁环磁场压机进行取向成型,然后等静压处理;
[0033]
(5)高温烧结、冷却以及回火热处理。
[0034]
所述磁环合金成分为r
x
t
y
m
z
b
(1-x-y-z)
,其中r为nd、pr、la、ce、ga、ho、dy和tb中的一种或多种,t为fe和co,fe和co的质量比为(40~100):1,在fe元素中掺杂适量co可有效提高磁环磁性能;m为cu、al、ga中的一种或多种以及nb、zr中的一种或两种;x为29~35wt%,y为55~70wt%,z为0.1~2wt%。
[0035]
步骤(1)中的熔炼温度为1450~1500℃,浇铸温度为1400~1450℃,铜辊转速为1.0m/s~1.5m/s。
[0036]
浇铸获得的速凝片未经高温热处理时,其柱状晶厚度约为3μm左右,在传统磁环的制备工艺中,为保证磁环不开裂,通常通过气流磨将磁粉磨粉至平均粒径约为5~6μm,但是磁粉磨粗一定程度上会导致磁粉为多晶粉末,降低磁环磁性能。
[0037]
本发明将浇铸获得的速凝片经过高温热处理,高温热处理的温度为800~1000℃,时间为20~30h,热处理在真空条件下进行,防止热处理导致速凝片氧化,真空度≤4*10-2
pa。速凝片经过高温热处理后,柱状晶长大为片状晶,通过控制高温热处理温度和时间使得片状晶的平均厚度为4~6μm。在粉末破碎过程中,本发明控制气流磨磁粉的平均粒径与速凝片的片状晶平均厚度相差0~0.5μm,优选为速凝片的片状晶平均厚度-气流磨磁粉的平均粒径=0~0.5μm,气流磨磁粉的平均粒径小于或等于速凝片的片状晶平均厚度,保证气流磨磁粉为单晶颗粒,提高磁环磁性能。
[0038]
进一步优选,气流磨磁粉平均粒径与速凝片的片状晶平均厚度保持一致,即速凝片的片状晶平均厚度为4μm时,控制气流磨磁粉的平均粒径也为4μm,速凝片的片状晶平均厚度为6μm时,气流磨磁粉的平均粒径为6μm。
[0039]
进一步优选,控制速凝片的片状晶平均厚度为5.8
±
0.2μm,气流磨磁粉的平均粒径也为5.8
±
0.2μm。气流磨磁粉平均粒径较大,有利于烧结磁环不开裂。
[0040]
步骤(4)取向成型的磁场强度优选为0.8~1.0t,等静压处理压力优选为150~200mpa。由于本发明的气流磨磁粉为单晶粉末,容易取向,磁场强度不易过大,磁场强度过大导致漏磁后,部分磁粉提前被弱场取向而导致后续取向困难,降低磁体性能。
[0041]
气流磨磁粉经取向成型和等静压处理后,进行高温烧结,高温烧结温度优选为1050~1100℃,烧结时间优选为4~6h。烧结冷却采用多级冷却,先真空自冷至600~750℃,充惰性气体(氩气或氮气)自冷到300~400℃,然后开风机风冷至室温结束烧结。采用多级冷却能避免快速冷却导致的材料内应力过大开裂,以及组织结构不均匀导致的性能下降。继续加热至一级回火温度800~950℃,回火2~4小时;降温至二级回火温度450~580℃,再回火4~6小时。
[0042]
本发明的润滑剂为本领域常规用于磁环中的润滑剂,如石蜡、丙三醇、硅酸酯、硅油、硬脂酸、硬脂酸锌、硼酸三丁酯等。润滑剂添加量为气流磨磁粉的0.2-0.5wt%。
[0043]
下面通过具体实施例对本发明的技术方案作进一步描述说明,本发明的保护范围不受以下实施例的限制。如果无特殊说明,本发明的实施例中所采用的原料均为本领域常用的原料,实施例中所采用的方法,均为本领域的常规方法。
[0044]
实施例1
[0045]
本实施例的磁环由以下步骤制备获得:
[0046]
1)采用工业用原材料prnd(75wt%nd)合金、纯dy、fe、co、ga、cu、al、zr金属按成分(prnd)
30
dy
1.8
cu
0.15
al
0.25
ga
0.20
co
1.5
zr
0.01
b
0.96
fe
余
(wt%)配料,将配置好的原料进行熔炼,浇铸甩带得平均厚度为0.3mm的速凝片,熔炼温度为1480℃,浇铸温度为1440℃,铜辊转速为1.5m/s;
[0047]
2)将速凝片装入带盖子的不锈钢桶中,并放入真空热处理炉进行热处理,热处理真空度保持≤4*10-2
pa,热处理温度为900℃,时间25h,速凝片的片状晶平均厚度长大为5.8μm(未经热处理时速凝片的柱状晶平均厚度约为3μm);
[0048]
3)将热处理完成的速凝片置于氢破炉中,充氢破碎,再经过脱氢热处理,使得粗破碎粉末氢含量≤600ppm,然后将粗破碎粉末送入气流磨机内进行磨粉,得到平均粒径为5.8μm的气流磨磁粉;
[0049]
4)往气流磨磁粉中添加0.3wt%润滑剂硬脂酸并搅拌4h,搅拌后进入磁环磁场压机进行取向成型,磁场强度为0.9t,压制成d25*d18*20的磁环,然后180mpa下等静压处理;
[0050]
5)等静压处理后进入真空烧结炉进行烧结,烧结温度1060℃,烧结时间5h;烧结结束后采用多级冷却控制,先真空自冷到700℃,充氩气自冷到350℃,然后开风机风冷到室温结束烧结;烧结后对烧结磁环进行二级回火:升温至920℃,保温3h,然后在500℃,保温5h。
[0051]
实施例2
[0052]
实施例2的磁环的制备方法与实施例1的区别仅在于,实施例2在取向成型时采用的磁场强度为1.2t,其它与实施例1相同,不在此赘述。
[0053]
实施例3
[0054]
本实施例的磁环由以下步骤制备获得:
[0055]
1)采用工业用原材料prnd(75wt%nd)合金、纯dy、fe、co、cu、al、zr金属按成分(prnd)
30
dy
1.2
cu
0.18
al
0.35
co
1.1
zr
0.03
b
1.02
fe
余
(wt%)配料,将配置好的原料进行熔炼,浇铸甩带得平均厚度为0.3mm的速凝片,熔炼温度为1470℃,浇铸温度为1420℃,铜辊转速为1.5m/s;
[0056]
2)将速凝片装入带盖子的不锈钢桶中,并放入真空热处理炉进行热处理,热处理真空度保持≤4*10-2
pa,热处理温度为900℃,时间21h,速凝片的片状晶平均厚度长大为5.5μm(未经热处理时速凝片的柱状晶平均厚度约为2.8μm);
[0057]
3)将热处理完成的速凝片置于氢破炉中,充氢破碎,再经过脱氢热处理,使得粗破碎粉末氢含量≤600ppm,然后将粗破碎粉末送入气流磨机内进行磨粉,得到平均粒径为5.1μm的气流磨磁粉;
[0058]
4)往气流磨磁粉中添加0.3wt%润滑剂硬脂酸并搅拌4h,搅拌后进入磁环磁场压机进行取向成型,磁场强度为1.0t,压制成d25*d18*20的磁环,然后200mpa下等静压处理;
[0059]
(5)等静压处理后进入真空烧结炉进行烧结,烧结温度1070℃,烧结时间4.5h;烧结结束后采用多级冷却控制,先真空自冷到710℃,充氩气自冷到320℃,然后开风机风冷到室温结束烧结;烧结后对烧结磁环进行二级回火:升温至900℃,保温2h,然后在450℃,保温5h。
[0060]
对比例1
[0061]
对比例1的磁环由以下步骤制备获得:
[0062]
1)采用工业用原材料prnd(75wt%nd)合金、纯dy、fe、co、ga、cu、al、zr金属按成分(prnd)
30
dy
1.8
cu
0.15
al
0.25
ga
0.20
co
1.5
zr
0.01
b
0.96
fe
余
(wt%)配料,将配置好的原料进行熔炼,浇铸甩带得平均厚度为0.3mm的速凝片,熔炼温度为1480℃,浇铸温度为1440℃,铜辊转速为1.5m/s;
[0063]
2)将速凝片置于氢破炉中,充氢破碎,再经过脱氢热处理,使得粗破碎粉末氢含量≤600ppm,然后将粗破碎粉末送入气流磨机内进行磨粉,得到平均粒径为3.0μm的气流磨磁粉;
[0064]
后续步骤同实施例1的。
[0065]
对比例2
[0066]
对比例2的磁环由以下步骤制备获得:
[0067]
1)采用工业用原材料prnd(75wt%nd)合金、纯dy、fe、co、ga、cu、al、zr金属按成分(prnd)
30
dy
1.8
cu
0.15
al
0.25
ga
0.20
co
1.5
zr
0.01
b
0.96
fe
余
(wt%)配料,将配置好的原料进行熔炼,浇铸甩带得平均厚度为0.3mm的速凝片,熔炼温度为1480℃,浇铸温度为1440℃,铜辊转速为1.5m/s;此时速凝片的柱状晶平均厚度约为3μm;
[0068]
2)将速凝片置于氢破炉中,充氢破碎,再经过脱氢热处理,使得粗破碎粉末氢含量≤600ppm,然后将粗破碎粉末送入气流磨机内进行磨粉,得到平均粒径为5.8μm的气流磨磁粉;
[0069]
后续步骤同实施例1的。
[0070]
对比例3
[0071]
对比例3的磁环由以下步骤制备获得:
[0072]
1)采用工业用原材料prnd(75wt%nd)合金、纯dy、fe、co、ga、cu、al、zr金属按成分(prnd)
30
dy
1.8
cu
0.15
al
0.25
ga
0.20
co
1.5
zr
0.01
b
0.96
fe
余
(wt%)配料,将配置好的原料进行熔炼,浇铸甩带得平均厚度为0.3mm的速凝片,熔炼温度为1480℃,浇铸温度为1440℃,铜辊转速为1.5m/s;
[0073]
2)将速凝片装入带盖子的不锈钢桶中,并放入真空热处理炉进行热处理,热处理真空度保持≤4*10-2
pa,热处理温度为600℃,时间25h,速凝片的晶体未见明显长大,晶体平均厚度为3.5μm;
[0074]
后续步骤同实施例1的。
[0075]
对比例4
[0076]
对比例4的磁环由以下步骤制备获得:
[0077]
1)采用工业用原材料prnd(75wt%nd)合金、纯dy、fe、co、ga、cu、al、zr金属按成分(prnd)
30
dy
1.8
cu
0.15
al
0.25
ga
0.20
co
1.5
zr
0.01
b
0.96
fe
余
(wt%)配料,将配置好的原料进行熔炼,浇铸甩带得平均厚度为0.3mm的速凝片,熔炼温度为1480℃,浇铸温度为1440℃,铜辊转速为1.5m/s;
[0078]
2)将速凝片装入带盖子的不锈钢桶中,并放入真空热处理炉进行热处理,热处理真空度保持≤4*10-2
pa,热处理温度为1200℃,时间30h,速凝片的片状晶平均厚度长大为7.6μm;
[0079]
后续步骤同实施例1的。
[0080]
对比例5
[0081]
对比例5的磁环由以下步骤制备获得:
[0082]
1)采用工业用原材料prnd(75wt%nd)合金、纯dy、fe、co、ga、cu、al、zr金属按成分(prnd)
30
dy
1.8
cu
0.15
al
0.25
ga
0.20
co
1.5
zr
0.01
b
0.96
fe
余
(wt%)配料,将配置好的原料进行熔炼,浇铸甩带得平均厚度为0.3mm的速凝片,熔炼温度为1480℃,浇铸温度为1440℃,铜辊转速为1.5m/s;
[0083]
2)将速凝片装入带盖子的不锈钢桶中,并放入真空热处理炉进行热处理,热处理真空度保持≤4*10-2
pa,热处理温度为900℃,时间25h,速凝片的片状晶平均厚度长大为5.8μm;
[0084]
3)将热处理完成的速凝片置于氢破炉中,充氢破碎,再经过脱氢热处理,使得粗破碎粉末氢含量≤600ppm,然后将粗破碎粉末送入气流磨机内进行磨粉,得到平均粒径为3.0μm的气流磨磁粉;
[0085]
后续步骤同实施例1的。
[0086]
将实施例1-3和对比例1-5制备的磁环中套一个d3*3的小样柱在pfm(脉冲磁场磁测仪)设备上磁性能检测,并检查磁环开裂情况,数据如下表1所示。
[0087]
表1实施例1-3和对比例1-5的磁环的磁性能及开裂情况
[0088][0089]
如表1所示,实施例1和实施例3为较优实施例,制备的磁环具有优异的磁性能,且磁环不开裂;实施例2磁环制备过程中采用的磁场强度较大,会降低磁环的磁性能;对比例1和对比例5的气流磨磁粉的平均粒径为3.0μm,采用细的磁粉烧结制备磁环会导致磁环极易开裂;对比例2的速凝片未经过高温处理,对比例3的热处理温度较低,均导致速凝片的晶粒粒径较小,当磨粉至平均粒径为5.8μm时,会导致磁粉为多晶粉末,降低磁环磁性能。
[0090]
本文中所描述的具体实施例仅仅是对本发明精神作举例说明。本发明所属技术领域的技术人员可以对所描述的具体实施例做各种各样的修改或补充或采用类似的方式替代,但并不会偏离本发明的精神或者超越所附权利要求书所定义的范围。