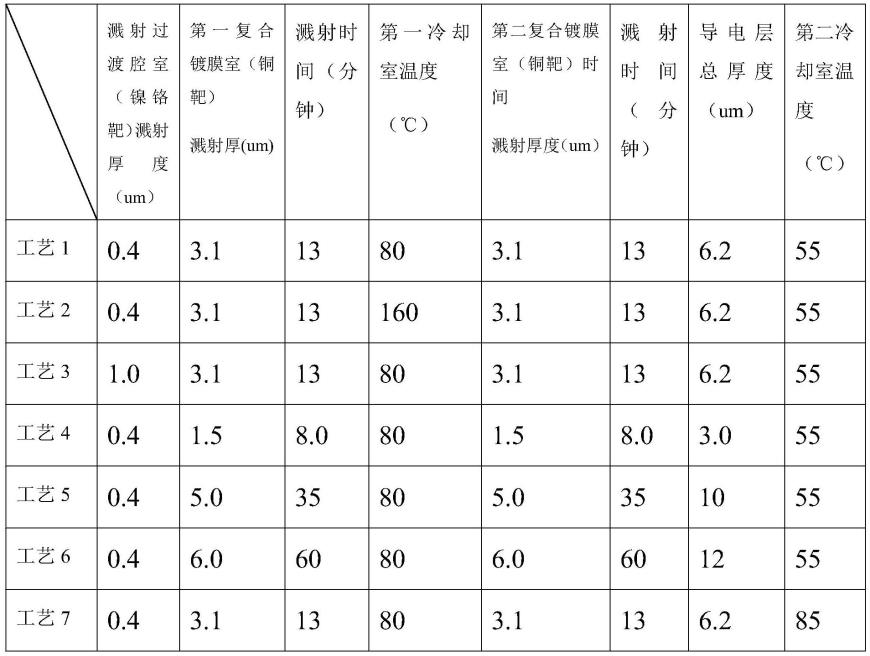
1.本发明涉及压敏电阻溅射电极制备技术,具体涉及一种压敏电阻制备方法及真空溅射镀膜设备、及其压敏电阻。
背景技术:2.氧化锌压敏电阻器现有制造工艺,通常为丝网印刷银浆或铜浆料,烘烤、烧结而成,形成有效的欧姆接触电极,也有通过电弧喷涂形成,高性能要求的压敏电阻,要求单位面积通过浪涌能力较高,目前性能稳定当属印刷银浆,通过烘烤烧结而成。压敏电阻主要用于电路中浪涌吸收,对应安装体积受限,对电阻单位面积通过电流能力要求较高的氧化锌压敏电阻产品,电极层中导电层的制作工艺尤为重要。目前采取的措施就是增加导电层厚度和降低欧姆接触电阻。
3.溅射技术用于压敏电阻电极制作是一项技术革命,通过镍铬或钛打底,再溅射导电层,相较于印刷、电镀、热浸等工艺由溅射工艺形成的导电层其致密性最优、导电性能最佳,也用于压敏电阻。然而现有技术中采用溅射技术直接制备的压敏电阻的金属导电层的厚度往往较薄,一般只能达到1μm左右。实际上,在现有工业技术中,采用溅射技术直接制备的压敏电阻的金属导电层镀膜厚度较薄的原因主要是溅射过厚(单次溅射时间过长)会导致温度升高,在真空状态下,温度过高会导致氧化锌脱氧还原,若采取在同一腔体或多腔体进行缓慢溅射达到较高厚度产品,需要时间较长,因真空下溅射形成的热量不能有效释放,温度难以降到产品适应温度,最终会导致生产的压敏电阻为不合格产品。
4.已经有一些现有技术致力于研究如何补足由溅射形成的压敏电阻的导电层(与电极引线直接相连的结构层),厚度:1、通过采用其他工艺与溅射工艺相结合制备压敏电阻电极层的方式来对压敏电阻的导电能力进行补足,例如:申请号为:201420644271的中国实用新型专利其采用电镀喷铝打底层+真空溅射铜导电层的方式来克服仅仅使用真空溅射形成的金属层厚度薄的不足,申请号为:2018105051972的中国发明专利其采用真空溅射打底层+热浸处理形成导电层的方式来克服仅仅使用真空溅射形成的金属层厚度薄、以及电镀均匀性较差的不足。但是上述工艺均采用的是其他工艺形成与溅射工艺相结合的方式来对溅射形成的导电层厚度进行补足,所形成的导电层的致密性差于由溅射技术直接形成的导电层。2、采用复合层结构设计来提高压敏电阻电极层的强度与厚度,例如:申请号为2013205912226的中国实用新型专利公开了一种复合电极结构的氧化锌压敏电阻器,其通过溅射多层复合打击结构(铬-铜镍合金-铬-铜镍合金),增加金属间致密性的方式来延长导电层铜电极的可溅射安全厚度,最终能够溅射形成0.5~1.5μm厚的导电层铜电极。
5.另外在现有的真空溅射镀膜设备中,已有设备通过设置多个用于连续镀膜的溅射腔室,从而通过多次溅射增加电极层的厚度,如申请号为2010102983273的中国专利,其公开了一种包括至少两个溅射室的连续式多室溅射镀膜室间气氛隔离系统,包括:在第一溅射室与第二溅射室之间加入过度室,过度室连接真空发生装置,过度室的真空度大于第一溅射室的真空度,过度室的真空度也大于第二溅射室的真空度;以通过真空度较高的过度
室防止两个溅射室内的保护气体混流造成污染。但是在连续性真空镀膜装置中,通常是在相邻溅射室溅射不同种类的金属(保护气体不同)时才需要进行防气流污染的保护;另一方面环境的真空度越高越不利益散热,在此种情况下,要求溅射的厚度越厚时间越长、连续溅射次数越多,整个真空系统的中温度就会越高,而单个溅射腔室温度达到350度以上时,氧化锌压敏电阻的主体材料-氧化锌会被脱氧还原,瓷片表层会形成导电层,所得到的电极层电性能指标都是废品,压敏电压较低、漏电流超出规定值,因此现有用于连续镀膜真空镀膜系统中单腔室溅射时间并不长,无法批量生产合格的压敏电阻产品。
技术实现要素:6.本发明的目的在于克服现有技术中所存在的无法通过溅射直接形成导电能力满足要求的压敏电阻的问题,提供一种压敏电阻制备方法及真空溅射镀膜设备、及其压敏电阻,本发明所提供的真空溅射镀膜设备与方法可以一次性镀膜得到5μm以上的压敏电阻导电层(电极层中与电极引线直接相连的结构层),在提高产品性能同时,可实现批量化生产。
7.为了实现上述发明目的,本发明提供了以下技术方案:
8.一种氧化锌材质的压敏电阻,包括:电极层,所述电极层包括:导电层,所述导电层由溅射工艺形成,且所述导电层厚度为d,且d∈(5,14]μm。
9.根据一种具体的实施方式,上述压敏电阻中,所述电极层还包括:底层过渡层,所述底层过渡层由溅射工艺形成,底层过渡层厚度不超过0.5μm。
10.其中,底层过渡层是用于增加电极层吸附力的结构层,导电层即为与电极引线直接相连的结构层;在本发明中,相应的导电层已经能够达到高性能的导电要求,因此适配的底层过渡层厚度无需过厚即可在满足吸附力要求的同时,进一步降低生产成本。
11.根据一种具体的实施方式,上述压敏电阻中,所述导电层厚度为6μm~10μm。
12.根据一种具体的实施方式,上述压敏电阻中,所述压敏电阻包括:两层所述电极层,氧化锌压敏陶瓷基片、以及电极引线,所述电极层分别设置在所述氧化锌压敏陶瓷基片的上下表面,两层所述电极层上分别设置有电极引线。其中,电极层中的导电层为与电极引线直接相连的结构层。
13.根据一种具体的实施方式,上述压敏电阻中,所述底层过渡层材料包括第一金属或其合金,所述第一金属包括:镍、铬或钛,所述导电层材料包括第二金属或其合金,所述第二金属包括:铜、银或镍。
14.其中,底层过渡层材料可以选择第一金属或者第一金属对应的金属合金,优选为镍铬合金;导电层材料可以选择第二金属或者第二金属对应的金属合金;优选为铜(可掺入少量的镍)。
15.在本发明进一步的实施例中,还提供一种氧化锌材质的压敏电阻制作方法,包括:在真空环境中密封溅镀所述压敏电阻的电极层;
16.其中,所述电极层包括:底层过渡层与导电层;所述导电层厚度为d,且d∈(5,14]μm。
17.根据一种具体的实施方式,上述氧化锌材质的压敏电阻制作方法中,所述底层过渡层厚度不超过0.5μm。
18.根据一种具体的实施方式,上述氧化锌材质的压敏电阻制作方法中,包括:在真空
环境或惰性气体环境下,分n次实施溅镀步骤以使所述压敏电阻的导电层达到厚度d,其中,n≥2;
19.在相邻两次导电层溅镀步骤之间加入冷却步骤,通过所述冷却步骤将压敏电阻的温度冷却至温度阈值以下。
20.根据一种具体的实施方式,上述氧化锌材质的压敏电阻制作方法中,所述冷却步骤采用分子流冷却技术将压敏电阻的温度冷却至温度阈值以下。
21.根据一种具体的实施方式,上述氧化锌材质的压敏电阻制作方法中,所述分子流为惰性气体。
22.根据一种具体的实施方式,上述氧化锌材质的压敏电阻制作方法中,所述温度阈值为:80℃~90℃。
23.根据一种具体的实施方式,上述氧化锌材质的压敏电阻制作方法中,所述导电层材料包括第二金属或其合金,所述第二金属包括:铜、银或镍。
24.在本发明进一步的实施例中,还提供一种真空溅射镀膜设备,包括:至少两个复合镀膜室;在相邻两个所述复合镀膜室之间设置第一冷却室,用于将相邻两个所述复合镀膜室之间的压敏工件温度降低至温度阈值以下;其中,所述第一冷却室与相邻两个所述复合镀膜室密封连接。
25.根据一种具体的实施方式,上述真空溅射镀膜设备中,所述温度阈值为:80℃~90℃。
26.根据一种具体的实施方式,上述真空溅射镀膜设备中,所述复合镀膜室用于溅镀所述压敏电阻的导电层;
27.且所有所述复合镀膜室的温度均低于安全温度阈值,所述安全温度阈值为:280℃~350℃。
28.具体的,导电层材料可以采用铜或银或镍或其合金中的一种,优选为铜。
29.根据一种具体的实施方式,上述真空溅射镀膜设备中,所述第一冷却室被配置为:采用分子流冷却技术将相邻两个所述复合镀膜室之间的压敏电阻的温度降低至温度阈值以下。
30.根据一种具体的实施方式,上述真空溅射镀膜设备中,所述复合镀膜室为单面溅射室或双面溅射室,在所述复合镀膜室中设置有闭环磁场。
31.根据一种具体的实施方式,上述真空溅射镀膜设备中,所述复合镀膜室为两个,
32.所述真空溅射镀膜设备包括依次连接的:预抽室、预溅射室、第一复合镀膜室、第一冷却室、第二复合镀膜室、后过渡室、以及第二冷却室。
33.与现有技术相比,本发明的有益效果:
34.1、本发明所提供的压敏电阻,其电极层中的导电层由溅射工艺形成,该电极层的致密性远大于印刷工艺得到的电极层,同时所述导电层厚度大于5μm,具有极佳的导电性能;进而在材料的选择上,可以通过选择低成本材料作为所述导电层的材料,降低压敏电阻电极的制作成本。根据压敏电阻性能测试结果可知,本发明所提供的压敏电阻,6μm厚度的铜膜导电层即可等效于现有印刷工艺13μm厚度银膜导电层的导电能力;是满足高性能要求的压敏电阻,性能指标可以提高到7ka/cm2以上。
35.2、本发明所提供的真空溅射镀膜设备在设置多个复合镀膜室的基础上,通过在相
邻两个所述复合镀膜室之间设置第一冷却室,以降低相邻两个所述复合镀膜室之间的压敏工件的温度,在提升单次真空溅射电极层厚度的同时,通过降低电极温度防止电极在多个复合镀膜室的溅射中因为温度过高被还原,所得本发明所提供的真空铜电极溅射制备装置可以一次性镀膜得到5μm以上的电极层,实验数据表明,本发明所提供的真空溅射镀膜设备每小时可以镀膜3~4台车高厚度的压敏电阻电极层(每台车可以装载直径14mm的压敏电阻5000只左右);可实现压敏电阻的批量化生产。
36.3、在复合镀膜室中设置闭环磁场增加沉积速度,缩短溅射时间、提高加工效率。
附图说明
37.图1为本发明实施例所述的真空溅射镀膜设备。
具体实施方式
38.下面结合试验例及具体实施方式对本发明作进一步的详细描述。但不应将此理解为本发明上述主题的范围仅限于以下的实施例,凡基于本发明内容所实现的技术均属于本发明的范围。
39.实施例1
40.图1示出了本发明示例性实施例的真空溅射镀膜设备,包括:至少两个复合镀膜室,相邻两个所述复合镀膜室之间设置有第一冷却室,用于将相邻两个所述复合镀膜室之间的压敏工件温度降低至温度阈值以下;其中,所述第一冷却室与相邻两个所述复合镀膜室密封连接。其中,所述温度阈值取值为:80℃~90℃。
41.具体的,所述复合镀膜室与所述第一冷却室之间具有供被镀物(本实施例中为压敏电阻,在设备中流转生产的压敏电阻半成品也称压敏工件)连续通过的通道。其中,第一冷却室可以采用现有多种冷却技术中的一种,本发明根据溅射工艺的特性,将第一冷却室优选配置为:采用分子流冷却技术(惰性气体冷却技术,优选为氮气)将压敏工件降至温度阈值以下。并且所述第一冷却室连接有真空发生装置,在压敏工件温度降低至温度阈值以下后,通过所述真空发生装置将环境真空度降低到与复合镀膜室真空度相同,或略低于复合镀膜室的真空度,在真空度满足要求后,再将压敏工件从第一冷却室相应的通道移送至下一个复合镀膜室,即可实现连续溅镀。进一步的,在本实施例中,所述复合镀膜室用于溅镀所述压敏电阻的导电层;且所有所述复合镀膜室的温度均低于安全温度阈值,所述安全温度阈值为:280℃~350℃。所述复合镀膜室可以采用单面溅射室或双面溅射室;并且,在所述复合镀膜室中设置有能够增加沉积速度的闭环磁场,以此缩短溅射时间、提高加工效率。考虑到增加溅射室会增加设备的成本,优选将复合镀膜室配置为两个,参考图1,所述真空溅射镀膜设备包括依次连接的:预抽室、预溅射室、第一复合镀膜室、第一冷却室、第二复合镀膜室、后过渡室、以及第二冷却室。其中,真空溅射镀膜设备中的各腔室(除开复合镀膜室与第一冷却室)之间均采用现有溅射设备的常规密封连接方式进行连接。其中,压敏工作经过第二冷却室的冷却之后即可离开真空环境进入空气环境,即第二冷却室用于将压敏工件冷却至氧化保护温度,并且考虑到时间成本,一般设定为50℃。在本实施中,第二冷却室也采用惰性气体分子流冷却技术。
42.实施例2
43.在本发明进一步的实施例中还提供一种氧化锌材质的压敏电阻制作方法,包括:在真空环境中密封溅镀所述压敏电阻的电极层;即在实施例1所提供的所提供的真空溅射镀膜设备加工压敏电阻的电极层;其中,所述电极层包括:底层过渡层与导电层;所述导电层厚度为d,且d∈(5,14]μm。
44.具体的,在真空环境或惰性气体环境下,分n次实施溅镀步骤以使所述压敏电阻的导电层达到厚度d,其中,n≥2;在相邻两次导电层溅镀步骤之间加入冷却步骤,以将压敏电阻的温度冷却至温度阈值以下。其中,冷却步骤采用分子流冷却技术将压敏电阻的温度冷却至温度阈值以下;分子流为惰性气体,优选为氮气。在压敏工件温度降低至温度阈值以下后,降低真空度再进入下次导电层溅镀步骤。
45.表1
[0046][0047]
如表1所示,本发明采用7组不同的工艺参数在真空环境中密封溅镀所述压敏电阻的电极层,以对本发明所提供的方法生产的压敏电阻进行性能测试。在工艺1~工艺7中,本发明所提供的真空溅射镀膜设备中的预抽真空室设置压力为15pa,真空室压力设置为5pa,溅射室(用于溅射底层过渡层的腔室)设置两个镍铬对靶,电压400~500v,采用氩原子轰击靶材,复合镀膜室设置铜靶6对,电压400~500v,采用氩原子轰击靶材,第二复合镀膜室6对铜靶,电压400~500v,冷却分子流采用氮气。
[0048]
进一步的,抽取氧化锌压敏电阻瓷片myn15-621k产品进行对比实验,该产品芯片直径为13.5mm左右,溅射瓷片导电层直径11.2mm。试验产品通过焊接包封后进行测试初始电性能和耐受8/20us电流冲击能力检测。8/20us电流冲击按照7ka/cm2进行检验,常规产品8/20us要求一般按照6ka/cm2。要求产品初始漏电流不超过20ua,电流冲击后压敏电压变化率不超过10%,外观无可见损伤。对表1中的工艺1~工艺7所生成的压敏电阻产品进行试验
对比实验数据见下表2~表8:
[0049]
表2:
[0050][0051]
表3:
[0052][0053]
表4:
[0054][0055]
表5:
[0056][0057]
表6:
[0058][0059]
表7:
[0060][0061]
表8:
[0062]
[0063][0064]
从表2~表8对比组测试结果可以看出:
[0065]
1、当底层过渡层厚度超过0.5um后,产品耐受冲击能力降低,从表4得知,冲击后包封层(位于压敏电阻最外层用于防潮保护的环氧树脂包封层)全部炸开,所有外观不合格。主要打底层镍铬导电不强,形成欧姆接触电阻加大,大电流冲击瞬间产生热量较高。
[0066]
2、第一冷却室达到160度或以上后,在相同工艺情况下溅射产品的初始漏电流较大,见表3所示,基本大于20ua。
[0067]
3、第二冷却室温度超过60度后,产品在自然条件下冷却,导电层表面氧化较快,导致产品导电能力下降、可焊锡较差。从表8中可以看出有产品冲击后外观不合格产品出现。
[0068]
4、在增大单个腔室镀膜厚度时,需降低沉积率,减缓温升,溅射厚度与时间不是正比例关系,当单腔室厚大达到5um时,再溅射1um厚度时间至少要延长20分钟,溅射的产品有出现漏电流不合格产品,见表6和表7,单产品耐受冲击能力要强些,主要是电极层厚度增加后,电阻值减小,产品在电流冲击后变化率较小。
[0069]
综上,效率最高、产品性能优良的为工艺1所生成的压敏电阻。并且优选打底0.5um以下,单腔室溅射厚度低于5um,冷却室温度低于80度,第二冷却室温度低于55度,导电层在6~10um左右比较好。
[0070]
实施例3
[0071]
在本发明进一步的实施例中还提供一种采用实施例2所述的氧化锌材质的压敏电阻制作方法制作的压敏电阻,所述压敏电阻包括:电极层,所述电极层包括:导电层和底层过渡层,所述底层过渡层、导电层由溅射工艺形成,且所述导电层厚度为5μm~14μm。所述底层过渡层小于0.5μm,材料为镍或铬或其合金中的一种,所述导电层材料为铜。
[0072]
进一步的,所述压敏电阻包括:两层所述电极层,氧化锌压敏陶瓷基片、以及电极引线,所述电极层分别设置在所述氧化锌压敏陶瓷基片的上下表面,两层所述电极层上分别设置有电极引线。其中,所述压敏电阻中除开电极层以外的结构均采用现有常规方法加工制成。
[0073]
以上所述仅为本发明的较佳实施例而已,并不用以限制本发明,凡在本发明的精神和原则之内所作的任何修改、等同替换和改进等,均应包含在本发明的保护范围之内。