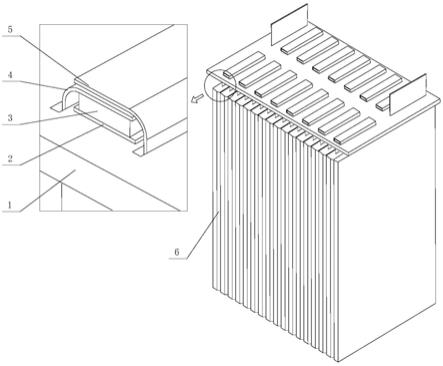
1.本实用新型涉及软包动力电池,特别是软包动力电池的极耳串联焊接结构。
背景技术:2.软包电池通常采用铝条和镍条引出,分别作为正极耳和负极耳,由于铝条无法锡焊,因此一般在铝极耳外面包覆镍条,两者之间采用点焊或超声波焊接。在实际应用中,软包电池往往需要串联成为电池组使用,常规采用锡焊直接将相邻电池正负极耳焊接在一起,或者通过导线锡焊桥接,该方法对于工作电流较小的情况是可行的。但是,对于软包动力电池,由于工作电流很大,正负极耳尺寸设计得较大,采用锡焊需要使用较大功率的烙铁,焊接时需要停留较长的时间才有可能焊接牢固,会使极耳发热温度过高,导致电池极耳引出部位密封和绝缘受损,严重时会发生电池短路,存在安全隐患,产品可靠性降低。
技术实现要素:3.本实用新型旨在提出一种软包动力电池串联结构,解决常规锡焊连接极耳过热导致电池损伤甚至短路的问题,提高电池安全性,简化电路接线,提高产品可靠性。
4.为解决上述技术问题,本实用新型采用的技术方案是:
5.一种软包动力电池串联结构,包括多个串联的单体电池,相邻的两个单体电池的正极耳和负极耳焊接,还包括,
6.印制板,所述印制板上开有至少两条通槽;
7.焊盘,所述焊盘设置在印制板表面上,且位于两条相邻的通槽之间;
8.镍片,所述镍片焊接固定在焊盘的表面;
9.相邻的两个单体电池的正极耳和负极耳分别穿过通槽后相连并焊接在镍片上。
10.优选的,所述焊盘为长方形焊盘。
11.优选的,所述印制板上的多条通槽平行排列,且通槽的宽度和厚度大于等于单体电池上正极耳和负极耳的宽度和厚度。
12.优选的,所述镍片锡焊在焊盘表面。
13.优选的,所述相邻的两个单体电池的正极耳和负极耳分别穿过通槽后与镍片激光焊接。
14.优选的,所述正极耳、负极耳和镍片按照从上到下依次为正极耳、负极耳、镍片或者负极耳、正极耳、镍片的顺序叠放,且均为面接触。
15.与现有技术相比,本实用新型的软包动力电池串联结构具备以下特点:
16.1)该结构采用激光焊接实现电池极耳串联,焊接热影响区很小,特别适合软包动力电池大尺寸极耳焊接串联,解决了常规锡焊连接极耳过热导致电池损伤甚至短路的问题,接触电阻小,承载电流大,提高了电池安全性。
17.2)印制板上预焊的镍片改善了电池极耳激光焊接的工艺可行性,焊盘还可设计用于焊接电压信号检测线或接插件。
18.3)印制板既作为电池极耳定位的结构件,又作为大电流通路导电零件的载体,实现了结构功能一体化,简化了电路接线,提高了产品可靠性。
附图说明
19.图1是软包动力电池串联结构的剖面示意图;
20.图2是软包动力电池串联结构的立体示意图;
21.图中:1-印制板;2-焊盘;3-镍片;4-极耳a;5-极耳b;6-单体电池。
具体实施方式
22.下面结合附图和具体实施例对本实用新型作进一步的说明,但不应就此理解为本实用新型所述主题的范围仅限于以下的实施例,在不脱离本实用新型上述技术思想情况下,凡根据本领域普通技术知识和惯用手段做出的各种修改、替换和变更,均包括在本实用新型的范围内。
23.如图1和图2所示,印制板1上开有多条平行间隔布置的狭窄长方形通槽,通槽的长宽尺寸与电池极耳匹配,以能电池极耳能够穿过为原则,通槽的数量取决于串联的电池数量和极耳数量,相邻的两个通槽中间设计有长方形焊盘2,焊盘2为板状且位于印制板1表面,焊盘2上端面用锡焊预焊有镍片3,电池组串联时,相邻单体电池6的极耳a4(正极耳或负极耳)和极耳b5(负极耳或正极耳)从印制板1的通槽中穿出,然后弯曲并面与面紧贴,再采用激光焊将镍片3、极耳a4、极耳b5三者焊接在一起。
24.图2中是16只软包动力电池的单体电池6串联时的状态示意图,图中放大的局部区域对应图1中的剖面。
25.以上对本实用新型的实施例进行了详细说明,但所述内容仅为本实用新型的较佳实施例,不能被认为限定本实用新型的实施范围。凡依本实用新型范围所作的均等变化与改进等,均应仍归属于本专利涵盖范围之内。