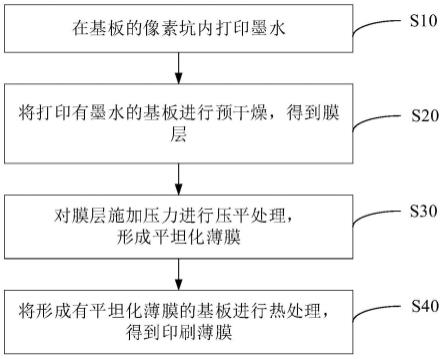
1.本发明涉及喷墨打印技术领域,特别涉及一种印刷薄膜及其制备方法。
背景技术:2.喷墨打印是在计算机控制下将功能材料的墨水按需逐滴喷射到对应位置上并形成图案的成膜方式,具有操作简单、非接触、无掩模、设备成本低、材料利用率高等优点,被认为是实现柔性大面积oled/qled显示器的有效途径。在oled和qled显示行业,常常采用喷墨打印技术对基底的打印区域进行打印,形成印刷薄膜。然而,打印的液滴在干燥过程常常会伴随“咖啡环现象”的发生,即干燥过程中液滴在边缘接触线处溶剂的挥发速度较快而形成由内向外的毛细流动,从而把溶质带到接触线处沉淀而形成薄膜周围厚中间薄的现象。对于显示器件而言,印刷薄膜的不均匀性不仅会降低显示器件的发光均匀性,而且会严重影响其寿命。
3.传统的提高印刷薄膜均匀性的方法主要包括优化墨水溶剂组分、像素限定层(bank)性质和形状、干燥设备和条件等。其中,通过墨水及像素限定层的优化来提高印刷薄膜的均匀性时,不仅要考虑墨水的成膜均匀性,还得兼顾墨水打印性、器件结构等多种因素,调控过程比较复杂,同时也会限制材料体系的选择,且器件结构设计上存在一定的局限性;当打印材料发生改变时,可能相应的墨水溶剂成膜、像素限定层性质等也需要同时调整。通过优化干燥设备和条件主要是设计特定的温度控制装置来控制墨水的温度,但由于墨水体系的多样性和像素限定层形状、大小的差异,以及对应rgb像素(红r、绿g、蓝b)不同的目标器件厚度不同,打印的墨水体积存在差异,而这些差异使得干燥后生成的薄膜形貌也会存在差异,从而对打印薄膜的均匀性改善存在一定的局限性。
技术实现要素:4.基于此,本发明提供了一种印刷薄膜及其制备方法,该制备方法可有效提高印刷薄膜的均匀性。
5.本发明解决上述技术问题的技术方案如下。
6.一种印刷薄膜的制备方法,包括如下步骤:
7.在基板上形成像素限定层,所述像素限定层具有像素坑;
8.在所述像素坑内设置墨水;
9.将设置有所述墨水的基板进行预干燥,得到膜层;
10.对所述膜层施加压力以进行压平处理,以使所述像素坑内的膜层平坦化并形成平坦化薄膜;
11.将形成有所述平坦化薄膜的基板进行热处理,得到印刷薄膜。
12.在其中一些实施例中,印刷薄膜的制备方法中,所述膜层不凸出于所在的像素坑。
13.在其中一些实施例中,印刷薄膜的制备方法中,所述预干燥的绝对压强为0.1torr~400torr,温度为20℃~30℃,时间为30s~1000s。
14.在其中一些实施例中,印刷薄膜的制备方法中,所述压平处理的方式为对所述膜层施加保护性气体,施加的所述保护性气体的气体压力大于所述膜层的表面张力。
15.在其中一些实施例中,印刷薄膜的制备方法中,通过控制所述保护性气体的通气量以控制施加的所述保护性气体的气体压力大小,所述保护性气体的通气量为0.5mpa~1mpa。
16.在其中一些实施例中,印刷薄膜的制备方法中,所述保护性气体选自氮气、氩气、氦气、氖气、氪气和氙气中的至少一种。
17.在其中一些实施例中,印刷薄膜的制备方法中,施加的所述保护性气体的气体压力方向垂直于所述基板所在的平面。
18.在其中一些实施例中,印刷薄膜的制备方法中,所述墨水的溶剂为单一溶剂,所述单一溶剂的沸点大于200℃。
19.在其中一些实施例中,印刷薄膜的制备方法中,所述墨水为oled墨水,所述oled墨水的溶剂包括高沸点溶剂和低沸点溶剂;
20.其中,所述高沸点溶剂选自3,4-二甲基苯甲醚、1,3-二甲基苯甲醚、1,2,4-三甲氧基苯、正十二烷、异佛尔酮和苯基环己烷中的至少一种;
21.所述低沸点溶剂选自甲苯、对二甲苯、氯苯、苯甲醚、氮苯、均三甲苯和乙酸丁酯中的至少一种。
22.在其中一些实施例中,印刷薄膜的制备方法中,所述墨水为qled墨水,所述qled墨水的溶剂包括高沸点的非极性溶剂和低沸点的极性溶剂;
23.其中,所述高沸点的非极性溶剂的沸点大于200℃,所述高沸点的非极性溶剂为卤代芳香烃及其衍生物;
24.所述低沸点的极性溶剂的沸点小于200℃,所述低沸点的极性溶剂选自为醇、酯和醚中的至少一种。
25.在其中一些实施例中,印刷薄膜的制备方法中,所述高沸点的非极性溶剂选自邻二氯苯、间二氯苯和邻溴甲苯中的至少一种,所述低沸点的极性溶剂选自甲醇、异丙醇、2-甲氧基乙醇、醋酸乙酯、醋酸丁酯、乙二醇一丁基醚和二丙二醇一甲基醚中的至少一种。
26.本发明还提供了一种发光器件,所述发光器件包括发光层和功能层;
27.所述发光层和/或所述功能层为采用如上所述的制备方法制备得到。
28.与现有技术相比较,本发明的印刷薄膜的制备方法具有如下有益效果:
29.本发明将像素坑内设置有墨水的基板进行预干燥,去除大部分溶剂,避免墨水干燥过度形成咖啡环固体薄膜。进一步地,对预干燥形成的膜层施加压力以进行压平处理,以使像素坑内高粘度液体状的膜层平坦化并形成平坦化薄膜,有效减小或消除在后续热处理过程中的像素坑内边缘与中心的溶剂挥发差异,使最终像素坑内平坦化薄膜中的溶质在热处理过程中均匀沉积,从而从本质上抑制了咖啡环的形成。同时,由于本发明先通过干燥去除打印墨水的大部分溶剂,再进行压平处理对预干燥的高粘度膜层进行平坦化,如此减小了打印先后顺序、打印不同体积以及打印中心与边缘由于溶剂挥发速率差异造成的形貌差异,进一步提高了打印薄膜的均匀性。
30.本发明的印刷薄膜的制备方法,使制备得到的印刷薄膜的均匀性较好。该印刷薄膜可为发光层或者功能层,该制备方法可用于制备显示器件中的发光层或者功能层,进而
有利于显示器件的发光均匀性、器件寿命的提升,确保了显示器件的质量。
附图说明
31.为了更清楚地说明本发明具体实施方式或现有技术中的技术方案,下面将对具体实施方式或现有技术描述中所需要使用的附图作简单地介绍,显而易见地,下面描述中的附图是本发明的一些实施方式,对于本领域普通技术人员来讲,在不付出创造性劳动的前提下,还可以根据这些附图获得其他的附图。
32.图1为实施例1的印刷薄膜的制备流程图;
33.图2为实施例1的印刷薄膜的制备流程的结构示意图;
34.图3为一示例的像素坑内打印的墨水的示意图;
35.图4为另一示例的像素坑内打印的墨水的示意图;
36.图5为一示例的像素坑内形成的印刷薄膜的示意图;
37.图6为另一示例中像素坑内形成的印刷薄膜的示意图;
38.图7为实施例像素内薄膜形貌一维截面图;
39.图8为对比例像素内薄膜形貌一维截面图;
40.附图标记说明:
41.100:基板;110:像素限定层;200:墨水;210:膜层;220:平坦化薄膜;230:印刷薄膜。
具体实施方式
42.以下结合具体实施例对本发明的印刷薄膜及其制备方法作进一步详细的说明。本发明可以以许多不同的形式来实现,并不限于本文所描述的实施方式。相反地,提供这些实施方式的目的是使对本发明公开内容理解更加透彻全面。
43.除非另有定义,本文所使用的所有的技术和科学术语与属于本发明的技术领域的技术人员通常理解的含义相同。本文中在本发明的说明书中所使用的术语只是为了描述具体的实施例的目的,不是旨在于限制本发明。本文所使用的术语“和/或”包括一个或多个相关的所列项目的任意的和所有的组合。
44.请参阅图1和图2,本发明一实施方式提供了一种印刷薄膜的制备方法,包括步骤s10~s40。
45.步骤s10:在基板100上形成像素限定层110,像素限定层110具有像素坑;在基板的像素坑内设置墨水200。可以理解,像素界定层的像素坑为多个,且多个像素坑呈阵列排布。
46.步骤s20:将打印有墨水200的基板100进行预干燥,得到膜层210。
47.步骤s30:对膜层210施加压力以进行压平处理,以使像素坑内的膜层210平坦化并形成平坦化薄膜220。
48.步骤s40:将形成有平坦化薄膜220的基板进行热处理,得到印刷薄膜230。
49.可以理解,步骤s20中得到的膜层210为粘度比原始墨水粘度大的液体,即形成在基板100上的墨水在预干燥过程中,墨水中的溶剂大部分会挥发,在显微镜下观察呈半干湿膜的状态,需要说明的是,该半干湿膜应做广义理解,预干燥后形成的膜层为待成膜状态,后续依次进行压平处理以及热处理后可以形成最终的印刷薄膜,而此时膜层呈待成膜状
态,膜层表面的表面张力大于预干燥前形成在基板上的墨水,预干燥后的膜层表面呈不流动状态,内部具有未干燥的溶剂。如此可以避免墨水干燥过度已形成咖啡环固体薄膜。
50.在其中一些示例中,步骤s20中,膜层210不凸出于所在的像素坑,即:膜层210中墨水200的最高位置不凸出于所在的像素坑。换言之,膜层210的最高位置不高于所在的像素限定层110的上顶面。通过控制膜层210不凸出于所在的像素坑,可防止后续对膜层210进行压平处理时,墨水200体积过多溢出特定的像素坑出现混色等问题
51.进一步地,基板100可以是刚性基板或者柔性基板。
52.在其中一些示例中,步骤s20中,可选的,膜层210的最高位置低于所在的像素坑的高度;换言之,膜层210中墨水200的最高液面低于所在的像素坑的高度。
53.喷墨打印时,不同像素坑内打印的墨水体积可能会存在差异。例如在一些像素坑内打印的墨水的最高液面高于像素坑,但未在像素坑顶部铺展润湿,如图3所示。例如在另一些像素坑内打印的墨水最高液面低于像素坑,如图4所示。而像素坑内墨水的打印体积或者打印先后差异会造成打印干燥前不同像素内的墨水体积差异,导致在干燥过程中像素间溶剂挥发差异,最终形成的薄膜形貌不同。例如,一些像素坑内最终形成的薄膜形貌,周围厚中间薄,如图5所示。例如在另一些像素坑内最终形成的薄膜形貌,周围薄中间凸,如图6所示。
54.对于显示器件而言,印刷薄膜的不均匀性不仅会降低显示器件的发光均匀性,而且会严重影响其寿命。
55.本发明将像素坑内打印有墨水的基板进行预干燥,去除大部分溶剂,形成膜层(如图2中的b)在显微镜下呈半干湿膜的状态,避免墨水干燥过度已形成咖啡环固体薄膜,以及控制膜层不凸出于所在的像素坑,可防止后续对膜层进行压平处理时,墨水体积过多溢出特定的像素坑出现混色等问题。进一步地,对膜层施加压力以进行压平处理,以使像素坑内的膜层平坦化并形成平坦化薄膜(如图2中的c),有效减小或消除了在后续热处理过程中的像素坑内边缘与中心的溶剂挥发差异,使最终像素坑内平坦化薄膜中的溶质在热处理过程中均匀沉积,从而从本质上抑制了咖啡环的形成。同时,由于本发明先通过干燥去除打印墨水的大部分溶剂,再进行压平处理对预干燥形成的的高粘度液体状的膜层进行平坦化,如此减小了打印先后顺序、打印不同体积以及打印中心与边缘由于溶剂挥发速率差异造成的形貌差异,进一步提高了打印薄膜的均匀性。
56.在其中一些示例中,步骤s10中,打印在像素坑内的墨水体积可以相同或者不同,但打印墨水的最大体积不能溢出像素坑,最小体积必须对像素坑底面进行完全浸润铺展。可以理解,打印的墨水在表面张力作用下形成如图2中a所示的上凸的形貌,即打印的墨水形成凸液面。
57.在其中一些示例中,步骤s10中,墨水的溶剂为单一溶剂,单一溶剂的沸点大于200℃。
58.在其中一些示例中,步骤s10中,墨水为oled墨水,oled墨水的溶剂包括高沸点溶剂和低沸点溶剂,高沸点溶剂选自3,4-二甲基苯甲醚、1,3-二甲基苯甲醚、1,2,4-三甲氧基苯、正十二烷、异佛尔酮和苯基环己烷中的至少一种,低沸点溶剂选自甲苯、对二甲苯、氯苯、苯甲醚、氮苯、均三甲苯和乙酸丁酯中的至少一种。
59.在其中一些示例中,步骤s10中,墨水为qled墨水,qled墨水的溶剂包括高沸点的
非极性溶剂,高沸点的非极性溶剂的沸点大于200℃。可选地,高沸点的非极性溶剂为卤代芳香烃及其衍生物。进一步地,高沸点的非极性溶剂选自邻二氯苯、间二氯苯和邻溴甲苯中的至少一种。
60.可以理解,在其中一些示例中,oled墨水选自hil墨水、htl墨水、eml墨水和etl墨水中的至少一种。
61.在其中一些示例中,步骤s10中,墨水为qled墨水,qled墨水的溶剂还包括表面张力调节剂。可选地,表面张力调节剂为低沸点的极性溶剂,低沸点的极性溶剂的沸点小于200℃。进一步地,低沸点的极性溶剂选自为醇、酯和醚中的至少一种。可选地,低沸点的极性溶剂选自甲醇、异丙醇、2-甲氧基乙醇、醋酸乙酯、醋酸丁酯、乙二醇一丁基醚和二丙二醇一甲基醚中的至少一种。
62.可以理解,在其中一些示例中,qled墨水选自hil墨水、htl墨水、qd墨水、zno和znmgo墨水中的至少一种。
63.可以理解,在高沸点的非极性溶剂的基础上加入表面张力调节剂,可以优化量子点墨水的粘度和表面张力。
64.打印墨水的溶剂需要较高的沸点,这样在打印过程中墨水的挥发速率相对较慢,减小了随着喷头处墨水中溶剂挥发溶质析出造成喷嘴的堵塞问题,提高了打印的稳定性。另外,采用高沸点和低沸点的共混溶剂体系,利用墨水中高低沸点的不同挥发速率,在液滴内部形成由外向内的马兰哥尼流毛细流动(marangoni flow),进一步促使干燥中溶质的均匀沉积。
65.在其中一些示例中,步骤s20中,预干燥的绝对压强为0.1torr~400torr,温度为20℃~30℃,时间为30s~1000s。可以理解,在一具体示例中,将打印有墨水的基板转入到真空干燥设备(vcd)中,抽真空去除墨水中大部分溶剂,像素坑内液面高度下降,形成高粘度液体状的膜层,如图6中的b所示,膜层为凸液面。
66.可选地,预干燥的绝对压强为1torr~100torr,温度为23℃~28℃,时间为30s~300s。预干燥的绝对压力为40torr,温度为15℃,时间为30s。
67.可以理解,在室温下以较慢的抽速对墨水进行抽真空干燥,确保溶剂缓慢挥发,去除大部分溶剂而不发生溶质大量沉积,形成半干的湿膜状态。依据打印墨水的沸点及体积可以优化真空干燥速率,体积大或者沸点高的墨水在此过程干燥速率相对慢;小体积或者低沸点的墨水的干燥速率快,以平衡墨水溶剂挥发与毛细流动平衡,抑制在干燥过程中墨水中溶质的沉积。
68.在其中一些示例中,步骤s30中,压平处理为对膜层的整个区域施加压力进行压平。可以理解,对膜层局部施加压力会使膜层受力不均,导致墨水左右晃动,减小了相邻像素液滴之间的融合,从而造成成膜不均匀;而对膜层的整个区域施加压力,可有效防止受力不均,降低串色、mura等问题。
69.在其中一些示例中,步骤s30中,压平处理的方式为对膜层施加保护性气体,施加的保护性气体的气体压力大于膜层的表面张力。可以理解,施加的压力太小,无法将上凸液面压平;而保护性气体可以使墨水材料不变质。
70.在其中一些示例中,步骤s30中,对膜层施加保护性气体不直接吹到基板表面,出气口与基板垂直距离》10cm。如此,可进一步避免墨水左右晃动而减小相邻像素液滴之间的
融合,从而防止成膜不均匀、串色、mura等问题的出现。
71.在其中一些示例中,步骤s30中,通过控制保护性气体的通气量以控制施加的保护性气体的气体压力大小,保护性气体的通气量为0.5mpa~1mpa。
72.在其中一些示例中,步骤s30中,保护性气体选自氮气、氩气、氦气、氖气、氪气和氙气中的至少一种。可选地,保护性气体选自氮气和氩气中的至少一种。
73.在其中一些示例中,步骤s30中,如图2中的c所示,施加的保护性气体的气体压力方向垂直于基板所在的平面。可以理解,基板平行于地面放置,施加保护性气体的气体压力方向垂直于地面,从墨水的正上方进行施加;对膜层施加正压,在正向压力作用下将上凸的膜层液面压平。由于液滴体积大小或者干燥速率差异形成的高低差异的上凸液面,在此过程中像素坑内的液面均被流平形成平坦液面;平坦的液面在后续进一步干燥过程中就不存在像素坑内边缘与中心的溶剂挥发差异,从而使最终像素坑内平坦化薄膜的溶质在后续热处理过程中均匀沉积,形成平坦均匀的薄膜。
74.在其中一些示例中,步骤s40中,将含有平坦化薄膜的基板置于热台上进行热处理,去除残余的溶剂,平坦化薄膜完全交联固化,形成平坦均匀的印刷薄膜,如图2中的d所示。
75.在其中一些示例中,步骤s40中,热处理的温度为100℃~250℃,热处理的时间为10min~60min。
76.本发明的印刷薄膜的制备方法,使制备得到的印刷薄膜的均匀性较好。该印刷薄膜可为发光层或者功能层,该制备方法可用于制备显示器件中的发光层或者功能层,进而有利于显示器件的发光均匀性、器件寿命的提升,确保了显示器件的质量。
77.本发明一实施方式提供了一种发光器件。发光器件包括发光层和功能层。
78.发光层和/或功能层为采用如上所述的印刷薄膜的制备方法制备得到。由此,该发光器件可以具有前面描述的方法所具有的全部特征以及优点。
79.可理解,发光器件还包括基板和像素限定层;基板和像素限定层层叠设置,发光层和/或功能层设于像素限定层的像素坑内。可理解,上述发光器件还可包括阳极和阴极。在一具体示例中,该发光器件包括基板、依次设于基板上的阳极和像素限定层、设于像素限定层的像素坑内的发光层,及设于发光层和像素限定层上的阴极;或者还包括设于像素限定层的像素坑内的功能层。
80.进一步地,功能层包括电子功能层和/或空穴功能层,电子功能层设于阴极和发光层之间;空穴功能层设于阳极和发光层之间。电子功能层包括但不限于依次设于发光层上的空穴阻挡层、电子传输层和电子注入层中的至少一种。空穴功能层包括但不限于依次设于阳极上的空穴注入层、空穴传输层和电子阻挡层中的至少一种。
81.可以理解,发光器件中在像素坑内打印液滴制得的功能层均可以采用上述的制备方法。
82.本发明一实施方式提供了一种发光器件的制备方法,发光器件中的发光层和功能层中至少一层的制备包括如下步骤:
83.在基板上形成像素限定层,像素限定层具有像素坑;
84.在像素坑内设置墨水;
85.将设置有墨水的基板进行预干燥,得到膜层;
86.对膜层进行压平处理,以使像素坑内的膜层平坦化形成平坦化薄膜;
87.将形成有平坦化薄膜的基板进行热处理。
88.具体实施例
89.以下按照本发明的印刷薄膜及其制备方法举例,可理解,本发明的印刷薄膜及其制备方法并不局限于下述实施例。
90.实施例
91.在基板的像素坑内打印浓度为2.0%的hil墨水65pl;将打印有墨水的基板转入到真空干燥设备,室温下抽真空至压强40torr,维持40torr压强干燥30s,形成高粘度液体状膜层。进一步将形成有高粘度液体状膜层的基板转入到封装加压脱泡的设备中(卓耀zy-qp6308sd),通过在基板垂直上方的进气口施加氮气达到设定压力0.5mpa,温度设定为室温25℃,维持压力15min,形成较平坦的薄膜;再将形成有平坦化薄膜的基板转入到230℃的加热台上进行干燥热处理30min,去除残余溶剂,使平坦化薄膜完全交联固化,得到印刷薄膜。
92.对比例1
93.与实施例基本相同,不同点在于,在基板的像素坑内打印完墨水后直接进行真空干燥,而不实施进一步的加压干燥处理。具体如下:
94.在基板的像素坑内打印浓度为2.0%的hil墨水65pl;将打印有墨水的基板转入到真空干燥设备中,室温下抽真空至压强40torr,维持40torr压强干燥180s后去除大部分溶剂,形成的薄膜形貌基本固定;然后将真空度抽至10-5
torr的高真空下维持真空干燥300s,形成干燥的薄膜;再将干燥的薄膜基板转入到230℃的加热台上进行干燥热处理30min,得到印刷薄膜。
95.对比例2
96.与实施例1基本相同,不同点在于,在基板的像素坑内打印完墨水后直接对其进行施加保护性气体,而不进行真空干燥形成高粘度液体状膜层的步骤。
97.在基板的像素坑内打印完墨水后,在基板垂直上方的进气口对其施加氮气,会出现像素之间墨水融合的问题,无法正常完成打印。
98.将实施例和对比例1中干燥后的薄膜传入到蒸镀机进行50nm银薄膜增加光的干涉强度,然后通过白光干涉仪进行薄膜均匀性测试。通过光学相干原理,测试出像素内薄膜厚度分布。测试像素两边设定空白未打印像素作为参考膜面,拉平基准面后测试目标像素内打印薄膜厚度及形貌。实施例像素内薄膜形貌一维截面图如图7所示;其中图7中的a)和b)分别对应像素的长轴和短轴的薄膜形貌;对比例1像素内薄膜形貌一维截面图如图8所示,其中图8中的a)和b)分别对应像素的长轴和短轴的薄膜形貌。实施例及对比例1中薄膜均匀性u%的测量结果如表1所示。薄膜的均匀性u%(uniformity)为薄膜厚度在中间平均膜厚
±
5nm范围内的面积s1占整个像素面积s的百分比,即:u%=s1/s。其中,平均膜厚为像素中心区域一定面积内的平均厚度,取平均的区域可以按照像素实际大小来确定。同时厚度偏差范围也可以按照实际要求来确定,如
±
10nm,或者目标膜厚的
±
3%/
±
5%。像素内打印薄膜均匀性评估是一个相对性概念,可以结合器件对厚度的要求及点亮要求来调整薄膜均匀性的方式和标准。表1中采用的是平均膜厚的
±
5nm来计算不同干燥方式下薄膜的均匀性。
99.表1
[0100][0101]
从白光干涉测试的一维截面图以及均匀性测试结果对比,实施例采用了加压干燥方式,减少了边缘与中心的液面高度差,从而减缓了边缘与中心干燥速率差异,有效抑制了溶质在干燥过程中在边缘的堆积,增加了像素内薄膜有效长短轴,得到更平坦的均匀薄膜。而对比例1直接采用真空干燥,溶质在边缘堆积严重,形成u型不平坦薄膜。打印干燥的薄膜均匀性提高有利于最终发光器件的效率寿命提升,同时提高大面板点亮均匀性。
[0102]
以上所述实施例的各技术特征可以进行任意的组合,为使描述简洁,未对上述实施例中的各个技术特征所有可能的组合都进行描述,然而,只要这些技术特征的组合不存在矛盾,都应当认为是本说明书记载的范围。
[0103]
以上所述实施例仅表达了本发明的几种实施方式,便于具体和详细地理解本发明的技术方案,但并不能因此而理解为对发明专利保护范围的限制。应当指出的是,对于本领域的普通技术人员来说,在不脱离本发明构思的前提下,还可以做出若干变形和改进,这些都属于本发明的保护范围。应当理解,本领域技术人员在本发明提供的技术方案的基础上,通过合乎逻辑的分析、推理或者有限的试验得到的技术方案,均在本发明所附权利要求的保护范围内。因此,本发明专利的保护范围应以所附权利要求的内容为准,说明书及附图可以用于解释权利要求的内容。