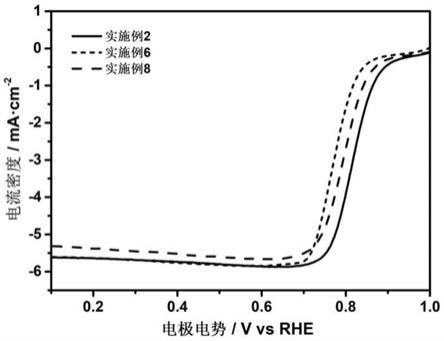
1.本发明涉及催化剂技术领域。更具体地,涉及一种催化剂前驱体、金属碳基催化剂及其制备方法和应用。
背景技术:2.能源危机和环境污染制约着全球的经济发展,然而,化石能源的广泛应用不但加剧了能源危机,而且还导致了世界范围内的环境污染和全球性气候变暖。在众多的可再生能源中,燃烧热值高、清洁无污染、来源广泛和适用范围较广的氢能源受到了各国的瞩目,对于全世界而言,开发氢能源将重新建立起一套高效能源体系,并且有效缓解世界共同面临的能源危机和气候问题。
3.用于氢能转换成电能的燃料电池是一类将化学能直接转换成电能的装置,可供其使用的“燃料”多样,不排放污染性气体,运行中噪声小,而且反应后只生成水,几乎不产生污染环境的含氮和硫氧化物。化学能转换成电能的反应步骤中不涉及燃烧过程,所以能量转换效率(高达60%~80%)不受卡诺循环的限制。目前人们将燃料电池投入到实际使用中,发现其可获得的能源效率是普通内燃机的2~3倍。
4.作为能源转换器件的质子交换膜燃料电池是目前发展最为成熟的燃料电池,其所具备的优势使之正在成为理想的可再生能源利用方式。质子交换膜燃料电池中起关键作用的氧还原反应受制于缓慢的动力学,因此需要高性能的催化剂降低其反应能垒。因此,迫切需要一种高效理想的氧还原催化剂,并应用于燃料电池使之表现出优异的性能。
5.目前,贵金属催化剂仍是再生能源技术和其他重要工业过程中应用最为广泛使用的催化剂。然而,贵金属催化剂具有多种缺点,例如资源匮乏、成本昂贵、稳定性较差、杂质中毒和燃料交叉效应、以及对环境具有不利影响。
6.过渡金属掺杂的碳基电催化剂因其具有更好的稳定性和抗甲醇中毒效应,被认为是最有希望取代贵金属催化剂的材料。其中单原子催化剂由于具有较高的本征活性和最大的原子利用效率,受到了最为广泛的关注。单原子催化剂的制备成本受到昂贵的实验设备要求和低生产效率的限制。因此,开发一种高效、可靠、环保、低成本的宏量制备非贵金属单原子或双原子催化剂的方法将在进一步的工业应用中具有重要意义。
7.因此,本发明提供了一种催化剂前驱体、金属碳基催化剂及其制备方法和应用。
技术实现要素:8.本发明的第一个目的在于提供一种催化剂前驱体。
9.本发明的第二个目的在于提供一种催化剂前驱体的制备方法。
10.本发明的第三个目的在于提供一种催化剂前驱体的应用。
11.本发明的第四个目的在于提供一种金属碳基催化剂。
12.本发明的第五个目的在于提供一种金属碳基催化剂的制备方法。
13.本发明的第六个目的在于提供一种金属碳基催化剂的应用。
14.为达到上述目的,本发明采用下述技术方案:
15.第一方面,本发明提供一种催化剂前驱体,所述催化剂前驱体为包括金属掺杂的沸石咪唑酯骨架材料和无机盐的混合物、或者为包括金属掺杂的沸石咪唑酯骨架材料和表面活性剂的混合物;其中,所述无机盐和金属掺杂的沸石咪唑酯骨架材料的质量比为2.70:0.67~5.40。
16.本发明提供的催化剂前驱体中,金属掺杂的沸石咪唑酯骨架材料的原子呈周期性排列,因此在使用该催化剂前驱体制备金属碳基催化剂过程中,由于锌元素的挥发,阻止了金属元素的团聚,金属元素和氮元素均匀地分布于材料中,且含量可控,这种对掺杂的调控有利于单原子活性位点或双原子活性位点的产生。
17.本发明提供的催化剂前驱体中,无机盐在制备金属碳基催化剂过程中,用作限域剂和蚀刻剂,利用无机盐在热解过程中起到的插层和剥离作用,使得生成的碳化物呈三维多孔状且边缘富含片状结构,产生更多的介孔,此外,结合金属掺杂的沸石咪唑酯骨架材料本身热分解会产生微孔结构的作用,使得获得的片状催化剂具有分级孔结构,具有更大的比表面积和孔隙率,改善了质量扩散性质,从而具有优异的催化活性和稳定性。
18.本发明提供的催化剂前驱体中,表面活性剂在制备金属碳基催化剂的过程中用作造孔剂,金属掺杂的沸石咪唑酯骨架材料在表面活性剂的作用下,构建出更多的孔结构,不仅增加了材料的比表面积和孔隙率,暴露出更多的单原子活性位点,而且有助于促进质子和电子的传输,有效提高了电催化性能;催化剂前驱体中不同的表面活性剂会对金属碳基催化剂的形成产生不同的作用,且有利于分析结构对氧还原性能的影响。
19.优选地,所述金属掺杂的沸石咪唑酯骨架材料中的金属为过渡金属;进一步地,所述过渡金属为铁。
20.优选地,所述无机盐为钠盐;进一步地,所述钠盐为氯化钠。
21.优选地,所述表面活性剂为p123。
22.第二方面,本发明提供一种催化剂前驱体的制备方法,包括如下步骤:
23.先将无机盐或表面活性剂进行球磨,然后再加入氧化锌、二甲基咪唑和含金属络合物溶液进行球磨,制得催化剂前驱体。
24.优选地,所述无机盐或表面活性剂、氧化锌、二甲基咪唑和含金属络合物溶液的质量比为700~900:60~90:150~170:40~60,进一步优选为800:81.38:164.2:50.72。
25.优选地,所述无机盐进行球磨的时间为20~60分钟。
26.优选地,所述加入氧化锌、二甲基咪唑和含金属络合物溶液进行球磨的时间为30~60分钟。
27.优选地,所述含金属络合物溶液中的含金属络合物为单金属络合物或多金属络合物。
28.优选地,所述单金属络合物通过摩尔比为1~3:6的铁盐a和邻菲罗啉络合而成。
29.优选地,所述铁盐a为醋酸亚铁。
30.优选地,所述双金属络合物通过摩尔比为3~5:1的铁盐b和钴盐络合而成。
31.优选地,所述铁盐b为乙酰丙酮铁。
32.优选地,所述钴盐为六水合硝酸钴。
33.优选地,所述含金属络合物溶液中的溶剂为无水乙醇。
34.优选地,所述催化剂前驱体的制备方法还包括将加入氧化锌、二甲基咪唑和含金属络合物溶液进行球磨后的球磨产物进行洗涤、干燥的步骤。
35.优选地,所述洗涤使用的洗涤剂为醇,进一步优选为乙醇;本发明中醇可以洗去多余的金属络合物;所述醇为甲醇或乙醇,其中乙醇比甲醇毒性更小,更适用于大规模制备合成催化剂前驱体。
36.优选地,所述干燥的条件为真空条件下干燥,干燥温度为70~90℃,干燥时间为12~24h;进一步地,所述干燥温度为80℃。
37.第三方面,本发明提供一种催化剂前驱体在制备金属碳基催化剂中的应用。
38.第四方面,本发明提供一种金属碳基催化剂,所述金属碳基催化剂通过将前述催化剂前驱体进行研磨,研磨产物置于惰性气氛中进行热解,然后将热解产物进行降温,降温过程中进行氨气处理制得。
39.优选地,所述金属碳基催化剂包括fe元素、n元素、o元素和c元素。
40.优选地,所述金属碳基催化剂中所述fe元素的占比为1.12at%,n元素的占比为8.7at%,o元素的占比为4.53at%,c元素的占比为85.66at%。
41.优选地,所述金属碳基催化剂呈三维多孔结构,且边缘为纳米片状结构。
42.优选地,所述金属碳基催化剂的比表面积为1200~1400m2g
‑1,进一步优选为1376.8m2g
‑1。
43.优选地,所述金属碳基催化剂的结构中介孔的占比为25~40%,进一步优选为30.47%。
44.优选地,所述金属碳基催化剂中的金属为铁。
45.第五方面,本发明提供一种金属碳基催化剂的制备方法,包括如下步骤:
46.将催化剂前驱体进行研磨,研磨产物置于惰性气氛中进行热解,然后将热解产物进行降温,降温过程中使用氨气进行处理,制得金属碳基催化剂。
47.优选地,所述催化剂前驱体进行研磨的时间为20~30min。
48.优选地,所述惰性气氛使用的惰性气体为氮气或氩气,其纯度≥99.999%(v/v)。
49.优选地,所述热解使用的设备为高温管式炉。
50.优选地,所述热解过程包括:以2~10℃/min的速率先升温至200~400℃,保温0.5~2h;然后以2~10℃/min的速率升温至800~1100℃,保温2~4h。
51.优选地,所述降温的过程包括:以2~10℃/min的速率降温至700~900℃,保温5~10min,停止通入惰性气体,并同时以60~80ml/min的速率通入氨气,保温5~20min结束,停止通入氨气并同时以60~150ml/min的速率通入惰性气体,自动降温到常温。
52.优选地,所述热解产物进行降温后获得的产物还需要经过洗涤、过滤和干燥的步骤;其中,所述洗涤为使用去离子水超声洗涤30~60min,从而除去多余无机盐或者其他杂质;所述过滤为抽滤3~6小时;所述干燥为真空条件下干燥10~16小时。
53.第六方面,本发明提供一种金属碳基催化剂在制备锌空电池或燃料电池中的应用。
54.另外,如无特殊说明,本发明所记载的任何范围包括端值以及端值之间的任何数值以及端值或者端值之间的任意数值所构成的任意子范围。
55.本发明的有益效果如下:
56.(1)本发明提供的催化剂前驱体中的组分相互配合,在金属碳基催化剂的制备过程中产生协同作用,从而令制得的金属碳基催化剂具有片状结构、较高的比表面积、产生了丰富的纳米孔和缺陷活性中心,而且暴露出更多的活性位点。
57.(2)本发明提供的催化剂前驱体的制备方法采用一步球磨法,可宏量制备,过程简单,不易引入其他杂质,有利于调控金属掺杂的沸石咪唑酯骨架材料中掺杂金属元素的分布和含量。
58.(3)本发明提供的金属碳基催化剂呈三维多孔结构,且边缘为纳米片状结构,拥有较大的比表面积。
59.(4)本发明提供的金属碳基催化剂的制备方法,采用本发明提供的催化剂前驱体进行制备,改善了金属碳基催化剂的质量扩散性质,令其具有优异的催化活性和稳定性。
60.(5)本发明提供的金属碳基催化剂的制备方法步骤简单、原料易得、成本低廉,绿色友好,易于放大生产。
61.(6)本发明提供的金属碳基催化剂具有突出的氧还原催化性能,抗甲醇能力和杰出的稳定性,同时在氢氧燃料电池、可再生燃料电池设备中表现出良好的性能,具有广泛的应用前景。
62.(7)本发明采用简便的合成方法制备了单金属原子掺杂的氧还原碳基催化剂,为宏量制备单原子氧还原催化剂提供了一种新的思路,也为构建高效电催化剂提供了新的方案,可为开发可再生能源转换和储存设备开辟新的途径。
附图说明
63.下面结合附图对本发明的具体实施方式作进一步详细的说明。
64.图1示出实施例2、实施例6和实施例8制得的金属碳基催化剂在0.1m hclo4下的氧还原反应的线性扫描伏安图。
65.图2示出实施例2制得的金属碳基催化剂的扫描电镜图。
66.图3示出实施例2制得的金属碳基催化剂的透射电镜图。
67.图4示出实施例2制得的金属碳基催化剂的高角度环形暗场像。
68.图5示出实施例2制得的金属碳基催化剂25000s电流
‑
时间稳定性曲线图。
69.图6示出实施例2制得的金属碳基催化剂应用于h2/o2燃料电池的放电极化曲线和功率密度曲线。
70.图7示出实施例1制得的催化剂前驱体的产物图。
71.图8示出实施例2制得的金属碳基催化剂的产物图。
72.图9示出实施例6制得的金属碳基催化剂的扫描电镜图。
具体实施方式
73.为了更清楚地说明本发明,下面结合优选实施例对本发明做进一步的说明。本领域技术人员应当理解,下面所具体描述的内容是说明性的而非限制性的,不应以此限制本发明的保护范围。
74.本发明中,制备方法如无特殊说明则均为常规方法;所用的原料如无特别说明均可从公开的商业途径获得;所述百分比如无特殊说明均为质量百分比。
75.下面,通过实施例对本发明的内容做进一步的说明。
76.实施例1
77.本实施例提供了一种催化剂前驱体的制备方法,包括如下步骤:
78.1)在球磨罐中加入800g氯化钠,然后在400rpm的转速下球磨30分钟;
79.2)将12.34g醋酸亚铁(fe(ac)2)和38.38g邻菲罗啉(摩尔比为1:3)溶于200ml乙醇中,超声30分钟形成含金属络合物溶液;
80.3)向球磨罐中加入81.38g氧化锌,164.2g 2
‑
甲基咪唑以及步骤2)制得的含金属络合物溶液,并在球磨机中球磨60分钟得到产物,将该产物转移至过滤装置中,用30l乙醇过滤洗涤,直到上清液变成无色,然后在80℃真空干燥箱中干燥24小时,得到催化剂前驱体,如图7。
81.实施例2
82.本实施例提供了一种金属碳基催化剂的制备方法,包括如下步骤:
83.1)将实施例1制得的1000g催化剂前驱体用研钵研磨30分钟形成粉末,放入瓷舟中,把瓷舟放入石英管中,于高温管式炉中进行热解;在热解过程中,通入流量为100ml/min的氩气≥99.999%(v/v),高温管式炉以3℃/min的速率升温至250℃并保持在该温度下热解1小时,然后以5℃/min的升温速率将温度进一步提高到900℃,并在这个热解温度下保温3小时,整个热解过程在氩气气氛保护下进行;
84.2)热解过程完成后进行降温,温度降至800℃时,关闭氩气,通入流量为70ml/min的氨气,并使得管式炉在800℃下保温8分钟,自然降温得到产物,将该产物转移至烧瓶中,加入1000ml的去离子水,超声50分钟,过滤洗涤,然后在80℃真空干燥箱中干燥24小时,得到金属碳基催化剂,如图8。
85.图2示出实施例2制得的金属碳基催化剂的扫描电镜图。在典型的扫描电镜示意图2中可以看到,实施例2制得的金属碳基催化剂含有明显的片状结构,除去某些区域的大规模片状结构,其他区域形成的三维多孔结构中,材料的外边缘都呈片状,某些片状发生了卷曲现象。这些片状结构相互连接组成了连续多孔的三维结构。在大规模连续片状结构中,也能清晰看到大量大孔的存在。
86.图3示出实施例2制得的金属碳基催化剂的透射电镜图,可以看到该金属碳基催化剂边缘呈超薄片状结构(电镜图非常透明),与扫描电镜的表征结果相符。
87.图4示出实施例2制得的金属碳基催化剂的高角度环形暗场像。白色圆圈圈出来的亮点对应于高度分散的单铁原子,因为铁原子比碳和氮原子重。且粒径大约为0.2纳米。
88.实施例3
89.本实施例提供了一种金属碳基催化剂的氧化原反应,包括如下步骤:
90.电化学测试在室温下使用电化学工作站(autolab)在三电极体系下进行。石墨棒和ag/agcl(kcl
‑
饱和)电极分别被用作对电极和参比电极,工作电极为玻碳旋转圆盘电极(面积为0.196cm2)。用0.05μm氧化铝浆抛光玻碳旋转圆盘电极,然后用超纯水冲洗。每次试验中,将5mg实施例2、实施例6和实施例8制得的金属碳基催化剂分别与10μl nafion溶液(5wt%)、495μl异丙醇和495μl超纯水混合,然后超声分散约30分钟,形成均匀油墨,分次共取20μl油墨滴在旋转圆盘电极表面并在环境条件下干燥。金属碳基催化剂的质量负载在0.5mg cm
‑2。在氧气饱和的0.1mhclo4中进行线性扫描伏安(lsv)测试。测试过程中,持续往
电解液中通入高纯氧气,使之保持氧气饱和的状态,扫描速率为5mv s
‑1,旋转速率为1600转,从1.0v扫描到0v(相对可逆氢电极),测试了金属碳基催化剂的氧还原性能。
91.图1示出实施例2、实施例6和实施例8制得的金属碳基催化剂在0.1m hclo4下的氧还原反应的线性扫描伏安图。测试得出实施例2制得的金属碳基催化剂其起始电位为0.951v,半波电位为0.820v,极限电流密度为5.68ma/cm2。实施例6制得的金属碳基催化剂其起始电位为0.912v,半波电位为0.775v,极限电流密度为5.67ma/cm2。实施例8制得的金属碳基催化剂其起始电位为0.932v,半波电位为0.801v,极限电流密度为5.32ma/cm2。
92.图5示出实施例2制得的金属碳基催化剂25000s电流
‑
时间稳定性曲线图。经过25000s的电流
‑
时间稳定性测试性能损失率仅有6%,可见制得的金属碳基催化剂具有优异的稳定性。
93.实施例4
94.本实施例提供了一种金属碳基催化剂在h2/o2燃料电池中的应用,包括如下步骤:
95.h2/o2燃料电池测试在具有直接平行流动通道的单电池燃料电池中进行。在每次测试中,将实施例2制得的金属碳基催化剂分散入水和异丙醇(1:8v/v)的溶液中,超声分散制备成均匀的催化剂油墨,然后用喷枪将催化剂油墨喷到nc700膜的一侧,制造的膜电极面积为5cm
‑2,形成催化剂负载为~2mg cm
‑2的催化剂涂层膜(ccm),并作为阴极。采用相同工艺在另一侧使用40%商用铂碳催化剂制备的催化剂涂层膜(~0.20mg
pt cm
‑2)作为阳极。将膜电极组装入燃料电池,然后在80℃,100%相对湿度(rh)和2.0bar的背压下评估由此制备的膜电极组件。500ml min
‑1的纯氢气和500ml min
‑1的纯氧气在测试过程中分别持续供给阳极和阴极。在电压控制模式下记录了燃料电池的极化曲线。
96.图6示出实施例2制得的金属碳基催化剂应用于h2/o2燃料电池的放电极化曲线和功率密度曲线。将实施例2制得的金属碳基催化剂组装成膜电极测试其在质子膜氢氧燃料电池中应用的实际性能,阳极hor催化剂为40%pt/c,负载量为1mg/cm2,采用质子膜为杜邦212膜,80℃,氢气流量为0.2l/min,氧气流量为0.2l/min,相对湿度100%。在2个大气压的背压下,其燃料电池开路电压为1.0v,最大功率为610mw/cm2。
97.实施例5
98.本实施例提供了一种催化剂前驱体的制备方法,包括如下步骤:
99.1)将12.34g醋酸亚铁(fe(ac)2)和38.38g邻菲罗啉(摩尔比为1:3)溶于200ml乙醇中,加入74.0g聚环氧乙烷
‑
聚环氧丙烷
‑
聚环氧乙烷三嵌段共聚物(p123),超声30分钟形成含金属络合物溶液;
100.2)向球磨罐中加入81.38g氧化锌,164.2g 2
‑
甲基咪唑以及步骤1)制得的含金属络合物溶液,并在球磨机中球磨60分钟得到产物,将该产物转移至过滤装置中,用30l乙醇过滤洗涤,直到上清液变成无色,然后在80℃真空干燥箱中干燥24小时,得到催化剂前驱体。
101.实施例6
102.本实施例提供了一种金属碳基催化剂的制备方法,包括如下步骤:
103.1)将实施例5制得的1000g催化剂前驱体用研钵研磨30分钟形成粉末,放入瓷舟中,把瓷舟放入石英管中,于高温管式炉中进行热解;在热解过程中,通入流量为100ml/min的氩气≥99.999%(v/v),高温管式炉以3℃/min的速率升温至250℃并保持在该温度下热
解1小时,然后以5℃/min的升温速率将温度进一步提高到900℃,并在这个热解温度下保温3小时,整个热解过程在氩气气氛保护下进行;
104.2)热解过程完成后进行降温,温度降至800℃时,关闭氩气,通入流量为70ml/min的氨气,并使得管式炉在800℃下保温8分钟,自然降温得到产物,将该产物转移至烧瓶中,加入1000ml的去离子水,超声50分钟,过滤洗涤,然后在80℃真空干燥箱中干燥24小时,得到金属碳基催化剂。
105.图9示出实施例6制得的金属碳基催化剂的扫描电镜图,催化剂呈颗粒状,含有明显的zif
‑
8的正十二面体形貌。
106.实施例7
107.本实施例提供了一种催化剂前驱体的制备方法,包括如下步骤:
108.1)在球磨罐中加入800g氯化钠,然后在400rpm的转速下球磨30分钟;
109.2)将24.08g乙酰丙酮铁和4.96g六水合硝酸钴(摩尔比为4:1)溶于100ml乙醇中,超声30分钟形成含金属络合物溶液;
110.3)向球磨罐中加入20.80g氧化锌,164.2g 2
‑
甲基咪唑以及步骤2)制得的含金属络合物溶液,并在球磨机中球磨60分钟得到产物,将该产物转移至过滤装置中,用30l乙醇过滤洗涤,直到上清液变成无色,然后在80℃真空干燥箱中干燥24小时,得到催化剂前驱体。
111.实施例8
112.本实施例提供了一种金属碳基催化剂的制备方法,包括如下步骤:
113.1)将实施例7制得的1000g催化剂前驱体用研钵研磨30分钟形成粉末,放入瓷舟中,把瓷舟放入石英管中,于高温管式炉中进行热解;在热解过程中,通入流量为100ml/min的氩气≥99.999%(v/v),高温管式炉以5℃/min的速率升温至950℃并保持在该温度下热解2小时,然后以5℃/min的升温速率将温度进一步提高到900℃,并在这个热解温度下保温3小时,整个热解过程在氩气气氛保护下进行;
114.2)热解过程完成后进行降温,温度降至800℃时,关闭氩气,通入流量为70ml/min的氨气,并使得管式炉在800℃下保温8分钟,自然降温得到产物,将该产物转移至烧瓶中,加入1000ml的去离子水,超声50分钟,过滤洗涤,然后在80℃真空干燥箱中干燥24小时,得到金属碳基催化剂。
115.显然,本发明的上述实施例仅仅是为清楚地说明本发明所作的举例,而并非是对本发明的实施方式的限定,对于所属领域的普通技术人员来说,在上述说明的基础上还可以做出其它不同形式的变化或变动,这里无法对所有的实施方式予以穷举,凡是属于本发明的技术方案所引伸出的显而易见的变化或变动仍处于本发明的保护范围之列。