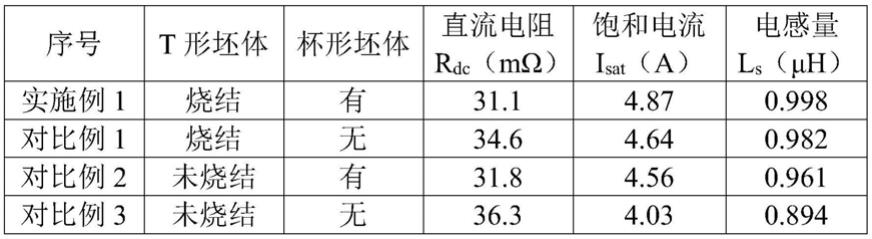
1.本发明涉及电感器的制造领域,尤其涉及一种片状功率电感的制造方法。
背景技术:2.随着电子信息产业的飞速发展,下游电子器件、通讯设备也逐渐向高频、小型、低压大电流方向发展,传统的插装式电感已不能满足下游电子整机的需求,而体积小、成本低、屏蔽性能优良、可靠性高、适合于高密度表面安装的贴片式电感在移动通讯、计算机、汽车电子、高分辨电视、广播卫星等领域获得广泛应用,逐步成为电感市场的主流。
3.目前片状功率电感的制造工艺较多,但基本方法为:(1)预先绕制空心线圈,将空心线圈放入模具的模穴内,然后将制备的软磁合金粉填充到模具内,压制获得片状功率电感的坯体,再进行后续的固化、制作电极等步骤(如专利cn111210986a、cn107689280a等);或者(2)先预制磁芯,然后制造磁芯和线圈的组合体,将磁芯和线圈组合体放入模具内,然后在模具内填入粉料,模压成型获得电感坯体,再进行后续的固化、制作电极等步骤(如专利cn104616878a、cn107768069a等)。
4.为适应当前功率电感向小型化、高频化、大电流化的发展需求,其内部线圈尺寸与电感成品的尺寸越来越接近,即在模压成型过程中,线圈与模穴侧壁之间的空间越来越小,这对功率电感的制造工艺提出了更高的要求,上述现有片状电感的制造工艺已难以满足当下需求,主要存在以下的缺陷:
5.(1)线圈与模穴壁之间的空隙太小,直接填粉会使模具内填粉不均匀,容易造成电感侧壁上粉料填充密度低、甚至线圈裸露的现象,显著降低电感成品的屏蔽性能和电感值;
6.(2)产品压制成型时需施加足够大的压力才能获得高的压实密度,但是压力过高容易使缠绕在坯体上的线圈被粉料刺破,使得层间绝缘不良,且在压制过程中会使得线圈变形,导致线圈变化量大;压力过低又会使得粉末压制的电感密度偏低,最终使得电感值偏低,影响后端产品的性能。
7.因此,针对目前片状功率电感制造方法上的不足,有待于做进一步的改进。
技术实现要素:8.针对现有技术中存在的问题,本发明提供一种片状功率电感的制造方法,本发明采取预制t形和杯形坯体,然后将t形、杯形坯体组合后热压成型的方式,即可获得性能优异的片状功率电感,与现有电感制造工艺相比,电感的压实密度均匀,线圈包覆完全、无变形,且电感性能稳定。
9.一种片状功率电感的制造方法,具体包括以下步骤:
10.s1、t形烧结坯体制备:将软磁合金粉材加工制备成t形烧结坯体;
11.s2、绕线:在步骤s1制得的所述t形烧结坯体的柱状凸起绕制漆包线,并将两端引脚折弯后贴合到所述t形烧结坯体的平板底面,得到绕线的t形烧结坯体;
12.s3、杯形坯体制备:将软磁合金粉材装入杯形模具中压制成型,获得杯形坯体,所
述杯形坯体不脱模,随模具进入下一步骤;
13.s4、热压成型:将步骤s3中制得的杯形坯体开口朝上随模具放置,将步骤s2中制得的所述绕线的t形烧结坯体按凸起处朝下植入到带有所述杯形坯体的模穴内,然后进行热压成型,得到第一电感坯体并进行烘烤,得到固化的电感坯体;
14.s5、喷涂:在步骤s4制得的所述电感坯体的表面喷涂绝缘树脂保护材料,得到片状功率电感半成品;
15.s6、电极制作:将步骤s5制得的所述片状功率电感半成品的铜电极处的绝缘保护材料和铜线漆皮剥除,并在剥漆处电镀电极,获得所述片状功率电感。
16.优选的,所述步骤s1中的t形烧结坯体的制备方法包括:将软磁合金粉材装入预设结构和尺寸的t形模具中进行压制成型,然后脱模、致密获得t形烧结坯体。
17.优选的,所述步骤s1中的t形烧结坯体的制备方法也可以包括:将软磁合金粉材,装入预设结构和尺寸的块状模具中并进行压制成型,然后脱模、烧结,之后采用机加工切削的方式获得t形烧结坯体;
18.优选的,步骤s1和步骤s3中所述软磁合金粉材包括软磁合金粉末、粘结剂和润滑剂等原料,经原料混合、造粒、筛分而制成。
19.所述粘结剂包括环氧树脂、聚氨酯、硅酮树脂、有机硅树脂、氨基树脂、聚酰亚胺、酚醛树脂、氰酸脂、丙烯酸树脂中的至少一种;粘结剂的含量为软磁合金粉末总质量的1%-5%。
20.所述润滑剂包括硬脂酸锌、硬脂酸镁、硬脂酸铝、硬脂酸钙、石墨粉和石墨烯中的至少一种;润滑剂的含量为软磁合金粉末总质量的0.1%-1%。
21.优选的,所述软磁合金粉末包括非晶软磁合金粉末、纳米晶软磁合金粉末、铁硅铝合金粉末、铁硅铬合金粉末、铁硅合金粉末、铁硅镍合金粉末、铁硅铝镍合金粉末、铁镍合金粉末、铁镍铝合金粉末、羰基铁粉中的至少一种。
22.优选的,步骤s1和步骤s3中,所述压制成型是采用高精度伺服成型压机进行冷压成型,冷压压力为2t/cm
2-15t/cm2,保压时间为0.3s-30s;所述坯体的烧结温度为400-700℃,烧结时间为1-8h。采用高温烧结可以使粉料中的部分有机物碳化挥发,有助于提高坯体强度,最终制得高强度的电感。
23.优选的,步骤s2中采用精密绕线机在所述t形烧结坯体的柱状凸起上精密绕制漆包线。
24.优选的,步骤s4中热压成型采用压力为0.5t/cm
2-10t/cm2,保压时间为1s-200s。
25.优选的,步骤s5中采用恒温加热喷涂设备进行喷涂,喷涂后可采用烘烤的方式使涂层材料固化;所述烘烤的温度为80℃-200℃,烘烤时间为0.5h-5h。
26.所述绝缘树脂保护材料包括环氧树脂、酚醛树脂、玻璃增强聚酯、硅树脂、聚酯类树脂、有机硅树脂中的至少一种。
27.优选的,步骤s6中采用激光剥漆设备将所述电感半成品的铜电极处的绝缘树脂保护材料和铜线漆皮剥除。
28.与现有技术相比,本发明主要有以下优点:
29.(1)本发明采用预制t形、杯形坯体组合压制制备电感,替代现有制造工艺中直接填粉的方法,能够有效提高电感中软磁粉材的填充密度,同时可以保护线圈,避免线圈在热
压过程中裸露、变形、甚至破裂,从而保证电感的屏蔽性能和电感值,提升产品的综合性能;杯形坯体不脱模,与t形坯体组合时可缩短工艺流程,节约时间,提高生产效率。
30.(2)本发明中t形坯体经冷压压制并烧结获得,提高了软磁材料的密度、电感量及电感坯体的强度,使得产品性能更为优异。
附图说明
31.图1为本发明实施例片状功率电感的制造方法的流程图;
32.图2为本发明实施例片状功率电感的t形坯体冷压成型的示意图;
33.图3为本发明实施例片状功率电感中t形坯体冷压成型后的立体图;
34.图4为本发明实施例片状功率电感中t形烧结坯体绕线后的立体图;
35.图5为本发明实施例片状功率电感的杯形坯体冷压成型的示意图;
36.图6为本发明实施例片状功率电感的杯形坯体立体图;
37.图7为本发明实施例片状功率电感的热压成型示意图;
38.图8为本发明实施例片状功率电感成品的结构示意图;
39.图9为对比例制备的片状功率电感成型的示意图;
40.附图标示:11、冷压成型模具上冲;12、冷压成型模具中模;13、冷压成型模具下冲;2、t形烧结坯体;21、第一t形坯体;22、柱状凸起;23、坯体底面;3、杯形坯体;41、热压成型模具上冲;42、中模底座;5、线圈;6、铜线引脚;61、电极;7、软磁合金粉末;8、绝缘保护材料;图中箭头方向为冷压成型模具上冲和热压成型模具上冲冲压方向。
具体实施方式
41.下面将结合本发明实施例中的附图,对本发明实施例中的技术方案进行清楚、完整地描述,显然,所描述的实施例仅仅是本发明一部分实施例,而不是全部的实施例。基于本发明中的实施例,本领域普通技术人员在没有作出创造性劳动的前提下所获得的所有其他实施例,都属于本发明保护的范围。
42.需要说明的是,在不冲突的情况下,本发明中的实施例及实施例中的特征可以相互组合。
43.下面结合附图和具体实施例对本发明作进一步说明,但不作为本发明的限定。
44.本发明提供一种片状功率电感的制造方法,属于电感器的制造领域,主旨是解决现有技术中电感侧壁粉料填充密度低、线圈裸露、电感量低等问题,本发明预制t形、杯形坯体组合压制制备电感,替代现有制造工艺中直接填粉的方法,通过对预制t形+杯形坯体的重量和尺寸管控,解决现有制造工艺中因直接填粉时粉料松散,压实密度低的问题;预制的t形坯体经冷压压制并烧结获得,提高了软磁材料的密度、电感量及电感坯体的强度,制备同密度电感仅需较小的成型压力,采用t形+杯形坯体制备电感,可以保护线圈,避免线圈在热压过程中变形、破裂,从而保证电感使用的稳定性,提升产品的综合性能。图1为本发明片状功率电感的制造方法的流程图。
45.实施例1
46.本实施例中软磁合金粉材选用fe-ni软磁合金粉末与铁粉混合的复合粉末,所用粘结剂为环氧树脂和硅酸钠,所用润滑剂为硬脂酸锌,将fe-ni软磁合金粉末和铁粉按照预
设的第一质量比5:5混合均匀形成粉料,将粉料与粘结剂、润滑剂和丙酮按照预设的第二质量比100:3:0.1:12、环氧树脂和硅酸钠质量比1:2混合均匀后进行造粒,并用超声波振动筛筛选出粒径在-80目至+200目的粉料,从而得到目标软磁粉材,本实施例中功率电感的制备方法具体包含以下步骤:
47.s1、t形烧结坯体制备:如图2所示,将筛选好的软磁合金粉材装入由冷压成型模具中模12、冷压成型模具下冲13组成的预设结构和尺寸的t形模具中,启动高精密伺服成型压机的冷压成型模具上冲11向下冲压成型(如图2箭头所示),并施加超声波振动,然后脱模,获得由柱状凸起22和坯体底面23组成的第一t形坯体21(如图3所示),将第一t形坯体21放入真空热处理炉中进行烧结致密,得到t形烧结坯体2,对其重量、外观进行检测;
48.其中,压制成第一t形坯体21时所采用的冷压压力为6t/cm2,保压时间为1s;烧结第一t形坯体21时所采用的烧结保温温度为450℃,烧结时间为4h。
49.s2、绕线:采用精密绕线机在由步骤s1中烧结制得、并且重量和外观检测合格的t形烧结坯体2的柱状凸起22上精密绕制线圈5,并将两端铜线引脚6折弯后贴合到t形烧结坯体2的平板底面,得到绕线的t形烧结坯体2(如图4所示)。
50.s3、杯形坯体制备:如图5所示,将筛选好的软磁合金粉材装入由冷压成型模具中模12、冷压成型模具下冲13组成的预设结构和尺寸的杯形模具中,启动高精密伺服成型压机的冷压成型模具上冲11向下冲压成型(如图5箭头所示),并施加超声波振动,获得带有凹槽的杯形坯体3(如图6所示),所述杯形坯体3与冷压成型模具中模12不脱离,随模具进入下一步骤;
51.其中,压制成杯形坯体时所采用的冷压压力为3t/cm2,保压时间为1s。
52.s4、热压成型:如图7所示,将步骤s3中制得的杯形坯体3呈开口朝上放置中模12,并固定于中模底座42上,将步骤s2中制得的绕有线圈5的t形烧结坯体2柱状凸起22朝下植入装有杯形坯体3的中模12的模穴内,然后启动热压成型模具上冲41向下冲压(如图7中箭头所示),制得第一电感坯体,再对第一电感坯体进行烘烤,得到固化的电感坯体;
53.其中,热压时所采用的热压压力为3t/cm2,保压时间150s,对第一电感坯体进行烘烤固化处理,具体的,将第一电感坯体放入烘箱中进行烘烤,使第一电感坯体中杯形坯体内部的树脂发生固化反应得到电感坯体。此处采用的树脂是环氧树脂,在固化时仅有较小的体积收缩,不至于让电感坯体在固化成型后变形。具体地,烘烤固化温度为150℃,此处可选用带有升降温阶梯曲线的烘烤设备,保温3h,最终获得电感半成品,电感半成品的尺寸为2.0mm
×
1.6mm
×
1.0mm。
54.s5、喷涂:采用恒温加热喷涂设备,在步骤s4制得的电感坯体表面喷涂一层环氧树脂保护材料,然后烘烤喷涂后的电感半成品,使电感半成品表面的环氧树脂固化。其中,烘烤条件为:在150℃下烘烤2h,使电感半成品表面树脂固化并且获得一定强度。
55.s6、电极制作:采用激光剥漆设备将步骤s5制得的电感半成品的铜电极处、即铜线引脚6处的环氧树脂保护材料和铜线漆皮剥除,使底部铜电极显露出来,在剥漆处电镀铜层、镍层和锡层,实现电极61引出,获得片状功率电感。如图8所示为片状功率电感成品结构示意图,软磁合金粉材7将漆包线圈5包覆于内部、与漆包线圈5上端面垂直的一平面上部有两个平行设置的电极61,功率电感外部喷涂有绝缘保护材料8,此处的绝缘保护材料选用的是环氧树脂。
56.对制备的功率电感进行测试,设定电感标准电感量为1μh,利用阻抗分析仪测试在1v,1mhz条件下的电感值ls为0.998μh,直流电阻r
dc
为31.1mω;饱和电流i
sat
为4.87a。
57.对比例1:
58.本对比例采用与实施例1相同的软磁合金粉材,具体制备步骤如下:
59.s1、t形烧结坯体制如实施例1中s1;
60.s2、绕线如实施例1中s2,得到绕线的t形烧结坯体2。
61.s3、热压成型:如图5所示,将筛选好的软磁合金粉材7填入热压成型模具中模42内的t形烧结坯体2和线圈5的顶部及线圈与模穴侧壁形成的缝隙内,启动热压成型模具上冲41向下冲压(如图9中箭头所示),制得第一电感坯体,再对第一电感坯体进行烘烤,得到固化的电感坯体;
62.其中,热压时所采用的热压压力为3t/cm2,保压时间150s,对第一电感坯体进行烘烤固化处理,具体的,将第一电感坯体放入烘箱中进行加热升温,使第一电感坯体中的树脂发生固化反应得到电感坯体。此处采用的树脂是环氧树脂,在固化时仅有较小的体积收缩,不至于让电感坯体在固化成型后变形。具体地,烘烤固化温度为150℃,此处可选用带有升降温阶梯曲线的烘烤设备,保温3h,最终获得电感半成品,电感半成品的尺寸为2.0mm
×
1.6mm
×
1.0mm。
63.s4、喷涂如实施例1中s5。
64.s5、电极制作如实施例中s6。采用与实施例1相同的性能测试条件,获得的性能参数如表1中所示。
65.对比例2:
66.选用与实施例1中相同的软磁合金粉材,仅对制备的t形坯体置于180℃带有升降温阶梯曲线烘烤设备中烘烤30min,不进行烧结处理,选用与实施例1相同的方法制备杯形坯体,其余制造方法、步骤、工艺参数与实施例1相同,获得片状功率电感。采用与实施例1相同的性能测试条件,获得的性能参数如表1中所示。
67.对比例3:
68.选用与实施例1中相同的软磁合金粉材,仅对制备的t形坯体置于180℃带有升降温阶梯曲线烘烤设备中烘烤30min,不进行烧结处理,且不制备杯形坯体3,其余制造方法、步骤、工艺参数与对比例1相同,获得片状功率电感。采用与实施例1相同的性能测试条件,获得的性能参数如表1中所示。
69.由此,上述实施例1以及对比例1-3得到的性能参数如下表1所示:
70.表1实施例1及对比例1-3制得的片状功率电感的性能参数
[0071][0072]
实施例2:
[0073]
本实施例中软磁合金粉末选用fe-si-b-nb-cu纳米晶软磁合金粉末与铁粉混合的复合粉末,其余制造方法、步骤、工艺参数与实施例1相同,获得片状功率电感。采用与实施例1相同的性能测试条件,获得的性能参数如表2中所示。
[0074]
对比例4:
[0075]
选用与实施例2中相同的软磁合金粉材,采用与对比例1相同的制造方法、步骤、工艺参数制造片状功率电感。采用与实施例1相同的性能测试条件,获得的性能参数如表2中所示。
[0076]
对比例5:
[0077]
选用与实施例2中相同的软磁合金粉材,采用与对比例2相同的制造方法、步骤、工艺参数制造片状功率电感。采用与实施例1相同的性能测试条件,获得的性能参数如表2中所示。
[0078]
对比例6:
[0079]
选用与实施例2中相同的软磁合金粉材,采用与对比例3相同的制造方法、步骤、工艺参数制造片状功率电感。采用与实施例1相同的性能测试条件,获得的性能参数如表2中所示。
[0080]
由此,上述实施例2以及对比例4-6得到的性能参数如下表2所示:
[0081]
表2实施例2及对比例4-6制得的片状功率电感的性能参数
[0082][0083]
表1、表2中包括实施例1-2及对比例1-6在片状功率电感制造工艺上的差别以及最终生成的片状功率电感的直流电阻r
dc
(mω)、饱和电流i
sat
(a)、电感量ls(μh)。
[0084]
通过比较实施例1和对比例2、3,实施例2和对比例5、6的制造工艺以及性能参数,确定在坯体制备过程中对t形坯体进行烧结致密,能显著提高电感产品的磁导率性能,这是烧结工艺增加了粉末的致密性,因而获得了更高的磁导率,即电感量大幅提升。
[0085]
通过比较实施例1和对比例1、3,实施例2和对比例4、6的制造工艺以及性能参数,确定采用预制杯形坯体与t形坯体组合制备电感能够有效提高电感产品的电感量和饱和电流,一方面预制的坯体较直接填粉具备更高的密度,另一方面能够有效保护内部线圈,减少压制成型过程中线圈的变形量,从而保证电感使用的稳定性,提升产品的综合性能。
[0086]
以上所述仅为本发明较佳的实施方式,并非因此限制本发明的实施方式及保护范围,对于本领域技术人员而言,应当能够意识到凡运用本说明书及图示内容所作出的等同替换和显而易见的变化所得到的方案,均应当包含在本发明的保护范围内。