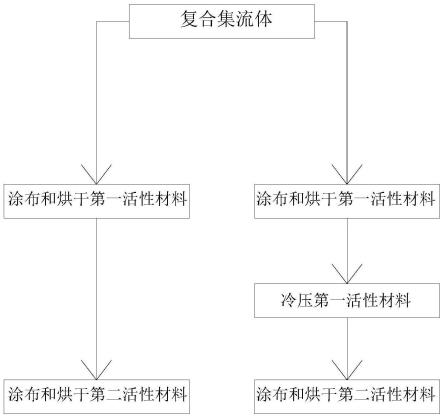
1.本技术涉及电池领域,具体而言,涉及一种极片涂布结构和方法。
背景技术:2.在电池行业中,传统地,极片制作工艺中,通常是通过冷压工艺实施。即在集流体上涂布主要包括活性材料的浆料后,进行辊压。并且,由于正极极片和负极极片是两个独立的部件,因此,正极极片和负极极片通过分别独立地进行冷压而制作。
技术实现要素:3.针对不能通过现有工艺制作将正极和负极结合为一体的复合集流体的问题,本技术提出了一种极片涂布结构和方法。
4.本技术是这样实现的:
5.在第一方面,本技术的示例提供了一种极片涂布方法。其中的极片包括集流体,且该集流体包括绝缘的支撑体以及分别形成于集流体的两侧表面且极性相反的第一导电层和第二导电层。该涂布方法包括:提供极性相反的第一活性材料和第二活性材料,第一活性材料的烘干温度大于或等于第二活性材料的烘干温度;将第一活性材料涂布于与其极性相同的第一导电层的表面并烘干,然后将第二活性材料涂布于与其极性相同的第二导电层的表面并烘干。
6.在本技术的一些示例中,涂布方法包括:在涂布第一活性材料并烘干之后、涂布第二活性材料之前执行的压片步骤。
7.在本技术的一些示例中,压片步骤是利用辊通过冷压实现的。
8.在本技术的一些示例中,在执行压片步骤的过程中,通过调整第一活性材料的压实密度以抑制集流体的卷曲。
9.在本技术的一些示例中,压实密度通过第一活性材料的面密度确定压实密度。
10.在本技术的一些示例中,涂布操作和烘干操作是同步进行的。
11.在本技术的一些示例中,烘干操作是在烘箱中通入热风实施的。
12.在本技术的一些示例中,涂布第一活性材料的速度、涂布第二活性材料的速度分别独立地控制于的第一范围,烘干第一活性材料的热风的风频、烘干第二活性材料的热风的风频分别独立地控制于的第二范围。
13.在本技术的一些示例中,第一活性材料的粘度为3000-8000mpa
·
s-1
、第二活性材料的粘度为4000-8000mpa
·
s-1
,涂布第一活性材料的速度、涂布第二活性材料的速度分别独立,控制于5-20m/min之间,烘干第一活性材料的热风的风频、烘干第二活性材料的热风的风频分别独立,控制于15-50m/min之间,第一活性材料的烘干温度为90-110℃,第二活性材料的烘干温度为60-90℃。
14.在第二方面,本技术的示例提出了一种极片涂布结构,其包括:复合集流体,具有绝缘膜层以及分别形成于所述绝缘膜层的两侧表面且极性相反的第一导电层和第二导电
层;干燥的第一活性材料层,附着于所述第一导电层表面;干燥的第二活性材料层,附着于所述第二导电层表面,所述第二活性材料层与所述第一活性材料层的极性相反。
15.在本技术的一些示例中,绝缘膜层的厚度分别大于第一导电层的厚度和第二导电层的厚度;或者,干燥的第二活性材料层的压实密度为1.0-2.2g/cm3;或者,第二活性材料层的表面是平整的。
16.在本技术的一些示例中,第一导电层为铝层。
17.在本技术的一些示例中,第二导电层为铜层。
18.在本技术的一些示例中,绝缘膜层为聚乙烯膜层、聚丙烯膜层或聚酰亚胺膜层。
19.在以上实现过程中,本技术实施例提供的极片涂布方法,在同时具有正极性导电层和负极性导电层的复合集流体(双极性集流体)的基础上,选择适当的涂布方式,从而改变了传统的涂布观念,实现了一种新的涂布方式。该方案适用于上述的双极性集流体,从而使得是制作双极性的极片的方案成为可能。
附图说明
20.为了更清楚地说明本技术实施例的技术方案,下面将对实施例中所需要使用的附图作简单地介绍,应当理解,以下附图仅示出了本技术的某些实施例,因此不应被看作是对范围的限定,对于本领域普通技术人员来讲,在不付出创造性劳动的前提下,还可以根据这些附图获得其他相关的附图。
21.图1为本技术实施例中提出的复合集流体的结构示意图;
22.图2示出了在图1的复合集流体的正极导电层表面形成正极活性材料以及第一种冷压后的结构变化;
23.图3示出了在图1的复合集流体的正极导电层表面形成正极活性材料以及第二种冷压后的结构变化;
24.图4为本技术实施例中提出的基于复合集流体的极片涂布流程示意图。
25.图标:100-复合集流体;101-聚合物薄膜;102-铝层;103-铜层;203-第一活性材料。
具体实施方式
26.传统的分别被独立地制作的正极极片、负极极片受电池壳容积和厚度的影响。并且,由于这些极片一般都是使用金属箔材如铜箔、铝箔,因此这些的极片厚度较大,从而会使卷绕层数较少,进而限制基于其的电池的容量的设计。
27.基于这样的现状分析,为了提高电池容量,可以通过降低极片的厚度,使得在相同的电池壳容积和厚度的情况下,可以装入卷绕层数更多的电芯。
28.基于此,在本技术示例中选择使用复合集流体,因此,采用该复合集流体可以制作复合的极片,从而在现有电池壳容积的情况下做到极片更薄、卷绕层数更多,从而使同一电池壳容积的情况下达到提升容量的要求。
29.并且,考虑到极片的制作方法,本技术对应开发了一种新的使用上述复合集流体的新型电池极片的制作工艺——具体涉及针对复合集流体的涂布方式的改进。
30.为了使本领域技术人员更清楚地和容易地实施本技术方案,示例中的复合集流体
100的结构如图1所示。
31.该复合集流体100包括聚合物薄膜101(或称绝缘的支撑体,或称绝缘膜层)、以及分别位于该聚合物薄膜101的两侧表面的铝层102和铜层103。其中铜层103作为负极性的结构层存在,而铝层102则作为正极性的结构层存在。
32.其中的聚合物薄膜101可以采用pet、pp、pi等物质,即聚乙烯膜层、聚丙烯膜层或聚酰亚胺膜层。聚合物薄膜101是绝缘的,以便电隔离铜层103和铝层102。其中铜层103和铝层102可以通过化学气相沉积等方式制作而成,且其厚度一般小于聚合物薄膜101的。
33.以下就上述结构的复合集流体100的极片的涂布方式进行说明。
34.由于复合集流体具有正极性导电层(下称第一导电层)和负极性导电层(下称第二导电层),因此,本技术示例中的涂布方式要实现在上述的正极性导电层上形成正极活性材料层(下称第一活性材料)、在上述的负极性导电层上形成负极活性材料层(下称第二活性材料)。
35.其中的正极活性材料一般可以选择为磷酸铁锂,三元,锰酸锂,钴酸锂等;其中的负极活性材料一般可以选择为石墨,硅碳,钛酸锂等。在具体的工艺中上述物质被配制为浆料,以便进行涂布。例如,将磷酸铁锂等活性物质(如磷酸铁锂、锰酸锂、钴酸锂、三元等)、导电剂(如sp,cnts等)以及粘结剂(如pvdf等)混合为黏稠状浆料。或者,将石墨等活性材料(石墨、硅碳、钛酸锂等)、导电剂(如sp、cnts、石墨烯等)以及粘结剂(cmc、sbr等)混合为黏稠状浆料。
36.总体上而言,在本技术的涂布的上述第一活性材料和第二活性材料根据各自的烘干温度对涂布方式进行选择。并且,上述第一活性材料和第二活性材料是通过分步而在不同的步骤中涂布完成的,参阅图4。
37.方案一
38.例如,当第一活性材料的烘干温度大于或等于第二活性材料的烘干温度时,则,先涂布第一活性材料,待其被烘干之后,再涂布第二活性材料并进行烘干。需要指出的是,在涂布操作中,极性相同的导电层和活性材料配合。即正极性的导电层(如铝)表面涂布正极性的活性材料(如磷酸铁锂)。
39.方案二
40.在另一些示例中,在分步涂布不同极性的活性材料中,还可以结合辊压(如冷压)。例如,当第一活性材料的烘干温度大于或等于第二活性材料的烘干温度时,先涂布第一活性材料,待第一活性材料被烘干之后对该第一活性材料进行冷压;然后,涂布第二活性材料并进行烘干。
41.上述的示例中,由于方案一进行了涂覆和烘干操作,因此,其操作相对比较简单。
42.方案二中还要进行冷压操作(压片步骤),并且是在第二次涂布之前先执行。由于冷压操作会对涂布的活性材料的应力情况产生影响,甚至于会导致膜材卷曲情况的发生,从而会严重地影响第二次涂布的正常进行。因此,需要对冷压操作进行特别地考虑。示例中,在执行该压片步骤的过程中,通过调整所述第一活性材料的压实密度以抑制集流体的卷曲。即避免对第一活性材料的过度挤压,从而抑制第一活性材料使复合集流体发生卷曲。
43.并且,在实践中,如果冷压操作的压实密度选择不当,会导致冷压侧向未涂布侧卷曲。例如,在复合集流体上的正极性层上涂布正极活性材料并进行了不当的冷压之后,以正
极侧向负极侧卷曲。参阅图2,在复合集流体上涂布第一活性材料203,经过烘干和恰当的冷压操作(例如压实密度为1.0至2.2g/cm3)后,第一活性材料203的厚度相对于涂布和烘干之后的厚度变得更薄,并且其整体仍然能够保持平整的结构。如果在涂布第一活性材料203和经过烘干,采用不当的冷压操作(例如压实密度大于2.2g/cm3),将会导致整体结构发生卷曲而不能保持平整,如图3所示。在图3中,被不恰当地冷压的第一活性材料203向内卷,从而使负极导电层(如铜层103)位于最内圈层。
44.在上述的涂布方案中,活性材料在涂布后都进行了烘干处理,这是基于活性材料的是以浆料的形式制作而成,且其中会含有溶剂、塑化剂等物质,因此,烘干处理可以将熔剂、塑化剂等物质去掉,以避免这些物质对电极的潜在不利影响,同时也使活性材料更易于附着在复合集流体表面。通常地,涂布操作和烘干操作可以同时进行。例如在加热的设备中进行涂布操作。利用使用具有涂布设备的烘箱进行涂布操作。
45.作为一种可替代的具体实例,第一涂布方式可通过下述方式实施。
46.步骤11、配制电极材料
47.第一活性材料(正极)的粘度为3000-8000mpa
·
s-1
,干燥温度为90至110℃;第二活性材料(负极)的粘度为4000-8000mpa
·
s-1
,干燥温度为60至90℃。正极浆料的具体组成为磷酸铁锂、超细导电炭黑和聚偏氟乙烯。负极浆料的具体组成为石墨、超细导电炭黑以及羧甲基纤维素钠。
48.步骤12、正极涂布
49.涂布的速度选择为5-20m/min,烘箱温度为90至110℃,风频为15-50m/min。
50.步骤13、负极涂布
51.涂布的速度选择为5-20m/min,烘箱温度为60至90℃,风频为15-20m/min。
52.或者,第二涂布方式还可通过下述方式实施。
53.步骤21、配制电极材料
54.第一活性材料(正极)的粘度为3000-8000mpa
·
s-1
,干燥温度为90至110℃;第二活性材料(负极)的粘度为4000-8000mpa
·
s-1
,干燥温度为60至90℃。具体组成为磷酸铁锂、超细导电炭黑和聚偏氟乙烯。正极浆料的具体组成为磷酸铁锂、超细导电炭黑和聚偏氟乙烯。负极浆料的具体组成为石墨、超细导电炭黑以及羧甲基纤维素钠。
55.步骤22、正极涂布
56.涂布的速度选择为5-20m/min,烘箱温度为90至110℃,风频为15-50m/min。
57.步骤23、正极冷压
58.将单面的正极极片按照1.0-2.0g/cm3的压实密度辊压至一定厚度后。
59.步骤24、负极涂布
60.涂布的速度选择为5-20m/min,烘箱温度为60至90℃,风频为15-20m/min。
61.对比例
62.第三涂布方式可通过下述方式实施。
63.步骤31、配制电极材料
64.第一活性材料(正极)的粘度为3000-8000mpa
·
s-1
,干燥温度为90至110℃;第二活性材料(负极)的粘度为4000-8000mpa
·
s-1
,干燥温度为60至90℃。正极浆料的具体组成为磷酸铁锂、超细导电炭黑和聚偏氟乙烯。负极浆料的具体组成为石墨、超细导电炭黑以及羧
甲基纤维素钠。
65.步骤32、负极涂布
66.涂布的速度选择为5-20m/min,烘箱温度为60至90℃,风频为15-20m/min。
67.步骤33、正极涂布
68.涂布的速度选择为5-20m/min,烘箱温度为90至110℃,风频为15-50m/min。
69.上述涂布方式会导致,先涂布的负极材料层出现开裂、脱落情况。
70.第四涂布方式还可通过下述方式实施。
71.步骤21、配制电极材料
72.第一活性材料(正极)的粘度为3000-8000mpa
·
s-1
,干燥温度为90至110℃;第二活性材料(负极)的粘度为4000-8000mpa
·
s-1
,干燥温度为60至90℃。正极浆料的具体组成为磷酸铁锂、超细导电炭黑和聚偏氟乙烯。负极浆料的具体组成为石墨、超细导电炭黑以及羧甲基纤维素钠。
73.步骤22、正极涂布
74.涂布的速度选择为5-20m/min,烘箱温度为90至110℃,风频为15-50m/min。
75.步骤23、正极冷压
76.将单面的正极极片按照2.2g/cm3的压实密度辊压至一定厚度后。
77.步骤24、负极涂布
78.涂布的速度选择为5-20m/min,烘箱温度为60至90℃,风频为15-20m/min。
79.上述涂布方式会导致,先涂布的正极材料层出现卷曲,并使符合集流体也出现卷曲。
80.综上,本技术方案对于复合集流体而言,选择对干燥温度高的电极材料先涂布和烘干,然后再对干燥温度低的电极材料进行涂布烘干。或者,在对干燥温度高的电极材料先涂布和烘干之后,经过冷压,然后再对干燥温度低的电极材料进行涂布烘干。
81.上述的涂布方式可以确保涂布质量更高,可以避免对干燥温度低的电极材料先涂布和烘干的方案所导致的问题——干燥温度高的电极材料在后涂布和烘干,会使先涂布的低干燥温度的电极材料层出现开裂、脱层等外观问题。
82.以上所述仅为本技术的优选实施例而已,并不用于限制本技术,对于本领域的技术人员来说,本技术可以有各种更改和变化。凡在本技术的精神和原则之内,所作的任何修改、等同替换、改进等,均应包含在本技术的保护范围之内。