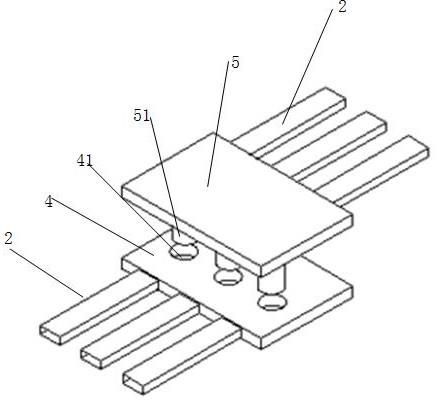
1.本实用新型涉及一种车用线束、车用线束连接结构及汽车,提高线束制造效率和汽车生产装配效率。
背景技术:2.随着汽车智能化、电气化程度的不断提高,汽车线束回路中涉及的信号传输回路不段增多,而随之带来小线径回路增加,据统计0.5 mm2及以下导线回路约占整车总回路的70%,数量达到约700条,同时还有不断增加的趋势。
3.小线径回路增多,必然带来整车线束外径的增加,在实车布置中,由于空间限制外径过大的线束往往带来干涉或挤压风险,增大了线束连接失效风险,同时也会增大线束尺寸制造偏差,给线束布置设计风险带来很多不可控因素。同时线束外径的增加,还会导致在总装过程中,工人卡接、扭曲线束的难度增大,直接带来装配效率的降低。而小线径回路增多给线束制造领域带来的困难则更大,随着小线径回路的大幅增多,供应商的物料状态准备种类更多,同时线束回路的压接、包装、存储、装运、调配、布线、插接工作量更大。给本身自动化程度就不高的线束制造行业,带来更多的人力投入,制造效率更加低下。
4.如何对数量巨大的小回路导线进行连接,是线束设计工程领域发展需要解决的问题。线束产品外形及尺寸稳定性差,以及线束制造自动化水平低下的问题,其实在目前的线束领域同样也面临这个难题,而小线径的增多则将这个难题显得更加突出。传统的汽车线束采用端子压接导线的方式进行连接,每颗压接端子后的导线回路需要人工进行包装、存储、装运、调配、布线、插接处理,直到手工插入到接插件相应的孔位上。可否通过调整导线的连接形式改变目前线束行业遇到的问题,是本实用新型要思考和解决问题的关键。
技术实现要素:5.本实用新型提出了一种车用线束、车用线束连接结构及汽车,优化了导体及线束结构,提高了线束成型稳定性。同时从传统的单回路连接提升到分块、分区域的连接,提高了连接制造效率。既解决了总装效率问题,也解决了线束制造领域效率低下的问题。
6.本实用新型的具体方案如下:
7.本实用新型实施例提供了一种车用线束,包括:
8.并排布置的多根导体以及将多根导体包裹住的绝缘外皮;各所述导体具有外露于所述绝缘外皮端部的导体焊接段;
9.相邻两根导体经由所述绝缘外皮分隔开;且各所述导体的截面形状均呈扁平状。
10.优选地,包裹住多根所述导体的绝缘外皮的截面形状呈扁平状。
11.本实用新型实施例还提供了一种车用线束连接结构,包括:与第一线束的导体焊接段相焊接的母端插座和与第二线束的导体焊接段相焊接的公端插头;所述第一线束和所述第二线束为上述的车用线束;
12.所述公端插头叠置于所述母端插座上,所述公端插头的公端端子伸出所述公端插
头的外壳后再伸入所述母端插座的外壳内与所述母端插座的母端端子对接。
13.优选地,所述母端插座的外壳内布置有相连的母端插座铜基板和母端端子,所述第一线束的导体焊接段伸入至所述母端插座的外壳内与所述母端插座铜基板通过超声波焊接固定。
14.优选地,所述公端插头的外壳内布置有相连的公端插头铜基板和公端端子;所述第二线束的导体焊接段伸入至所述公端插头的外壳内与所述公端插头铜基板通过超声波焊接固定;所述公端端子远离所述公端插头铜基板的一端伸出所述公端插头的外壳后再伸入所述母端插座的外壳内与所述母端插座的母端端子对接。
15.本实用新型还提供了一种汽车,包括上述的车用线束连接结构。
16.本实用新型的有益效果为:
17.通过将导线的圆形导体更改成扁平形导体,这样各导体的间距可以规则、紧密地进行排布。由于整个导线内的导体呈现为规则的扁平形分布,导线的外观上也设计为扁平形分布,使线束外观更方正,避免了传统包扎型线束外径不一、扭曲变形的缺点,使线束装配效率更高。
18.本实施例中得利于矩形导体导线的规则排布,可以将传统的端子压接方式调整成连接效率更高的超声波焊接方式,这样在增加制造效率的同时还节省了端子压接成本及大量人工成本。
附图说明
19.图1 为传统线束的结构图;
20.图2 为本实施例中的线束的结构图;
21.图3为本实施例中的线束和母端插座的连接示意图;
22.图4为本实施例中的线束和母端插座的连接示意图;
23.图5为本实施例中的线束和公端插头的连接示意图;
24.图6 为本实施例中的线束和母端插座及公端插头的装配示意图;
25.图7为本实施例中的线束和母端插座及公端插头装配成多层的示意图;
26.附图标记说明:1
‑
圆形导体;11
‑
圆形导体;12
‑
圆形绝缘层;3
‑
包扎物;
[0027]2‑
车用线束;21
‑
导体;22
‑
绝缘外皮;23
‑
导体焊接段;4
‑
母端插座;41
‑
母端端子;42
‑
母端插座铜基板;5
‑
公端插头;51
‑
公端端子。
具体实施方式
[0028]
传统的线束连接回路,由圆形导线进行连接,其结构形式如图1所示,本文仅从3个回路的连接方式来阐述传统结构与本实用新型的区别,其它数量可按此方式进行推演。传统的线束为采用圆形导线1,其由圆形导体11包裹圆形绝缘外皮12组成,多根圆形导线1组合在一起,并通过包覆物3将其包扎成一束,其包覆后的外形不规则,导线间间距较大,直接导致整个线束的外径增大,不利于整车环境下的空间布置。
[0029]
本实用新型实施例中,提供了一种车用线束2,通过调整线束内的导体结构,将导体由圆形设计为方形,形成如图2所示的截面形状呈扁平形(扁平线的具体形状可以是方形或者其它形状)的车用线束2,车用线束2由截面形状呈扁平形状的导体21和绝缘外皮22组
成,一根车用线束2中可以设置多根导体21。
[0030]
由于车用线束2中的导体21之间的间距可以根据需要进行设计,所以车用线束2不仅外观上可以保持良好的稳定性,同时导体21的位置也可以保持很好的稳定性,这样就给多根导体21同时连接至公端插头5或母端插座4提供了可行的位置准确度。
[0031]
本实施例中车用线束将不再采用现有端子与导线压接的方式进行电路连接,原因在于现有这种方式每根导体回路均需要单独连接,增加了制造时间。为此本实用新型实施例中还提供了一种实现两根线束连接的结构,采用超声波焊接的形式来实现两根线束之间的连接,首先将第一线束的导体21的导体焊接段23与母端插座4的母端插座铜基板42进行超声波焊接,然后将第二线束的导体21的导体焊接段23与公端插头5的公端插头铜基板进行超声波焊接;最后将公端插头5的公端端子51插入母端插座4内与母端端子41对接,实现第一线束和第二线束的连接。由于车用线束2中的各导体21位置精准度较高,可以对车用线束2中的所有导体21同时进行焊接,提高电路连接制造效率。
[0032]
在母端插座4中,母端端子41与母端插座铜基板42结构上设计连为一体,所以在导体21的导体焊接段23与母端插座铜基板42焊接后,车用线束2中的导体21中的某一回路就直接与母端插座4中的母端端子41相连,这样的连接方式就将传统的需要人工将端子插入到护套相应孔位的操作省去。将整个端子压接、压接、包装、存储、装运、调配、布线、插接的制造过程,精简只有超声波焊接这一个过程,同时也把大量需要人工参与的流程,直接过度到由机器一步执行到位。同理的,车用线束2在与公端插头5连接时,在公端插头5中,公端端子51与公端插头铜基板结构上设计连为一体,所以在导体21的导体焊接段23与公端插头铜基板焊接后,车用线束2中的导体21中的某一回路就直接与公端插头51中的公端端子51相连。
[0033]
在母端插座4与公端插头5的对插过程中,其配合结构形式同目前的设计方式,通过母端端子41与公端端子51的对接配合来实现。本实用新型的车用线束2可通过导体21的数量增加来实现回路数的扩展。同时也可以通过相同回路数的车用线束2叠加来实现连接回路的增加,而在接插件处则如图7通过多片母端插座4与公端插头5的叠加实现转接对插功能。
[0034]
本实用新型基于小线径的汽车线束,重新设计了线束内部的导体形状和实现两根线束连接的连接结构,可以实现传统导线的连接及对插功能,同时确保了线束外形的稳定,便于尺寸控制及工艺装配。在线束制造领域大幅度减少了工艺流程,将以前需要多步靠工人操作执行的端子压接到端子插接到护套中的过程,精简到由机器一步执行到位,提高了生产效率及降低制造成本。
[0035]
本实施例中,将车用线束2的截面形状设计为扁平形(优选为方形),使该车用线束2插入至宽度足够的缝隙中时,可以选择以图2中的方向水平插入;在插入至某些宽度很狭窄的缝隙中时,可以选择以纵向插入的方式插入,使该车用线束2能够插入至狭窄缝隙中。当车用线束2的截面形状设计为方形时,还可便于机器人夹持该车用线束2(原因在于,机器人的夹持部和车用线束2的接触方式为面接触,相对于圆形线束来说,增大了夹持时的接触面积)。
[0036]
此外,将导体21的截面形状设计为扁平形,可以使车用线束2的整体纵向高度变低;同时,扁平形的设计还便于导体21的导体焊接段23与母端插座铜基板42和公端插头铜
基板焊接(原因在于焊接的接触方式为面接触而非线接触)。
[0037]
本实用新型实施例还提供了一种汽车,该汽车包括上述的车用线束2、母端插座4和公端插头5连接后构成的车用线束连接结构。