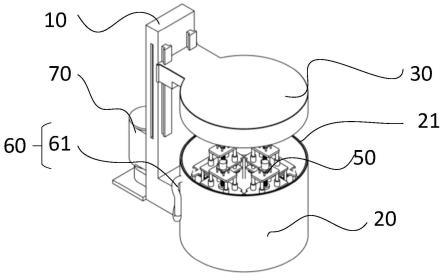
1.本发明涉及电池封装技术领域,具体涉及一种软包电芯二次封装装置及封装方法。
背景技术:2.随着新能源汽车对锂离子电池续航里程和安全性能要求的不断提高,软包电池得到日益发展。软包电芯内包含正极、负极、隔膜和电解液,需用铝塑膜进行密封。因尺寸不断增大,软包电芯的生产制造难度不断增大。
3.软包电芯在使用前需要经过小电流充电活化,即化成工艺。化成将产生废气。小部分废气残存于正负极片间,影响电芯性能;大部分废气暂存于气袋中。软包电芯二次封装工艺即为排出电芯极片间和气袋中的废气,并将与气袋连接的铝塑膜边进行热压封装的步骤,是软包电芯生产重要工序之一。
4.当前一般的生产制造是把软包电芯平放于二次封装设备的电芯夹具中,经导轨送至特定位置。此特定位置上方和下方均有可垂直往复运动的腔体,电芯夹具设计在下腔体中,上腔体降下,使得两腔体合并后形成密闭空间;随后用刺刀刺破气袋,同时进行负压抽气。经充分抽气后,上、下封头相对运动,对气袋侧铝塑膜进行热封。这种方式容易导致电解液被吸出并从刺破口飞溅,造成铝塑膜、刺刀和封头等设备部件的腐蚀。此外,该装置对负压真空度生产条件要求苛刻:真空度低难以抽出电芯内部废气,耗时长,生产效率降低;真空度高容易吸出甚至气化电解液,导致电解液损失,电芯保液量难控制,不利于生产效率和良率的提高。当残余电解液在二次封装区域,存在影响封装可靠性的风险。此外,当常规设备需要提高生产效率和增加工位时,需要配置数量对应的上下腔体,增加生产制造成本和设备体积。
技术实现要素:5.有鉴于此,本发明提供一种软包电芯二次封装装置及封装方法,可解决电解液负压二次封装过程中负压抽气时电解液飞溅的问题。
6.本发明提供的一种软包电芯二次封装装置,包括底座、设于所述底座上的主腔体和上盖、以及设于所述主腔体上的抽真空装置,所述主腔体的内部安装有旋转平台以及设于所述旋转平台上的热压封装装置,所述热压封装装置包括封装装置和刺破装置,所述旋转平台在软包电芯二次封装的过程中转动,使软包电芯内的电解液在离心力作用下向外运动。
7.进一步地,所述热压封装装置还包括电芯夹具,所述封装装置设于所述刺破装置和所述电芯夹具之间。
8.进一步地,所述封装装置包括位于所述旋转平台上方的第一驱动部以及位于所述旋转平台下方的第二驱动部,所述第一驱动部包括固定于所述旋转平台上的第一固定柱、固定于所述第一固定柱上部的第一支撑板、以及能够相对所述第一支撑板上下运动的第一
封装板,所述第二驱动部包括固定于所述旋转平台下部的第二固定柱、固定于所述第二固定柱上的第二支撑板、以及能够相对所述第二支撑板上下运动的第二封装板,所述第一封装板下部内侧固定有所述刺破装置,所述第一封装板下部和所述第二封装板的上部的外侧分别固定有上封头和下封头,所述电芯夹具位于所述上封头和所述下封头的外侧。
9.进一步地,所述旋转平台上设有供所述上封头和所述下封头穿过的条形槽。
10.进一步地,所述第一驱动部还包括第一导杆、第一螺纹杆、第一电机安装板和第一电机,所述第一电机固定于所述第一电机安装板上且与所述第一螺纹杆固定连接,所述第一螺纹杆穿过所述第一电机安装板和所述第一支撑板且与所述第一支撑板螺纹配合,所述第一导杆穿过所述第一支撑板且与所述第一电机安装板和所述第一封装板固定连接;所述第二驱动部还包括第二导杆、第二螺纹杆、第二电机安装板和第二电机,所述第二电机固定于所述第二电机安装板上且与所述第二螺纹杆固定连接,所述第二螺纹杆穿过所述第二电机安装板和所述第二支撑板且与所述第二支撑板螺纹配合,所述第二导杆穿过所述第二支撑板且与所述第二电机安装板和所述第二封装板固定连接。
11.进一步地,所述电芯夹具包括滑杆和能够相对所述滑杆滑动的第一夹板。
12.进一步地,所述底座包括水平部、和所述水平部连接的垂直部、以及安装在所述垂直部上并与之平行的传送导轨,所述上盖安装在所述传送导轨上,能够沿所述传送导轨上下运动。
13.进一步地,所述旋转平台的底部设有转动轴,所述转动轴穿过所述主腔体安装在所述底座上并与一驱动装置连接。
14.进一步地,所述抽真空装置包括位于主腔体外部的抽气管,所述主腔体端口部还设有密封圈,与所述上盖完全闭合后,通过所述抽真空装置可实现腔体内部真空度的控制。
15.本发明还提供了一种上述所述的软包电芯二次封装装置的封装方法包括以下步骤:将软包电芯固定于所述旋转平台;利用所述上盖封闭所述主腔体;控制所述旋转平台转动并达到目标转速;利用抽真空装置对所述主腔体内部抽真空;利用所述刺破装置刺穿软包电芯,使软包电芯内部废气排出;利用所述封装装置对软包电芯进行热压封装;二次封装完成。
16.与现有的技术相比,本发明具有以下有益的技术效果:
17.本发明提供的一种软包电芯二次封装装置及封装方法,通过上盖和主腔体形成密闭负压内腔,通过抽真空装置实现腔内真空度的控制,降低了生产调试的复杂性;通过驱动装置带动旋转平台及软包电芯进行有目标的转速的离心运动,电芯内部的电解液向电芯底部方向移动,与负压抽气的方向相反,避免了常规软包二次封装装置和方法导致的电解液从刺破口被吸出并飞溅的问题,避免了铝塑膜、刺刀和封头等设备部件的腐蚀。可有效提高电解液的保持量,减少电解液的损失,提高电芯品质。在刺破装置和封装装置的共同作用下可快速实现软包电芯的二次封装,且本发明中的热压封装装置可根据需要调整数量,实现多工位共用同时操作,提高了软包电芯的生产效率。
附图说明
18.图1为本发明软包电芯二次封装装置外观结构示意图。
19.图2为本发明软包电芯二次封装装置的剖视图。
20.图3为本发明中旋转平台及热压封装装置组装后的结构示意图。
21.图4为本发明中热压封装装置的结构示意图。
22.图5为本发明中刺破装置和电芯夹具结构放大示意图。
23.其中:10-底座;11-水平部;12-垂直部;13-传送导轨;14-皮带;20-主腔体;21-密封圈;30-上盖;40-旋转平台;41-条形槽;42-转动轴;50-热压封装装置;51-封装装置;511-第一驱动部;5111-第一固定柱;5112-第一支撑板;5113-第一导杆;5114-第一封装板;5115-第一螺纹杆;5116-第一电机;5117-上封头;5118-第一电机安装板;512-第二驱动部;5121-第二固定柱;5122-第二支撑板;5123-第二导杆;5124-第二封装板;5125-第二螺纹杆;5126-第二电机;5127-下封头;5128-第二电机安装板;52-刺破装置;521-刺刀;53-电芯夹具;531-滑杆;532-第一夹板;533-第二夹板;5331-刀槽;60-抽真空装置;61-抽气管;70-驱动装置。
具体实施方式
24.下面结合附图和实施例,对本发明的具体实施方式作进一步详细描述。以下实施例用于说明本发明,但不用来限制本发明的范围。
25.在本发明的描述中,需要说明的是,本描述中指示的方位或位置关系为基于附图所示的方位或位置关系,仅是为了便于描述本发明和简化描述,而不是指示或暗示所指的装置或元件必须具有特定的方位、以特定的方位构造和操作,因此不能理解为对本发明的限制。
26.请参图1-2,本发明提供一种软包电芯二次封装装置及封装方法,包括底座10、设于底座10上的主腔体20和上盖30、以及设于主腔体20上的抽真空装置60,主腔体20的内部安装有旋转平台40以及设于旋转平台40上的热压封装装置50,热压封装装置50包括封装装置51(参见图4)和刺破装置52(参见图4),旋转平台40在软包电芯二次封装的过程中转动,使软包电芯内的电解液在离心力作用下向外运动。
27.具体的,参见图2,底座10包括水平部11、与水平部11连接的垂直部12、安装在垂直部12上且与之平行的传送导轨13以及皮带14,皮带14安装在所述水平部11内腔中且与之平行。主腔体20安装在底座的水平部11上,主腔体20的端口部设有密封圈21,上盖30安装在传送导轨13上,通过传送导轨13竖直往复升降,实现上盖30与主腔体20的闭合与开启。请参图1,抽真空装置60至少包括位于主腔体20外部的抽气管61,主腔体20与上盖30完全闭合后,通过抽真空装置60可实现腔内真空度的控制,从而实现负压抽气功能。
28.具体的,请参图2-3,旋转平台40上设有多个与热压封装装置50的安装位置相对应的条形槽41,旋转平台40的底部连接有能够带动旋转平台40转动的转动轴42,转动轴42穿过主腔体20安装在底座10的水平部11上。底座10远离主腔体20的一侧还安装有驱动装置70,驱动装置70包括电动机、变速器和联轴器,且通过皮带14与旋转平台转动轴42相连,实现旋转平台40的可变速旋转。
29.需要说明的是,每个条形槽41对应一个热压封装装置50,用于进行一个工位的生产,实际上,可以根据生产需求调整旋转平台40上安装的热压封装装置50的数量,实现多工位同时操作。在本实施例的图3中只展示了一个热压封装装置50的结构示意图。
30.进一步地,请参图4及图5,热压封装装置50至少包括封装装置51、刺破装置52以及
电芯夹具53。
31.具体地,请继续再参图4,封装装置51至少包括位于旋转平台40上方的第一驱动部511以及位于旋转平台40下方的第二驱动部512,第一驱动部511至少包括第一固定柱5111、第一支撑板5112、第一导杆5113、第一封装板5114、第一螺纹杆5115、第一电机安装板5118、第一电机5116、以及上封头5117,第一固定柱5111的两端分别与旋转平台40和第一支撑板5112固定连接,将第一驱动部511安装在旋转平台40的上方,第一导杆5113穿过第一支撑板5112,其两端分别与第一封装板5114和第一电机安装板5118固定连接,上封头5117位于第一封装板5114上,自第一封装板5114的外侧向靠近旋转平台40的方向延伸,第一电机5116位于第一电机安装板5118上,与第一螺纹杆5115的一端连接,第一螺纹杆穿过第一电机安装板5118和第一支撑板5112,且与第一支撑杆5112螺纹配合,使第一电机安装板5118和第一封装板5114在第一电机5116驱动第一螺纹杆5115转动时能够沿垂直方向上下运动,带动第一封装板5114上的刺破装置52和上封头5117上下运动。
32.同样的,第二驱动部512至少包括第二固定柱5121、第二支撑板5122、第二导杆5123、第二封装板5124、第二螺纹杆5125、第二电机安装板5218、第二电机5126、以及下封头5127,第二固定柱5121、第二支撑板5122、第二导杆5123、第二封装板5124、第二螺纹杆5125、第二电机安装板5218、第二电机5126、以及下封头5127的结构和工作原理与第一驱动部511中对应元件的结构和工作原理相同。
33.上封头5117及下封头5127均连接有加热源,通过内置电源提供能量。第一封装板5114和第二封装板5124通过电机的驱动沿竖直方向移动,带动上封头5117和下封头5127穿过条形槽41压紧闭合,为软包电芯提供压紧力。
34.具体地,请再参图5,刺破装置52位于第一封装板5114的下方,至少包括多个排成一列的刺刀521,刺刀521固定至第一封装板5114上,随着第一封装板5114的上下运动而上下运动。刺刀521在向下运动的过程中可以将软包电芯的气袋刺破,便于将其内部废气的排出。
35.请再参图5,电芯夹具53位于旋转平台40之上,其尺寸与目标电芯的尺寸相配合,至少包括滑杆531、用于压紧固定电芯的第一夹板532以及第二夹板533,滑杆531穿过第一夹板532和第二夹板533固定在旋转平台40上,第二夹板533固定在旋转平台40上,且第二夹板533上设有与条形槽41位置及大小均相对应的槽,便于上封头5117和下封头5127的闭合,第一夹板532可以在滑动驱动装置(图5中未显示)的驱动下沿滑杆531上下滑动,与第二夹板533配合,将软包电芯夹紧。第二夹板533上还设有与刺刀521相对应的刀槽5331。
36.需要说明的是,本发明中的电芯夹具53不限于本实施例中所描述的电芯夹具53,凡是具有夹紧软包电芯功能的夹具装置均可以替代本实施例中所述描述的电芯夹具53,关于现有技术中的夹具装置的结构在本发明中不再赘述。
37.进一步地,旋转平台40旋转时,封装装置51、刺破装置52、电芯夹具53及放置在电芯夹具53上的软包电芯随旋转平台40旋转,处于相对静止的状态,软包电芯里的电解液向电芯底部方向,也就是电芯夹具53的外侧移动,与负压抽气的方向相反,避免了电解液的外溅。
38.本发明还提供了一种应用上述的软包电芯二次封装装置的封装方法,包括以下步骤:首先将软包电芯放置于电芯夹具53的第一夹板532和第二夹板533上,令第一夹板532沿
着滑杆531滑动,将软包电芯压紧固定;接着,上盖30沿传送导轨13下降并与主腔体20闭合;旋转平台40在驱动装置70的带动下开始旋转并达到目标转速;随后抽真空装置60启动,将主腔体20内的空气抽走,使腔内真空度达到设定值后维持旋转平台40转速不变,随后第一封装板5114和第二封装板5124在对应电机的驱动下带动刺刀521运动,刺破电芯气袋,此时,由于电芯内部的气压大于主腔体20的内部气压,于是电芯内部废气便被排出,排出完全后(一定时间后)利用对应的电机驱动上封头5117和下封头5127运动,直至上封头5117和下封头5127贴合,热封完成。热封后,抽真空装置60继续运作,将热封后进入主腔体20内部的气体抽掉,同时旋转平台40开始减速。当主腔体20内部的真空度为0pa且旋转平台40的转速为0转/min后,上盖30沿传送导轨13上升与主腔体20分离,取出完成二次封装的软包电芯,软包电芯负压二次封装至此完成。
39.经过上面的叙述可以知道,本发明提供的软包电芯二次封装装置及封装方法,通过上盖和主腔体形成密闭负压内腔,通过抽真空装置实现腔内真空度的控制,降低了生产调试的复杂性;通过驱动装置带动旋转平台及软包电芯进行离心运动,使电芯内部的电解液向电芯底部方向移动,与负压抽气的方向相反,避免了常规软包二次封装装置和方法导致的电解液从刺破口被吸出并飞溅的问题,避免了铝塑膜、刺刀和封头等设备部件的腐蚀。可有效提高电解液的保持量,减少电解液的损失,提高电芯品质。在刺破装置和封装装置的共同作用下可快速实现软包电芯的二次封装,且本发明中的热压封装装置可根据需要调整数量,实现多工位同时操作,提高了软包电芯的生产效率。
40.以上所述,仅为本发明的具体实施方式,但本发明的保护范围并不局限于此,任何熟悉本技术领域的技术人员在本发明揭露的技术范围内,可轻易想到变化或替换,都应涵盖在本发明的保护范围之内。因此,本发明的保护范围应以所述权利要求的保护范围为准。