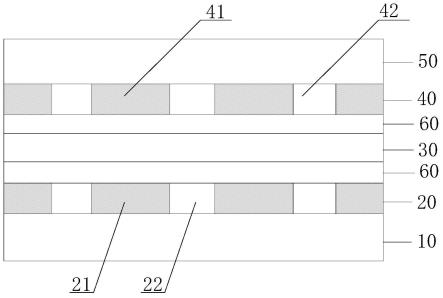
1.本发明涉及薄膜电感领域,具体而言,涉及一种薄膜电感结构及其制备方法。
背景技术:2.随着电子电力的迅猛发展,对大功率大电流电感的需求越来越大,而在大功率、大电流应用中,低损耗,低成本、高转换效率的合金磁性材料越来越受到人们的青睐。cn105590747b公开了一种功率型元器件及其制作方法。其采用ltcc工艺制作,其中为达到耐大电流,采用印刷沟槽填充银浆的方式增加银层厚度,但是这种工艺在小型化电感上具有明显的限制性,很难实现1.6
×
0.8mm以下尺寸电感的大批量生产。cn110060836a公开了一种多层导电图案电感器及其制造方法。其采用先制作线圈层,然后在线圈层上下表面直接叠加磁片的方式,由于线圈部分电极间存在开口空间,平面磁片直接叠加很容易造成电感厚度不均。cn110660554a公开了一种高磁导率高频率平面电感及其制备方法,其软磁薄膜采用磁控溅射工艺形成,但成本高,效率低且成型厚膜不易控制。
3.目前,电子小型化集成化的趋势越来越明晰,传统绕线和一体成型工艺已越来越不能满足发展要求,因此发展尺寸更小、厚度更薄的薄膜功率电感成为必然趋势,为保证薄膜电感大饱和电流的特性,电极线圈要么把线宽做宽、要么把线厚做厚,而由于电感尺寸的限制,线宽做宽势必会牺牲电感量,因此对于电极线圈来说,增加线厚来提高饱和电流更为有利。但是,对传统的三明治结构的薄膜电感来说,增加线厚会导致基板磁片与线圈层压合时,由于电极图案部分厚度落差过大而导致两者贴合不够紧密,进而引起切割时出现产品开裂甚至分层的弊端。
4.因此,有必要提供一种薄膜电感,使其线圈层和基板磁片结合性更佳,不易在切割时出现开裂甚至严重分层的现象。
技术实现要素:5.本发明的主要目的在于提供一种薄膜电感结构及其制备方法,以解决现有技术中因线圈较厚导致的线圈层和基板磁片结合性差,从而易在切割时出现开裂甚至严重分层现象的问题。
6.为了实现上述目的,根据本发明的一个方面,提供了一种薄膜电感结构,薄膜电感结构包括:第一基板层,具有第一表面,且第一表面分为第一区域和第二区域;第一线圈层,设置在第一基板层的第一表面上,第一线圈层包括第一电极线圈和第一填充部,第一电极线圈设置在第一区域,第一填充部设置在至少部分第二区域;绝缘层,设置在第一线圈层的远离第一基板层的表面,绝缘层的远离第一基板层的表面分为第三区域和第四区域,且第三区域在第一表面的垂直投影与第一区域完全重合;第二线圈层,设置在绝缘层的远离第一基板层的表面,第二线圈层包括第二电极线圈和第二填充部,第二电极线圈设置在第三区域,第二填充部设置在至少部分第四区域;第二基板层,设置在第二线圈层的远离第一基板层的表面;其中,第一填充部及第二填充部的材料各自独立地包括软磁合金、热固性树脂
及热塑性树脂。
7.进一步地,第一电极线圈与第一填充部的远离第一基板层的表面齐平;第二电极线圈和第二填充部的远离第一基板层的表面齐平。
8.进一步地,第一电极线圈与第一表面接触的区域与第一区域完全重合,且第一填充部设置在全部的第二区域;第二电极线圈与绝缘层表面接触的区域与第三区域完全重合,且第二填充部设置在全部的第四区域。
9.进一步地,热固性树脂选自双酚a型环氧树脂、双酚f型环氧树脂、有机硅树脂和环氧改性硅树脂中的一种或多种;热塑性树脂选自聚甲基丙烯酸甲酯和/或聚乙烯醇缩丁醛。
10.进一步地,按重量份计,第一填充部及第二填充部的材料各自独立地包括90~95份的软磁合金、3~6份的热固性树脂热塑性树脂及2~4份的热塑性树脂。
11.进一步地,软磁合金为颗粒状;优选地,软磁合金的粒径为2~10μm。
12.进一步地,绝缘层的材料为聚酰亚胺、聚酯、聚酰亚胺、氟碳膜或芳香族聚酰胺;优选地,绝缘层的厚度为13~25μm;优选地,薄膜电感结构还包括胶层,胶层分别设置在第一线圈层与绝缘层之间,以及第二线圈层与绝缘层之间;优选地,胶层的材料为环氧树脂、丙烯酸酯树脂、酚醛改性聚乙烯醇缩丁醛树脂、聚酯树脂或聚酰亚胺树脂中的一种或多种;优选地,胶层的厚度为3~5μm。
13.进一步地,第一填充部及第二填充部的材料均还包括固化剂及促进剂;优选地,固化剂为间苯二甲胺、异氟尔酮二胺、二乙基甲苯二胺或双氰胺中的一种或多种;优选地,促进剂为2-甲基咪唑、2-乙基-4-甲基咪唑或水杨酸中的一种或多种。
14.进一步地,第一线圈层及第二线圈层的厚度各自独立地为20~100μm,第一基板层及第二基板层的厚度各自独立地为50~200μm。
15.为了实现上述目的,根据本发明的一个方面,提供了一种上述薄膜电感结构的制备方法,制备方法包括以下步骤:制作线圈层,线圈层包括第一线圈层、绝缘层和第二线圈层,第一线圈层包括第一电极线圈及第一填充部,第二线圈层包括第二电极线圈及第二填充部;将第一基板层置于第一线圈层远离绝缘层的一侧,将第二基板层置于第二线圈层远离绝缘层的一侧,热压后得到薄膜电感结构;其中,第一基板层具有第一表面,且第一表面分为第一区域和第二区域;第一电极线圈设置在第一区域,第一填充部设置在至少部分第二区域;绝缘层的远离第一基板层的表面分为第三区域和第四区域,且第三区域在第一表面的垂直投影与第一区域完全重合;第二电极线圈设置在第三区域,第二填充部设置在至少部分第四区域;第一填充部及第二填充部的材料各自独立地包括软磁合金、热固性树脂及热塑性树脂。
16.进一步地,制作线圈层的步骤包括:通过胶层将第一电极线圈和第二电极线圈粘附在绝缘层的相对的两侧表面,形成预备线圈;将第一填充部的材料放置于绝缘层所欲形成第一填充部的位置,并使其高度超出第一电极线圈3~5μm;将第二填充部的材料放置于绝缘层所欲形成第二填充部的位置,并使其高度超出第二电极线圈3~5μm;得到待压线圈;对待压线圈进行第一次热压处理,形成线圈层;优选地,第一次热压处理步骤中,操作温度为65~80℃,操作压力为2~8mpa,操作时间为5~10min。
17.进一步地,热压制备薄膜电感结构的步骤包括:将放置后的第一基板层、线圈层及第二基板层依次第二次热压处理和等静压处理,得到薄膜电感结构;优选地,第二次热压处
理过程中,操作温度为100~150℃,操作压力为15~20mpa,操作时间为10~15min;优选地,等静压处理过程中,操作温度为60~80℃,操作压力为40~60mpa,操作时间为10~25min。
18.本发明的薄膜电感结构中,通过在第一线圈层及第二线圈层中设置的填充部,使其弥补了现有技术中较厚的电极线圈与基板层之间的高度差;与此同时,本发明利用软磁合金、热固性树脂及热塑性树脂作为填充部材料,并使其表面与电极线圈表面平齐,也大幅度地提高了基板磁片与线圈层在后续压合处理时的层间结合作用,促使基板磁片和线圈层结合力度更强。以上两方面因素下,避免了后续切割时薄膜电感开裂甚至严重分层现象的产生。
附图说明
19.构成本技术的一部分的说明书附图用来提供对本发明的进一步理解,本发明的示意性实施例及其说明用于解释本发明,并不构成对本发明的不当限定。在附图中:
20.图1示出了根据本发明实施例1的薄膜电感结构示意图;以及
21.图2示出了本发明实施例1中薄膜电感结构线圈层示意图。
22.其中,上述附图包括以下附图标记:
23.10、第一基板层;20、第一线圈层;21、第一电极线圈;22、第一填充部;30、绝缘层;40、第二线圈层;41、第二电极线圈;42、第二填充部;50、第二基板层;60、胶层。
具体实施方式
24.需要说明的是,在不冲突的情况下,本技术中的实施例及实施例中的特征可以相互组合。下面将参考附图并结合实施例来详细说明本发明。
25.正如背景技术部分所描述的,现有技术中因线圈较厚导致的线圈层和基板磁片结合性差,从而易在切割时出现开裂甚至严重分层现象的问题。
26.为了解决这一问题,本发明提供了一种薄膜电感结构,如图1所示,该薄膜电感结构包括第一基板层10、第一线圈层20、绝缘层30、第二线圈层40及第二基板层50;第一基板层10,具有第一表面,且第一表面分为第一区域和第二区域;第一线圈层20,设置在第一基板层10的第一表面上,第一线圈层20包括第一电极线圈21和第一填充部22,第一电极线圈21设置在第一区域,第一填充部22设置在至少部分第二区域;绝缘层30,设置在第一线圈层20的远离第一基板层10的表面,绝缘层30的远离第一基板层10的表面分为第三区域和第四区域,且第三区域在第一表面的垂直投影与第一区域完全重合;第二线圈层40,设置在绝缘层30的远离第一基板层10的表面,第二线圈层40包括第二电极线圈41和第二填充部42,第二电极线圈41设置在第三区域,第二填充部42设置在至少部分第四区域;第二基板层50,设置在第二线圈层40的远离第一基板层10的表面;其中,第一填充部22及第二填充部42的材料各自独立地包括软磁合金、热固性树脂及热塑性树脂。
27.首先,本发明的薄膜电感结构中,通过在第一线圈层及第二线圈层中设置填充部,使其弥补了现有技术中较厚的电极线圈与基板层之间的高度差。与此同时,本发明利用软磁合金、热固性树脂及热塑性树脂作为填充部材料,使其大幅度地提高了基板磁片与线圈层在后续压合处理时的层间结合作用,促使基板磁片和线圈层结合力度更强。以上两方面因素下,避免了后续切割时薄膜电感开裂甚至中间区域分层严重。其次,本发明以热塑性树
脂、热固性树脂与软磁合金为原料,构成了第一填充部及第二填充部。这样,一方面,可以进一步提高后续压合处理时基板磁片与线圈层间的粘合作用。另一方面,还可以增加产品的强度,使其不易变形。本发明的薄膜电感不需要高温烧结,在后续工序经180~220℃充分固化后,即可拥有与常规ltcc工艺经过高温烧结制成的叠层功率电感相当的磁体强度,可以满足功率电感最高160℃的严苛使用环境,使用寿命较长。
28.为了进一步平衡电感的强度性能以及结合性能,第一电极线圈21与第一填充部22的远离第一基板层10的表面齐平;第二电极线圈41和第二填充部42的远离第一基板层10的表面齐平。
29.为了进一步提高线圈层和基板层之间的结合力,优选第一电极线圈21与第一表面接触的区域与第一区域完全重合,且第一填充部22设置在全部的第二区域;第二电极线圈41与绝缘层30表面接触的区域与第三区域完全重合,且第二填充部42设置在全部的第四区域。
30.优选地,热固性树脂选自双酚a型环氧树脂、双酚f型环氧树脂、有机硅树脂和环氧改性硅树脂中的一种或多种;热塑性树脂选自聚甲基丙烯酸甲酯和/或聚乙烯醇缩丁醛。其中,第一填充部22及第二填充部42的材料类型可以一样也可以不一样。基于上述特定类型树脂的搭配,进一步提高了后续压合处理时基板磁片与线圈层间的粘合作用以及产品的强度。具体地,上述热固性树脂包括但不限于e44、e51、e54;热塑性树脂包括但不限于a21、b44、b76、b79、b98。
31.为了进一步平衡线圈层和基板层之间的结合力以及产品的强度特性,按重量份计,优选第一填充部22及第二填充部42的材料各自独立地包括90~95份的软磁合金、3~6份的热固性树脂热塑性树脂及2~4份的热塑性树脂。优选地,软磁合金为颗粒状;更优选地,软磁合金的粒径为2~10μm(d50)。
32.在一种优选的实施方案中,绝缘层30的材料为聚酰亚胺、聚酯、聚酰亚胺、氟碳膜或芳香族聚酰胺;优选地,绝缘层30的厚度为13~25μm。优选地,薄膜电感结构还包括胶层60,胶层60分别设置在第一线圈层20与绝缘层30之间,以及第二线圈层40与绝缘层30之间;优选地,胶层60的材料为环氧树脂、丙烯酸酯树脂、酚醛改性聚乙烯醇缩丁醛树脂、聚酯树脂或聚酰亚胺树脂中的一种或多种;优选地,胶层60的厚度为3~5μm。上述绝缘层的材料及胶层的材料均为本领域常用材料,本领域技术人员可根据自身产品需求选择相应的材料,在此不多赘述。
33.第一填充部22及第二填充部42各自独立地包括软磁合金、热固性树脂及热塑性树脂。其中,软磁合金的表面包覆有一层厚度小于500nm的无机绝缘薄膜,可以使软磁合金之间形成隔离,提高绝缘电阻率,从而降低涡流损耗。第一填充部22及第二填充部42中软磁合金的密度>4.0g/mm3。
34.为了进一步提高上述各层在固化处理时的固化效率,进而提高产品的特性,优选第一填充部22及第二填充部42的材料均还包括固化剂及促进剂;优选地,固化剂为间苯二甲胺、异氟尔酮二胺、二乙基甲苯二胺或双氰胺中的一种或多种;优选地,促进剂为2-甲基咪唑、2-乙基-4-甲基咪唑或水杨酸中的一种或多种。更优选地,固化剂的含量为软磁合金粉颗粒重量的0.3~1%,促进剂的含量为软磁合金粉颗粒重量的0.1~0.3%。
35.在一种优选的实施方案中,第一线圈层20及第二线圈层40的厚度各自独立地为20
~100μm。线圈层的厚度是根据电感电性能确定的,这是本领域技术人员可根据自身产品需求自行选择的,在此不多赘述。本发明的薄膜电感结构中,第一线圈层及第二线圈层中填充部和电极线圈的上述特定设置方式,也是在满足电感电性能常规使用基础上进行的。
36.在一种优选的实施方案中,第一基板层10及第二基板层50的厚度各自独立地为50~200μm。第一基板层10及第二基板层50各自独立地包括软磁合金、热固性树脂及热塑性树脂。其中,软磁合金颗粒的表面包覆有一层厚度小于500nm的无机绝缘薄膜,可以使软磁合金颗粒之间形成隔离,提高绝缘电阻率,从而降低涡流损耗。第一基板层10及第二基板层50中,软磁合金颗粒的密度>4.0g/mm3,按重量份数计,其结构组成为:90~95wt%的软磁合金粉颗粒作为主结构骨架,5~10wt%的有机添加剂填充于合金粉颗粒间的缝隙中,软磁合金粉颗粒的粒径为5~15μm(d90)。有机添加剂包括热固性树脂如双酚a型环氧树脂、双酚f型环氧树脂中的任意一种;包括热塑性树脂如聚甲基丙烯酸甲酯、聚乙烯醇缩丁醛中的任意一种;还包括固化剂如间苯二甲胺、异氟尔酮二胺、二乙基甲苯二胺或双氰胺中的任意一种;还包括固化剂促进剂如2-甲基咪唑、2-乙基-4-甲基咪唑或水杨酸中的任意一种或多种。优选地,固化剂的含量为软磁合金粉颗粒重量的0.3~1%,固化剂促进剂的含量为软磁合金粉颗粒重量的0.1~0.3%。
37.在一种优选的实施方案中,第一填充部、第二填充部与第一基板层、第二基板层的材料组成一致,区别仅在于填充部使用的软磁合金其粒径可以略小于基板层。基于此,线圈层和基板层之间的结合力以及产品的强度特性均更佳。
38.在一种优选的实施方案中,绝缘层30的材料为聚酰亚胺膜、聚酯膜、氟碳膜或芳香族聚酰胺纸;优选地,绝缘层30的厚度为13~25μm。这是本领域技术人员可根据自身产品需求自行选择的,在此不多赘述。
39.为了进一步提高绝缘层和各线圈层结合作用的目的,优选地,如图1所示,薄膜电感结构还包括厚度为10~15μm的胶层60,胶层60分别设置在第一线圈层20与绝缘层30之间,以及,第二线圈层40与绝缘层30之间;优选地,胶层的材料为环氧树脂、丙烯酸酯树脂、酚醛改性聚乙烯醇缩丁醛树脂、聚酯树脂、聚酰亚胺树脂其中一种。
40.本发明还提供了一种上述的薄膜电感结构的制备方法,制备方法包括以下步骤:制作线圈层,线圈层包括第一线圈层20、绝缘层30和第二线圈层40,第一线圈层20包括第一电极线圈21及第一填充部22构,第二线圈层40包括第二电极线圈41及第二填充部42;将第一基板层10置于第一线圈层20远离绝缘层30的一侧,将第二基板层50置于第二线圈层40远离绝缘层30的一侧,热压后得到薄膜电感结构;其中,第一基板层10具有第一表面,且第一表面分为第一区域和第二区域;第一电极线圈21设置在第一区域,第一填充部22设置在至少部分第二区域;绝缘层30的远离第一基板层10的表面分为第三区域和第四区域,且第三区域在第一表面的垂直投影与第一区域完全重合;第二电极线圈41设置在第三区域,第二填充部42设置在至少部分第四区域;第一填充部22及第二填充部42的材料各自独立地包括软磁合金、热固性树脂及热塑性树脂。
41.基于前文的各项原因,首先,本发明通过第一线圈层及第二线圈层中填充部和电极线圈的特定设置方式,更有效地避免了由于电极线圈厚度过大从而导致的线圈层和基板层存在厚度差的问题,进而大幅度地提高了基板磁片与线圈层在后续压合处理时的层间结合作用,促使基板磁片和线圈层结合性更佳,避免了后续切割时薄膜电感开裂甚至严重分
层的产生。其次,本发明将热塑性树脂和热固性树脂配合使用构成了第一填充部22及第二填充部42,一方面,进一步提高了后续压合处理时基板磁片与线圈层间的粘合作用。另一方面,还增加了产品的强度,使其不易变形。本发明的薄膜电感不需要高温烧结,在后续工序经180~220℃充分固化后,即可拥有与常规ltcc工艺经过高温烧结制成的叠层功率电感相当的磁体强度,可以满足功率电感最高160℃的严苛使用环境。
42.优选地,线圈层结构如图2所示,制作线圈层的步骤包括:通过胶层60将第一电极线圈21和第二电极线圈41粘附在绝缘层30的相对的两侧表面,形成预备线圈;将第一填充部22的材料放置于绝缘层30所欲形成第一填充部22的位置,并使其高度超出第一电极线圈3~5μm;将第二填充部42的材料放置于绝缘层30所欲形成第二填充部42的位置,并使其高度超出第二电极线圈3~5μm;得到待压线圈;对待压线圈进行第一次热压处理,形成线圈层。这样,在第一次热压处理后,第一电极线圈与第一填充部的远离第一基板层的表面齐平;第二电极线圈和第二填充部的远离第一基板层的表面齐平。优选地,第一次热压处理步骤中,操作温度为65~80℃,操作压力为2~8mpa,操作时间为5~10min。基于此,可以进一步发挥热塑性树脂的黏合特性,进而进一步加强线圈层和基板层间的结合力。
43.优选地,热压制备薄膜电感结构的步骤包括:将放置后的第一基板层10、线圈层及第二基板层50依次第二次热压处理和等静压处理,得到薄膜电感结构;为了进一步提高层压处理后产品的表面平整性及层间紧密性,进而提高产品的强度,优选地,第二次热压处理过程中,操作温度为100~150℃,操作压力为15~20mpa,操作时间为10~15min;为了进一步提高产品的性能均一性,优选地,等静压处理过程中,操作温度为60~80℃,操作压力为40~60mpa,操作时间为10~25min。
44.具体地,先提供与第一填充部22材料组成完全一样的第一料片,以及与第二填充部42材料组成完全一样的第二料片,利用激光雕刻机将上述料片上相应对应第一电极线圈21及第二电极线圈41位置的材料去除,同时将压合时需要ccd对位的对位标记打出。然后,再利用热压机将各填充部和各电极线圈进行压合处理,为进一步提高各填充部和各电极线圈在后续成品中的齐平特性,原始的各填充部的厚度优选大于各电极线圈线厚度3~5μm。接着,利用热压机将第一基板层10、第一线圈层20、绝缘层30、第二线圈层40及第二基板层50进行压合处理。最后,将层压步骤后的中间产品装入塑封袋中进行真空塑封,继而置于等静压机中进行等静压。等静压能够利用液体介质对产品各方面施加均等的压力,且在此步骤中,热塑性树脂软化便于颗粒挪动重排,从而使产品更加致密化。
45.以下结合具体实施例对本技术作进一步详细描述,这些实施例不能理解为限制本技术所要求保护的范围。
46.实施例1
47.制作型号为121003(尺寸1.2
×
1.0
×
0.3mm)的薄膜电感,其产品结构的示意图如图1所示,其中,第一基板层厚度为73~76μm;第一线圈层厚度为60μm;绝缘层(材料为聚酰亚胺膜)厚度为13μm,第二线圈层厚度为60μm;第二基板层厚度为73~76μm;胶层(材料为丙烯酸树脂)厚度为3μm。
48.其制备工艺如下:
49.填充部雕刻步骤:取两张裁切好的厚度为63μm的磁片(磁片上另附带有100μm厚度的pet膜),利用激光雕刻机分别将磁片指定位置上材料去除,pet膜不打穿,两张磁片去除
材料部分的图案分别与第一电极线圈及第二电极线圈图案一致,同时将压合时需要ccd对位的对位标记打出,得到第一填充部的材料及第二填充部的材料。其中,第一填充部及第二填充部的材料各自独立地包括91份的软磁合金(d50为5μm的铁硅铬,采用磷酸钝化包覆)、5.45份的热固性树脂(e51环氧树脂)及2.9份的热塑性树脂(丙烯酸树脂),0.5份的固化剂(2-乙基甲苯二胺)及0.15份的促进剂(水杨酸)。
50.线圈层制作步骤:通过胶层将第一电极线圈和第二电极线圈粘附在绝缘层的相对的两侧表面,形成预备线圈;将第一填充部的材料放置于绝缘层所欲形成第一填充部的位置,其高度超出第一电极线圈3μm;将第二填充部的材料放置于绝缘层所欲形成第二填充部的位置,其高度超出第二电极线圈3μm;得到待压线圈;对待压线圈进行第一次热压处理,形成线圈层;剥离第一填充部及第二填充部磁片附带的pet膜,制备得到后的线圈层示意图如图2所示。其中,热压温度控制在70
±
3℃,压力控制在5
±
1mpa,时间为8min。在第一次热压处理后,第一电极线圈与第一填充部的远离第一基板层的表面齐平;第二电极线圈和第二填充部的远离第一基板层的表面齐平。
51.第二次热压步骤:将两片80μm厚的基板层磁片(材料成分和填充部完全一致)分别整齐置于已完成填充的线圈层上下两面,利用热压机进行第二次热压处理。其中,热压温度控制在150℃,压力控制在18mpa,时间为15min。
52.等静压步骤:将两次热压处理之后的中间产品装入塑封袋中进行真空塑封,然后将其置于等静压机中进行等静压处理,等静压压力为50mpa,温度为80℃,保压时间为20min。
53.切割步骤:等静压处理后,利用切割机将压合完成的整版半成品切割成单只产品,然后置于烘箱内进行高温固化,固化温度220℃,保温时间2.5小时。
54.实施例2
55.和实施例1的区别仅在于:
56.填充部雕刻步骤中:磁片厚度为40μm。
57.线圈层制作步骤中:热压温度控制在75
±
3℃,压力控制在8
±
1mpa,时间为5min。将第一填充部的材料放置于绝缘层所欲形成第一填充部的位置,其高度低于第一电极线圈20μm;将第二填充部的材料放置于绝缘层所欲形成第二填充部的位置,其高度低于第二电极线圈20μm。
58.第二次热压步骤中:热压温度控制在120℃,压力控制在20mpa,时间为10min。
59.等静压步骤中:温度70℃,保压时间为25min。
60.切割步骤中:固化温度200℃,保温时间3小时。
61.实施例3
62.和实施例1的区别仅在于:
63.填充部雕刻步骤中:磁片厚度为25μm。
64.线圈层制作步骤中:热压温度控制在70
±
3℃,压力控制在8
±
1mpa,时间7min。将第一填充部的材料放置于绝缘层所欲形成第一填充部的位置,其高度低于第一电极线圈35μm;将第二填充部的材料放置于绝缘层所欲形成第二填充部的位置,其高度低于第二电极线圈35μm。
65.第二次热压步骤中:热压温度控制在140℃,压力控制在20mpa,时间10min。
66.等静压步骤中:温度75℃,保压时间为22min。
67.切割步骤中:固化温度200℃,保温时间3小时。
68.实施例4
69.制作型号为121003(尺寸1.2
×
1.0
×
0.4mm)的薄膜电感,其中,第一基板层厚度为70~73μm;第一线圈层厚度为90μm;绝缘层(材料为聚酯膜)厚度为25μm,第二线圈层厚度为90μm;第二基板层厚度为70~73μm;胶层(材料为聚乙烯醇缩丁醛)厚度为4μm。
70.其制备工艺如下:
71.填充部雕刻步骤:取两张裁切好的厚度为93μm的磁片(磁片上另附带有100μm厚度的pet膜),利用激光雕刻机分别将磁片指定位置上材料去除,pet膜不打穿,两张磁片去除材料部分的图案分别与第一电极线圈及第二电极线圈图案一致,同时将压合时需要ccd对位的对位标记打出,得到第一填充部的材料及第二填充部的材料。其中,第一填充部及第二填充部的材料各自独立地包括94份的软磁合金(d50为5μm的铁硅铬,采用磷酸钝化包覆)、4份的热固性树脂(环氧改性硅树脂)及2份的热塑性树脂(丙烯酸树脂)。
72.线圈层制作步骤:通过胶层将第一电极线圈和第二电极线圈粘附在绝缘层的相对的两侧表面,形成预备线圈;将第一填充部的材料放置于绝缘层所欲形成第一填充部的位置,其高度超出第一电极线圈3μm;将第二填充部的材料放置于绝缘层所欲形成第二填充部的位置,其高度超出第二电极线圈3μm;得到待压线圈;对待压线圈进行第一次热压处理,形成线圈层;剥离第一填充部及第二填充部磁片附带的pet膜。其中,热压温度控制在75
±
3℃,压力控制在3
±
1mpa,时间为10min。在第一次热压处理后,第一电极线圈与第一填充部的远离第一基板层的表面齐平;第二电极线圈和第二填充部的远离第一基板层的表面齐平。
73.第二次热压步骤:将两片75μm厚的基板层磁片(材料成分和填充部完全一致)分别整齐置于已完成填充的线圈层上下两面,利用热压机进行第二次热压处理。其中,热压温度控制在150℃,压力控制在15mpa,时间为10min。
74.等静压步骤:将两次热压处理之后的中间产品装入塑封袋中进行真空塑封,然后将其置于等静压机中进行等静压处理,等静压压力为60mpa,温度为78℃,保压时间为15min。
75.切割步骤:等静压处理后,利用切割机将压合完成的整版半成品切割成单只产品,然后置于烘箱内进行高温固化,固化温度200℃,保温时间1.5小时。
76.实施例5
77.制作型号为201208(尺寸2.0
×
1.2
×
0.7mm)的薄膜电感,其中,第一基板层厚度为183~186μm;第一线圈层厚度为100μm;绝缘层(材料为聚酰亚胺)厚度为20μm,第二线圈层厚度为100μm;第二基板层厚度为183~186μm;胶层(材料为聚氨酯)厚度为5μm。
78.其制备工艺如下:
79.填充部雕刻步骤:取两张裁切好的厚度为105μm的磁片(磁片上另附带有100μm厚度的pet膜),利用激光雕刻机分别将磁片指定位置上材料去除,pet膜不打穿,两张磁片去除材料部分的图案分别与第一电极线圈及第二电极线圈图案一致,同时将压合时需要ccd对位的对位标记打出,得到第一填充部的材料及第二填充部的材料。其中,第一填充部及第二填充部的材料各自独立地包括90份的软磁合金(d50为5μm的非晶合金,采用磷酸钝化包
覆)、5.7份的热固性树脂(环氧树脂)及4份的热塑性树脂(聚乙烯醇缩丁醛树脂),0.21份的固化剂(间苯二甲胺)及0.09份的促进剂(2-甲基咪唑)。
80.线圈层制作步骤:通过胶层将第一电极线圈和第二电极线圈粘附在绝缘层的相对的两侧表面,形成预备线圈;将第一填充部的材料放置于绝缘层所欲形成第一填充部的位置,其高度超出第一电极线圈5μm;将第二填充部的材料放置于绝缘层所欲形成第二填充部的位置,其高度超出第二电极线圈5μm;得到待压线圈;对待压线圈进行第一次热压处理,形成线圈层;剥离第一填充部及第二填充部磁片附带的pet膜。其中,热压温度控制在80
±
3℃,压力控制在3
±
1mpa,时间为10min。在第一次热压处理后,第一电极线圈与第一填充部的远离第一基板层的表面齐平;第二电极线圈和第二填充部的远离第一基板层的表面齐平。
81.第二次热压步骤:将两片192μm厚的基板层磁片(材料成分和填充部完全一致)分别整齐置于已完成填充的线圈层上下两面,利用热压机进行第二次热压处理。其中,热压温度控制在150℃,压力控制在15mpa,时间为10min。
82.等静压步骤:将两次热压处理之后的中间产品装入塑封袋中进行真空塑封,然后将其置于等静压机中进行等静压处理,等静压压力为40mpa,温度为70℃,保压时间为25min。
83.切割步骤:等静压处理后,利用切割机将压合完成的整版半成品切割成单只产品,然后置于烘箱内进行高温固化,固化温度200℃,保温时间2.5小时。
84.对比例1
85.和实施例1的区别仅在于没有添加第一填充部及第二填充部。
86.性能表征:
87.(一)测试磁体强度
88.分别测试抗弯强度与跌落。
89.抗弯强度测试标准参考叠层电感可靠性测试标准,测试条件:弯曲2mm、加压速度0.5mm/s、保持时间30s,磁体不发生断裂,记为合格。
90.跌落实验条件:是产品从1m高度自由落体到混凝土地板上,产品不发生明显机械损伤,记为合格。
91.(二)分层测试
92.80倍工业显微镜下观察热固化之后的产品侧面是否存在分层(层间开裂)情况,检查数量80pcs,计算分层数。
93.性能结果如下表1所示:
94.表1
[0095] 磁体抗弯强度跌落试验分层数量/pcs实施例1合格合格0实施例2合格合格2实施例3合格合格16实施例4合格合格0实施例5合格合格0对比例1合格合格切割时中间区域分层严重
[0096]
由实施例1至5和对比例1的性能结果可知,本发明方案制作的薄膜电感磁体强度优异,在切割时,无严重的中间区域分层现象。
[0097]
尤其是,根据实施例1至3的数据可知,第一电极线圈与第一填充部的远离第一基板层的表面齐平;第二电极线圈和第二填充部的远离第一基板层的表面齐平。且第一电极线圈与第一表面接触的区域与第一区域完全重合,第一填充部设置在全部的第二区域;第二电极线圈与绝缘层表面接触的区域与第三区域完全重合,第二填充部设置在全部的第四区域。基于此,可以更有效地避免电感的分层现象,产品层间结合力更佳。
[0098]
以上仅为本发明的优选实施例而已,并不用于限制本发明,对于本领域的技术人员来说,本发明可以有各种更改和变化。凡在本发明的精神和原则之内,所作的任何修改、等同替换、改进等,均应包含在本发明的保护范围之内。