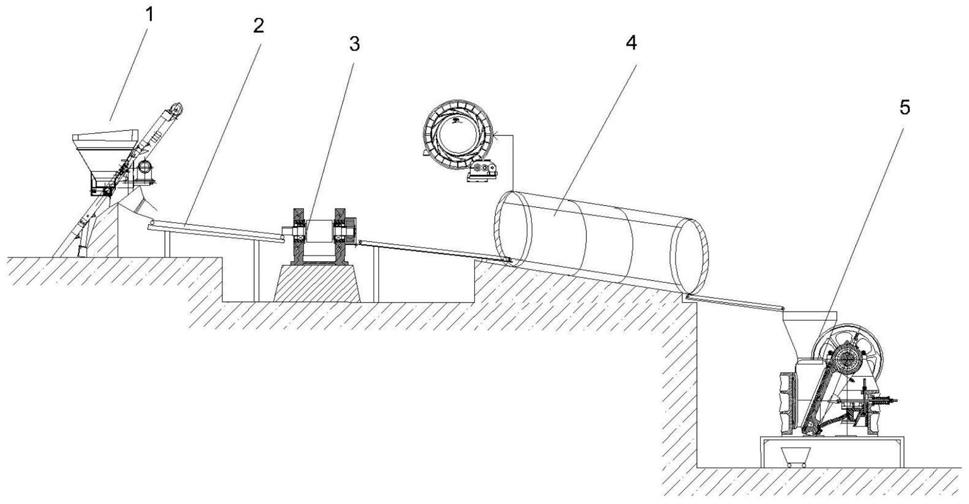
1.本发明涉及一种锂电池正极材料的加工方法及生产线,属于锂电池制备技术领域。
背景技术:2.锂离子电池在3c数码产品、能源储备及汽车动力等领域有极为广泛的应用,其主要由正极、负极、隔膜和电解液四个部分组成。其中,正极材料的耗费占比高达30~40%。锂电池的正极材料由li、co、mn、ni等构成,其制备工艺通常是将原料物质装在匣钵中并以400~1000℃进行烧成。在高温固相反应工序中,辊道窑由于其气氛易控制、温度场均一、产量较大且成本低,便于实现自动化等优点而多被采用。但在此过程中,li及co化合物熔融而渗透到匣钵的气孔中,与构成成分反应而诱发匣钵本体的裂隙及剥离。一方面,匣钵剥离的反应物质使正极材料的品质降低;另一方面,匣钵因裂隙而破损,破损的匣钵在循环使用的过程中也存在降低所焙烧正极材料活性的弊端。其次,在辊道窑中以匣钵为承装载体焙烧锂电池正极材料的粉体,其烧成效率较低,目前国内的锂电池正极材料的总体产能远远达不到实际需求量。
3.从行业协会的统计数据来看,锂电池正极材料用匣钵承装煅烧,而匣钵的使用寿命为平均20~30炉次。仅2019年,中国锂电池正极材料焙烧用匣钵的消耗量就高达4.3万吨。由于正极材料与匣钵之间的反应及正极材料向匣钵微结构中的渗透,导致废弃匣钵成为难以处理的固体危废,对环境造成巨大的压力。目前,匣钵是朝着将反应活性较小的物质涂覆于匣钵的表面或提高匣钵本身热冲击抵抗性的方向开发。但是,由于涂覆的复杂性而难以大量生产,或存在因与匣钵材料的热膨胀系数差异而出现剥离的缺点。另外,匣钵本体与需焙烧的电池材料之间的反应仅仅只是反应程度降低而已,从本质上而言,无法断绝其与正极活性物质反应,也无法实现正极材料连续化的大批量生产。
技术实现要素:4.本发明的目的是为了解决现有上述问题,提供了一种锂电池正极材料的加工方法及生产线,该生产线环境友好、简易高效,采用该生产线进行锂电池正极材料的生产,可实现锂电池正极材料连续化的大批量生产,具有很大的产业化前景。
5.为了解决上述技术问题,本发明采用的一种技术方案是,所述锂电池正极材料的加工方法,包括以下步骤:(1)正极材料粉料混合均匀后,由向下方倾斜的传送带定向输送到成型系统;(2)将正极材料粉料在成型系统中进行高速造粒或造块,形成球形化正极材料或块状正极材料;(3)将球形化正极材料或块状正极材料经由向下方倾斜的传送带定向输送到焙烧系统进行焙烧并冷却;(4)继续将焙烧冷却后的球形正极材料由传送带输送至破碎机,粉碎后直接进入
收料车进行收集。
6.进一步地,所述球形正极材料的平均直径为5~20cm,孔隙率≤5%,球形度≥0.85。
7.进一步地,所述块状正极材料的长、宽、高尺寸范围为5~20cm,孔隙率≤3.5%。
8.本发明还提供一种用于加工锂电池正极材料的生产线,包括依次设置的混料机、成型系统、焙烧系统、破碎机和收料机,所述混料机的出料口与造粒系统之间、所述造粒系统与焙烧系统的进料口之间、所述焙烧系统的出料口与破碎机的进料口之间分别通过传送带相连接,破碎机的出料口设置收料车。
9.进一步的,所述混料机的出料口与造粒系统之间的传送带向成型系统一侧倾斜,所述造粒系统与焙烧系统的进料口之间的传送带向焙烧系统一侧倾斜,所述焙烧系统的出料口与破碎机的进料口之间的传送带向破碎机一侧倾斜。
10.进一步的,所述成型系统为滚压成球或机压成球的造粒机、或者为机压成块的螺旋压机。
11.进一步的,所述焙烧系统为回转窑、竖窑、摇摆窑、隧道窑或梭式窑中的一种。
12.进一步的,在所述焙烧系统的出料口配置有风冷装置。
13.进一步的,所述混料机、成型系统、焙烧系统和破碎机均配有除尘系统。
14.进一步的,所述破碎机采用鄂式破碎机。
15.本发明具有以下优点:(1)本发明将锂电池正极材料经成型系统制球或制块后进入焙烧系统内进行焙烧,与传统匣钵焙烧粉体的方式不同,其焙烧窑炉的内衬材料与锂电池正极材料球团的接触面积达到最小化,接触时间也相对较短,能最大化避免焙烧过程中内衬材料与正极材料之间的物理/化学反应,从而提升锂电池正极材料焙烧后的合格率;(2)本发明无需搭配匣钵的装卸,能最大化提高焙烧效率,提升生产速度,实现锂电池正极材料连续化的大批量生产,提升燃料的加热效率,缓解能源行业的原料供应压力;(3)本发明无需使用匣钵盛装,避免在焙烧过程中二氧化碳副产物在电池原料旁的富集,对烧制产品污染较低且产能较大,并能够满足其频繁使用的要求,可替代传统辊道窑与匣钵的搭配,市场前景可观;(4)本发明具有环境友好和简易高效的特点;所装备的锂电池正极材料生产线可解决现存的技术问题,实现锂电池正极材料连续化的大批量生产,具有很大的产业化前景。
附图说明
16.图1是本发明中实施例2
‑
5的生产线结构示意图。
17.图2是本发明中实施例6的生产线结构示意图。
具体实施方式
18.为了使本发明的上述目的、特征和优点能够更加明显易懂,下面结合具体附图对本发明的具体实施方式作进一步的说明。
19.在下面的描述中阐述了很多具体细节以便于充分理解本发明,但是本发明还可以采用其他不同于在此描述的其它方式来实施例,本领域技术人员可以在不违背本发明内涵的情况下做类似推广,因此本发明不受下面公开的具体实施例的限制。
20.实施例1:本发明所述锂电池正极材料的生产线,包括依次设置的混料机1、成型系统3、焙烧系统4、破碎机5和收料机6,所述混料机1的出料口与造粒系统3之间、所述造粒系统3与焙烧系统4的进料口之间、所述焙烧系统4的出料口与破碎机5的进料口之间分别通过传送带2相连接,破碎机5的出料口设置收料车6。为便于输送,所述混料机1的出料口与造粒系统3之间的传送带向成型系统3一侧倾斜,所述造粒系统3与焙烧系统4的进料口之间的传送带2向焙烧系统一侧倾斜,所述焙烧系统4的出料口与破碎机5的进料口之间的传送带2向破碎机5一侧倾斜。
21.所述成型系统3为滚压成球或机压成球的造粒机、或者为机压成块的螺旋压机。
22.所述焙烧系统4为回转窑、竖窑、摇摆窑、隧道窑或梭式窑中的一种,且在焙烧系统4的出料口配置有风冷装置。
23.所述混料机1、成型系统3、焙烧系统4和破碎机5均配有除尘系统。
24.所述破碎机5采用鄂式破碎机。
25.实施例2:本发明所述锂电池正极材料的加工方法,包括以下步骤:(1)混料机1内的正极材料粉料经均匀混合后,由向下方倾斜的传送带2定向输送到成型系统3的入料口;(2)该正极材料粉料在成型系统3中进行高速离心造粒,形成具备高致密度及高球形度的球形化正极材料;所述球形正极材料的平均直径为5cm,孔隙率为3%,球形度为0.88;(3)将步骤(2)得到的球形化正极材料经由向下方倾斜的传送带定向输送到焙烧系统4的入料口,焙烧系统4可以采用回转窑;球形正极材料在焙烧系统4中进行焙烧并冷却;所述焙烧温度为550℃,时间为12h,冷却速度为10℃/min,冷却至常温;(4)继续将焙烧冷却后的球形正极材料由传送带输送至颚式破碎机的入料口进行粉碎,粉碎至直径<0.045mm,粉碎后的正极材料直接进入收料车6进行收集;(5)经上述混合、造粒、焙烧及粉碎工艺,高效快速得到大批量、连续化产出的高性能锂电池正极材料。
26.实施例3:本发明所述锂电池正极材料的加工方法,包括以下步骤:(1)混料机1内的正极材料粉料经均匀混合后,由向下方倾斜的传送带2定向输送到成型系统3的入料口;(2)该正极材料粉料在成型系统3中进行高速离心造粒,形成具备高致密度及高球形度的球形化正极材料;所述球形正极材料的平均直径为20cm,孔隙率为5%,球形度为0.85;(3)将步骤(2)得到的球形化正极材料经由向下方倾斜的传送带定向输送到焙烧系统4的入料口,焙烧系统4可以采用回转窑;球形正极材料在焙烧系统4中进行焙烧并冷却;所述焙烧温度为700℃,时间为12h,冷却速度为10℃/min,冷却至常温;(4)继续将焙烧冷却后的球形正极材料由传送带输送至颚式破碎机的入料口进行粉碎,粉碎至直径<0.045mm,粉碎后的正极材料直接进入收料车6进行收集;(5)经上述混合、造粒、焙烧及粉碎工艺,高效快速得到大批量、连续化产出的高性
能锂电池正极材料。
27.实施例4:本发明所述锂电池正极材料的加工方法,包括以下步骤:(1)混料机1内的正极材料粉料经均匀混合后,由向下方倾斜的传送带2定向输送到成型系统3的入料口;(2)该正极材料粉料在成型系统3中进行高速离心造粒,形成具备高致密度及高球形度的球形化正极材料;所述球形正极材料的平均直径为15cm,孔隙率为4.5%,球形度为0.95;(3)将步骤(2)得到的球形化正极材料经由向下方倾斜的传送带定向输送到焙烧系统4的入料口,焙烧系统4可以采用回转窑;球形正极材料在焙烧系统4中进行焙烧并冷却;所述焙烧温度为750℃,时间为3h,冷却速度为10℃/min,冷却至常温;(4)继续将焙烧冷却后的球形正极材料由传送带输送至颚式破碎机的入料口进行粉碎,粉碎至直径<0.045mm,粉碎后的正极材料直接进入收料车6进行收集;(5)经上述混合、造粒、焙烧及粉碎工艺,高效快速得到大批量、连续化产出的高性能锂电池正极材料。
28.实施例5:本发明所述锂电池正极材料的加工方法,包括以下步骤:(1)混料机1内的正极材料粉料经均匀混合后,由向下方倾斜的传送带2定向输送到成型系统3的入料口;(2)该正极材料粉料在成型系统3中进行高速离心造粒,形成具备高致密度及高球形度的球形化正极材料;所述球形正极材料的平均直径为15cm,孔隙率为5%,球形度为0.86;(3)将步骤(2)得到的球形化正极材料经由向下方倾斜的传送带定向输送到焙烧系统4的入料口,焙烧系统4可以采用回转窑;球形正极材料在焙烧系统4中进行焙烧并冷却;所述焙烧温度为720℃,时间为8h,冷却速度为10℃/min,冷却至常温;(4)继续将焙烧冷却后的球形正极材料由传送带输送至颚式破碎机的入料口进行粉碎,粉碎至直径<0.045mm,粉碎后的正极材料直接进入收料车6进行收集;(5)经上述混合、造粒、焙烧及粉碎工艺,高效快速得到大批量、连续化产出的高性能锂电池正极材料。
29.实施例6:本发明所述锂电池正极材料的加工方法,包括以下步骤:(1)混料机1内的正极材料粉料经均匀混合后,由向下方倾斜的传送带2定向输送到成型系统3的入料口;(2)该正极材料粉料在成型系统3(采用螺旋压机)中进行板压成块,形成具备高致密度及高球形度的块状正极材料,板压条件采用双面加压或等静压成型,所述块状正极材料的长、宽、高尺寸范围为5~20cm,孔隙率≤3.5%;(3)将步骤(2)得到的球形化正极材料经由向下方倾斜的传送带定向输送到焙烧系统4的入料口,焙烧系统4可以采用回转窑;球形正极材料在焙烧系统4中进行焙烧并冷却;所述焙烧温度为600℃,时间为6h,冷却速率 10℃/min;温度 700~750℃,时间1.5~
2.5h,冷却速率 5℃/min;(4)继续将焙烧冷却后的球形正极材料由传送带输送至颚式破碎机的入料口进行粉碎,粉碎后直径<0.045m,粉碎后的正极材料直接进入收料车6进行收集;(5)经上述混合、造粒、焙烧及粉碎工艺,高效快速得到大批量、连续化产出的高性能锂电池正极材料。