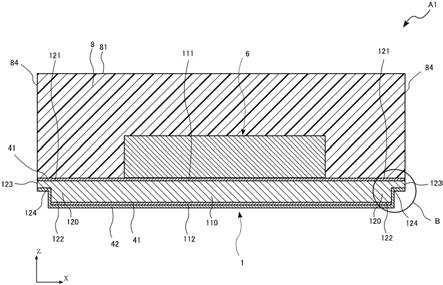
1.本发明涉及半导体器件和半导体器件的制造方法。
背景技术:2.关于具有半导体元件(晶体管等)的半导体器件,提案有各种各样的结构。作为半导体器件的一个例子,有利用密封树脂覆盖半导体元件而得的半导体器件。这样的半导体器件通过在引线框搭载半导体元件,用密封树脂覆盖该半导体元件(和引线框的一部分)之后,沿规定的切断线将引线框和密封树脂切断而制造。
3.具有上述的结构的半导体器件例如经由接合材料安装在电路板。此时,作为确认半导体器件是否恰当地安装于电路板的方法,优选能够从外部公开确认接合材料的状态。作为其一个例子,专利文献1例示了在半导体器件的背面(与电路板相对的面)的缘部设置倾斜部分的方式。具体而言,依照该文献的例示,在引线框搭载半导体元件而形成了密封树脂之后,将引线框从背面半切而形成倾斜的切断面。然后,在引线框的背面和切断面形成镀层,对引线框进行全切。
4.在专利文献1中公开的半导体器件的制造工艺中,除上述的工序以外,还包含利用导线将半导体元件的电极和引线框相连的导线接合工序。此外,在导线接合工序之前,为了提高接合导线的接合性,在引线框上例如形成银镀层。此时,为了防止由银镀层引起的引线框与密封树脂的紧贴性(密接性)下降,银镀层仅限于在供接合导线接合的区域形成。此外,在半切工序之前,为了抑制由于切削而在引线框产生毛刺,在引线框的背面例如形成锡镀层。然后,如上所述,在半切工序之后,为了覆盖由于半切而露出的切断面而再次形成锡镀层。也就是说,依照现有的制造方法,至少需要3次镀敷工序。
5.现有技术文献
6.专利文献
7.专利文献1:日本特开2005
‑
38927号公报
技术实现要素:8.发明要解决的技术问题
9.鉴于上述情况,本发明的目的在于提供能够简化制造工艺的半导体器件。
10.用于解决技术问题的技术方案
11.基于本发明提供的半导体器件包括:第1引线部,其具有在厚度方向上彼此朝向相反侧的第1主面及第1背面、和从上述第1背面凹向上述第1主面侧的第1凹部;搭载于上述第1主面的半导体元件;覆盖上述半导体元件的密封树脂部;与上述第1主面和上述第1背面接触地形成的第1镀层;以及第2镀层。上述第1凹部从上述密封树脂部露出。上述第1镀层具有覆盖上述第1背面的第1部分。上述第2镀层与上述第1凹部和上述第1部分接触地形成。依照这样的构成,能够通过第1镀层的形成和第2镀层的形成这2次镀敷工序,来制造半导体器件,实现制造工艺的简化。
12.本发明的其它特征和优点,能够通过参照附图在以下进行的详细的说明来进一步明确。
附图说明
13.图1是表示第1实施方式的半导体器件的立体图。
14.图2是图1所示的半导体器件的立体图,表示以底面侧为上侧时的状态。
15.图3是图1所示的半导体器件的俯视图。
16.图4是图1所示的半导体器件的底视图。
17.图5是沿图3的v
‑
v线的截面图。
18.图6是沿图3的vi
‑
vi线的截面图。
19.图7是沿图3的vii
‑
vii线的截面图。
20.图8是图1所示的半导体器件的主要部分放大截面图。
21.图9是表示图1所示的半导体器件的制造工艺的俯视图。
22.图10是表示图1所示的半导体器件的制造工艺的截面图。
23.图11是表示图1所示的半导体器件的制造工艺的俯视图。
24.图12是表示图1所示的半导体器件的制造工艺的截面图。
25.图13是表示图1所示的半导体器件的制造工艺的截面图。
26.图14是表示图1所示的半导体器件的制造工艺的截面图。
27.图15是表示图1所示的半导体器件的制造工艺的截面图。
28.图16是表示图1所示的半导体器件的制造工艺的截面图。
29.图17是表示图1所示的半导体器件的变形例的主要部分放大截面图。
30.图18是表示图1所示的半导体器件的变形例的主要部分放大截面图。
31.图19是表示图1所示的半导体器件的变形例的主要部分放大截面图。
32.图20是表示第2实施方式的半导体器件的立体图,表示以底面侧为上侧时的状态。
33.图21是图20所示的半导体器件的底视图。
34.图22是表示图20所示的半导体器件的制造工艺的俯视图。
35.图23是表示图20所示的半导体器件的制造工艺的底视图。
36.图24是表示第3实施方式的半导体器件的截面图。
37.图25是表示第4实施方式的半导体器件的俯视图。
具体实施方式
38.以下,参照附图,对本发明的优选实施方式具体地进行说明。
39.基于图1~图7,说明本发明的第1实施方式的半导体器件a1。图示的半导体器件a1包括多个引线部1~3、半导体元件6、接合导线(bonding wire:接合导线)71、72和密封树脂部8。
40.图1是表示半导体器件a1的立体图。图2是表示半导体器件a1的立体图,是以底面侧为上侧时的状态的图。图3是表示半导体器件a1的俯视图。在图3中,为了便于理解,透视密封树脂部8,用假想线(二点划线)表示密封树脂部8的外形。图4是表示半导体器件a1的底视图。图5是沿图3的v
‑
v线的截面图。图6是沿图3的vi
‑
vi线的截面图。图7是沿图3的vii
‑
vii线的截面图。图8是将图5的圆圈b的部分放大的主要部分放大截面图。
41.半导体器件a1是能够表面安装在各种设备的电路板的装置。半导体器件a1的厚度方向观察时的形状为矩形。为了便于说明,以半导体器件a1的厚度方向为z方向,以沿与z方向正交的半导体器件a1的一个边的方向(图3中的左右方向)为x方向,以与z方向和x方向正交的方向(图3中的上下方向)为y方向。半导体器件a1的大小没有特别限定,在图示的例子中,例如x方向尺寸为1~3mm程度,y方向尺寸为1~3mm程度,z方向尺寸为0.3~1mm程度。
42.如图3所示,引线部1(第1引线部)支承半导体元件6,引线部2、3(第2、第3引线部)经由接合导线(后述)与半导体元件6导通。引线部1~3例如通过对金属板实施冲压加工、蚀刻处理等来形成。引线部1~3由金属构成,优选由cu和ni中的任一者、或者它们的合金及42合金等构成。在图示的例子中,引线部1~3由cu构成。引线部1~3的厚度例如为0.08~0.3mm,在图示的例子中为0.2mm程度。
43.如图3所示,第1引线部1配置在半导体器件a1的y方向的一端(在图3中为上侧),向整个x方向扩展。第2引线部2和第3引线部3,分别与第1引线部1隔开间隔并且在x方向上并排且彼此隔开间隔地配置在半导体器件a1的y方向的另一端(在图3中为下侧)。z方向观察时的尺寸(面积)为,第1引线部1最大,第3引线部3最小。
44.在图示的例子中,第1引线部1包括搭载部110、多个端子部120和多个连结部130。
45.搭载部110在z方向观察时为大致矩形形状。搭载部110具有搭载部主面111、搭载部背面112和搭载部凹部113。搭载部主面111和搭载部背面112在z方向上彼此朝向相反侧。搭载部主面111是朝向图5~图7的上方的面。搭载部主面111是搭载半导体元件6的面。搭载部背面112是朝向图5~图7的下方的面。搭载部背面112从密封树脂部8露出,成为背面端子。搭载部凹部113是搭载部110的一部分从搭载部背面112向搭载部主面111侧凹陷的部分。搭载部110中的搭载部凹部113所在的部分的厚度(z方向的尺寸),为搭载部背面112所在的部分的厚度的一半程度。搭载部凹部113例如通过半蚀刻处理形成。如图7所示,搭载部凹部113不从密封树脂部8露出,而被密封树脂部8覆盖。由此,能够抑制第1引线部1从密封树脂部8剥离。搭载部110的形状并不限定于图示的例子。搭载部110也可以不具有搭载部凹部113。
46.端子部120与搭载部110相连,z方向观察时为大致矩形形状。端子部120在搭载部110的x方向的两个端面各配置2个,合计配置有4个。各端子部120具有端子部主面121、端子部背面122、端子部端面123和端子部凹部124。端子部主面121和端子部背面122在z方向上彼此朝向相反侧。端子部主面121是朝向图5~图7的上方的面。端子部主面121与搭载部主面111成为一个面。端子部背面122是朝向图5~图7的下方的面。端子部背面122与搭载部背面112成为一个面。端子部端面123是与端子部主面121和端子部背面122正交,并与端子部主面121相连的面,是朝向x方向外侧的面。端子部端面123通过后述的制造工艺的第1切断工序中的全切割形成。端子部凹部124从端子部背面122向端子部主面121侧凹陷,位于端子部背面122的x方向外侧的端缘,延伸至y方向的两端。端子部凹部124与端子部背面122和端子部端面123相连。端子部凹部124通过后述的制造工艺的槽部形成工序中的半切割形成。端子部端面123、端子部背面122和端子部凹部124分别从密封树脂部8露出而彼此相连,成为端子(参照图4和图5)。端子部120的形状、配置位置和个数没有限定。
47.连结部130与搭载部110相连,z方向观察时为大致矩形形状。连结部130在搭载部
110的y方向的一个端面(在图3中为朝向上方的端面)在x方向上排列地配置有3个。连结部130的厚度(z方向的尺寸),为与搭载部凹部113所在的搭载部110的厚度相同程度的厚度。连结部130例如通过半蚀刻处理形成。各连结部130具有连结部主面131、连结部背面132和连结部端面133。连结部主面131和连结部背面132在z方向上彼此朝向相反侧。连结部主面131是朝向图5~图7的上方的面。连结部主面131与搭载部主面111成为一个面。因此,搭载部主面111、端子部主面121和连结部主面131成为成了一个面的一体的面(参照图3)。连结部背面132是朝向图5~图7的下方的面。连结部背面132与搭载部凹部113成为一个面。连结部端面133是将连结部主面131和连结部背面132相连的面,是朝向y方向外侧的面。连结部端面133通过后述的制造工艺的第2切断工序中的全切割形成。连结部端面133从密封树脂部8露出。连结部130的形状、配置位置和个数没有限定。
48.如图5、图7和图8所示,第1引线部1的表面的大部分被第1镀层41覆盖。具体而言,第1引线部1的搭载部主面111、端子部主面121和连结部主面131被第1镀层41覆盖,且第1引线部1的搭载部背面112、搭载部凹部113、端子部背面122和连结部背面132被第1镀层41覆盖。如图8所示,第1镀层41是将镍镀层(内侧层)411、钯镀层(中间层)412和金镀层(外侧层)413而得到的层。
49.镍镀层411以与第1引线部1接触的方式形成。镍镀层411由ni或ni合金构成。在镍镀层411的表面(与第1引线部1相反侧的面),也可以形成有粗糙的镍层。镍镀层411的厚度例如为0.5μm~2.0μm。钯镀层412以与镍镀层411接触且重叠的方式形成。钯镀层412的厚度例如为0.01μm~0.15μm。金镀层413以与钯镀层412接触且重叠的方式形成。金镀层413的厚度例如为0.003μm~0.015μm。第1镀层41的构成没有限定。
50.如后所述,在制造工艺中,在引线框的整个面形成第1镀层41,不过因为端子部端面123和连结部端面133是在第1切断工序或第2切断工序中被切断的切断面,因此没有形成第1镀层41。
51.如图5和图7所示,第1镀层41具有形成于搭载部背面112和端子部背面122的部分(“第1部分”)。在该第1镀层41的第1部分和端子部凹部124,形成有第2镀层42。第2镀层42由与作为第1引线部1的母材的cu相比焊料润湿性高的材料形成。第2镀层42由以sn为主成分的合金构成。作为该合金,具体而言为sn
‑
sb类合金或sn
‑
ag类合金等的无铅焊料。第2镀层42的构成没有限定。
52.虽然在端子部端面123没有形成第1镀层41和第2镀层42,但是在端子部凹部124形成有第2镀层42。因此,在将半导体器件a1安装于电路板的情况下,在端子部凹部124的第2镀层42形成焊接圆角。由此,能够提高半导体器件a1在电路板的安装强度。此外,能够通过外观检查容易地判断安装后的第1引线部1与电路板的接合状态。
53.第2引线部2在z方向观察时,配置在半导体器件a1的角部(在图3中为右下的角部),包括导线接合部210、端子部220和连结部230。
54.导线接合部210在z方向观察时为x方向上较长的大致矩形形状,在第2引线部2中位于第1引线部1侧。导线接合部210具有导线接合部主面211、导线接合部背面212和导线接合部凹部213。导线接合部主面211和导线接合部背面212在z方向上彼此朝向相反侧。导线接合部主面211是朝向图5~图7的上方的面。导线接合部主面211是供接合导线71接合的面。导线接合部背面212是朝向图5~图7的下方的面。导线接合部背面212从密封树脂部8露
出,成为背面端子。导线接合部凹部213是导线接合部210的一部分从导线接合部背面212向导线接合部主面211侧凹陷的部分。导线接合部210中导线接合部凹部213所在的部分的厚度(z方向的尺寸)为导线接合部背面212所在的部分的厚度的一半程度。导线接合部凹部213例如通过半蚀刻处理形成。如图6和图7所示,导线接合部凹部213不从密封树脂部8露出,而被密封树脂部8覆盖。由此,能够抑制第2引线部2从密封树脂部8剥离。导线接合部210的形状没有限定。例如,也可以没有导线接合部凹部213。
55.端子部220与导线接合部210相连,z方向观察时为大致矩形形状。端子部220位于导线接合部210的与第3引线部相反侧,在x方向的一个端面(在图3中为右侧的端面)配置有1个。端子部220具有端子部主面221、端子部背面222、端子部端面223和端子部凹部224。端子部主面221和端子部背面222在z方向上彼此朝向相反侧。端子部主面221是朝向图5~图7的上方的面。端子部主面221与导线接合部主面211成为一个面。端子部背面222是朝向图5~图7的下方的面。端子部背面222与导线接合部背面212成为一个面。端子部端面223是与端子部主面221和端子部背面222正交,且与端子部主面221相连的面,是朝向x方向外侧的面。端子部端面223通过后述的制造工艺的第1切断工序中的全切割形成。端子部凹部224从端子部背面222向端子部主面221侧凹陷,位于端子部背面222的x方向外侧的端缘,延伸至y方向的两端。端子部凹部224与端子部背面222和端子部端面223相连。端子部凹部224通过后述的制造工艺的槽部形成工序中的半切割形成。端子部端面223、端子部背面222和端子部凹部224分别从密封树脂部8露出而彼此相连,成为端子(参照图4和图6)。端子部220的形状、配置位置和个数没有限定。
56.连结部230与导线接合部210相连,z方向观察时为大致矩形形状。连结部230在导线接合部210的y方向的一个端面(在图3中为朝向下方的端面),在x方向上并排地配置有2个。连结部230的厚度(z方向的尺寸)为与导线接合部凹部213所在的导线接合部210的厚度相同程度的厚度。连结部230例如通过半蚀刻处理形成。各连结部230具有连结部主面231、连结部背面232和连结部端面233。连结部主面231和连结部背面232在z方向上彼此朝向相反侧。连结部主面231是朝向图5~图7的上方的面。连结部主面231与导线接合部主面211成为一个面。因此,导线接合部主面211、端子部主面221和连结部主面231成为成了一个面的一体的面(参照图3)。连结部背面232是朝向图5~图7的下方的面。连结部背面232与导线接合部凹部223成为一个面。连结部端面233是将连结部主面231和连结部背面232相连的面,是朝向y方向外侧的面。连结部端面233通过后述的制造工艺的第2切断工序中的全切割形成。连结部端面233从密封树脂部8露出。连结部230的形状、配置位置和个数没有限定。
57.如图6和图7所示,在第2引线部2的表面中的导线接合部主面211、端子部主面221、连结部主面231、导线接合部背面212、导线接合部凹部213、端子部背面222和连结部背面232,形成有第1镀层41。第1镀层41是与形成于第1引线部1的第1镀层41相同的层。如后所述,在制造工艺中,在引线框的整个面形成第1镀层41,不过由于端子部端面223和连结部端面233是在第1切断工序或第2切断工序中被切断的切断面,因此没有形成第1镀层41。
58.如图6和图7所示,第1镀层41具有在导线接合部背面212和端子部背面222形成的部分(“第2部分”)。在该第1镀层41的第2部分和端子部凹部224,形成有第2镀层42。第2镀层42与形成于第1引线部1的第2镀层42相同。
59.虽然在端子部端面223没有形成第1镀层41和第2镀层42,但是在端子部凹部224形
成有第2镀层42。因此,在将半导体器件a1安装于电路板的情况下,在端子部凹部224的第2镀层42形成焊接圆角。由此,能够提高半导体器件a1在电路板的安装强度。此外,能够通过外观检查容易地判断安装后的第2引线部2与电路板的接合状态。
60.第3引线部3在z方向观察时,配置在半导体器件a1的角部(在图3中为左下的角部),包括导线接合部310、端子部320和连结部330。
61.导线接合部310在z方向观察时为大致矩形形状,在第3引线部3中位于第1引线部1侧。导线接合部310具有导线接合部主面311、导线接合部背面312和导线接合部凹部313。导线接合部主面311和导线接合部背面312在z方向上彼此朝向相反侧。导线接合部主面311是朝向图5~图7的上方的面。导线接合部主面311是供接合导线72接合的面。导线接合部背面312是朝向图5~图7的下方的面。导线接合部背面312从密封树脂部8露出,成为背面端子。导线接合部凹部313是导线接合部310的一部分从导线接合部背面312向导线接合部主面311侧凹陷的部分。导线接合部310中的导线接合部凹部313所在的部分的厚度(z方向的尺寸)为导线接合部背面312所在的部分的厚度的一半程度。导线接合部凹部313例如通过半蚀刻处理形成。如图6所示,导线接合部凹部313不从密封树脂部8露出,而被密封树脂部8覆盖。由此,能够抑制第2引线部2从密封树脂部8剥离。此外,导线接合部310的形状没有限定。例如,也可以没有导线接合部凹部313。
62.端子部320与导线接合部310相连,z方向观察时为大致矩形形状。端子部320位于导线接合部310的与第3引线部相反侧,在x方向的一个端面(在图3中为左侧的端面)配置有1个。端子部320具有端子部主面321、端子部背面322、端子部端面323和端子部凹部324。端子部主面321和端子部背面322在z方向上彼此朝向相反侧。端子部主面321是朝向图5~图7的上方的面。端子部主面321与导线接合部主面311成为一个面。端子部背面322是朝向图5~图7的下方的面。端子部背面322与导线接合部背面312成为一个面。端子部端面323是与端子部主面321和端子部背面322正交,且与端子部主面321相连的面,是朝向x方向外侧的面。端子部端面323通过后述的制造工艺的第1切断工序中的全切割形成。端子部凹部324从端子部背面322向端子部主面321侧凹陷,位于端子部背面322的x方向外侧的端缘,延伸至y方向的两端。端子部凹部324与端子部背面322和端子部端面323相连。端子部凹部324通过后述的制造工艺的槽部形成工序中的半切割形成。端子部端面323、端子部背面322和端子部凹部324从密封树脂部8露出而彼此相连,成为端子(参照图4和图6)。端子部320的形状、配置位置和个数没有限定。
63.连结部330与导线接合部310相连,z方向观察时为大致矩形形状。连结部330在导线接合部310的y方向的一个端面(在图3中为朝向下方的端面)配置有1个。连结部330的厚度(z方向的尺寸)为与导线接合部凹部313所在的导线接合部310的厚度相同程度的厚度。连结部330例如通过半蚀刻处理形成。连结部330具有连结部主面331、连结部背面332和连结部端面333。连结部主面331和连结部背面332在z方向上彼此朝向相反侧。连结部主面331是朝向图5~图7的上方的面。连结部主面331与导线接合部主面311成为一个面。因此,导线接合部主面311、端子部主面321和连结部主面331成为成了一个面的一体的面(参照图3)。连结部背面332是朝向图5~图7的下方的面。连结部背面332与导线接合部凹部323成为一个面。连结部端面333是将连结部主面331和连结部背面332相连的面,是朝向y方向外侧的面。连结部端面333通过后述的制造工艺的第2切断工序中的全切割形成。连结部端面333从
密封树脂部8露出。连结部330的形状、配置位置和个数没有限定。
64.如图6所示,在第3引线部3的表面中的导线接合部主面311、端子部主面321、连结部主面331、导线接合部背面312、导线接合部凹部313、端子部背面322和连结部背面332,形成有第1镀层41。第1镀层41是与形成于第1引线部1的第1镀层41相同的层。如后所述,在制造工艺中,在引线框的整个面形成第1镀层41,不过由于端子部端面323和连结部端面333是在第1切断工序或第2切断工序中被切断的切断面,因此没有形成第1镀层41。
65.如图6所示,在形成于导线接合部背面312和端子部背面322的第1镀层41和端子部凹部324,形成有第2镀层42。第2镀层42是与形成于第1引线部1的第2镀层42相同的层。
66.虽然在端子部端面323没有形成第1镀层41和第2镀层42,但是在端子部凹部324形成有第2镀层42。因此,在将半导体器件a1安装于电路板的情况下,在端子部凹部324的第2镀层42形成焊接圆角。由此,能够提高半导体器件a1在电路板的安装强度。此外,能够通过外观检查容易地判断安装后的第3引线部3与电路板的接合状态。
67.半导体元件6是发挥半导体器件a1的电气功能的要素。半导体元件6的种类没有特别限定。例如,半导体元件6为mosfet(metal
‑
oxide
‑
semiconductor field
‑
effect transistor:金属氧化物半导体场效应晶体管)等晶体管。半导体元件6具有元件主体60、第1电极61、第2电极62和第3电极63。
68.第1电极61和第2电极62设置在元件主体60中的朝向与第1引线部1相反侧的面。第3电极63设置在元件主体60中的与第1引线部1相对的面。在图示的例子中,第1电极61是栅极电极,第2电极62是源极电极,第3电极63是漏极电极。
69.半导体元件6经由未图示的导电性接合材料,搭载在形成有第1镀层41的第1引线部1的搭载部主面111的中央。由此,半导体元件6的第3电极63由导电性接合材料与第1引线部1电连接。接合导线71与半导体元件6的第1电极61和形成有第1镀层41的第3引线部3的导线接合部主面311连接。由此,半导体元件6的第1电极61与第3引线部3电连接。多个接合导线72与半导体元件6的第2电极62和形成有第1镀层41的第2引线部2的导线接合部主面211连接。由此,半导体元件6的第2电极62与第2引线部2电连接。
70.上述的半导体元件6的结构和与各引线部1~3的连接方法只是一个例子。半导体元件6的种类、搭载数量和配置没有限定,连接方法也没有限定。
71.密封树脂部8覆盖引线部1~3各自的一部分、半导体元件6和接合导线71、72。密封树脂部8例如由黑色的环氧树脂构成。
72.密封树脂部8具有树脂主面81、树脂背面82、树脂第1侧面83、树脂第2侧面84和树脂凹部85。树脂主面81与树脂背面82在z方向上彼此朝向相反侧。树脂主面81是朝向图5~图7的上方的面,树脂背面82是朝向图5~图7的下方的面。树脂第1侧面83是将树脂主面81和树脂背面82相连的面,是朝向y方向的外侧的面。树脂第1侧面83通过后述的制造工艺的第2切断工序中的全切割形成。树脂第2侧面84是与树脂主面81和树脂背面82正交,且与树脂主面81相连的面,是朝向x方向的外侧的面。树脂第2侧面84通过后述的制造工艺的第1切断工序中的全切割形成。树脂凹部85从树脂背面82向树脂主面81侧凹陷,分别设置在树脂背面82的x方向的两端缘,延伸至y方向的两端。树脂凹部85与树脂背面82和树脂第2侧面84相连。树脂凹部85通过后述的制造工艺的槽部形成工序中的半切割形成。
73.第1引线部1的各连结部端面133与一个(在图4中为下侧的)树脂第1侧面83彼此成
为一个面,第2引线部2的各连结部端面233和第3引线部3的连结部端面333与另一个(在图4中为上侧的)树脂第1侧面83彼此成为一个面。第1引线部1的x方向的一侧(在图4中为右侧)的各端子部端面123和第2引线部2的端子部端面223与一侧(在图4中为右侧)的树脂第2侧面84彼此成为一个面。第1引线部1的x方向的另一侧(在图4中为左侧)的各端子部端面123和第3引线部3的端子部端面323与另一侧(在图4中为左侧)的树脂第2侧面84彼此成为一个面。
74.下面,参照图9~图16,在下文中对半导体器件a1的制造方法的一个例子进行说明。
75.首先,如图9所示准备引线框900(准备工序)。引线框900是要形成各引线部1~3的板状的材料。在图示的例子中,引线框900的母材由cu构成。例如,引线框900通过对金属板实施蚀刻处理而形成。此外,引线框900也可以通过其它方法形成,例如通过对金属板实施冲压加工而形成。引线框900具有主面901、背面902、凹部903和贯通孔906。
76.主面901和背面902在z方向上彼此朝向相反侧。主面901是朝向图10的上方的面,是成为第1引线部1的搭载部主面111、端子部主面121和连结部主面131、第2引线部2的导线接合部主面211、端子部主面221和连结部主面231、第3引线部3的导线接合部主面311、以及端子部主面321和连结部主面331的面。背面902是朝向图10的下方的面,是成为第1引线部1的搭载部背面112和端子部背面122、第2引线部2的导线接合部背面212和端子部背面222、以及第3引线部3的导线接合部背面312和端子部背面322的面。
77.凹部903是从背面902向主面901侧凹陷的部分,例如通过半蚀刻处理形成。凹部903是成为第1引线部1的搭载部凹部113和连结部背面132、第2引线部2的导线接合部凹部213和连结部背面232、以及第3引线部3的导线接合部凹部313和连结部背面332的面。在图9中,用虚线表示背面902与凹部903的边界线。贯通孔906是从主面901贯通至背面902或凹部903的部分,例如通过蚀刻处理形成。在作为引线框900的母材的板材,从主面901侧和背面902侧进行了蚀刻处理的部分贯通而成为贯通孔906,仅从背面902侧进行了蚀刻处理的部分成为凹部903。
78.在图9中,施加了比较稀疏的阴影线的区域中的、在y方向上延伸的区域,是在后述的第1切断工序中要除去的第1除去区域s1。第1除去区域s1被设定成,在引线框900的在x方向上相邻的要成为第1引线部1的部分之间在y方向上延伸。施加了比较稀疏的阴影线的区域中的、在x方向上延伸的区域,是在后述的第2切断工序中要除去的第2除去区域s2。第2除去区域s2被设定成,在引线框900的相邻的要形成半导体器件a1的部分之间在x方向产延伸。在图9中,将施加了比较密集的阴影线的区域和施加了比较稀疏的阴影线的在y方向上延伸的区域(第1除去区域s1)合在一起的区域,是在后述的槽部形成工序中在背面902要形成槽部的槽部形成区域s3。槽部形成区域s3被设定成,在引线框900的在x方向上相邻的要成为第1引线部1的部分之间在y方向上延伸。槽部形成区域s3的x方向的尺寸即宽度比第1除去区域s1的宽度大,且在x方向的中央包含第1除去区域s1。即,第1除去区域s1的宽度比槽部形成区域s3窄,其整个与槽部形成区域s3重叠。
79.接着,如图10所示,在引线框900的整个面形成第1镀层911(第1镀敷工序)。第1镀层911通过将引线框900作为导电路径的电镀形成。第1镀层911也可以通过无电镀(化学镀)形成。在图示的例子中,第1镀层911通过依次层叠镍镀层411、钯镀层412和金镀层413而形
成。第1镀层911在主面901、背面902、凹部903和贯通孔906的侧面形成。第1镀层911成为第1镀层41。
80.接着,如图11所示,在引线框900搭载半导体元件6(搭载工序)。在搭载工序中,首先,在引线框900的主面901中,在成为第1引线部1的搭载部主面111的部分,利用导电性接合材料将半导体元件6接合。接着,将接合导线72与半导体元件6的第1电极61和成为第3引线部3的导线接合部主面311的部分接合,将多个接合导线71与半导体元件6的第2电极62和成为第2引线部2的导线接合部主面211的部分接合。此时,由于在引线框900的主面901形成有第1镀层911,因此接合导线71、72的接合性良好。
81.接着,如图12所示,通过使树脂材料固化,形成覆盖引线框900的一部分、半导体元件6和接合导线71、72的密封树脂920(树脂形成工序)。密封树脂920例如由黑色的环氧树脂构成。在树脂形成工序中,在使引线框900的背面902与模具抵接状态下使流动化的树脂材料流入模具,因此引线框900的背面902从密封树脂920露出,引线框900的背面902与密封树脂920的跟背面902朝向相同方向的面,彼此成为一个面。由于树脂材料流入模具与凹部903之间,因此凹部903被密封树脂920覆盖。密封树脂920成为密封树脂部8。
82.接着,如图13所示,形成槽部904(槽部形成工序)。槽部904是从引线框900的背面902侧向主面901侧凹陷,且在y方向上延伸的槽,在与图9所示的槽部形成区域s3对应的位置形成。槽部904跨引线框900和密封树脂920形成。槽部904具有底面904a和侧面904b。底面904a是与引线框900的背面902朝向相同方向的面。侧面904b是将引线框900的背面902和朝向跟背面902相同的方向的密封树脂920的面与底面904a相连的面。在引线框900中的要成为第1引线部1的端子部120的部分形成的槽部904,成为端子部凹部124,在要成为第2引线部2的端子部220的部分形成的槽部904,成为端子部凹部224,在要成为第3引线部3的端子部320的部分形成的槽部904,成为端子部凹部324。此外,在密封树脂920形成的槽部904中的一部分,成为树脂凹部85。
83.槽部形成工序,如图12所示,通过利用第1刀片951切削引线框900的背面902的半切割处理来进行。第1刀片951的厚度(x方向的尺寸)与槽部形成区域s3的x方向的尺寸一致。在该半切割处理中,从背面902侧切削与图9所示的槽部形成区域s3相应的部分。此外,在该半切割处理中,将切削进行至引线框900的z方向的中途(参照图12中用二点划线表示的第1刀片951)。切削的深度例如为引线框900的厚度(z方向的尺寸)的一半以上,作为一个例子为4分之3程度。在图示的例子中,由于在引线框900的背面902形成有第1镀层911,因此能够抑制由引线框900的切削引起的毛刺的产生。在槽部形成工序中,也可以通过利用刀片的半切割以外的方法形成槽部904。
84.接着,如图14所示,形成第2镀层912(第2镀敷工序)。第2镀层912通过将引线框900作为导电路径的电镀形成。第2镀层912也可以通过无电镀形成。第2镀层912形成在引线框900中的从密封树脂920露出的部分,即形成于背面902的第1镀层911、以及位于槽部904的底面904a和侧面904b的部分。第2镀层912成为第2镀层42。
85.接着,如图15所示,在密封树脂920的、与引线框900的主面901朝向相同方向的面,粘贴保护胶带970。保护胶带970在后述的第1切断工序和第2切断工序中,防止各个片四散开。
86.接着,如图16所示,不将保护胶带970切断,而将引线框900和密封树脂920沿y方向
切断(第1切断工序)。第1切断工序如图15所示,通过从引线框900的背面902侧起利用第2刀片952进行切削的全切割处理来进行。第2刀片952的厚度(x方向的尺寸)与第1除去区域s1的x方向的尺寸一致,比槽部形成工序中使用的第1刀片951的厚度薄。在该全切割处理中,从背面902侧起,将与图9所示的第1除去区域s1相应的部分切削至到达保护胶带970。因此,引线框900和密封树脂920的、z方向观察时与第1除去区域s1重叠的部分,在z方向的整个区域被除去。由此,在引线框900形成朝向x方向的切断面。这些切断面中的在成为第1引线部1的端子部120的部分形成的切断面,成为端子部端面123,在成为第2引线部2的端子部220的部分形成的切断面,成为端子部端面223,在成为第3引线部3的端子部320的部分形成的切断面,成为端子部端面323。在密封树脂920形成的切断面,成为树脂第2侧面84。在图示的例子中,由于在引线框900的槽部904形成有第2镀层912,因此能够抑制由引线框900的切削引起的毛刺的产生。在第1切断工序中,也可以通过利用刀片的全切割以外的方法来进行切断。例如,也可以在第1切断工序中,通过等离子体切割或激光切割来进行切断。通过第1切断工序,引线框900和密封树脂920在x方向上被分割。
87.接着,不切断保护胶带970,而将引线框900和密封树脂920沿x方向切断(第2切断工序)。在图示的例子中,第2切断工序通过从引线框900的背面902侧起利用第2刀片952进行切削的全切割处理来进行。在该全切割处理中,从背面902侧起,切削与图9所示的第2除去区域s2相应的部分。因此,引线框900和密封树脂920的、z方向观察时与第2除去区域s2重叠的部分,在z方向的整个区域被除去。由此,在引线框900形成朝向y方向的切断面。这些切断面中的在成为第1引线部1的端子部130的部分形成的切断面,成为端子部端面133,在成为第2引线部2的端子部230的部分形成的切断面,成为端子部端面233,在成为第3引线部3的端子部330的部分形成的切断面,成为端子部端面333。在密封树脂920形成的切断面,成为树脂第1侧面83。由于在引线框900的凹部903形成有第1镀层911,因此能够抑制由引线框900的切削引起的毛刺的产生。在第2切断工序中,也可以通过利用刀片的全切割以外的方法来进行切断。例如,也可以在第2切断工序中,通过等离子体切割或激光切割来进行切断。通过第2切断工序,引线框900和密封树脂920在y方向上被分割,成为各半导体元件6这多个片由保护胶带970相连的状态。
88.接着,剥离保护胶带970。由此,分割为各半导体元件6这多个片。通过经过以上的工序,得到图1~图7所示的半导体器件a1。
89.下面,对半导体器件a1的作用效果进行说明。
90.依照上述的实施方式,第1镀层41与引线部1~3的各主面和各背面接触地形成。第1镀层41是在第1镀敷工序中,在引线框900的整个面形成的层。此外,第2镀层42与形成于引线部1~3的各背面的第1镀层41和各端子部凹部124、224、324接触地形成。第2镀层42是在第2镀敷工序中,在形成于引线框900的背面902的第1镀层911和槽部904形成的层。半导体器件a1通过第1镀敷工序和第2镀敷工序这2次镀敷工序制造。因此,与需要3次镀敷工序的现有的半导体器件相比,能够简化制造工艺。此外,在第1镀敷工序中,在引线框900的整个面形成第1镀层911,而不需要掩模。由此,与仅限定于在供接合导线接合的区域形成银镀层的情况相比,能够抑制制造成本。
91.依照上述的实施方式,在第1镀敷工序中在引线框900的背面902形成第1镀层911。因此,在槽部形成工序中,能够抑制由引线框900的切削引起的毛刺的产生。此外,在第2镀
敷工序中在槽部904的底面904a形成第2镀层912。因此,在第1切断工序中,能够抑制由引线框900的切削引起的毛刺的产生。此外,在第1镀敷工序中在引线框900的凹部903形成有第1镀层911,因此在第2切断工序中,也能够抑制由引线框900的切削引起的毛刺的产生。
92.依照上述的实施方式,在第1镀敷工序中在引线框900的主面901形成第1镀层911。由此,在导线接合部主面211和导线接合部主面311形成有第1镀层41。因此,接合导线71、72的接合性良好。
93.依照上述的本实施方式,第2镀层42形成于各端子部凹部124、224、324。因此,在将半导体器件a1安装于电路板的情况下,在各端子部凹部124、224、324的第2镀层42形成焊接圆角。由此,能够提高半导体器件a1在电路板的安装强度。此外,能够通过外观检查容易地判断安装后的各引线部1~3与电路板的接合状态。
94.在上述的实施方式中,第1镀层41是层叠了镍镀层411、钯镀层412和金镀层413的层。与此不同,也可以如图17所示,第1镀层41是没有层叠钯镀层412,而层叠了镍镀层411和金镀层413的层。此外,也可以如图18所示,第1镀层41是没有层叠金镀层413,而层叠了镍镀层411和钯镀层412的层。此外,也可以如图19所示,第1镀层41可以不是层叠了多个镀层的层,可以仅由1个镀层形成。例如,第1镀层41也可以由以sn为主成分的合金等形成。第1镀层41只要比直接切削引线框900时更能够抑制毛刺的产生即可。第1镀层41优选与引线部1~3(引线框900)的紧贴性高,且接合导线71、72的接合性高。
95.在上述的实施方式中,第2镀层42由以sn为主成分的合金构成,不过本发明并不限定于此。第2镀层42例如也可以由以au为主成分的合金等形成。此外,第2镀层42也可以为层叠了镍镀层411、钯镀层412和金镀层413的层等。第2镀层42只要是焊料润湿性比引线部1~3(引线框900)的母材高的材料即可。
96.基于图20~图23,对本发明的第2实施方式的半导体器件a2进行说明。在各图中,对与上述的半导体器件a1相同或类似的要素标注相同的附图标记,而省略重复的说明。图20是表示半导体器件a2的立体图,是以底面侧为上侧的状态的图。图21是表示半导体器件a2的底视图。图22是表示半导体器件a2的制造方法的工序的俯视图。图23是表示半导体器件a2的制造方法的工序的底视图。
97.关于图示的半导体器件a2,各端子部120、220、320在半导体器件a1的y方向的端部也有配置,形成于底面侧的凹部不仅在x方向的两个端部而且在y方向的两个端部也有配置,在这方面,图示的半导体器件a2与第1实施方式的半导体器件a1不同。
98.在半导体器件a2中,第1引线部1的端子部120不仅在x方向的两个端部而且在y方向的端部也有配置。即,代替连结部130而配置有端子部120。配置于y方向的端部的端子部120,在端子部背面122的y方向外侧的端缘形成有端子部凹部124。该端子部凹部124通过后述的制造工艺的第2槽部形成工序中的半切割形成。在配置于y方向的端部的端子部120,端子部端面123、端子部背面122和端子部凹部124也从密封树脂部8露出而相连,成为端子(参照图21)。在端子部主面121和端子部背面122,形成有第1镀层41,在形成于端子部背面122的第1镀层41和端子部凹部124,形成有第2镀层42。
99.在半导体器件a2中,第2引线部2的端子部220不仅在x方向的端部而且在y方向的端部也有配置。即,代替连结部230而配置有端子部220。配置于y方向的端部的端子部220,在端子部背面222的y方向外侧的端缘形成有端子部凹部224。该端子部凹部224通过后述的
制造工艺的第2槽部形成工序中的半切割形成。在配置于y方向的端部的端子部220,端子部端面223、端子部背面222和端子部凹部224也从密封树脂部8露出而相连,成为端子(参照图21)。在端子部主面221和端子部背面222,形成有第1镀层41,在形成于端子部背面222的第1镀层41和端子部凹部224,形成有第2镀层42。
100.在半导体器件a2中,第3引线部3的端子部320不仅在x方向的端部而且在y方向的端部也有配置。即,代替连结部330而配置有端子部320。配置于y方向的端部的端子部320,在端子部背面322的y方向外侧的端缘形成有端子部凹部324。该端子部凹部324通过后述的制造工艺的第2槽部形成工序中的半切割形成。在配置于y方向的端部的端子部320,端子部端面323、端子部背面322和端子部凹部324也从密封树脂部8露出而相连,成为端子(参照图21)。此外,在端子部主面321和端子部背面322,形成有第1镀层41,在形成于端子部背面322的第1镀层41和端子部凹部324,形成有第2镀层42。
101.在半导体器件a2中,密封树脂部8具有树脂凹部86。树脂凹部86从树脂背面82向树脂主面81侧凹陷,分别位于树脂背面82的y方向的两个端缘,延伸至x方向的两端。树脂凹部86与树脂背面82和树脂第1侧面83相连。树脂凹部86通过后述的制造工艺的第2槽部形成工序中的半切割形成。
102.下面,参照图22~图23,在下文中对半导体器件a2的制造方法的一个例子进行说明。对于与第1实施方式的半导体器件a1的制造方法相同的部分,省略说明。
103.首先,如图22所示准备引线框900(准备工序)。在引线框900设定有第2槽部形成区域s4。第2槽部形成区域s4在图22中是将施加了比较密集的阴影线的在x方向上延伸的区域与施加了比较稀疏的阴影线的在x方向上延伸的区域(第2除去区域s2)合在一起的区域,是在后述的第2槽部形成工序中在背面902形成槽部的区域。第2槽部形成区域s4被设定成,在引线框900的相邻的要形成半导体器件a2的部分之间在x方向上延伸。第2槽部形成区域s4的y方向的尺寸即宽度大于第2除去区域s2的宽度,在y方向的中央包含第2除去区域s2。即,第2除去区域s2的宽度比第2槽部形成区域s4窄,其整个与第2槽部形成区域s4重叠。
104.接着,在引线框900的整个面形成第1镀层911(第1镀敷工序),在引线框900搭载半导体元件6(搭载工序),形成密封树脂920(树脂形成工序),形成槽部904(槽部形成工序)。这些工序与第1实施方式相同。
105.接着,如图23所示,形成槽部905(第2槽部形成工序)。在图23中,对密封树脂920添加了点状阴影。槽部905是从引线框900的背面902侧向主面901侧凹陷,并在x方向上延伸的槽,在与图22所示的第2槽部形成区域s4对应的位置形成。如图23所示,槽部905跨引线框900和密封树脂920形成。槽部905具有底面905a和侧面905b。底面905a是与引线框900的背面902朝向相同方向的面。侧面905b是将引线框900的背面902、与背面902朝向相同的方向的密封树脂920的面、以及底面905a相连的面。在引线框900中的成为第1引线部1的端子部120的部分形成的槽部905,成为端子部凹部124,在成为第2引线部2的端子部220的部分形成的槽部905,成为端子部凹部224,在成为第3引线部3的端子部320的部分形成的槽部905,成为端子部凹部324。在密封树脂920形成的槽部905中的一部分,成为树脂凹部86。
106.第2槽部形成工序也与槽部形成工序一样,通过利用第1刀片951切削引线框900的背面902的半切割处理来进行。在该半切割处理中,从背面902侧起,切削与图22所示的第2槽部形成区域s4相应的部分。在该半切割处理中,将切削进行至引线框900的z方向的中途。
在图示的例子中,将切削进行至引线框900的厚度(z方向的尺寸)的一半以上,例如4分之3程度的深度。由于在引线框900的背面902形成有第1镀层911,因此能够抑制由引线框900的切削引起的毛刺的产生。在第2槽部形成工序中,也可以通过利用刀片的半切割以外的方法来形成槽部905。
107.接着,形成第2镀层912(第2镀敷工序),粘贴保护胶带970,将引线框900和密封树脂920沿y方向切断(第1切断工序)。然后,将引线框900和密封树脂920沿x方向切断(第2切断工序)。这些工序与第1实施方式相同。
108.半导体器件a2通过第1镀敷工序和第2镀敷工序这2次镀敷工序来制造。因此,与需要3次镀敷工序的现有的半导体器件相比,能够简化制造工艺。此外,在第1镀敷工序中,在引线框900的整个面形成第1镀层911,而不需要掩模。由此,与仅限定于在供接合导线接合的区域形成银镀层的情况相比,能够抑制制造成本。
109.依照本实施方式,在第1镀敷工序在引线框900的背面902形成第1镀层911。因此,在槽部形成工序和第2槽部形成工序中,能够抑制由引线框900的切削引起的毛刺的产生。此外,在第2镀敷工序中,在槽部904的底面904a和槽部905的底面905a形成第2镀层912。因此,在第1切断工序和第2切断工序中,能够抑制由引线框900的切削引起的毛刺的产生。
110.依照本实施方式,在第1镀敷工序中在引线框900的主面901形成第1镀层911。由此,在导线接合部主面211和导线接合部主面311形成第1镀层41。因此,接合导线71、72的接合性良好。
111.依照本实施方式,第2镀层42形成于各端子部凹部124、224、324。因此,在将半导体器件a2安装于电路板的情况下,在各端子部凹部124、224、324的第2镀层42形成焊接圆角。由此,能够提高半导体器件a2在电路板的安装强度。此外,能够通过外观检查容易地判断安装后的各引线部1~3与电路板的接合状态。
112.基于图24,对本发明的第3实施方式的半导体器件a3进行说明。在图24中,对与上述的半导体器件a1相同或类似的要素标注相同的附图标记,而省略重复的说明。图24是表示半导体器件a3的截面图,是与第1实施方式中的图7对应的图。
113.图示的半导体器件a3没有在各引线部1~3的整个面形成第1镀层41,而仅在一部分形成第1镀层41,这一方面与第1实施方式的半导体器件a1不同。
114.在半导体器件a3中,第1引线部1仅在搭载部背面112、搭载部凹部113、端子部背面122和连结部背面132形成有第1镀层41。在第1引线部1的搭载部主面111、端子部主面121和连结部主面131,没有形成第1镀层41。此外,第2引线部2仅在导线接合部背面212、导线接合部凹部213、端子部背面222和连结部背面232、以及导线接合部主面211中的供接合导线71接合的区域,形成有第1镀层41。虽然在图24中未图示,但是第3引线部3仅在导线接合部背面312、导线接合部凹部313、端子部背面322和连结部背面332、以及导线接合部主面311中的供接合导线72接合的区域,形成有第1镀层41。
115.在半导体器件a3的制造工艺的第1镀敷工序中,在引线框900的背面902和凹部903的整个面,形成第1镀层911。另一方面,在引线框900的主面901,使用掩模,以仅在接合接合导线71、72的区域形成第1镀层41。
116.半导体器件a3通过第1镀敷工序和第2镀敷工序这2次镀敷工序来制造。因此,与需要3次镀敷工序的现有的半导体器件相比,能够简化制造工艺。
117.依照本实施方式,在第1镀敷工序在引线框900的背面902形成第1镀层911。因此,在槽部形成工序中,能够抑制由引线框900的切削引起的毛刺的产生。此外,在第2镀敷工序中,在槽部904的底面904a形成第2镀层912。因此,在第1切断工序中,能够抑制由引线框900的切削引起的毛刺的产生。此外,由于在第1镀敷工序中在引线框900的凹部903形成第1镀层911,因此在第2切断工序中,也能够抑制由引线框900的切削引起的毛刺的产生。
118.依照本实施方式,在第1镀敷工序中,在引线框900的主面901的需要接合的区域形成第1镀层911。由此,在导线接合部主面211和导线接合部主面311的需要接合的区域形成有第1镀层41。因此,接合导线71、72的接合性良好。
119.依照本实施方式,第2镀层42形成于各端子部凹部124、224、324。因此,在将半导体器件a3安装于电路板的情况下,在各端子部凹部124、224、324的第2镀层42形成焊接圆角。由此,能够提高半导体器件a3在电路板的安装强度。此外,能够通过外观检查容易地判断安装后的各引线部1~3与电路板的接合状态。
120.依照本实施方式,在引线框900的主面901,仅在需要接合的区域形成第1镀层41,因此能够抑制镀金的使用量。
121.基于图25,对本发明的第4实施方式的半导体器件a4进行说明。在图25中,对与上述的半导体器件a1相同或类似的要素标注相同的附图标记,而省略重复的说明。图25是表示半导体器件a4的俯视图,是与第1实施方式中的图3对应的图。在图3中,为了便于理解,透视密封树脂部8,用假想线(二点划线)表示密封树脂部8的外形。
122.图示的半导体器件a4的半导体元件6为二极管,这一方面与第1实施方式的半导体器件a1不同。
123.半导体器件a4没有设置第3引线部3,且第2引线部2在半导体器件a4的y方向的另一端(在图25中为下侧),向整个x方向扩展地配置。第2引线部2的形状、配置位置和个数并不限定于图示的例子。
124.二极管(半导体元件)6具有元件主体60、第1电极61和第3电极63。第1电极61设置于元件主体60中的朝向与第1引线部1相反侧的面。第3电极63设置于元件主体60中的与第1引线部1相对的面。在图示的例子中,第1电极61为阳极电极,第3电极63为阴极电极。二极管6经由未图示的导电性接合材料,搭载于形成有第1镀层41的第1引线部1的搭载部主面111的中央。由此,二极管6的第3电极63由导电性接合材料与第1引线部1电连接。多个接合导线71与二极管6的第1电极61和形成有第1镀层41的第2引线部2的导线接合部主面211连接。由此,二极管6的第1电极61与第2引线部2电连接。
125.半导体器件a4通过第1镀敷工序和第2镀敷工序这2次镀敷工序来制造,能够起到与第1实施方式相同的效果。
126.本发明的半导体器件和半导体器件的制造方法并不限定于上述的实施方式。本发明的半导体器件和半导体器件的制造方法的各部分的具体构成在设计上可以自由改变。
127.付记1.
128.一种半导体器件,其包括:
129.第1引线部,其具有在厚度方向彼此朝向相反侧的第1主面及第1背面、和从上述第1背面向上述第1主面侧凹陷的第1凹部;
130.搭载于上述第1主面的半导体元件;
131.覆盖上述半导体元件的密封树脂部;
132.与上述第1主面和上述第1背面接触地形成的第1镀层;以及
133.第2镀层,
134.上述第1凹部从上述密封树脂部露出,
135.上述第1镀层具有覆盖上述第1背面的第1部分,
136.上述第2镀层与上述第1凹部和上述第1部分接触地形成。
137.付记2.
138.如付记1记载的半导体器件,其中,
139.上述第1镀层抑制伴随上述第1凹部的形成而来的毛刺的产生。
140.付记3.
141.如付记1或2记载的半导体器件,其中,
142.上述第1镀层包括含有ni且与上述第1引线部接触的第1层。
143.付记4.
144.如付记3记载的半导体器件,其中,
145.上述第1镀层包括含有au且与上述第2镀层接触的第2层。
146.付记5.
147.如付记3或4记载的半导体器件,其中,
148.上述第1镀层包括含有pd且与上述第1层接触的第3层。
149.付记6.
150.如付记1至5中任一项记载的半导体器件,其中,
151.上述第2镀层由与上述第1引线部相比焊料润湿性高的材料构成。
152.付记7.
153.如付记1至6中任一项记载的半导体器件,其中,
154.上述第2镀层含有sn。
155.付记8.
156.如付记1至7中任一项记载的半导体器件,其中,
157.上述第1引线部含有cu。
158.付记9.
159.如付记1至8中任一项记载的半导体器件,其中,
160.上述第1引线部包括从上述第1背面向上述第1主面侧凹陷且被上述密封树脂部覆盖的第2凹部。
161.付记10.
162.如付记1至9中任一项记载的半导体器件,其中,
163.还包括与上述第1引线部隔开间隔的第2引线部和接合导线,
164.上述第2引线部具有在上述厚度方向上彼此朝向相反侧的第2主面和第2背面,并且形成有从上述第2背面向上述第2主面侧凹陷的第1凹部,
165.上述接合导线与上述半导体元件和上述第2主面连接,
166.上述第2引线部的上述第1凹部从上述密封树脂部露出,
167.上述第1镀层具有覆盖上述第2背面的第2部分,
168.上述第2镀层与上述第2引线部的上述第1凹部和上述第2部分接触地形成。
169.付记11.
170.如付记10记载的半导体器件,其中,
171.上述第1镀层由与上述第1引线部相比与上述接合导线的接合性更好的材料构成。
172.付记12.
173.如付记10或11记载的半导体器件,其中,
174.上述第2引线部包括从上述第2背面向上述第2主面侧凹陷且被上述密封树脂部覆盖的第2凹部。
175.付记13.一种半导体器件的制造方法,其包括:
176.准备工序,其准备具有在厚度方向上彼此朝向相反侧的主面和背面的引线框;
177.在上述主面和上述背面形成第1镀层的第1镀敷工序;
178.在上述主面搭载半导体元件的搭载工序;
179.利用密封树脂覆盖上述半导体元件的树脂形成工序;
180.槽部形成工序,其通过将切削从上述引线框的上述背面进行至上述引线框的上述厚度方向的中途来形成槽部;
181.在上述背面和上述槽部形成第2镀层的第2镀敷工序;以及
182.切断工序,其沿上述槽部,在上述厚度方向观察时宽度比上述槽部窄且其整个与上述槽部重叠的除去区域中将上述引线框和上述密封树脂在上述厚度方向的整个区域中除去。
183.付记14.
184.如付记13记载的半导体器件的制造方法,其中,
185.在上述槽部形成工序中,通过利用第1刀片的半切割来形成上述槽部,
186.在上述切断工序中,通过利用比上述第1刀片薄的第2刀片的全切割来进行除去。
187.付记15.
188.如付记13或14记载的半导体器件的制造方法,其中,
189.在上述槽部形成工序中,形成沿与上述厚度方向正交的第1方向延伸的第1槽部和与上述第1槽部正交的第2槽部。
190.付记16.
191.如付记15记载的半导体器件的制造方法,其中,
192.上述切断工序包括:在沿上述第1槽部的第1除去区域中进行除去的第1切断工序;和在沿上述第2槽部的第2除去区域中进行除去的第2切断工序。
193.附图标记说明
194.a1~a4:半导体器件
195.1:第1引线部
196.110:搭载部
197.111:搭载部主面
198.112:搭载部背面
199.113:搭载部凹部
200.120:端子部
201.121:端子部主面
202.122:端子部背面
203.123:端子部端面
204.124:端子部凹部
205.130:连结部
206.131:连结部主面
207.132:连结部背面
208.133:连结部端面
209.2:第2引线部
210.210:导线接合部
211.211:导线接合部主面
212.212:导线接合部背面
213.213:导线接合部凹部
214.220:端子部
215.221:端子部主面
216.222:端子部背面
217.223:端子部端面
218.224:端子部凹部
219.230:连结部
220.231:连结部主面
221.232:连结部背面
222.233:连结部端面
223.3:第3引线部
224.310:导线接合部
225.311:导线接合部主面
226.312:导线接合部背面
227.313:导线接合部凹部
228.320:端子部
229.321:端子部主面
230.322:端子部背面
231.323:端子部端面
232.324:端子部凹部
233.330:连结部
234.331:连结部主面
235.332:连结部背面
236.333:连结部端面
237.41:第1镀层
238.411:镍镀层
239.412:钯镀层
240.413:金镀层
241.42:第2镀层
242.6:半导体元件
243.60:元件主体
244.61:第1电极
245.62:第2电极
246.63:第3电极
247.71、72:接合导线
248.8:密封树脂部
249.81:树脂主面
250.82:树脂背面
251.83:树脂第1侧面
252.84:树脂第2侧面
253.85、86:树脂凹部
254.900:引线框
255.901:主面
256.902:背面
257.903:凹部
258.904:槽部
259.904a:底面
260.904b:侧面
261.905:槽部
262.905a:底面
263.905b:侧面
264.906:贯通孔
265.911:第1镀层
266.912:第2镀层
267.920:密封树脂
268.951:第1刀片
269.952:第2刀片
270.970:保护胶带
271.s1:第1除去区域
272.s2:第2除去区域
273.s3:槽部形成区域
274.s4:第2槽部形成区域。