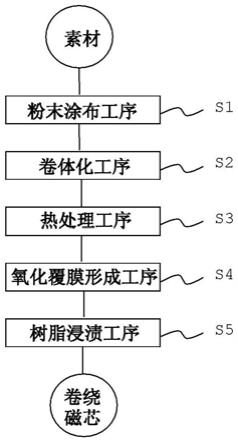
1.本发明涉及卷绕磁芯的制造方法、及卷绕磁芯。
背景技术:2.目前,在家用电器、工业设备、车辆等各种用途中,使用感应器、变压器、扼流圈等线圈零件。线圈零件由敷设于磁芯的线圈构成,在该磁芯中,磁特性优异的非晶质及结晶质的软磁性金属薄带的卷体即卷绕磁芯被广泛使用。
3.卷绕磁芯形成为对通常还被称为条带及带的软磁性金属薄带一边施加张力,一边牢固地缠绕于支承体(卷轴)的周围,并在卷径方向上将软磁性金属薄带多层地重叠的环状的卷体。将卸下支承体的卷体在卷绕开始、卷绕结束的软磁性金属薄带的端部焊接并固定,以使软磁性金属薄带不会散开。或者,将带支承体的卷体在该卷绕结束的软磁性金属薄带的端部焊接并固定。接着,实施缓和在卷体形成时被赋予的应力,或纳米晶体化而体现期望的磁特性的热处理。软磁性金属薄带不会因以热处理后、经时变化、施加于卷体的外力而散开的方式浸渍环氧树脂等,维持卷绕状态。
4.软磁性金属薄带的厚度非常薄,通常为10μm~数百μm的厚度且在表面具有数μm的凹凸,但宏观上为平滑的面。软磁性金属薄带为良导体,因此,如果平滑面彼此短路,且薄带之间的绝缘不足,则有时产生在薄带之间流动的涡电流,使卷绕磁芯产生大的电力损失。特别是,在超100khz的高频用途中,该趋势显著,如果薄带之间没有适当地电绝缘,则作为线圈零件,不适合在高频下的使用。
5.目前,为了在薄带之间得到高的绝缘性,在专利文献1中提出了在磁性金属薄带的表面附着由非磁性的绝缘性无机物构成的微粉制成卷绕磁芯,在专利文献2中提出了使磁性金属薄带氧化,在层间形成包含氧化铁的绝缘层。
6.现有技术文献
7.专利文献
8.专利文献1:特开平1-259510号公报
9.专利文献2:特表2003-500850号公报
技术实现要素:10.发明所要解决的问题
11.根据使用的环境,有时因雷电等而对线圈零件施加高的浪涌电压。在这种线圈零件中,寻求不会因施加于线圈的浪涌电压引起的电压振动而产生绝缘破坏,为了确认线圈零件的绝缘的耐力,有时实施脉冲试验。在脉冲试验中,将在kv级的高电压下,以数百ns以下上升的宽度的窄的脉冲电压施加于线圈零件的线圈两端。如果进行脉冲试验,则判明了由于卷绕磁芯中产生的快速的磁通变化而在薄带中产生磁致伸缩振动,即使以在薄带之间得到高的绝缘性的方式如专利文献1及专利文献2那样构成卷绕磁芯,在脉冲试验后的卷绕磁芯中,也有时薄带之间短路等、薄带之间的绝缘变差。在要求对电涌的耐性的情况下,即
使不会导致绝缘破坏,这样的线圈零件也不适于高频下的使用。如果在薄带之间得到高的绝缘性,则也可以附着更厚的由绝缘性无机物构成的微粉、或形成厚的包含氧化铁的绝缘层而扩大薄带之间的间隔。但是,卷绕磁芯的占积率(还称为填充因子)降低,有时不能满足卷绕磁芯大型化而确定的线圈零件的尺寸规格。另外,即使以规定的尺寸构成卷绕磁芯,也有时得不到期望的磁特性。
12.因此,本发明的目的在于,提供一种能够提高将软磁性金属薄带卷绕而形成为环状的卷体的卷绕磁芯的薄带之间的绝缘性的卷绕磁芯的制造方法和卷绕磁芯。
13.用于解决问题的技术方案
14.根据本发明的一方式,能够提供一种卷绕磁芯的制造方法,其具有:第一工序,在非晶质组织的软磁性金属薄带的表面附着非磁性且具有绝缘性的金属氧化物的粉末;第二工序,在所述第一工序后,将所述软磁性金属薄带卷绕成环状,得到在薄带之间夹杂金属氧化物的粉末的卷体;第三工序,在非氧化性气氛中对所述卷体进行热处理;第四工序,在所述第三工序后,在比所述第三工序的热处理温度低的温度、且氧化气氛中,对所述卷体进行氧化覆膜形成处理,使所述软磁性金属薄带的表面氧化;第五工序,在所述第四工序后,在所述卷体的薄带之间浸渍树脂并固化。
15.另外,根据本发明的一方式,优选的是,所述第三工序是在所述非晶质组织的软磁性金属薄带中使纳米晶体析出的热处理a,或对所述非晶质组织的软磁性金属薄带进行应力缓和的热处理b。
16.另外,根据本发明的一方式,优选的是,将所述第一工序中的金属氧化物的粉末的附着量以由下式(1)得到的金属氧化物的重量比设为0.1%以上1.2%以下。
17.金属氧化物的重量比(%)=附着于软磁性金属薄带的金属氧化物的重量/软磁性金属薄带的重量
×
100
……
(1)
18.另外,根据本发明的一方式,优选的是,将所述第三工序中的热处理的温度在所述热处理a中设为450℃以上620℃以下,在所述热处理b中设为250℃以上400℃以下。
19.另外,根据本发明的一方式,优选的是,将所述第四工序的氧化覆膜形成处理在氧化气氛中,在240℃以上、且未满所述第三工序的热处理温度的温度下进行。
20.根据本发明的其它方式,提供一种卷绕磁芯,其卷绕有软磁性金属薄带,其中,所述软磁性金属薄带具有非晶质组织或纳米晶体组织,在所述软磁性金属薄带的表面具有构成所述软磁性金属薄带的源自金属的fe的氧化层,在所述软磁性金属薄带之间夹杂非磁性且具有绝缘性的金属氧化物的粉末,且浸渍树脂,占积率为65%以上75%以下。
21.根据本发明的其它方式,优选的是,所述fe的氧化层包含赤铁矿(fe2o3)。
22.根据本发明的其它方式,优选的是,由下式(2)得到的频率1mhz的阻抗变化率的绝对值为20%以下。
23.阻抗变化率(%)=(脉冲试验前的阻抗
‑
脉冲试验后的阻抗)/脉冲试验前的阻抗
×
100
……
(2)
24.发明效果
25.根据本发明,能够提供一种能够提高将软磁性金属薄带卷绕而形成为环状的卷体的卷绕磁芯的薄带之间的绝缘性的卷绕磁芯的制造方法和卷绕磁芯。
附图说明
26.图1是本发明的一实施方式的卷绕磁芯的制造工序的流程图。
27.图2是用于本发明的一实施方式的卷绕磁芯的制造的粉末涂布装置的概略图。
28.图3(a)是金属氧化物的粉末附着于表面的状态的软磁性金属薄带的截面示意图,(b)是表示其它附着状态的软磁性金属薄带的截面示意图。
29.图4是与表示卷体的薄带之间的状态的卷轴正交的截面的放大示意图。
30.图5是表示根据卷绕磁芯的脉冲试验前后的阻抗求出的阻抗变化率和频率的关系的图。
31.图6是表示金属氧化物的粉末的附着量(mgo重量比)和脉冲试验前后的阻抗的变化率之间的图。
32.图7是用于说明脉冲试验的电路图。
具体实施方式
33.以下,对本发明的实施方式进行具体说明,但本发明不限定于此。
34.图1是本发明的卷绕磁芯的制造方法的制造工序的流程图。如图1所示,在第一工序中,将非晶质组织的软磁性金属薄带作为素材,在其表面附着非磁性且具有绝缘性的金属氧化物的粉末(粉末涂布工序s1)。在第二工序中,以成为规定的形状、大小的卷体的方式,将在所述第一工序中得到的非晶质组织的软磁性金属薄带卷绕成环状,制成在薄带之间夹杂金属氧化物的粉末的卷体(卷体化工序s2)。在第三工序中,在非氧化性气氛中对卷体进行热处理,在所述非晶质组织的软磁性金属薄带中使纳米晶体析出,或对上述非晶质组织的软磁性金属薄带进行应力缓和(热处理工序s3)。在第四工序中,调整为比上述热处理工序s3的热处理温度低的温度,并在氧化气氛中进行氧化覆膜形成处理,使软磁性金属薄带的表面氧化(氧化覆膜形成工序s4)。在第五工序中,在得到的卷体的薄带之间浸渍树脂并使其固化,将上述金属氧化物的粉末粘着制成卷绕磁芯(树脂浸渍工序s5)。
35.本实施方式的卷绕磁芯为卷绕有软磁性金属薄带的卷绕磁芯。上述软磁性金属薄带具有非晶质组织或纳米晶体组织,在上述软磁性金属薄带的表面形成有构成上述软磁性金属薄带的源自金属的金属的氧化层,在上述软磁性金属薄带之间利用树脂粘着有非磁性且具有绝缘性的金属氧化物的粉末。以下,对各工序进行详细说明。
36.(1)素材
37.本实施方式中成为素材的非晶质组织的软磁性金属薄带优选由以fe为主成分的软磁性合金构成。通常,为fe的含量为65原子%以上的软磁性合金,软磁性合金的组成除以fe为主成分这一点以外,没有特别限制。也取决于与其它非铁金属的平衡,但由于对饱和磁化等磁特性造成影响,因此,优选包含以原子%计为77.5%以上的fe,更优选为包含78.0%以上的fe。作为成为该素材的非晶质组织的软磁性金属薄带,通过热处理,能够制成纳米晶体组织的软磁性金属薄带,或非晶质组织的软磁性金属薄带。
38.构成卷绕磁芯的软磁性合金薄带具有非晶质组织或纳米晶体组织。软磁性金属薄带为非晶质组织、或纳米晶体组织的区别能够通过x射线衍射法的x射线衍射谱而易于同定。例如,纳米晶体组织的薄带的x射线衍射谱在表示结晶质相的部分(衍射角2θ=45
°
附近)具有衍射峰,非晶质组织的薄带的x射线衍射谱具有表示非晶质相的光晕(halo)图案。
衍射角2θ=45
°
附近的衍射峰为bcc结构的fe结晶或fesi结晶的(110)衍射峰。衍射峰的角度包含由于元素的固溶等而相对于jcpds卡的数据变动等误差,因此,将与各个jcpds卡极其接近的衍射峰的角度(2θ)的情况设为“附近”。
39.非晶质组织没有结晶结构。另一方面,纳米晶体组织具有通常平均晶粒径为100nm以下的晶粒。纳米晶体组织通常为从非晶质相以成为结晶化的核的cu及其它非铁金属的集群为起点结晶化的、平均晶粒径例如为30nm以下的fe结晶、或fesi结晶的颗粒,成为纳米晶体在非晶质相中随机地取向并分散的组织。纳米晶体组织通过对可纳米晶体化的非晶质组织的软磁性金属薄带实施热处理来获得。
40.作为纳米晶体组织的软磁性金属薄带,例如,能够设为fe-si-m1-b-cu系的软磁性合金和fe-m2-b系的软磁性合金,也可以为其它软磁性合金。m1优选为选自由nb、ti、zr、hf、v、ta、mo构成的组中的1种以上。另外,m2优选为选自由nb、cu、zr、hf构成的组中的1种以上。作为fe-si-m1-b-cu系的软磁性合金,已知的有日立金属株式会社的
ファインメット
(finemet、注册商标)、vacuumschmelze gmbh&co.kg.的vitroperm(注册商标),作为fe-m2-b系的软磁性合金,已知有magnetec gesellschaft fur magnettechnologie mbh的nanoperm(注册商标),能够使用这些合金。
41.作为非晶质组织的软磁性金属薄带,例如为fe-si-b系的软磁性合金,已知有metglas,inc.的metglas(注册商标)2605sa1,能够使用该合金。
42.软磁性金属薄带通过使合金的熔液急冷凝固的液态急冷法来获得。通常,通过被称为得到106℃/秒左右、或其以上的冷却速度的单辊法或双辊法的公知的方法连续地形成为长条。软磁性金属薄带能够使用在市场上流通的程度的宽度和厚度的金属薄带,也可以使用从在市场上流通的程度的宽度的材料切割的宽度的金属薄带,例如,能够使用2~300mm左右的宽度的金属薄带。另外,厚度为10μm以上且数百μm以下的厚度,软磁性金属薄带从能形成非晶质方面考虑优选设为50μm以下的厚度。
43.(2)粉末涂布工序s1
44.准备调整成规定的宽度、长度的软磁性金属薄带和非磁性且具有绝缘性的金属氧化物的粉末。金属氧化物的粉末优选为氧化镁(mgo)、氧化钛(tio2)、或氧化铝(al2o3)中的任一个。通过激光衍射散射式粒度分布测定装置测定的金属氧化物的粉末的平均粒径(累积粒度分布中的中值粒径d50)优选为0.5μm以上1.0μm以下,以在软磁性金属薄带的表面均匀地附着金属氧化物的粉末,并且,在得到卷绕磁芯的占积率的同时得到规定的薄带之间的间隔。另外,如果考虑应力对薄带的影响,则不优选粗大的粉末夹杂于薄带之间,粉末的最大粒径优选为7μm以下。在此,最大粒径为95体积%粒径(d95)。
45.将金属氧化物的粉末分散到甲苯、异丙醇、乙醇等溶剂中,制成悬浮液。金属氧化物的粉末对软磁性金属薄带的附着量能够通过悬浮液的浓度进行调整。将卷绕磁芯的占积率设为65%以上也取决于施加于设为卷体时的软磁性金属薄带的张力,但如果金属氧化物为氧化镁(mgo),则mgo相对于溶剂1kg优选为30~200g。准备调整成规定的粉末浓度的悬浮液,并将其涂布于软磁性金属薄带的表面。图2表示用于说明将软磁性金属薄带浸渍于悬浮液中,并涂布金属氧化物的粉末的粉末涂布装置的概略图。在图示的装置中,使用制成卷筒状的软磁性金属薄带100,引出其端部,并将其浸渍于加入了悬浮液120的容器150后,从悬浮液中引出软磁性金属薄带,穿过刮掉软磁性金属薄带的辊面(在通过单辊法得到软磁性
金属薄带的情况下,与冷却辊接触的面)侧的剩余的悬浮液的杆145,穿过旋转的刮板140,控制软磁性金属薄带的自由面(在通过单辊法得到软磁性金属薄带的情况下,未与冷却辊接触的面)侧的悬浮液,继续穿过调整成规定的温度的干燥炉130,使将规定量的金属氧化物的粉末涂布于表面的软磁性金属薄带卷取成卷筒状。除此以外,也可以通过辊涂机将悬浮液涂布于软磁性金属薄带的表面,或进行喷雾并涂布。
46.图3表示金属氧化物的粉末附着于表面的状态的软磁性金属薄带的截面示意图。在软磁性金属薄带上也可以具有凹处及突起,但未图示。如图3(a),穿过杆145后的软磁性金属薄带在一表面(自由面、图中的上表面)的整体大致均匀地附着金属氧化物的粉末,在另一表面(辊面、图中的下表面)除去金属氧化物的粉末的大部分。此外,在利用刮板(刮刀、刮件)140控制软磁性金属薄带的一面侧的悬浮液后,如图3(b),在软磁性金属薄带10的一表面(自由面、图中的上表面)上,金属氧化物的粉末20的附着变少。金属氧化物的粉末的附着量也取决于使用的金属氧化物的粉末,但以金属氧化物的重量比优选为0.1%以上1.2%以下。优选为0.2%以上,更优选为0.3%以上。另外,优选为1.1%以下,更优选为1.0%以下。如果为mgo,则每单位面积优选为0.1
×
10
-3
kg/m2以上1.5
×
10
-3
kg/m2以下。
47.附着于软磁性金属薄带10的表面的金属氧化物的粉末20在用手指轻轻擦的程度下容易脱落。因此,通过干燥后搬运机械装置内的软磁性金属薄带,金属氧化物的粉末容易附着、堆积到与软磁性金属薄带接触的零件、特别是搬运辊等零件,有时产生搬运不稳定的不便等。另外,由于金属氧化物的粉末的脱落,金属氧化物的粉末向软磁性金属薄带的附着量在粉末涂布开始和结束时不同,也有时难以使金属氧化物的粉末均匀地附着。因此,在与机械装置的零件接触的一侧的软磁性金属薄带的一表面(例如,辊面)上优选减少金属氧化物的粉末的附着。另外,也可以设为软磁性金属薄带的一表面不附着金属氧化物的粉末的状态。此外,在附着了金属氧化物的粉末后,通过在软磁性金属薄带的一表面上除去金属氧化物的粉末,能够形成减少金属氧化物的粉末的附着、或未附着金属氧化物的粉末的状态。
48.另外,在通过单辊法得到软磁性金属薄带的情况下,已知软磁性金属薄带的表面形态在与冷却辊接触的面(辊面)侧和未接触的面(自由面)侧不同。在辊面上,容易产生冷却辊的瑕疵及异物的附着、或铸造时的气氛气体的卷入引起的深度数μm~十数μm左右的凹处,在自由面上容易产生十μm以下的高度的突起。突起对薄带之间的短路造成影响,因此,如果考虑软磁性金属薄带的表面形态,则金属氧化物的粉末优选至少附着于软磁性金属薄带的自由面。
49.(3)卷体化工序s2
50.将表面附着有金属氧化物的粉末的卷筒状的软磁性金属薄带安装于收卷装置,将软磁性金属薄带的端部引出,一边施加张力,一边强力地缠绕于支承体(卷轴)的周围,制成在卷径方向上重叠多层软磁性金属薄带的环状的卷体。软磁性金属薄带的卷取速度优选为10m/分钟以上500m/分钟以下。卷体的尺寸多种多样,但例如优选设为内径5mm以上140mm以下、外径20mm以上200mm以下。从卷体卸下支承体,对软磁性金属薄带的开始卷取的端部、及结束卷取的端部进行点焊并固定,从而制成卷体。通过金属氧化物的粉末,能够制成软磁性金属薄带的滑动及卷紧变得良好,卷绕时的张力的调整容易且作业性优异,从内周到外周的薄带之间的间隔的偏差小的卷体。
51.图4是与表示卷体的薄带之间的状态的卷轴正交的截面的示意图。构成在软磁性
金属薄带10之间夹杂金属氧化物的粉末20的空气层30。在薄带之间,金属氧化物的粉末并未图示,但粒度大的颗粒在薄带之间被夹持,但最多成为附着于软磁性金属薄带的一表面的状态。
52.薄带之间的间隔能够通过在制成卷体时给予软磁性金属薄带的张力、软磁性金属薄带的表面的凹凸状态、软磁性金属薄带的表面的金属氧化物的粉末的厚度来调整,但薄带之间的间隔越宽,卷绕磁芯的占积率越低,有时不能得到期望的磁特性。另外,如果考虑在对后述的软磁性金属薄带的表面形成氧化覆膜时向薄带之间供给氧,则优选适当选择金属氧化物的粉末及卷体的形成的条件,以使卷绕磁芯的占积率成为65%以上75%以下,另外,即使薄带之间的间隔窄,占积率也为0.2μm以上。
53.(4)热处理工序s3
54.接着,在非氧化性的气氛下以规定的温度对卷体进行热处理,缓和在卷体形成时被赋予的应力,或使其纳米晶体化,体现期望的磁特性。非氧化性的气氛为氧浓度只要为100ppm以下的n2、ar等不活泼性气体气氛中即可。虽然也取决于合金组成,但如果软磁性金属薄带为非晶质组织,则优选在非氧化性气氛中在250℃以上的温度下进行热处理,进行应力缓和。当过于提高温度时,开始结晶化,因此,优选为比合金的结晶化温度低10℃~150℃的温度,典型而言,优选为400℃以下。例如,如果为metglas(注册商标)2605sa1,则优选为340℃~400℃的热处理温度。热处理温度为升温后最高到达温度,在将该温度保持规定时间的情况下,也是该保持温度。
55.另外,在软磁性金属薄带中使纳米晶体析出,制成具有纳米晶体组织的软磁性金属薄带的情况下,优选在构成软磁性金属薄带的软磁性合金的结晶化温度以上的温度下进行热处理。如果过于提高温度,则结晶磁各向异性高,有时使软磁特性恶化的fe2b等结晶相析出,因此,热处理温度为合金的结晶化温度以上,并且,期望为500℃以上620℃以下,优选为540℃以上590℃以下的范围。纳米晶体组织是fe结晶、或fesi结晶的纳米晶体粒在非晶质相中随机取向并分散的组织。纳米晶体粒的平均晶粒径优选为30nm以下,更优选为20nm以下。纳米晶体粒的平均晶粒径为使用x射线衍射谱中的bccfe(si)〔衍射面(110)〕的峰值,通过谢勒公式(scherrer公式)得到的微晶的大小。另外,在纳米晶体组织中,纳米晶体粒优选占据30体积%以上,更优选为50体积%以上。纳米晶体组织的纳米晶体粒的体积分率通过线段法来计算。此外,已知在通过热处理使非晶质组织的软磁性金属薄带结晶化,制成纳米晶体组织时,在软磁性金属薄带中产生1%左右的体积收缩。通过在薄带之间夹杂金属氧化物的粉末,易于软磁性金属薄带在卷绕的周向上的滑动,因此,通过收缩导致的卷体的卷紧,能够抑制对软磁性金属薄带施加应力。
56.在应力缓和的情况、或纳米晶体化的情况没有区别的情况下,热处理时间期望为5分钟以上14小时以下。热处理时间为在最高到达温度下保持的时间。如果热处理中使用的炉为在非氧化性气氛中可温度控制到620℃附近的加热炉,则即使为任意的加热炉,也能够没有特别问题地使用,但如果为可控制氧浓度的加热炉,则更优选能够使用以下的氧化膜形成工序s4中相同的加热炉,进行连续地处理。
57.(5)氧化覆膜形成工序s4
58.在热处理工序s3后,卷体在氧化气氛中,优选在氧浓度1%以上50%以下的气氛中,且在240℃以上,低于热处理工序s3中的热处理温度(最高到达温度)的温度下进行氧化
覆膜形成处理,在软磁性金属薄带的表面形成氧化覆膜。气氛中的氧浓度优选为50体积%以下,更优选为大气气氛。卷体具备在软磁性金属薄带10之间夹杂金属氧化物的粉末10而形成的空气层30。通过该氧化覆膜形成处理,氧也被供给到空气层30,在卷体的外表面上体现的软磁性金属薄带不用说在卷入的软磁性金属薄带的表面上形成氧化覆膜。氧化覆膜的厚度为提高薄带之间的绝缘性,作为卷绕磁芯抑制磁特性的降低的程度的厚度,且优选为超过基于自然氧化的氧化覆膜的厚度(~十几nm左右),数十nm~数百nm。氧化覆膜的厚度能够通过利用透射电子显微镜(tem)以50k~200k倍进行观察来定量,也可以使用x射线光电子能谱法(xps)等手法。
59.另外,氧化覆膜为源自构成软磁性金属薄带的金属的金属的氧化层,优选为赤铁矿(fe2o3)、磁铁矿(fe3o4)。也可以包含方铁矿(feo),但与赤铁矿和磁铁矿相比,为低电阻,因此,期望为少量的。氧化物的同定能够通过拉曼光谱等分析手法进行。在氧化覆膜形成后,薄带之间的金属氧化物的粉末与卷体形成时同样,仍旧附着于软磁性金属薄带的表面。如果软磁性金属薄带为纳米晶体组织,则期望将氧化覆膜形成温度设为240以上350℃以下的范围。另外,如果软磁性金属薄带为非晶质组织,则期望将热处理温度设为240以上300℃以下的范围。
60.(6)树脂浸渍工序s5
61.在氧化覆膜形成工序s4后,在得到的卷体的表面和软磁性金属薄带的薄带之间浸渍绝缘树脂,并使其固化,制成卷绕磁芯。通过用绝缘树脂将薄带之间粘接,成为磁性合金薄带被一体化的结构,能够防止卷体状态的软磁性金属薄带通过外力等松开,并维持卷绕状态。另外,使金属氧化物的粉末粘接于薄带之间,并且,还有助于薄带之间的绝缘。此外,绝缘树脂优选无斑地覆盖软磁性金属薄带的表面,但在卷体的薄带之间,至少软磁性金属薄带的表面的3%以上优选由绝缘树脂覆盖。
62.作为绝缘树脂,优选使用环氧系及聚酰亚胺系的热固化性树脂。作为在卷体的薄带之间浸渍绝缘树脂的方法,可以将卷体浸渍于绝缘树脂的浴槽并使其浸渍,也可以将绝缘树脂及其前体涂布于卷体的卷轴方向上体现的侧面并使其浸渍。另外,也可以采用真空浸渍等方法,促进树脂向卷体的薄带之间的浸渍。为了使在卷体的表面、及薄带之间涂布的热固化性树脂、或其前体固化,在规定的温度下进行固化处理。固化处理的温度也取决于使用的树脂,但如果为环氧系树脂,则优选在20~180℃的温度下进行1分钟~24小时固化。
63.实施例
64.(实施例1)
65.作为素材的软磁性金属薄带,准备以fe为主成分,由包含si、b及微量的cu、nb的软磁性合金构成的非晶质组织的软磁性金属薄带,即能够热处理而可析出纳米晶体的日立金属株式会社制
ファインメット
(注册商标)ft-3。软磁性金属薄带为长条,其厚度为14μm,宽度为20mm。密度为7.3
×
103kg/m3。通过差示扫描量热仪(dsc)的测定,确认到该合金的结晶化开始温度为470℃。
66.在粉末涂布工序s1中在软磁性金属薄带的表面上附着金属氧化物的粉末。作为非磁性且具有绝缘性的金属氧化物的粉末,准备了平均粒径(d50)为0.7μm的氧化镁(mgo)的粉末。氧化镁的密度为3.6
×
103kg/m3。将异丙醇作为溶剂,使相对于溶剂1kg为100g的氧化镁的粉末分散到溶剂中,制成悬浮液。将悬浮液移到图2中所示的粉末涂布装置的容器,一
边搅拌悬浮液,一边将软磁性金属薄带100在悬浮液中浸渍0.5秒,以在悬浮液中防止氧化镁的凝集及沉淀。从悬浮液中引出软磁性金属薄带100,穿过刮掉软磁性金属薄带的辊面侧的剩余的悬浮液的杆145,穿过旋转的刮板140,使软磁性金属薄带的表面的剩余的悬浮液落下,控制自由面侧的悬浮液,继续穿过调整成80℃的温度的干燥炉130,得到表面涂布有规定量的mgo的粉末的软磁性金属薄带100。
67.通过以下式计算mgo粉末向软磁性金属薄带的表面的附着量作为mgo重量比(金属氧化物的重量比)。mgo重量比为0.73%。
68.mgo重量比=附着于软磁性金属薄带的mgo重量/软磁性金属薄带的重量
×
100(%)
69.此外,软磁性金属薄带的重量为粉末涂布工序前的卷筒1卷量的软磁性金属薄带的重量a,附着于软磁性金属薄带的mgo重量为从粉末涂布工序后的卷筒1卷量的软磁性金属薄带的重量b中减去上述重量a的重量。
70.将卷体化工序s2中在表面上附着有金属氧化物的粉末的软磁性金属薄带设为卷体。将在粉末涂布工序s1中得到的软磁性金属薄带安装于收卷装置,将软磁性金属薄带的端部引出,并强力地缠绕于不锈钢制的支承体的周围,在卷径方向上卷绕多层软磁性金属薄带。从卷体卸下支承体,对软磁性金属薄带的卷绕开始、卷绕结束的软磁性金属薄带的端部进行点焊并固定,制成内径33mm、外径50mm的卷体。
71.在热处理工序s3中对卷体实施热处理,进行将软磁性金属薄带的非晶质组织制成纳米晶体组织的纳米晶体化。将卷体在电炉中且氮气氛中以最高温度580℃、保持时间20分钟的条件(温度曲线)进行热处理,将非晶质组织的软磁性金属薄带制成纳米晶体组织的软磁性金属薄带。
72.使用透射型电子显微镜(tem)以倍率20,000倍对从纳米晶体组织的软磁性金属薄带得到的试样进行了组织观察。在得到的照片中画出长度lt的任意的直线,求出直线与能够目视确认的大小的纳米晶体粒交叉的部分的长度的合计lc,并计算沿着直线的晶粒的比例ll=lc/lt。反复五次该操作,将ll进行平均,由此,求出纳米晶体粒的体积分率。在此,体积分率vl=vc/vt(vc为纳米晶体粒的体积的总和,vt为试样的体积。)近似地视为vl≒lc3/lt3=ll3。对于软磁性金属薄带而言,纳米晶体粒的基于x射线衍射的平均晶粒径为10nm,纳米晶体组织中所占的体积分率为80体积%。
73.在氧化覆膜形成工序s4中对热处理工序s3的卷体实施热处理,在软磁性金属薄带的表面上形成氧化覆膜。将结束了纳米晶体化的热处理的卷体在电炉中且大气中以最高温度280℃、保持时间2小时的条件(温度曲线)进行热处理,从而在软磁性金属薄带的表面形成氧化覆膜。从卷体的外周剥离软磁性金属薄带的一部分,进行拉曼光谱分析和透射电子显微镜(tem)的截面观察,其结果,形成于得到的卷体的软磁性金属薄带的表面的氧化覆膜主要为赤铁矿(fe2o3)。另外,形成比附着金属氧化物的粉末前的软磁性金属薄带的表面厚的氧化覆膜。
74.使氧化覆膜形成工序s4后的卷体浸渍于树脂。将形成有氧化覆膜的卷体浸渍于将环氧树脂稀释成以丙酮计为5%~30%浓度的浸渍液中1分钟后,在调整成150℃的恒温槽中使环氧树脂固化,得到占积率为70%的卷绕磁芯。此外,占积率以下述方式计算。
75.占积率=(we/ρ)/{(od2-id2)
×
ht
×
π/4}
76.在此,
77.we:氧化覆膜形成后的卷体重量(g)
78.ρ:软磁性金属薄带的密度(g/cm3)
79.od:氧化覆膜形成后的卷体外径(cm)
80.id:氧化覆膜形成后的卷体内径(cm)
81.ht:氧化覆膜形成后的卷体高度(cm)
82.在图7所示的电路中,作为峰值电压1.6kv、电压施加宽度200nsec的条件,对经过树脂浸渍工序s5得到的卷绕磁芯实施脉冲试验。在试验前后测定阻抗,以该变化评价卷绕磁芯的绝缘性。此外,就阻抗而言,将1匝的线圈穿过卷绕磁芯的内径,通过阻抗分析仪hp4194a以频率1khz~10mhz评价阻抗,通过下式计算试验前后的阻抗变化率。
83.阻抗变化率=(脉冲试验前的阻抗
‑
脉冲试验后的阻抗)/脉冲试验前的阻抗
×
100(%)
84.另外,使用供脉冲试验的卷绕磁芯,通过直流电阻仪hioki3227对其内径侧表面和外径侧表面评价脉冲试验前后的直流电阻rdc。试验前的直流电阻rdc为161ω,试验后的直流电阻rdc为81ω。
85.(比较例1)
86.除在软磁性金属薄带的表面未附着金属氧化物的粉末,另外在软磁性金属薄带的表面也没有进行氧化覆膜形成以外,在与实施例1同样的顺序和条件下制作卷绕磁芯。占积率为73.8%。对得到的卷绕磁芯实施脉冲试验,评价试验前后的阻抗变化率和直流电阻rdc。试验前的直流电阻rdc为34ω,试验后的直流电阻rdc为1.7ω。
87.(比较例2)
88.除在软磁性金属薄带的表面未附着金属氧化物的粉末的以外,在与实施例1同样的顺序和条件下制作卷绕磁芯。占积率为73.7%。另外,对得到的卷绕磁芯实施脉冲试验,评价试验前后的阻抗变化率和直流电阻rdc。试验前的直流电阻rdc为92ω,试验后的直流电阻rdc为2.1ω。
89.(比较例3)
90.在软磁性金属薄带的表面没有进行氧化覆膜形成以外,在与实施例1同样的顺序和条件下制作卷绕磁芯。占积率为72.8%。另外,对得到的卷绕磁芯实施脉冲试验,评价试验前后的阻抗变化率和直流电阻rdc。试验前的直流电阻rdc为105ω,试验后的直流电阻rdc为4.4ω。
91.图5表示根据脉冲试验前后的阻抗算出的阻抗变化率和频率的关系。对于比较例1~3的卷绕磁芯,在实施例1的卷绕磁芯中,试验前后的直流电阻rdc高,高频段的阻抗的变化被抑制。
92.(实施例2~6)
93.除通过悬浮液的浓度调整金属氧化物的粉末对软磁性金属薄带的附着量的以外,与实施例1同样,制作卷绕磁芯。对得到的卷绕磁芯实施脉冲试验,评价试验前后的频率1mhz下的阻抗变化率和直流电阻rdc。
94.(比较例4~8)
95.除通过悬浮液的浓度调整金属氧化物的粉末对软磁性金属薄带的附着量,另外,
在软磁性金属薄带的表面没有进行氧化覆膜形成以外,在与实施例1同样的顺序和条件下制作卷绕磁芯。对得到的卷绕磁芯实施脉冲试验,评价试验前后的阻抗变化率和直流电阻rdc。
96.将实施例2~6、比较例4~6的卷绕磁芯的占积率、氧化覆膜形成前后的重量变化率、脉冲试验前后的直流电阻rdc、阻抗示于表1。另外,图6表示金属氧化物的粉末的附着量(mgo重量比)和脉冲试验前后的阻抗的变化率的关系。
97.【表1】
[0098][0099]
实施例2~6的卷绕磁芯的脉冲试验前后的阻抗的变化均小,且阻抗变化率的绝对值为20%以下。另外,脉冲试验后的直流电阻rdc也被高地维持。即使金属氧化物的粉末对软磁性金属薄带的表面的附着少,也能够得到优异的绝缘性能。
[0100]
符号说明
[0101]
10、100软磁性金属薄带
[0102]
20属氧化物的粉末
[0103]
30空气层
[0104]
120悬浮液
[0105]
130干燥炉
[0106]
140刮板(刮刀)
[0107]
150容器。