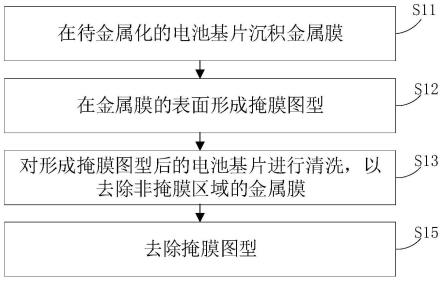
1.本发明属于太阳能电池技术领域,尤其涉及一种电池电极的制作方法和太阳能电池。
背景技术:2.相关技术中,在制作太阳能电池时,需要在硅片制造电极,以将太阳能电池金属化。然而,现有的制造方法成本较高。例如,可通过电镀的方式在硅片表面形成电极。然而,普通的电镀需要使用掩膜和干膜,成本依然很高。基于此,如何降低太阳能电池的生产过程中制造电极的成本,成为了亟待解决的问题。
技术实现要素:3.本技术提供一种电池电极的制作方法和太阳能电池,旨在解决如何降低太阳能电池的生产过程中制造电极的成本的问题。
4.第一方面,本技术提供一种电池电极的制作方法。所述制作方法包括:
5.在待金属化的电池基片沉积金属膜;
6.在所述金属膜的表面形成掩膜图型;
7.对形成掩膜图型后的所述电池基片进行清洗,以去除非掩膜区域的金属膜;
8.去除所述掩膜图型。
9.可选地,所述电池基片包括正面和背面,在待金属化的电池基片沉积金属膜,包括:
10.在所述正面和所述背面均沉积金属膜。
11.可选地,所述金属膜为铜膜。
12.可选地,在所述金属膜的表面形成掩膜图型,包括:
13.利用喷墨技术或3d打印技术在所述金属膜的表面形成掩膜图型。
14.可选地,对形成掩膜图型后的所述电池基片进行清洗以去除非掩膜区域的金属膜,包括:
15.将所述电池基片置入酸溶液中进行清洗。
16.可选地,在所述将所述电池基片置入酸溶液中进行清洗的步骤之后,所述制作方法还包括:
17.对所述电池基片进行水冲洗。
18.可选地,去除所述掩膜图型,包括:
19.将所述电池基片置入碱溶液中进行清洗。
20.可选地,所述金属膜的厚度范围为:[2μm,8μm]。
[0021]
可选地,所述掩膜图型包括正面细栅掩膜,所述正面细栅掩膜的宽度范围为[20μm,30μm],所述正面细栅掩膜的线数范围为[110条,130条];和/或,
[0022]
所述掩膜图型包括背面细栅掩膜,所述背面细栅掩膜的宽度范围为[30μm,60μm],
所述正面细栅掩膜的线数范围为[170条,210条]。
[0023]
第二方面,本技术还提供一种太阳能电池。所述太阳能电池包括电池基片和设置在电池基片上的电极,所述电极采用上述任一项所述的方法制作得到。
[0024]
本发明实施例的制作方法和太阳能电池中,在待金属化的电池基片沉积金属膜,去除自非掩膜区域的金属膜和掩膜图型,使得电池基片剩下的金属膜,与掩膜图型覆盖的部分一致,从而形成电极。这样,避免了电镀形成电极的过程中产生的高昂费用,可以降低太阳能电池的生产过程中制造电极的成本。
附图说明
[0025]
图1是本技术一个实施例提供的电池电极的制作方法的流程示意图;
[0026]
图2是本技术一个实施例提供的电池电极的制作方法的流程示意图;
[0027]
图3是本技术一个实施例提供的电池电极的制作方法的流程示意图;
[0028]
图4是本技术一个实施例提供的电池电极的制作方法的流程示意图;
[0029]
图5是本技术一个实施例提供的电池电极的制作方法的流程示意图;
[0030]
图6是本技术一个实施例提供的电池电极的制作方法的流程示意图;
[0031]
图7是本技术一个实施例提供的电池电极的制作方法的流程示意图。
具体实施例
[0032]
为了使本发明的目的、技术方案及优点更加清楚明白,以下结合附图及实施例,对本发明进行进一步详细说明。应当理解,此处所描述的具体实施例仅仅用以解释本发明,并不用于限定本发明。
[0033]
现有技术在制作太阳能电池的过程中,制造电极的成本较高。本技术提供一种制造方法和太阳能电池,在待金属化的电池基片沉积金属膜,并去除自掩膜图型露出的金属膜和掩膜图型,从而形成电极。这样可以降低太阳能电池的生产过程中制造电极的成本。
[0034]
请参阅图1,本技术实施例提供的制作方法用于制作太阳能电池,制作方法包括:
[0035]
步骤s11:在待金属化的电池基片沉积金属膜;
[0036]
步骤s12:在金属膜的表面形成掩膜图型;
[0037]
步骤s13:对形成掩膜图型后的电池基片进行清洗,以去除非掩膜区域的金属膜;
[0038]
步骤s15:去除掩膜图型。
[0039]
本技术实施例的制作方法,在待金属化的电池基片沉积金属膜,去除非掩膜区域的金属膜和掩膜图型,使得电池基片剩下的金属膜,与掩膜图型覆盖的部分一致,从而形成电极。这样,避免了电镀形成电极的过程中产生的高昂费用,可以降低太阳能电池的生产过程中制造电极的成本。
[0040]
可以理解,在现有的电镀方案中,需要ni、cu、ag或sn的化学电镀液槽,还需要大量水洗和对废液进行处理。而本技术实施例的制作方法,没有采用电镀的方案,省去了这些成本。
[0041]
具体地,在本技术实施例中,太阳能电池为异质结电池(heterojunction with intrinsic thin-layer,hjt)。采用本技术实施例的制作方法,可降低hjt电池的金属化成本,推进hjt电池的产业化进程。
[0042]
可以理解,在其他的实施例中,太阳能电池可包括发射极和背面钝化电池(passivatedemitterandrearcell,perc)、硅薄膜异质结电池(silicon hetero-junction,shj)等其他类型的电池。在此不对太阳能电池的具体形式进行限定。
[0043]
具体地,可通过物理气相沉积(physical vapour deposition,pvd)、溅射等方式在金属膜的表面形成金属膜。在此不进行限定。
[0044]
具体地,非掩膜区域是指未被掩膜图型覆盖的区域。掩膜区域是指被掩膜图型覆盖的区域。
[0045]
可选地,在步骤s11之前,制作方法包括:对硅片进行制绒,以在硅片上形成绒面;清洗制绒后的硅片;对清洗后的硅片进行非晶硅沉积;对进行了非晶硅沉积后的硅片沉积导电层和减反膜,以得到待金属化的电池基片。如此,可以生成待金属化的电池基片,以便在电池基片上制作电极。
[0046]
具体地,硅片可为单晶硅片,也可为多晶硅片。硅片可为n型硅片,也可为p型硅片。在此不对硅片的具体种类进行限定。
[0047]
具体地,可利用氢氧化钾,采用双面制绒的工艺,来对硅片制绒。如此,可在硅片上形成起伏不平的绒面,减少反射,增加硅片对太阳光的吸收。
[0048]
可以理解,在其他的实施例中,也可以利用酸来制绒。
[0049]
进一步地,绒面可呈金字塔状。绒面的高度的范围可为[2μm,5μm],例如为2μm、2.6μm、3.1μm、4.5μm、5μm。绒面的反射率的范围为[9%,11%],例如为9%、9.2%、9.8%、10.3%、11%。
[0050]
具体地,可采用rca标准清洗法或者臭氧(o3)工艺进行对制绒后的硅片进行清洗。如此,可以高效地去除硅片表面的有机物、碱液、金属离子或表面颗粒物,避免其对制作过程产生不利影响。
[0051]
具体地,可先双面沉积本征非晶硅,再在双面本征非晶硅层中的一面沉积非晶硅n薄膜,在双面本征非晶硅层中的另一面沉积非晶硅p薄膜。本征非晶硅的厚度范围为[2nm,8nm],例如为2nm、2.6nm、3.1nm、4.5nm、5nm、5.7nm、6.1nm、7.2nm、8nm。非晶硅n薄膜的厚度范围为[3nm,10nm],例如为3nm、3.1nm、4.5nm、5nm、5.7nm、6.1nm、7.2nm、8nm、8.3nm、9.5nm、10nm。非晶硅p薄膜的厚度范围为[3nm,10nm],例如为3nm、3.1nm、4.5nm、5nm、5.7nm、6.1nm、7.2nm、8nm、8.3nm、9.5nm、10nm。如此,可形成pn结。
[0052]
具体地,导电层可包括透明导电氧化物(tco)薄膜。导电层的厚度范围为[70nm,110nm],例如为70nm、79nm、82nm、91nm、96nm、100nm、104nm、110nm。如此,可收集横向电流。
[0053]
具体地,减反膜可包括sin膜。减反膜的厚度范围为[70nm,110nm],例如为70nm、79nm、82nm、91nm、96nm、100nm、104nm、110nm。如此,可减少反射,增加硅片对太阳光的吸收。
[0054]
进一步地,可在低压、高温或射频激发等条件下,使得通入的sih4与nh3发生电离,从而在电池片的表面形成sin膜。
[0055]
请参阅图2,可选地,电池基片包括正面和背面,步骤s11包括:
[0056]
步骤s111:在正面和背面均沉积金属膜。
[0057]
如此,通过在电池基片的两面均沉积金属膜,从而在两面都采用本技术实施例的制作方法制作电极,避免了两面制作电极的方式不同所导致的工艺繁琐和容易出错,有利于提高制作的效率。
[0058]
具体地,可在正面和背面整面地沉积金属膜,也可在正面和背面的部分区域沉积金属膜。在此不对沉积金属膜的范围进行限定。
[0059]
具体地,可在正面和背面同时沉积金属膜;可先在正面沉积金属膜,再在背面沉积金属膜;也可先在背面沉积金属膜,再在正面沉积金属膜。在此不对在两面沉积金属膜的顺序进行限定。
[0060]
请参阅图3,可选地,步骤s11包括:
[0061]
步骤s112:在待金属化的电池基片沉积铜膜。
[0062]
换言之,金属膜为铜膜。
[0063]
如此,采用铜作为制造电极的材料,由于铜的价格较便宜,故能够进一步降低成本。而且,含铜的废液容易回收和再利用,故整体的成本较低。
[0064]
可以理解,在其他的实施例中,也可以在待金属化的电池基片沉积银膜、铝膜、钛膜、铬膜、镍膜、铂合金膜或其他金属膜。在此不对金属膜的具体形式进行限定。
[0065]
请参阅图4,可选地,步骤s12包括:
[0066]
步骤s121:利用喷墨技术或3d打印技术在金属膜的表面形成掩膜图型。
[0067]
如此,在形成掩膜图型的过程中,喷墨的机器与电池基片无接触、无压力,可以避免电池基片因形成掩膜图型而损坏,从而提高成品率,有利于从整体上降低成本。而利用3d打印技术制作掩膜图型,效率较高。
[0068]
可以理解,在其他的实施例中,也可通过物理气相沉积、溅射、热蒸发、旋涂或原子层沉积等方式在金属膜的表面形成掩膜图型。
[0069]
请参阅图5,可选地,步骤s13包括:
[0070]
步骤s131:将电池基片置入酸溶液中进行清洗。
[0071]
如此,可以高效地去除自掩膜图型露出的金属膜,成本较低。具体地,酸溶液可包括硫酸、硝酸、盐酸、和磷酸中的至少一种。在本实施例中,酸溶液为硫酸。
[0072]
具体地,清洗时,温度小于或等于65℃,时间小于或等于600s。温度例如为45℃、47℃、56℃、58℃、62℃、65℃。时间例如为300s、350s、420s、480s、560s、600s。
[0073]
具体地,掩膜可由耐酸材料制成。如此,保证掩膜不会被酸去除,从而保证被掩膜遮挡的金属膜不会被去除。
[0074]
请注意,酸溶液还可去除非掩膜区域的tco薄膜。
[0075]
可以理解,在其他的实施方式中,除化学刻蚀的方式之外,还可以采用物理刻蚀的方式去除自掩膜图型露出的金属膜。在此不进行限定。
[0076]
请参阅图6,可选地,在步骤s13之后,制作方法包括:
[0077]
步骤s14:对电池基片进行水冲洗。
[0078]
如此,可以去除电池基片上的酸和杂质,避免残留的酸和杂质在电池基片上停留时间过长而损坏电池基片,可以提高成品率,有利于从整体上降低成本。
[0079]
具体地,水可为蒸馏水。可用水冲洗电池基片或浸泡电池基片。在此不对水清洗电池基片的具体方式进行限定。
[0080]
请参阅图7,可选地,步骤s15包括:
[0081]
步骤s151:将电池基片置入碱溶液中进行清洗。
[0082]
如此,可以高效地去除自掩膜图型,成本较低。具体地,碱可包括氢氧化钠、氢氧化
钾或氢氧化钙中的至少一种。在本实施例中,碱溶液为氢氧化钾koh。
[0083]
具体地,清洗时,温度小于或等于65℃,时间小于或等于600s。温度例如为45℃、47℃、56℃、58℃、62℃、65℃。时间例如为300s、350s、420s、480s、560s、600s。
[0084]
具体地,掩膜可由不耐碱材料制成。如此,保证掩膜被碱去除。
[0085]
可以理解,在其他的实施方式中,除化学去除的方式之外,还可以采用物理去除的方式去除掩膜图型。在此不进行限定。
[0086]
可选地,金属膜的厚度范围为:[2μm,8μm]。例如为2μm、2.6μm、3.1μm、4.5μm、5μm、6.3μm、7.5μm、8μm。如此,有利于保证保证基于金属膜所形成的电极的可靠性。
[0087]
可选地,掩膜图型包括正面细栅掩膜,正面细栅掩膜的宽度范围为[20μm,30μm],例如为20μm、22μm、23μm、27μm、30μm。正面细栅掩膜的线数范围为[110条,130条],例如为110条、112条、126条、129条、130条。可以理解,由于被掩膜图型覆盖的金属膜未被刻蚀,最终保留,故正面电极的细栅宽度和线数,与正面细栅掩膜的参数一致。为避免冗余,在此不再赘述。如此,可将电池基片的电流导出。
[0088]
可选地,掩膜图型包括背面细栅掩膜,背面细栅掩膜的宽度范围为[30μm,60μm],例如为30μm、34μm、45μm、58μm、60μm。正面细栅掩膜的线数范围为[170条,210条],例如为170条、176条、183条、198条、203条、210条。可以理解,由于被掩膜图型覆盖的金属膜未被刻蚀,最终保留,故背面电极的细栅宽度和线数,与背面细栅掩膜的参数一致。为避免冗余,在此不再赘述。如此,可将电池基片的电流导出。
[0089]
在本实施例中,细栅的线数与g12型硅片的尺寸匹配。g12型硅片尺寸较大,市场占有率高,容易获得,有利于降低成本。
[0090]
可选地,在形成电极后,可进行铜细线的串焊和层压,可使用铜线垂直连接的焊接技术,以形成电池组件。
[0091]
本技术实施例提供的太阳能电池,包括电池基片和设置在电池基片上的电极,电极采用上述任一项的方法制作得到。
[0092]
例如采用下列方法制作得到:
[0093]
步骤s11:在待金属化的电池基片沉积金属膜;
[0094]
步骤s12:在金属膜的表面形成掩膜图型;
[0095]
步骤s13:去除自掩膜图型露出的金属膜;
[0096]
步骤s15:去除掩膜图型,以使被掩膜图型覆盖的金属膜露出。
[0097]
本技术实施例的太阳能电池,在待金属化的电池基片沉积金属膜,去除非掩膜区域的金属膜和掩膜图型,使得电池基片剩下的金属膜,与掩膜图型覆盖的部分一致,从而形成电极。这样,避免了电镀形成电极的过程中产生的高昂费用,可以降低太阳能电池的生产过程中制造电极的成本。
[0098]
请注意,关于太阳能电池的解释和说明请参照前文关于制作方法的解释和说明,为避免冗余,在此不再赘述。
[0099]
以上仅为本发明的较佳实施例而已,并不用以限制本发明,凡在本发明的精神和原则之内所作的任何修改、等同替换和改进等,均应包含在本发明的保护范围之内。