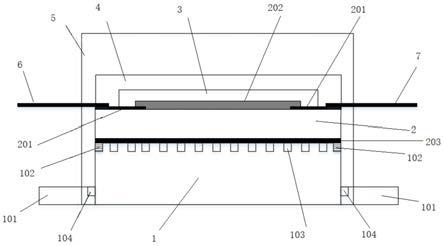
1.本发明属于电子元器件领域,具体来说,属于电阻器领域,更进一步来说,属于厚膜功率电阻器领域。
背景技术:2.目前,随着电子系统高可靠及微型化的快速发展,特别是在大功率、高频电子模块部分,涉及到大量的散热、屏蔽系统,决定着电子系统的高可靠及微型化程度,对于大功率、小体积电阻器的使用越来越普遍,对电阻器的性能要求也越来越高。在这种应用中金属电阻器,如金属丝、线、箔或片等,具有优秀的抗脉冲性能,但功率需求越大体积也会很大,且固有电感值也随之增大,不能满足小型化、大功率、高频和抗干扰的应用需求。为了尽量简化额外的散热系统,提高系统的可靠性,直接带散热式的厚膜功率电阻器的使用越来越普遍。在现有技术中,同类型的散热式厚膜功率电阻器的主要结构为平面型散热底板、陶瓷基片、电极层、电阻层、包封层和复数个金属引脚,由于在电阻器结构上不够完善,对于同体积的电阻器,散热能力、比功率和抗脉冲性能不足,当经受过载脉冲功率能量时,不能及时开路,导致对电子系统产生不良影响。
3.有鉴于此,特提出本发明。
技术实现要素:4.本发明的目的是:解决现有电阻器散热能力不足、额定功率冗余度小、抗强脉冲负荷能力不足等问题。
5.为解决此问题,本发明的总体构思是:在包封层与塑封层之间增加硅橡胶层,以提升电阻层过载平稳开路能力和封装体的顶部散热能力;采用复数个金属引脚,复数个金属引脚均匀焊接在电阻层两端的表面电极层上,提升散热能力;陶瓷基片的背面增加金属化层,使陶瓷基片与散热底板实现原子间致密接触,提升封装体中间部位的热量传输能力;与陶瓷基片的粘接面,采用表面带多个凹槽的平面型散热底板,使散热底板与陶瓷基片背面金属化层焊接时,保证焊透率,增大封装体的底部散热能力。
6.为此,本发明提供一种散热式无感厚膜功率电阻器及制造方法,结构示意图如图1所示,包括:散热底板1,散热底板延伸部101,表面横向凹槽102,表面纵向凹槽103,延伸部凹槽104,陶瓷基片2,表面电极层201,厚膜电阻层202,基片背面金属化层203,包封层3,硅橡胶层4,塑封外壳5,第一金属引脚6,第二金属引脚7。
7.所述散热底板1的一端的两侧有散热底板延伸部101,以增大散热底板的散热面积;所述散热底板1的陶瓷基片焊接区有表面横向凹槽102或表面纵向凹槽103,使其与陶瓷基片背面金属层焊接时,能很好的进行定位焊接,并且控制焊料满足高焊透率焊接要求,使电阻器达到最佳的散热性能,该结构保证了电阻器的额定功率冗余度;所述散热底板延伸部101的内侧设有延伸部凹槽104,保证了注塑绝缘材料时使注塑绝缘材料与散热底板之间结合的更牢固。
8.所述陶瓷基片2的上表面依次有表面电极层201、厚膜电阻层202,所述陶瓷基片2的背面有背面金属化层203。
9.所述包封层3覆盖整个厚膜电阻层202和部分表面电极层201。
10.所述第一金属引脚6和第二金属引脚7组成复数个金属引脚,第一金属引脚6和第二金属引脚7的首端通过耐高温焊料分别焊接在电阻层两端的表面电极层201上,第一金属引脚6和第二金属引脚7的尾端作为引出端通过通用锡焊接在其他器件上,第一金属引脚6和第二金属引脚7的首端使用的锡料的熔点高于第一金属引脚6和第二金属引脚7的尾端使用锡料的熔点,充分保证了该电阻器的可靠性。
11.所述硅橡胶层4覆盖整个包封层3,及包封层3未覆盖其余表面电极层201。
12.所述塑封外壳5为最外层。
13.本发明提供的一种散热式无感厚膜功率电阻器的制造方法,其特征在于,包括如下步骤:
14.(1)陶瓷基片准备
15.(2)在陶瓷基片的表面印制表面电极层,在陶瓷基片的背面印制背面金属化层。将印制完表面电极层、背面金属化层后的陶瓷基片烘干,烘干后,对印制完表面电极层、背面金属化层的陶瓷基片进行烧结。
16.(3)在烧结后的陶瓷基片上印制厚膜电阻层,厚膜电阻层搭接于陶瓷基片两端表面电极层之间。将印制完电阻层后的陶瓷基片烘干,对印制完厚膜电阻层的陶瓷基片进行烧结,烧结后,通过激光进行阻值修正。
17.(4)在阻值修正后的电阻层上印制包封层,包封层烘干,然后进行烧结,确保包封层完全覆盖电阻层及部分表面电极层。
18.(5)对陶瓷基片进行镀镍、镀锡的端面处理。
19.(6)准备在首端左右两侧分别设置延伸部位的散热底板。
20.(7)将散热底板、制作有表面电极层、背面金属化层及厚膜电阻层陶瓷基片和复数个金属引脚依次叠层放置,两两之间的焊接区域均匀填充焊膏,通过专用定位焊接夹具进行真空共晶焊接,将复数个金属引脚的首端焊接在电阻层两端的表面电极层上,将散热底板焊接在陶瓷基片背面金属化层上。
21.(8)将硅橡胶均匀涂覆于焊接后的包封层上,并进行固化。所述硅橡胶材料为室温硫化硅橡胶,具有优秀的绝缘性和良好的导热性。
22.(9)塑封前预热处理,然后放入塑封模具中进行模压塑封。所述塑封材料采用热固性绝缘材料,具有高耐热性和良好的散热性。
23.(10)对复数个金属引脚的尾端和散热底板进行端面镀锡处理。
24.本发明所属的一种散热式无感厚膜功率电阻器,底板中心温度不大于70℃时,额定功率可达35w,绝缘耐压能力为1800vac;所用硅橡胶具有优秀的绝缘性,可防止电阻层温升过高导致包封层材料和塑封材料碳化,或防止电阻层过载开路产生的电弧导致包封层材料和塑封材料碳化,造成电阻器阻值降低或短路的失效模式。同时,具有良好的导热性。
25.本发明的优势是,相比于现有技术,通过优化无感结构设计,提高电阻器额定功率冗余度,保证了焊点和电阻层的可靠性,使焊接区域满足高焊透率要求,提升了电阻器的可靠性,通过设置散热底板下表面直接焊接或安装在散热面上,使电阻器达到最佳的散热性
能。当电阻器经受过载脉冲功率能量时,能实现平稳开路,防止包封层和塑封材料碳化,造成电阻器短路或阻值降低的失效模式,对其应用的电子系统起到保护作用,可广泛应用于高可靠及微型化电子系统中。
附图说明
26.图1是本发明散热式无感厚膜功率电阻器的结构示意图。
27.图中:1为散热底板,101为散热底板延伸部,102为表面横向凹槽,103为表面纵向凹槽,104为延伸部凹槽,2为陶瓷基片,201为表面电极层,202为厚膜电阻层,203为基片背面金属化层,3为包封层,4为硅橡胶层,5为塑封外壳,6为第一金属引脚,7为第二金属引脚。
具体实施方式
28.为实现上述目的,所述散热底板和复数个金属引脚材料为镀镍紫铜,所述陶瓷基片为96%氧化铝陶瓷基片,所述表面电极层、基片背面金属化层为银钯浆料,所述厚膜电阻层为钌系浆料,所述包封层为玻璃浆料,所述硅橡胶层为硫化硅橡胶,所述塑封外壳为热固性绝缘材料。下面结合优选实施例就本发明的技术方案作进一步的说明。
29.实施例1:
30.(1)选择长度为8.0mm、宽度为5.5mm、厚度为0.635mm的陶瓷基片。
31.(2)在陶瓷基片的表面印制表面电极层,在陶瓷基片的背面印制背面金属化层。将印制完表面电极层、背面金属化层后的陶瓷基片烘干,烘干后,表面电极层干燥膜厚为(24
±
3)μm,背面金属化层干燥膜厚为(15
±
3)μm。对印制完表面电极层、背面金属化层的陶瓷基片在(830~870)℃下烧结(8~15)min。
32.(3)在烧结后的陶瓷基片上印制电阻层,电阻层搭接于陶瓷基片两端表面电极层之间。将印制完电阻层后的陶瓷基片烘干,电阻层干燥膜厚为(36
±
5)μm。对印制完电阻层的陶瓷基片在(830~870)℃下烧结(8~15)min,烧结后,通过激光进行阻值修正。
33.(4)在阻值修正后的电阻层上印制包封层,确保包封层完全覆盖电阻层及部分表面电极层,包封层烘干厚度为(80
±
6)μm,然后在(550~650)℃下烧结(8~15)min。
34.(5)对陶瓷基片表面电极层、背面金属化层进行镀镍(5~20)μm厚、镀锡(5~20)μm厚。
35.(6)散热底板首端左右两侧分别设置延伸部位,且延伸部位的内侧开设有内凹槽。在散热底板的陶瓷基片焊接区表面有多个横向凹槽或纵向凹槽。所述散热底板其整体长度为10.1mm、宽度为8.4mm、厚度为1.0mm。所述散热底板和复数个金属引脚材质为紫铜,镀镍(5~8)μm。
36.(7)对散热底板、陶瓷基片和复数个金属引脚依次叠层放置,两两之间的焊接区域均匀填充焊膏,通过专用定位焊接夹具进行真空共晶焊接,将复数个金属引脚的首端焊接在电阻层两端的表面电极层上,将散热底板焊接在陶瓷基片背面金属化层上,真空焊接温度为(300~360)℃,焊接时间为(50~90)s,焊透率≥99%。
37.(8)将硅橡胶均匀涂覆于焊接后的包封层上,硅橡胶涂覆厚度为(0.7~1.2)
㎜
,涂覆完成后待其固化,固化时间(24~36)h。所述硅橡胶材料为室温硫化硅橡胶。
38.(9)塑封前预热处理,预热温度为(190
±
5)℃,预热时间为(1~2)min,然后放入塑
封模具中进行模压塑封,塑封温度(180~200)℃,塑封时间(2~3)min。所述塑封材料采用热固性绝缘材料。
39.(10)将塑封后复数个金属引脚的尾端和散热底板进行镀锡处理,镀锡厚度为(5~20)μm。
40.实施例2:
41.陶瓷基片的尺寸选择为:长度为6.4mm、宽度为5.10mm、厚度为1.0mm。
42.散热底板的尺寸选择为:长度为7.0mm、宽度为6.35mm、厚度为1.0mm。
43.其他工艺步骤及工艺条件与实施例1相同。
44.如实施例2所属的一种散热式无感厚膜功率电阻器,在底板中心温度不大于70℃时,额定功率可达35w,绝缘耐压能力为2000vac。
45.以上仅为本发明的原理和优选地实施例而已。并不用以限制本发明,应当指出,凡在本发明的精神和原则之内所作的任何修改、等同替换和改进等,均应包含在本发明的保护范围之内。