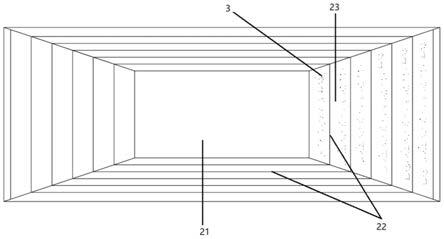
1.本发明属于锂离子电池技术领域,具体涉及一种用于三元电芯的内凹型动力电池铝壳及铝壳电池。
背景技术:2.全世界环境问题突出,各国对新能源汽车发展的支持力度逐渐加大,新能源汽车得到了快速的发展。随着电芯内的正极材料朝着高镍化方向发展,新能源汽车的续航里程已经能够达到700km以上,但高镍化的三元电芯产气量更大,对电芯的外壳要求也随之变高。目前,市场上使用的外壳有方形铝壳、软包铝塑膜、圆柱钢壳等,由于方形铝壳具有重量轻、灵活性高、成组效率高、密封性强、成本低等优点,在市场上的使用量最大,也更适合用于三元电芯。方形铝壳在动力电池中主要起到封装芯包、承载电解液和保护防爆的作用。现有方形电池的铝壳一般呈长方体结构,铝壳体的顶面为开口面,通过顶盖焊接进行密封,密封后组装成模组和电池包开始充放电循环使用。
3.三元电芯的正极材料从使用3系,到5系,再到6系,最后到8系和9系,镍含量不断提高,电芯循环过程中的产气量快速增加,导致电芯的底部和侧面发生鼓胀,底部的鼓胀会使模组的顶部挡板被撑开,模组发生损坏;而侧面鼓胀会使电芯的循环寿命快速衰减。当内压过大时,气体会顶开防爆阀,甚至可能会发生断路、短路、自燃等。
4.现有技术中为了减少铝壳的鼓胀变形,通常会增加方形铝壳的厚度或者硬度。增加厚度后,会导致铝壳的重量增加,电芯的能量密度降低;而增加硬度后,电芯内部相同体积下憋压更加严重,气压承受力下降,防爆阀更容易爆开。
5.因此,仍旧需要一种新型结构的电池铝壳,既不增加铝壳的重量又不能起到一定的缓冲泄压作用,提高电芯的安全性能。
技术实现要素:6.针对现有技术的不足,本发明的目的之一在于提供一种适用于三元电芯的、结构合理、安全性高的底部内凹型方形铝壳,该铝壳可根据三元正极材料的镍含量选择合适的加强筋面积,使得三元电芯内压承受力可控,灵活性高,解决了三元电芯产气导致电芯鼓胀的问题,并可替代传统cid结构,降低成本,提高电芯安全性。
7.本发明的另一目的在于提供采用这种内凹型动力电池铝壳封装的铝壳电池。
8.为实现以上发明目的,本发明采用如下的技术方案:
9.一种用于三元电芯的内凹型动力电池铝壳,包括具有底部和侧壁的铝壳本体,所述铝壳本体的底部经一体冲压成型向本体内凹一定深度;与内凹底面相邻的四个侧面进行“回”字型加强筋成型,在四个侧面上形成具有多个凹槽的加强筋;所述具有凹槽的加强筋面积占比x与待封装动力电池的内压y和三元材料中镍的摩尔含量z之间满足以下关系式:y=230.65x
5-836.46x4+1205.3x
3-863.39x2+307.95x-42.925和y=1.0179z
2-0.6554z+0.6739,其中,x表示具有凹槽的加强筋面积占四个侧面面积的比值,y表示待封装动力电池
的内压,z表示三元材料中镍的摩尔含量。
10.在一个具体的实施方案中,所述铝壳本体的底部向本体内凹的角度α为10
°
~45
°
,优选为20
°
~30
°
。
11.在一个具体的实施方案中,所述四个侧面加强筋成型后形成“锯齿状”凹槽。
12.在一个具体的实施方案中,所述“锯齿状”凹槽为一组或多组,优选在四个侧面上平均分布。
13.在一个具体的实施方案中,整个底部的“回”字形加强筋面积占整个底部面积的0.5~0.9,优选为0.7~0.8。
14.在一个具体的实施方案中,所述铝壳的材质为铝合金,优选为铝与mn、cu、mg、si的合金;优选地,所述铝壳本体的底部利用高温挤压冲击铸造进行加强筋柔性成型。
15.在一个具体的实施方案中,在所述凹槽内可填充阻燃剂,优选地,所述阻燃剂选自2-羧乙基苯基次膦酸、苯基羟甲基次膦酸、双(对羧苯基)苯基氧化膦中的一种或几种。
16.在一个具体的实施方案中,在凹槽添加阻燃剂的添加量为1~10g,优选为4~6g。
17.另一方面,一种铝壳电池,采用前述的用于三元电芯的内凹型动力电池铝壳封装而成。
18.在一个具体的实施方案中,所述铝壳电池包括不同镍含量的三元材料,优选地,三元材料中镍的摩尔百分含量为30%~90%。
19.与现有技术相比,本发明具有以下有益效果:
20.1)本发明的内凹型三元动力电池铝壳,包括铝壳本体,所述铝壳本体进行一体冲压成型时,底部内凹;三元动力电池铝壳的底部经过加强筋的作用后,底部由刚性成型变为柔性成型,内部气压压力都转移到底部,底部更容易发生鼓胀,减轻了电芯内部产气对电芯侧面和顶部的压力,从而减轻了侧面的鼓胀,因此有效解决了电芯鼓胀撑开模组导致模组损坏的问题。
21.2)本发明的电池铝壳中“回”字形加强筋的内压承受能力可控,可根据加强筋的面积占比调节承受内压的大小,当超过底部加强筋的最大承受压力时,加强筋柔性区域就会破裂,从而达到泄压的效果,即可作为电芯安全的第一道保障。该作用类似于电芯顶盖上的cid结构,使用该“回”形加强筋,可取消cid的使用,至少可以降低顶盖成本的1/3。
22.3)本发明还可以充分利用加强筋凹槽的空间,在凹槽中添加阻燃剂,作为电芯安全的第二道保障,提高了电芯的安全性。
23.4)本发明的铝壳电池还可根据三元正极材料镍含量来确定加强筋面积,使得不同三元正极材料镍含量导致的内压与加强筋面积适配,使得加强筋可承受适度的内压,无需过度加工,使得本发明的铝壳电池内压承受力可控,灵活性高。
附图说明
24.图1为现有技术中三元电芯方形铝壳的结构示意图。
25.图2为本发明方形铝壳的结构示意图。
26.图3为本发明方形铝壳底部加强筋成型立体图。
27.图4为本发明方形铝壳底部加强筋的俯视图。
28.图5为本发明方形铝壳底部加强筋面积与内压关系曲线图。
29.图6为本发明铝壳电池适用的不同镍含量三元正极材料与内压关系曲线图。
30.其中,1-方形铝壳、2-铝壳本体、20-侧面、21-底部、22-加强筋、23-凹槽、3-阻燃剂。
具体实施方式
31.为了更好的理解本发明的技术方案,下面的实施例将对本发明所提供的方法予以进一步的说明,但本发明不限于所列出的实施例,还应包括在本发明的权利要求范围内其他任何公知的改变。
32.如图1所示,现有技术的三元电芯方形铝壳1为一长方体结构,包括一底面和四个侧壁,铝壳体的顶面为开口面,通过顶盖焊接进行密封,密封后组装成模组和电池包。
33.如图2所示,本发明的一种用于三元电芯的内凹型动力电池铝壳,包括铝壳本体2,铝壳本体2的底面进行一体冲压成型时,形成内凹的底部21以及与底部21四周邻接的四个倾斜的侧面20,从而内凹的底部21与原来未冲压成型前的底面(近似为水平面)之间形成了一定的内凹角度,使得侧面20与水平面的夹角即内凹角度α为10
°
~45
°
,优选为20
°
~30
°
。同时,内凹角度α,意味着底部的内凹程度,可通过冲压成型工艺来实现内凹角度的调控,内凹角度α过小时,底部鼓胀空间不够,可承受的内压有限;内凹过大时,芯包可用空间不足,导致电芯能量密度降低。
34.其中,铝壳的材质一般为铝合金,尤其是铝锰合金,它含有的主要合金成分有mn、cu、mg、si等,这四种合金在电池铝壳中发挥着不同的作用,如cu和mg是提高强度与硬度,抵制电池的鼓胀,也进一步影响电池性能;mn提高耐腐蚀性;而si能增强含镁铝合金的热处理效果,有利于加强筋结构的成型。常用的铝壳合金材质质量比例例如为1.4-1.6wt%的cu;1.2-1.4wt%的mn;0.7-0.9wt%的mg;0.2-0.6wt%的si;余量为铝和不可避免的杂质。
35.如图3所示,除底部内凹冲压成型处理外,本发明还通过在内凹的底部21进行冲击铸造,作挤压铸造模具冲击四个斜面20,四个斜面20铸造后形成含有多个凹槽23的直线锯齿状的加强筋22。如图4所示,其为铝壳底部加强筋成型后的俯视图,可以看出,通过对与内凹底面相邻的四个侧面进行“回”字型加强筋成型,在四个侧面上形成具有多个凹槽23的“回”字型加强筋22,在凹槽23的空间内可填充阻燃剂3。
36.具体地,在内凹的底部进行高温挤压冲击铸造的工艺为:在900~1300℃的温度下,挤压铸造模具冲击四个斜面,四个斜面铸造后形成含有多个直线锯齿状的斜面,具体如图3。在行业内,把铝壳的高温挤压冲击铸造定义为底部加强筋成型。例如该挤压铸造模具例如参考cn109004169 a的锂电池极耳加强筋成型装置,最后得到该参考专利附图5中v型加强筋。经过成型后,底部由刚性成型变为柔性成型,内部气压压力都转移到底部,底部更容易发生鼓胀,减轻了电芯内部产气对电芯侧面和顶部的压力,从而减轻了侧面的鼓胀。
37.本发明的底部加强筋为“回”字形,加强筋的面积占整个底部面积的0.5~0.9。其中,所述整个底部面积即为图2中底部21的面积和四个侧面20的面积之和。而底部四个斜面铸造面积的大小即加强筋的面积大小,可以通过更换不同大小的模头来实现,模头面积决定了加强筋的面积,这样即可根据需求铸造不同面积的加强筋。加强筋区域类似于“锯齿”状,由于锯齿状的根部较薄,承受内压能力有限,因此将根部定义为柔性区域,即加强筋凹槽23。通过控制加强筋的面积,可以控制内部气压的承受能力,当超过底部的最大承受压力
时,加强筋中的柔性区域由于承受不住内压而破裂,而达到泄压的效果,即可作为电芯安全的第一道保障。该作用类似于电芯顶盖上的cid结构,使用该“回”形加强筋,可取消cid的使用,至少降低了顶盖成本的1/3。
38.具体地,在加强筋22成型时,会产生多条加强筋凹槽23,在凹槽内添加阻燃剂3,可充分利用了底部的空间,作为电芯安全的第二道保障,提高了电芯的安全性能。其中,阻燃剂可采用本领域常见的阻燃剂,没有任何的限制,例如可以选取2-羧乙基苯基次膦酸、苯基羟甲基次膦酸、双(对羧苯基)苯基氧化膦等阻燃剂。其中,阻燃剂3的添加量优选为1~10g,添加过少,阻燃效果不明显;添加过多,一方面影响电芯性能,另一方面还降低了电芯的能量密度。
39.本发明的动力电池铝壳中,加强筋面积决定了铝壳内部气压承受力的上下限,而承受力取决于内部产气量的大小,产气量的大小取决于不同三元材料的镍含量。底部加强筋面积和内压关系曲线如图5所示,加强筋面积占比x与内压y的关系式为y=230.65x
5-836.46x4+1205.3x
3-863.39x2+307.95x-42.925。随着加强筋区域面积占比从40%到90%,电芯内部承受压力也是逐渐增加。但是随着面积占比过大时,内压承受能力提升率降低。
40.同时,三元材料镍含量与内压关系曲线如图6所示,镍含量z与内压y的关系式为y=1.0179z
2-0.6554z+0.6739,随着镍含量逐渐增加,材料的产气量也随之增加,则会导致内压气压也逐渐变大。因此,根据本发明的电池铝壳,可根据拟封装的三元正极材料镍含量,来选择加强筋面积,从而使得三元材料包内压承受力可控、适配,灵活性高。本发明的用于三元电芯的内凹型动力电池铝壳适用于三元正极材料镍含量在30%~90%。
41.根据本发明的构思,可以根据拟封装的动力电池所用三元正极材料中的镍含量计算出可能产能的内压大小,从而得到合适的加强筋面积,选择合适的模具加工出对应的加强筋面积的铝壳底部区域,实现内压和加强筋面积的适配,更加科学地指导电池的封装,使得电池内压承受力完全可控,有利于提高电芯的安全性。
42.进一步地,在本发明地电池铝壳加强筋成型时会产生多条锯齿状的柔性区域,在该区域内可添加一定量的阻燃剂,优选添加1~10g,有助于提高电芯的安全性。
43.下面通过更具体的实施例进一步解释说明本发明,但不构成任何的限制。
44.以下实施例和对比例采用的主要原料如下:
45.三元正极材料:型号为ncm523,烟台卓能锂电池有限公司;
46.铝壳:型号为26mm(厚度)*148mm(长度)*95(高度)mm,芜湖天弋能源有限公司;
47.阻燃剂:苯基羟甲基次膦酸,amadis chemical company。
48.相关性能测试采用如下的方法:
49.阻燃性能:在防爆房间里,对电芯一直进行充电,充电电流为1c,直到电芯发生起火燃烧(根据国标gb 38031-2020中过充测试的测试方法,截止条件更改为直到电芯起火)。记录电芯从开始充电到起火燃烧的时间,该时间越长,即表示阻燃性能越好。
50.电池能量密度:根据gb/t 31486-2015中容量的测试方法,测得容量后乘以3.6v,再除以电芯重量,即可得到电池能量密度。
51.实施例1
52.首先将铝壳进行内凹成型,内凹角度为10
°
;再进行加强筋成型,加强筋区域面积占底部面积的0.5,电池正极材料镍含量为50%。将添加不同量阻燃剂的十个满电电芯进行
过充电实验,并测试能量密度。
53.具体步骤为:
54.1)确定好铝壳底部的内凹角度为10
°
,进行模具冲压,得到内凹角度为10
°
成型的铝壳;
55.2)确定加强筋区域面积占比为50%,对内凹成型的铝壳进行模具冲压加强筋成型,四个斜面呈现“锯齿”状的均匀形状,使加强筋区域面积占比50%;
56.3)参考cn 110783528 a中锂电池的制备方法进行电芯组装,选择ncm523(镍含量50%)作为正极材料,通过搅拌、涂布、辊压、分条、模切、卷绕、热压、超声焊接、极耳焊接、顶盖焊接、烘烤、注液、化成、分容等步骤,组装成一个完整的电芯。
57.其中,在本实施例中,将卷芯放入铝壳进行顶盖焊接前,需要在铝壳底部添加不同量的阻燃剂。电芯组装完成后,对电芯进行容量测试,继而得到电芯能量密度。
58.能量密度测试完成后,分别对每个电芯进行过充测试,直到电芯发生起火燃烧,记录记录电芯从开始充电到起火燃烧的时间。
59.本实施例1添加阻燃剂的量分别为1、3、5、7、9g。
60.对比例1
61.对比例1仍然添加组成完全相同的阻燃剂,添加量分别更改为0、0.1、0.5、15、20g,其它与实施例1完全相同。
62.表1实施例及比较例的能量密度、开始燃烧时间对比
[0063][0064]
从表1数据中可以看出,加入阻燃剂之后,电池过充导致电池开始燃烧的时间明显比不加阻燃剂的时间要长。当加入阻燃剂的量小于1g时,延后的时间差别不大;当阻燃剂的量大于1g且逐渐增加时,时间延后的越发明显,从1g到9g时,时间从11.5分钟已经延后到18.3分钟。值得注意的是,当阻燃剂的量为15和20g时,虽然开始燃烧的时间还在继续延长,但是差别已不大,主要是由于随着时间的延长,过充已到电池的极限值,此时电池电压非常高,单纯靠添加阻燃剂来阻燃燃烧效果已经不明显,而且会导致电池能量密度的明显降低,因此实施例的添加范围效果较好。
[0065]
实施例2
[0066]
本实施例和对比例中使用冲压模具对铝壳底部进行高温冲击铸造,形成不同面积的加强筋区域,再用该铝壳组装成不带cid的电池,测试不同镍含量的电池在2c充放电循环后,底部加强筋锯齿状的柔性区域破裂泄压的时间。
[0067]
具体步骤为:
[0068]
1)确定铝壳底部的内凹角度为45
°
,进行模具冲压,得到内凹角度为45
°
成型的铝壳;
[0069]
2)确定加强筋区域面积占比为50%,对内凹成型的铝壳进行模具冲压加强筋成型,四个斜面呈现“锯齿”状的均匀形状,使加强筋区域面积占比50%。
[0070]
3)更换模头,增加底部锯齿状区域面积,分别进行冲压铸造加强筋区域面积占比
为60%,70%,80%,90%的铝壳。
[0071]
4)参考cn 110783528 a中锂电池的制备方法进行电芯组装,选择不同镍含量的三元材料作为正极材料,通过搅拌、涂布、辊压、分条、模切、卷绕、热压、超声焊接、极耳焊接、顶盖焊接、烘烤、注液、化成、分容等步骤,组装成一个完整的电芯。
[0072]
其中,在本实施例中,将卷芯放入铝壳进行顶盖焊接前,需要选择表2中加强筋区域面积占比不同的铝壳来进行焊接。电芯组装完成后,对电芯进行2c充放电循环,记录电芯从开始循环到底部加强筋破裂的时间。
[0073]
其中,三元材料镍含量分别为30%,50%,60%,70%,80%;加强筋面积占底部的比例分别为50%,60%,70%,80%,90%。
[0074]
对比例2
[0075]
跟实施例2相比,加强筋面积占底部的比例分别更改为0,10%,20%,30%,40%,其它与实施例2完全相同。
[0076]
表2实施例及比较例在不同镍含量的电池充放电循环中加强筋破裂时间对比
[0077][0078]
从表2中可以看出,一方面加强筋面积的大小对电池循环有着至关重要的作用,当没有加强筋时,电池循环的时间只有2.5~4.3天,而当增加了10%加强筋区域后,循环时间明显增加;加强筋区域从10%增加到40%。对比例中的循环时间增加的较慢,而当增加到实施例中的范围后,循环时间增加幅度变大,特别是到70%时,增速最快。另外一方面,从表中可以看出随着镍含量的增加,产气速率变快,内部气压增加较大,加强筋破裂时间变短,意味着循环时间变少。因此,加强筋一定程度上起到了cid的作用,对电池的循环性能和安全性能至关重要。
[0079]
尽管本发明的内容已经通过上述优选实施例作了详细介绍,但应当认识到上述的描述不应被认为是对本发明的限制。本领域技术人员可以理解,在本说明书的教导之下,可对本发明做出一些修改或调整。这些修改或调整也应当在本发明权利要求所限定的范围之内。