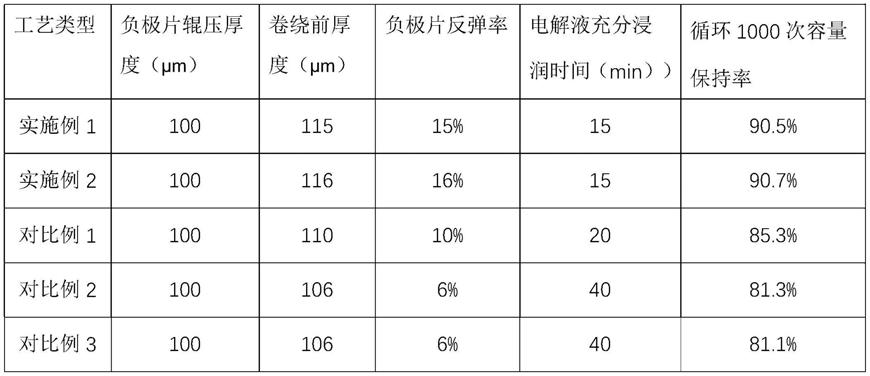
1.本发明涉及锂电池技术领域,具体为一种圆柱型锂离子电池负极片辊压后二次烘烤工艺。
背景技术:2.锂离子电池因为其能量密度高,倍率性能好,电压高、重量轻、循环寿命长、工作温度范围宽、无记忆效应,在目前技术条件下是新能源汽车领域最广泛应用的产品。开发循环寿命更长的动力电池产品,可以有效提高电池寿命,降低用户使用及维护成本,提高用户满意度,是目前行业内的共识。
3.目前圆柱型锂离子电池在新能源行业有着举足轻重的作用,广泛应用于储能和新能源汽车领域,型号众多,如:18650、21700、32700、26650、32135等,圆柱电池因特有的封装材料,外面为钢壳束缚内部卷芯,如果不消除物理内应力,会导致电池在充放电过程中因过多的物理内应力膨胀,加大了正负极片的间距,同时卷芯挤压钢壳,导致卷芯坍塌,导致循环寿命下降;另一方面,缩短浸润时间,提高电解液的浸润效率也是行业需要解决的问题。
4.目前圆柱锂离子电池行业内负极辊压后的工艺主要有2种工艺:
5.a:辊压
→
分切小卷
→
卷绕
6.b:辊压
→
分切小卷
→
小卷烘烤
→
卷绕
7.以上两种工艺均不能达到释放负极片物理内应力和提高电解液的浸润效率的效果。因此提供一种可以解决以上问题的方法,从而提高电池循环寿命的工艺方法具有重要意义。
技术实现要素:8.针对现有技术无法消除物理内应力而导致电池循环寿命下降的问题,本发明的目的是提供一种圆柱型锂离子电池负极辊压后二次烘烤工艺,使得负极片物理内应力得到充分释放,从而提高电池循环寿命。
9.为实现上述发明目的,本发明的技术方案是:
10.一种圆柱型锂离子电池负极辊压后二次烘烤工艺,包括以下步骤:
11.步骤一:将涂布后的圆柱型锂离子电池负极片进行辊压;
12.步骤二:将步骤一所得负极片进行第一烘烤,使得负极片厚度反弹率为9%
‑
11%;
13.步骤三:将步骤二所得负极片搁置,冷却到室温;
14.步骤四:将步骤三所得负极片进行第二次烘烤,使得负极片厚度反弹率为4%
‑
6%;
15.步骤五:将步骤四所得负极片分切小卷,,得到卷绕好的圆柱型锂离子电池负极片,进行卷绕,进入电池制作的后续工艺。
16.优选方案,步骤一所述辊压厚度工艺要求100
±
2微米。
17.优选方案,步骤二所述烘烤温度为105
‑
115℃。
18.优选方案,步骤二烘烤的时间为1.5
‑
2.5s。
19.优选方案,步骤三所述室温为20℃
‑
25℃。
20.优选方案,步骤三所述搁置的时间为1
‑
2h。
21.优选方案,步骤四第二次烘烤时间为1.5
‑
2.5s。
22.优选方案,步骤四第二次烘烤温度为130℃
‑
135℃。
23.本发明专利主要从:一:让负极片辊压后卷绕前极片厚度反弹率达到最大,达到消除物理内应力的效果,保证消除电池在充放电时的物理反弹。二:缩短电解液浸润时间,从以上两点入手提高循环性能。
24.本发明几个关键控制点:
25.1、控制两次烘烤后极片的厚度反弹率,第一烘烤,使得负极片厚度反弹率为9%
‑
11%;第二次烘烤,使得负极片厚度反弹率为4%
‑
6%;总反弹率要求15%左右,才能更好的达到消除物理内应力的效果,保证消除电池在充放电时的物理反弹。厚度反弹率主要是通过烘烤温度和烘烤时间来控制,达到所需的反弹效果。
26.2、控制两次烘烤的温度,第二次烘烤的温度要高于第一次烘烤的温度,因为因为负极片第二次反弹难度更大,提高二次烘烤温度使得负极片达到二次烘烤反弹效果。
27.3、两次烘烤之间必须有一段时间的搁置,使负极片充分冷却到室温,搁置时间太短,负极片冷却不充分,达不到二次烘烤反弹效果,搁置时间太长影响生产效率。
28.与现有技术相比,本发明的优势是:
29.1、本发明的二次烘烤的工艺使负极片在卷绕前厚度反弹率达到最大,从而达到彻底释放负极片辊压后材料颗粒间的物理内应力,消除了电池在充电时因物理内应力导致的负极片厚度反弹,保证了正负极片接触更紧密,缩短锂离子迁移路径,从而提高电池的循环性能。
30.2、本发明的二次烘烤的工艺使负极片在卷绕前厚度反弹率达到最大,有效地提高了负极片的孔隙率,达到电解液的充分浸润的效果同时缩短了浸润时间,有效地解决了充放电过程中因电解液浸润不充分导致的反应热,从而提高电池的循环性能。
具体实施方式
31.以下结合具体实施方式对本发明作进一步的详细说明,但本发明的实施方式不限于此。
32.实施例1:
33.步骤一:将涂布后的圆柱型锂离子电池负极片进行辊压,辊压后负极片厚度工艺要求为100μm;
34.步骤二:烘烤步骤一所得负极片,烘烤温度为110℃,烘烤时间2s;
35.步骤三:将步骤二所得负极片搁置1
‑
2h后,冷却至室温,负极片厚度反弹为110μm;
36.步骤四:将步骤三所得负极片进行二次烘烤,二次烘烤工艺为烘烤温度130℃,烘烤时间2s;
37.步骤五:将步骤四所得负极片分切小卷,在卷绕前测得负极片厚度为115μm,进行卷绕,得到卷绕好的圆柱型锂离子电池负极片,进入电池制作的后续工艺。
38.计算与结果:负极片厚度反弹率为(115
‑
100)/100=15%,电解液完全浸润时间
15min。通过跟踪电池充放电循环到1000次后,容量保持率为90.5%。
39.实施例2:
40.工艺步骤依次为:辊压、极片烘烤、搁置冷却、极片烘烤、分切小卷、卷绕,辊压厚度工艺要求100μ,第一次烘烤工艺为:烘烤温度115℃,烘烤时间2.5s,搁置2h后厚度111μ,第二次烘烤工艺为烘烤温度135℃,烘烤时间2.5s,卷绕前厚度为116μ,厚度反弹率为(116
‑
100)/100=16%,电解液完全浸润时间为15min。通过跟踪电池充放电循环到1000次后,容量保持率为90.7%。
41.对比例1:
42.步骤一:将涂布后的圆柱型锂离子电池负极片进行辊压,辊压后负极片厚度工艺要求为100μm;
43.步骤二:烘烤步骤一所得负极片,烘烤温度为110℃,烘烤时间2s;
44.步骤三:将步骤二所得负极片搁置1
‑
2h后冷却至室温;
45.步骤四:将步骤三所得负极片分切小卷,在卷绕前测得负极片厚度反弹至110μm,进行卷绕,得到卷绕好的圆柱型锂离子电池负极片,进入电池制作的后续工艺。
46.计算与结果:负极片厚度反弹率为(110
‑
100)/100=10%,电解液完全浸润时间为20min,负极片在无张力束缚的情况下高温烘烤可以让负极片厚度迅速反弹,但通过验证,辊压后一次烘烤极片没有充分反弹,物理内应力没有完全释放。通过跟踪电池充放电循环到1000次后,容量保持率为85.3%。
47.对比例2:
48.步骤一:将涂布后的圆柱型锂离子电池负极片进行辊压,辊压后负极片厚度工艺要求为100μm;
49.步骤二:将步骤四所得负极片分切小卷;
50.步骤三:烘烤步骤二所得负极片,烘烤温度110
±
5℃,烘烤时间2s;
51.步骤四:在卷绕前测得负极片厚度反弹至106μm,将步骤三所得负极片进行卷绕,得到卷绕好的圆柱型锂离子电池负极片,进入电池制作的后续工艺。
52.计算与结果:负极片厚度反弹率为(106
‑
100)/100=6%,电解液完全浸润时间为40min因为小卷有张力束缚,小卷烘烤时应力被张力束缚,即使烘烤,负极片厚度也不会有变化,应力也无法释放。通过跟踪电池充放电循环到1000次后,容量保持率为81.3%
53.对比例3:
54.步骤一:将涂布后的圆柱型锂离子电池负极片进行辊压,辊压后负极片厚度工艺要求为100μm;
55.步骤二:将步骤四所得负极片分切小卷;
56.步骤三:在卷绕前测得负极片厚度反弹至106μm,将步骤二所得负极片进行卷绕,得到卷绕好的圆柱型锂离子电池负极片,进入电池制作的后续工艺。
57.计算与结果:负极片厚度反弹率为(106
‑
100)/100=6%,电解液完全浸润时间为40min.通过跟踪电池充放电循环到1000次后,容量保持率为81.1%。
58.表1、实验数据对比表
[0059][0060]
本发明通过工艺调整,让负极片辊压后卷绕前负极片厚度反弹率达到最大,从而达到彻底释放负极片辊压后材料颗粒间的物理内应力,消除了电池在充电时因物理内应力导致的负极片厚度反弹,保证了正负极片接触更紧密,缩短锂离子迁移路径从而提高电池的循环性能,另一方面本负极片辊压后厚度充分反弹也有效地提高了负极片的孔隙率,达到电解液的充分浸润的同时缩短了浸润时间,有效地解决了充放电过程中因电解液浸润不充分导致的反应热,从而提高电池的循环性能。
[0061]
以上所述为本发明的具体实施方式,但本发明的保护范围不局限于此,任何熟悉技术领域的技术人员在本发明揭露的技术范围内,根据本发明的技术方案及其构思加以等同替换或改变,都应涵盖在本发明权利要求的保护范围之内。