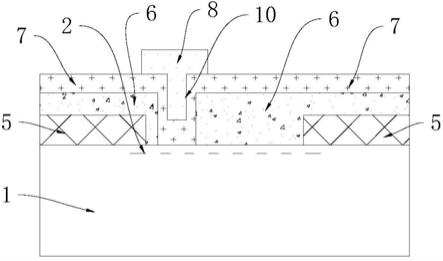
1.本发明属于金刚石场效应晶体管器件技术领域,更具体地说,是涉及一种金刚石场效应晶体管及制备方法。
背景技术:2.目前,金刚石场效应晶体管的研究主要基于氢终端结构的二维空穴气导电,氢终端金刚石暴露在空气中若干小时,表面会出现某些带电离子(如hco3+,oh
‑
,hco3‑
,no3‑
等)组成的吸附物,由于氢终端金刚石负的电子亲和势,其表面的电子会转移到吸附层中,从而在金刚石表面产生一层二维空穴气,形成p型导电沟道。目前氢终端金刚石的载流子迁移率通常<200cm2/v
·
s,方阻~10,000ω,载流子面密度~10
12
‑
10
14
/cm2,较低的迁移率和较高的方阻,严重制约了金刚石场效应晶体管的直流和射频性能。理论分析表明,氢终端金刚石与介质层之间的界面态引入的离化杂质散射是制约其迁移率的主要因素之一,目前氢终端金刚石与介质层之间的界面态密度通常在10
12
/cm2,迁移率可达到~1000cm2/v
·
s;界面态密度降低至10
10
/cm2,迁移率可达到~3000cm2/v
·
s;因此解决金刚石与介质之间界面问题,降低界面态密度是实现高性能金刚石场效应晶体管的关键。
技术实现要素:3.本发明的目的在于提供一种金刚石场效应晶体管及制备方法,旨在解决金刚石场效应晶体管的界面态密度高的技术问题。
4.为实现上述目的,本发明采用的技术方案是:提供一种金刚石场效应晶体管,包括金刚石衬底、氢终端、欧姆接触金属层、介质层、h
‑
bn介质层和栅金属层,氢终端形成于所述金刚石衬底的上表面;欧姆接触金属层形成于所述氢终端的上表面,且所述欧姆接触金属层包括间隔设置的两个电极,所述欧姆接触金属层所覆盖的至少部分氢终端以及所述两个电极之间的氢终端为导电沟道区;介质层形成于所述欧姆接触金属层和所述氢终端上,且所述介质层在与所述导电沟道区对应的区域形成有裸露所述氢终端的刻蚀槽;h
‑
bn介质层形成于所述介质层上和所述刻蚀槽内,且所述h
‑
bn介质层与所述刻蚀槽对应的区域设置有栅金属槽,所述栅金属槽未裸露所述氢终端;栅金属层形成于所述栅金属槽内和与所述栅金属槽相邻的所述h
‑
bn介质层上。
5.在一种可能的实现方式中,在所述介质层上表面涂覆光刻胶,并通过刻蚀工艺刻蚀所述介质层,以形成所述刻蚀槽,刻蚀后在氢气环境下进行退火处理。
6.本发明提供的金刚石场效应晶体管的有益效果在于:与现有技术相比,本发明金刚石场效应晶体管包括金刚石衬底、氢终端、欧姆接触金属层、介质层、h
‑
bn介质层和栅金属层,氢终端形成于金刚石衬底的上表面,欧姆接触金属层形成于氢终端的上表面,且欧姆接触金属层包括间隔设置的两个电极,欧姆接触金属层所覆盖的至少部分氢终端以及两个电极之间的氢终端为导电沟道区,介质层形成于欧姆接触金属层和氢终端上,且介质层在与导电沟道区对应的区域形成有裸露氢终端的刻蚀槽,h
‑
bn介质层形成于介质层上和刻蚀
槽内,且h
‑
bn介质层与刻蚀槽对应的区域设置有栅金属槽,栅金属槽未裸露氢终端,栅金属层形成于栅金属槽内和与栅金属槽相邻的h
‑
bn介质层上,解决了金刚石场效应晶体管的界面态密度高的技术问题,具有降低金刚石场效应晶体管的界面态密度,提升器件的直流和射频性能的技术效果。
7.本发明还提供了一种金刚石场效应晶体管的制备方法,包括:
8.在金刚石衬底上形成氢终端;
9.在所述氢终端金刚石上形成欧姆接触金属层,所述欧姆接触金属层包括间隔设置的两个电极,所述欧姆接触金属层所覆盖的至少部分氢终端以及所述两个电极之间的氢终端为导电沟道区;
10.在所述欧姆接触金属层和所述氢终端上形成介质层,在所述介质层在与所述导电沟道区对应的区域形成有裸露所述氢终端的刻蚀槽;
11.在所述介质层上和所述刻蚀槽内形成h
‑
bn介质层,在所述h
‑
bn介质层与所述刻蚀槽对应的区域设置有栅金属槽,所述栅金属槽未裸露所述氢终端;
12.在所述栅金属槽内和与所述栅金属槽相邻的所述h
‑
bn介质层上形成栅金属层。
13.在一种可能的实现方式中,在金刚石衬底上形成氢终端,包括:
14.在所述氢终端金刚石上表面通过蒸发金属的方式制备牺牲层,所述牺牲层的金属为au。
15.在一种可能的实现方式中,在所述氢终端金刚石上形成欧姆接触金属层,包括:
16.在所述氢终端金刚石上表面通过沉积方式沉积欧姆接触金属,以形成欧姆接触金属层;
17.通过湿法腐蚀方式或干法刻蚀方式去除所述氢终端金刚石上的所述牺牲层。
18.在一种可能的实现方式中,在所述欧姆接触金属层和所述氢终端上形成介质层,在所述介质层在与所述导电沟道区对应的区域形成有裸露所述氢终端的刻蚀槽,包括:
19.在所述介质层上涂覆光刻胶,并通过刻蚀方式刻蚀所述介质层,以形成所述刻蚀槽,刻蚀后置于氢气条件下进行退火;
20.所述介质层为单层介质或多层介质,所述介质层的厚度为1
‑
500nm;
21.通过刻蚀方式刻蚀所述介质层选用的方式为干法刻蚀或湿法刻蚀或干法与湿法结合刻蚀。
22.在一种可能的实现方式中,在所述介质层上和所述刻蚀槽内形成h
‑
bn介质层,在所述栅金属槽内和与所述栅金属槽相邻的所述h
‑
bn介质层上形成栅金属层,包括:
23.通过干法转移或湿法转移的方式在所述介质层上和所述刻蚀槽内转移h
‑
bn介质层,所述h
‑
bn介质层为一层介质或多层介质;
24.通过沉积方式沉积栅金属,以形成所述栅金属层,并剥离形成栅极。
25.在一种可能的实现方式中,所述欧姆接触金属层的金属至少为一种金属,或者可通过合金工艺形成的多种金属。
26.在一种可能的实现方式中,所述金刚石衬底为单晶金刚石或多晶金刚石,所述氢终端通过氢等离子体处理并在氢气条件下退火处理或在氢气条件下外延生长获得。
27.在一种可能的实现方式中,所述栅金属层的形貌为直栅、t型栅、tt型栅、ttt型栅、u型栅、y型栅中的一种或多种组合。
28.本发明提供的金刚石场效应晶体管的制备方法有益效果在于:与现有技术相比,本发明金刚石场效应晶体管的制备方法包括在金刚石衬底上形成氢终端
‑
在氢终端金刚石上形成欧姆接触金属层
‑
在欧姆接触金属层上和氢终端上形成介质层
‑
在介质层上形成刻蚀槽
‑
在介质层上和刻蚀槽内形成h
‑
bn介质层
‑
在h
‑
bn介质层与刻蚀槽对应的区域设置有栅金属槽
‑
在栅金属槽内和与栅金属槽相邻的h
‑
bn介质层上形成栅金属层。本发明提供的金刚石场效应晶体管及制备方法,解决了金刚石场效应晶体管的界面态密度高的技术问题,具有降低金刚石场效应晶体管的界面态密度,提升器件的直流和射频性能的技术效果。
附图说明
29.为了更清楚地说明本发明实施例中的技术方案,下面将对实施例或现有技术描述中所需要使用的附图作简单地介绍,显而易见地,下面描述中的附图仅仅是本发明的一些实施例,对于本领域普通技术人员来讲,在不付出创造性劳动的前提下,还可以根据这些附图获得其他的附图。
30.图1为本发明实施例提供的金刚石场效应晶体管的结构示意图;
31.图2为本发明实施例提供的金刚石场效应晶体管的制备方法流程图。
32.附图标记说明:
33.1、金刚石衬底;2、氢终端;3、牺牲层;4、有源区;5、欧姆接触金属层;6、介质层;7、h
‑
bn介质层;8、栅金属层;9、刻蚀槽;10、栅金属槽。
具体实施方式
34.为了使本发明所要解决的技术问题、技术方案及有益效果更加清楚明白,以下结合附图及实施例,对本发明进行进一步详细说明。应当理解,此处所描述的具体实施例仅仅用以解释本发明,并不用于限定本发明。
35.请一并参阅图1,现对本发明提供的金刚石场效应晶体管进行说明。所述金刚石场效应晶体管,包括金刚石衬底1、氢终端2、欧姆接触金属层5、介质层6、h
‑
bn介质层7和栅金属层8,氢终端2形成于金刚石衬底1的上表面;欧姆接触金属层5形成于氢终端2的上表面,且欧姆接触金属层5包括间隔设置的两个电极,欧姆接触金属层5所覆盖的至少部分氢终端2以及两个电极之间的氢终端2为导电沟道区;介质层6形成于欧姆接触金属层5和氢终端2上,且介质层6在与导电沟道区对应的区域形成有裸露氢终端的刻蚀槽9;h
‑
bn介质层7形成于介质层上和刻蚀槽9内,且h
‑
bn介质层7与刻蚀槽9对应的区域设置有栅金属槽10,栅金属槽10未裸露氢终端2;栅金属层8形成于栅金属槽10内和与栅金属槽10相邻的h
‑
bn介质层7上。
36.本发明提供的金刚石场效应晶体管的有益效果在于:与现有技术相比,本发明金刚石场效应晶体管包括金刚石衬底1、氢终端2、欧姆接触金属层5、介质层6、h
‑
bn介质层7和栅金属层8,氢终端2形成于金刚石衬底1的上表面;欧姆接触金属层5形成于氢终端2的上表面,且欧姆接触金属层5包括间隔设置的两个电极,欧姆接触金属层5所覆盖的至少部分氢终端2以及两个电极之间的氢终端2为导电沟道区;介质层6形成于欧姆接触金属层5和氢终端2上,且介质层6在与导电沟道区对应的区域形成有裸露氢终端的刻蚀槽9;h
‑
bn介质层7形成于介质层上和刻蚀槽9内,且h
‑
bn介质层7与刻蚀槽9对应的区域设置有栅金属槽10,栅
金属槽10未裸露氢终端2;栅金属层8形成于栅金属槽10内和与栅金属槽10相邻的h
‑
bn介质层7上,解决了金刚石场效应晶体管的界面态密度高的技术问题,具有降低金刚石场效应晶体管的界面态密度,提升器件的直流和射频性能的技术效果。
37.在一些实施例中,请参阅图1,在介质层6上表面涂覆光刻胶,并通过刻蚀工艺刻蚀介质层6,以形成所述刻蚀槽9,刻蚀后在氢气环境下进行退火处理。
38.具体的,在氢终端2金刚石上制备有牺牲层3,在牺牲层3中部为有源区4;欧姆接触金属层5位于有源区4外部的被去除牺牲层3的金刚石衬底1上;介质层6位于金刚石衬底1上被去除的有源区4内的牺牲层3上和欧姆接触金属层5上。在牺牲层3上涂覆光刻胶并覆盖有源区4,有源区4为器件的导电沟道区,去除有源区4外部的牺牲层3,通过沉积方式沉积欧姆接触金属层5。
39.请参阅图2,本发明还提供了一种金刚石场效应晶体管的制备方法,包括:
40.在金刚石衬底1上形成氢终端2;
41.在所述氢终端2金刚石上形成欧姆接触金属层5,所述欧姆接触金属层5包括间隔设置的两个电极,所述欧姆接触金属层5所覆盖的至少部分氢终端2以及所述两个电极之间的氢终端为导电沟道区;
42.在所述欧姆接触金属层5和所述氢终端2上形成介质层6,在所述介质层6在与所述导电沟道区对应的区域形成有裸露所述氢终端2的刻蚀槽9;
43.在所述介质层6上和所述刻蚀槽9内形成h
‑
bn介质层7,在所述h
‑
bn介质层7与所述刻蚀槽9对应的区域设置有栅金属槽10,所述栅金属槽10未裸露所述氢终端2;
44.在所述栅金属槽10内和与所述栅金属槽10相邻的所述h
‑
bn介质层7上形成栅金属层8。
45.本发明提供的金刚石场效应晶体管的制备方法有益效果在于:与现有技术相比,本发明金刚石场效应晶体管的制备方法包括在金刚石衬底上形成氢终端2
‑
在氢终端2金刚石上形成欧姆接触金属层5
‑
在欧姆接触金属层5上和氢终端2上形成介质层6
‑
在介质层6上形成刻蚀槽9
‑
在介质层6上和刻蚀槽9内形成h
‑
bn介质层7
‑
在h
‑
bn介质层7与刻蚀槽9对应的区域设置有栅金属槽10
‑
在栅金属槽10内和与栅金属槽10相邻的h
‑
bn介质层7上形成栅金属层8。本发明提供的金刚石场效应晶体管及制备方法,解决了金刚石场效应晶体管的界面态密度高的技术问题,具有降低金刚石场效应晶体管的界面态密度,提升器件的直流和射频性能的技术效果。
46.具体的,在氢终端2金刚石上制备有牺牲层3,在牺牲层3中部为有源区4;欧姆接触金属层5位于有源区4外部的被去除牺牲层3的金刚石衬底1上;介质层6位于金刚石衬底1上被去除的有源区4内的牺牲层3上和欧姆接触金属层5上。在牺牲层3上涂覆光刻胶并覆盖有源区4,有源区4为器件的导电沟道区,去除有源区4外部的牺牲层3,通过沉积方式沉积欧姆接触金属层5。
47.取单晶金刚石衬底1,表面通过微波等离子体化学气相沉积设备在氢等离子体的环境下,温度为850℃的条件下处理10分钟,形成具有氢终端2的金刚石衬底1。
48.在一些实施例中,请参阅图2,在金刚石衬底1上形成氢终端2,包括:
49.在所述氢终端2金刚石上表面通过蒸发金属的方式制备牺牲层,所述牺牲层的金属为au。
50.蒸发金属的方式可采用现有技术手段实现,具体为蒸发厚度为30nm的金属au作为牺牲层3。
51.在氢终端2的金刚石衬底1的牺牲层3上进行光刻,光刻胶覆盖有源区4,有源区4为器件的导电沟道区,以光刻胶为掩膜,将有源区4外部的牺牲层3au通过碘/碘化钾溶液湿法腐蚀去除,氢终端2的金刚石衬底1导电沟道通过氧等离子体轰击去除,实现台面隔离。
52.在一些实施例中,请参阅图2,在所述氢终端2金刚石上形成欧姆接触金属层5,包括:
53.在所述氢终端2金刚石上表面通过沉积方式沉积欧姆接触金属,以形成欧姆接触金属层5;
54.通过湿法腐蚀方式或干法刻蚀方式去除所述氢终端2金刚石上的所述牺牲层3。
55.具体的,通过湿法腐蚀方式或干法刻蚀方式去除位于有源区4外部的牺牲层3,通过干法刻蚀方式去除有源区4内的牺牲层3。通过沉积方式、湿法腐蚀方式和干法刻蚀方式均可采用现有技术手段实现。
56.在一些实施例中,请参阅图2,在所述欧姆接触金属层5和所述氢终端2上形成介质层6,在所述介质层6在与所述导电沟道区对应的区域形成有裸露所述氢终端2的刻蚀槽9,包括:
57.在所述介质层6上涂覆光刻胶,并通过刻蚀方式刻蚀所述介质层6,以形成所述刻蚀槽9,刻蚀后置于氢气条件下进行退火;
58.所述介质层6为单层介质或多层介质,所述介质层6的厚度为1
‑
500nm;
59.通过刻蚀方式刻蚀所述介质层6选用的方式为干法刻蚀或湿法刻蚀或干法与湿法结合刻蚀。
60.通过碘/碘化钾溶液腐蚀金刚石衬底1上的牺牲层3au,并通过原子层沉积技术沉积60nm厚度sio2介质层6。
61.通过电子束在介质层6上光刻500nm长度的图形,以光刻胶为掩膜,将该区域的sio2介质层6通过干法刻蚀完全去除,刻蚀后在氢气气氛下退火,修复金刚石衬底1表面的氢终端2。
62.刻蚀槽9的样式在本实施例中不作限制,能完成刻蚀即可。优选为立方体形状的凹槽。
63.在一些实施例中,请参阅图2,在所述介质层6上和所述刻蚀槽9内形成h
‑
bn介质层7,在所述栅金属槽10内和与所述栅金属槽10相邻的所述h
‑
bn介质层7上形成栅金属层8,包括:
64.通过干法转移或湿法转移的方式在所述介质层6上和所述刻蚀槽9内转移h
‑
bn介质层7,所述h
‑
bn介质层7为一层介质或多层介质;
65.通过沉积方式沉积栅金属,以形成所述栅金属层8,并剥离形成栅极。
66.具体的,光刻1微米长度的栅,沉积栅金属al/au,剥离形成栅极。
67.在一些实施例中,请参阅图2,所述欧姆接触金属层5的金属至少为一种金属,或者可通过合金工艺形成的多种金属。
68.优选的,欧姆接触金属层5的金属为三种,并通过合金工艺形成,为ti/pt/au,并在700℃的温度下进行合金,合金时间为1小时,以形成欧姆接触。
69.在一些实施例中,请参阅图2,所述金刚石衬底1为单晶金刚石或多晶金刚石,所述氢终端2通过氢等离子体处理并在氢气条件下退火处理或在氢气条件下外延生长获得。
70.在一些实施例中,请参阅图2,所述栅金属层8的形貌为直栅、t型栅、tt型栅、ttt型栅、u型栅、y型栅中的一种或多种组合。栅金属层8形成在位于h
‑
bn介质层7上的与刻蚀槽9对应的栅金属槽10内。
71.以上所述仅为本发明的较佳实施例而已,并不用以限制本发明,凡在本发明的精神和原则之内所作的任何修改、等同替换和改进等,均应包含在本发明的保护范围之内。