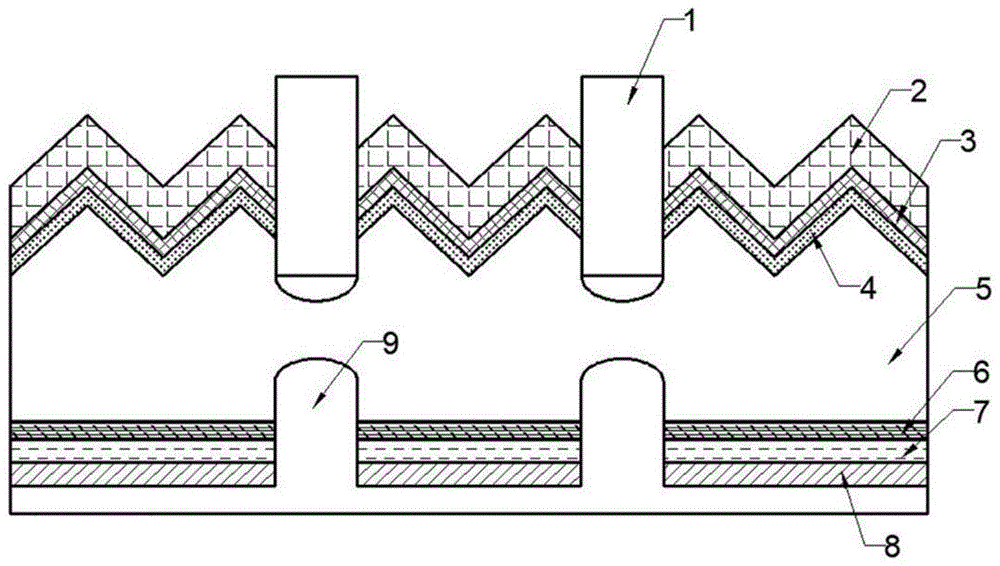
本发明属于光伏电池
技术领域:
,涉及一种perc电池背钝化结构、perc电池及制备方法。
背景技术:
:perc电池即钝化发射极和背面电池技术,起源于上世纪80年代,通过在常规电池的背面叠加钝化层,可以提高转化效率。perc电池一般的工艺流程有以下步骤:制绒→扩散→se激光→氧化→刻蚀(去psg)→退火→背膜→正膜→激光开槽→丝网印刷→烧结→光注入或电注入→测试分拣。其中镀膜工艺是perc电池产线工艺中及其重要的一环。电池片在生产过程中,需要在正面镀一层减反膜,降低光的反射,增强光的吸收。在背面镀一层钝化膜,一般钝化膜是通过钝化硅表面的悬挂键来降低表面的复合速率从而起到表面钝化或者体钝化的作用。同时其高折射率可以增强背面的反射率进一步提升电池效率,可以说钝化膜的好坏直接影响到太阳能电池的性能。二氧化硅是一种很好的钝化材料,产业化的sio2薄膜生长方式主要是热氧化法,将硅片放入高温的石英炉管内,硅片表面在氧化物质作用下生长sio2膜,根据氧化气氛的不同,又可以多采用热氧化分为干氧氧化、水汽氧化和湿氧氧化。该氧化层能够有效降低界面态缺陷密度。si-sio2界面起主导作用的是饱和悬挂键的化学钝化效果,在si-sio2界面带有一定的固定正电荷,电荷密度量级在1010cm-2,其电荷量同退火处理条件相关,相较于alox的固定负电荷(1012cm-2)可以忽略不计,即siox钝化膜所带的正电荷基本不会影响alox的场钝化效应,不过热氧化生长的一个缺陷生长速度比较慢,且厚度长不了太厚。cn105470349a公开一种perc太阳能电池及其制备方法,其中perc太阳能电池包括硅片、位于硅片上表面的二氧化硅层和银层、位于二氧化硅层上表面的正面氮化硅钝化层、位于硅片下表面的氧化铝钝化层、位于氧化铝钝化层下表面的背面氮化硅钝化层,在背面氮化硅钝化层上间隔开设有若干个开孔,在开孔中填充有腐蚀掉氧化铝钝化层后与硅片形成铝硅合金的铝层。本发明在背面氮化硅钝化层上通过激光开孔方式开孔,孔的深度控制在打穿背面氮化硅钝化层而不打穿氧化铝钝化层,然后印刷铝浆,通过烧结工艺,铝浆腐蚀掉氧化铝钝化层后与硅片形成铝硅合金。cn209515679u公开了一种perc电池结构,包括:衬底、正面二氧化硅层、抗反射层、正面氮化硅层、背面钝化层,以及保护结构;所述正面二氧化硅层设于所述衬底的正面,所述抗反射层设于所述正面二氧化硅层的与所述衬底相背的一侧,所述正面氮化硅层设于所述抗反射层的与所述正面二氧化硅层相背的一侧。cn110854240a公开了一种perc电池及其制备方法,制备方法包括制绒、扩散、刻蚀、背面抛光、退火、背面镀膜及正面镀膜。背面镀膜步骤包括:向装有退火后的硅片的设备中通入臭氧气体进行氧化处理,使硅片的背面形成背面二氧化硅层。然后在同一设备中继续通入臭氧作为氧源,并加入铝源,在背面二氧化硅层上沉积背面氧化铝层。在背面氧化铝层上沉积背面氮化硅层。目前,常用的二氧化硅层的沉积方法为等离子体增强化学气相沉积法(pecvd),利用硅烷和笑气沉积氧化硅,pecvd生长速度较快,可沉积的氧化硅薄膜也较厚,但其结构较疏松,钝化效果较差。技术实现要素:针对现有技术存在的不足,本发明的目的在于提供一种perc电池背钝化结构、perc电池及制备方法,本发明采用晶态氧化硅替换传统的非晶态氧化硅,晶态氧化硅中的原子分布具有长程有序性,因此,相比于非晶态氧化硅层,晶态氧化硅层的致密程度更高,钝化效果更好,界面态缺陷密度可以低至1010cm-2ev-1,提升了perc电池的综合性能。为达此目的,本发明采用以下技术方案:第一方面,本发明提供了一种perc电池背钝化结构,所述的perc电池背钝化结构包括设置于硅基体背面的晶态氧化硅层。perc电池的背钝化结构中的氧化硅层多采用非晶态氧化硅,但非晶态氧化硅的硅氢键结合较弱,钝化效果较差,本发明采用晶态氧化硅替换传统的非晶态氧化硅,虽然非晶态氧化硅中的原子分布也具有一定的有序性,但只是短程有序性,而晶态氧化硅中的原子分布具有长程有序性,因此,相比于非晶态氧化硅层,晶态氧化硅层的致密程度更高,钝化效果更好,界面态缺陷密度可以低至1010cm-2ev-1,提升了perc电池的综合性能。需要说明的是,本发明要求保护的背钝化结构是perc电池中的部分结构,可以理解的是,在此限定的保护范围之内,对perc电池中的其他结构并未进行具体要求和特殊限定,换言之,在本发明限定的背钝化结构的基础上,本领域技术人员可以基于现有技术对其他结构进行常规替换或创造性改进。示例性地,本发明提供了一种perc电池的完整结构,包括硅基体,硅基体的正面依次层叠设置有发射极、正面氧化硅层和正面氮化硅层(正面氮化硅层可以替换为氮氧化硅层或碳化硅层),同时,正面还垂直插入了正面电极。硅基体的背面依次层叠设置有晶态氧化硅层、氧化铝层和背面氮化硅层(背面氮化硅层可以替换为氮氧化硅层或碳化硅层),同时,背面还垂直插入了背面电极。本领域技术人员可以对除晶态氧化硅层之外的其余各层进行创造性改进,或改进材料,或增加其他功能层,或剔除其中某层,当然,无论进行何种改进方式,只要采用了本发明提供的背钝化结构,那么改进后的perc电池同样落入本发明的保护范围和公开范围之内。作为本发明一种优选的技术方案,所述的晶态氧化硅层的厚度为1~20nm,例如可以是1nm、2nm、3nm、4nm、5nm、6nm、7nm、8nm、9nm、10nm、11nm、12nm、13nm、14nm、15nm、16nm、17nm、18nm、19nm或20nm,但并不仅限于所列举的数值,该数值范围内其他未列举的数值同样适用。作为本发明一种优选的技术方案,所述晶态氧化硅层的表面依次层叠设置有氧化铝层和背面氮化硅层。所述的氧化铝层的厚度为5~10nm,例如可以是5nm、5.5nm、6nm、6.5nm、7nm、7.5nm、8nm、8.5nm、9nm、9.5nm或10nm,但并不仅限于所列举的数值,该数值范围内其他未列举的数值同样适用。所述的背面氮化硅层的厚度为10~200nm,例如可以是10nm、20nm、30nm、40nm、50nm、60nm、70nm、80nm、90nm、100nm、110nm、120nm、130nm、140nm、150nm、160nm、170nm、180nm、190nm或200nm,但并不仅限于所列举的数值,该数值范围内其他未列举的数值同样适用。第二方面,本发明提供了一种第一方面所述的perc电池背钝化结构的制备方法,所述的制备方法包括:硅基体背面沉积形成非晶态氧化硅薄膜,经退火处理后,非晶态氧化硅薄膜转变为晶态氧化硅层。本发明首先在硅基体背面沉积形成非晶态氧化硅薄膜,但非晶态氧化硅薄膜的结构较疏松,沉积的氧化硅均是非晶态,硅氢键结合较弱,钝化效果较差。随后经过退火处理后,使得非晶态的氧化硅逐渐转变成富氢的晶态氧化硅,大大增强了钝化效果,最终得到较厚且钝化效果较好的晶态氧化硅层,界面态缺陷密度可以低至1010cm-2ev-1,提升了太阳能电池的综合性能。作为本发明一种优选的技术方案,所述的非晶态氧化硅薄膜的沉积过程具体包括:将硅基体放入成膜腔室内,向成膜腔室内通入笑气和硅烷,维持成膜腔室内的压力,采用等离子体增强化学气相沉积法在硅基体背面沉积形成非晶态氧化硅薄膜。本发明将pecvd和热氧化法加以结合制备得到了单晶perc电池的背钝化结构,首先,通过pecvd的方式,利用硅烷和笑气在等离子体的辅助下沉积形成氧化硅层,相较于热氧化,采用pecvd法沉积氧化硅层的生长速度较快,可沉积的氧化硅层也较厚,但相应地,氧化硅层结构较疏松,沉积的氧化硅均是非晶态,硅氢键结合较弱,钝化效果劣于热氧化法形成的氧化硅层。在次基础上,本发明通过热氧化法,使得非晶态的氧化硅逐渐转变成晶态氧化硅,大大增强了钝化效果,最终得到较厚且钝化效果较好的晶态氧化硅层,界面态缺陷密度可以低至1010cm-2ev-1,提升了太阳能电池的综合性能。作为本发明一种优选的技术方案,所述笑气的通入流量为4000~6000sccm,例如可以是4000sccm、4200sccm、4400sccm、4600sccm、4800sccm、5000sccm、5200sccm、5400sccm、5600sccm、5800sccm或6000sccm,但并不仅限于所列举的数值,该数值范围内其他未列举的数值同样适用。所述硅烷的通入流量为500~800sccm,例如可以是500sccm、520sccm、540sccm、560sccm、580sccm、600sccm、620sccm、640sccm、660sccm、680sccm、700sccm、720sccm、740sccm、760sccm、780sccm或800sccm,但并不仅限于所列举的数值,该数值范围内其他未列举的数值同样适用。所述成膜腔室内的压力维持在1400~1600pa,例如可以是1400pa、1420pa、1440pa、1460pa、1480pa、1500pa、1520pa、1540pa、1560pa、1580pa或1600pa,但并不仅限于所列举的数值,该数值范围内其他未列举的数值同样适用。所述等离子体的射频功率为6000~10000w,例如可以是6000w、6500w、7000w、7500w、8000w、8500w、9000w、9500w或10000w,但并不仅限于所列举的数值,该数值范围内其他未列举的数值同样适用。所述的沉积时间为10~300s,例如可以是10s、50s、100s、150s、200s、250s或300s,但并不仅限于所列举的数值,该数值范围内其他未列举的数值同样适用。作为本发明一种优选的技术方案,所述的退火过程在富氢气氛下进行。所述的富氢气氛为包括氢气的混合气体,所述氢气占混合气体总体积的40~80%,例如可以是40%、45%、50%、55%、60%、65%、70%、75%或80%,但并不仅限于所列举的数值,该数值范围内其他未列举的数值同样适用。在本发明中,由于si和sio2的界面处会存在较多硅原子的悬挂键(即未与氧原子结合的价键),悬挂键的存在会影响界面态缺陷密度,从而降低二氧化硅层的钝化效果。因此,本发明在富氢气氛下进行退火处理,使得氢原子进入到界面中并与悬挂键形成si-h键,以减小界面处存在的悬挂键,减小si/sio2界面态密度,提高二氧化硅层的钝化效果。所述的混合气体中还包括氮气和/或惰性气体。作为本发明一种优选的技术方案,所述的退火温度为850~1300℃,例如可以是850℃、900℃、950℃、1000℃、1050℃、1100℃、1150℃、1200℃、1250℃或1300℃,但并不仅限于所列举的数值,该数值范围内其他未列举的数值同样适用。本发明特别限定了退火温度为850~1300℃,当退火温度低于850℃时,导致温度达不到sio2的晶化温度,当退火温度高于1300℃时,导致能耗变大,对硅片的热损伤程度也加大。所述的退火时间为1~20min,例如可以是1min、2min、3min、4min、5min、6min、7min、8min、9min、10min、11min、12min、13min、14min、15min、16min、17min、18min、19min或20min,但并不仅限于所列举的数值,该数值范围内其他未列举的数值同样适用。作为本发明一种优选的技术方案,所述的制备方法还包括:在晶态氧化硅层表面依次沉积形成氧化铝层和背面氮化硅层。第三方面,一种包括第一方面所述的perc电池背钝化结构的perc电池,所述的perc电池包括硅基体,所述的perc电池包括硅基体,所述硅基体的正面依次层叠设置有发射极、正面氧化硅层和正面氮化硅层,所述硅基体的背面设置有第一方面所述的背钝化结构。所述的perc电池还包括正面电极和背面电极,所述的正面电极由perc电池的正面垂直插入至硅基体内,所述的背面电极由perc电池的背面垂直插入至硅基体内。需要说明的是,本发明特别限定了晶态氧化硅层的制备方法为pecvd和热氧化法,但对于perc电池中其他层结构的制备方法并未作出具体要求和特殊限定。示例性地,本发明提供了如下制备方法供本领域技术人员参考,但不作为对本发明保护范围的限定:(1)对单晶硅基体的表面进行制绒处理,形成绒面,制绒后对单晶硅基体进行清洗;(2)对清洗好的硅基体进行磷扩散,表面生成磷硅玻璃,采用激光掺杂在硅基体正面形成局部重掺区,得到选择性发射极;(3)通过hf水溶液刻蚀去除硅基体其余表面的磷硅玻璃;(4)采用热氧化法在选择性发射极表面沉积形成正面氧化硅层;(5)将硅基体放入成膜腔室内,向成膜腔室内通入笑气和硅烷,采用等离子体增强化学气相沉积法在硅基体背面沉积形成非晶态氧化硅薄膜;(6)随后在富氢气氛下对硅基体进行退火处理,富氢气氛为氮气和/或惰性气体的混合气体,退火完成后,非晶态氧化硅薄膜转变为晶态氧化硅层;(7)采用ald在晶态氧化硅表面沉积形成氧化铝层;(8)采用pecvd在氧化铝层表面沉积形成背面氮化硅层;(9)采用pecvd在正面氧化硅层表面沉积形成正面氮化硅层;(10)通过丝网印刷和烧结在硅片的正面和背面分别形成正面电极和背面电极。与现有技术相比,本发明的有益效果为:perc电池的背钝化结构中的氧化硅层多采用非晶态氧化硅,但非晶态氧化硅的硅氢键结合较弱,钝化效果较差,本发明采用晶态氧化硅替换传统的非晶态氧化硅,虽然非晶态氧化硅中的原子分布也具有一定的有序性,但只是短程有序性,而晶态氧化硅中的原子分布具有长程有序性,因此,相比于非晶态氧化硅层,晶态氧化硅层的致密程度更高,钝化效果更好,界面态缺陷密度可以低至1010cm-2ev-1,提升了perc电池的综合性能。附图说明图1为本发明一个具体实施方式提供的perc电池的结构示意图。其中,1-正面电极;2-正面氮化硅层;3-正面氧化硅层;4-发射极;5-硅基体;6-晶态氧化硅层;7-氧化铝层;8-背面氮化硅层;9-背面电极。具体实施方式下面结合附图并通过具体实施方式来进一步说明本发明的技术方案。实施例1本实施例提供了一种perc电池的制备方法,所述的制备方法包括如下步骤:(1)采用naoh、水和乙醇的混合溶液在70℃下对单晶硅基体5的表面进行制绒处理,形成绒面,naoh、水和乙醇的体积比为8:240:3;制绒后对单晶硅基体5进行清洗;(2)对清洗好的硅基体5进行磷扩散,表面生成磷硅玻璃,采用激光掺杂在硅基体5正面形成局部重掺区,得到选择性发射极4;(3)通过hf水溶液刻蚀去除硅基体5其余表面的磷硅玻璃,hf水溶液中的水和hf的体积比为35:3;(4)采用热氧化法在选择性发射极4表面沉积形成正面氧化硅层3,其中,氧气流量为1000sccm,沉积压力为100pa,热氧化温度为600℃,沉积时间为10min;(5)将硅基体5放入成膜腔室内,向成膜腔室内通入笑气和硅烷,笑气的通入流量为4000sccm,硅烷的通入流量为500sccm;成膜腔室内的压力维持在1400pa,采用等离子体增强化学气相沉积法在硅基体5背面沉积形成非晶态氧化硅薄膜,等离子体的射频功率为6000w,沉积时间为10s;(6)随后在富氢气氛下对硅基体5进行退火处理,富氢气氛为氢气和氮气的混合气体,氢气占混合气体总体积的40%,退火温度为850℃,退火时间为1min,退火完成后,非晶态氧化硅薄膜转变为晶态氧化硅层6;(7)采用ald在晶态氧化硅表面沉积形成氧化铝层7,氧化铝层7的沉积工艺参数为:射频功率450w,沉积温度350℃,沉积压力10pa,tma流量300sccm,氧气流量400sccm,氮气流量350sccm,沉积时间8s;(8)采用pecvd在氧化铝层7表面沉积形成背面氮化硅层8,氮化硅的沉积工艺参数为:沉积射频功率9000w,沉积温度450℃,沉积压力300pa,氨气流量6250sccm,硅烷流量680sccm,沉积时间800s;(9)采用pecvd在正面氧化硅层3表面沉积形成正面氮化硅层2,氮化硅的沉积工艺参数为:沉积射频功率9000w,沉积温度450℃,沉积压力300pa,氨气流量6250sccm,硅烷流量680sccm,沉积时间800s;(10)通过丝网印刷和烧结在硅片的正面和背面分别形成正面电极1和背面电极9。最终制备得到的perc电池如图1所示,包括硅基体5,硅基体5的正面依次层叠设置有发射极4、正面氧化硅层3和正面氮化硅层2,正面氧化硅层3的厚度为1nm,正面氮化硅层2的厚度为15nm,正面还设置有正面电极1。硅基体5的背面依次层叠设置有晶态氧化硅层6、氧化铝层7和背面氮化硅层8,晶态氧化硅层6的厚度为5nm,氧化铝层7的厚度为5nm,背面氮化硅层8的厚度为15nm,背面还设置有背面电极9。实施例2本实施例提供了一种perc电池的制备方法,所述的制备方法包括如下步骤:(1)采用koh、水和异丙醇的混合溶液在75℃下对单晶硅基体5的表面进行制绒处理,形成绒面,koh、水和异丙醇的体积比为10:280:2.5;制绒后对单晶硅基体5进行清洗;(2)对清洗好的硅基体5进行磷扩散,表面生成磷硅玻璃,采用激光掺杂在硅基体5正面形成局部重掺区,得到选择性发射极4;(3)通过hf水溶液刻蚀去除硅基体5其余表面的磷硅玻璃,hf水溶液中的水和hf的体积比为37:3;(4)采用热氧化法在选择性发射极4表面沉积形成正面氧化硅层3,其中,氧气流量为1200sccm,沉积压力为140pa,热氧化温度为620℃,沉积时间为15min;(5)将硅基体5放入成膜腔室内,向成膜腔室内通入笑气和硅烷,笑气的通入流量为4500sccm,硅烷的通入流量为560sccm;成膜腔室内的压力维持在1450pa,采用等离子体增强化学气相沉积法在硅基体5背面沉积形成非晶态氧化硅薄膜,等离子体的射频功率为6800w,沉积时间为50s;(6)随后在富氢气氛下对硅基体5进行退火处理,富氢气氛为氮气和氩气的混合气体,氢气占混合气体总体积的50%,退火温度为950℃,退火时间为3min,退火完成后,非晶态氧化硅薄膜转变为晶态氧化硅层6;(7)采用ald在晶态氧化硅表面沉积形成氧化铝层7,氧化铝层7的沉积工艺参数为:射频功率450w,沉积温度370℃,沉积压力10.4pa,tma流量320sccm,氧气流量420sccm,氮气流量360sccm,沉积时间8.5s;(8)采用pecvd在氧化铝层7表面沉积形成背面氮化硅层8,氮化硅的沉积工艺参数为:沉积射频功率9000w,沉积温度456℃,沉积压力250pa,氨气流量6250sccm,硅烷流量680sccm,沉积时间830s;(9)采用pecvd在正面氧化硅层3表面沉积形成氮化硅层,氮化硅的沉积工艺参数为:沉积射频功率9000w,沉积温度456℃,沉积压力250pa,氨气流量6250sccm,硅烷流量680sccm,沉积时间830s;(10)通过丝网印刷和烧结在硅片的正面和背面分别形成正面电极1和背面电极9。最终制备得到的perc电池包括硅基体5,硅基体5的正面依次层叠设置有发射极4、正面氧化硅层3和正面氮化硅层2,正面氧化硅层3的厚度为3nm,正面氮化硅层2的厚度为50nm,正面还设置有正面电极1。硅基体5的背面依次层叠设置有晶态氧化硅层6、氧化铝层7和背面氮化硅层8,晶态氧化硅层6的厚度为10nm,氧化铝层7的厚度为8nm,氮化硅层的厚度为50nm,背面还设置有背面电极9。实施例3本实施例提供了一种perc电池的制备方法,所述的制备方法包括如下步骤:(1)采用naoh、水和乙醇的混合溶液在80℃下对单晶硅基体5的表面进行制绒处理,形成绒面,naoh、水和乙醇的体积比为10:330:2.2;制绒后对单晶硅基体5进行清洗;(2)对清洗好的硅基体5进行磷扩散,表面生成磷硅玻璃,采用激光掺杂在硅基体5正面形成局部重掺区,得到选择性发射极4;(3)通过hf水溶液刻蚀去除硅基体5其余表面的磷硅玻璃,hf水溶液中的水和hf的体积比为40:3;(4)采用热氧化法在选择性发射极4表面沉积形成正面氧化硅层3,其中,氧气流量为1400sccm,沉积压力为180pa,热氧化温度为640℃,沉积时间为20min;(5)将硅基体5放入成膜腔室内,向成膜腔室内通入笑气和硅烷,笑气的通入流量为5000sccm,硅烷的通入流量为620sccm;成膜腔室内的压力维持在1500pa,采用等离子体增强化学气相沉积法在硅基体5背面沉积形成非晶态氧化硅薄膜,等离子体的射频功率为7600w,沉积时间为100s;(6)随后在富氢气氛下对硅基体5进行退火处理,富氢气氛为氮气和氦气的混合气体,氢气占混合气体总体积的60%,退火温度为1050℃,退火时间为5min,退火完成后,非晶态氧化硅薄膜转变为晶态氧化硅层6;(7)采用ald在晶态氧化硅表面沉积形成氧化铝层7,氧化铝层7的沉积工艺参数为:射频功率450w,沉积温度400℃,沉积压力10.8pa,tma流量340sccm,氧气流量440sccm,氮气流量370sccm,沉积时间9s;(8)采用pecvd在氧化铝层7表面沉积形成背面氮化硅层8,氮化硅的沉积工艺参数为:沉积射频功率9000w,沉积温度462℃,沉积压力280pa,氨气流量6250sccm,硅烷流量680sccm,沉积时间860s;(9)采用pecvd在正面氧化硅层3表面沉积形成氮化硅层,氮化硅的沉积工艺参数为:沉积射频功率9000w,沉积温度462℃,沉积压力280pa,氨气流量6250sccm,硅烷流量680sccm,沉积时间860s;(10)通过丝网印刷和烧结在硅片的正面和背面分别形成正面电极1和背面电极9。最终制备得到的perc电池包括硅基体5,硅基体5的正面依次层叠设置有发射极4、正面氧化硅层3和正面氮化硅层2,正面氧化硅层3的厚度为2nm,正面氮化硅层2的厚度为80nm,正面还设置有正面电极1。硅基体5的背面依次层叠设置有晶态氧化硅层6、氧化铝层7和背面氮化硅层8,晶态氧化硅层6的厚度为15nm,氧化铝层7的厚度为8nm,氮化硅层的厚度为80nm,背面还设置有背面电极9。实施例4本实施例提供了一种perc电池的制备方法,所述的制备方法包括如下步骤:(1)采用koh、水和异丙醇的混合溶液在82℃下对单晶硅基体5的表面进行制绒处理,形成绒面,koh、水和异丙醇的体积比为11:330:2.5;制绒后对单晶硅基体5进行清洗;(2)对清洗好的硅基体5进行磷扩散,表面生成磷硅玻璃,采用激光掺杂在硅基体5正面形成局部重掺区,得到选择性发射极4;(3)通过hf水溶液刻蚀去除硅基体5其余表面的磷硅玻璃,hf水溶液中的水和hf的体积比为42:3;(4)采用热氧化法在选择性发射极4表面沉积形成正面氧化硅层3,其中,氧气流量为1600sccm,沉积压力为220pa,热氧化温度为660℃,沉积时间为22min;(5)将硅基体5放入成膜腔室内,向成膜腔室内通入笑气和硅烷,笑气的通入流量为5300sccm,硅烷的通入流量为680sccm;成膜腔室内的压力维持在1530pa,采用等离子体增强化学气相沉积法在硅基体5背面沉积形成非晶态氧化硅薄膜,等离子体的射频功率8400w,沉积时间为150s;(6)随后在富氢气氛下对硅基体5进行退火处理,富氢气氛为氮气和氮气的混合气体,氢气占混合气体总体积的65%,退火温度为1150℃,退火时间为10min,退火完成后,非晶态氧化硅薄膜转变为晶态氧化硅层6;(7)采用ald在晶态氧化硅表面沉积形成氧化铝层7,氧化铝层7的沉积工艺参数为:射频功率450w,沉积温度420℃,沉积压力11.2pa,tma流量360sccm,氧气流量460sccm,氮气流量380sccm,沉积时间9.3s;(8)采用pecvd在氧化铝层7表面沉积形成背面氮化硅层8,氮化硅的沉积工艺参数为:沉积射频功率9000w,沉积温度468℃,沉积压力250pa,氨气流量6250sccm,硅烷流量680sccm,沉积时间890s;(9)采用pecvd在正面氧化硅层3表面沉积形成氮化硅层,氮化硅的沉积工艺参数为:沉积射频功率9000w,沉积温度468℃,沉积压力250pa,氨气流量6250sccm,硅烷流量680sccm,沉积时间890s;(10)通过丝网印刷和烧结在硅片的正面和背面分别形成正面电极1和背面电极9。最终制备得到的perc电池包括硅基体5,硅基体5的正面依次层叠设置有发射极4、正面氧化硅层3和正面氮化硅层2,正面氧化硅层3的厚度为4nm,正面氮化硅层2的厚度为100nm,正面还设置有正面电极1。硅基体5的背面依次层叠设置有晶态氧化硅层6、氧化铝层7和背面氮化硅层8,晶态氧化硅层6的厚度为16nm,氧化铝层7的厚度为8nm,背面氮化硅层8的厚度为100nm,背面还设置有背面电极9。实施例5本实施例提供了一种perc电池的制备方法,所述的制备方法包括如下步骤:(1)采用naoh、水和乙醇的混合溶液在88℃下对单晶硅基体5的表面进行制绒处理,形成绒面,naoh、水和乙醇的体积比为11.5:350:2.5;制绒后对单晶硅基体5进行清洗;(2)对清洗好的硅基体5进行磷扩散,表面生成磷硅玻璃,采用激光掺杂在硅基体5正面形成局部重掺区,得到选择性发射极4;(3)通过hf水溶液刻蚀去除硅基体5其余表面的磷硅玻璃,hf水溶液中的水和hf的体积比为43:3;(4)采用热氧化法在选择性发射极4表面沉积形成正面氧化硅层3,其中,氧气流量为1800sccm,沉积压力为260pa,热氧化温度为680℃,沉积时间为26min;(5)将硅基体5放入成膜腔室内,向成膜腔室内通入笑气和硅烷,笑气的通入流量为5600sccm,硅烷的通入流量为720sccm;成膜腔室内的压力维持在1560pa,采用等离子体增强化学气相沉积法在硅基体5背面沉积形成非晶态氧化硅薄膜,等离子体的射频功率为9200w,沉积时间为200s;(6)随后在富氢气氛下对硅基体5进行退火处理,富氢气氛为氮气和氩气的混合气体,氢气占混合气体总体积的70%,退火温度为1250℃,退火时间为15min,退火完成后,非晶态氧化硅薄膜转变为晶态氧化硅层6;(7)采用ald在晶态氧化硅表面沉积形成氧化铝层7,氧化铝层7的沉积工艺参数为:射频功率450w,沉积温度440℃,沉积压力11.6pa,tma流量380sccm,氧气流量480sccm,氮气流量390sccm,沉积时间9.6s;(8)采用pecvd在氧化铝层7表面沉积形成背面氮化硅层8,氮化硅的沉积工艺参数为:沉积射频功率9000w,沉积温度475℃,沉积压力300pa,氨气流量6250sccm,硅烷流量680sccm,沉积时间920s;(9)采用pecvd在正面氧化硅层3表面沉积形成氮化硅层,氮化硅的沉积工艺参数为:沉积射频功率9000w,沉积温度475℃,沉积压力300pa,氨气流量6250sccm,硅烷流量680sccm,沉积时间920s;(10)通过丝网印刷和烧结在硅片的正面和背面分别形成正面电极1和背面电极9。最终制备得到的perc电池包括硅基体5,硅基体5的正面依次层叠设置有发射极4、正面氧化硅层3和正面氮化硅层2,正面氧化硅层3的厚度为3nm,正面氮化硅层2的厚度为150nm,正面还设置有正面电极1。硅基体5的背面依次层叠设置有晶态氧化硅层6、氧化铝层7和背面氮化硅层8,晶态氧化硅层6的厚度为18nm,氧化铝层7的厚度为10nm,背面氮化硅层8的厚度为18nm,背面还设置有背面电极9。实施例6本实施例提供了一种perc电池的制备方法,所述的制备方法包括如下步骤:(1)采用koh、水和异丙醇的混合溶液在90℃下对单晶硅基体5的表面进行制绒处理,形成绒面,koh、水和异丙醇的体积比为12:360:3;制绒后对单晶硅基体5进行清洗;(2)对清洗好的硅基体5进行磷扩散,表面生成磷硅玻璃,采用激光掺杂在硅基体5正面形成局部重掺区,得到选择性发射极4;(3)通过hf水溶液刻蚀去除硅基体5其余表面的磷硅玻璃,hf水溶液中的水和hf的体积比为45:3;(4)采用热氧化法在选择性发射极4表面沉积形成正面氧化硅层3,其中,氧气流量为2000sccm,沉积压力为300pa,热氧化温度为700℃,沉积时间为30min;(5)将硅基体5放入成膜腔室内,向成膜腔室内通入笑气和硅烷,笑气的通入流量为6000sccm,硅烷的通入流量为800sccm;成膜腔室内的压力维持在1600pa,采用等离子体增强化学气相沉积法在硅基体5背面沉积形成非晶态氧化硅薄膜,等离子体的射频功率为10000w,沉积时间为300s;(6)随后在富氢气氛下对硅基体5进行退火处理,富氢气氛为氮气和氦气的混合气体,氢气占混合气体总体积的80%,退火温度为1300℃,退火时间为20min,退火完成后,非晶态氧化硅薄膜转变为晶态氧化硅层6;(7)采用ald在晶态氧化硅表面沉积形成氧化铝层7,氧化铝层7的沉积工艺参数为:射频功率450w,沉积温度450℃,沉积压力12pa,tma流量400sccm,氧气流量500sccm,氮气流量400sccm,沉积时间10s;(8)采用pecvd在氧化铝层7表面沉积形成背面氮化硅层8,氮化硅的沉积工艺参数为:沉积射频功率9000w,沉积温度480℃,沉积压力200pa,氨气流量6250sccm,硅烷流量680sccm,沉积时间950s;(9)采用pecvd在正面氧化硅层3表面沉积形成氮化硅层,氮化硅的沉积工艺参数为:沉积射频功率9000w,沉积温度480℃,沉积压力200pa,氨气流量6250sccm,硅烷流量680sccm,沉积时间950s;(10)通过丝网印刷和烧结在硅片的正面和背面分别形成正面电极1和背面电极9。最终制备得到的perc电池包括硅基体5,硅基体5的正面依次层叠设置有发射极4、正面氧化硅层3和正面氮化硅层2,正面氧化硅层3的厚度为5nm,正面氮化硅层2的厚度为200nm,正面还设置有正面电极1。硅基体5的背面依次层叠设置有晶态氧化硅层6、氧化铝层7和背面氮化硅层8,晶态氧化硅层6的厚度为20nm,氧化铝层7的厚度为10nm,背面氮化硅层8的厚度为200nm,背面还设置有背面电极9。实施例7本实施例提供了一种perc电池的制备方法,与实施例3的区别在于,步骤(6)中的退火温度调整为800℃,其他工艺参数及操作步骤与实施例3完全相同。实施例8本实施例提供了一种perc电池的制备方法,与实施例3的区别在于,步骤(6)中的退火温度调整为1400℃,其他工艺参数及操作步骤与实施例3完全相同。对比例1本实施例提供了一种perc电池的制备方法,所述的制备方法包括如下步骤:(1)采用naoh、水和乙醇的混合溶液在80℃下对单晶硅基体5的表面进行制绒处理,形成绒面,naoh、水和乙醇的体积比为10:330:2.2;制绒后对单晶硅基体5进行清洗;(2)对清洗好的硅基体5进行磷扩散,表面生成磷硅玻璃,采用激光掺杂在硅基体5正面形成局部重掺区,得到选择性发射极4;(3)通过hf水溶液刻蚀去除硅基体5其余表面的磷硅玻璃,hf水溶液中的水和hf的体积比为40:3;(4)采用热氧化法在选择性发射极4表面沉积形成正面氧化硅层3,其中,氧气流量为1400sccm,沉积压力为180pa,热氧化温度为640℃,沉积时间为20min;(5)采用热氧化法在硅基体5背面沉积形成晶态氧化硅层6,其中,氧气流量为1400sccm,沉积压力为180pa,热氧化温度为640℃,沉积时间为20min;(6)采用ald在晶态氧化硅表面沉积形成氧化铝层7,氧化铝层7的沉积工艺参数为:射频功率450w,沉积温度400℃,沉积压力10.8pa,tma流量340sccm,氧气流量440sccm,氮气流量370sccm,沉积时间9s;(7)采用pecvd在氧化铝层7表面沉积形成背面氮化硅层8,氮化硅的沉积工艺参数为:沉积射频功率9000w,沉积温度462℃,沉积压力280pa,氨气流量6250sccm,硅烷流量680sccm,沉积时间860s;(8)采用pecvd在正面氧化硅层3表面沉积形成氮化硅层,氮化硅的沉积工艺参数为:沉积射频功率9000w,沉积温度462℃,沉积压力280pa,氨气流量6250sccm,硅烷流量680sccm,沉积时间860s;(9)通过丝网印刷和烧结在硅片的正面和背面分别形成正面电极1和背面电极9。最终制备得到的perc电池包括硅基体5,硅基体5的正面依次层叠设置有发射极4、正面氧化硅层3和正面氮化硅层2,正面氧化硅层3的厚度为2nm,正面氮化硅层2的厚度为80nm,正面还设置有正面电极1。硅基体5的背面依次层叠设置有背面氧化硅层、氧化铝层7和背面氮化硅层8,背面氧化硅层的厚度为2nm,氧化铝层7的厚度为8nm,氮化硅层的厚度为80nm,背面还设置有背面电极9。对比例2本实施例提供了一种perc电池的制备方法,所述的制备方法包括如下步骤:(1)采用naoh、水和乙醇的混合溶液在80℃下对单晶硅基体5的表面进行制绒处理,形成绒面,naoh、水和乙醇的体积比为10:330:2.2;制绒后对单晶硅基体5进行清洗;(2)对清洗好的硅基体5进行磷扩散,表面生成磷硅玻璃,采用激光掺杂在硅基体5正面形成局部重掺区,得到选择性发射极4;(3)通过hf水溶液刻蚀去除硅基体5其余表面的磷硅玻璃,hf水溶液中的水和hf的体积比为40:3;(4)采用热氧化法在选择性发射极4表面沉积形成正面氧化硅层3,其中,氧气流量为1400sccm,沉积压力为180pa,热氧化温度为640℃,沉积时间为20min;(5)将硅基体5放入成膜腔室内,向成膜腔室内通入笑气和硅烷,笑气的通入流量为5000sccm,硅烷的通入流量为620sccm;成膜腔室内的压力维持在1500pa,采用等离子体增强化学气相沉积法在硅基体5背面沉积形成非晶态氧化硅层,等离子体的射频功率为7600w,沉积时间为100s;(7)采用ald在非晶态氧化硅层表面沉积形成氧化铝层7,氧化铝层7的沉积工艺参数为:射频功率450w,沉积温度400℃,沉积压力10.8pa,tma流量340sccm,氧气流量440sccm,氮气流量370sccm,沉积时间9s;(8)采用pecvd在氧化铝层7表面沉积形成背面氮化硅层8,氮化硅的沉积工艺参数为:沉积射频功率9000w,沉积温度462℃,沉积压力280pa,氨气流量6250sccm,硅烷流量680sccm,沉积时间860s;(9)采用pecvd在正面氧化硅层3表面沉积形成氮化硅层,氮化硅的沉积工艺参数为:沉积射频功率9000w,沉积温度462℃,沉积压力280pa,氨气流量6250sccm,硅烷流量680sccm,沉积时间860s;(10)通过丝网印刷和烧结在硅片的正面和背面分别形成正面电极1和背面电极9。最终制备得到的perc电池包括硅基体5,硅基体5的正面依次层叠设置有发射极4、正面氧化硅层3和正面氮化硅层2,正面氧化硅层3的厚度为15nm,正面氮化硅层2的厚度为80nm,正面还设置有正面电极1。硅基体5的背面依次层叠设置有晶态氧化硅层6、氧化铝层7和背面氮化硅层8,晶态氧化硅层6的厚度为15nm,氧化铝层7的厚度为8nm,氮化硅层的厚度为80nm,背面还设置有背面电极9。分别测量实施例1~8和对比例1~2提供的perc电池的开路电压(uoc)、短路电流(isc)、填充因子(ff)、光电转化率(eta)和界面态缺陷密度(dit),其结果如表1所示。需要说明的是,硅基体与钝化层界面处的缺陷密度是衡量钝化效果的关键因素,缺陷密度越低,表明钝化效果越优秀。表1界面态缺陷密度dit(1010cm-2ev-1)实施例11.0实施例21.2实施例31.2实施例41.1实施例51.0实施例61.0实施例71.3实施例81.4对比例11.5对比例25.0表2根据实施例3、实施例7、实施例8和对比例1和对比例2并结合表1数据可以看出如下两点:(1)实施例3的界面态缺陷密度略低于对比例1,说明实施例3的钝化效果优于对比例1,这是由于对比例1仅采用了热氧化法制备氧化硅,而实施例3则是采用了pecvd和热氧化法联合制备氧化硅,虽然二者制备得到的都是晶态氧化硅,但对比例1制备得到的氧化硅层的厚度远小于实施例3(对比例1中晶态氧化硅层6的厚度为2nm,实施例3中晶态氧化硅层6的厚度为15nm),因此导致对比例1的钝化效果劣于实施例3。(2)实施例3的的界面态缺陷密度远低于对比例2,说明实施例3的钝化效果远超对比例2,这是由于实施例3采用pecvd和热氧化法联合制备得到的是晶态氧化硅,而对比例2仅采用pecvd制备得到的是非晶态氧化硅,晶态氧化硅的钝化效果优于非晶态氧化硅。(3)实施例7和实施例8的数据略小于实施例3,这是由于退火温度过高或过低均影响了制备得到的晶态氧化硅层6的钝化效果。由此也可以看出,本发明采用pecvd和热氧化法联合制备氧化硅,通过pecvd弥补了热氧化法的厚度缺陷,热氧化法弥补了pecvd的非晶态缺陷,二者结合最终得到了较厚的晶态氧化硅层6。由表2可以看出,钝化效果的提升也提高了perc电池的综合性能。申请人声明,以上所述仅为本发明的具体实施方式,但本发明的保护范围并不局限于此,所属
技术领域:
的技术人员应该明了,任何属于本
技术领域:
的技术人员在本发明揭露的技术范围内,可轻易想到的变化或替换,均落在本发明的保护范围和公开范围之内。当前第1页12