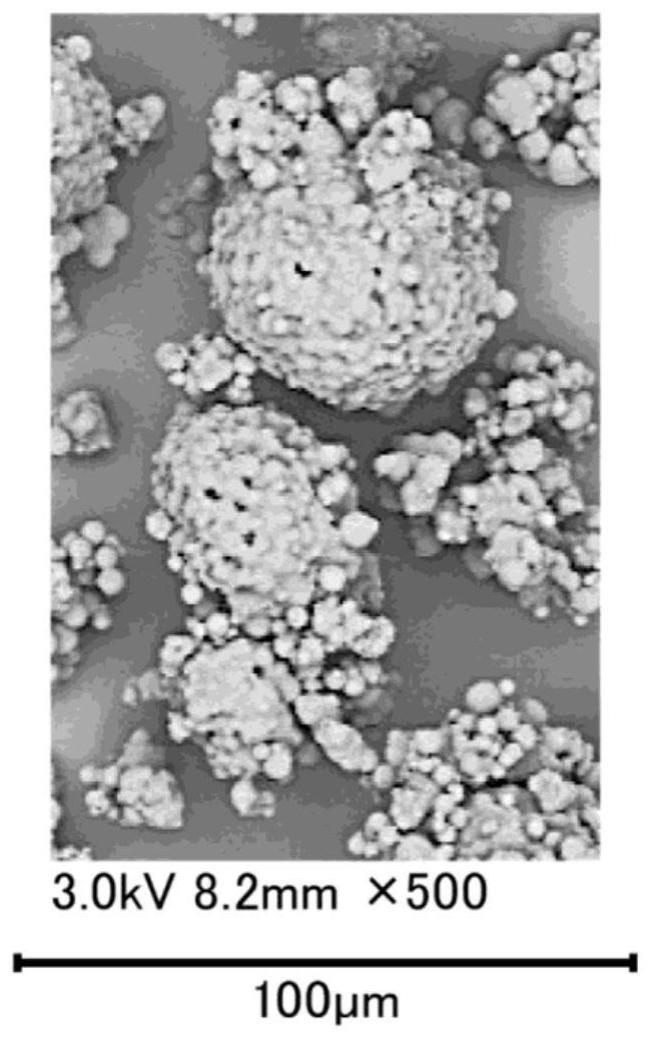
1.本发明涉及磁粉的制造方法、压粉成型体的制造方法、磁粉和压粉成型体。
背景技术:2.作为制造压粉磁芯的方法,在专利文献1中有如下记载:将软磁粉末、环氧树脂(粘合材料)和甲苯(有机溶剂)混合,得到混合物。搅拌得到的混合物,然后进行干燥,得到块状的干燥物。接下来,将该干燥物过筛,将干燥物粉碎,得到造粒粉末。将得到的造粒粉末填充到成型模具,得到成型物。对得到的成型物进行加热,使粘合材料固化。由此,得到压粉磁芯。
3.现有技术文献
4.专利文献
5.专利文献1:日本特开2008-244023号公报
技术实现要素:6.在制造压粉磁芯时,通过高密度地填充造粒粉末,从而可以使压粉磁芯的磁导率升高。但是,在由包含软磁粉末的混合物的干燥物制作造粒粉末的方法中,得到的造粒粉末容易凝集,因此,难以高密度地填充造粒粉末。因此,可以考虑如专利文献1所述那样,在填充造粒粉末的工序前,进行将造粒粉末裂解的工序和分级的工序。但是,凝集情况下的造粒粉末会变硬,因此,难以使其粒径减小,而且会增加多余的工序,因此制造工序会变得复杂。进而,在裂解造粒粉末的情况下,有时在裂解的面上没有形成环氧树脂等的绝缘膜,因此会有绝缘膜的形成不充分的风险。
7.另外,作为进一步提高压粉磁芯的磁导率的方法,可以考虑添加平均粒径比软磁粉末更小、例如平均粒径为纳米水平的磁性体粒子。例如,基于专利文献1所记载的方法,可以考虑加入软磁粉末,由包含微小的磁性体粒子的混合物的干燥物制作造粒粉末的方法。但是,该方法中,由于微小的磁性体粒子的范德华力,使得造粒粉末更容易凝集。
8.本发明的目的在于提供一种磁粉的制造方法,该磁粉混合有微小的磁性体粒子且可以抑制凝集。进而,本发明的目的在于提供一种方法,该方法使用由上述制造方法得到的磁粉来制造压粉成型体。另外,本发明的目的在于提供一种磁粉和一种压粉成型体,该磁粉混合有微小的磁性体粒子且可以抑制凝集,该压粉成型体包含上述磁粉。
9.本发明的磁粉的制造方法具备:将包含第1磁性体粒子、第2磁性体粒子、热固化性树脂和有机溶剂的喷雾液进行喷雾并干燥从而得到磁粉的工序;上述磁粉具备上述第1磁性体粒子和设置在上述第1磁性体粒子的表面的热固化性的树脂被膜,上述第1磁性体粒子为软磁性金属粒子,上述树脂被膜的内部混合有上述第2磁性体粒子,上述第2磁性体粒子的平均粒径比上述第1磁性体粒子的平均粒径小。
10.本发明的压粉成型体的制造方法具备:通过本发明的磁粉的制造方法而得到磁粉的工序;通过对上述磁粉进行热压制成型,从而使上述热固化性树脂固化,得到压粉成型体
的工序。
11.本发明的磁粉具备第1磁性体粒子和设置在上述第1磁性体粒子的表面的热固化性的树脂被膜,上述第1磁性体粒子为软磁性金属粒子,上述树脂被膜的内部混合有第2磁性体粒子,上述第2磁性体粒子的平均粒径比上述第1磁性体粒子的平均粒径小。
12.本发明的压粉成型体包含上述磁粉。
13.根据本发明,可以得到混合有微小的磁性体粒子且可以抑制凝集的磁粉。
附图说明
14.图1为表示在喷雾液的喷雾干燥后得到的磁粉的一个例子的扫描型电子显微镜照片。
15.图2为表示具备二流体喷嘴或四流体喷嘴的喷雾干燥机的构成的一个例子的示意图。
16.图3为示意性地表示本发明的磁粉的一个例子的剖面图。
17.图4为示意性地表示本发明的磁粉的另一个例子的剖面图。
18.图5为示意性地表示具备压粉磁芯的线圈零件的一个例子的立体图。
19.图6为示意性地表示具备压粉磁芯的线圈零件的另一个例子的立体图。
20.图7为表示实施例1中的磁导率的频率特性的坐标图。
21.图8为表示实施例2中的磁导率的频率特性的坐标图。
22.符号说明
23.10、10a 磁粉
24.11 第1磁性体粒子
25.12 第2磁性体粒子
26.21 树脂被膜
27.50、60 线圈零件
28.51、61 压粉磁芯
29.52、62 导线
30.52a 导线的第1端部
31.52b 导线的第2端部
32.53、63 线圈导体
33.54a 第1连接端部
34.54b 第2连接端部
35.100 喷雾干燥机
36.110 喷嘴
37.120 干燥室
38.121 开口部
39.122 排出口
40.130 回收部
41.131 旋风分离器
42.132 袋式过滤器
43.133 配管
44.134 鼓风机
45.x 喷雾液
具体实施方式
46.以下,对本发明的实施方式进行说明。
47.但是,本发明不限于以下的实施方式,在不改变本发明的要旨的范围内,可以适当改变并使用。将以下实施方式中所记载的本发明的各期望构成组合2个以上的方案也属于本发明。
48.[磁粉的制造方法]
[0049]
本发明的磁粉的制造方法具备将喷雾液进行喷雾并干燥从而得到磁粉的工序。
[0050]
喷雾液包含第1磁性体粒子、第2磁性体粒子、热固化性树脂和有机溶剂。
[0051]
例如在后述的实施例中,可以使用以下所示的第1磁性体粒子、第2磁性体粒子、热固化性树脂和有机溶剂。
[0052]
第1磁性体粒子:羰基铁粉(平均粒径d50:5μm)
···a[0053]
第2磁性体粒子:锰铁氧体粉(组成:(feo,mno)
·
fe2o3、平均粒径:91nm或250nm)
···b[0054]
热固化性树脂的主剂:双酚a型环氧树脂
···c[0055]
热固化性树脂的固化剂:酚固化剂
···d[0056]
有机溶剂:甲乙酮
···e[0057]
配合比
···
第1磁性体粒子:第2磁性体粒子=75重量%:25重量%等
[0058]
将热固化性树脂的主剂和热固化性树脂的固化剂的合计重量相对于第1磁性体粒子、第2磁性体粒子、热固化性树脂的主剂和热固化性树脂的固化剂的合计重量的比例(c+d/a+b+c+d)定义为“树脂量”;将第1磁性体粒子、第2磁性体粒子、热固化性树脂的主剂和热固化性树脂的固化剂的合计重量相对于第1磁性体粒子、第2磁性体粒子、热固化性树脂的主剂、热固化性树脂的固化剂和有机溶剂的合计重量的比例(a+b+c+d/a+b+c+d+e)定义为“喷雾浓度”,此时,例如在以树脂量为10重量%以下(后述实施例中为2.5重量%)的方式调合各成分的同时,以喷雾浓度为约50重量%~60重量%(后述实施例中为59.5重量%)的方式稀释上述有机溶剂,制备喷雾液。
[0059]
第1磁性体粒子为软磁性金属粒子。作为软磁性金属粒子,可以使用结晶性粉末或无定形粉末。作为结晶性粉末,例如可举出羰基铁粉、铁硅铝合金(sendust)磁粉、fe-si-cr系金属粉末、fe-si金属粉末等fe基磁性金属粉末、坡莫合金磁粉等fe-ni系磁性金属粉末、坡曼德合金等fe-co系磁性金属粉末、fe-si-b-nb-cu系纳米结晶磁性金属粉末等。作为无定形粉末,可举出fe-si-cr系或fe-b-si系无定形磁粉等。
[0060]
第2磁性体粒子例如为金属氧化物磁性体粒子,优选为铁氧体磁性粒子。在第2磁性体粒子为金属氧化物磁性体粒子的情况下,与第2磁性体粒子为金属磁性体粒子的情况相比,可以提高压粉成型体的绝缘性和安全性。因此,适合作为高速信号系的emi(electro magnetic interference)对策零件的用途。
[0061]
特别是在第2磁性体粒子为铁氧体磁性粒子的情况下,直到高频段为止都可以得
到压粉成型体的高磁导率化和低磁芯损耗化。
[0062]
在第2磁性体粒子为铁氧体磁性粒子的情况下,铁氧体磁性粒子例如包含选自磁铁矿(铁铁氧体)、锰铁氧体、镁铁氧体、锶铁氧体、镍锌铁氧体和镍铁氧体中1种以上的铁氧体。
[0063]
在第2磁性体粒子为铁氧体磁性粒子的情况下,在铁氧体磁性粒子中,优选以合计为65重量%以上来包含磁铁矿和锰铁氧体中的一者或两者。通过在铁氧体磁性粒子中以规定量包含磁铁矿和锰铁氧体中的一者或两者,从而可以得到更高的饱和磁化。
[0064]
或者,第2磁性体粒子也可以是金属磁性体粒子。在第2磁性体粒子为金属磁性体粒子的情况下,可以提高压粉成型体的直流叠加特性。因此,适合功率电感器等作为emi对策零件的用途。
[0065]
第2磁性体粒子优选为球状。球状不仅包含完全的球形,也包含近似于球形的形状。如果第2磁性体粒子为球状,则可以将第2磁性体粒子高密度地填充到第1磁性体粒子间,因此,可以提高磁导率。
[0066]
第2磁性体粒子的平均粒径比第1磁性体粒子的平均粒径小。通过混杂平均粒径比第1磁性体粒子更小的第2磁性体粒子,从而在得到的磁粉中,可以用第2磁性体粒子填满第1磁性体粒子彼此的间隙。通过对这样的磁粉进行热压制成型来制作压粉成型体而可以使磁导率进一步提高。
[0067]
第2磁性体粒子的平均粒径例如为1nm~1μm,优选为40nm~250nm。
[0068]
另外,第2磁性体粒子的平均粒径优选为第1磁性体粒子的平均粒径的1/10以下。
[0069]
通过将铁氧体磁性粒子等第2磁性体粒子的平均粒径控制在上述范围内,从而可以抑制第2磁性体粒子彼此的凝集。因此,可以制作在第1磁性体粒子的表面均匀地形成了树脂被膜的磁粉。另外,通过对这样的磁粉进行热压制成型,从而可以得到将第2磁性体粒子高密度地填充到第1磁性体粒子间的压粉成型体。
[0070]
第2磁性体粒子的平均粒径可如下求出:在使用扫描型电子显微镜(sem)的倍率50000倍的观察中,通过图像解析求出各粒子(但因粒子彼此重合等而导致粒子的外周部分不可见的情况除外)的等效圆直径,根据其平均值而算出。另一方面,第1磁性体粒子的平均粒径是指通过激光衍射
·
散射法求出的粒度分布中的、在积分值50%的粒径d50。
[0071]
第1磁性体粒子的平均粒径没有特别限定,例如为2μm~35μm。
[0072]
作为第1磁性体粒子,可以并用平均粒径相对较大的第1磁性体粗粒和平均粒径相对较小的第1磁性体微粒。该情况下,第2磁性体粒子的平均粒径比第1磁性体粗粒的平均粒径小且比第1磁性体微粒的平均粒径小。构成第1磁性体粗粒的软磁性金属可以与构成第1磁性体微粒的软磁性金属相同,也可以不同。
[0073]
作为热固化性树脂的主剂,例如可举出双酚a型环氧树脂、双酚f型环氧树脂、酚醛清漆型环氧树脂、聚酰亚胺树脂、聚苯硫醚树脂等。这些主剂可以单独使用,也可以并用。
[0074]
作为热固化性树脂的固化剂,例如可举出酚系固化剂、芳香族胺系固化剂、咪唑系固化剂、酰亚胺系固化剂等。这些固化剂可以单独使用,也可以并用。
[0075]
作为有机溶剂,例如可举出甲乙酮、甲苯、乙酸甲酯、乙酸乙酯、丙酮等。
[0076]
通过将得到的喷雾液喷雾并干燥,从而可以制作在第1磁性体粒子的表面设置热固化性的树脂被膜,在树脂被膜的内部混杂第2磁性体粒子的磁粉。
[0077]
本说明书中,“热固化性的树脂被膜”是指由处于未固化状态的热固化性树脂构成的树脂被膜。未固化的状态不仅仅是指处于未进行固化的状态的热固化性树脂的预聚物,还包括处于固化开始进行但尚未完全固化的半固化状态的b阶段。
[0078]
作为将喷雾液喷雾并干燥的方法,优选使用具备二流体喷嘴或四流体喷嘴的喷雾干燥机(也称为micromist spray dryer)的方法。通过使喷雾液从二流体喷嘴或四流体喷嘴喷射而使有机溶剂挥发,从而可以得到磁粉。
[0079]
例如,后述的实施例中,用micromist spray dryer(蒸发能力1.3kg/h)的四流体喷嘴将上述喷雾液进行喷雾,在由氧分压控制的封闭系统内,在70℃~110℃的温度进行加热干燥。
[0080]
通过将喷雾液喷雾并干燥,从而使上述定义的树脂量降低。通过使喷雾液的喷雾干燥后的树脂量减少,从而可以抑制第1磁性体粒子彼此的凝集,容易在各第1磁性体粒子的表面形成树脂被膜。其结果是,可以一口气地得到粒径均匀的磁粉。因此,得到的磁粉无需进行裂解工序和分级工序,可以直接使用。
[0081]
例如,以通过造粒后的热重量(tg)分析而测定的实测值计,在喷雾液的调合时为2.5重量%的树脂量,在喷雾液的喷雾干燥后降低至1.5重量%。
[0082]
喷雾液的喷雾干燥后的树脂量以通过造粒后的tg分析而测定的实测值计,优选为0.15重量%~3重量%。
[0083]
图1为表示在喷雾液的喷雾干燥后得到的磁粉的一个例子的扫描型电子显微镜照片。
[0084]
如图1所示,将喷雾液喷雾并干燥而得到的磁粉中,第1磁性体粒子彼此不凝集,在各第1磁性体粒子的表面形成埋没了第2磁性体粒子的树脂被膜。图1中,磁粉的最大粒径为30μm左右。
[0085]
如上所述,本发明的磁粉的制造方法中,可以抑制第1磁性体粒子彼此的凝集,一次性得到粒径均匀的磁粉。由此,无需进行裂解工序和分级工序等工序,因此,可以直接使用得到的磁粉。或者,可以使裂解工序和分级工序等工序简化。通过对这样的磁粉进行热压制成型,可以制作高密度地填充了磁粉的压粉成型体,其结果是,可以提高磁导率。
[0086]
图2为表示具备二流体喷嘴或四流体喷嘴的喷雾干燥机的构成的一个例子的示意图。
[0087]
图2所示的喷雾干燥机100具备喷嘴110、干燥室120和回收部130;干燥室120中,使用喷嘴110将喷雾液x进行喷射,使喷雾液x所包含的有机溶剂挥发,从而使磁粉干燥;回收部130用于回收在干燥室120中干燥的磁粉。
[0088]
在干燥室120的垂直方向上部设置有盖体,贯通盖体而设置有喷嘴110。喷嘴110为二流体喷嘴或四流体喷嘴。可以从喷嘴110向垂直方向下方喷射喷雾液x。另外,盖体上设置有开口部121,其从喷嘴110的喷雾液x的喷射方向(垂直方向下方)的上游侧起,沿着喷射方向,供给流动的热风(例如空气)。
[0089]
在干燥室120的垂直方向下游侧,设置有将干燥的磁粉排出到干燥室120外的排出口122。
[0090]
回收部130具备旋风分离器131和袋式过滤器132。干燥室120的排出口122和旋风分离器131通过配管133而连接,凭借热风的气流将干燥的磁粉运送至旋风分离器131,被该
旋风分离器131回收。未能被旋风分离器131回收的干燥的磁粉会被设置在比旋风分离器131更靠近热风流动方向下游侧的袋式过滤器132回收。作为回收磁粉的手段,只要具备旋风分离器131和袋式过滤器132任一者即可,通过同时具备两者,从而可以使磁粉的回收率提高。在袋式过滤器132的热风流动方向下游侧,具备用于将装置内的气体进行排气的鼓风机134,从鼓风机134将热风和流经喷嘴110的气体流路的空气排出到装置外。
[0091]
[磁粉]
[0092]
通过上述工序得到的磁粉具备第1磁性体粒子和设置在上述第1磁性体粒子的表面的热固化性的树脂被膜,上述第1磁性体粒子为软磁性金属粒子,上述树脂被膜的内部混合有第2磁性体粒子,上述第2磁性体粒子的平均粒径比上述第1磁性体粒子的平均粒径小。这样的磁粉也是本发明之一。
[0093]
图3为示意性地表示本发明的磁粉的一个例子的剖面图。
[0094]
在图3所示的磁粉10中,在第1磁性体粒子11的表面设置有热固化性的树脂被膜21,在树脂被膜21的内部混合有第2磁性体粒子12。在图3所示的磁粉10中,在多个第2磁性体粒子12之中,一部分第2磁性体粒子12埋没在树脂被膜21中,剩余的第2磁性体粒子12从树脂被膜21突出。因此,在磁粉10的表面形成凹凸。树脂被膜21的厚度可以是恒定的,也可以在各处不同。埋没在树脂被膜21中的第2磁性体粒子12的比例和从树脂被膜21突出的第2磁性体粒子12的比例例如可以通过调节第1磁性体粒子和第2磁性体粒子的粒径、第1磁性体粒子、第2磁性体粒子与热固化性树脂的配合比等来调节。
[0095]
图4为示意性地表示本发明的磁粉的另一个例子的剖面图。
[0096]
在图4所示的磁粉10a中,在第1磁性体粒子11的表面设置有热固化性的树脂被膜21,在树脂被膜21的内部混合有第2磁性体粒子12。在图4所示的磁粉10a中,所有的第2磁性体粒子12都埋没在树脂被膜21中。如图4所示那样,树脂被膜21的厚度可以是恒定的,也可以在各处不同。在树脂被膜21的厚度不为定值的情况下,磁粉10a的表面会形成凹凸。
[0097]
在由本发明的磁粉的制造方法而得到的磁粉或本发明的磁粉中,优选至少一部分第2磁性体粒子埋没在树脂被膜中,更优选所有的第2磁性体粒子埋没在树脂被膜中。如果第2磁性体粒子埋没在树脂被膜中,则为了得到后述的压粉成型体而对磁粉进行热压制成型时,磁粉彼此容易结合。
[0098]
本发明的磁粉的制造方法中,可以得到一种包含如图3所示那样一部分第2磁性体粒子从树脂被膜突出的磁粉、以及如图4所示那样所有的第2磁性体粒子埋没在树脂被膜中的磁粉的混合物。同样地,本发明的磁粉也可以是包含如图3所示那样一部分第2磁性体粒子从树脂被膜突出的磁粉、以及如图4所示那样所有的第2磁性体粒子埋没在树脂被膜中的磁粉的混合物。
[0099]
第1磁性体粒子为软磁性金属粒子。作为软磁性金属粒子,可举出结晶性粉末或无定形粉末。作为结晶性粉末,例如可举出羰基铁粉、铁硅铝合金(sendust)磁粉、fe-si-cr系金属粉末、fe-si金属粉末等fe基磁性金属粉末、坡莫合金磁粉等fe-ni系磁性金属粉末、坡曼德合金等fe-co系磁性金属粉末、fe-si-b-nb-cu系纳米结晶磁性金属粉末等。作为无定形粉末,可举出fe-si-cr系或fe-b-si系无定形磁粉等。
[0100]
第2磁性体粒子例如为金属氧化物磁性体粒子,优选为铁氧体磁性粒子。
[0101]
在第2磁性体粒子为铁氧体磁性粒子的情况下,铁氧体磁性粒子例如包含选自磁
铁矿(铁铁氧体)、锰铁氧体、镁铁氧体、锶铁氧体、镍锌铁氧体和镍铁氧体中1种以上的铁氧体。
[0102]
在第2磁性体粒子为铁氧体磁性粒子的情况下,在铁氧体磁性粒子中,优选以合计为65重量%以上来包含磁铁矿和锰铁氧体中的一者或两者。通过在铁氧体磁性粒子中以规定量包含磁铁矿和锰铁氧体中的一者或两者,从而可以得到更高的饱和磁化。
[0103]
或者,第2磁性体粒子也可以是金属磁性体粒子。
[0104]
第2磁性体粒子优选为球状。
[0105]
第2磁性体粒子的平均粒径比第1磁性体粒子的平均粒径小。
[0106]
第2磁性体粒子的平均粒径例如为1nm~1μm,优选为40nm~250nm。
[0107]
另外,第2磁性体粒子的平均粒径优选为第1磁性体粒子的平均粒径的1/10以下。
[0108]
第1磁性体粒子的平均粒径没有特别限定,例如为2μm~35μm。
[0109]
作为热固化性树脂,例如可举出双酚a型环氧树脂、双酚f型环氧树脂、酚醛清漆型环氧树脂、聚酰亚胺树脂、聚苯硫醚树脂等。这些热固化性树脂可以单独使用,也可以并用。
[0110]
[压粉成型体的制造方法]
[0111]
本发明的压粉成型体的制造方法具备:通过本发明的磁粉的制造方法而得到磁粉的工序;通过对上述磁粉进行热压制成型,从而使热固化性的树脂被膜固化,得到压粉成型体的工序。
[0112]
本发明的压粉成型体的制造方法中,可以对包含第1磁性体粒子、第2磁性体粒子和树脂被膜的磁粉进行热压制,也可以如以下所示的变形例那样,对包含2种以上的磁粉的混合物进行热压制。
[0113]
(变形例1)
[0114]
一种混合物,包含第1磁粉和第2磁粉,第1磁粉包含第1磁性体粗粒、第2磁性体粒子和树脂被膜,第2磁粉包含第1磁性体微粒、第2磁性体粒子和树脂被膜。
[0115]
(变形例2)
[0116]
一种混合物,包含第1磁粉和第2磁粉,第1磁粉包含第1磁性体粗粒、第2磁性体粒子和树脂被膜,第2磁粉包含第1磁性体微粒和树脂被膜。
[0117]
(变形例3)
[0118]
一种混合物,包含第1磁粉和第2磁粉,第1磁粉包含第1磁性体粗粒和树脂被膜,第2磁粉包含第1磁性体微粒、第2磁性体粒子和树脂被膜。
[0119]
在得到压粉成型体的工序中,可以对包含上述磁粉和氧化物粉末的混合物进行热压制成型。该情况下,氧化物粉末作为润滑剂发挥作用,可以使热压制时的磁粉的流动性提高。
[0120]
作为氧化物粉末,例如可以使用熔融石英等二氧化硅粒子。
[0121]
氧化物粉末的平均粒径优选为10nm~100nm。
[0122]
氧化物粉末的添加量优选为:相对于磁粉100重量份氧化物粉末为0.1重量份~0.25重量份。
[0123]
[压粉成型体]
[0124]
由以上工序而得到的压粉成型体例如可用作压粉磁芯。因此,本发明的压粉成型体的制造方法可以进一步具备在压粉成型体的内部或表面配置线圈导体的工序。
[0125]
另外,包含本发明的磁粉的压粉成型体也是本发明之一。本发明的压粉成型体可以进一步包含上述氧化物粉末。
[0126]
本发明的压粉成型体例如可用作压粉磁芯。因此,本发明的压粉成型体中,在压粉成型体的内部或表面可以配置线圈导体。
[0127]
图5为示意性地表示具备压粉磁芯的线圈零件的一个例子的立体图。
[0128]
图5所示的线圈零件50为在内部配置了线圈导体的压粉成型体的一个例子。线圈零件50具备:具有箱型的形状的压粉磁芯51、在压粉磁芯51的内部埋设有导线52的线圈导体53。导线52的第1端部52a和第2端部52b位于压粉磁芯51的表面并露出。压粉磁芯51的表面的一部分被互相电独立的第1连接端部54a和第2连接端部54b覆盖。第1连接端部54a与导线52的第1端部52a电连接,第2连接端部54b与导线52的第2端部52b电连接。线圈零件50中,导线52的第1端部52a被第1连接端部54a覆盖,导线52的第2端部52b被第2连接端部54b覆盖。
[0129]
将线圈导体53埋设到压粉磁芯51的内部的方法没有特别限定。例如,可以将卷绕了导线52的构件配置在模具内,进一步将磁粉供给到模具内,进行热压制成型。或者,准备多个将磁粉提前预成型而成的构件,将这些构件组合,将导线52配置在此时形成的空隙部内,得到组装物,对该组装物进行热压制成型。
[0130]
图6为示意性地表示具备压粉磁芯的线圈零件的另一个例子的立体图。
[0131]
图6所示的线圈零件60为在表面配置了线圈导体的压粉成型体的一个例子。线圈零件60是环状的压粉磁芯(环状芯)61、在压粉磁芯61的表面卷绕有导线62的线圈导体63。
[0132]
实施例
[0133]
以下,示出进一步公开本发明的实施例。应予说明,本发明并不仅限定于这些实施例。
[0134]
[实施例1]
[0135]
将包含第1磁性体粒子、第2磁性体粒子、热固化性树脂和有机溶剂的喷雾液喷雾并干燥,从而制作磁粉。使用平均粒径5μm的羰基铁粉作为第1磁性体粒子,使用平均粒径91nm的锰铁氧体粉作为第2磁性体粒子,使用双酚a型环氧树脂作为热固化性树脂的主剂,使用酚固化剂作为热固化性树脂的固化剂。第1磁性体粒子与第2磁性体粒子的配合比如图7所示。调合时的树脂量为2.4重量%,干燥后的树脂量以通过造粒后的tg分析而测定的实测值计为1.5重量%。实施例1中,可以抑制第1磁性体粒子彼此的凝集,可以得到形成了在第1磁性体粒子的表面埋没了第2磁性体粒子的树脂被膜的磁粉。将得到的磁粉在150℃、690mpa下热压制成型30分钟,之后,在150℃下热处理2小时,制作环状芯试样。
[0136]
[实施例2]
[0137]
使用平均粒径250nm的锰铁氧体粉作为第2磁性体粒子,将第1磁性体粒子与第2磁性体粒子的配合比变为图8所示的值除此以外,通过与实施例1同样的方法制作磁粉,制作环状芯试样。实施例2中,可以抑制第1磁性体粒子彼此的凝集,可以得到形成了在第1磁性体粒子的表面埋没了第2磁性体粒子的树脂被膜的磁粉。
[0138]
对于制作的环状芯试样,使用keysight e4991a rf射频阻抗/材料分析仪来测定磁导率。
[0139]
图7为表示实施例1中的磁导率的频率特性的坐标图。图8为表示实施例2中的磁导
率的频率特性的坐标图。图7和图8中,第1磁性体粒子与第2磁性体粒子的配合比表示为重量比。图7和图8中,用实线表示磁导率的实数部μ',用虚线表示作为损失的虚数部μ"。
[0140]
如图7和图8所示那样,通过在设置于第1磁性体粒子的表面的树脂被膜中混杂第2磁性体粒子,从而可以得到高磁导率。进而,通过将铁氧体磁性粒子用作第2磁性体粒子,从而可以得到直到高频段为止的高磁导率化和低磁芯损耗化。