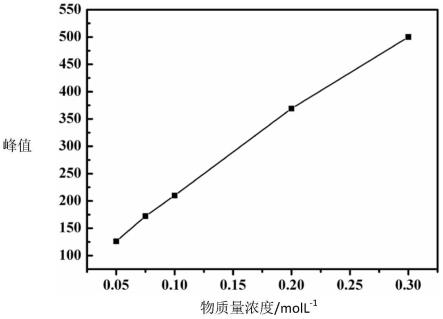
1.本发明属于高温聚合物电解质膜燃料电池领域,特别涉及一种高性能高温聚合物电解质膜燃料电池膜电极的压合制备方法。
背景技术:2.高温质子交换膜燃料电池(ht-pemfc)的工作温度通常在150-200℃,具有较强的耐co毒化的能力,较高的尾气废热利用价值,因此ht-pemfc具有燃料选择范围广、系统简单、综合能量利用率高等优势,在车载电源、便携式电源、固定电站以及微型热电联产系统等领域表现出了巨大的潜力。
3.作为其中关键材料,聚合物电解质膜在燃料电池中的作用包括绝缘、隔绝阴阳极气体、传导质子和提供电化学三相反应界面所需的质子。作为燃料电池中质子传输介质,磷酸的管理对燃料电池性能、可靠性与寿命的影响不容忽视,展开磷酸在燃料电池全寿命周期变化的研究工作对于提高其性能,延长其寿命具有比较重要的意义。文献中针对磷酸的再分布与流失做了大量的研究报道,通过阐述燃料电池不同工况对磷酸流失的影响,揭示磷酸的流失对燃料电池放电产生的极化因素,从而阐释对其性能衰减或者对电池寿命的影响。膜电极制备过程直接决定其中磷酸的量及其分布,然而,由于膜中大量水的存在,尤其是溶胶溶胶法制备的pbi/h3po4膜含水量达45%,在膜电极制备过程中会造成大量的水残留于电极中,一方面造成膜电极中磷酸含量低,膜电极的寿命不能满足要求,另一方面会使得大量的磷酸溶液充斥于电极中,造成电极酸淹现象,产生较大的电化学反应极化和传质极化,严重影响燃料电池的性能。
技术实现要素:4.针对上述问题,本发明的目的在于提出一种高性能高温聚合物电解质膜燃料电池的制备方法,用以控制磷酸的合理分布,提高燃料电池性能,延长其寿命。
5.所述一种高性能高温聚合物电解质膜燃料电池的制备方法,包括以下制备步骤,
6.(1)膜电极的组合放置:将膜电极材料阳极、膜、以及阴极依次层叠放置;
7.(2)膜电极压合制备:为了避免水在膜电极中残留同时保证酸在膜中的保留避免电极酸淹影响传质,膜电极的压合制备过程包括预压合与压合两个步骤,
8.预压过程是为了除去膜里大部分的水分而避免或尽量减少磷酸从膜中流失,使得膜中的水分减少78%-92%,磷酸保留量为85%-100%;而压合过程目的是控制磷酸在膜与电极中的分布,避免过多的磷酸到达电极,造成电极酸淹现象,膜中磷酸与电极中磷酸的量控制在85%-100%;
9.a、预压合:
10.先将限位模具置于热压合设备的下加热板上预加热,然后再将步骤(1)中组合放置的膜电极材料放置于已经预加热的模具上,使得阴极靠近压合设备的上加热板一侧放置;或者先将步骤(1)中组合放置的膜电极材料放置于模具上,然后再将放置了组合成功的
膜电极各材料的模具放置于压合设备下加热板上,使得阴极靠近压合设备的上加热板一侧放置;
11.通过压合设备对膜电极材料上下二侧施压,使上加热板与膜电极阴极表面接触,进行预压;预压过程的温度为60-200℃;预压压力为0-50磅/cm2;所述预压时间为1-600s;预压合过程的温度优选80-180℃;预压压力为优选0-20磅/cm2,优选0-10磅/cm2;所述预压时间优选1-300s;
12.b、压合:提高压合设备的压合力,取下压合完毕的膜电极;压合过程的温度为30-200℃;压力为10-500磅/cm2;所述压合过程时间为10-1200s;压合过程的温度为优选40-180℃;压力为15-400磅/cm2,优选20-300磅/cm2;所述压合过程时间为15-1000s。
13.压合与预压合过程的温度相同或不同。
14.所述限位模具为一平板,平板中部为膜电极材料的放置区,于膜电极材料的放置区四周设置有环型突起,环型突起围绕于放置区四周,于环型突起上设有通孔或贯穿突起内外壁面的凹槽,作为液体透过孔道。
15.所述限位模具为6-12mm厚平板,环型突起的内壁面与放置膜电极材料区域之间的距离为5-100mm,环型突起的高度为0.4-1.5mm,优选0.5-1.2mm,较优选0.55-0.95mm。
16.平板的形状和尺寸依据膜电极的形状和尺寸改变;
17.通孔或凹槽的底部位于平板所在的平面上;
18.压合后的膜电极的厚度与环型突起的高度相同或略高于环型突起的高度,可通过调变模具环型突起的高度(环型突起远离平板表面的平面与平板表面间的距离)调变压合后的膜电极的厚度。
19.步骤(1)中所述膜为采用后浸渍法制备的聚苯并咪唑掺杂磷酸膜或者采用溶胶凝胶法制备的聚苯并咪唑/h3po4膜,聚苯并咪唑的分子结构如下所示中的一种或二种以上聚合物:
20.21.[0022][0023]
其中n和m各自为大于或等于50的整数,优选大于或等于100的整数,较优选200-3000的整数。
[0024]
所述阳极、阴极和膜的靠近外边缘的四周环状区域分别与一聚合物密封材料相贴接;内边缘尺寸小于阳极、阴极和膜的尺寸,聚合物密封材料的外边缘的尺寸大于或等于阳极、阴极和膜的外边缘的尺寸。聚合物密封材料的内边缘形状和尺寸与电池的有效面积相同或相当。
[0025]
所述聚合物密封材料为聚酰亚胺、fep表面涂覆的聚酰亚胺(kapton)、氟化聚乙烯丙烯、全氟烷氧基化合物、聚偏氟乙烯、聚四氟乙烯、聚砜中的一种或二种以上,优选聚酰亚胺、fep涂覆的聚酰亚胺(kapton)、聚砜中的一种或二种以上;
[0026]
所述的制备方法制备获得的膜电极。
[0027]
所述的膜电极在高温聚合物电解质膜燃料电池、浓差电池、温差电池或氢泵中的应用。
[0028]
膜电极中的电极与膜中酸量及其分布定量:采用非原位方法模拟膜电极压合过程,将膜放置于滤纸中间,采用相同于膜电极的压合条件对其进行压合,通过测定压合前后膜的失重与膜中保留的酸与水定量压合后膜电极中酸在膜与电极中的量与分布情况(滴定测量方法)。
[0029]
膜电极组装单池性能测试:将上述制备的膜电极放置于两个密封垫中间或者叠放于一个密封垫上,然后将密封垫与膜电极放置于带有进气口、出气口、螺栓插入口、热偶口与加热部分的由金属端板与带有流场的极板组成的测试夹具之间。其中进气口、出气口分布于极板与端板上,热偶口在极板之上,螺栓插入口与加热部分在端板上。
[0030]
这种方法不仅适用于溶胶-凝胶法制备pbi/h3po4膜的膜电极的制备,通过条件的改变同样适用于后浸渍法制备pbi/h3po4膜的膜电极的制备,以改善磷酸在膜与电极中的定量分布,避免传质极化造成电池性能差的问题。
[0031]
本方法操作可实现性高、易于高温聚合物电解质膜燃料电池膜电极的批量制备。
[0032]
预压过程通过预压温度、预压时间与预压压力的控制实现膜中磷酸与水的分离,压合步骤通过压合温度与压合压力的控制实现磷酸在膜与电极中的分布,最终得到磷酸含量高、磷酸在膜与电极中合理分布、电化学性能好的膜电极。本方法特征在于通过压合制备过程对磷酸实现定量、合理地分配,得到性能高的膜电极,操作可实现性高、易于膜电极的批量制备,不仅适用于基于溶胶凝胶法高温聚合物电解质膜的膜电极的制备,同样适用于
后浸渍法高温聚合物电解质膜的膜电极的制备。
附图说明
[0033]
图1为实施例1中磷酸二氢钠溶液xrf峰值对应浓度标准曲线。
[0034]
图2为实施例1中制备得到膜电极组装单池进行放电性能极化曲线测试。
具体实施方式
[0035]
所述限位模具为一平板,平板中部为膜电极材料的放置区,于膜电极材料的放置区四周设置有环型突起,环型突起围绕于放置区四周,于环型突起上设有通孔,通孔的底部位于平板所在的平面上;作为液体透过孔道。所述限位模具为10mm厚平板。
[0036]
实施例1
[0037]
(1)膜电极的组合放置:将质量为0.38g面积为长*宽=5*5cm2的阳极、0.13g的内边缘面积约为长*宽=4.5*4.5cm2、外边缘面积约为长*宽=5.5*5.5cm2的环状聚合物密封材料、质量1.77g面积为长*宽=5.1*5.1cm2的溶胶凝胶法制备的pbi/h3po4膜、0.13g的内边缘面积约为长*宽=4.5*4.5cm2、外边缘面积约为长*宽=5.5*5.5cm2的环状聚合物密封材料、质量为0.4g面积为长*宽=5*5cm2的阴极依次放置于环型突起的高度为0.62mm的限位模具上,环型突起的内壁面与放置膜电极材料区域之间的距离为10mm。
[0038]
(2)膜电极压合制备:包括预压合与压合两个步骤,
[0039]
a、预压合:
[0040]
将放置了组合放置的膜电极的模具放置于压合设备下加热板上,加热至120℃的压合设备上,使上加热板与膜电极阴极表面接触,施加力使加热板闭合,并对放置有材料的模具施加100磅的力,保持30s;
[0041]
b、压合:继续加压至2000磅,并维持90s,卸压后用滤纸将膜电极表面擦干,称量质量为1.9g,厚度约为0.62mm。
[0042]
所述膜为pbi/h3po4膜(basf公司生产的膜,给定磷酸含量为51%-59%),环状聚合物密封材料为聚酰亚胺.
[0043]
膜中酸含量确定:(1)磷酸二氢钠溶液xrf峰值对应浓度标准曲线绘制在室温条件下,分别配制0.05m、0.075m、0.10m、0.20m、0.30m的磷酸二氢钠水溶液。静置4h后,取2ml进行xrf表征,采用的模式为low zb。分别记录xrf峰值与浓度关系。每个浓度的磷酸二氢钠溶液的xrf表征进行至少10次,在绘制曲线前,取表征次数数值的平均值。绘制出的xrf峰值随浓度之间关系曲线如图1。从图1可以看出,当每次取磷酸二氢钠溶液的体积一定时,所做出来的xrf表征的峰值与其溶液的物质量浓度基本呈线性关系。得到的标准曲线为y=1042c+101.8。其中y为xrf测试得到的峰值,c为磷酸二氢钠溶液的浓度;(2)膜中磷酸含量的确定:称取与上述面积、质量相同的采用溶胶凝胶法制备的pbi/h3po4膜(basf公司生产的膜,给定磷酸含量为51%-59%),在其两侧分别放置两层厚度与电极厚度相同的滤纸,将其放置于模具上,采用上述压合方式对齐进行热压,将热处理后的膜放入250ml的广口瓶中,加入45g 0.5m naoh溶液,在57℃下搅拌8h倒入烧杯中,再向广口瓶中加入34g 1m naoh溶液洗涤26h,再采用35g 2m naoh溶液处理24h,用去离子水将膜表面清洗干净,用xrf光谱技术在low za模式检测膜中是否存在磷元素,如果无法检测出来则认为无磷酸残余,
收集所有洗涤溶液测量其体积约为110.6ml。然后取2ml洗液进行xrf测试,所用模式为lowzb,反复进行10次表征。将10次xrf表征结果取平均值159.3。按照标准曲线,计算此时洗液的磷浓度为0.0552mol/l,结合溶液体积,可以计算出处理后膜中磷酸质量m=0.598g,膜中磷酸的面密度约为25mg/cm2。
[0044]
非原位压合后膜中酸含量的测定方法包括含磷溶液标准曲线制定与用碱液洗涤后溶液中磷含量的确定。所述含磷溶液标准曲线的制定过程为为取一定体积物质的量浓度的磷酸盐溶液,然后采用x射线荧光光谱分析(xrf)手段中的lowzb模式进行测试,得到xrf表征结果中峰值强度与溶液中磷酸根物质的量浓度(分别作为横纵坐标)之间的关系曲线,记为含p溶液的标准曲线;所述磷酸盐溶液包括磷酸氢二铵、磷酸一氢铵、磷酸二氢铵、磷酸铵、磷酸氢二钠、磷酸一氢钠、磷酸二氢钠、磷酸钠、磷酸二氢锂,尤其是磷酸氢二铵、磷酸一氢铵、磷酸二氢铵、磷酸铵、磷酸氢二钠、磷酸一氢钠、磷酸二氢钠、磷酸钠中的一种或二种以上;所述洗涤膜中磷酸所用的碱液为0.5-3mol/l氨水、氢氧化钠、氢氧化锂、碳酸氢铵、碳酸铵、碳酸钠、碳酸氢钠中的一种或二种以上;所述采用碱液洗涤膜的温度为35-70℃,处理的次数》3次;采用xrf的模式为low za测试所洗的膜中无磷的特征峰时,将洗涤液收集到一起采用xrf的low zb模式进行磷元素测试,将测得p含量与上述含p溶液的标准曲线进行对应,即得到清洗用碱液中p浓度c(mol/l),再依据公式m=cv*98/1000可计算出膜中磷酸质量m,再根据wt%=m/m*100%即可得出pbi/h3po4膜中磷酸含量wt%。
[0045]
电极中磷酸含量为压合后膜电极的质量减去阳极、阴极、阴阳极对应密封材料与非原位压合后膜的质量,即为电极中酸的含量;
[0046]
通过计算,得出阳极、阴极中磷酸的含量为0.2g(其中pbi聚合物的质量设定为0.06g),磷酸的面密度为10.0mg/cm2。
[0047]
将上述制备的膜电极组装成单池,采用的ptfe作为密封垫,电加热给单池加热,加热至120℃后,阳极、阴极分别通氢气、空气,流量分别为0.1ml/min与0.3ml/min,并设定电流为2a进行恒流放电,当电池升温至160℃后将电流改至4a进行恒流放电,活化24h后,进行i-v测试。如图2为单池放电i-v曲线。从曲线中分析可知,单池的性能在200macm-2
时可以达到0.72v,500macm-2
时能达到0.63v,与basf公司膜电极的性能相当。
[0048]
实施例2
[0049]
采用实施例1中的材料与工艺,测试条件与实施例1相同。改变压合温度为160℃,压合时间不变,此工艺下磷酸在膜中的面密度变为26mg/cm2,而电极中磷酸面密度为13.2mg/cm2,单池的性能在200macm-2
时可以达到0.7v。
[0050]
实施例3
[0051]
采用实施例1中的材料与工艺,测试条件与实施例1相同。改变压合温度为120℃,压合时间不变,单池的性能在200macm-2
时也可以达到0.69v。
[0052]
实施例4
[0053]
采用实施例1中的材料与工艺,测试条件与实施例1相同。压合时间延长至300s,单池的性能在200macm-2
时也可以达到0.7v。
[0054]
实施例5
[0055]
采用实施例1中的材料与工艺,测试条件与实施例1相同。压合时间延长至600s,单池的性能在200macm-2
时也可以达到0.7v。
[0056]
对比例1
[0057]
采用实施例1中材料与放置顺序,测试条件与实施例1相同。在120℃采用2000磅力压合90s,膜电极的厚度为0.67mm,质量为1.95g,组装单池,压缩比与实施例1相同,单池性能在200macm-2
时仅为0.58v
[0058]
对比例2
[0059]
将对比例1中的压合温度降至40℃进行压合后,单池的性能在200macm-2
时仅为0.28v。测试条件与实施例1相同。
[0060]
对比例3
[0061]
采用实施例1中材料与放置顺序,在140℃采用2000磅力压合90s,膜电极的厚度为0.68mm,组装单池,压缩比与实施例1相同,单池性能在200macm-2
时为0.61v。测试条件与实施例1相同。
[0062]
对比例4
[0063]
采用实施例1中材料与放置顺序,在160℃采用2000磅力压合90s,膜电极的厚度为0.65mm,组装单池,压缩比与实施例1相同,单池性能在200macm-2
时为0.60v。测试条件与实施例1相同。
[0064]
对比例5
[0065]
将实施例1中的预压或压合温度升至200℃后,组装单池测试,在200macm-2
时几乎不放电,猜测此时磷酸多以多聚磷酸形式存在,对电池的欧姆极化和电化学反应极化影响较大。测试条件与实施例1相同。
[0066]
对比例6
[0067]
采用实施例1中材料与工艺,不采用模具进行限位,得到的膜电极的厚度仅为0.52mm,而且出现聚合物密封材料内边缘与膜贴合处膜破损现象,而且极限电流达到5macm-2
。测试条件与实施例1相同。