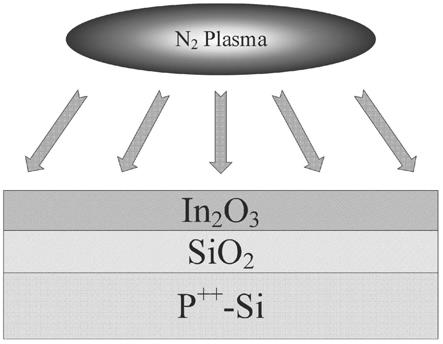
一种tmo薄膜和tmo-tft的超低温制备方法
【技术领域】
1.本发明涉及半导体技术及等离子技术领域,尤其涉及一种tmo薄膜和tmo-tft的超低温制备方法。
背景技术:2.信息时代的深度发展及人工智能的应用,开启了万物互联的智能时代,促使了智能终端的快速发展。显示屏作为智能终端进行人机交互的主要“窗口”,是消费者感官体验的关键。随着智慧城市的发展及消费者对智能化美好生活的追求,促使智能手机、智能电视、电脑、智慧大屏、智能汽车及智能家居等终端设备的功能日益强大,使得终端设备在对处理器芯片提出更高要求的同时,为了满足消费者更好的感官体验,对显示器的分辨率、对比度、响应度、轻薄度、柔性化、色域及能耗提出了更高的要求,从而促使了更高性能新型显示器件的发展。随着曲面屏及折叠屏手机的相继商用,柔性显示技术倍受业界关注的同时,激发了消费者的浓厚兴趣。柔性显示技术在刚性显示技术的基础上发展而来,相对刚性显示技术,在柔性基板上实现柔性显示器件的制备对显示组件的制备温度提出了一定的要求。
3.tft作为显示技术的的核心共性与关键技术,其低温制备成为实现高质量柔性显示器件的关键。自2004年日本东京工业大学细野秀雄研究组报道了具有高可见光透过率、高场效应迁移率、好的制备均一性,可低温制备的igzo-tft以来,tmo-tft迅速引起了广泛关注。经过近十几年的发展,tmo-tft已拥有直流/磁控溅射、分子束外延、激光脉冲沉积、溶液法等多种制备方法。其中溶液法由于工艺简单、成本低、产出高、以及易于大面积制备的特点,被广泛应用于tmo-tft的制备中。然而传统溶液法通常需要》400℃的高温退火过程实现tmo-tft的有效激活,该退火温度高于大多数柔性基板的耐受温度,从而限制了传统溶液法在柔性显示技术中的应用。因此,针对tmo薄膜及tmo-tft低温溶液法制备技术的研究对实现低成本、大面积、快速印刷制备柔性显示器件具有重大意义。
4.等离子体是由中性原子团和电离产生的正负离子混合而成的离子态气体化合物,具有良好的导电性,利用一些特殊的方法可以实现等离子体的捕捉、移动或者加速,由于其特殊的存在状态,被称为第四种物质存在形态。在等离子体中,粒子之间的相互作用力长程有效,等离子体中带电粒子的运动,能引起带电粒子的重新分布从而产生电场,或者引起电荷的定向运动形成电流,进而产生磁场,产生的电场和磁场又会影响其它带电粒子的运动状态,整个过程伴随着热辐射和热传导的产生。将等离子体应用于化学反应中时,反应过程中所需的热能可被等离子体中生成的热辐射和热传导以及离子放电的电能转化提供,从而大大降低化学反应过程所需的温度。由此可见,将等离子处理引入到tmo薄膜的制备过程中,具有实现溶液法tmo薄膜低温制备的潜力。
5.因此,有必要研究一种tmo薄膜和tmo-tft的超低温制备方法来应对现有技术的不足,以解决或减轻上述一个或多个问题。
技术实现要素:6.有鉴于此,本发明提供了一种tmo薄膜和tmo-tft的超低温制备方法,在保证tmo薄膜具有良好半导体特性以及tmo-tft具有优异电学特性的同时,实现tmo薄膜及tmo-tft的超低温制备,从而增强tmo-tft与柔性基板的柔性兼容性。
7.一方面,本发明提供一种基于溶液法tmo薄膜的超低温制备方法,所述tmo薄膜的超低温制备方法包括以下步骤:
8.s1:制备tmo前驱液;
9.s2:对基片进行清洗和表面活化;
10.s3:采用s1中获得的前驱液在s2中清洗活化后的基片上实现预沉积tmo湿膜的制备;
11.s4:对s3中获得的预沉积tmo湿膜进行预退火,获得预退火tmo薄膜;
12.s5:对s4中获得的预退火tmo薄膜进行n2等离子处理或进行n2等离子处理与后退火,获得tmo薄膜。
13.如上所述的方面和任一可能的实现方式,进一步提供一种实现方式,所述s1具体包括:
14.称取定量的前驱物,将前驱物溶于定量的前驱溶剂中,根据需求添加相应的添加剂,在0-100℃的温度下磁力搅拌0.5-24小时,获得相应的tmo前驱液,获得tmo前驱液,其中前驱液的浓度控制在0.01-1mol/l。
15.如上所述的方面和任一可能的实现方式,进一步提供一种实现方式,所述s1中tmo前驱液的前驱物包括但不限于金属硝酸盐、金属氯化物、金属氟化物和有机金属盐;所述s1中tmo前驱液的前驱溶剂包括但不限于高纯水、蒸馏水、二甲氧基乙醇、乙醇和n,n二甲基甲酰胺;所述s1中tmo前驱液的添加剂包括但不限于稳定剂、燃烧剂和氧化剂;所述s1中tmo前驱液的元素成分包括但不限于in2o3或zno等二元tmo前驱液、单元素掺杂in2o3或zno等三元tmo前驱液和共掺杂in2o3或zno等多元tmo前驱液;所述s1中获得的tmo前驱液种类包括但不限于水基前驱液、醇基前驱液、以及在水基及醇基前驱液的基础上通过前驱液工程开发的添加燃烧剂、强氧化剂和/或反应配体的前驱液。
16.如上所述的方面和任一可能的实现方式,进一步提供一种实现方式,所述s2中基片的清洗过程为:首先将备好的基片依次在去离子水、丙酮、异丙醇或乙醇、去离子水中各超声清洗5-40min,温度设置为25-70℃,然后取出基片,用氮气吹干或者用烘箱烘干;
17.所述s2中基片的表面活化程为:将清洗后的基片放入等离子清洗机内,等离子处理1-30min,使得基片表面活化,去除基片表面有机残余的同时,改善基片表面浸润性;其中等离子处理功率为10-200w、等离子处理温度为25-100℃、气流量为10-200sccm、等离子处理气氛为o2或ar。
18.如上所述的方面和任一可能的实现方式,进一步提供一种实现方式,所述s3中预沉积tmo湿膜的成膜方式包括但不限于旋涂、棒涂、提拉、滴涂和喷墨打印技术。
19.如上所述的方面和任一可能的实现方式,进一步提供一种实现方式,所述s4中预沉积tmo湿膜在加热盘上完成预退火,其中加热盘温度为30-150℃,预退火时间为1-30min。
20.如上所述的方面和任一可能的实现方式,进一步提供一种实现方式,所述s5中n2等离子处理过程,采用高纯n2或者超纯n2作为等离子气源,气流量为10-700sccm,等离子处
理功率为10-200w,等离子处理温度为25-250℃,等离子处理时间为30s-60min,等离子处理压强为500-1500mtorr。
21.所述s5中后退火环境包括大气环境、n2环境、o2环境、ar环境,此外退火温度为25-250℃,退火时间为0-12h;其中退火时间为0h时,不对tmo薄膜进行后退火处理。
22.如上所述的方面和任一可能的实现方式,进一步提供一种tmo薄膜器件化应用场景,通过所述tmo薄膜的超低温制备方法制备而成,所述tmo薄膜通过器件化制备后,可用于tft的有源层、太阳能电池中的电子传输层或可见光传感器中的光敏化层。
23.如上所述的方面和任一可能的实现方式,进一步提供一种tmo-tft的超低温制备方法,包括所述tmo薄膜的超低温制备方法,所述tmo-tft的超低温制备方法还包括:
24.s6:对s5中所述获得的tmo薄膜进行tft器件化制备,其中tmo薄膜用作tft的有源层,制备得到tmo-tft,并采用半导体分析仪表征其电学特性。
25.如上所述的方面和任一可能的实现方式,进一步提供一种实现方式,所述tft的结构包括底栅顶接触型、底栅底接触型、顶栅底接触型和顶栅顶接触型四种结构,四种结构的基本形式均由栅/源/漏电极、栅绝缘层、有源层组成;其中栅/源/漏电极包括但不限于金属电极和透明导电电极,电极厚度为10-200nm,其中源/漏电极形成沟道的宽长比为1-20;栅绝缘层材料包括但不限于无机绝缘层材料、pvp和蛋白质。
26.与现有技术相比,本发明可以获得包括以下技术效果:
27.1):采用n2等离子处理预退火tmo薄膜,有效的将电能转化为tmo薄膜成膜反应过程所需的化学能,可以大幅度降低成膜反应过程中凝结及致密化反应温度,从而实现tmo薄膜的超低温制备,即对s4中获得的预退火tmo薄膜进行n2等离子处理后,不需要再进行后退火处理,tmo薄膜即可成膜,或者,对s4中获得的预退火tmo薄膜进行n2等离子处理后,仅需要以较低的温度进行后退火处理,tmo薄膜即可成膜;
28.2):经n2等离子处理超低温制备tmo薄膜展现出良好的半导体特性,将其作为沟道层应用于tmo-tft时,展现出优异的电学特性,大大提高了tmo-tft与柔性基板的兼容性;
29.3):在一定的n2等离子处理条件下,有助于二元tmo薄膜在低温下结晶化,形成低温多晶氧化物;
30.4):n2等离子处理低温激活tmo薄膜的同时,实现n离子的注入,形成n掺杂tmo薄膜;
31.5):n2等离子处理相对h2,nh3,n2o,cl2等离子处理具有更低的电离能、较弱的刻蚀作用、更高的安全性及环境友好性。
32.当然,实施本发明的任一产品并不一定需要同时达到以上所述的所有技术效果。
【附图说明】
33.为了更清楚地说明本发明实施例的技术方案,下面将对实施例中所需要使用的附图作简单地介绍,显而易见地,下面描述中的附图仅仅是本发明的一些实施例,对于本领域普通技术人员来讲,在不付出创造性劳动的前提下,还可以根据这些附图获得其它的附图。
34.图1是本发明一个实施例提供的tmo薄膜以及tmo-tft的制备流程图;
35.图2是本发明一个实施例提供的n2等离子体的光发射光谱(oes);
36.图3是本发明一个实施例提供的o2等离子处理p
++
热氧化硅片的示意图;
37.图4是本发明一个实施例提供的n2等离子处理预退火in2o3薄膜的示意图;
38.图5是本发明一个实施例提供的底栅顶接触型in2o
3-tft的示意图;
39.图6是本发明一个实施例提供的70℃制备温度下,有无后退火处理in2o
3-tft的转移特性曲线;
40.图7是本发明一个实施例提供的70℃制备温度下,有无n2等离子体处理in2o
3-tft的转移特性曲线;
41.图8是本发明一个实施例提供的45℃制备温度下,n2等离子体处理in2o
3-tft的转移特性曲线。
【具体实施方式】
42.为了更好的理解本发明的技术方案,下面结合附图对本发明实施例进行详细描述。
43.应当明确,所描述的实施例仅仅是本发明一部分实施例,而不是全部的实施例。基于本发明中的实施例,本领域普通技术人员在没有作出创造性劳动前提下所获得的所有其它实施例,都属于本发明保护的范围。
44.在本发明实施例中使用的术语是仅仅出于描述特定实施例的目的,而非旨在限制本发明。在本发明实施例和所附权利要求书中所使用的单数形式的“一种”、“所述”和“该”也旨在包括多数形式,除非上下文清楚地表示其他含义。
45.本发明提供tmo薄膜和tmo-tft的超低温制备方法,所述溶液法tmo薄膜以及tmo-tft的制备方法如下,对应的制备流程图如图1所示:
46.s1、in2o3基和/或zno基前驱液的制备;
47.s2、基片的清洗及表面活化;
48.s3、采用s1中获得的前驱液在s2中清洗活化后的基片上实现预沉积tmo湿膜的制备;
49.s4、对s3中获得的预沉积tmo湿膜进行预退火,获得预退火tmo薄膜;
50.s5、对s4中获得的预退火tmo薄膜进行n2等离子处理或进行n2等离子处理与后退火,获得tmo薄膜;
51.s6、对tmo薄膜进行tft器件化制备,并表征其电学特性。
52.在一个具体实施例中,所述步骤s1中前驱液的制备过程:称取定量的前驱物,将前驱物溶于定量的前驱溶剂中,根据需求添加相应的添加剂,在0-100℃的温度下磁力搅拌0.5-24小时,获得相应的tmo前驱液,其中前驱液的浓度控制在0.01-1mol/l;
53.在一个具体实施例中,所述步骤s1中tmo前驱液的前驱物包括相应金属的金属硝酸盐、金属氯化物、金属氟化物、有机金属盐以及其它种类的金属盐类型;
54.在一个具体实施例中,所述步骤s1中tmo前驱液的前驱溶剂包括高纯水、蒸馏水、二甲氧基乙醇、乙醇、n,n二甲基甲酰胺以及其它常用的前驱溶剂;
55.在一个具体实施例中,所述步骤s1中tmo前驱液的添加剂包括单乙醇胺等稳定剂,尿素、乙酰丙酮等燃烧剂,双氧水、高氯酸等氧化剂,以及其它种类的添加剂;
56.在一个具体实施例中,所述步骤s1中最终获得的tmo前驱液种类包括水基前驱液、醇基前驱液、以及在水基及醇基前驱液的基础上通过前驱液工程开发的添加燃烧剂、强氧
化剂、反应配体以及其他添加物的前驱液。
57.在一个具体实施例中,所述步骤s1中tmo前驱液元素成分包括in2o3、或zno二元tmo前驱液、单元素掺杂in2o3或zno的三元tmo前驱液(eg.inzno、ingao、inhfo)、以及共掺杂in2o3或zno的多元tmo前驱液(eg.ingazno、ingazno:n)。
58.在一个具体实施例中,所述步骤s2中基片的清洗过程为:首先将备好的基片依次在去离子水、丙酮、异丙醇(或乙醇)、去离子水中各超声清洗5-40min,温度设置为25-70℃,然后取出基片,用氮气吹干或者用烘箱烘干;
59.在一个具体实施例中,所述步骤s2中基片的表面活化过程为:将清洗后的基片放入等离子清洗机内,等离子处理1-30min,使得基片表面活化,去除基片表面有机残余的同时,改善基片表面浸润性。其中等离子处理功率为10-200w、等离子处理温度为25-100℃、气流量为10-200sccm、等离子处理气氛为o2或ar。
60.在一个具体实施例中,所述步骤s3中预沉积tmo湿膜的成膜方式包括旋涂、棒涂、提拉、滴涂、喷墨打印技术等常规溶液法制备技术。
61.在一个具体实施例中,所述步骤s4中预沉积tmo湿膜在加热盘上完成预退火,其中加热盘温度为30-150℃,预退火时间为1-30min。
62.在一个具体实施例中,所述步骤s5中n2等离子处理过程,n2等离子处理的光发射光谱如图2所示,采用高纯n2或者超纯n2作为等离子气源,气流量为10-700sccm,等离子处理功率为10-200w,等离子处理温度为25-250℃,等离子处理时间为30s-60min,等离子处理压强为500-1500mtorr。
63.在一个具体实施例中,所述步骤s5中后退火环境包括大气环境、n2环境、o2环境、ar环境,此外退火温度为40-250℃,退火时间为0-12h。其中退火时间为0h时,不对tmo薄膜进行后退火处理。
64.在一个具体实施例中,所述步骤s6中所述器件化制备为tmo-tft制备。所述tmo-tft的结构包含底栅顶接触型、底栅底接触型、顶栅底接触型、顶栅顶接触型四种结构;
65.在一个具体实施例中,所述步骤s6中四种类型tmo-tft的结构均由最基本的栅/源/漏电极、栅绝缘层、有源层组成;
66.在一个具体实施例中,所述步骤s6中tmo-tft的栅/源/漏电极材料包括al、au、ag、cu、ni、mo、ito和azo等金属电极及透明导电电极,电极厚度为10-200nm,其中源/漏电极形成沟道的宽长比为1-20;
67.在一个具体实施例中,所述步骤s6中tmo-tft的栅绝缘层材料包括sinx、sio2、sinox、al2o3、hfox、zrox、mgo等无机绝缘层材料,以及pvp、蛋白质等有机绝缘层材料;进一步地,所述步骤s6中tft的有源层采用步骤s5获得的tmo薄膜,从而形成tmo-tft。
68.在本发明中,tmo:透明金属氧化物(transparent metal oxide),tft(thin-filmtransistor):薄膜晶体管,tmo-tft(transparent metal oxide thin-film transistor)透明金属氧化物薄膜晶体管。本发明在保证tmo薄膜具有良好半导体特性以及tmo-tft具有优异电学特性的同时,实现tmo薄膜及tmo-tft的超低温制备,从而增强tmo-tft与柔性基板的柔性兼容性,进而降低制备过程对柔性衬底的影响。其中实现tmo薄膜及tmo-tft的超低温制备的关键在于tmo薄膜制备过程中n2等离子处理的引入,其中n2等离子处理的超低温激活原理如下:
69.本发明中,通过实验设计及验证,相比h2,nh3,n2o,cl2等气源,n2在较低的温度下可以实现有效电离,其中,70℃等离子处理温度下n2等离子处理的光发射光谱(oes)如图2所示。如图所示n2在电场作用下分解成激发态氮分子(n21st-ps、n
2 2nd-ps)、正电荷氮分子(n
2+
)、激发态氮原子(n
*
)、正电荷氮原子(n
+
)、中性氮原子(n)等多种形式自由基。各种自由基在电场的作用下轰击预退火的tmo薄膜,在离子轰击的作用下,自由基将自身携带的电荷及自由能转化为tmo薄膜成膜反应所需的化学能,与此同时部分n自由基注入tmo薄膜,以填补氧空位或者替代氧原子的方式实现tmo薄膜的n掺杂。一方面,n2等离子体将电能转化为tmo薄膜成膜反应的化学能,大大降低了tmo薄膜成膜反应所需的热能,从而大大降低后退火过程中的后退火温度;另一方面,相应的n自由基通过填补氧空位,降低了tmo薄膜的氧缺陷,其中n相关自由基的掺杂还增加tmo薄膜的载流子浓度,降低了tmo薄膜的电阻率,提高了tmo薄膜的半导体特性。在过去的研究中,多认为n2等离子体处理钝化tmo薄膜,降低了tmo薄膜的载流子浓度,需要配合常见的施主掺杂等离子体(如h2等离子体、nh3等离子体)对tmo薄膜的h扩散,从而实现tmo薄膜的电阻率的降低,而本发明有别于上述针对n2等离子体处理研究的传统认识,本发明通过对n2等离子体的生成方式及生成条件的设计研究,仅通过n2等离子体处理即可实现tmo薄膜的超低温激活及薄膜电阻率的降低。综合以上作用,在n2等离子体的作用下,可以在保证tmo薄膜具有良好半导体特性以及tmo-tft具有优异电学特性的同时,实现tmo薄膜及tmo-tft的超低温制备。
70.实施例1:
71.本实施例中的基片选用商业购买的单面抛光p
++
热氧化硅片,其中热氧化硅厚度为100nm;水合硝酸铟购买于sigma-aldrich公司;超纯水为自制18.2mω去离子水。具体制备过程如下:
72.步骤1:制备in2o3前驱液:
73.先将水合硝酸铟溶于去离子水中,配置浓度为0.2mol/l,然后在室温下磁力搅拌6小时,获得无色透明的in2o3前驱液,静置以备用;
74.步骤2:基片清洗:
75.先将准备的p
++
热氧化硅片依次在去离子水、丙酮、异丙醇、去离子水中各超声清洗10min,然后用氮气吹干;
76.步骤3:基片表面活化:
77.将清洗后的p
++
热氧化硅片置于等离子清洗腔内,以100w的等离子处理功率,在室温下o2等离子体处理10min,使得基片表面活化,从而去除表面有机残余,增加表面浸润性,o2等离子处理p
++
热氧化硅片的示意图如图3所示;
78.步骤4:制备in2o3薄膜:
79.首先采用0.22μl的水系过滤头过滤in2o3前驱液,去除溶液中的不溶物杂质;然后在相对湿度小于25%的环境中将过滤后的in2o3前驱液滴加在吸附于匀胶机转盘上的p
++
热氧化硅片上,以4500转/min的转速,旋涂30s,获得in2o3湿膜;最后将in2o3湿膜置于加热盘上,在大气环境中,70℃预退火10min,从而得到预退火的in2o3薄膜;
80.步骤5:n2等离子处理预退火in2o3薄膜:
81.如图4所示,将步骤4得到的预退火in2o3薄膜置于等离子处理装置中进行n2等离子体处理30min,其中控制等离子处理温度为70℃,等离子处理功率为100w,等离子工作压强
为1000mtorr,n2的气通量为400sccm;
82.步骤6:in2o3薄膜的后退火:
83.在大气中,将步骤5中经n2等离子处理后的得到的in2o3薄膜置于加热盘上70℃后退火4h,得到后退火的in2o3薄膜;
84.步骤7:源漏电极的制备:
85.采用热蒸发的方式,采用掩膜版在步骤6中获得的后退火in2o3薄膜上镀制100nm厚的al膜作为源/漏电极,其中沟道区宽长比为1000/100μm,从而得到如图4所示的底栅顶接触型in2o
3-tft;
86.步骤8:在v
ds
=20v的条件下对制备得到的in2o
3-tft进行i-v测试,其转移特性曲线如图6、图7中n
2-plasma+70℃-4h所示。
87.对比例1:
88.选材及步骤1-5同实施例1;
89.步骤6:源漏电极的制备:
90.采用热蒸发的方式,采用掩膜版在步骤5中获得的经n2等离子处理后的in2o3薄膜上镀制100nm厚的al膜作为源/漏电极,其中沟道区宽长比为1000/100μm,从而得到如图5所示的底栅顶接触型in2o
3-tft;
91.步骤7:在v
ds
=20v的条件下对制备得到的in2o
3-tft进行i-v测试,其转移特性曲线如图6中n
2-plasma所示;
92.对比例1相对实施例1取消了后退火处理过程,对比例1的作用即作为实施例1的对比,对比n2等离子处理后有无后退火处理过程对in2o
3-tft电学性能的影响,有无后退火处理in2o
3-tft的转移特性曲线如图6所示。图6表明,在70℃n2等离子处理后,有无70℃-4h的后退火过程对in2o
3-tft的器件性能影响较小,所以在in2o
3-tft的制备过程中,在n2等离子处理的情况下,可以去除后退火过程,从而减少工艺过程,缩短工艺时间。
93.对比例2:
94.选材及步骤1-4同实施例1;
95.步骤5:in2o3薄膜的后退火:
96.在大气中,将步骤4中预退火in2o3薄膜置于加热盘上70℃后退火4h,得到后退火的in2o3薄膜;
97.步骤6:源漏电极的制备:
98.采用热蒸发的方式,采用掩膜版在步骤5中获得的后退火in2o3薄膜上镀制100nm厚的al膜作为源/漏电极,其中沟道区宽长比为1000/100μm,从而得到如图5所示的底栅顶接触型in2o
3-tft;
99.步骤7:在v
ds
=20v的条件下对制备得到的in2o
3-tft进行i-v测试,其转移特性曲线如图7中70℃-4h所示;
100.对比例2相对实施例1取消了n2等离子处理过程,对比例2的作用即作为实施例1的对比,对比有无n2等离子处理过程对in2o
3-tft电学性能的影响,如图7所示,无n2等离子体处理过程的in2o
3-tft处于未激活状态,未展现出tft的开关特性,而有n2等离子体处理过程的in2o
3-tft展现出良好的电学特性,从而表明,n2等离子体处理可以在70℃的超低温下,实现in2o
3-tft的有效激活。
101.实施例2:
102.选材及步骤1-3同实施例1;
103.步骤4:制备in2o3薄膜:
104.首先采用0.22μl的水系过滤头过滤in2o3前驱液,去除溶液中的不溶物杂质;然后在相对湿度小于25%的环境中将过滤后的in2o3前驱液滴加在吸附于匀胶机转盘上的p
++
热氧化硅片上,以4500转/min的转速,旋涂30s,获得in2o3湿膜;最后将in2o3湿膜置于加热盘上,在大气环境中,45℃预退火10min,从而得到预退火的in2o3薄膜;
105.步骤5:n2等离子处理预退火in2o3薄膜:
106.如图4所示,将步骤4得到的预退火in2o3薄膜置于等离子处理装置中进行n2等离子体处理30min,其中控制等离子处理温度为45℃,等离子处理功率为100w,等离子工作压强为1000mtorr,n2的气通量为400sccm;
107.步骤6:源漏电极的制备:
108.采用热蒸发的方式,采用掩膜版在步骤5中获得的经n2等离子处理后的in2o3薄膜上镀制100nm厚的al膜作为源/漏电极,其中沟道区宽长比为1000/100μm,从而得到如图5所示的底栅顶接触型in2o
3-tft;
109.步骤7:在v
ds
=20v的条件下对制备得到的in2o
3-tft进行i-v测试,其转移特性曲线如图8所示。如图8所示,in2o
3-tft展现出良好的电学特性,从而表明n2等离子体处理可以在45℃的超低温下,实现in2o
3-tft的有效激活。
110.以上对本技术实施例所提供的一种tmo薄膜和tmo-tft的超低温制备方法,进行了详细介绍。以上实施例的说明只是用于帮助理解本技术的方法及其核心思想;同时,对于本领域的一般技术人员,依据本技术的思想,在具体实施方式及应用范围上均会有改变之处,综上所述,本说明书内容不应理解为对本技术的限制。
111.如在说明书及权利要求书当中使用了某些词汇来指称特定组件。本领域技术人员应可理解,硬件制造商可能会用不同名词来称呼同一个组件。本说明书及权利要求书并不以名称的差异来作为区分组件的方式,而是以组件在功能上的差异来作为区分的准则。如在通篇说明书及权利要求书当中所提及的“包含”、“包括”为一开放式用语,故应解释成“包含/包括但不限定于”。“大致”是指在可接收的误差范围内,本领域技术人员能够在一定误差范围内解决所述技术问题,基本达到所述技术效果。说明书后续描述为实施本技术的较佳实施方式,然所述描述乃以说明本技术的一般原则为目的,并非用以限定本技术的范围。本技术的保护范围当视所附权利要求书所界定者为准。
112.还需要说明的是,术语“包括”、“包含”或者其任何其他变体意在涵盖非排他性的包含,从而使得包括一系列要素的商品或者系统不仅包括那些要素,而且还包括没有明确列出的其他要素,或者是还包括为这种商品或者系统所固有的要素。在没有更多限制的情况下,由语句“包括一个
……”
限定的要素,并不排除在包括所述要素的商品或者系统中还存在另外的相同要素。
113.应当理解,本文中使用的术语“和/或”仅仅是一种描述关联对象的关联关系,表示可以存在三种关系,例如,a和/或b,可以表示:单独存在a,同时存在a和b,单独存在b这三种情况。另外,本文中字符“/”,一般表示前后关联对象是一种“或”的关系。
114.上述说明示出并描述了本技术的若干优选实施例,但如前所述,应当理解本技术
并非局限于本文所披露的形式,不应看作是对其他实施例的排除,而可用于各种其他组合、修改和环境,并能够在本文所述申请构想范围内,通过上述教导或相关领域的技术或知识进行改动。而本领域人员所进行的改动和变化不脱离本技术的精神和范围,则都应在本技术所附权利要求书的保护范围内。