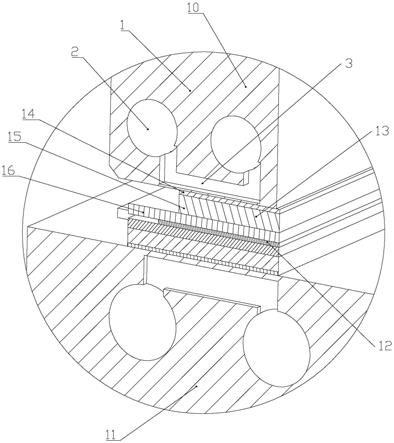
一种低热阻bar条封装工艺
技术领域
1.本发明涉及激光芯片封装技术领域,更具体的说是一种低热阻bar条封装工艺。
背景技术:2.高功率半导体激光器的工作性能、长期可靠性及使用寿命等在很大程度上决定于芯片的封装,它的主要任务是给激光芯片提供电流和散热,其中散热尤其重要。
3.现有的激光芯片在封装时通过设置宏通道热沉的方式实现对激光芯片的降温,但宏通道的设置方式导致热沉普遍较厚,进而导致散热效果不良,同时由于宏通道的设置方式使得在激光发光面与冷却水道之间需要采用o型圈进行隔离,同时为了防止激光腔内湿度增高,需要输入惰性气体,从而导致成本上升,o形圈的隔离方式在长期使用过程中容易被水分子渗透,导致芯片损坏,有鉴于此,需要一种能够获得优良散热效果,同时避免水分子渗透的低热阻bar条封装工艺。
技术实现要素:4.针对现有技术存在的不足,本发明的目的在于提供一种能够获得优良散热效果,同时避免水分子渗透的低热阻bar条封装工艺。
5.为实现上述目的,本发明提供了如下技术方案:一种低热阻bar条封装工艺,包括以下步骤:
6.步骤1、在热沉侧面开设进出水道,在热沉上通过激光加工获得冷却水槽,同时冷却水槽两端加深与进出水道连通;
7.步骤2、通过焊接的方式在冷却水槽上焊接金属板,该金属板将冷却水槽完全覆盖;
8.步骤3、将热沉与电镀工装安装,所述电镀工装上设有电镀腔,所述金属板容纳于电镀腔中;
9.步骤4、通过电镀工装对金属板表面以及金属板和水道的连接处进行电镀形成电镀层;
10.步骤5、将电镀层进行表面平面度处理;
11.步骤6、将热沉与芯片之间叠加电阻层形成封装体;
12.步骤7、将封装体进行加热焊接。
13.作为本发明的进一步改进,步骤1中所述激光加工为激光刻线,所述冷却水槽包括多个依次排列的冷却槽。
14.作为本发明的进一步改进,所述激光刻线宽度与筋宽比为1∶1,所述刻线深度为槽宽2-4倍。
15.作为本发明的进一步改进,步骤2中所述焊接为金锡焊。
16.作为本发明的进一步改进,步骤3中所述电镀工装为绝缘材料,所述电镀工装上设有连通至电镀腔的入口和出口。
17.作为本发明的进一步改进,所述电镀腔周向设有密封圈。
18.作为本发明的进一步改进,步骤5中表面平面度处理包括机械切削,该平面度小于0.003um。
19.作为本发明的进一步改进,步骤6中所述热沉包括正极热沉和负极热沉,所述正极热沉和负极热沉对称设置于激光芯片两侧。
20.作为本发明的进一步改进,步骤6中所述电阻层包括铟层,碳化硅层和钨铜层,所述铟层、碳化硅层和钨铜层由热沉向激光芯片方向依次层叠。
21.作为本发明的进一步改进,步骤7中所述加热焊接为置于300度的真空炉中加热焊接。
22.本发明的有益效果:通过激光加工的方式使得冷却水槽内壁厚度大幅度减小,从而改善激光芯片的冷却效果,焊接金属板后通过电镀的方式形成电镀层能够有效解决单一焊接金属板所存在的气密性缺陷,形成良好的密封环境,同时与焊接金属板一起获得较长的使用寿命,同时通过将电镀层表面平面度处理能够减小电镀层表面起伏,从而在后续安装中获得更高的安装精度,同时能够减小芯片的安装应力,同时电阻层的设置能够减小激光芯片对其他部件的影响,电镀工装的绝缘设置能够避免电镀过程中对其余部件产生影响。
附图说明
23.图1为本发明激光芯片、热层和电阻层的安装剖视图;
24.图2为本发明冷却水槽示意图;
25.图3为本发明金属板安装图;
26.图4为本发明热层与电镀工装安装剖视图。
27.附图标记:1、热沉;2、进出水道;3、冷却水槽;4、金属板;5、电镀工装;6、电镀腔;7、电镀层;8、冷却槽;9、密封圈;10、负极热沉;11、正极热层;12、激光芯片;13、电阻层;14、铟层;15、碳化硅层;16、钨铜层。
具体实施方式
28.下面结合附图和实施例,对本发明进一步详细说明。其中相同的零部件用相同的附图标记表示。
29.如图1-4所示,一种低热阻bar条封装工艺,包括以下步骤:
30.步骤1、在热沉1侧面开设进出水道2,在热沉1上通过激光加工获得冷却水槽3,同时冷却水槽3两端加深与进出水道2连通,所述冷却水槽3两端可通过激光加工或铣削的方式完成加深,所述进出水道2的开设方式包括铣削、电火花、激光加工和水加工;
31.步骤2、通过焊接的方式在冷却水槽3上焊接金属板4,该金属板4将冷却水槽3完全覆盖;
32.步骤3、将热沉1与电镀工装5安装,所述电镀工装5上设有电镀腔6,所述金属板4容纳于电镀腔6中;
33.步骤4、通过电镀工装5对金属板4表面以及金属板4和冷却水槽3的连接处进行电镀形成电镀层7;
34.步骤5、将电镀层7进行表面平面度处理,所述表面平行度处理包括铣削和磨削;步骤6、将热沉1与激光芯片12之间叠加电阻层13形成封装体;
35.步骤7、将封装体进行加热焊接;
36.通过激光加工的方式使得冷却水槽3内壁厚度大幅度减小,从而增大了冷却面积,焊接金属板4后通过电镀的方式形成电镀层7能够有效解决单一焊接金属板4所存在的气密性缺陷,形成良好的密封环境,同时与焊接金属板4一起获得较长的使用寿命,降低了在使用过程中水分子渗透的可能性。
37.优选的,在本实施例中,步骤2中所述金属板4为铜板,铜板的设置能够保证优良导热性能的同时减少成本。
38.优选的,步骤1中所述激光加工为激光刻线,所述冷却水槽3包括多个依次排列的冷却槽8,多个所述冷却槽8沿进出水道2长度方向排列,多个冷却槽8的排列设置能够增大冷却面积以及加快冷却槽内的液体流速,从而获得更好的冷却效果。
39.优选的,所述激光刻线宽度与筋宽比为1∶1,所述刻线深度为槽宽2-4倍,通过对刻线深度与槽宽的比值设置能够获得最好的冷却效果。
40.优选的,步骤2中所述焊接为金锡焊,通过金锡焊的焊接方式能够使得焊点处具备高耐腐蚀性、高抗蠕变性以及良好的导热性能。
41.优选的,步骤3中所述电镀工装5为绝缘材料,所述电镀工装5上设有连通至电镀腔6的入口和出口,电镀工装5绝缘设置能够避免电镀过程中对其余部件产生影响。
42.优选的,所述电镀腔6周向设有密封圈9,密封圈9的设置能够保证电镀过程中减少电镀液泄漏,从而保证电镀效果。
43.优选的,步骤5中表面平面度处理包括机械切削,该平面度小于0.003um,通过将电镀层7表面平面度处理能够减小电镀层7表面起伏,从而在后续安装中获得更高的安装精度,
44.优选的,步骤6中所述热沉1包括正极热沉11和负极热沉10,所述正极热沉11和负极热沉10对称设置于激光芯片12两侧,实现对激光芯片12的双面冷却,使得散热效果增加。
45.优选的,步骤6中所述电阻层13包括铟层14,碳化硅层15和钨铜层16,所述铟层14、碳化硅层15和钨铜层16由热沉1向激光芯片12方向依次层叠,铟层14、碳化硅层15和钨铜层16的层叠设置能够实现电阻的同时获得优良的导热性能。
46.优选的,步骤7中所述加热焊接为置于300度的真空炉中加热焊接,通过真空焊接的方式能够有效地排除空气对工件的有害影响,使得焊点具有良好的力学性能和耐腐蚀性。
47.以上所述仅是本发明的优选实施方式,本发明的保护范围并不仅局限于上述实施例,凡属于本发明思路下的技术方案均属于本发明的保护范围。应当指出,对于本技术领域的普通技术人员来说,在不脱离本发明原理前提下的若干改进和润饰,这些改进和润饰也应视为本发明的保护范围。