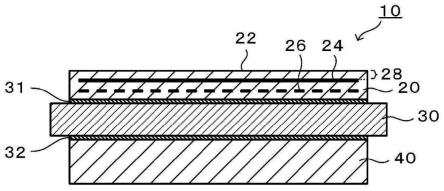
1.本发明涉及半导体制造装置用构件及其制法。
背景技术:2.以往,已知一种半导体制造装置用构件,其具备:具有晶片载置面的陶瓷制的静电卡盘、以及在中央比周缘凹陷的形状的凹面上金属接合有静电卡盘的支撑基板(例如参照专利文献1)。在该半导体制造装置用构件中,静电卡盘在变形为与支撑基板的凹面相同的形状的状态下接合。另外,静电卡盘的陶瓷与构成支撑基板的复合材料的热膨胀系数差的绝对值为0.2
×
10-6
/k以下。根据这样的半导体制造装置用构件,认为由于静电卡盘的晶片载置面是凹面,因此能够将晶片稳定地保持在晶片载置面上。
3.现有技术文献
4.专利文献
5.专利文献1:日本专利第6741548号公报
技术实现要素:6.发明所要解决的课题
7.但是,在专利文献1中,难以高精度地对支撑基板的凹面进行精加工。因此,难以得到尺寸精度高的凹形状的晶片载置面。
8.本发明是为了解决这样的课题而完成的,其主要目的在于提供一种具备尺寸精度高的凹形状或凸形状的晶片载置面的半导体制造装置用构件。
9.用于解决课题的方案
10.本发明的半导体制造装置用构件具备:
11.陶瓷制的上部板,其具有凹形状或凸形状的晶片载置面,并内置有静电电极;
12.中间板,其经由第一金属接合层而接合于所述上部板的与所述晶片载置面相反侧的面上;以及
13.下部板,其经由第二金属接合层而接合于所述中间板的与接合所述上部板的面相反侧的面上,
14.所述中间板的热膨胀系数大于所述上部板和所述下部板的热膨胀系数。
15.在该半导体制造装置用构件中,中间板的热膨胀系数大于上部板和下部板的热膨胀系数。因此,能够利用中间板与上部板的热膨胀差和中间板与下部板的热膨胀差,使晶片载置面成为尺寸精度高的凹形状或凸形状。
16.在本发明的半导体制造装置用构件中,所述中间板可以是金属与陶瓷的复合材料制或金属制,所述下部板可以是与所述上部板相同的陶瓷制,并具有与所述上部板不同的厚度。这样一来,容易使中间板的热膨胀系数大于上部板和下部板的热膨胀系数。另外,虽然上部板和下部板是相同的陶瓷制,但由于厚度不同,因此容易使晶片载置面成为凹形状或凸形状。
17.在该情况下,所述晶片载置面可以是凹形状,所述上部板可以比所述下部板薄。或者,所述晶片载置面也可以是凸形状,所述上部板可以比所述下部板厚。
18.另外,也可以是,在所述上部板和所述下部板的至少一方内置有电阻发热体。这样一来,能够将半导体制造装置用构件用作静电卡盘加热器。在所述下部板也可以内置有电阻发热体,布线有所述电阻发热体的区域的直径可以为所述上部板的直径以上。这样一来,由于电阻发热体能够对上部板的晶片载置面整个面进行加热,因此晶片的均热性提高。
19.本发明的半导体制造装置用构件的制法包括:
20.(a)准备下部板、具有晶片载置面并内置有静电电极的陶瓷制的上部板、以及热膨胀系数大于所述上部板和所述下部板的中间板的工序;以及
21.(b)在所述中间板的上表面和所述上部板的与所述晶片载置面相反侧的面之间配置第一金属接合材料,并且在所述中间板的下表面和所述下部板的上表面之间配置第二金属接合材料,在该状态下进行加压加热后恢复至室温,由此得到接合体的工序。
22.根据该半导体制造装置用构件的制法,能够利用工序(b)中产生的中间板与上部板的热膨胀差、中间板与下部板的热膨胀差,使晶片载置面高精度地成为凹形状或凸形状。
23.在本发明的半导体制造装置用构件的制法中,也可以是在所述工序(a)中,在准备所述下部板时,事先以使所述下部板的厚度成为预先确定的目标厚度的方式进行加工。通过这样在得到接合体之前使下部板的厚度成为目标厚度,从而能够使晶片载置面高精度地成为凹形状或凸形状。
24.在本发明的半导体制造装置用构件的制法中,也可以是在所述工序(b)中,在得到所述接合体后,加工所述下部板以使所述下部板的厚度成为与所述上部板的厚度不同的预先确定的目标厚度。通过这样在得到接合体之后使下部板的厚度成为目标厚度,从而能够使晶片载置面高精度地成为凹形状或凸形状。
25.在本发明的半导体制造装置用构件的制法中,也可以是在所述工序(b)中,在得到所述接合体后,调整所述下部板的厚度以使所述上部板的形状成为预先确定的凹形状或凸形状。这样一来,能够使晶片载置面更高精度地成为凹形状或凸形状。
附图说明
26.图1是半导体制造装置用构件10的剖视图。
27.图2是晶片载置面22的俯视图。
28.图3是晶片载置面22的放大剖视图。
29.图4是表示将半导体制造装置用构件10安装于冷却装置50的情形的剖视图。
30.图5是半导体制造装置用构件10的制造工序图。
31.图6是半导体制造装置用构件110的剖视图。
32.图7是晶片载置面122的放大剖视图。
33.图8是半导体制造装置用构件210的剖视图。
具体实施方式
34.以下,参照附图对本发明的优选实施方式进行说明。图1是半导体制造装置用构件10的剖视图(用穿过构件10的中心的垂直面切断时的剖视图),图2是晶片载置面22的俯视
图,图3是晶片载置面22的放大剖视图。
35.半导体制造装置用构件10具备上部板20、中间板30、下部板40、以及第一和第二金属接合层31、32。
36.上部板20是直径与实施等离子体处理的硅制的晶片w相同的圆盘状且陶瓷(例如氧化铝、氮化铝)制的板,内置有静电电极24和电阻发热体26。因此,上部板20作为静电卡盘发挥功能,并且还作为加热器发挥功能。上部板20的直径没有特别限定,例如可以设为250~350mm。上部板20的上表面是晶片载置面22。
37.如图3所示,晶片载置面22呈凹形状(中央部比外周部凹陷的形状)。载置于该载置面22的晶片w使用凹形状的晶片。即,晶片载置面22仿照凹形状的晶片w而形成。晶片载置面22中的最凹陷的部位的深度(晶片载置面22的最大高度与最小高度之差,也称为平面度)优选为1~500μm,更优选为30~300μm。如图2和图3所示,在晶片载置面22中,沿着外缘形成有密封带22a,在整个面形成有多个圆形突起22b。密封带22a和圆形突起22b为相同的高度,其高度例如为数μm~数10μm。
38.静电电极24是能够经由未图示的供电端子通过外部电源施加直流电压的圆形的面电极。上部板20中的晶片载置面22与静电电极24之间的部分作为电介质层28发挥功能。关于电介质层28的厚度,考虑吸附晶片w的力而调整为预定的厚度(例如50~500μm)。当对该静电电极24施加直流电压时,载置于晶片载置面22的晶片w被吸附固定于晶片载置面22,当解除直流电压的施加时,晶片在晶片载置面22上的吸附固定被解除。如图3所示,吸附于晶片载置面22的晶片w的背面与密封带22a的上表面和圆形突起22b的上表面接触。另外,在晶片w的背面与晶片载置面22中未设置密封带22a、圆形突起22b的部分之间产生空间s1。通过沿上下方向贯通半导体制造装置用构件10的未图示的气体供给通路向该空间s1中供给导热气体(例如he气体)。利用该导热气体高效地进行上部板20与晶片w的热交换。电阻发热体26以遍及上部板20的整个面进行布线的方式以一笔画的要领进行图案形成,若施加电压则发热而对晶片w进行加热。布线有电阻发热体26的区域在俯视时为圆形。静电电极24和电阻发热体26均与晶片载置面22平行地设置。需要说明的是,“平行”除了完全平行的情况以外,即使不完全平行,但只要在公差的范围内,则也视为平行。
39.中间板30是圆盘状的板,其直径比上部板20和下部板40的直径大。中间板30经由第一金属接合层31而接合于上部板20的与晶片载置面22相反侧的面上。中间板30的热膨胀系数大于上部板20和下部板40的热膨胀系数。在此,热膨胀系数也可以是例如40~570℃的线热膨胀系数。作为中间板30的材料,可举出复合材料、金属等。作为复合材料,可举出陶瓷-金属复合材料(也称为金属基复合物(mmc))。作为mmc,可举出含有si、sic和ti的材料(也称为sisicti)、使al和/或si含浸于sic多孔质体而得到的材料等。作为金属,可举出ti、mo等。关于中间板30的材料,选择具有比上部板20和下部板40的热膨胀系数大的热膨胀系数的材料。
40.下部板40经由第二金属接合层32而接合于中间板30的与接合上部板20的面相反侧的面上。下部板40既可以为金属制,也可以为mmc制,也可以为陶瓷制,优选为陶瓷制。在本实施方式中,下部板40是与上部板20的陶瓷相同的材料,上部板20比下部板40薄。由此,上部板20的晶片载置面22成为凹形状。需要说明的是,中间板30优选比上部板20、下部板40厚。例如,也可以将上部板20的厚度设为1mm以上3mm以下,将下部板40的厚度设为6mm以上
10mm以下,将中间板30的厚度设为大于10mm且20mm以下。
41.在上部板20和下部板40的材料为氧化铝的情况下,中间板30的材料优选为sisicti或金属ti。在上部板20和下部板40的材料为氮化铝的情况下,中间板30的材料优选为使si含浸于sic多孔质体而得到的材料或金属mo。但是,只要是满足中间板30的热膨胀系数比上部板20和下部板40的热膨胀系数大这样的关系的材料的组合,则并不特别限定于该组合。
42.第一和第二金属接合层31、32例如由al-si-mg系或al-mg系材料等含al材料构成。第一和第二金属接合层31、32的厚度没有特别限定,优选为1~300μm,更优选为50~150μm。另外,优选第一金属接合层31的外周不从上部板20的外周伸出,优选第二金属接合层32的外周不从下部板40的外周伸出。第一和第二金属接合层31、32例如通过tcb(thermal compression bonding,热压接合)形成。tcb是指在接合对象的2个构件之间夹入金属接合材料,在加热至金属接合材料的固相线温度以下的温度的状态下将2个构件加压接合的公知的方法。
43.接着,对半导体制造装置用构件10的使用例进行说明。图4是表示将半导体制造装置用构件10安装于冷却装置50的情形的剖视图。首先,将半导体制造装置用构件10安装在设置于未图示的真空腔内的冷却装置50上。冷却装置50是铝等金属制的圆盘构件,在内部具有能够使制冷剂循环的制冷剂通路52。在冷却装置50的上表面的中央设置有圆形槽54。在圆形槽54中插入下部板40。冷却装置50具有包围圆形槽54的周围的环状面56。半导体制造装置用构件10通过在中间板30背面的外周部与环状面56之间配置环状的密封构件57并将下部板40插入圆形槽54的状态下,利用紧固环60而固定于冷却装置50。密封构件57的外径比圆形槽54的直径大且比中间板30的直径小。作为密封构件57,例如可举出金属垫片等。紧固环60配置于冷却装置50的环状面56上。在紧固环60的内周面设有台阶62,该台阶62能够从上方按压中间板30的外周部的上表面。另外,紧固环60具有能够插通螺钉71的纵孔64、能够与螺钉72螺纹结合的螺纹孔66。螺钉71从上方插入至纵孔64而与设置于冷却装置50的环状面56的螺纹孔58螺纹结合。螺钉72从下方插入至沿上下方向贯通冷却装置50的螺钉插入孔59,并与设置在紧固环60的背面的螺纹孔66螺纹结合。这样的螺钉71、72在紧固环60的周向上等间隔地设置有多个(例如8个)。由此,由圆形槽54、下部板40和密封构件57包围的空间s2被密闭。在密闭的空间s2中填充导热片或导热气体。这样,半导体制造装置用构件10的中间板30中的从上部板20、下部板40向外侧伸出的部分被用作用于安装于冷却装置50的凸缘。
44.在将半导体制造装置用构件10安装于冷却装置50之后,将凹形状的晶片w载置于晶片载置面22。然后,利用真空泵对真空腔内进行减压而调整为预定的真空度,对静电电极24施加直流电压而将晶片w吸附固定于晶片载置面22。由于晶片载置面22为凹形状,因此凹形状的晶片w无间隙地与晶片载置面22的密封带22a、圆形突起22b密合,空间s1被密闭。向该空间s1供给导热气体。由于导热气体是被封入的,因此能够在上部板20与晶片w之间高效地进行热传导。接着,使真空腔内成为预定压力(例如数10~数100pa)的反应气体气氛,在该状态下,产生等离子体。然后,利用所产生的等离子体进行晶片w的表面蚀刻。未图示的控制器控制向电阻发热体26供给的电力,以使晶片w的温度成为预先确定的目标温度。
45.接着,对半导体制造装置用构件10的制造例进行说明。图5是半导体制造装置用构
件10的制造工序图。以下,以上部板20和下部板40的材料为氧化铝、中间板30的材料为sisicti的情况为例进行说明。
46.首先,准备上部板20、中间板30和下部板40(参照图5(a))。将该工序称为工序(a)。
47.上部板20能够以如下方式制造。在此,对氧化铝制的上部板20的制造例进行说明。首先,准备圆盘状的氧化铝制的第一和第二生片,在第一生片的表面形成静电电极24,在第二生片的表面形成电阻发热体26。作为静电电极24和电阻发热体26的形成方法,例如可以使用丝网印刷、pvd、cvd、镀覆等。接着,在第一生片的形成有静电电极24的面上层叠其他的氧化铝制的生片(第三生片),在其上以使电阻发热体26与第三生片接触的方式层叠第二生片,制成层叠体。或者,也可以在模具中以静电电极24朝上的方式配置第一生片,在形成有该静电电极24的面上,将造粒后的氧化铝颗粒以成为预定的厚度的方式铺满,在其上以使电阻发热体26与氧化铝颗粒的层接触的方式层叠第二生片,一并进行压制而制成层叠体。接着,通过热压法将层叠体进行烧成,从而得到埋设有静电电极24和电阻发热体26的氧化铝烧结体。通过对得到的氧化铝烧结体的两面实施磨削加工或喷砂加工等来调整形状、厚度,得到平板状的上部板20(参照图5(a))。在该时刻,电介质层28的厚度被加工成预先确定的预定厚度,但在晶片载置面22上不形成密封带22a、圆形突起22b。需要说明的是,也可以使用通过浇铸法(例如模铸法)制作的氧化铝成形体来代替氧化铝制的生片。或者,也可以使用氧化铝烧结体来代替第一和第二生片,或使用氧化铝烧结体来代替第三生片。关于上部板20的具体的制造条件,例如参考日本特开2006-196864号公报中记载的条件来设定即可。
48.中间板30能够以如下方式制造。在此,对sisicti制的中间板30的制造例进行说明。首先,制作sisicti制的圆盘构件。例如,制作粉体混合物,该粉体混合物包含以含有39~51质量%的平均粒径为10μm以上且25μm以下的碳化硅原料粒子、且含有包含ti和si的方式选择的1种以上的原料,对于来源于除碳化硅以外的原料的si和ti而言,si/(si+ti)的质量比为0.26~0.54。作为原料,例如可以使用碳化硅、金属si和金属ti。此时,优选以碳化硅为39~51质量%、金属si为16~24质量%、金属ti为26~43质量%的方式进行混合。接着,将得到的粉体混合物通过单轴加压成形制作圆盘状的成形体,使该成形体在非活性气氛下通过热压在1370~1460℃烧结,由此得到sisicti制的圆盘构件。需要说明的是,热压时的冲压压力设定为例如50~300kgf/cm2。接着,通过磨削加工等对得到的圆盘构件进行形状、厚度的调整,得到中间板30(参照图5(a))。上部板20为氧化铝制的情况下,氧化铝的40~570℃的线热膨胀系数为7.7
×
10-6
/k。因此,作为中间板30,制作40~570℃的线热膨胀系数超过7.7
×
10-6
/k的板。关于中间板30的具体制造条件,例如参考日本专利第5666748号公报中记载的条件来设定即可。
49.下部板40能够以如下方式制造。在此,对氧化铝制的下部板40的制造例进行说明。首先,制作圆盘状的氧化铝成形体,将该氧化铝成形体烧成而制成氧化铝烧结体,通过对得到的氧化铝烧结体的两面实施磨削加工或喷砂加工等来调整形状、厚度,得到平板状的下部板40(参照图5(a))。在本实施方式中,事先将下部板40的厚度调整为预先确定的目标厚度(超过上部板20的厚度的厚度)。
50.接着,在下部板40的上表面载置与下部板40同径的平板状的第二金属接合材料302,在其上载置中间板30,进而在中间板30的上表面载置与上部板20同径的平板状的第一
金属接合材料301,将上部板20以与晶片载置面22相反侧的面和第一金属接合材料301接触的方式载置。由此,能够得到中间板30隔着各金属接合材料301、302而被夹在上部板20与下部板40之间的状态的夹层层叠体。接着,在第一和第二金属接合材料301、302的固相线温度以下(例如,从固相线温度减去20℃所得的温度以上且固相线温度以下)的温度对夹层层叠体进行加压,将上部板20、中间板30和下部板40进行tcb接合(参照图5(b)),然后恢复到室温。由此,得到第一金属接合材料301成为了第一金属接合层31、第二金属接合材料302成为了第二金属接合层32的接合体80(参照图5(c))。将该工序称为工序(b)。作为第一和第二金属接合材料301、302,可以使用al-mg系接合材料、al-si-mg系接合材料。例如,在使用al-si-mg系接合材料(含有88.5重量%的al、10重量%的si、1.5重量%的mg,固相线温度为约560℃)进行tcb接合的情况下,在真空气氛下,加热到540~560℃(例如550℃)的状态下,以0.5~2.0kg/mm2(例如1.5kg/mm2)的压力对上部板20进行数小时加压。第一和第二金属接合材料301、302优选使用厚度为100μm左右的材料。由于中间板30的热膨胀系数比上部板20和下部板40的热膨胀系数大,上部板20比下部板40薄,从而接合体80的上部板20的晶片载置面22成为凹形状。
51.接着,在接合体80的上部板20的晶片载置面22上粘贴图案掩模,所述图案掩模在形成密封带22a及圆形突起22b的部分开孔,喷射喷砂介质来进行喷砂加工(参照图5(c))。通过喷砂加工在晶片载置面22形成密封带22a、圆形突起22b。然后,卸下掩模,得到半导体制造装置用构件10(参照图5(d))。根据需要,可以将下部板40的底面加工成平坦,也可以通过磨削加工调整下部板40的厚度,以使晶片载置面22的凹形状成为目标的凹形状。
52.根据以上详述的半导体制造装置用构件10,由于中间板30的热膨胀系数比上部板20和下部板40的热膨胀系数大,因此能够利用中间板30与上部板20的热膨胀差和中间板30与下部板40的热膨胀差,使晶片载置面22成为尺寸精度高的凹形状。
53.另外,中间板30为金属与陶瓷的复合材料制或金属制,上部板20和下部板40为相同的陶瓷制,因此,容易使中间板30的热膨胀系数大于上部板20和下部板40的热膨胀系数。另外,由于上部板20比下部板40薄,因此容易使晶片载置面22成为凹形状。
54.进而,上部板20中内置有静电电极24和电阻发热体26。因此,能够将半导体制造装置用构件10用作静电卡盘加热器。另外,也能够通过内置于上部板20的静电电极24和电阻发热体26来调整晶片载置面22的凹形状。
55.此外,半导体制造装置用构件10的制法包括以下工序:(a)准备下部板40、具有晶片载置面22且内置有静电电极24的陶瓷制的上部板20、以及热膨胀系数比上部板20和下部板40大的中间板30的工序;(b)在中间板30的上表面和上部板20的与晶片载置面22相反侧的面之间配置第一金属接合材料301,并且在中间板30的下表面与下部板40的上表面之间配置第二金属接合材料302,在该状态下进行加压加热后恢复至室温,由此得到接合体的工序。这样一来,能够利用在工序(b)中产生的中间板30与上部板20的热膨胀差、中间板30与下部板40的热膨胀差,使晶片载置面22高精度地成为凹形状。
56.而且,在工序(a)中,在准备下部板40时,以使下部板40的厚度成为目标厚度的方式进行加工。通过这样在得到接合体80之前将下部板40的厚度设为目标厚度,从而能够使晶片载置面22高精度地成为凹形状。
57.需要说明的是,不言而喻,本发明不受上述实施方式的任何限定,只要属于本发明
的技术范围,则当然能够以各种方式实施。
58.例如,在上述的实施方式中,在工序(a)中将下部板40的厚度调整为目标厚度,但也可以在工序(a)中将下部板40的厚度形成得比目标厚度厚,在工序(b)中得到接合体80之后,以使下部板40的厚度成为目标厚度的方式加工下部板40。这样操作,也能够高精度地使晶片载置面22成为凹形状。或者,也可以在工序(b)中得到接合体80之后,调整下部板40的厚度,以使晶片载置面22成为预先确定的凹形状。这样一来,能够使晶片载置面22更高精度地成为凹形状。
59.在上述的实施方式中,在工序(a)中准备的上部板20上没有形成密封带22a和圆形突起22b,但也可以在该阶段通过喷砂加工在上部板20形成密封带22a和圆形突起22b。
60.在上述的实施方式中,使晶片载置面22成为凹形状,上部板20和下部板40为相同的陶瓷制,且上部板20比下部板40薄,但并不特别限定于此。例如,也可以如图6以及图7所示的半导体制造装置用构件110那样,使上部板120的晶片载置面122成为凸形状(中央部比外周部突出的形状),上部板120与下部板140为相同的陶瓷制,上部板120比下部板140厚。需要说明的是,在图6以及图7中,对与上述的实施方式相同的构成要素标注相同的附图标记。在该情况下,载置于晶片载置面122的晶片w使用凸形状的晶片。即,晶片载置面122仿照凸形状的晶片w而形成。因此,凸形状的晶片w无间隙地与晶片载置面122的密封带22a、圆形突起22b密合,空间s1被密闭。在半导体制造装置用构件110中,例如也可以将上部板120的厚度设为3mm以上5mm以下,将下部板140的厚度设为1mm以上3mm以下,将中间板30的厚度设为大于10mm且20mm以下。
61.在此,晶片载置面122为凸形状的半导体制造装置用构件110能够根据上述实施方式的制法来制造。具体而言,在工序(a)中,在准备下部板140时,以下部板40的厚度成为预先确定的目标厚度(比上部板120薄的值)的方式进行加工。通过这样在得到接合体之前使下部板140的厚度成为目标厚度,能够使晶片载置面122高精度地成为凸形状。或者,在工序(b)中,也可以在得到接合体后,以下部板140的厚度成为目标厚度(比上部板120薄的值)的方式加工下部板140。这样操作,也能够使晶片载置面122高精度地成为凸形状。进而,在工序(b)中,也可以在得到接合体后,调整下部板140的厚度,以使晶片载置面122成为预先确定的凸形状。这样一来,能够使晶片载置面122更高精度地成为凸形状。需要说明的是,下部板140的下表面也可以以最终加工为平坦。
62.在上述的实施方式中,在上部板20中埋设有电阻发热体26,但也可以如图8所示的半导体制造装置用构件210那样,不在上部板220中埋设电阻发热体26,而在下部板240中埋设电阻发热体226。在该情况下,埋设有电阻发热体226的区域(俯视时圆形区域)的直径d2优选为上部板220的直径d1以上。这样一来,在对具有与上部板20的直径d1相同直径的晶片w进行加热时能够均匀地进行加热。
63.在上述的实施方式中,使上部板20的直径与晶片w的直径相同,但也可以使上部板20的直径大于晶片w的直径,也可以使上部板20的直径小于晶片w的直径。
64.[实施例]
[0065]
以下,对本发明的优选实施例进行说明。本发明不受以下实施例的任何限定。实验例1、3~6、8~11、13~15相当于本发明的实施例,实验例2、7、12相当于比较例。将它们的结果示于表1。
[0066]
[表1]
[0067][0068]
[实验例1]
[0069]
准备al2o3制的上部板20和下部板40、以及sisicti制的中间板30,通过上述的制造方法来制造上述实施方式的半导体制造装置用构件10。al2o3的40~570℃的线热膨胀系数为7.7
×
10-6
/k、sisicti的40~570℃的线热膨胀系数为7.8
×
10-6
/k。作为第一和第二金属接合材料301、302,使用al-si-mg系接合材料,通过tcb将上部板20、中间板30和下部板40接合。在接合前将上部板20的厚度调整为2mm。需要说明的是,电介质层28的厚度和从晶片载
置面22到电阻发热体26的距离在所有的实验例中设为相同的值。中间板30的厚度和下部板40的厚度在接合前分别调整为15mm、8mm。其结果,得到的半导体制造装置用构件10具有凹形状的晶片载置面22,晶片载置面22的平面度(晶片载置面22的最大高度与最小高度之差)为0.06mm。
[0070]
[实验例2]
[0071]
在实验例1中,将接合前的上部板和下部板的厚度均变更为4mm,除此以外,与实验例1同样地操作,制造半导体制造装置用构件。其结果,得到的半导体制造装置用构件具有平坦的晶片载置面,其平面度为0.00mm。
[0072]
[实验例3]
[0073]
在实验例1中,将接合前的上部板的厚度变更为4mm,将下部板的厚度变更为2mm,除此以外,与实验例1同样地操作,制造半导体制造装置用构件。其结果,得到的半导体制造装置用构件具有凸形状的晶片载置面,其平面度为0.03mm。
[0074]
[实验例4]
[0075]
在实验例1中,将接合前的下部板的厚度变更为10mm,在接合后将下部板的厚度磨削为8mm,除此以外,与实验例1同样地操作,制造半导体制造装置用构件。其结果,得到的半导体制造装置用构件具有凹形状的晶片载置面,其平面度为0.06mm。
[0076]
[实验例5]
[0077]
在实验例3中,将接合前的下部板的厚度变更为4mm,在接合后磨削下部板的底面以使下部板的厚度为2mm,除此以外,与实验例3同样地操作,制造半导体制造装置用构件。其结果,得到的半导体制造装置用构件具有凸形状的晶片载置面,其平面度为0.03mm。
[0078]
[实验例6]
[0079]
在实验例1中,将中间板变更为金属ti制,除此以外,与实验例1同样地操作,制造半导体制造装置用构件。金属ti的40~570℃的线热膨胀系数为11.1
×
10-6
/k。所得到的半导体制造装置用构件具有凹形状的晶片载置面,其平面度为0.30mm。
[0080]
[实验例7]
[0081]
在实验例2中,将中间板变更为金属ti制,除此以外,与实验例2同样地操作,制造半导体制造装置用构件。其结果,得到的半导体制造装置用构件具有平坦的晶片载置面,其平面度为0.00mm。
[0082]
[实验例8]
[0083]
在实验例3中,将中间板变更为金属ti制,除此以外,与实验例3同样地操作,制造半导体制造装置用构件。其结果,得到的半导体制造装置用构件具有凸形状的晶片载置面,其平面度为0.15mm。
[0084]
[实验例9]
[0085]
在实验例4中,将中间板变更为金属ti制,除此以外,与实验例4同样地操作,制造半导体制造装置用构件。其结果,得到的半导体制造装置用构件具有凹形状的晶片载置面,其平面度为0.30mm。
[0086]
[实验例10]
[0087]
在实验例5中,将中间板变更为金属ti制,除此以外,与实验例5同样地操作,制造半导体制造装置用构件。其结果,得到的半导体制造装置用构件具有凸形状的晶片载置面,
其平面度为0.15mm。
[0088]
[实验例11]
[0089]
在实验例1中,将上部板和下部板设为aln制,将中间板变更为金属mo制,除此以外,与实验例1同样地操作,制造半导体制造装置用构件。aln的40~570℃的线热膨胀系数为5.9
×
10-6
/k、金属mo的40~570℃的线热膨胀系数为6.1
×
10-6
/k。所得到的半导体制造装置用构件具有凹形状的晶片载置面,其平面度为0.18mm。
[0090]
[实验例12]
[0091]
在实验例2中,将上部板和下部板设为aln制,将中间板变更为金属mo制,除此以外,与实验例2同样地操作,制造半导体制造装置用构件。其结果,得到的半导体制造装置用构件具有平坦的晶片载置面,其平面度为0.00mm。
[0092]
[实验例13]
[0093]
在实验例3中,将上部板和下部板设为aln制,将中间板变更为金属mo制,除此以外,与实验例3同样地操作,制造半导体制造装置用构件。其结果,得到的半导体制造装置用构件具有凸形状的晶片载置面,其平面度为0.09mm。
[0094]
[实验例14]
[0095]
在实验例4中,将上部板和下部板设为aln制,将中间板变更为金属mo制,除此以外,与实验例4同样地操作,制造半导体制造装置用构件。其结果,得到的半导体制造装置用构件具有凹形状的晶片载置面,其平面度为0.18mm。
[0096]
[实验例15]
[0097]
在实验例5中,将上部板和下部板设为aln制,将中间板变更为金属mo制,除此以外,与实验例5同样地操作,制造半导体制造装置用构件。其结果,得到的半导体制造装置用构件具有凸形状的晶片载置面,其平面度为0.09mm。
[0098]
符号说明
[0099]
10、110、210:半导体制造装置用构件,20、120、220:上部板,22、122:晶片载置面,22a:密封带,22b:圆形突起,24:静电电极,26、226:电阻发热体,28:电介质层,30:中间板,31:第一金属接合层,32:第二金属接合层,40、140、240:下部板,50:冷却装置,52:制冷剂通路,54:圆形槽,56:环状面,57:密封构件,58:螺纹孔,59:螺钉插入孔,60:紧固环,62:台阶,64:纵孔,66:螺纹孔,71、72:螺钉,80:接合体,301:第一金属接合材料,302:第二金属接合材料,w:晶片,s1、s2:空间。