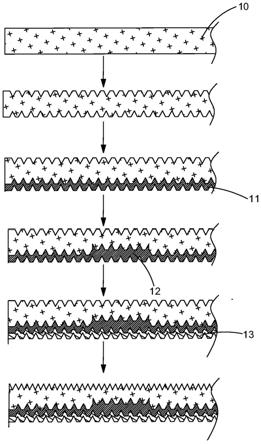
n型单晶硅双面太阳电池及其制备方法
技术领域
1.本技术涉及太阳能电池领域,具体而言,涉及一种n型单晶硅双面太阳电池及其制备方法。
背景技术:2.当前,市场上晶体硅太阳电池大多以p型的单、多晶常规铝背表面场电池为主,其制备工艺相对简单、成本低廉。但由于p型硅电池光电转换效率难以达到23.5%以上,并且未能彻底解决以p型硅片为基底的电池所产生的光衰现象,这些因素都成为其进一步量产推广的障碍。与p型硅相比,n型硅体少子寿命更长,对fe等金属有更高的容忍度,不易发生由于b-o复合体导致的lid(lightinduced degradation)光致诱导衰减现象;以n型硅为基底的电池片转换效率更高,可以相对降低光伏发电的制造成本,这使其成为高效晶体硅太阳电池的必选材料。
3.但目前n型高效电池一般需要多次高温扩散、氧化掩膜、去结刻蚀等复杂工艺,制备效率低且成本高,同时存在因刻蚀不彻底引起并联失效的问题。
技术实现要素:4.本技术提供了一种n型单晶硅双面太阳电池及其制备方法,其能够解决上述至少一个技术问题。
5.本技术的实施例是这样实现的:
6.在第一方面,本技术示例提供了一种n型单晶硅双面太阳电池的制备方法,其包括以下步骤:
7.s1、双面制绒,获得正背面分别具有第一绒面结构的n型单晶硅。
8.s2、背面磷扩散掺杂形成背表面场。
9.s3、去除正背面绕镀及psg,于背表面场的表面形成用于保护背面的第一绒面结构的掩膜,在n型单晶硅的正面制得第二绒面结构,第二绒面结构具有金字塔型绒面形貌。
10.s4、正面硼扩散掺杂形成正面掺杂发射结层。
11.s5、去除掩膜、正背面绕镀和bsg后,在正面掺杂发射结层的表面沉积钝化减反射层,于背表面场的表面沉积钝化层。
12.s6、制备正面电极、背面电极。
13.上述制备方法中,采用先进行背面加工后进行正面加工的新的工艺路线进行加工,简化制作步骤,利用掩膜的设置保护背面的第一绒面结构,避免在正面制备第二绒面结构的同时影响背面的第一绒面结构。同时将掩膜在步骤s5去除,以在进行步骤s4的硼掺杂扩时,由掩膜的存在,使得硼掺杂时不会绕扩到背面,随后在步骤s5去bsg时将背面的掩膜一起去掉,相比常规的刻蚀方法不仅节省工序,同时去除了酸抛或碱抛刻蚀工序,可以有效降低生产成本,降低高氮排放,不存在因刻蚀不彻底引起并联失效的问题,进而提升n型单晶硅双面太阳电池的双面量子转化效率及改善接触性能。
14.而且背面第一绒面结构能够保证背面具有一定的粗糙程度,能够与背面电极达到更好的接触,同时第一绒面结构可根据实际的需求进行设定,进而可减少背面的反射率,以提升n型单晶硅双面太阳电池背面量子转换效率。
15.在第二方面,本技术示例提供了一种n型单晶硅双面太阳电池,其由上述制备方法制得,其中,第一绒面结构具有平台型绒面形貌,第一绒面结构包括多个呈阵列布置的平台结构,平台结构的高度为0.3-0.5μm,每个平台结构具有与n型单晶硅相连接的下平面及与下平面相对的上平面,下平面的尺寸大于上平面,平台结构的下表面宽度为10-15μm,第一绒面结构的反射率为25-35%。
16.上述n型单晶硅双面太阳电池由于其制备工艺原因,不存在因刻蚀不彻底引起并联失效的问题,同时利用背面第一绒面结构,使得背面量子转换效率明显提升,进而提升n型单晶硅双面太阳电池的双面量子转化率。
附图说明
17.为了更清楚地说明本技术实施例的技术方案,下面将对实施例中所需要使用的附图作简单地介绍,应当理解,以下附图仅示出了本技术的某些实施例,因此不应被看作是对范围的限定,对于本领域普通技术人员来讲,在不付出创造性劳动的前提下,还可以根据这些附图获得其他相关的附图。
18.图1为步骤s1至s3的制备流程图;
19.图2为步骤s3至s6的制备流程图。
20.图标:10-n型单晶硅;11-背表面场;12-局部重掺杂区;13-掩膜;14-背面氮化硅层;15-背面电极;21-正面掺杂发射结层;22-三氧化二铝层;23-正面氮化硅层;24-正面电极。
具体实施方式
21.下面将结合实施例对本技术的实施方案进行详细描述,但是本领域技术人员将会理解,下列实施例仅用于说明本技术,而不应视为限制本技术的范围。实施例中未注明具体条件者,按照常规条件或制造商建议的条件进行。所用试剂或仪器未注明生产厂商者,均为可以通过市售购买获得的常规产品。
22.以下针对本技术实施例的n型单晶硅双面太阳电池及其制备方法进行具体说明:
23.请参阅图1以及图2,一种n型单晶硅双面太阳电池的制备方法,其包括以下步骤:
24.s1、双面制绒,获得正背面分别具有第一绒面结构的n型单晶硅10。
25.其中,请参阅图1,第一绒面结构具有平台型绒面形貌,其包括多个呈阵列布置的平台结构,每个平台结构具有与n型单晶硅10相连接的下平面及与下平面相对的上平面,下平面的尺寸大于上平面。
26.可选地,平台结构的高度为0.3-0.5μm,平台结构的下表面宽度为10-15μm,平台型绒面形貌的反射率为25-35%。
27.其中,步骤s1中,双面制绒的步骤包括:先使用强碱水溶液进行碱制绒,获得正背面分别呈金字塔绒面形貌的n型单晶硅10,然后对正背面分别呈金字塔绒面形貌的n型单晶硅10进行酸制绒,获得正背面分别呈平台型绒面形貌(也即是第一绒面结构)的n型单晶硅
10。
28.上述步骤中,采用先碱制绒形成金字塔绒面形貌,然后利用酸将金字塔绒面形貌的顶端使用化学的方法腐蚀掉,形成平台型绒面形貌,该制备过程简单可控,且平台型绒面形貌可减少背面的反射率,还能够保证背面一定的粗糙程度,能够与背面电极15达到更好的接触,提升n型单晶硅双面太阳电池的背面的量子转化效率。
29.可选地,碱制绒的步骤包括:浸渍在含有制绒添加剂且强碱的质量浓度为1.5-3%的强碱水溶液,在65-75℃的条件下制绒50-200s,例如制绒50s、70s、100s、130s、150s、180s或200s等。此处的强碱例如为naoh溶液或koh溶液。制绒添加剂用于控制生长的金字塔大小及高度,其为可直接购买于市面常规制绒添加剂,在此不做限定。
30.可选地,酸制绒的步骤包括:浸渍在由体积比为0.9-1.1:0.9-1.1,例如体积比为0.9:1、0.9:1.1、1:1、1.1:0.9等的氢氟酸水溶液和硝酸水溶液组成的酸液在8-15℃制绒20-100s,例如制绒20s、30s、50s、70s、80s或100s等,其中氢氟酸水溶液的质量浓度为20-40%,硝酸水溶液的质量浓度为20-40%。
31.通过上述特定的配比,可将金字塔绒面形貌的顶端削平,形成平台型绒面形貌。
32.需要说明的是,由于双面制绒过程中,温度、浓度的不均匀将严重影响平台结构的均匀性以及尺寸,因此可选地,本技术实施例双面制绒及后续步骤s3中的正面制绒,均采用cn201910331455.4所示的制绒槽进行,由于上述制绒槽对硅片酸洗进行精确的温度控制,通过专门的弧形槽底结合搅拌装置,通过机械搅拌及氮气气泡搅拌,可以最大程度的使整个槽体内溶液的浓度和温度达到均衡,从而可以控制绒面的反应速度,得到背面及背面出现平台型绒面结构。
33.可选地,n型单晶硅10的尺寸≥180mm,也即是采用上述装置采用上述制备方式,适用于n型单晶硅10的尺寸≥180mm的大型单晶硅,可保证得到的平台型绒面结构中平台结构的均匀布置。
34.s2、背面磷扩散掺杂形成背表面场11。
35.背面磷扩散掺杂的方式可采用低压扩散工艺,以形成高表面浓度浅结。
36.其中,低压扩散工艺的低压扩散的压强为50-100mpa,磷源流量为800-1200sccm,后氧化3-8min,推结温度为840-860℃。通过两步沉积工艺,最终在n型单晶硅10的背面依次生成背表面场11以及psg(磷硅酸盐玻璃),磷扩散后得到的n型单晶硅10的方阻为150-170ω之间。
37.在一些可选地示例中,背面磷扩散掺杂形成背表面场11后,步骤s2还包括:采用激光在n型单晶硅10的背面预备设置背面电极15的位置进行局部重掺杂,以获得局部重掺杂区12,进而实现选择性磷扩散的目的,进而提高背面收集率,改善背面电极15烧结性能,同时使得表层的psg变的疏松和稀薄,便于后续去除。
38.s3、请参阅图1以及图2,去除正背面绕镀及psg,于背表面场11的表面形成用于保护背面的平台型绒面结构的掩膜13,在n型单晶硅10的正面制得第二绒面结构,第二绒面结构具有金字塔型绒面形貌。
39.其中,可采用氢氟酸水溶液清洗步骤s2得到的n型单晶硅10,进而利用hf去除正背面绕镀及psg。此处采用的氢氟酸水溶液的质量浓度为5-50%,可选为20-40%。
40.可选地,在n型单晶硅的正面制得第二绒面结构的步骤包括:浸渍在体积浓度为
1.5-3%的强碱水溶液中,于65-75℃的条件下制绒50-200s,然后依次采用氢氟酸水溶液及盐酸水溶液进行表面清洗。
41.也即是采用碱制绒的方式将平台型绒面形貌变为金字塔型绒面形貌。
42.可选地,掩膜13的材质包括氮化硅,其与后续制备金字塔型绒面形貌的强碱溶液不反应,有效保护背面平台型绒面形貌,避免背表面场的深度在步骤s4中显著增加。
43.其中,掩膜13可采用板式pecvd制得。
44.可选地,掩膜13的厚度为15-25nm,例如掩膜13的厚度为15nm、17nm、19nm、20nm、22nm、24nm或25nm等。
45.也即是,利用掩膜13的设置保护背面的平台型绒面形貌,避免在正面制备金字塔型绒面形貌的同时影响背面的平台型绒面形貌。同时将掩膜13在步骤s5去除,以在进行步骤s4的硼掺杂扩时,由掩膜13的存在,使得硼掺杂时不会绕扩到背面,随后在步骤s5去bsg时将背面的掩膜13一起去掉,相比常规的刻蚀方法不仅节省工序,同时不存在因刻蚀不彻底引起并联失效的问题,进而提升n型单晶硅双面太阳电池的双面量子转化效率及改善接触性能。
46.s4、正面硼扩散掺杂形成正面掺杂发射结层21。
47.在正面进行硼扩散掺杂,产生正面掺杂发射结层21,同时产生bsg。
48.s5、去除掩膜13、正背面绕镀和bsg后,在正面掺杂发射结层21的表面沉积钝化减反射层,于背表面场11的表面沉积钝化层。
49.其中,去除正背面绕镀、bsg以及掩膜13的步骤包括:采用氢氟酸水溶液清洗去除所述掩膜、正背面绕镀和bsg。也即是相比于现有技术对于去除绕镀没有经过刻蚀工序,只需经过氢氟酸浸泡即可,节省工序流程,进而降低n型单晶硅双面太阳电池的生产成本。其中,氢氟酸水溶液的质量浓度为5-50%,可选为20-40%。
50.可选地,在氢氟酸水溶液中去除正背面绕镀、bsg以及掩膜13,然后进行清洗,去除效果佳。
51.可选地,在正面掺杂发射结层21的表面沉积钝化减反射层的步骤包括:在正面掺杂发射结层21的表面依次沉积三氧化二铝层22以及正面氮化硅层23,其中三氧化二铝层22厚度在1-3nm,氮化硅层厚度为75-82nm,上述三氧化二铝层22可有效降低绕镀,实现氧化铝对n型太阳能电池的高效钝化,结合氮化硅层,有效提升钝化效果。
52.可选地,在背表面场11的表面沉积钝化减反射层的步骤包括:在背表面场11的表面沉积背面氮化硅层14,此处背面氮化硅层14膜厚为80-85nm,例如氮化硅层膜厚为80nm、82nm、83nm、84nm或85nm等。
53.s6、制备正面电极24、背面电极15。
54.正面电极24、背面电极15的材质包括但不局限于银、铝、铜、镍、钛、锡、铅、镉、金、锌的一种或多种金属或其合金。
55.可选地,制备正面电极24、背面电极15的步骤包括:印刷正面和背面的银浆栅线后烧结。
56.本技术还提供一种n型单晶硅双面太阳电池,其由上述制备方法制得。
57.其中,其中,第一绒面结构具有平台型绒面形貌,第一绒面结构包括多个呈阵列布置的平台结构,平台结构的高度为0.3-0.5μm,每个平台结构具有与n型单晶硅相连接的下
平面及与下平面相对的上平面,下平面的尺寸大于上平面,平台结构的下表面宽度为10-15μm,第一绒面结构的反射率为25-35%。
58.以下结合实施例对本技术的n型单晶硅双面太阳电池及其制备方法作进一步的详细描述。
59.实施例1
60.1、获得995片厚度为180
±
5μm,大小为210mm
×
210mm的n型单晶硅。
61.2、双面制绒:对每片n型单晶硅的表面进行清洗,然后对其先进行碱制绒,利用购买于时创的碱制绒添加剂(以下简称为制绒时创添加剂)控制其生长的金字塔大小及高度,然后在制绒槽中进行控温酸制绒,制得正背面分别具有平台型绒面形貌的n型单晶硅作为样品1,平台型绒面形貌包括多个呈阵列布置的平台结构,每个平台结构具有与n型单晶硅相连接的下平面及与下平面相对的上平面,下平面的尺寸大于上平面。
62.其中,碱制绒的步骤包括:采用质量浓度为2%的氢氧化钾水溶液,温度为70℃,制绒时间为180s,制绒添加剂为时创添加剂,其与氢氧化钾水溶液按照质量比为9:10的条件混合。
63.控温酸制绒配比:采用由体积比为1:1的氢氟酸水溶液和硝酸水溶液组成的酸液在10℃制绒80s,其中氢氟酸水溶液的质量浓度为30%,硝酸水溶液的质量浓度为30%。
64.经过测试,平台结构的下表面宽度为14μm,高度为0.4μm,反射率(全波段300-1200nm)为27%。
65.3、背面磷扩散掺杂:采用低压高温扩散工艺对样品1进行背面磷扩散掺杂,最终在电池背面生成背表面场以及psg,作为样品2。其中,低压扩散工艺采用:压强为75mpa,磷源流量为1000sccm,后氧化5min,推进温度为850℃。扩散后的方阻为160ω/sq。
66.4、激光se:激光在样品2的背面预备设置背面电极的位置进行激光脉冲加热,使磷原子向硅基体扩散分别形成局部重掺杂区,作为样品3,其中局部重掺杂区的测试方阻为80ω/sq。
67.5、去psg和背面形成掩膜:通过hf水溶液清洗去除样品3正背面的psg,然后再利用板式pecvd在背面形成一层氮化硅掩膜,作为样品4。
68.其中,氮化硅掩膜的厚度为21nm。
69.6、碱制绒:将样品4先经过质量浓度为35%的hf水溶液清洗,去除步骤5中n型单晶硅的正面在板式pecvd高温过程中生成的少量的氧化层清洗掉,然后对清洗后的样品4进行碱制绒,碱制绒步骤中减重控制在0.255g/片。然后经过质量浓度为21%的hf水溶液清洗,再经过质量浓度为23%的hcl水溶液清洗,获得样品5,样品5的n型单晶硅的正面具有反射率为9.7%的金字塔型绒面形貌。
70.其中,碱制绒的步骤包括:采用含有制绒时创添加剂且koh强碱质量浓度为2%的强碱水溶液,在70℃的条件下制绒180s。
71.7、硼扩后再进行去bsg:对样品5的n型单晶硅的正面进行硼扩散掺杂之后,再进入去bsg设备中,正面硼扩层的方阻为77ω/sq时,采用质量浓度为24%的hf水溶液去除bsg及氮化硅掩膜,并进行清洗,作为样品6。
72.8、ald:在样品6的正面生长一层三氧化二铝,测试其厚度在2.5nm,作为样品7。
73.9、镀膜工序:在样品7的正面和背面分别生长一层氮化硅,其中正面的氮化硅膜厚
为80nm,背面的氮化硅膜厚为82nm。
74.10、印刷正面和背面的银浆栅线后烧结。
75.最终获得成品985片,对实施例1获得的985片n型单晶硅双面太阳电池进行性能测试,每片n型单晶硅双面太阳电池的平均性能参数的结果如表1所示。
76.表1试验结果
[0077][0078]
实施例2
[0079]
1、获得1024片厚度为180
±
5μm,大小为210mm
×
210mm的n型单晶硅。
[0080]
2、双面制绒:对每片n型单晶硅的表面进行清洗,然后对其先进行碱制绒,利用时创制绒添加剂控制其生长的金字塔大小及高度,然后在制绒槽中进行控温酸制绒,制得正背面分别具有平台型绒面形貌的n型单晶硅作为样品1,平台型绒面形貌包括多个呈阵列布置的平台结构,每个平台结构具有与n型单晶硅相连接的下平面及与下平面相对的上平面,下平面的尺寸大于上平面。
[0081]
其中,碱制绒的步骤包括:采用质量浓度为3%的氢氧化钾水溶液,温度为72℃,制绒时间为170s,制绒添加剂时创,其与氢氧化钾水溶液按照质量比为7:19的条件混合。
[0082]
控温酸制绒配比:采用由体积比为1:1的氢氟酸水溶液和硝酸水溶液组成的酸液在10℃制绒82s,其中氢氟酸水溶液的质量浓度为30%,硝酸水溶液的质量浓度为30%。
[0083]
经过测试,实施例1平台结构的下表面宽度为14.5μm,高度为0.32μm,反射率(全波段300-1200nm)为33%。
[0084]
3、背面磷扩散掺杂:采用低压扩散工艺对样品1进行背面磷扩散掺杂,最终在电池背面生成背表面场以及psg,作为样品2。其中,低压扩散工艺采用:压力为75mpa,磷源流量为1000sccm,后氧化5min,推结温度为850℃。扩散后的方阻为160ω/sq。
[0085]
4、激光se:激光在样品2的背面预备设置背面电极的位置进行激光脉冲加热,使磷原子向硅基体扩散分别形成局部重掺杂区,作为样品3,其中重掺杂区的测试方阻为80ω/sq。
[0086]
5、去psg和背面形成掩膜:通过hf水溶液清洗去除样品3正背面的psg,然后再利用板式pecvd在背面形成一层氮化硅掩膜,作为样品4。
[0087]
其中,氮化硅掩膜的厚度为21nm。
[0088]
6、碱制绒:将样品4先经过质量浓度为35%的hf水溶液清洗,去除步骤5中n型单晶硅的正面在板式pecvd高温过程中生成的少量的氧化层清洗掉,然后对清洗后的样品4进行碱制绒,碱制绒步骤中减重控制在0.255g/片。然后经过质量浓度为21%的hf水溶液清洗,再经过质量浓度为23%的hcl水溶液清洗,获得样品5,样品5的n型单晶硅的正面具有反射率为9.7%的金字塔型绒面形貌。
[0089]
其中,碱制绒的步骤包括:采用含有时创制绒添加剂且koh强碱质量浓度为2%的强碱水溶液,在70℃的条件下制绒180s。
[0090]
7、硼扩后再进行去bsg:对样品5的n型单晶硅的正面进行硼扩散掺杂之后,再进入
去bsg设备中,正面硼扩层的方阻为77ω/sq时,采用质量浓度为24%的hf水溶液去除bsg及氮化硅掩膜,并进行清洗,作为样品6。
[0091]
8、ald:在样品6的正面生长一层三氧化二铝,测试其厚度在2nm,作为样品7。
[0092]
9、镀膜工序:在样品7的正面和背面分别生长一层氮化硅,其中正面的氮化硅膜厚为80.1nm,背面的氮化硅膜厚为82.4nm。
[0093]
10、印刷正面和背面的银浆栅线后烧结。
[0094]
最终获得成品1011片,对实施例2获得的1011片n型单晶硅双面太阳电池的采用实施例1的测试方式进行性能测试,每片n型单晶硅双面太阳电池的平均性能参数的结果如表2所示。
[0095]
表2试验结果
[0096][0097]
对比例1
[0098]
n型单晶硅双面太阳电池,其具体包括以下步骤:
[0099]
1、获得1055片厚度为180
±
5μm,大小为210mm
×
210mm的n型单晶硅。
[0100]
2、双面制绒:对每片n型单晶硅的表面进行清洗,然后对其先进行碱制绒,利用制绒时创添加剂控制其生长的金字塔大小及高度,其中,碱制绒的步骤包括:采用质量浓度为2%的氢氧化钾水溶液,温度为70℃,制绒时间为180s,制绒添加剂为时创添加剂,其与氢氧化钾水溶液按照质量比为9:10的条件混合。
[0101]
3、n型单晶硅的正面进行硼扩散掺杂之后,正面硼扩层的方阻为77ω/sq。
[0102]
4、采用背面进行链式酸洗,质量浓度为24%的hf水溶液去除bsg进行清洗。
[0103]
5、在背面形成台阶结构绒面,使用含四甲基氢氧化铵和异丙醇的碱性药液,温度是80℃,时间是700s,制备台阶绒面,同时去除背面硼掺杂层。
[0104]
6、背面磷扩散,低压扩散工艺采用:压力为75mpa,磷源流量为1000sccm,后氧化5min,推结温度为850℃。扩散后的方阻为80ω/sq。
[0105]
7、背面ald:在样品6的正面生长一层三氧化二铝,测试其厚度在2.3nm。
[0106]
8、镀膜工序:的正面和背面分别生长一层氮化硅,其中正面的氮化硅膜厚为80.1nm,背面的氮化硅膜厚为82.7nm。
[0107]
9、印刷正面和背面的银浆栅线后烧结。
[0108]
最终获得成品1046片,对对比例1获得的1046片n型单晶硅双面太阳电池采用实施例1的测试方式进行性能测试,每片n型单晶硅双面太阳电池的平均性能参数的结果如表3所示。
[0109]
表3测试数据
[0110]
片数eta/%uoc/visc/aff/%rs/ωrsh/ωirev 2/a104623.1240.683010.15481.4660.0044238.70.043
[0111]
根据表1以及表3数据对比可以看出,在其他参数相差不多的条件下,对比例1的并联电阻rsh显著低于实施例1、2,说明采用本技术的方式由于特定的制备流程以及掩膜的存
在,可避免因刻蚀不彻底引起并联失效的问题。
[0112]
综上,本技术提供的n型单晶硅双面太阳电池的制备方法制作步骤简单,去除了酸抛或碱抛刻蚀工序,可以有效降低生产成本,避免因刻蚀不彻底引起并联失效的问题,而且背面第一绒面结构的引入,可减少背面的反射率,还能够保证背面具有一定的粗糙程度,能够与背面电极达到更好的接触,提升n型单晶硅双面太阳电池背面量子转换效率。
[0113]
以上所述仅为本技术的具体实施例而已,并不用于限制本技术,对于本领域的技术人员来说,本技术可以有各种更改和变化。凡在本技术的精神和原则之内,所作的任何修改、等同替换、改进等,均应包含在本技术的保护范围之内。