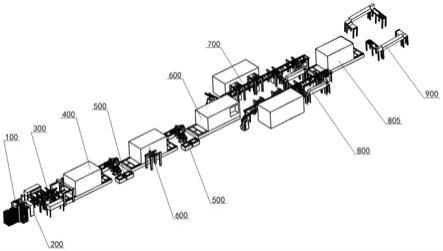
1.本发明涉及电容器生产加工技术领域,特别涉及一种电容器自动化处理线。
背景技术:2.电容器是储存电量和电能(电势能)的元件,电容器是电子设备等中大量使用的电子元件之一,作为常规的电子元件被广泛地应用在工业及日常的各类产品中。电容器的加工生产过程包括多道工序,且主体结构在完成制造后还需要经过多道后处理工序,确保电容器成品的合格、满足质量及使用要求。目前,电容器产品的后处理工序主要还是依靠独立的设备完成,并未形成流水线式的处理方式,不利于处理效率的提升以及处理质量的把控。
3.应该注意,上面对技术背景的介绍只是为了方便对本技术的技术方案进行清楚、完整的说明,并方便本领域技术人员的理解而阐述的。不能仅仅因为这些方案在本技术的背景技术部分进行了阐述而认为上述技术方案为本领域技术人员所公知。
技术实现要素:4.本发明的目的是为了克服现有技术的不足,提供一种流水线式的电容器处理线,采用自动化的方式完成电容器的后处理工序,以提升处理效率及处理质量。
5.为了达到上述目的,本发明提供了一种电容器自动化处理线,包括输送线以及沿输送线依次设置的上料工位、毛刺烧除工位、涂油工位、第一烘干工位、浸液工位、第二烘干工位、喷粉工位、脱脂工位以及脱粒工位,电容器部件通过上料工位上料至输送线,毛刺烧除工位将电容器部件表面的毛刺烧除,涂油工位使电容器部件的表面涂抹油层,第一烘干工位将电容器部件烘干使油层固定,浸液工位使电容器部件的表面附着浸液,第二烘干工位将电容器部件烘干使浸液层固定,喷粉工位对电容器部件的表面喷粉,脱脂工位使电容器部件表面的油脂去除,脱粒工位使电容器部件表面离散的颗粒去除。
6.进一步地,所述输送线设置有料盘移动的导轨以及驱动料盘输送的驱动部,所述上料工位设置有上料组件,所述上料组件包括料盘码垛机以及料盘上料机,所述料盘上料机将料盘码垛机上装有电容器部件的料盘依次上料至输送线;所述毛刺烧除工位设置有毛刺烧除机,所述输送线经过所述毛刺烧除机,使输送的料盘中的电容器部件停留于毛刺烧除机内完成毛刺烧除。
7.进一步地,所述涂油工位设置有涂油机以及涂油机械手,所述涂油机设置有涂油入料口和涂油出料口,所述涂油机械手将料盘中的电容器部件拾取并放置于所述涂油入料口,电容器部件从所述涂油入料口进入所述涂油机,完成涂油后从所述涂油出料口移出,所述涂油机械手将完成涂油的电容器部件放回所述输送线上的、空的料盘中。
8.进一步地,所述第一烘干工位设置有第一烘干炉以及第一烘干机械手,所述第一烘干机械手将完成涂油的电容器部件所在的料盘移动至所述第一烘干炉,所述第一烘干炉将电容器部件烘干。
9.进一步地,所述浸液工位设置有浸液槽以及浸液机械手,所述浸液槽内装有浸液,
所述浸液机械手将输送线上的电容器部件拾取并没入所述浸液槽中。
10.进一步地,所述浸液槽包括第一浸液槽以及第二浸液槽,所述浸液机械手对应包括第一浸液机械手以及第二浸液机械手,所述第一浸液槽内为预浸工序,所述第二浸液槽内为包封工序,所述第二烘干工位设置有第二烘干机以及第三烘干机,所述第二烘干机设置在所述第一浸液槽与所述第二浸液槽之间,所述第三烘干机设置在所述第二浸液槽之后,电容器组件在预浸工序以及包封工序后分别通过第二烘干机以及第三烘干机烘干处理。
11.进一步地,所述喷粉工位设置有喷粉机以及喷粉机械手,所述喷粉机设置有喷粉入料口和喷粉出料口,所述喷粉机械手将所述料盘中的电容器部件拾取并放置于所述喷粉入料口,电容器部件从所述涂油入料口进入所述涂油机,完成喷粉后从所述喷粉出料口移出,所述喷粉机械手将完成喷粉的电容器部件拾取并放回所述输送线上的、空的料盘中。
12.进一步地,所述脱脂工位设置有脱脂机以及脱脂机械手,所述脱脂机设置有脱脂入料口和脱脂出料口,所述脱脂机械手将所述料盘中的电容器部件拾取并放置于所述脱脂入料口,电容器部件从所述脱脂入料口进入所述脱脂机,完成脱脂后从所述脱脂出料口移出,所述脱脂机械手将完成喷粉的电容器部件拾取并放回所述输送线上的、空的料盘中。
13.进一步地,所述脱脂工位的后方设置有第四烘干机,所述第四烘干机将脱脂后的电容器部件烘干处理。
14.进一步地,所述脱粒工位设置有脱粒机以及脱粒机械手,所述脱粒机设置有脱粒入料口和脱粒出料口,所述脱粒机械手将所述料盘中的电容器部件拾取并放置于所述脱粒入料口,电容器部件从所述脱粒入料口进入所述脱粒机,完成脱粒后从所述脱粒出料口移出,所述脱粒机械手将完成喷粉的电容器部件拾取并放置于料箱中装箱。
15.本发明的上述方案有如下的有益效果:
16.本发明提供的电容器自动化处理线,通过各工位以及设备的布置使电容器组件能依次完成毛刺去除、涂油、浸液、喷粉、脱脂以及脱粒等工序,设计合理,衔接配合紧凑,采用自动化的方式控制,有效提升了电容器部件后处理的效率及质量,降低了生产成本;
17.本发明的其它有益效果将在随后的具体实施方式部分予以详细说明。
附图说明
18.图1为本发明的整体结构示意图;
19.图2为本发明的上料工位、毛刺烧除工位以及涂油工位相关设备结构示意图;
20.图3为本发明的第一烘干工位、浸液工位以及第二烘干工位相关设备结构示意图;
21.图4为本发明的喷粉工位以及脱脂工位相关设备结构示意图。
22.【附图标记说明】
23.100
‑
上料工位;101
‑
料盘码垛机;102
‑
料盘上料机;103
‑
料盘;200
‑
毛刺烧除工位;201
‑
毛刺烧除机;300
‑
涂油工位;301
‑
涂油机;302
‑
涂油机械手;303
‑
涂油入料口;304
‑
涂油出料口;400
‑
第一烘干工位;401
‑
第一烘干炉;402
‑
第一烘干机械手;500
‑
浸液工位;501
‑
第一浸液槽;502
‑
第二浸液槽;503
‑
第一浸液机械手;504
‑
第二浸液机械手;600
‑
第二烘干工位;601
‑
第二烘干机;602
‑
第三烘干机;700
‑
喷粉工位;701
‑
喷粉机;702
‑
喷粉机械手;703
‑
喷粉入料口;704
‑
喷粉出料口;800
‑
脱脂工位;801
‑
脱脂机;802
‑
脱脂机械手;803
‑
脱脂入料
口;804
‑
脱脂出料口;805
‑
第四烘干机;900
‑
脱粒工位。
具体实施方式
24.为使本发明要解决的技术问题、技术方案和优点更加清楚,下面将结合附图及具体实施例进行详细描述。显然,所描述的实施例是本发明一部分实施例,而不是全部的实施例。基于本发明中的实施例,本领域普通技术人员在没有做出创造性劳动前提下所获得的所有其他实施例,都属于本发明保护的范围。此外,下面所描述的本发明不同实施方式中所涉及的技术特征只要彼此之间未构成冲突就可以相互结合。
25.在本发明的描述中,需要说明的是,术语“中心”、“上”、“下”、“左”、“右”、“竖直”、“水平”、“内”、“外”等指示的方位或位置关系为基于附图所示的方位或位置关系,仅是为了便于描述本发明和简化描述,而不是指示或暗示所指的装置或元件必须具有特定的方位、以特定的方位构造和操作,因此不能理解为对本发明的限制。此外,术语“第一”、“第二”、“第三”仅用于描述目的,而不能理解为指示或暗示相对重要性。除非另有明确的规定和限定,术语“安装”、“相连”、“连接”应做广义理解,例如,可以是锁定连接,也可以是可拆卸连接,或一体地连接;可以是机械连接,也可以是电连接;可以是直接相连,也可以通过中间媒介间接相连,可以是两个元件内部的连通。对于本领域的普通技术人员而言,可以具体情况理解上述术语在本发明中的具体含义。
26.如图1所示,本发明的实施例提供了一种电容器自动化处理线,包括输送线以及沿输送线依次设置的上料工位100、毛刺烧除工位200、涂油工位300、第一烘干工位400、浸液工位500、第二烘干工位600、喷粉工位700、脱脂工位800以及脱粒工位900。其中,电容器部件通过上料工位100上料至输送线,毛刺烧除工位200将电容器部件表面的毛刺烧除,涂油工位300使电容器部件的表面涂抹油层,第一烘干工位400将电容器部件烘干使油层固定,浸液工位500使电容器部件的表面附着浸液,第二烘干工位600将电容器部件烘干使浸液层固定,喷粉工位700对电容器部件的表面喷粉,脱脂工位800使电容器部件表面的油脂去除,脱粒工位900使电容器部件表面离散的颗粒去除,最终完成电容器部件的全部后处理工序,确保电容器部件组装为成品后质量合格且能满足使用要求。
27.同时如图2所示,输送线设置有料盘移动的导轨以及驱动料盘输送的驱动部。上料工位100设置有上料组件,上料组件包括料盘码垛机101以及料盘上料机102。其中,料盘码垛机101上码垛堆叠有多个料盘103,料盘上料机102将料盘码垛机101上装有电容器部件的料盘103依次拾取并上料至输送线,使装载有电容器部件的料盘沿输送线依次输送,经过各个工位完成对应后处理工序。
28.在本实施例中,毛刺烧除工位200设置有毛刺烧除机201,输送线经过毛刺烧除机201,使输送的料盘中的电容器部件停留于毛刺烧除机内部,依靠毛刺烧除机的火焰、高温等方式完成电容器部件表面的毛刺烧除。
29.在本实施例中,涂油工位300设置有涂油机301以及涂油机械手302。其中,涂油机301设置有涂油入料口303和涂油出料口304,涂油入料口303以及涂油出料口304均设置有输送结构,涂油机械手302将料盘103中的电容器部件拾取并放置于涂油入料口303,电容器部件在输送结构作用下从涂油入料口303进入涂油机301,由涂油机301将电容器部件的表面涂抹油层,完成涂油后电容器部件从涂油出料口304移出,涂油机械手302将其放回输送
线上的、空的料盘103中,以随料盘103移动至后续工序。
30.同时如图3所示,第一烘干工位400设置有第一烘干炉401以及第一烘干机械手402,由于与第一烘干炉401对接的输送线部分低于涂油工位300的输送线部分,因此通过第一烘干机械手402的设置,将完成涂油的电容器部件所在的料盘103转移至第一烘干炉401所在的输送线部分,再输送至第一烘干炉401内,使电容器部件被烘干,表面的油层被固定。
31.在本实施例中,浸液工位500设置有浸液槽以及浸液机械手,浸液槽内装有浸液,浸液机械手将输送线上的电容器部件拾取并没入槽中完成浸液处理。其中,浸液槽包括第一浸液槽501以及第二浸液槽502,浸液机械手对应包括第一浸液机械手503以及第二浸液机械手504,第一浸液槽501内为预浸工序,第二浸液槽502内为包封工序,电容器部件由第一浸液机械手503移动至第一浸液槽501中,使表面预附着第一层浸液,再由第二浸液机械手503移动至第二浸液槽504中附着第二层浸液,最终形成两层浸液层。另外,第二烘干工位600设置有第二烘干机601以及第三烘干机602,第二烘干机601设置在第一浸液槽501与第二浸液槽502之间,第三烘干机602设置在第二浸液槽502之后,电容器组件在预浸工序以及包封工序后分别通过第二烘干机601以及第三烘干机602烘干处理,确保形成两层稳定的浸液层。
32.同时如图4所示,喷粉工位700设置有喷粉机701以及喷粉机械手702。其中,喷粉机701设置有喷粉入料口703和喷粉出料口704,喷粉入料口703以及喷粉出料口704均设置有输送结构,喷粉机械手702将料盘103中的电容器部件拾取并放置于喷粉入料口703,电容器部件在输送结构作用下从喷粉入料口703进入喷粉机701,由喷粉机701将电容器部件的表面喷粉后从喷粉出料口704移出,喷粉机械手702将完成喷粉的电容器部件拾取并放回输送线上的、空的料盘103中,以随料盘103移动至后续工序。
33.在本实施例中,脱脂工位800设置有脱脂机801以及脱脂机械手802。其中,脱脂机801设置有脱脂入料口803和脱脂出料口804,脱脂入料口803以及脱脂出料口804均设置有输送结构,脱脂机械手802将料盘103中的电容器部件拾取并放置于脱脂入料口803,电容器部件在输送结构作用下从脱脂入料口803进入脱脂机801,由脱脂机801将电容器部件表面的油脂去除后从脱脂出料口804移出,脱脂机械手802将完成脱脂的电容器部件拾取并放回输送线上的、空的料盘103中,以随料盘103移动至后续工序。
34.在本实施例中,脱脂工位800的后方还设置有第四烘干机805,第四烘干机805将脱脂后的电容器部件烘干处理,完成最后一道烘干工序。
35.在本实施例中,脱粒工位900设置有脱粒机以及脱粒机械手,脱粒机设置有脱粒入料口和脱粒出料口,脱粒机械手将料盘中完成全部烘干工序的电容器部件拾取并放置于脱粒入料口,电容器部件在输送结构作用下从脱粒入料口进入脱粒机,由脱粒机将电容器部件表面的离散颗粒去除后从脱粒出料口移出,脱粒机械手将完成脱粒的电容器部件拾取并放置于料箱中装箱,至此完成了电容器部件的全部后处理工序,可通过人工或视觉检测的方式对电容器部件的装箱进行检查。
36.以上所述是本发明的优选实施方式,应当指出,对于本技术领域的普通技术人员来说,在不脱离本发明所述原理的前提下,还可以作出若干改进和润饰,这些改进和润饰也应视为本发明的保护范围。