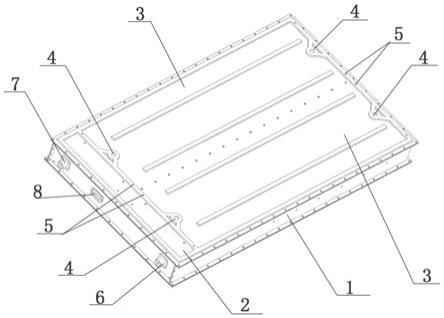
1.本发明属于锂电池制备技术领域,涉及一种安全节能的电池外壳,具体地说是一种单体电芯与电池包合二为一的电池外壳。
背景技术:2.随着科技的发展,锂电池在人们的生产生活中发挥着越来越重要的作用。
3.目前,国内外锂离子电池的制备一般采用以下步骤:首先,将裸体电芯装入电池壳内采用真空烤箱干燥;其次,在恒湿环境中为电池壳内的裸体电芯注液;接着,静置一定时间后在5v低压化成柜上充放电化成;然后,采用激光焊、热封、钢珠等方法密封;最后,电芯分容、分组后串并联制成高压电池包。
4.上述制备过程,工艺复杂、效率低下、耗能耗材量大,制造成本高;而且,制成的锂离子电池使用过程普遍存在安全性能差、能量密度低、循环寿命短的问题。
5.国内外技术研究人员一直致力于锂离子电池的电池壳密封、冷却、加装排气阀等方面的研究,以求改变上述现状,然而收效甚微。
6.通常情况下,传统的电池外壳和电池包外壳是分离的,由单体电芯组成的高压电池包内部存在大量空隙,为防止浸水、结露造成安全事故,人们采用了ip68密封,但是成本高、容易失效。
7.如果能够发明一种单体电芯与电池包合二为一的电池外壳将会极大地改变上述现状。
技术实现要素:8.本发明的目的,是要提供一种单体电芯与电池包合二为一的电池外壳,其结构简单、制造工艺简化、节能降耗,制造成本低。
9.一种单体电芯与电池包合二为一的电池外壳,包括一体结构的壳体,所述壳体内部具有容纳空间、且被分割成相对独立的电控仓和至少一个电池仓,电池仓与电控仓之间的壳体内设置有电池管理信号直采系统;所述电池仓内安装有无电芯高压能量模块,电池仓的仓壁上安装有注液密封阀、液位导电传感器,所述无电芯高压能量模块是指若干个正负极首尾相接的锂离子电池裸体电芯;所述电控仓的仓壁上安装有正极接线端子、负极接线端子、can通讯低压电源接线端子;所述电池管理信号直采系统一方面与无电芯高压能量模块插接采集电压、温度信号,另一方面通过自身的正极接头、负极接头、can接头与正极接线端子、负极接线端子、can通讯低压电源接线端子分别一一对应连接。
10.作为限定:所述电池仓内壁与无电芯高压能量模块之间的所有空隙均用灌封胶灌注密封,灌封后的注液密封阀、液位导电传感器直接转换为安全泄爆阀。
11.作为第二种限定:所述锂离子电池裸体电芯采用磷酸铁锂离子电池裸体电芯、镍钴锰三元锂离子电池裸体电芯、锰酸锂离子电池裸体电芯、钴酸锂离子电池裸体电芯或高镍锂离子电池裸体电芯。
12.作为第三种限定:所述注液密封阀是临时弹性密封阀。
13.作为第四种限定:所述电池管理信号直采系统的启动电源端外接低压电源供电控制,或与无电芯高压能量模块的电源输出端相连,所述电池管理信号直采系统全寿命工作。
14.本发明由于采用了上述的技术方案,其与现有技术相比,所取得的技术进步在于:(1)传统高压电池包制造工艺至少需要二十道工序,而本发明提供的单体电芯与电池包合二为一的电池外壳的制作仅需五道工序,大大简化了锂离子电池及其电池包的制作工艺,工艺流程缩短60%;(2)传统制造工艺中高压电池包中每个单体电芯都有串并联连接件,本发明不需要电芯串并联连接件,所以零部件耗材数量至少减少80%;(3)本发明在锂离子电池及其电池包的制作过程中不再需要恒湿环境和大量的真空烤箱,可节约能耗40%;(4)本发明提供的二合一式结构,其生产过程中采用灌封方法,能够彻底解决壳体密封失效问题,电池使用安全可靠;(5)传统工艺中单体电芯外包装、转极耳、电池模组零部件、电芯串并联耗材等原辅材料在电池包制造成本中的占比已超过15%,本发明提供的二合一式结构不需要这些原辅材料,在电池制造过程中节能降耗,制造成本降低10%~15%,,除此之外,还通过降低能耗、提高效率、提高材料利用率等降低成本,市场前景广阔,经济价值巨大;(6)本发明灌封后的注液密封阀、液位导电传感器直接转换为安全泄爆阀,使用过程中能够及时泄爆,从而完全杜绝使用过程的爆炸事故。
15.本发明属于锂电池制备技术领域,能够应用于新能源汽车及各种化学储能。
附图说明
16.附图用来提供对本发明的进一步理解,并且构成说明书的一部分,与本发明的实施例一起用于解释本发明,并不构成对本发明的限制。
17.在附图中:图1为本发明实施例的外部三维图。
18.图中:1、壳体,2、电控仓,3、电池仓,4、注液密封阀,5、液位导电传感器,6、正极接线端子,7、负极接线端子,8、can通讯低压电源接线端子。
具体实施方式
19.以下结合附图对本发明的优选实施例进行说明。应当理解,此处所描述的优选实施例仅用于说明和解释本发明,并不用于限定本发明。
20.实施例单体电芯与电池包合二为一的电池外壳如图1所示,本实施例包括一体结构的长方体形状的壳体1。壳体1内部具有容纳空间、且被分割成相对独立的电控仓2和两个结构完全相同的电池仓3。电池仓3与电控仓2之间的壳体1内设置有电池管理信号直采系统。本实施例中,壳体1的材料为普碳钢喷塑,通过
一次冲压成型制成。
21.下面以其中一个电池仓3为例进行说明。电池仓3内安装有无电芯高压能量模块,电池仓3的仓壁上两端分别安装一个注液密封阀4、一个液位导电传感器5。无电芯高压能量模块是指若干个正负极首尾相接的锂离子电池裸体电芯且正负极首尾连接处设有电压及温度信号采集插接端子直接插入电池管理信号直采系统,无需导线连接;本实施例中无电芯高压能量模块采用从市场上购买的三十二个磷酸铁锂离子裸体电芯串联而成的无电芯高压能量模块,无电芯高压能量模块的容量及电压规格为100ah/102.4v。
22.如图1所示,电控仓2的仓壁上安装有正极接线端子6、负极接线端子7、can通讯低压电源接线端子8。
23.电池管理信号直采系统一方面与无电芯高压能量模块插接采集电压、温度信号,另一方面通过自身的正极接头、负极接头、can接头与正极接线端子6、负极接线端子7、can通讯低压电源接线端子8分别一一对应连接。电池管理信号直采系统采用外接dc12v低压电源供电启动,上限压dc116.8v,下限压dc89.6v,限电流200a,限温度55℃,且具有限电流、限电压、限温度充放电截止功能。正极接线端子6、负极接线端子7、can通讯低压电源接线端子8再分别连接外部dc400v高压充放电柜的相应接线端子后对无电芯高压能量模块进行特殊制式的高压充放电化成。其中,正极接线端子6、负极接线端子7在非工作状态输出电压电流为零。
24.本实施例中,注液密封阀4是临时弹性密封阀,具体为设置在壳体1上的pe材料密封膜,可以刺破可以自封闭。氮气流洗无电芯高压能量模块后含水量150ppm。液位导电传感器5采用一对包覆pp绝缘层的直径为1mm的紫铜探针,其接触电解液后导通传出液位信号,检测精度高,能够使注液重量误差小于2.5%。
25.制作时,用三通针管刺破注液密封阀4对密封在电池仓3内的无电芯高压能量模块充氮气抽真空流洗干燥之后再采用外界的电解液注液机注入电解液,在此过程中,液位导电传感器5的信号输出端与电解液注液机的反馈信号输入端相连,实时监测液位并反馈至电解液注液机,电解液注液机根据反馈信息控制注液量,当达到预设液位时,电解液注液机停止注液。在本实施例中,为了保证产品质量,电解液是从电池仓3的一端注入从另一端流出的,所以注液密封阀4要成对使用;为了不造成电解液注入量浪费或不足,液位导电传感器5也是成对使用。
26.最后,将注液密封阀4、液位导电传感器5、电池管理信号直采系统、正极接线端子6、负极接线端子7、can通讯低压电源接线端子8以及无电芯高压能量模块一并采用两组分ab结构树脂胶灌注密封在电池仓3、电控仓2和壳体1的相应位置,仅留正极接线端子6、负极接线端子7、can通讯低压电源接线端子8对壳体1外输入输出电压电流。
27.电池仓3的内壁与无电芯高压能量模块之间的所有空隙均由两组分ab结构树脂胶灌注密封,灌封后的注液密封阀4、液位导电传感器5直接转换为安全泄爆阀,在温度180℃时注液密封阀4中的pe膜熔化放出气体,安全可靠。
28.表1
如表1所示,是本实施例的对比测试实验,其中对比组为传统单体电芯电池,实验组1和实验组2均为本实施例提供的单体电芯与电池包合二为一的电池外壳。从测试结果可以看出,本实施例提供的电池包合二为一的电池外壳的测试结果各项指标均优于或明显优于对比组,特别是电池容量、密度、寿命更是具有很大的提升,此外其在使用中安全性明显优于对比组,制造成本大大降低。
29.本实施例只是以锂离子电池裸体电芯采用磷酸铁锂离子电池裸体电芯为例进行说明,实际生产中还可采用镍钴锰三元锂离子电池裸体电芯、锰酸锂离子电池裸体电芯、钴酸锂离子电池裸体电芯或高镍锂离子电池裸体电芯。本实施例中,电池仓3的数量以及磷酸铁锂离子裸体电芯的数量只是为了举例说明,实际上电池仓3也可以为一个或多个,磷酸铁锂离子裸体电芯的数量可根据实际需要改变。
30.实际上,也可在制作时直接将电池管理信号直采系统的启动电源与无电芯高压能量模块的电源输出端相连,采用无电芯高压能量模块的电源为其供电,电池管理信号直采系统全寿命工作。