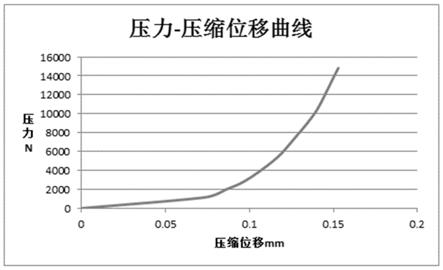
1.本发明属于动力电池技术领域,尤其是涉及一种模组膨胀安全评估方法。
背景技术:2.软包锂离子电池具有能量密度高、安全性好、制造工艺简单等优点,但是在模块化组成电池包时难度较大。电池体积膨胀是主要的难点之一。锂离子电池在充电过程中锂离子不断嵌入负极材料,使得碳负极材料发生膨胀,导致电池体积有一定程度的膨胀。因此在进行模块设计时需要考虑使模块结构具备容纳此膨胀的能力。在动力电池包结构中如果不采用压力或者该压力太小,则电池在随车体振动时容易被损坏。该压力太大则对电池的寿命会产生负面影响,甚至直接损坏电池使其报废。锂电池中碳负极材料中应力分布在制造过程和循环过程中都是不均匀的,该不可逆的应力在循环过程仍在产生和积累,这不仅导致负极厚度膨胀,而且导致石墨颗粒破裂甚至降解。软包电池中堆叠应力是动态量,随着充电/放电波动,并且随着长时间的循环不可逆地逐渐增加。小的堆叠压力能防止层与层脱开,对电池长期寿命有利。
3.目前已有的研究主要是电池内部的力学特性,对于电池包成组的力学研究十分稀少。常见的软包锂电池模块结构中,平板状锂电池是层层叠置的。现有的电池厂商一般仅会从固定模快和电池拼接的角度来设计安装电池包,几乎没有研究甚至考虑电池包外围结构的力学变化对电池寿命的影响。
技术实现要素:4.有鉴于此,本发明旨在提出一种模组膨胀安全评估方法,以提供一种兼顾模组内外因素的高精度模组膨胀安全评估方法。
5.为达到上述目的,本发明的技术方案是这样实现的:
6.一种模组膨胀安全评估方法,包括如下步骤:
7.s1、通过电池膨胀力测试设备对电芯进行压缩,并记录电芯的压缩位移和压力的关系;
8.s2、测量电芯的膨胀力和对应位移,确定电芯膨胀刚度;
9.s3、通过电池膨胀力测试设备对泡棉进行压缩,并记录泡棉的压缩位移和压力的关系;
10.s4、确定模组框架弹性极限承载力和位移;
11.s5、根据步骤s1至步骤s4各步骤中的数据,制定软包模组膨胀设计准则,并对模组膨胀进行评估。
12.进一步的,所述步骤s1通过实验测试可以得出:电芯压缩位移在0.1mm以下时,压力值增加比较平缓,超过0.1mm后,压力值增加比较快。
13.进一步的,所述步骤s2的具体方法为:
14.s21、测量电芯自由状态不同的soc厚度;
15.s22、0%soc电芯固定厚度约束,测量充电100%soc膨胀力。
16.进一步的,所述步骤s3通过实验测试可以得出:泡棉压缩位移在1.4mm以下时,压力值增加比较平缓,超过1.4mm后,压力值增加比较快。
17.进一步的,所述步骤s4的具体方法为:利用大型通用有限元分析软件模块对模组框架结构的3d数模进行合理简化后得到有限元分析可用的几何结构,并根据几何结构大小采用网格划分技术对其进行网格划分,以便于得到高精度的有限元分析模型,并进行边界条件、求解器参数设置后进行求解,对结果进行后处理,确定模组框架弹性极限承载力和位移。
18.进一步的,在所述步骤s5中,软包模组膨胀设计准则为:
19.s51、电芯弹性段极限压缩位移+泡棉弹性段极限压缩位移+框架弹性极限位移大于电芯eol膨胀位移;
20.s52、模组膨胀力小于框架弹性极限承载力;
21.s53、电芯充/放电过程中,保证泡棉一直处于压缩状态。
22.相对于现有技术,本发明所述的模组膨胀安全评估方法具有以下优势:
23.(1)本发明所述的模组膨胀安全评估方法,在模组膨胀安全评估中考虑了电芯压缩、泡棉压缩、框架膨胀位移、装配过程、电芯充放电呼吸过程、循环膨胀过程,大大提高了评估的精确度。
附图说明
24.构成本发明的一部分的附图用来提供对本发明的进一步理解,本发明的示意性实施例及其说明用于解释本发明,并不构成对本发明的不当限定。在附图中:
25.图1为本发明实施例所述的电芯的压力
‑
压缩位移曲线图;
26.图2为本发明实施例所述的泡棉的压力
‑
压缩位移曲线图;
27.图3为本发明实施例所述的模组框架的几何模型;
28.图4为本发明实施例所述的模组框架的边界条件;
29.图5为本发明实施例所述的模组框架的应力仿真结果;
30.图6为本发明实施例所述的模组框架的位移仿真结果。
具体实施方式
31.需要说明的是,在不冲突的情况下,本发明中的实施例及实施例中的特征可以相互组合。
32.在本发明的描述中,需要理解的是,术语“中心”、“纵向”、“横向”、“上”、“下”、“前”、“后”、“左”、“右”、“竖直”、“水平”、“顶”、“底”、“内”、“外”等指示的方位或位置关系为基于附图所示的方位或位置关系,仅是为了便于描述本发明和简化描述,而不是指示或暗示所指的装置或元件必须具有特定的方位、以特定的方位构造和操作,因此不能理解为对本发明的限制。此外,术语“第一”、“第二”等仅用于描述目的,而不能理解为指示或暗示相对重要性或者隐含指明所指示的技术特征的数量。由此,限定有“第一”、“第二”等的特征可以明示或者隐含地包括一个或者更多个该特征。在本发明的描述中,除非另有说明,“多个”的含义是两个或两个以上。
33.在本发明的描述中,需要说明的是,除非另有明确的规定和限定,术语“安装”、“相连”、“连接”应做广义理解,例如,可以是固定连接,也可以是可拆卸连接,或一体地连接;可以是机械连接,也可以是电连接;可以是直接相连,也可以通过中间媒介间接相连,可以是两个元件内部的连通。对于本领域的普通技术人员而言,可以通过具体情况理解上述术语在本发明中的具体含义。
34.下面将参考附图并结合实施例来详细说明本发明。
35.模组eol:一种测试系统。
36.一种模组膨胀安全评估方法,如图1至图6所示,包括步骤:
37.s1、通过电池膨胀力测试设备对电芯进行压缩,并记录压缩位移和压力的关系,如表1所示,并根据表1得出压力
‑
压缩位移曲线图,如图1所示。
38.电池膨胀力测试设备为可施加预紧力的电池膨胀力测试设备,电池单体放置到测试工装中,施加一定预紧力后,对电池单体进行充放电测试,在实验过程中显示、记录、存储电池单体产生的膨胀力、循环次数、充放电循环状态、循环时间试验参数等。可实现:(1)恒力下测量电芯循环膨胀位移。(2)恒位移下测量电芯循环膨胀力。优选的,电池膨胀力测试设备为中创试验机。
39.表1电芯压力
‑
压缩位移数据表
40.压缩位移mm压力n000.073511500.085919700.09627500.106139100.113849500.119558700.124268400.127675500.131984700.136695200.141106700.1471127800.1491135300.152814810
41.通过实验测试可以得出:电芯压缩位移在0.1mm以下时,压力值增加比较平缓,超过0.1mm后,压力值增加比较快。(电芯弹性压缩极限取0.1mm)
42.s2、确定电芯膨胀刚度;
43.s21、测量电芯自由状态不同的soc厚度,如表2所示;
44.s22、0%soc电芯固定厚度约束,测量充电100%soc膨胀力,如表3所示。
45.表2电芯自由状态不同的soc厚度
[0046][0047]
表3
[0048][0049]
通过实验测试可以看出:
[0050]
电芯膨胀刚度=膨胀力/对应位移(100%厚度
‑
0%厚度),
[0051]
ꢀꢀꢀꢀꢀꢀꢀꢀꢀꢀꢀꢀ
=13.445*1000/(14.6
‑
14.1)
[0052]
ꢀꢀꢀꢀꢀꢀꢀꢀꢀꢀꢀꢀ
=26890n/mm
[0053]
s3、通过电池膨胀力测试设备对泡棉进行压缩,并记录压缩位移和压力的关系,如表4所示,并根据表4得出压力
‑
压缩位移曲线图,如图2所示。
[0054]
表4电芯压力
‑
压缩位移数据表
[0055]
泡棉压力
‑
压缩位移曲线
[0056][0057][0058]
通过实验测试可以看出:
[0059]
泡棉压缩位移在1.4mm(70%压缩量)以下时,压力值增加比较平缓,超过1.4mm后,压力值增加比较快。(泡棉弹性压缩极限取1.4mm)。
[0060]
泡棉弹性刚度=弹性压力/压缩位移
[0061]
ꢀꢀꢀꢀꢀꢀꢀꢀꢀꢀꢀꢀ
=5390/1.4346
[0062]
ꢀꢀꢀꢀꢀꢀꢀꢀꢀꢀꢀꢀ
=3757n/mm
[0063]
s4、确定模组框架弹性极限承载力和位移;
[0064]
如图3至图6所示,利用大型通用有限元分析软件ansys workbench模块对模组框架结构的3d数模进行合理简化后得到有限元分析可用的几何结构,并根据几何结构大小采用适当的网格划分技术对其进行网格划分,以便于得到高精度的有限元分析模型,并进行边界条件、求解器等参数设置后进行求解,并对结果进行后处理,确定模组框架弹性极限承载力和位移。
[0065]
如图3所示,利用大型通用有限元分析软件ansys workbench模块对模组框架结构的3d数模进行合理简化后得到有限元分析可用的几何模型;如图4所示,设置模型的边界条件,在模组两侧端板各施加25000n鼓胀力;仿真结果如图5和图6所示,其中图5为应力分析结果,图6为位移分析结果。
[0066]
从仿真计算结果可以看出,在满足材料屈服强度(158mpa)条件下,模组框架单侧可承受25000n弹性极限力,膨胀单侧位移0.21mm。
[0067]
s5、对模组膨胀进行评估
[0068]
模组,结构上一个模组的电芯对应一块泡棉。
[0069]
在一个实施例中,采用的模组型号为2p28s,共56个电芯;泡棉厚度为2mm,一个电芯对应一块泡棉,共56块泡棉。
[0070]
s51、电芯弹性段极限压缩位移+泡棉弹性段极限压缩位移+框架弹性极限位移大于电芯eol膨胀位移。
[0071]
根据步骤s1至步骤s4的实验数据确定:
[0072]
单个电芯弹性极限压缩位移0.1mm,56个电芯弹性极限压缩位移0.1*56=5.6mm
[0073]
单个泡棉弹性极限压缩位移1.4mm,56个泡棉弹性极限压缩位移1.4*56=78.4mm
[0074]
模组框架弹性极限位移0.21mm
[0075]
电芯弹性段极限压缩位移+泡棉弹性段极限压缩位移+框架弹性极限位移=5.6+78.4+0.21=84.21mm
[0076]
如果单个电芯预估eol膨胀位移<1.5mm,56个电芯预估eol膨胀位移<1.5*56=84mm
[0077]
结论:
[0078]
模组预估eol膨胀位移84mm<(电芯弹性段极限压缩位移+泡棉弹性段极限压缩位移+框架弹性极限位移=84.21mm),因此模组结构是安全可靠的。
[0079]
s52、模组膨胀力小于框架弹性极限承载力。
[0080]
单个电芯预估eol膨胀位移1.5mm
[0081]
泡棉弹性压缩极限取1.4mm,即泡棉吸收1.4mm位移,
[0082]
泡棉弹性刚度=弹性压力/压缩位移
[0083]
ꢀꢀꢀꢀꢀꢀꢀꢀꢀꢀꢀꢀ
=5390/1.4346
[0084]
ꢀꢀꢀꢀꢀꢀꢀꢀꢀꢀꢀꢀ
=3757n/mm
[0085]
泡棉压缩膨胀力=泡棉刚度*泡棉压缩位移=3757*1.4=5260n。
[0086]
电芯膨胀刚度=膨胀力/对应位移(100%厚度
‑
0%厚度),
[0087]
ꢀꢀꢀꢀꢀꢀꢀꢀꢀꢀꢀꢀ
=13.445*1000/(14.6
‑
14.1)
[0088]
ꢀꢀꢀꢀꢀꢀꢀꢀꢀꢀꢀꢀ
=26890n/mm
[0089]
电芯膨胀力=电芯膨胀刚度*(电芯预估膨胀位移
‑
泡棉压缩位移)=26890*(1.5
‑
1.4)=2689n
[0090]
模组膨胀力=泡棉压缩膨胀力+电芯膨胀力=3757+2689=6446n
[0091]
根据仿真结果可以得出,模组框架弹性极限承载力25000n。
[0092]
结论:
[0093]
模组eol膨胀力6446n小于模组框架弹性极限承载里力25000n,因此结构是安全可靠的。
[0094]
s53、电芯充/放电过程中,保证泡棉一直处于压缩状态
[0095]
模组初装力=泡棉刚度*对应位移(30%soc厚度
‑
0%soc厚度),
[0096]
ꢀꢀꢀꢀꢀꢀꢀꢀꢀꢀ
=3757*(14.3
‑
14.1)
[0097]
ꢀꢀꢀꢀꢀꢀꢀꢀꢀꢀ
=751n
[0098]
本方案在模组膨胀安全评估中考虑了电芯压缩、泡棉压缩、框架膨胀位移、装配过程、电芯充放电呼吸过程、循环膨胀过程,大大提高了评估的精确度。
[0099]
以上所述仅为本发明的较佳实施例而已,并不用以限制本发明,凡在本发明的精神和原则之内,所作的任何修改、等同替换、改进等,均应包含在本发明的保护范围之内。