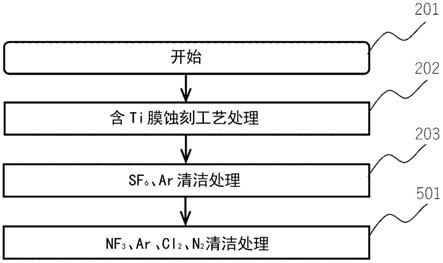
1.本发明涉及真空处理方法。
背景技术:2.在半导体器件的制造工序中,谋求应对半导体装置中所含的构件的微细化、集成化。例如在集成电路、纳米电气机械系统中,进一步推进结构物的纳米尺度化。
3.通常在半导体器件的制造工序中,为了成形微细图案而使用光刻技术。该技术在抗蚀剂层上运用器件结构的图案,对通过抗蚀剂层的图案而露出的基板选择性地进行蚀刻除去。若在之后的处理工序中使其他材料沉积在蚀刻区域内,就能形成集成电路。
4.作为现有技术,在专利文献1中公开了一种处理装置,为了以干式处理高精度地进行各向同性蚀刻,进行吸附/脱离方式的原子层蚀刻处理。
5.根据该现有技术的处理装置,对配置于真空容器内部的处理室内的工作台上所载置的晶片实施基于自由基的反应层生成工序和基于红外线加热的反应层除去工序。关于上述反应层生成工序,首先对处理室上部的自由基生成空间供给处理气体,将气体激活,由此生成自由基。将形成的自由基粒子经由连通其与下部处理室之间的气体导入管,供给到载置于处理室的晶片上表面,在这里生成反应层。
6.进而,上述反应层除去工序在反应层生成工序后实施,从配置于晶片上部的灯照射红外光,将晶片上表面的生成物气化来除去反应层。交替重复这些工序,来除去晶片表面的处理对象的膜。
7.在上述蚀刻处理工序中,存在在各种工序中产生反应生成物,附着或沉积到处理室内的课题。特别是反应生成物较多附着、沉积在处理室内的腔内侧壁、工作台表面、配置于晶片近旁的基座环。
8.反应生成物的附着、沉积会给处理装置的蚀刻性能带来种种问题。例如作为给晶片的影响,由于在蚀刻处理工序中反应生成物残留于处理室内,蚀刻工序中附着、沉积在处理室内的反应生成物飞散到器件上,由此成为异物,会引起图案缺陷,或者由于随时间变化而在器件的加工尺寸中出现偏差,变得不能发挥所期望的性能。另外,作为给处理装置的影响,反应生成物沉积在工作台表面,由此引起静电吸附不良等性能劣化。
9.为了抑制这些问题,要求通过定期的清洁进行反应生成物的除去。作为代表性的清洁手段,如专利文献2记载的那样,广为人知如下方法:用六氟化硫(sf6)气体与氩(ar)气体的混合气体生成反应性高的卤素自由基,使其与沉积物反应,由此将反应生成物气化并向真空容器外排气,从而进行除去。
10.现有技术文献
11.专利文献
12.专利文献1:jp特开2017-143186号公报
13.专利文献2:jp特开2003-273082号公报
技术实现要素:14.发明要解决的课题
15.但在上述现有的清洁方法中有如下课题。
16.在对含钛(ti)膜晶片进行了蚀刻处理加工时,生成钛(ti)系反应生成物,如上述记载的那样,易于附着、沉积在真空容器内部的处理室内。但在利用了六氟化硫(sf6)气体与氩(ar)气体的混合气体的现有技术的清洁方法中,虽然对硅(si)系反应生成物的反应性高,但与钛(ti)系反应生成物的反应性低。因此,虽然硅(si)系反应生成物的除去效果高,但钛(ti)系反应生成物未从处理室内被除去,照样附着、沉积。
17.特别是由于工作台表面、基座环配置于晶片近旁,因此,通过处理工序产生的钛(ti)系反应生成物易于附着、沉积,其飞散到晶片上,由此有异物多发的问题。
18.本发明目的在于,提供能防止钛(ti)系反应生成物所导致的向晶片上的异物附着的真空处理方法。
19.用于解决课题的手段
20.为了解决上述课题,代表性的本发明所涉及的真空处理方法之一,通过如下而达成:一种真空处理方法,在处理室内蚀刻含有钛的膜,所述真空处理方法具有如下工序:对所述膜进行蚀刻;使用三氟化氮即nf3气体、氩即ar气体和氯即cl2气体的混合气体来对所述处理室内进行清洁。
21.发明的效果
22.根据本发明,能提供能防止钛(ti)系反应生成物所导致的向晶片上的异物附着的真空处理方法。
23.上述以外的课题、结构以及效果通过以下的实施方式的说明而得以明确。
附图说明
24.图1是表示本发明的实施方式所涉及的等离子处理装置的结构的概略的纵截面图。
25.图2是比较例,是在图1所示的等离子处理装置中示出清洁处理的序列的流程的流程图。
26.图3是表示在本实施方式中研时的在清洁处理中使用的各气体的组合所带来的蚀刻速率结果的图。
27.图4是表示表征添加的氮(n2)气体的流量比依赖性的蚀刻速率结果的图。
28.图5是表示在图1所示的等离子处理装置中实施的本实施方式的清洁处理的序列的流程的流程图。
具体实施方式
29.参考附图来说明本发明的实施方式。
30.图1是示意表示本发明的实施方式所涉及的等离子处理装置100的纵截面图。
31.首先参考图1来说明等离子处理装置100的结构。该图所示的等离子处理装置100具备真空容器101,在其下部,为了将真空容器101减压,成为设有排气用的开口并从开口部经过排气管连接真空泵1015的结构。在开口部与真空泵1015的路径上配置调压阀1016,增
减路径或开口部的流路截面积来调整排气的流量或速度。
32.真空容器101大致由真空容器上部的放电部102以及真空容器下部的处理室104构成。放电部102以及处理室104是具有圆筒形的空间,其中心轴配置在同轴上或近似成视作配置在同轴上的程度的位置。在它们之间,通过同样配置在中心轴一致或近似成视作中心轴一致的程度的位置的圆形的分散板106进行区分。放电部102以及处理室104经过同心圆状配置在分散板106的多个贯通孔而连通。
33.在放电部102设置圆筒型的石英腔107,在石英腔107的外侧设置icp线圈108。icp线圈108经由匹配器109与高频电源110连接,等离子处理装置100能以感应耦合式等离子(icp)放电方式生成等离子1011。高频电源110的高频电力的频率设为13.56mhz等数十mhz的频率带。
34.在放电部102的上部设置顶板1012。在顶板1012的下部设置气体分散板,处理气体经由气体分散板被导入真空容器101内。在顶板1012与放电部侧壁的上端部上表面之间夹着o环等密封构件。由此将放电部102内部与真空容器101外部之间气密地密封。
35.从处理气体源1013供给的处理气体被按每个气体种类没置的质量流量控制器1014调整供给流量。作为处理气体,使用可燃性气体、助燃性气体以及它们的混合气体、或者用惰性气体稀释过的它们的混合气体。由处理气体源1013和质量流量控制器1014构成气体供给装置。
36.真空容器101下部的处理室104在与放电部102以及处理室104的中心轴一致或近似成视作与放电部102以及处理室104的中心轴一致的位置配置载置晶片1017的样品台103。
37.在样品台103与放电部102之间,为了加热晶片1017而设置ir灯组件(加热装置)105。ir灯组件105主要由辐射作为电磁波的ir光的ir灯1018、用于反射ir光的反射板1019、ir光透过窗1020构成。
38.ir灯1018使用圈型(圆形)的灯。另外,从ir灯1018放出以可见光到红外光区域的光为主的光(这里称作ir光)。ir灯1018与供给电力的灯用电源1021连接,在两者之间配置用于使得对icp线圈施加的高频电力的噪声不会流入灯用电源的高频截止滤波器1022。
39.配置在同心圆上的多个(图中3个)ir灯1018构成为能在各自中独立调整对各自的圆弧状的部分供给的电力的大小,能调整晶片1017的加热量的径向分布。
40.在ir灯1018的上方设置用于将辐射状输出的ir光向下方(晶片设置方向)反射的反射板1019。
41.从ir灯组件105的下表面延续到内周侧壁面地配置用于使ir光穿过的石英制的ir光透过窗1020。
42.ir灯组件105的内周内侧的空间是在配置于上方的放电部102内形成的等离子1011所流通的流路,在该流路内设置将在等离子中生成的离子、电子遮蔽、将气体的中性粒子、自由基透过的电介质制的分散板106。
43.另外,在本实施方式中,分散板106也由石英等透过性构件构成,从其外周侧辐射的ir光不被分散板106遮挡地透过其,大部分到达处理室104内部。
44.接着,以将清洁方法运用于等离子处理装置的示例为比较例,使用图2的流程图示出。
45.从步骤201开始处理,在步骤202实施含钛(ti)膜晶片的蚀刻工艺处理(对膜进行蚀刻的处理)。之后,在步骤203,对放电部102供给六氟化硫(sf6)气体、氩(ar)气体,并进行放电。将这时进行解离而产生的自由基导入处理室104,使其与在处理室内沉积的硅(si)系反应生成物反应,通过来自ir灯1018的ir光的照射进行加热、脱离,由此来进行清洁处理。之后,由于将在处理室内浮游的反应生成物从处理室104排气,因此通过调压阀1016使排气压上下变化来进行净化。
46.但在利用了将六氟化硫(sf6)气体用氩(ar)气体稀释后的混合气体的清洁方法中,钛(ti)系反应生成物的除去效果低。
47.对此,本发明的发明者想到,若为了将处理含钛(ti)膜晶片时产生的钛(ti)系反应生成物除去而与反应性高的自由基反应,生成挥发性高的反应生成物,应该就能向真空容器外排气而除去。
48.因此,本发明的发明者模拟在处理室104内沉积的钛(ti)系反应生成物,通过含钛(ti)膜晶片实施确认蚀刻速率的实验。在相关的实验中,作为含钛(ti)膜晶片而测试氮化钛(tin)膜晶片。由于若蚀刻速率高,则与钛(ti)系反应生成物的反应性变高,因此期待清洁效果提升。
49.接下来,示出图3所示的各气体的组合中的确认蚀刻速率的实验结果。
50.为了比较,通过利用了将六氟化硫(sf6)气体用氩(ar)气体稀释后的混合气体的清洁来进行蚀刻速率确认实验,结果得到4.2nm/min的蚀刻速率结果301。
51.接着,进行了用在本实施方式的清洁中的气体的蚀刻速率确认实验。在图1的等离子处理装置中,在以下的条件下进行实验:将腔内的压力通过真空泵1015和调压阀1016设定为125pa以下,将电源rf电力设定为800w。另外,取代六氟化硫(sf6)气体而使用在氟系系气体中能得到最高速率的三氟化氮(nf3)气体。通过使用三氟化氮(nf3)气体,易于与耦合能量高的钛(ti)系反应生成物进行反应,能生成挥发性高的四氟化钛(tif4),并将其除去。
52.进而,通过添加与金属膜的反应性高的氯(cl2)气体,生成四氯化钛(ticl4)。由于与四氟化钛(tif4)相比,四氯化钛(ticl4)蒸汽压更高,因此在低温部也能效率良好地除去钛(ti)系反应生成物。
53.通过以上,进行了利用了三氟化氮(nf3)气体、氯(cl2)气体、氩(ar)气体的混合气体的清洁的实验,结果,能得到11.4nm/min的蚀刻速率结果302。与利用了六氟化硫(sf6)气体、氩(ar)气体的混合气体的实验结果比较,可知蚀刻速率增加,对钛(ti)系反应生成物的清洁效果高。
54.进而,本发明的发明者在上述的三氟化氮(nf3)气体、氯(cl2)气体、氩(ar)气体的混合气体添加氮(n2)气体,进行了蚀刻速率确认实验。通过添加氮(n2)气体,能将氮化钛(tin)的键合分割成钛(ti)和氮(n2),能促进钛(ti)的氯化、氟化。
55.如此地,通过利用了三氟化氮(nf3)气体、氯(cl2)气体、氩(ar)气体、氮(n2)气体的混合气体的清洁而进行了确认实验,结果,能得到72.6nm/min的蚀刻速率结果303。通过添加氮(n2)气体,能更加使氮化钛(tin)的速率增加。
56.接下来,对氮(n2)气体添加流量依赖性实施蚀刻速率的确认实验。实验的结果可知,如图4所示那样,在氮(n2)气体相对于三氟化氮(nf3)气体、氯(cl2)气体、氩(ar)气体的混合气体的流量比是百分之0的情况下,也确保蚀刻速率。
57.另外,随着从百分之0起上述流量比增大,蚀刻速率也增加,上述流量比成为百分之14时成为蚀刻速率最大。之后,判明了具有到流量比百分之30为止蚀刻速率逐渐降低的特性。通过以上可知,通过添加氮(n2)气体,虽然清洁效果提高,但若过多添加氮(n2)气体,蚀刻速率就会降低,因此有可能变得不能实施效率良好的清洁。
58.因此,优选氮(n2)气体相对于三氟化氮(nf3)气体、氯(cl2)气体、氩(ar)气体、氮(n2)气体的混合气体的流量比设定得成为超过0%且30%以下的范围。
59.将对通过以上得到的钛(ti)系反应生成物的清洁的实施方式作为真空处理方法而在图5的流程图示出,但省略与图2所示的工序共通的工序的说明。其中,优选在膜的蚀刻工序中进行循环蚀刻(包含原子层蚀刻(atomic layer etching:ale))。或者,也可以是通常的利用了等离子的蚀刻。根据本实施方式,在清洁处理工序的步骤203后,作为清洁处理工序的步骤501,将通过上述实验确认过效果的三氟化氮(nf3)气体、氯(cl2)气体、氩(ar)气体和氮(n2)气体的混合气体供给到放电部102,并进行放电,将这时进行解离而产生的自由基(或等离子)导入处理室104,与在处理室内沉积的钛(ti)系反应生成物反应,通过用ir灯1018进行加热来进行脱离,进行清洁。通过该清洁,能效率良好地除去在腔内附着、沉积的钛(ti)系反应生成物。
60.另外,尽管在本实施方式中使用感应耦合型等离子蚀刻装置,但本发明不管等离子的生成方法如何都能运用。例如,对螺旋波等离子蚀刻装置、利用了微波的ecr等离子蚀刻装置、电容耦合型等离子蚀刻装置等,也能运用本发明。
61.进而,在利用了通过三氟化氮(nf3)气体、氯(cl2)气体和氩(ar)气体的混合气体、或者三氟化氮(nf3)气体、氯(cl2)气体、氩(ar)气体和氮(n2)气体的混合气体生成的等离子的清洁中,也能效率良好地除去在腔内附着、沉积的钛(ti)系反应生成物。
62.上述的实施方式为了易于理解地说明本发明而详细进行了说明,但不一定限定于具备说明的全部结构。另外,能将某实施方式的结构的一部分置换成其他实施方式的结构,另外,还能在某实施方式的结构中加进其他实施方式的结构。另外,能对各实施方式的结构的一部分进行其他结构的追加、删除、置换。
63.附图标记的说明
64.100 等离子处理装置、101 真空容器、102 放电部、104 处理室、105 ir灯组件、106 分散板、107 石英腔、108 icp线圈、109 匹配器、110 高频电源、1011 等离子、1012 顶板、1015 真空泵、1016 调压阀、1017 晶片、1018 ir灯、1019 反射板、1020 ir光透过板、1021 灯用电源、1022 高频截止滤波器。