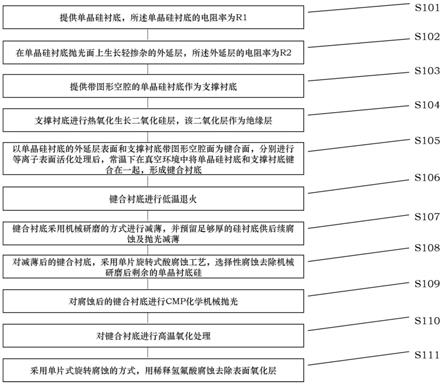
1.本发明涉及集成电路材料的制备方法,尤其涉及带空腔的绝缘体上硅衬底的制备工艺。
背景技术:2.绝缘衬底上的硅技术(silicon
‑
on
‑
insulator)soi是在顶层器件硅和支撑衬底之间引入了一层作为绝缘层的埋氧化层。绝缘体上的硅材料具有了体硅所无法比拟的优点:可以实现集成电路中元器件的物理上的完全隔离,彻底消除了体硅cmos电路中的寄生闩锁效应;减小了寄生电容,在功耗,运行速度,抗辐照以及器件集成度方面具有明显的优势。
3.soi材料在mems(微机电系统)中的应用也越来越广泛;随着mems技术的发展,带cavity图形化空腔的绝缘体上硅衬底材料在压力传感器,陀螺仪,麦克风,超声探头等mems器件上得到越来越多的应用。采用besoi键合减薄技术制备带空腔的绝缘体上硅soi材料时,会在键合之前,对作为支撑的衬底硅片会进行光刻及刻蚀工艺,在支撑硅表面形成了图形化的一些结构空腔,这些空腔的尺寸大小从几微米到上百微米不等,空腔的深度也从几微米到上百微米不等。因为这些空腔的存在,使得在制备绝缘体上硅衬底的过程中,支撑衬底与器件硅衬底的接触面积大大减小,仅靠非图形空腔区的一些侧墙硅与器件硅衬底键合在一起,空腔区上部的器件硅呈悬空状态。键合之后在进行减薄时,这些悬空状态下的器件硅,容易被机械研磨过程的应力造成损伤,以及研磨设备中的厚度实时监控的传感器压杆下压之下产生损伤,这些损伤无法被修复,严重的会直接导致器件硅层磨损以及整个硅片的碎片风险。机械研磨的减薄过程中,当器件层厚度越薄时,这些损伤会越严重。一般来说,当器件硅层厚度小于10um时,机械研磨就非常容易导致器件层的破损,所以在常规besoi键合减薄工艺方式制备带空腔的绝缘体上硅衬底时,很难突破器件层10μm的限制,且因为固有的抛光工艺能力限制,无法保证器件层厚度的良好的均匀性;因此对于一些薄膜器件层的带空腔绝缘体上硅衬底,需要采用新的制备工艺。同时,键合过程如果在常压下进行,则空气会被包裹在空腔中,在后续的高温热处理过程中,这些空气会膨胀撑开键合界面从而影响键合强度,更严重的会导致空腔上部的器件层硅破损,造成器件失效。
4.针对带空腔的绝缘体上硅衬底,我们提出了基于外延工艺及真空键合工艺,结合选择性腐蚀和抛光加氧化减薄工艺,开发出了适用于支撑体带空腔的薄膜器件层绝缘体上硅材料的制备工艺,可以满足对于器件层厚度小于10um的要求。
技术实现要素:5.本发明的目的是提供一种带空腔的绝缘体上硅衬底的制备工艺,在常规besoi键合减薄工艺的基础上,针对支撑衬底带图形化空腔的特殊结构,通过键合前的等离子活化处理,以及键合后的两步热处理,第一步低温退火可以确保经过等离子表面活化处理的硅衬底有足够的键合强度来应对后续的减薄工艺,减薄完成后进行第二步高温氧化处理既提升了键合强度,又可以实现精准的厚度控制;在机械研磨的减薄过程中预留足够的厚度来
防止空腔结构上的器件层硅破损,然后结合cmp抛光和高温氧化减薄工艺进行表面处理;从而以层转移的方式,将作为器件层的外延层转移至带图形空腔的支撑衬底上,获得具有相对较薄(<10um)器件层的带空腔的绝缘体上硅衬底材料。
6.本发明通过如下技术方案实现上述目的:一种带绝缘埋层的硅衬底的制备工艺,包括以下步骤:
7.s101,提供单晶硅衬底,正面为抛光面;
8.s102,在单晶硅衬底表面生长一层轻掺杂单晶外延硅层;
9.s103,提供带图形化空腔的单晶硅衬底作为支撑衬底;
10.s104,支撑衬底进行热氧化,生长二氧化硅作为绝缘层;
11.s105,以单晶硅衬底的外延层表面和支撑衬底表面有图形化空腔的表面为键合面,分别进行等离子表面活化处理后,常温下将单晶硅衬底和支撑衬底在真空环境中键合在一起,形成键合衬底;
12.s106,将键合衬底放入炉管进行低温退火;
13.s107,对键合衬底采用机械研磨的减薄方式,去除大部分的衬底单晶硅,剩余衬底单晶硅通过后续工艺进行去除;
14.s108,对减薄后的键合衬底进行酸腐蚀,采用氢氟酸,硝酸和醋酸的混合腐蚀溶液,喷涂在旋转的键合衬底上,择优腐蚀掉单晶衬底硅后自停止在外延界面,确保将机械研磨后预留的单晶硅衬底去除干净;
15.s109,对腐蚀后的键合衬底进行化学机械抛光,得到所需的表面粗糙度;
16.s110,对抛光后的键合衬底进行高温热氧化,进一步提升键合强度;
17.s111,对氧化后的键合衬底进行单片式旋转喷涂氢氟酸的化学腐蚀,去除表面二氧化硅层。
18.进一步的,所述s101单晶硅衬底为直拉cz单晶抛光硅片,硅衬底正面为抛光面,电阻率小于0.01ohm.cm。
19.进一步的,所述s102在单晶硅衬底表面生长一层轻掺杂单晶外延硅层,电阻率大于1ohm.cm;外延厚度大于2um。
20.进一步的,所述s103提供带图形化空腔的支撑衬底,通过光刻及刻蚀工艺完成图形化的空腔结构。
21.进一步的,所述s104支撑衬底进行热氧化,生长二氧化硅作为绝缘层,其二氧化硅的厚度大于0.1um;
22.进一步的,所述s105以单晶硅衬底的外延层表面和支撑衬底表面有图形化空腔的表面为键合面,分别进行等离子表面活化处理后,常温下将单晶硅衬底和支撑衬底在真空环境中键合在一起,形成键合衬底,等离子表面活化采用n2,o2或n2/o2混合气体,键合的温度为常温,键合腔室处于真空环境下,真空压力小于10mbar;
23.进一步的,所述s106的低温退火温度不超过400度,退火时间大于1小时。
24.进一步的,所述s107的机械研磨的减薄方式为粗磨(砂轮目数小于800#)加精磨(砂轮目数大于3000#)的组合方式,研磨过程采用非接触式厚度测试监控,研磨后预留的顶硅厚度为20~50um。
25.进一步的,所述s108的酸腐蚀,为单片式旋涂腐蚀液的选择性腐蚀,腐蚀液位hf,
hno3及醋酸的混合溶液;腐蚀速率为2~5um/min;
26.进一步的,所述s109中cmp抛光去除量小于2um。
27.进一步的,所述s110中的高温热氧化,工艺温度大于1000度,时间大于2小时。
28.进一步的,所述s111的化学腐蚀采用旋转式单片腐蚀,hf溶液浓度小于10%,过腐蚀量不超过30%。
29.与现有技术相比,本发明的有益效果是:打破原有常规键合减薄工艺只能制备器件层大于10um以上的带空腔绝缘体上硅衬底材料的限制,通过层转移的方式,综合运用了等离子表面活化处理和低温退火工艺,来保证键合强度来应对后续的减薄工艺,减薄工艺过程结合了机械研磨进行大去除量的减薄和以选择性化学腐蚀停止在外延层与衬底硅界面的方式,实现厚度较薄的外延层转移至带图形化空腔的支撑衬底上,最后通过高温氧化工艺进行键合强度的提升并以氧化减薄的方式对顶层器件硅层厚度进行精确控制,从而制备出器件层厚度小于10um的带空腔的绝缘体上硅衬底材料。
附图说明
30.图1是本发明具体实施方式的实施步骤流程图。
31.图2是步骤s101和步骤s102的产品状态示意图。
32.图3是步骤s103和步骤s104的产品状态示意图。
33.图4是步骤s105和步骤106的产品状态示意图。
34.图5是步骤s107的产品状态示意图。
35.图6是步骤s108的产品状态示意图。
36.图7是步骤s109的产品状态示意图。
37.图8是步骤s110的产品状态示意图。
38.图9是步骤s111的产品状态示意图。
具体实施方式
39.下面结合附图对本发明提供的带绝缘埋层的硅衬底的制备方法具体实施方式做详细说明。
40.图1所示为本具体实施方式的实施步骤流程图,一种带绝缘埋层的硅衬底的制备工艺,包括如下步骤:
41.s101,提供单晶硅衬底,正面为抛光面;
42.s102,在单晶硅衬底表面生长一层轻掺杂单晶外延硅层;
43.s103,提供带图形化空腔的支撑衬底;
44.s104,支撑衬底进行热氧化,生长二氧化硅作为绝缘层;
45.s105,以单晶硅衬底的外延层表面和支撑衬底表面有图形化空腔的表面为键合面,分别进行等离子表面活化处理后,常温下将单晶硅衬底和支撑衬底在真空环境中键合在一起,形成键合衬底;
46.s106,将键合衬底放入炉管进行低温退火;
47.s107,对键合衬底采用机械研磨的减薄方式,减薄过程设备采用非接触式厚度监控,去除大部分的衬底单晶硅,剩余衬底单晶硅通过后续工艺进行去除;
48.s108,对减薄后的键合衬底进行酸腐蚀,采用氢氟酸,硝酸和醋酸的混合腐蚀溶液,喷涂在旋转的键合衬底上,择优腐蚀掉单晶衬底硅后自停止在外延界面,确保将机械研磨后预留的单晶硅衬底去除干净;
49.s109,对腐蚀后的键合衬底进行化学机械抛光,得到所需的表面粗糙度;
50.s110,对抛光后的键合衬底进行高温热氧化,进一步提升键合强度;
51.s111,对氧化后的键合衬底进行单片式旋转喷涂氢氟酸的化学腐蚀,去除表面二氧化硅层。
52.附图2所示,参考步骤s101和步骤s102,提供单晶硅衬底100,所述单晶硅衬底100的电阻率r1<0.01ohm.cm,以外延方式生长一层单晶硅外延层110,电阻率r2>1ohm.cm。
53.附图3所示,参考步骤s103和s104,提供单晶硅支撑衬底200,所述支撑衬底200正面为抛光面,通过光刻和刻蚀工艺,形成图形化的带空腔结构;然后进行热氧化,在支撑衬底表面形成热氧化层210,将作为最终键合衬底材料的绝缘层。优选二氧化硅厚度0.5~1um。
54.附图4所示,参考步骤s105和s106,分别对支撑衬底的绝缘层210表面和单晶衬底硅层100的表面进行等离子表面活化,然后在常温下将这两个面贴合在一起完成键合,形成键合衬底。优选为采用n2为气源,在真空腔室内进行等离子处理。
55.因为步骤s105已对键合前的表面进行过等离子活化处理,只需一个低温退火即可达到足够强的键合强度;退火气氛可以是氮气,氧气或其他惰性气体。退火时间大于2小时。退火温度低于400度,可以满足后续减薄工艺对键合强度的要求。优选退火温度300℃,退火时间3小时。
56.附图5参考步骤s107,采用机械研磨的减薄方式,将单晶衬底100的厚度减薄至20~50um的预留厚度;优选预留厚度20~30um。
57.附图6参考步骤s108,采用旋转式单片腐蚀工艺,对机械研磨后的键合衬底片进行酸腐蚀去除机械研磨过程预留的单晶衬底100;酸腐蚀后将自动停止在外延层界面,从而留下外延层110。
58.附图7参考步骤s109,对腐蚀后的键合衬底进行cmp抛光,抛光去除量不超过2um,既满足完全去除外延层过渡区的要求,又满足表面粗糙度及平整度要求。优选去除量1~1.5um。
59.附图8参考步骤s110,对抛光后的键合衬底进行高温氧化处理,氧化工艺温度不低于1000度,退火时间不低于2小时,该步骤既可以进一步提升键合强度,又可以通过氧化将一部分器件层硅转变为氧化硅进行去除,从而间接进行器件层硅厚度的精确调节。优选高温氧化温度1150度,氧化工艺时间2小时。
60.附图9参考步骤s111,对于高温氧化后的键合衬底进行旋转式单片hf腐蚀,以去除表面的氧化层,同时不影响背面氧化层的厚度。优选的hf浓度为5%~10%。
61.本发明打破原有常规键合减薄工艺只能制备器件层大于10um以上的带空腔绝缘体上硅衬底材料的限制,通过层转移的方式,综合运用了等离子表面活化处理和低温退火工艺,来保证键合强度来应对后续的减薄工艺,减薄工艺过程首先采用机械研磨进行大去除量的减薄,同时预留足够的厚度防止研磨过程顶硅器件层的破损,然后以选择性化学腐蚀停止在外延层与衬底硅界面的方式,实现厚度较薄的外延层转移至带图形化空腔的支撑
衬底上,最后通过高温氧化工艺进行键合强度的提升并以氧化减薄的方式对顶层器件硅层厚度进行精确控制,从而制备出器件层厚度小于10um的带空腔的绝缘体上硅衬底材料。。
62.以上所述仅是本发明的优选实施方式,应当指出,对于本技术领域的普通技术人员,在不脱离本发明原理的前提下,还可以做出若干改进和调整,这些改进和调整也应视为本发明的保护范围。