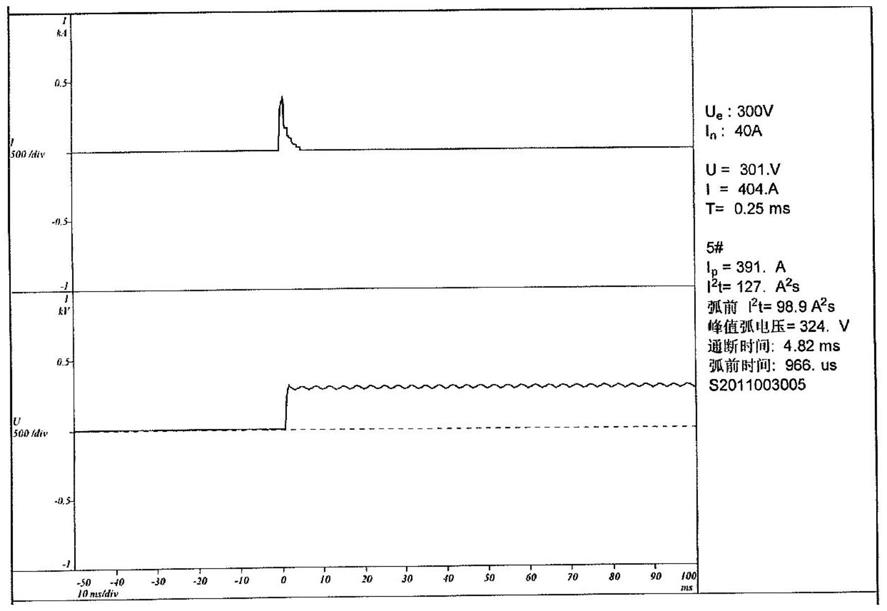
1.本发明涉及一种可用于管状熔断器灭弧的灭弧粉,特别涉及一种具有产气效果的灭弧粉,以及该种灭弧粉的制备方法。
背景技术:2.分断能力要达到dc300v400a及以上的表面贴装管状微型熔断器产品,其内部一般都需要填充灭弧材料,用以熄灭金属熔体在过电流熔断时所产生的电弧,并缓冲熔断瞬间产生的爆炸压力对熔断器外壳所带来的巨大冲击。
3.熔体在分断过程中除产生大量热能外,还会伴随出现两种形式的压力:熔体气化起弧瞬间产生脉冲形式的爆炸压力和整个燃弧期间产生的燃弧压力。常规的灭弧材料一般都可以在高温热流作用下,通过材料本身发生热解、熔化、蒸发、升华和侵蚀等物理和化学变化,在材料表面引起质量消耗来带走热量,从而降低熔体分断时产生的热能影响。但由于高温的存在,石英砂、硅胶、热固性树脂、玻璃涂层等常规灭弧材料往往没有对爆炸压力的弹性缓冲能力,灭弧部件产生的热解气体更会造成灭弧装置内部的压力升高,因而容易在持续飞弧时引起熔断器分断不良的发生。
4.现有低压熔断器在高电压和高分断能力下,通常使用高纯度石英砂作为灭弧材料,主要是因为石英砂具有较高的导热性和绝缘的性能,而且与电弧有很大的接触面积,因此便于吸收电弧能量,所以能够使电弧迅速冷却,确保熔断器能够安全分断短路电流。但是石英砂作为熔断器的填料存在如下问题:石英砂作为矿物质,受产地影响较大,铁等金属杂质难以去除;石英砂的表面粗糙,在熔断器组装时难以控制填充密度的均一度,进而影响分断效果;导热系数大,散热较快,使熔断器难以分断低倍过载。
5.同时,随着电子设备产品向着小型化、便携化发展,电路板空间缩小,分配给熔断器体积进一步缩小,同时熔断器需要实现贴片化,高耐压,大电流,高分断能力。因此需要研制一种新型的灭弧材料。
技术实现要素:6.发明目的:本发明的目的是提供一种新的产气灭弧粉,用以解决如何降低金属离子浓度及碰撞几率、产生消游离作用而快速熄灭电弧的技术问题。
7.本发明同时提供了上述灭弧粉的制备方法。
8.为达到上述目的,本发明灭弧粉采用如下技术方案:
9.一种产气灭弧粉,包括5wt%~30wt%的气相二氧化硅粉,10~20wt%的无机阻燃剂,20~40wt%的有机阻燃剂,30~40wt%的纳米孔结构三聚氰胺酚醛复合气凝胶,10~30wt%的硅酸盐。
10.进一步的,所述气相二氧化硅粉为目数为500~1000目。
11.进一步的,所述无机阻燃剂为al(oh)3或mg(oh)。
12.进一步的,所述硅酸盐为硅酸镁。
13.进一步的,所述有机阻燃剂为三聚氰胺改性脲醛树脂。
14.进一步的,所述纳米孔结构三聚氰胺酚醛复合气凝胶通过间苯二酚甲醛和三聚氰胺复合,然后通过乙醇溶剂置换和超临界干燥得到。
15.进一步的,该产气灭弧粉用以填充至管状熔断器的绝缘管内。
16.而上述产气灭弧粉的制备方法可采用以下技术方案:
17.包括如下步骤,
18.(1)物料称量:按配方比例称取所需质量的各种原材料以备用;
19.(2)气相二氧化硅粉体中无机阻燃剂的加入:将要求质量比的无机阻燃剂粉料与步骤1)得到的气相二氧化硅粉体在造粒机中混合造粒,使无机阻燃剂粉均匀包覆在气相二氧化硅粉体表面;
20.(3)硅酸盐的加入:将要求质量比的硅酸盐粉料与步骤(2)得到的包覆粉体在造粒机中混合造粒,使硅酸盐粉料均匀包覆在粉体表面;
21.(4)有机阻燃剂的加入:将要求质量比的有机阻燃剂粉料与步骤(3)得到的包覆粉体在造粒机中混合造粒,使有机阻燃剂粉料均匀包覆在粉体表面;
22.(5)纳米孔结构三聚氰胺酚醛复合气凝胶的加入:间苯二酚:甲醛:三聚氰胺:乙醇:酸按摩尔比1:3~4:0.02~0.2:10~12:0.06~0.08混合通过磁力搅拌并放置于烘箱内凝胶,均匀制备三聚氰胺掺杂间苯二酚
‑
甲醛溶胶,然后用玛瑙研钵磨成粉末状,通过筛网筛选出80~120目后将步骤(4)所获得的包覆粉体与其在造粒机中混合造粒,使得纳米孔结构三聚氰胺酚醛复合气凝胶均匀的包覆在粉体表面,获得球形灭弧材料;
23.(6)干燥烘烤:将步骤(5)所获得的球形灭弧材料放置干燥烘箱内烘烤一段时间后取出。
24.进一步的,步骤(5)中的纳米孔结构三聚氰胺酚醛复合气凝胶按照:间苯二酚:甲醛:三聚氰胺:乙醇:酸按摩尔比1:3:0.1:11:0.06。
25.进一步的,步骤(6)中干燥烘烤条件为:在125℃下烘烤20min或在100℃下烘烤30min。
26.有益效果:相对于现有技术,本发明提供的产气灭弧粉具有以下有益效果。
27.1、无毒无害,环保安全。该配方中的无机阻燃剂al(oh)3在燃烧时既不发烟也不生成腐蚀性或有毒性的气体,且成本低,是一种干净的阻燃剂。
28.2、快速熄弧。“三聚氰胺改性脲醛树脂+纳米孔结构三聚氰胺酚醛复合气凝胶+硅酸盐”为主晶相的高分断能力灭弧粉材料,所以在分断中电弧的高温灼烧下,氨基树脂不但能分解出大量的氢、氮、水蒸气、一氧化碳、二氧化碳等利于熄弧的气体,而且碳化轻。同时无机阻燃剂al(oh)3、mg(oh)2在电弧的高温灼烧下,在210℃~220℃开始产生水汽,同时和碳作用产生一氧化碳和氢气,这两个吸热反应起着冷却电弧、加速去游离作用,利于熄弧,并能把沉积在表面的碳去掉,生成co2气体和更容易熄灭电弧的h2。且增加产品内部压力,降低金属离子浓度及碰撞几率,产生消游离作用而快速熄灭电弧。
29.3、熄弧能力强。目前行业内灭弧材料能力多在dc250v 100a左右,随着电子设备产品向着小型化、便携化发展,电路板空间缩小,分配给熔断器体积进一步缩小,同时熔断器需要实现贴片化,高耐压,大电流,高分断能力。本发明所制备的产气灭弧材料分断能力可达dc300v 400a及以上。
附图说明
30.图1是现有技术中福建产100~200目石英砂外貌图;
31.图2是以现有技术中福建产100~200目石英砂作为填充材料,在dc300v400a测试出来的波形图;
32.图3是本发明100~200目产气灭弧材料的外貌图;
33.图4是以本发明实施例1所制100~200目产气灭弧材料作为填充材料,在dc300v400a测试出来的波形图。
具体实施方式
34.本发明提供一种产气灭弧粉
35.一种低导热系数灭弧粉,包括5wt%~30wt%的气相二氧化硅粉,10~20wt%的无机阻燃剂,20~40wt%的有机阻燃剂,30~40wt%的纳米孔结构三聚氰胺酚醛复合气凝胶,10~30wt%的硅酸盐。
36.所述气相二氧化硅粉为目数约500~1000目的微米级粉体,其主要特性为导热系数与空气相当;所述无机阻燃剂,如mg(oh)2、al(oh)3等,如al(oh)3在燃烧时既不发烟也不生成腐蚀性或有毒性的气体,且成本低,是一种干净的阻燃剂。al(oh)3在210℃~220℃就开始产生水蒸汽,如下式:
[0037][0038]
同时水蒸气和碳作用,生成一氧化碳和氢气,如下式:
[0039][0040]
这两个吸热反应起着冷却电弧、加速去游离作用,利于熄弧,并能把沉积在表面的碳去掉,生成co2气体和更容易熄灭电弧的h2。al(oh)3是惰性化合物,能形成良好的绝缘层,使产品绝缘电阻较快恢复。所述有机阻燃剂,如三聚氰胺、三聚氰胺改性脲醛树脂、氰尿酸三聚氰胺、有机硅等,如三聚氰胺改性脲醛树脂由脲素、三聚氰胺、甲醛共缩聚形成。从它们的分子结构来看,碳原子含量都较低,分别为12.5%、20%、22%。因此缩聚成的氨基树脂的碳原子含量也较低,氢和氮原子含量高,所以在电弧的高温灼烧下,氨基树脂不但能分解出大量的氢、氮、水蒸气、一氧化碳、二氧化碳等利于熄弧的气体,而且碳化轻;所述纳米孔结构三聚氰胺酚醛复合气凝胶通过rf(间苯二酚甲醛)和三聚氰胺复合,然后通过乙醇溶剂置换和超临界干燥得到。所述硅酸盐,如硅酸镁mg3〔si4o10〕(oh)2、硅酸铁、硅酸铝等,具有润滑性、抗黏、助流、耐火性、绝缘性、熔点高、化学性不活泼、遮盖力良好、柔软、光泽好、吸附力强等优良的物理特性。
[0041]
而上述产气灭弧粉的制备方法可采用以下技术方案:
[0042]
包括如下步骤,
[0043]
(1)物料称量:按配方比例称取所需质量的各种原材料以备用;
[0044]
(2)气相二氧化硅粉体中无机阻燃剂的加入:将要求质量比的无机阻燃剂粉料与步骤1)得到的气相二氧化硅粉体在造粒机中混合造粒,使无机阻燃剂粉均匀包覆在气相二氧化硅粉体表面;
[0045]
(3)硅酸盐的加入:将要求质量比的硅酸盐粉料与步骤(2)得到的包覆粉体在造粒机中混合造粒,使硅酸盐粉料均匀包覆在粉体表面;
[0046]
(4)有机阻燃剂的加入:将要求质量比的有机阻燃剂粉料与步骤(3)得到的包覆粉体在造粒机中混合造粒,使有机阻燃剂粉料均匀包覆在粉体表面;
[0047]
(5)纳米孔结构三聚氰胺酚醛复合气凝胶的加入:间苯二酚:甲醛:三聚氰胺:乙醇:酸按摩尔比1:3~4:0.02~0.2:10~12:0.06~0.08混合通过磁力搅拌并放置于烘箱内凝胶,均匀制备三聚氰胺掺杂间苯二酚
‑
甲醛溶胶,然后用玛瑙研钵磨成粉末状,通过筛网筛选出80~120目后将步骤(4)所获得的包覆粉体与其在造粒机中混合造粒,使得纳米孔结构三聚氰胺酚醛复合气凝胶均匀的包覆在粉体表面,获得球形灭弧材料;
[0048]
(6)干燥烘烤:将步骤(5)所获得的球形灭弧材料放置干燥烘箱内烘烤一段时间后取出。
[0049]
为通过具体实施例并结合试验结论说明本发明提供的产气灭弧粉的技术效果。
[0050]
实施例1:
[0051]
在一容器内称取质量比为气相二氧化硅粉:三聚氰胺改性脲醛树脂:硅酸镁=5wt%:25wt%:30wt%的配比边搅拌边加入到该容器内,随后倒入造粒机内进行造粒,并通过100~200目的筛网筛出后放置于另一干净容器内,得到半成品球形粉体1。随后按照步骤(4)加入质量比为半成品球形粉体1:al(oh)3=60wt%:10wt%的配比于盛半成品球形粉体1的容器内,用玻璃棒充分搅拌混合后,再次倒入造粒机内进行二次造粒后,并通过100~200目的筛网筛出后得到粉体2。然后将间苯二酚:甲醛:三聚氰胺:乙醇:酸按摩尔比1:3:0.1:11:0.06混合通过磁力搅拌并放置于烘箱内凝胶,均匀制备三聚氰胺掺杂间苯二酚
‑
甲醛(n
‑
rf)溶胶,然后用玛瑙研钵磨成粉末状,通过筛网筛选出80~120目的粉体3,称取其质量百分比为30wt%后,将粉体2和粉体3放置于造粒机内混合造粒,使得纳米孔结构三聚氰胺酚醛复合气凝胶粉末3均匀的包覆在粉体2表面,获得球形灭弧材料,并放置于托盘内。将其放入烘箱内进行在125℃下烘烤20min后,得到目数在100~200目的灭弧粉。
[0052]
以10mm*3.2mm尺寸、额定电流40a的表面贴装管状熔断器产品产品进行填充后分断能力试验,采用ag100%片材组装得到的产品,对所述填充本实施例配方灭弧粉的产品进行dc300v 400a的分断能力测试,可满足分断条件要求。测试波形图如图4所示。
[0053]
而作为一个对比例,以10mm*3.2mm尺寸、额定电流40a的表面贴装管状熔断器产品产品用现有技术中福建100~200目的石英砂填充后进行dc300v400a分断能力测试,不可满足该分断条件,熔断器管体炸裂,其测试波形图如图2所示。
[0054]
实施例2:
[0055]
在一容器内称取质量比为气相二氧化硅:三聚氰胺改性脲醛树脂:硅酸镁=10wt%:20wt%:20wt%的配比边搅拌边加入到该容器内,随后倒入造粒机内进行造粒,并通过100~200目的筛网筛出后放置于另一干净容器内,得到半成品球形粉体1。随后按照步骤(4)加入质量比为半成品球形粉体1:mg(oh)2=50wt%:15wt%的配比于盛半成品球形粉体1的容器内,用玻璃棒充分搅拌混合后,再次倒入造粒机内进行二次造粒后,并通过100~200目的筛网筛出后得到粉体2,然后将间苯二酚:甲醛:三聚氰胺:乙醇:酸按摩尔比1:4:0.08:10:0.07混合通过磁力搅拌并放置于烘箱内凝胶,均匀制备三聚氰胺掺杂间苯二酚
‑
甲醛(n
‑
rf)溶胶,然后用玛瑙研钵磨成粉末状,通过筛网筛选出100~120目的粉体3,称取
其质量百分比为35wt%后,将粉体2和粉体3放置于造粒机内混合造粒,使得纳米孔结构三聚氰胺酚醛复合气凝胶粉末3均匀的包覆在粉体2表面,获得球形灭弧材料,并放置于托盘内。将其放入烘箱内进行在100℃下烘烤30min后,得到目数在100~200目的灭弧粉。
[0056]
以10mm*3.2mm尺寸、额定电流40a的表面贴装管状熔断器产品进行填充后分断能力试验,采用ag100%片材组装得到的产品,对所述填充本实施例配方灭弧粉的产品进行dc300v 400a的分断能力测试,可满足分断条件要求。
[0057]
实施例3:
[0058]
在一容器内称取质量比为气相二氧化硅:三聚氰胺改性脲醛树脂:硅酸镁=15wt%:25wt%:10wt%的配比边搅拌边加入到该容器内,随后倒入造粒机内进行造粒,并通过100~200目的筛网筛出后放置于另一干净容器内,得到半成品球形粉体1。随后按照步骤(4)加入质量比为半成品球形粉体1:al(oh)3=50wt%:10wt%的配比于盛半成品球形粉体1的容器内,用玻璃棒充分搅拌混合后,再次倒入造粒机内进行二次造粒后,并通过100~200目的筛网筛出后得到粉体2,然后将间苯二酚:甲醛:三聚氰胺:乙醇:酸按摩尔比1:3.5:0.2:12:0.08混合通过磁力搅拌并放置于烘箱内凝胶,均匀制备三聚氰胺掺杂间苯二酚
‑
甲醛(n
‑
rf)溶胶,然后用玛瑙研钵磨成粉末状,通过筛网筛选出100~120目的粉体3,称取其质量百分比为40wt%后,将粉体2和粉体3放置于造粒机内混合造粒,使得纳米孔结构三聚氰胺酚醛复合气凝胶粉末3均匀的包覆在粉体2表面,获得球形灭弧材料,并放置于托盘内。将其放入烘箱内进行在125℃下烘烤20min后,得到目数在100~200目的灭弧粉。
[0059]
以10mm*3.2mm尺寸、额定电流40a的表面贴装管状熔断器产品产品进行填充后分断能力试验,采用ag100%片材组装得到的产品,对所述填充本实施例配方灭弧粉的产品进行dc300v 400a的分断能力测试,可满足分断条件要求。
[0060]
另外,本发明的具体实现方法和途径很多,以上所述仅是本发明的优选实施方式。应当指出,对于本技术领域的普通技术人员来说,在不脱离本发明原理的前提下,还可以做出若干改进和润饰,这些改进和润饰也应视为本发明的保护范围。