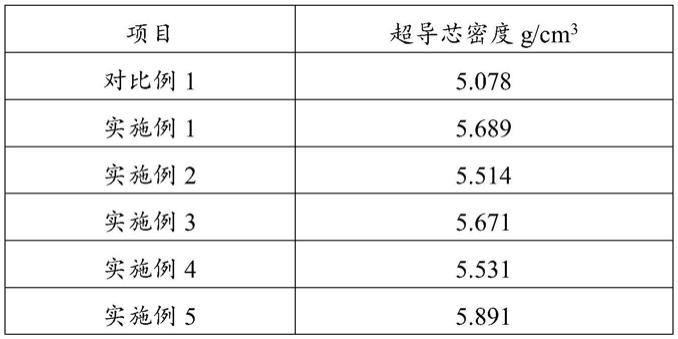
1.本发明属于铁基超导材料技术领域,尤其涉及一种11系铁基超导带材的制备方法。
背景技术:2.2008年,细野秀雄小组发现lafeaso1‑
x
f
x
具有26k的临界转变温度(t
c
),拉开了铁基超导研究的热潮。经过科学家们的不懈努力,共发现了百余种铁基超导材料。
3.铁基超导体具有高t
c
、高上临界场和低各向异性等特点,是最有发展前景的新型高温超导体之一。在众多铁基超导体中,隶属于11系的铁基超导体的fese
x
te1‑
x
(0<x≤1)不含有毒元素、不稳定元素和稀有元素,更满足实用化要求。
4.同其他铁基超导体相同,fese
x
te1‑
x
超导带材多使用先位粉末装管法制备。其主要过程是将fese
x
te1‑
x
粉末装入金属管后进行旋锻拉拔等冷变形,最后将得到的初始fese
x
te1‑
x
带材在一定温度(525~1000℃)下进行烧结(2~72h)获得超导带材。但由于fese
x
te1‑
x
成相区间非常小,在最终的烧结过程中,会产生非超导第二相,这些第二相会导致超导芯的晶间弱连接,严重影响电流的传输。此外,由于fese
x
te1‑
x
活性较高,长时间的高温烧结时非常容易与金属包套发生反应生成非超导的反应层,也会降低fese
x
te1‑
x
超导带材的超导性能;导致fese
x
te1‑
x
超导带材的临界传输电流密度降低,甚至只有磁化电流。
技术实现要素:5.有鉴于此,本发明提供了一种11系铁基超导带材的制备方法,本发明提供的制备方法显著提升了fese
x
te1‑
x
超导带材的临界传输电流密度。
6.为了实现上述发明目的,本发明提供以下技术方案:
7.本发明提供了一种fese
x
te1‑
x
超导带材的制备方法,包括以下步骤:
8.将初始fese
x
te1‑
x
带材进行加压处理和热处理,得到所述fese
x
te1‑
x
超导带材;
9.所述加压处理和热处理包括第一方式或第二方式;
10.所述第一方式为:将所述初始fese
x
te1‑
x
带材进行第一加压处理,泄压后将所述第一加压处理后的初始fese
x
te1‑
x
带材进行第一热处理;
11.所述第二方式为:将初始fese
x
te1‑
x
带材升温至第二热处理的保温温度,在保温条件下对所述初始fese
x
te1‑
x
带材进行第二加压处理。
12.优选的,所述第一热处理为第一升温至第一保温温度进行第一保温;
13.所述第二热处理为第二升温至第二保温温度进行第二保温;
14.所述第一保温温度和第二保温温度独立的为200~400℃,所述第一保温时间和第二保温时间独立的为10~40min。
15.优选的,所述第一升温和第二升温的速率独立的为5~30℃/min。
16.优选的,所述第一加压处理为第一升压至第一保压压力进行第一保压;
17.所述第一保压的压力为1~3gpa,所述第一保压的时间为10~40min。
18.优选的,所述第一升压的速率为1000~7000mpa/min。
19.优选的,所述第二加压处理为第二升压至第二保压压力进行第二保压;
20.所述第二保压的压力为10~500mp。
21.优选的,所述第二升压的速率为25~100mpa/min。
22.优选的,所述第一热处理和第二热处理独立的在真空氛围或保护气氛围中进行。
23.优选的,所述初始fese
x
te1‑
x
带材的制备方法包括以下步骤:
24.将fese
x
te1‑
x
粉末装入金属管密封后依次进行旋锻、拉拔和轧制,得到所述初始fese
x
te1‑
x
带材。
25.优选的,所述第一热处理后还包括:将所述第一热处理后得到第一热处理产物进行淬火。
26.本发明提供了一种fese
x
te1‑
x
超导带材的制备方法,包括以下步骤将初始fese
x
te1‑
x
带材进行加压处理和热处理,得到所述fese
x
te1‑
x
超导带材;所述加压处理和热处理包括第一方式或第二方式;所述第一方式为:将所述初始fese
x
te1‑
x
带材进行第一加压处理,泄压后将所述第一加压处理后的初始fese
x
te1‑
x
带材进行第一热处理;所述第二方式为:将初始fese
x
te1‑
x
带材升温至第二热处理的保温温度时,在保温条件下对所述初始fese
x
te1‑
x
带材进行第二加压处理。本发明提供的制备方法通过在进行热处理之前首先进行加压处理或在进行热处理的保温时同时进行加压处理,能够促进热处理中晶界间的反应,使fese
x
te1‑
x
粉末在较低温度和较短时间下进行热处理即可达到良好的烧结,同时有效避免高温时fese
x
te1‑
x
超导带材中非超导第二相的生成及超导芯与包套间的反应,提升了fese
x
te1‑
x
超导带材的纯度。此外,第一加压处理和第二加压处理还提高了fese
x
te1‑
x
超导带材的致密程度,减少了孔洞和裂纹。本发明显著提升fese
x
te1‑
x
超导带材的临界传输电流密度。由实施例的结果表明,本发明提供的制备方法得到的fese
x
te1‑
x
超导带材的纯度≥98.5%,临界传输电流密度高达15000a/cm3。
附图说明
27.图1为实施例3制备得到的fese
x
te1‑
x
超导带材的截面形貌光镜照片;
28.图2为实施例10制备得到的fese
x
te1‑
x
超导带材的截面形貌光镜照片;
29.图3为对比例1制备得到的fese
x
te1‑
x
超导带材的截面形貌光镜照片。
具体实施方式
30.本发明提供了一种fese
x
te1‑
x
超导带材的制备方法,包括以下步骤:
31.将初始fese
x
te1‑
x
带材进行加压处理和热处理,得到所述fese
x
te1‑
x
超导带材;
32.所述加压处理和热处理包括第一方式或第二方式;
33.所述第一方式包括:将所述初始fese
x
te1‑
x
带材进行第一加压处理,泄压后将所述第一加压处理后的初始fese
x
te1‑
x
带材进行第一热处理;
34.所述第二方式包括:将初始fese
x
te1‑
x
带材升温至第二热处理的保温温度,在保温条件下对所述初始fese
x
te1‑
x
超导带材进行第二加压处理。
35.如无特殊说明,在本发明中,所用原料均为本领域技术人员熟知的市售产品。
36.在本发明中,所述第一方式包括:将所述初始fese
x
te1‑
x
带材进行第一加压处理,
泄压后将所述第一加压处理后的初始fese
x
te1‑
x
带材进行第一热处理。
37.本发明将初始fese
x
te1‑
x
带材进行第一加压处理。
38.在本发明中,所述初始fese
x
te1‑
x
带材是指热处理前的带材;本发明对所述初始fese
x
te1‑
x
带材的来源没有特殊的限制,采用本领域技术人员熟知的技术方案制备即可。在本发明实施例中,所述初始fese
x
te1‑
x
带材的制备方法优选包括以下步骤:
39.将fese
x
te1‑
x
粉末装入金属管密封后依次进行旋锻、拉拔和轧制,得到所述初始fese
x
te1‑
x
带材。
40.在本发明中,所述fese
x
te1‑
x
粉末优选通过熔融法制备得到,本发明对所述熔融法制备fese
x
te1‑
x
粉末的具体实施过程没有特殊要求,采用本领域技术人员熟知的熔融法即可。
41.本发明将所述fese
x
te1‑
x
粉末装入金属管密封后依次进行旋锻、拉拔和轧制,在本发明中,所述金属管优选为铁管、铌管或银管,在本发明的具体实施例中,所述金属管的内径优选为5mm,所述金属管的外径优选为8mm,本发明对所述旋锻、拉拔和轧制的具体实施过程没有特殊要求,采用本领域技术人员熟知的操作进行即可;在本发明中,制备所述初始fese
x
te1‑
x
带材时优选在保护气氛围中进行,所述保护气优选为惰性气体,更优选为氩气。
42.在本发明中,所述初始fese
x
te1‑
x
带材宽优选为4mm,所述初始fese
x
te1‑
x
带材厚优选为0.4mm。
43.在本发明中,所述第一加压处理优选为第一升压至第一保压压力进行第一保压,所述第一保压压力优选为1~3gpa,更优选为1.2~2.5gpa,在本发明的具体实施例中,所述第一保压压力优选为1gpa、2gpa或3gpa;所述第一保压的时间优选为10~40min,更优选为20~30min,在本发明的具体实施例中,所述第一保压的时间优选为10min、20min或30min。
44.在本发明中,第一升压的速率优选为1000~7000mpa/min,更优选为3000~6000mpa/min。
45.本发明优选将所述初始fese
x
te1‑
x
带材放置于合金压头之间进行所述第一加压处理,在本发明中,进行所述第一加压处理时初始fese
x
te1‑
x
带材的数量优选≥1,更优选≥2;在本发明中,所述第一加压处理时初始fese
x
te1‑
x
带材的数量的最大值优选以合金压头的接触面面积确定;在本发明中,所述合金压头优选为钨钴合金压头或钨钛合金压头,所述钨钴合金压头优选为yg8合金压头,所述钨钛合金压头优选为yt15合金压头。
46.所述第一加压处理后,本发明泄压后将所述第一加压处理后的初始fese
x
te1‑
x
带材进行第一热处理,得到所述fese
x
te1‑
x
超导带材。
47.在本发明中,所述第一热处理优选为第一升温至第一保温温度进行第一保温,所述第一保温温度优选为200~400℃,更优选为220~380℃,在本发明的具体实施例中,所述第一保温温度优选为200℃、300℃或400℃;所述第一保温时间优选为10~40min,更优选为12~25min。
48.在本发明中,所述第一升温的速率优选为5~30℃/min,更优选为10~20℃/min,最优选为15℃/min。
49.在本发明中,所述第一热处理优选在真空氛围或保护气氛围中进行,更优选在真空氛围中进行;所述保护气氛围优选为惰性气体氛围,所述惰性气体优选为氩气;所述真空氛围的真空度优选为1
×
10
‑3~1
×
10
‑5pa。
50.本发明优选将泄压的初始fese
x
te1‑
x
带材装入石英管中进行所述第一热处理,所述第一热处理优选在箱式炉中进行。
51.所述第一热处理后,本发明优选还包括:将所述第一热处理后得到第一热处理产物进行淬火,得到所述fese
x
te1‑
x
超导带材;在本发明中,所述淬火的介质优选为水,所述水的温度优选为室温;本发明对所述淬火的具体实施过程没有特殊要求。
52.在本发明中,所述第二方式为:将初始fese
x
te1‑
x
带材升温至第二热处理的保温温度时,在保温条件下对所述初始fese
x
te1‑
x
带材进行第二加压处理。
53.在本发明中,所述初始fese
x
te1‑
x
带材的制备方法和尺寸优选与上文中记载的所述初始fese
x
te1‑
x
带材的制备方法相同和尺寸相同,在此不再赘述。
54.本发明优选在所述第二热处理前对所述初始fese
x
te1‑
x
带材进行前处理,在本发明中,所述前处理优选为在所述初始fese
x
te1‑
x
带材表面涂覆保护涂层,在本发明中,所述保护涂层的材质优选为氮化硼,本发明对所述保护涂层的涂覆厚度没有特殊要求。
55.在本发明中,所述第二热处理优选为第二升温至第二保温温度进行第二保温,所述第二保温温度优选为200~400℃,更优选为300~400℃,在本发明的具体实施例中,所述第二保温温度优选为200℃、300℃或400℃;所述第二保温时间优选为10~40min,更优选为12~23min。
56.在本发明中,所述第二升温的速率优选为5~30℃/min,更优选为15~25℃/min,最优选为12~20℃/min。
57.在本发明中,所述第二热处理优选在真空氛围或保护气氛围中进行,更优选在保护气氛围中进行;所述保护气氛围优选为惰性气体氛围,所述惰性气体优选为氩气。
58.升温至第二保温温度时,本发明在第二保温的条件下对初始fese
x
te1‑
x
超导带材进行第二加压处理。
59.在本发明中,所述第二加压处理优选为第二升压至第二保压压力进行第二保压,所述第二保压的压力优选为10~500mpa,更优选为25~300mpa,最优选为50~200mpa。
60.在本发明中,所述第二保压的时间优选为所述第二热处理的保温时间与升压至所述第二加压处理的保压压力的时间之差。
61.在本发明中,所述第二升压的速率优选为25~100mpa/min,更优选为30~80mpa/min。
62.本发明优选将所述初始fese
x
te1‑
x
带材放置于合金压头之间。然后将所述合金压头放置于热压烧结炉中进行所述第二热处理,当升温至所述第二热处理的保温温度时,对所述合金压头施加单轴压力,同时进行第二加压处理;在本发明中,进行所述第二热处理时初始fese
x
te1‑
x
带材的数量优选≥1,更优选≥2;在本发明中,所述第二热处理时初始fese
x
te1‑
x
超导带材的数量的最大值优选以合金压头接触面的面积确定;在本发明中,所述合金压头优选为钨钴合金压头或钨钛合金压头,所述钨钴合金压头优选为yg8合金压头,所述钨钛合金压头优选为yt15合金压头。
63.本发明提供的fese
x
te1‑
x
超导带材的制备方法将初始fese
x
te1‑
x
带材进行加压处理和热处理,得到所述fese
x
te1‑
x
超导带材;所述加压处理和热处理包括第一方式或第二方式;其中,第一种方式将初始fese
x
te1‑
x
带材进行第一加压处理(室温冷压)后泄压再进行第一热处理;第二种方式进行第二热处理升温至保温温度时,在保温条件下进行第二加压处
理(热压),促进了第一或第二热处理过程中晶界间的反应,提升热处理效率,在较低热处理温度(200~400℃)和较短热处理的时间(10~30min)时即可达到良好的烧结效果,获得晶界连接性良好的超导芯。同时,使用本发明中的热处理工艺还可以避免非超导第二相在晶界间的生成,进一步提高fese
x
te1‑
x
超导带材晶界连接性的同时也提升了超导芯的纯度。此外,低温短时间热处理还能够减缓金属包套与超导芯材之间的反应,提升超导芯的纯度。最后,本发明通过第一加压或第二加压处理还能够提高超导芯的致密程度,减少孔洞和裂纹等缺陷,最终提高了fese
x
te1‑
x
超导带材的临界传输电流密度。
64.本发明提供的制备方法由于第一加压处理(室温冷压)在进行热处理之前,而第二加压处理(热压)在进行热处理保温时,因此,第一加压处理的保压压力大于所述第二加压处理的保压压力。
65.下面将结合本发明中的实施例,对本发明中的技术方案进行清楚、完整地描述。显然,所描述的实施例仅是本发明一部分实施例,而不是全部的实施例。基于本发明中的实施例,本领域普通技术人员在没有做出创造性劳动前提下所获得的所有其他实施例,都属于本发明保护的范围。
66.实施例1
67.在氩气手套箱中,将fese
x
te1‑
x
粉末装入内径为5mm外径为8mm的fe管中,两端密封。经过旋锻、拉拔、轧制得到宽4mm,厚度为0.4mm的初始fese
x
te1‑
x
带材;
68.将1片初始fese
x
te1‑
x
带材置于硬质合金压头之间,以5000mpa/min的速度升压至3gpa的压力,保持40min后卸载压力并取出带材,得到加压fese
x
te1‑
x
带材;
69.将加压fese
x
te1‑
x
带材封入真空石英管(真空度为1
×
10
‑3pa)中,在箱式炉中以15℃/min升温至400℃保温20min取出后放入水中进行淬火,即可获得fese
x
te1‑
x
超导带材。
70.实施例2
71.在氩气手套箱中,将fese
x
te1‑
x
粉末装入内径为5mm外径为8mm的fe管中,两端密封。经过旋锻、拉拔、轧制得到宽4mm,厚度为0.4mm的初始fese
x
te1‑
x
带材;
72.将1片初始fese
x
te1‑
x
带材置于硬质合金压头之间,以5000mpa/min的速度升压至3gpa的压力,保持40min后卸载压力并取出带材,得到加压fese
x
te1‑
x
超导带材;
73.将加压fese
x
te1‑
x
带材封入真空石英管(真空度为1
×
10
‑3pa)中,在箱式炉中以15℃/min升温至200℃保温30min取出后放入水中进行淬火,即可获得fese
x
te1‑
x
超导带材。
74.实施例3
75.在氩气手套箱中,将fese
x
te1‑
x
粉末装入内径为5mm外径为8mm的nb管中,两端密封。经过旋锻、拉拔、轧制得到宽4mm,厚度为0.4mm的初始fese
x
te1‑
x
带材;
76.将1片初始fese
x
te1‑
x
带材置于硬质合金压头之间,以5000mpa/min的速度升压至2gpa的压力,保持30min后卸载压力并取出带材,得到加压fese
x
te1‑
x
带材;
77.将加压fese
x
te1‑
x
带材封入真空石英管(真空度为1
×
10
‑3pa)中,在箱式炉中以15℃/min升温至400℃保温20min取出后放入水中进行淬火,即可获得fese
x
te1‑
x
超导带材。
78.图1为本发明实施例3制备的fese
x
te1‑
x
超导带材的截面形貌图,由图1可以得出,本发明实施例3制备的fese
x
te1‑
x
超导带材芯部晶界连接性好,且致密程度高、无孔洞和裂纹。
79.实施例4
80.在氩气手套箱中,将fese
x
te1‑
x
粉末装入内径为5mm外径为8mm的nb管中,两端密封。经过旋锻、拉拔、轧制得到宽4mm,厚度为0.4mm的初始fese
x
te1‑
x
带材;
81.将1片初始fese
x
te1‑
x
带材置于硬质合金压头之间,以5000mpa/min的速度升压至2gpa的压力,保持30min后卸载压力并取出带材,得到加压fese
x
te1‑
x
带材;
82.将加压fese
x
te1‑
x
带材封入真空石英管(真空度为1
×
10
‑3pa)中,在箱式炉中以15℃/min升温至300℃保温30min取出后放入水中进行淬火,即可获得fese
x
te1‑
x
超导带材。
83.实施例5
84.在氩气手套箱中,将fese
x
te1‑
x
粉末装入内径为5mm外径为8mm的ag管中,两端密封。经过旋锻、拉拔、轧制得到宽4mm,厚度为0.4mm的初始fese
x
te1‑
x
带材;
85.将1片初始fese
x
te1‑
x
带材置于硬质合金压头之间,以5000mpa/min的速度升压至1gpa的压力,保持20min后卸载压力并取出带材,得到加压fese
x
te1‑
x
带材;
86.将加压fese
x
te1‑
x
带材封入真空石英管(真空度为1
×
10
‑3pa)中,在箱式炉中以15℃/min升温至300℃保温10min取出后放入水中进行淬火,即可获得fese
x
te1‑
x
超导带材。
87.实施例6
88.在氩气手套箱中,将fese
x
te1‑
x
粉末装入内径为5mm外径为8mm的ag管中,两端密封。经过旋锻、拉拔、轧制得到宽4mm,厚度为0.4mm的初始fese
x
te1‑
x
带材;
89.将1片初始fese
x
te1‑
x
带材置于硬质合金压头之间,以5000mpa/min的速度升压至1gpa的压力,保持20min后卸载压力并取出带材,得到加压fese
x
te1‑
x
带材;
90.将加压fese
x
te1‑
x
带材封入真空石英管(真空度为1
×
10
‑3pa)中,在箱式炉中以15℃/min升温至200℃保温10min取出后放入水中进行淬火,即可获得fese
x
te1‑
x
超导带材。
91.实施例7
92.在氩气手套箱中,将fese
x
te1‑
x
粉末装入内径为5mm外径为8mm的fe管中,两端密封。经过旋锻、拉拔、轧制得到宽4mm,厚度为0.4mm的初始fese
x
te1‑
x
带材;
93.将2片初始fese
x
te1‑
x
带材涂抹氮化硼后置于两块硬质合金压头之间,将压头放入热压机中。在氩气保护下,将热压机以20℃/min的升温速率升高到400℃,并保温12min,同时到达400℃时,经过2分钟将施加于初始fese
x
te1‑
x
带材上的单轴压力匀速提升至200mpa,并保持10分钟。待保压时间和保温时间同时结束后,卸载压力并自然冷却热压机至室温,得到fese
x
te1‑
x
超导带材。
94.实施例8
95.在氩气手套箱中,将fese
x
te1‑
x
粉末装入内径为5mm外径为8mm的fe管中,两端密封。经过旋锻、拉拔、轧制得到宽4mm,厚度为0.4mm的初始fese
x
te1‑
x
带材;
96.将2片初始fese
x
te1‑
x
带材涂抹氮化硼后置于两块硬质合金压头之间,将压头放入热压机中。在氩气保护下,将热压机以20℃/min的升温速率升高到400℃,并保温22min,同时到达400℃时,经过2分钟将施加于初始fese
x
te1‑
x
带材上的单轴压力匀速提升至100mpa,并保持20分钟。待保压时间和保温时间同时结束后,卸载压力并自然冷却热压机至室温,得到fese
x
te1‑
x
超导带材。
97.实施例9
98.在氩气手套箱中,将fese
x
te1‑
x
粉末装入内径为5mm外径为8mm的fe管中,两端密封。经过旋锻、拉拔、轧制得到宽4mm,厚度为0.4mm的初始fese
x
te1‑
x
带材;
99.将2片初始fese
x
te1‑
x
带材涂抹氮化硼后置于两块硬质合金压头之间,将压头放入热压机中。在氩气保护下,将热压机以20℃/min的升温速率升高到300℃,并保温22min,同时到达300℃时,经过2分钟将施加于初始fese
x
te1‑
x
带材上的单轴压力匀速提升至200mpa,并保持20分钟。待保压时间和保温时间同时结束后,卸载压力并自然冷却热压机至室温,得到fese
x
te1‑
x
超导带材。
100.实施例10
101.在氩气手套箱中,将fese
x
te1‑
x
粉末装入内径为5mm外径为8mm的nb管中,两端密封。经过旋锻、拉拔、轧制得到宽4mm,厚度为0.4mm的初始fese
x
te1‑
x
带材;
102.将2片初始fese
x
te1‑
x
带材涂抹氮化硼后置于两块硬质合金压头之间,将压头放入热压机中。在氩气保护下,将热压机以20℃/min的升温速率升高到400℃,并保温12min,同时到达400℃时,经过2分钟将施加于初始fese
x
te1‑
x
带材上的单轴压力匀速提升至100mpa,并保持10分钟。待保压时间和保温时间同时结束后,卸载压力并自然冷却热压机至室温,得到fese
x
te1‑
x
超导带材。
103.图2为本发明实施例10制备的fese
x
te1‑
x
超导带材的截面形貌图,由图2可以得出,本发明实施例10制备的fese
x
te1‑
x
超导带材芯部晶界连接性好,且致密程度高、无孔洞和裂纹。
104.实施例11
105.在氩气手套箱中,将fese
x
te1‑
x
粉末装入内径为5mm外径为8mm的fe管中,两端密封。经过旋锻、拉拔、轧制得到宽4mm,厚度为0.4mm的初始fese
x
te1‑
x
带材;
106.将2片初始fese
x
te1‑
x
带材涂抹氮化硼后置于两块硬质合金压头之间,将压头放入热压机中。在氩气保护下,将热压机以20℃/min的升温速率升高到300℃,并保温22min,同时到达300℃时,经过2分钟将施加于初始fese
x
te1‑
x
带材上的单轴压力匀速提升至100mpa,并保持20分钟。待保压时间和保温时间同时结束后,卸载压力并自然冷却热压机至室温,得到fese
x
te1‑
x
超导带材。
107.实施例12
108.在氩气手套箱中,将fese
x
te1‑
x
粉末装入内径为5mm外径为8mm的nb管中,两端密封。经过旋锻、拉拔、轧制得到宽4mm,厚度为0.4mm的初始fese
x
te1‑
x
带材;
109.将2片初始fese
x
te1‑
x
带材涂抹氮化硼后置于两块硬质合金压头之间,将压头放入热压机中。在氩气保护下,将热压机以20℃/min的升温速率升高到400℃,并保温22min,同时到达400℃时,经过2分钟将施加于初始fese
x
te1‑
x
带材上的单轴压力匀速提升至50mpa,并保持20分钟。待保压时间和保温时间同时结束后,卸载压力并自然冷却热压机至室温,得到fese
x
te1‑
x
超导带材。
110.实施例13
111.在氩气手套箱中,将fese
x
te1‑
x
粉末装入内径为5mm外径为8mm的ag管中,两端密封。经过旋锻、拉拔、轧制得到宽4mm,厚度为0.4mm的初始fese
x
te1‑
x
带材;
112.将2片初始fese
x
te1‑
x
带材涂抹氮化硼后置于两块硬质合金压头之间,将压头放入热压机中。在氩气保护下,将热压机以20℃/min的升温速率升高到300℃,并保温22min,同时到达300℃时,经过2分钟将施加于初始fese
x
te1‑
x
带材上的单轴压力匀速提升至100mpa,并保持20分钟。待保压时间和保温时间同时结束后,卸载压力并自然冷却热压机至室温,得
到fese
x
te1‑
x
超导带材。
113.实施例14
114.在氩气手套箱中,将fese
x
te1‑
x
粉末装入内径为5mm外径为8mm的ag管中,两端密封。经过旋锻、拉拔、轧制得到宽4mm,厚度为0.4mm的初始fese
x
te1‑
x
带材;
115.将2片初始fese
x
te1‑
x
带材涂抹氮化硼后置于两块硬质合金压头之间,将压头放入热压机中。在氩气保护下,将热压机以20℃/min的升温速率升高到200℃,并保温22min,同时到达200℃时,经过2分钟将施加于初始fese
x
te1‑
x
带材上的单轴压力匀速提升至100mpa,并保持20分钟。待保压时间和保温时间同时结束后,卸载压力并自然冷却热压机至室温,得到fese
x
te1‑
x
超导带材。
116.实施例15
117.在氩气手套箱中,将fese
x
te1‑
x
粉末装入内径为5mm外径为8mm的ag管中,两端密封。经过旋锻、拉拔、轧制得到宽4mm,厚度为0.4mm的初始fese
x
te1‑
x
超导带材;
118.将2片初始fese
x
te1‑
x
超导带材涂抹氮化硼后置于两块硬质合金压头之间,将压头放入热压机中。在氩气保护下,将热压机以10℃/min的升温速率升高到200℃,并保温22min,同时到达200℃时,经过2分钟将施加于初始fese
x
te1‑
x
超导带材上的单轴压力匀速提升至50mpa,并保持20分钟。待保压时间和保温时间同时结束后,卸载压力并自然冷却热压机至室温,得到fese
x
te1‑
x
超导带材。
119.对比例1
120.在氩气手套箱中,将fese
x
te1‑
x
粉末装入内径为5mm外径为8mm的nb管中,两端密封。经过旋锻、拉拔、轧制得到宽4mm,厚度为0.4mm的初始fese
x
te1‑
x
带材;
121.将初始fese
x
te1‑
x
带材封入真空石英管(真空度为1
×
10
‑3pa)中,在箱式炉中以8℃/min升温至200℃保温2h,取出后放入水中进行淬火,即可获得fese
x
te1‑
x
超导带材。
122.图3为本发明对比例1制备的fese
x
te1‑
x
超导带材的截面形貌图,由图3可以得出,本发明实施例1制备的fese
x
te1‑
x
超导带材芯部晶界连接性不好,且存在明显的裂纹。
123.对比例2
124.参考文献:transport properties ofiron
‑
based fete
0.5
se
0.5 superconducting wire,toshinori ozaki,keita deguchi,yoshikazu mizuguchi,hiroaki kumakura,andyoshihiko takano,2010;
125.在氩气手套箱中,将fese
x
te1‑
x
粉末装入内径为3.5mm外径为6mm的fe管中,两端密封。经过旋锻、拉拔得到直径为1.1mm初始fese
x
te1‑
x
线材;
126.将初始fese
x
te1‑
x
线材封入真空石英管(真空度为1
×
10
‑3pa)中,在箱式炉中迅速加热到200℃并保温2h,即可获得fese
x
te1‑
x
超导线材。
127.对比例3
128.参考文献:fabrication of fete
0.4
se
0.6 superconducting tapes by achemical
‑
transformation pit process;hiroki izawa,yoshikazu mizuguchi,yoshihiko takano,osuke miura,2014;physica c;
129.在氩气手套箱中,将fese
x
te1‑
x
粉末装入内径为4mm外径为6.2mm的fe管中,两端密封。经过旋锻、拉拔、轧制得到0.5mm的初始fese
x
te1‑
x
带材;
130.将初始fese
x
te1‑
x
带材封入真空石英管(真空度为1
×
10
‑3pa)中,在箱式炉中525℃
保温3小时再降至200℃保温2小时,即可获得fese
x
te1‑
x
超导带材。
131.对比例4
132.参考文献:fabrication of nb
‑
sheathed fese
0.5
te
0.5 tape by an ex
‑
situ powder
‑
in tube method;xiong li,yufeng zhang,feifei yuan,jincheng zhuang,zhimin cao,xiangzhuo xing,wei zhou,zhixiang shi,2015;
133.在氩气手套箱中,将fese
x
te1‑
x
粉末装入内径为4.6mm外径为6.4mm的nb管中,两端密封。经过旋锻、拉拔、轧制得到厚度为0.15mm的初始fese
x
te1‑
x
带材;
134.将初始fese
x
te1‑
x
带材封入真空石英管(真空度为1
×
10
‑3pa)中,在箱式炉中550℃保温10min,取出后在空气中进行淬火,即可获得fese
x
te1‑
x
超导带材。
135.对比例5
136.参考文献:exploring the feasibility of fe(se,te)conductors by ex
‑
situ powder
‑
in
‑
tube method;m.palombo,a.malagoli,m.pani,c.bernini,p.manfrinetti,a.palenzona,and m.putti;2015;
137.在氩气手套箱中,将fese
x
te1‑
x
粉末装入fe管中,两端密封。经过旋锻、拉拔得到直径为1mm的线材。
138.将初始线材封入真空石英管中,在箱式炉中800℃保温1小时,即可获得fese
x
te1‑
x
超导线材。
139.对比例6
140.参考文献:fabrication offese superconducting tapes with high
‑
energy ball milling aided pit process;jianqing feng,shengnan zhang,jixing liu,chengshan li,xiaobo ma,pingxiang zhang;2015;
141.在氩气手套箱中,将fese粉末装入fe管中,两端密封。经过旋锻、拉拔、轧制得到宽4.5mm,厚度为0.5mm的初始fese带材;
142.将初始fese带材封入真空石英管(真空度为1
×
10
‑3pa)中,在箱式炉中加热至800℃,即可获得fese超导带材。
143.对比例7
144.参考文献:critical current and microstructure of fese wires and tapes preparedby pit method;vladimira.vlasenko,kirill s.pervakov,yuri f.eltsev,vladimir d.berbentsev,anastasiia s.tsapleva,pavel a.lukyanov,ildar m.abdyukhanov,andvladimirm.pudalov;2019;
145.在氩气手套箱中,将fese粉末装入不锈钢容器中,两端密封。经过950℃热气挤压得到fese线材;
146.将fese线材在350℃保温72h,即可获得fese超导线材。
147.测试例1
148.对实施例1~15和对比例1制备的产品进行密度测定,测试结果如表1所示,实施例1~6(冷压)和实施例7~15(热压)制备得到的产品的密度明显大于对比例1(普通烧结)制备的产品,表明本发明提供的制备方法制备得到的fese
x
te1‑
x
超导带材致密度更好。
149.表1实施例1~15和对比例1制备的产品密度测定结果
[0150][0151][0152]
测试例2
[0153]
对实施例1~15、对比例1~7(其中对比例2~7为现有技术)制备的产品进行传输电流密度、超导转变温度进行测定,结果如表2所示,由表2可以得出,本发明提供的制备方法得到的fese
x
te1‑
x
超导带材产品具有优异的传输电流密度和较高的超导转变温度。
[0154]
表2实施例1~15和对比例1~7制备的产品性能测试结果
[0155][0156][0157]
虽然本发明所揭示的实施方式如上,但所述的内容仅为便于理解本发明而采用的实施方式,并非用以限定本发明。任何本发明所属领域内的技术人员,在不脱离本发明所揭示的精神和范围的前提下,可以在实施的形式及细节上进行任何的修改与变化,但本发明的专利保护范围,仍须以所附的权利要求书所界定的范围为准。