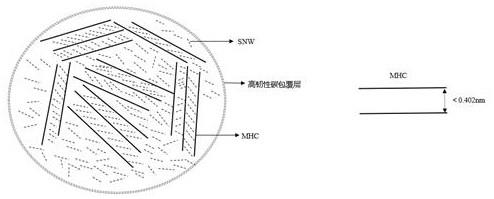
1.本发明涉及锂电池技术领域,具体为一种掺硅补锂技术方案及其锂离子电池的组装方法。
背景技术:2.随着当下面向碳中和的新能源汽车的创新与发展,2020年是新能源汽车行业峰回路转的一年,也是新能源汽车2012
‑
2020规划圆满收官的标志年,新能源汽车从政策驱动到市场驱动的转折年。从行业政治操作向公司商业运作的转型,锂离子电池的应用领域越来越广泛、应用场景也越来越多,对高性能锂离子电池的要求越来越高,而锂电池的核心技术还是锂电池材料,电池材料创新需要平衡比能量、循环寿命、高功率、高安全、低成本等相互矛盾的性能指标。
3.锂电池正极材料的能量当前很难在有大的提升,而当前的石墨负极材料有很大的提升空间,硅基负极材料有高于石墨负极材料接近10倍的克容量,可在更高能量密度的锂离子电池中发挥重要作用。但以商业化的硅基材料作为负极的电极在充放电过程中会产生较大的体积膨胀,导致活性物质脱落,循环性能下降,当前的改善方式主要是硅基材料的纳米化、碳包覆、掺杂改性、硅基材料和石墨或硬碳材料的复合,材料的研究深度和广度也越来越高,但始终还是没达到终端的产业化阶段,各方面的改性需要平衡到一定水平,满足锂离子电池全生命周期的使用需要。
技术实现要素:4.(一)解决的技术问题针对现有技术的不足,本发明提供了一种掺硅补锂技术方案及其锂离子电池的组装方法,解决了首次充电锂离子消耗不可逆的问题。
5.(二)技术方案为实现以上目的,本发明通过以下技术方案予以实现:一种掺硅补锂技术方案,具体包括如下步骤:步骤一.改性开孔硬碳(mhc)的制备:按照质量比8:1:0.1:0.1:0.1:3分别将浓硫酸、双氧水、聚乙二醇400、氨基丙醇、无水乙醇、硬碳加入到搅拌容器中,保持环境为0℃,搅拌时间约15
‑
20分钟至溶液粘稠;将以上粘稠溶液用去离子水清洗至溶液ph为6
±
0.5,然后在100℃下烘干,最后在300
‑
350℃下处理24h,获得mhc;步骤二:snw和mhc的材料组装和高韧性碳包覆膜处理:按照质量比8:12将snw和mhc在真空条件下强力机械搅拌融合,搅拌时间45
‑
60分钟,获得snw和mhc的复合物;将snw和mhc复合物、单壁碳纳米管
‑
swcnt(0.65%wt)和cmc(0.35%wt)复合溶液、苯胺、蔗糖按照96:2:1:1的质量比加入去离子水中,溶液的固含量为15
‑
20%,搅拌60
‑
90分钟,在180℃下喷雾干燥,在氩气条件下400
‑
450℃煅烧120分钟,获得本发明的高韧性碳包覆snw和mhc复合物;
步骤三:可预锂化隔膜(pls)的制备:按照质量比70:15:15将聚偏氟乙烯
‑
pvdf、聚氧化乙烯
‑
peo、li2co3等溶解在n
‑
甲基吡咯烷酮
‑
nmp和无水乙腈(质量比—nmp:无水乙腈=8:2)的溶液中,固含量为20
‑
25%,真空搅拌120分钟,然后利用隔膜涂敷设备将以上浆体均匀涂敷在高孔隙率聚丙烯(pp)基膜正反两面,干燥后的涂敷厚度约为2
‑3µ
m,获得本发明的预锂化隔膜
‑
pls。
6.优选的,所述步骤一中浓硫酸和双氧水可与硬碳材料结合在一起且插入硬碳材料的碳层间隙内,聚乙二醇400、氨基丙醇和无水乙醇可促进材料的分散和孔隙率的调控,便于硬碳材料获得均一稳定的碳层间距、多孔结构,ph的控制条件也是为了控制硬碳材料的开孔程度,ph越小开孔程度越大,300
‑
350℃下的热处理可使得浓硫酸和双氧水的氧化分解而产生气体,从而使得硬碳材料的层间距打开且获得更多的孔隙结构。
7.优选的,所述步骤二中snw和mhc的强力机械搅拌融合可使得snw较好的嵌入和插层到mhc的多孔结构中,也可将snw和mhc较好的均匀复合在一起;单壁碳纳米管
‑
swcnt(0.65%wt)和cmc(0.35%wt)复合溶液的包覆不仅可以提高电极材料的导电性,还能提高包覆层的韧性,抵抗材料膨胀导致结构崩塌的风险,苯胺、蔗糖的二次包覆可减少材料与电解液的直接接触,降低副反应的发生。
8.优选的,所述步骤三中高孔隙率pp基膜可为高锂离子通量创造条件,pvdf和peo可增强极片与隔膜的粘附力,降低极片与隔膜的间隙也可在一定程度上为极片的膨胀提供缓冲空间,同时提高保液能力和离子传输能力,而li2co3可提供预锂化,为snw和mhc材料首次充电消耗的不可逆锂离子提供补充。
9.一种锂离子电池的组装方法,包括如下具体步骤:步骤一:负极极片的制备,负极复合活性材料的质量比为snw:mhc:ag=8:12:80,负极浆料的物质配比为负极复合活性材料:sp:pvdf=94.5%:2%:3.5%,按照以上质量比分别加入负极复合活性材料、sp、pvdf,干混15
‑
20分钟,加入一定量nmp,控制浆料的固含量为45%
‑
50%,搅拌120
‑
140分钟后慢搅备用;依次经过涂布、冷压、模切、分条后获得负极极片;步骤二:正极极片的制备,正极浆料的物质配比为li(ni
0.8
co
0.1
mn
0.1
)o2 :sp:cnt:pvdf=94.5%:3.5%:0.5%:1.5%,按照以上质量比分别加入li(ni
0.8
co
0.1
mn
0.1
)o2 、sp、cnt、pvdf,加入一定量nmp,控制浆料的固含量为60%
‑
65%,搅拌120
‑
140分钟后慢搅备用;依次经过涂布、冷压、模切、分条后获得正极极片;电池的组装:以本发明获得的预锂化隔膜
‑
pls为隔膜,搭配步骤一和步骤二的极片完成卷绕、热压、hi
‑
pot、焊接、装配、烘烤、注液、静置、化成、老化、容量、测k、包装完成电池的组装,获得高能量密度锂离子电池。
10.(三)有益效果本发明提供了一种掺硅补锂技术方案及其锂离子电池的组装方法。具备以下有益效果:1、snw和mhc和ag的复合阳极制备过程包括硬碳的开孔处理、snw和mhc的材料组装和高韧性碳包覆膜处理、snw和mhc和ag复合阳极制备,硬碳的开孔处理可为硅纳米线的融入提供空间,同时也为硅在电池的全生命周期内充放电产生的膨胀预留空间,硬碳的开孔处理方法为表面活性剂(聚乙二醇400、氨基丙醇、无水乙醇)、氧化剂(双氧水)、插层剂(浓硫酸)的热激发处理;snw和mhc的材料组装和高韧性碳包覆膜处理包括snw和mhc的强力融
合使得snw嵌入mhc的多孔空间结构中,同时将单壁碳纳米管
‑
swcnt(0.65%wt)和cmc(0.35%wt)的复合溶液、苯胺、蔗糖、水与以上snw和mhc的复合物均匀混合在一起,喷雾干燥后煅烧,最后得到有高韧性碳包覆层的snw和mhc复合物,snw和mhc的有机结合可为高能量密度、长循环周期、低膨胀系数、高安全可靠性的锂离子电池阳极提供解决方案,而高韧性的碳包覆层可扫除snw和mhc的低首效缺陷,为snw和mhc的产业化使用提供保障;snw和mhc和ag复合阳极的制备中三种材料的质量比为snw:mhc:ag=8:12:80,snw和mhc材料较高的克容量(snw
‑
3600mah/g,mhc
‑
450 mah/g)可提高电池的能量密度,mhc具有极好的倍率性能可提升锂离子电池的低温性能,ag具有较好的加工性能和压实密度,snw和mhc和ag的复合可以实现很高的性能优势。其中预锂化隔膜(pls)包括高孔隙率聚丙烯(pp)基膜和有机和无机预锂涂层,高孔隙率pp基膜可为高锂离子通量创造条件,有机和无机预锂涂层为聚偏氟乙烯
‑
pvdf、聚氧化乙烯
‑
peo、锂盐(不限于li2co3等),其中pvdf和peo可增强极片与隔膜的粘附力,降低极片与隔膜的间隙也可在一定程度上为极片的膨胀提供缓冲空间,而li2co3可提供预锂化,为首次充电消耗的不可逆锂离子提供补充。所述锂离子电池为以本发明的复合阳极材料为阳极主材、li(ni0.8co0.1mn0.1)o2 为阴极材料、预锂化隔膜为隔膜、长寿命型电解液组装而成的高能量密度锂离子电池。
11.2、本发明的一种掺硅补锂技术及高能量密度锂离子电池可解决当前硅碳负极的产业化瓶颈、可弥补硅碳负极的性能缺陷、可为高能量密度锂离子电池提供解决方案。硬碳材料的开孔膨化处理和snw和mhc的组装可为硅在电池的全生命周期内充放电产生的膨胀预留空间,解决硅碳负极的反复膨胀收缩引起的极片粉化、极片应力集中、极片孔隙率分布不均引起的电性能恶化,同时硬碳材料的各向同性、多孔结构、较大层间距可大幅度提升电池的低温性能和功率性能;snw和mhc材料的高韧性碳包覆膜可大幅度避免snw和mhc和电解液的直接接触,减少副反应,提高首效,同时高韧性碳包覆膜中含有单壁碳纳米管,可降低颗粒之间的接触电阻,提高电子传输速度。预锂化隔膜(pls)中的有机和无机预锂涂层可提高锂离子通量、增强极片与隔膜高粘附力、为极片的膨胀提供缓冲空间且为首次充电消耗的不可逆锂离子提供补充。本发明可为硅碳负极材料的产业化使用、高能量密度锂离子电池的可靠性创造条件,也可为当前锂离子电池低温下充放电困难提供解决方案,为新能源汽车的长续航、高功率、低温下正常充放电使用保驾护航。
附图说明
12.图1为本发明高韧性碳包覆snw和mhc材料组装示图;图2为本发明首次库伦效率图;图3为本发明循环性能图;图4为本发明
‑
30℃下的容量保持率。
具体实施方式
13.下面将结合本发明实施例中的附图,对本发明实施例中的技术方案进行清楚、完整地描述,显然,所描述的实施例仅仅是本发明一部分实施例,而不是全部的实施例。基于本发明中的实施例,本领域普通技术人员在没有做出创造性劳动前提下所获得的所有其他实施例,都属于本发明保护的范围。
14.实施例:如图1
‑
4所示,本发明实施例提供一种掺硅补锂技术方案,具体包括如下步骤:步骤一.改性开孔硬碳(mhc)的制备:按照质量比8:1:0.1:0.1:0.1:3分别将浓硫酸、双氧水、聚乙二醇400、氨基丙醇、无水乙醇、硬碳加入到搅拌容器中,保持环境为0℃,搅拌时间约15分钟至溶液粘稠;将以上粘稠溶液用去离子水清洗至溶液ph为6
±
0.5,然后在100℃下烘干,最后在300℃下处理24h,获得mhc;步骤二:snw和mhc的材料组装和高韧性碳包覆膜处理:按照质量比8:12将snw和mhc在真空条件下强力机械搅拌融合,搅拌时间45分钟,获得snw和mhc的复合物;将snw和mhc复合物、单壁碳纳米管
‑
swcnt(0.65%wt)和cmc(0.35%wt)复合溶液、苯胺、蔗糖按照96:2:1:1的质量比加入去离子水中,溶液的固含量为15%,搅拌60分钟,在180℃下喷雾干燥,在氩气条件下400℃煅烧120分钟,获得本发明的高韧性碳包覆snw和mhc复合物;步骤三:可预锂化隔膜(pls)的制备:按照质量比70:15:15将聚偏氟乙烯
‑
pvdf、聚氧化乙烯
‑
peo、li2co3等溶解在n
‑
甲基吡咯烷酮
‑
nmp和无水乙腈(质量比—nmp:无水乙腈=8:2)的溶液中,固含量为20%,真空搅拌120分钟,然后利用隔膜涂敷设备将以上浆体均匀涂敷在高孔隙率聚丙烯(pp)基膜正反两面,干燥后的涂敷厚度约为2
µ
m,获得本发明的预锂化隔膜
‑
pls。
15.步骤一中浓硫酸和双氧水可与硬碳材料结合在一起且插入硬碳材料的碳层间隙内,聚乙二醇400、氨基丙醇和无水乙醇可促进材料的分散和孔隙率的调控,便于硬碳材料获得均一稳定的碳层间距、多孔结构,ph的控制条件也是为了控制硬碳材料的开孔程度,ph越小开孔程度越大,300℃下的热处理可使得浓硫酸和双氧水的氧化分解而产生气体,从而使得硬碳材料的层间距打开且获得更多的孔隙结构。
16.步骤二中snw和mhc的强力机械搅拌融合可使得snw较好的嵌入和插层到mhc的多孔结构中,也可将snw和mhc较好的均匀复合在一起;单壁碳纳米管
‑
swcnt(0.65%wt)和cmc(0.35%wt)复合溶液的包覆不仅可以提高电极材料的导电性,还能提高包覆层的韧性,抵抗材料膨胀导致结构崩塌的风险,苯胺、蔗糖的二次包覆可减少材料与电解液的直接接触,降低副反应的发生。
17.步骤三中高孔隙率pp基膜可为高锂离子通量创造条件,pvdf和peo可增强极片与隔膜的粘附力,降低极片与隔膜的间隙也可在一定程度上为极片的膨胀提供缓冲空间,同时提高保液能力和离子传输能力,而li2co3可提供预锂化,为snw和mhc材料首次充电消耗的不可逆锂离子提供补充。
18.一种锂离子电池的组装方法,包括如下具体步骤:步骤一:负极极片的制备,负极复合活性材料的质量比为snw:mhc:ag=8:12:80,负极浆料的物质配比为负极复合活性材料:sp:pvdf=94.5%:2%:3.5%,按照以上质量比分别加入负极复合活性材料、sp、pvdf,干混15分钟,加入一定量nmp,控制浆料的固含量为45%,搅拌120分钟后慢搅备用;依次经过涂布、冷压、模切、分条后获得负极极片;步骤二:正极极片的制备,正极浆料的物质配比为li(ni
0.8
co
0.1
mn
0.1
)o2 :sp:cnt:pvdf=94.5%:3.5%:0.5%:1.5%,按照以上质量比分别加入li(ni
0.8
co
0.1
mn
0.1
)o2 、sp、cnt、pvdf,加入一定量nmp,控制浆料的固含量为60%,搅拌120分钟后慢搅备用;依次经过涂布、冷压、模切、分条后获得正极极片;
电池的组装:以本发明获得的预锂化隔膜
‑
pls为隔膜,搭配步骤一和步骤二的极片完成卷绕、热压、hi
‑
pot、焊接、装配、烘烤、注液、静置、化成、老化、容量、测k、包装完成电池的组装,获得高能量密度锂离子电池。
19.电性能测试和数据收集:(1)首次库伦效率计算:提取单个电池的化成和容量的充放电容量,计算出每个电池的首次库伦效率
‑
ice;(2)循环性能测试:常温条件下,以1c的倍率充到4.2v,恒压充电的截止电流为0.05c,以1c的倍率放电到3.0v;(3)低温性能测试:在
‑
30℃下,以1c的倍率充到4.2v,恒压充电的截止电流为0.05c,记录此时的充电容量,以1c的倍率放电到3.0v,记录此时的放电容量,用以上充、放电容量和常温下的充、放电容量对比,计算电池在低温下的充、放电容量保持率。
20.尽管已经示出和描述了本发明的实施例,对于本领域的普通技术人员而言,可以理解在不脱离本发明的原理和精神的情况下可以对这些实施例进行多种变化、修改、替换和变型,本发明的范围由所附权利要求及其等同物限定。