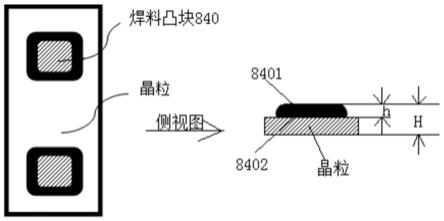
焊料凸块及其焊盘、半导体器件及其制备方法、封装件、背光单元及照明设备
1.技术领域
2.本发明涉及半导体器件领域,特别涉及一种焊料凸块及其焊盘、半导体器件及其制备方法、封装件、背光单元及照明设备。
背景技术:3.现有技术中,在led的电极上印刷印刷的焊料形状通常为穹顶形状的焊料,如图1所示,led主要分为方形尺寸的led(图1左)和长条尺寸的led(图1右)两种,由于方形尺寸的led一般设计4个焊料点,长条尺寸的led一般设计2个焊料点,在按照客户要求将led倒膜出货时,需要将蓝膜贴在焊料一面,如图2,由于焊料的形状为穹顶形状,与蓝膜接触面积小,方形led由于焊料的接触点多(图2左),焊料点上下左右对称,倒膜时不易出现倒膜损失以及倒膜后晶粒歪斜的情况。客户在固晶时,同样由于焊料点对称的缘故,不会出现固晶歪斜的情况。而长条尺寸的led由于接触点少(图2左),只上下或左右对称,倒膜时易出现倒膜损失以及受外力作用导致的晶粒歪斜,固晶时由于外力作用以及高温回流的影响,晶粒固晶后会出现偏移歪斜现象,影响晶粒的出光效果,尤其针对出光效果要求高的背光及mini产品,上述缺陷尤其明显。具有穹顶形状的焊料的半导体器件简图如图3所示。
4.形成在发光二极管的半导体芯片的电极上的焊料凸块可通过在金属反射层上形成焊料以及使焊料回流而形成,由于在回流处理期间焊料的相变,使得形成在焊料与金属反射层之间的金属间化合物层会由于金属反射层的润湿性而扩散至金属反射层的第二表面(侧表面),进而导致焊料或金属间化合物层与电极接触,相变所产生的残余应力会导致金属间化合物层中与电极接触的部分产生裂纹,从而会使得焊料凸块与电极分离。
5.公开号为cn105591016a、发明名称为互连凸块、半导体器件、半导体器件封装件和照明设备的发明专利中,通过在凸块下冶金层的第二表面(侧表面)上覆盖阻挡层,以防止焊料凸块或金属间化合物层中的其中之一扩散至凸块下冶金层的第二表面(侧表面),进而防止焊料凸块或金属间化合物层中的其中之一经第二表面(侧表面)扩散至凸块下冶金层下方的电极。该专利中,凸块下冶金层的第一表面(与电极相对的表面)与金属间化合物层之间没有阻挡层,且在焊料回流过程中,金属间化合物或焊料凸块没有形成在阻挡层中。这是因为在该专利中,凸块下冶金层的作用仅是形成共晶作用。
6.而为了提高芯片光性能,目前的凸块下冶金层通常使用al或ag材料作为金属反射层,以达到提高焊盘反射率的目的,在焊料回流过程中,若凸块下冶金层的第一表面(与电极相对的表面)与金属间化合物层之间没有阻挡层,则会出现金属间化合物或焊料凸块与凸块下冶金层的第一表面回流互溶的情况,这样就会导致金属反射层的反射率下降影响光性能,而且多次回流后底层粘附层也被焊料回流互溶,就会有焊盘脱落现象。
7.另外,现有技术中,由于镀膜工艺问题,金属间化合物在金属反射层的第一表面
(与电极相对的表面)的厚度(顶面金属间化合物层的厚度)通常会大于第二表面(侧表面)的厚度(侧面金属间化合物层的厚度),因此在回流焊后,焊料凸块与金属反射层的第二表面之间容易出现空洞,如图9所示,影响出光效率及器件的稳定性。
技术实现要素:8.发明目的:针对现有技术中存在的问题,本发明提供一种焊料凸块及其焊盘、半导体器件及其制备方法、封装件、背光单元及照明设备,本发明中的焊料凸块具有平整的上表面,增大了焊料凸块表面与蓝膜的接触面积,减少倒膜损失异常;不易出现固晶后晶粒偏移和歪斜的现象,保证了晶粒理想的出光效果,减少因固晶偏移或歪斜而进行返工的成本损失,提高了固晶良率与效率。
9.技术方案:本发明提供了一种用于半导体器件中的焊料凸块,所述焊料凸块的上表面和下表面均为平面,侧视截面为锥台型结构。
10.优选地,所述焊料凸块的上表面面积与下表面面积比大于50%。
11.优选地,所述焊料凸块的高度h大于其所在半导体器件的芯片整体高度h的5%,小于其所在半导体器件的芯片整体高度的50%。
12.优选地,所述焊料凸块的材质为sn成分大于40%的合金材料。优选snagcu合金、sncu合金。
13.本发明还提供了一种焊盘,用于半导体器件上,包括金属反射层,具有与所述半导体器件中电极的表面相对的第一表面,以及从所述第一表面的边缘延伸并连接至所述电极的第二表面;阻挡层,具有与所述第一表面相对的顶面阻挡层,该顶面阻挡层覆盖于所述第一表面上;金属间化合物层,具有顶面金属间化合物层,该顶面金属间化合物层覆盖于所述顶面阻挡层上;所述的焊料凸块,其键合至所述阻挡层,并使所述金属间化合物层介于所述焊料凸块与所述阻挡层之间。
14.进一步地,所述阻挡层还具有与所述第二表面相对的侧面阻挡层,该侧面阻挡层覆盖所述第二表面的部分或全部。阻挡层的顶面阻挡层覆盖金属反射层的第一表面,侧面阻挡层覆盖第二表面的部分或全部,使得整个金属反射层的第一表面的全部以及第二表面的部分或全部能够被阻挡层覆盖,有效隔离金属间化合物层或焊料凸块扩散至金属反射层,防止焊料和反射层互溶导致反射率下降影响性能,也防止经过多次回流后焊料对焊盘底层互溶导致焊盘脱落,还能有效防止金属间化合物层或焊料凸块经金属反射层扩散至电极,避免焊料在回流处理时由于相变所产生的残余应力导致金属间化合物层中与电极接触的部分产生裂纹,从而有效防止焊料凸块与电极分离。
15.优选地,所述侧面阻挡层的厚度大于或等于所述顶面阻挡层的厚度。受镀膜工艺的影响,覆盖在金属反射层的第一表面上的顶面阻挡层的厚度通常会大于位于覆盖在金属反射层的第二表面上的侧面阻挡层的厚度,当侧面阻挡层的厚度小于顶面阻挡层的厚度时,在焊料回流后,焊料凸块与金属反射层的第二表面之间容易出现空洞,影响出光效率及器件的稳定性,所以在本技术中,优选将侧面阻挡层的厚度设计成大于顶面阻挡层的厚度,防止焊料回流后出现焊料凸块与金属反射层的第二表面之间出现空洞的缺陷;本技术中通过改变沉积时焊盘角度,和沉积方法的变更,实现侧面阻挡层的厚度大于顶面阻挡层的厚度。
16.进一步地,所述金属间化合物层还具有与所述侧面阻挡层相对的侧面金属间化合物层,该侧面金属间化合物层覆盖所述侧面阻挡层。侧面金属间化合物层的设置是为了形成共晶层增强焊料的粘附性。
17.优选地,所述侧面金属间化合物层的厚度大于所述顶面金属间化合物层的厚度。受镀膜工艺的影响,覆盖在顶面阻挡层上的顶面金属间化合物层的厚度通常会大于位于覆盖在侧面阻挡层上的侧面金属间化合物层的厚度,当侧面金属间化合物层的厚度小于顶面金属间化合物层的厚度时,在焊料回流后,焊料凸块与金属反射层的第二表面之间容易出现空洞,影响出光效率及器件的稳定性,所以在本技术中,优选将侧面金属间化合物层的厚度设计成大于顶面金属间化合物层的厚度,防止焊料回流后出现焊料凸块与金属反射层的第二表面之间出现空洞的缺陷;本技术中通过改变沉积时焊盘角度,和沉积方法的变更实现侧面金属间化合物层的厚度大于顶面金属间化合物层的厚度。
18.优选地,所述侧面金属间化合物层的厚度与所述顶面金属间化合物层的厚度之差大于等于所述金属间化合物层与所述焊料凸块互溶的厚度。这样设计侧面金属间化合物层的厚度与顶面金属间化合物层的厚度之差,才能确保焊料回流后不会在焊料凸块与金属反射层的第二表面之间出现空洞的缺陷。
19.优选地,所述金属反射层为cr层、ti层、ni层、al层或ag层。本技术中金属反射层采用cr、ti、ni、al或ag材质,是为了实现粘附力好,反射率高功能,以达到提高光电性能的目的。
20.优选地,所述金属反射层的厚度为5000a~20000a。金属反射层的厚度较厚,优选为16000a。
21.优选地,所述阻挡层为ti/pt/ti三层结构。阻挡层中的ti/pt/ti三层结构中,pt层不易氧化,具有较强的阻挡作用;ti层具有粘附性,使pt层与上下两层ti层黏附,防止其上方的金属件化合物层和下方的金属反射层脱落。
22.优选地,所述阻挡层的ti/pt/ti三层结构中,上下ti层的厚度分别为 500~2000a,中间pt层的厚度为500~3000a。
23.优选地,所述金属间化合物层,为ni层或ni/au层。
24.优选地,所述金属间化合物层中的ni层的厚度为3000~10000a,au层的厚度>1000a。
25.本发明还提供了一种半导体器件,发光结构,该发光结构包括第一导电类型的半导体层、第二导电类型的半导体层和位于二者之间的有源层,以及所述的焊料凸块;所述焊料凸块位于第一导电类型的半导体层和第二导电类型的半导体层中的至少一个的电极上。
26.本发明还提供了一种半导体器件的制作方法,包括以下步骤:步骤1:在制备好的具有所述电极的圆片表面上电极所在位置印刷锡膏,再通过高温回流得到具有穹顶形状焊料的圆片;步骤2:对所述具有穹顶形状焊料的圆片进行清洗,去除表面残留的助焊剂以及杂质;步骤3:对所述圆片具有穹顶形状焊料的一面进行抛光,抛光至所述具有穹顶形状的焊料形成所述焊料凸块时止,得到所述半导体器件。
27.本发明还提供了一种半导体器件,包括发光结构,该发光结构包括第一导电类型的半导体层、第二导电类型的半导体层和位于二者之间的有源层,以及所述的焊盘;所述焊盘中的金属反射层位于第一导电类型的半导体层和第二导电类型的半导体层中的至少一
个的电极上。
28.本发明还提供了一种半导体器件的制作方法,包括以下步骤:步骤1:在制备好的具有所述金属间化合物层的圆片表面上金属间化合物层所在位置印刷锡膏,再通过高温回流得到具有穹顶形状焊料的圆片;步骤2:对所述具有穹顶形状焊料的圆片进行清洗,去除表面残留的助焊剂以及杂质;步骤3:对所述圆片具有穹顶形状焊料的一面进行抛光,抛光至所述具有穹顶形状的焊料形成所述焊料凸块时止,得到所述半导体器件。
29.本发明还提供了一种半导体器件封装件,包括所述的半导体器件。
30.进一步地,所述的半导体器件封装件还包括:封装件主体,所述半导体器件设置于所述封装件主体上,以及对所述半导体器件进行包封的包封部分。
31.本发明还提供了一种半导体器件的背光单元,包括至少一个所述的半导体器件封装件。
32.本发明还提供了一种照明设备,包括至少一个所述的半导体器件封装件。
33.有益效果:本发明中改进后表面平坦化的焊料凸块应用在半导体器件上时,一方面出货倒膜时,晶粒与蓝膜接触时,不再是原先的点接触,而是面接触,增大了焊料凸块表面与蓝膜的接触面积,进而改善了晶粒出货时倒膜损失的异常;另一方面,封装厂在固晶作业时,由于焊料凸块表面抛光成为平面,固晶时晶粒与基板或支架是面接触,不易出现固晶后晶粒偏移和歪斜的现象,保证了晶粒理想的出光效果,减少因固晶偏移或歪斜而进行返工的成本损失,提高了固晶良率与效率。
34.本技术中用于半导体器件上的焊盘结构中,金属反射层的作用是提高焊盘的金属反射率,为了提高芯片的光电性能,需要避免金属间化合物层或焊料凸块扩散至金属反射层,所以,本技术中的金属反射层的第一表面(与电极相对的表面)通过阻挡层与金属间化合物层(回流处理后与焊料凸块互溶形成的共晶层)隔离,该阻挡层的设置一方面能够有效隔离金属间化合物层或焊料凸块与金属反射层,防止金属间化合物层或焊料凸块扩散至金属反射层;另一方面能够有效防止金属间化合物层或焊料凸块经金属反射层扩散至电极;避免焊料在回流处理时由于相变所产生的残余应力导致金属间化合物层中与电极接触的部分产生裂纹,从而有效防止焊料凸块与电极分离,提高使用该焊盘半导体器件的出光效率及稳定性。
35.本发明中的焊盘结构能够有效隔离金属间化合物层或焊料凸块与金属反射层,防止金属间化合物层或焊料凸块扩散至金属反射层,进而防止金属间化合物层或焊料凸块经金属反射层扩散至电极。
36.本技术提供了制备具有上述焊料凸块的半导体器件的方法,通过在焊料凸块回流清洗后增加正面抛光工艺,将带有焊料凸块的圆片正面朝上,背面凃蜡的方式固定在陶瓷盘上,再将陶瓷盘装载到抛光机上,设置合理的压力以及抛光时间进行抛光,将原先穹顶形状结构焊料顶部抛光掉,抛光成表面为平面结构,进而得到一种平坦化焊料凸块的半导体器件。在实际应用中,也可以通过光刻、蒸镀的形式将锡或锡合金镀在圆片的电极表面,以此得到表面平整的焊料凸块。
附图说明
37.图1为现有技术中方形led-穹顶形状焊料(左)和长条led-穹顶形状焊料(右)示意图;图2为现有技术中方形led-穹顶形状焊料(左)和长条led-穹顶形状焊料(右)倒膜时的示意图;图3为现有技术中具有穹顶形状焊料的led结构简图;图4为实施方式1中led-平坦表面焊料凸块的俯视图(左)和侧视图(右);图5为实施方式1中led-平坦表面焊料凸块倒膜(上)和固晶(下)时的示意图;图6为实施方式2中焊盘的结构示意图;图7为实施方式3中焊盘的结构示意图;图8为覆盖在金属反射层的第一表面上的顶面阻挡层的厚度大于位于覆盖在金属反射层的第二表面上的侧面阻挡层的厚度的焊盘结构示意图;图9为侧面阻挡层比顶面阻挡层厚度薄、或者侧面金属间化合物层比顶面金属间化合物层薄时,焊料凸块与金属反射层的第二表面之间出现空洞时的扫描电子显微镜图片;图10为实施方式4中焊盘的结构示意图;图11和图12为实施方式5中焊盘的结构示意图;图13为实施方式6中焊盘的结构示意图;图14为图1所示的焊盘结构在金属间化合物层与焊料凸块回流互溶后的示意图;图15为实施方式7中半导体器件的结构示意图;图16为制备实施方式7中半导体器件时的结构示意图;图17为实施方式8中半导体器件的结构示意图;图18和19为实施方式9中半导体器件封装件的结构示意图;图20和21为实施方式10中半导体器件的背光单元的截面图;图22为实施方式11中半导体器件的照明设备的分解透视图;图23为实施方式11中半导体器件的照明设备为条形灯时的部分结构示意图。
具体实施方式
38.下面结合附图对本发明进行详细的介绍。
39.实施方式1:本实施方式提供了一种用于半导体器件上的焊料凸块840,该焊料凸块840的上表面8401和下表面8402均为平面,侧视截面为锥台型结构,实际应用中,该焊料凸块840的下表面可以为方形、圆形、多边形等;上部可以为椭圆形,侧视图为堆台形。上表面8401面积与下表面8402面积比大于50%。焊料凸块840的高度h大于其所在半导体器件的芯片整体高度h的5%,小于其所在半导体器件的芯片整体高度h的50%,芯片的整体高度h是指从衬底100下表面至焊料凸块840上表面的高度。焊料凸块的材质优选snagcu合金、sncu合金,其中的sn成分大于40%。如图5所示为具有该焊料凸块840的晶粒俯视图,图6为具有该焊料凸块840的晶粒在倒模(图6上,焊料凸块840一面贴上蓝膜)和固晶(图6下,焊料凸块840一面与基板或支架焊合)时的示意图。
40.实施方式2:本实施方式提供了一种用于半导体器件上的焊盘,如图6所示,其特征在于,包括:金属反射层810,具有与半导体器件中电极721或722的表面相对的第一表面811,以及从第一表面811的边缘延伸并连接至电极721或722的第二表面812;阻挡层820,具有与第一表面811相对的顶面阻挡层821,该顶面阻挡层821覆盖于第一表面811上;金属间化合物层830,具有顶面金属间化合物层831,该顶面金属间化合物层831覆盖于顶面阻挡层821上;实施方式1中的焊料凸块840,其键合至阻挡层820,并使金属间化合物层830介于焊料凸块840与阻挡层820之间。
41.上述金属反射层810为ag层,厚度为16000a。上述阻挡层820为ti/pt/ti三层结构,其中,上下ti层的厚度分别为 1500a,中间pt层的厚度为2000a。上述金属间化合物层830为ni层,厚度为6000a。上述焊料凸块840为sn层。
42.实施方式3:本实施方式为实施方式2的进一步改进,主要改进之处在于,在实施方式2中,阻挡层820仅具有覆盖在第一表面811的顶面阻挡层821,在焊料回流处理时,金属间化合物层830或焊料凸块840很有可能会扩散至金属反射层810,进而经金属反射层810扩散至电极,最终导致金属间化合物层830与电极721或722接触的部分产生裂纹,导致焊料凸块840与电极721或722分离。而在本实施方式中,阻挡层820还具有与第二表面812相对的侧面阻挡层822,该侧面阻挡层822覆盖第二表面812的部分或全部(如图7所示为侧面阻挡层822部分覆盖第二表面812的示意图)。这样设计后使得整个金属反射层810的第一表面811的全部以及第二表面812的部分或全部能够被阻挡层820覆盖,有效隔离金属间化合物层830或焊料凸块840扩散至金属反射层810,防止对金属反射层产生互溶导致反射率下降,还能有效防止金属间化合物层830或焊料凸块840经金属反射层810扩散至电极721或722,避免焊料在回流处理时由于相变所产生的残余应力导致金属间化合物层830中与电极721或722接触的部分产生裂纹,从而有效防止焊料凸块840与电极721或722分离。
43.除此之外,本实施方式与实施方式2完全相同,此处不做赘述。
44.实施方式4:本实施方式为实施方式3的进一步改进,主要改进之处在于,在实施方式3中,受镀膜工艺的影响,覆盖在金属反射层810的第一表面811上的顶面阻挡层821的厚度通常会大于位于覆盖在金属反射层810的第二表面812上的侧面阻挡层822的厚度,如图8,在焊料回流后,焊料凸块840与金属反射层810的第二表面812之间容易出现空洞,如图9,影响出光效率及器件的稳定性,所以在本实施方式中,优选将侧面阻挡层822的厚度设计成大于或等于顶面阻挡层821的厚度,防止焊料回流后出现焊料凸块840与金属反射层810的第二表面812之间出现空洞的缺陷,如图10所示。本实施方式通过改变焊盘角度和金属沉积方式的方法实现侧面阻挡层822的厚度大于顶面阻挡层821的厚度。
45.除此之外,本实施方式与实施方式3完全相同,此处不做赘述。
46.实施方式5:本实施方式为实施方式3或4的进一步改进,主要改进之处在于,在实施方式3或4中,金属间化合物层830仅具有覆盖在顶面阻挡层821上的顶面金属间化合物层831,这样可能会导致侧面焊料会互溶金属反射层,或者有间隙导致粘附力偏弱。所以,在本实施方式
中,金属间化合物层830还具有与侧面阻挡层822相对的侧面金属间化合物层832,如图11和12,该侧面金属间化合物层832覆盖侧面阻挡层822,能够有效避免焊料对焊盘反射层产生互溶影响反射率。
47.除此之外,本实施方式与实施方式3或4完全相同,此处不做赘述。
48.实施方式6:本实施方式为对实施方式5中图12的进一步改进,主要改进之处在于,在实施方式5的图12中,受镀膜工艺的影响,覆盖在顶面阻挡层821上的顶面金属间化合物层831的厚度通常会大于位于覆盖在侧面阻挡层822上的侧面金属间化合物层832的厚度,如图12,在焊料回流后,焊料凸块840与金属反射层810的第二表面812之间容易出现空洞,如图9,影响出光效率及器件的稳定性,所以在本实施方式中,优选将侧面金属间化合物层832的厚度设计成大于顶面金属间化合物层831的厚度,如图13,防止焊料回流后出现焊料凸块840与金属反射层810的第二表面812之间出现空洞的缺陷;本技术中通过改变焊盘角度和金属沉积方式的方法实现侧面金属间化合物层832的厚度大于顶面金属间化合物层831的厚度。
49.另外,为了确保焊料回流后不会在焊料凸块840与金属反射层810的第二表面812之间出现空洞的缺陷,本实施方式中侧面金属间化合物层832的厚度与顶面金属间化合物层831的厚度之差大于等于金属间化合物层830与焊料凸块840互溶的厚度。
50.图6所示的焊盘结构在金属间化合物层830与焊料凸块840回流互溶后的示意图如图14所示,其中的831为金属间化合物层830与焊料凸块840互溶界面层。还可以看出回流焊后,焊料凸块840与金属反射层810之间也填满焊料,没有空隙。
51.除此之外,本实施方式与实施方式5完全相同,此处不做赘述。
52.实施方式7:本实施方式提供了一种半导体器件1000,如图15所示,包括具有多个电极的发光结构,该发光结构包括第一导电类型的半导体层210、第二导电类型的半导体层220和位于二者之间的有源层230,第一导电类型的半导体层210下方为衬底100,第二导电类型的半导体层220上方具有cbl电流阻挡层300,cbl电流阻挡层300上方覆盖ito电流扩展层400,图中的211为n gan台阶区,110为iso隔离槽,711、712分别为第一电极pn-finger;500为pv保护层dbr,721、722分别为第二电极pn-metal,600为覆盖于半导体器件上除焊盘840位置的绝缘层;840为上述实施方式1中所述的焊料凸块;焊料凸块840位于第一导电类型的半导体层210和第二导电类型的半导体层220中的各第二电极p-metal 721、第二电极n
ꢀ‑ꢀ
metal 722上。上述第一导电类型的半导体层210和第二导电类型的半导体层220均包括al
x
inyga
(1-x-y)
n,其中0≤x<1,0≤y<1,并且0≤x+y<1。
53.上述半导体器件1000的制作方法如下:步骤1:在制备好的具有第二电极p-metal 721、第二电极n
ꢀ‑ꢀ
metal 722的圆片表面上各第二电极所在位置印刷锡膏,再将圆片通过高温回流焊机台回流得到具有穹顶形状焊料的圆片;(具有第二电极p-metal 721、第二电极n
ꢀ‑ꢀ
metal 722的圆片的制备方法可以参考公开号为“cn 111799356 a、专利名称为一种具有凸点焊盘的led芯片设计方法”的发明专利。)步骤2:对具有穹顶形状焊料的圆片放在特殊清洗溶液中进行清洗,去除表面残留的助焊剂以及杂质;
步骤3:将清洗后带穹顶形状焊料的圆片通过高温上蜡的形式,固定在陶瓷盘上,需保证具有穹顶形状焊料的一面朝上,再将陶瓷盘安装在抛光机,保证具有穹顶形状焊料的一面与抛光机底面抛光垫直接接触,如图16所示,设置好合理的压力以及抛光时间,开始抛光,达到设定的抛光厚度后,具有穹顶形状的焊料形成焊料凸块,将陶瓷盘取下并高温下蜡,再将圆片进行下蜡清洗,得到半导体器件。
54.实施方式8:本实施方式提供了一种半导体器件1000,如图17所示,与实施方式7中的半导体器件1000大致相同,不同点仅在于,在各第二电极p-metal 721、第二电极n
ꢀ‑ꢀ
metal 722上,键合的是实施方式2至6中任一项所述的焊盘。焊盘800中的金属反射层810位于第一导电类型的半导体层210和第二导电类型的半导体层220中的各第二电极p-metal 721、第二电极n
ꢀ‑ꢀ
metal 722上。
55.上述半导体器件1000的制作方法与实施方式7中半导体器件的制作方法大致相同,不同点仅在于步骤1中,在制备好的具有金属反射层810的圆片表面上各金属反射层810所在位置印刷锡膏,再通过高温回流得到具有穹顶形状焊料的圆片。
56.除此之外,本实施方式与实施方式7完全相同,此处不做赘述。
57.实施方式9:本实施方式提供了一种半导体器件封装件2000,如图18所示,包括封装件主体2001、实施方式7或8中所述的半导体器件2002(相当于图15或图17所示的半导体器件1000,并将省略其描述),一对引线框架2003以及对半导体器件2002进行包封的包封部分2004,半导体器件2002设置于封装件主体2001上,半导体器件2002中的焊盘2005(相当于图15或图17中所示的焊盘800,并将省略其描述)可通过焊料20051电连接至引线框架2003。
58.参照图19,半导体器件封装件2000可包括半导体器件2002(相当于图15或图17所示的半导体器件1000,并将省略其描述)、安装衬底2006和包封部分2007。半导体器件2002可安装在安装衬底2006上,半导体器件2002中的焊盘2005(相当于图15或图17中所示的焊盘800,并将省略其描述)可通过焊料20051电连接至安装衬底2006上的电路图案20061。
59.半导体器件2002可由包封部分2007包封。通过这种方式,可提供板上芯片(cob)型封装件结构。可将安装衬底2006提供为诸如印刷电路板(pcb)、金属芯印刷电路板(mcpcb)、多层印刷电路板(mpcb) 或柔性印刷电路板(fpcb) 的衬底,并且可按照多种不同的方式对安装衬底2006的结构进行应用。
60.实施方式10:本实施方式提供了一种半导体器件的背光单元,如图20和图21是示出包括实施方式9中的半导体器件封装件的背光单元的截面图。
61.参照图20,背光单元3000可包括安装在衬底3002上的光源3001以及设置在光源3001 上方的至少一个光学片材3003。可使用具有参照图18和图19描述的半导体器件封装件2000结构或者与其相同或相似结构的半导体器件封装件来作为光源3001,或者可按照所谓cob型的方式将如图15或图17所述的半导体器件1000直接安装在衬底3002上。
62.图20所示的背光单元3000中的光源3001可沿着设置液晶显示(lcd)器件的方向向上发射光。
63.在图21所示的另一示例的背光单元4000中,安装在衬底4002上的光源4001 (可使
用具有参照图18和图19描述的半导体器件封装件2000结构或者与其相同或相似结构的半导体器件封装件来作为光源4001,或者可按照所谓cob型的方式将如图15或图17所述的半导体器件1000直接安装在衬底4002上)可在横向方向上发光,从而使发射的光可入射至导光板4003上,以将其转换为表面光源的形式。已穿过导光板4003的光可向上消散,并且反射层4004可设置在导光板4003下方以提高光提取效率。
64.实施方式11:本实施方式提供了一种半导体器件的照明设备,如图22和图23示出包括实施方式9中的半导体器件封装件2000的照明设备的分解透视图。
65.参照图22,照明设备5000示为灯泡型照明器,并且可包括发光模块5010、驱动单元5020 和外部连接单元5030。另外,照明设备5000还可包括诸如外部壳体5040、内部壳体5050 和盖体单元5060 的外部结构。
66.发光模块5010可包括具有与图15或图17的半导体器件1000相同或相似结构的半导体器件5011以及其上安装有半导体器件5011的电路衬底5012。在本实施方式中,示例了单个半导体器件5011安装在电路衬底5012上的示例;然而,根据需要,可将多个半导体器件5011安装在电路衬底5012 上。此外,半导体器件5011可以不直接安装在电路衬底5012上,而是可在按照图18和图19所示的半导体器件封装件2000的形式进行制造之后将其安装在电路衬底5012上。
67.外部壳体5040 可用作散热单元,并且可包括与发光模块5010直接接触以提高散热效果的散热板5041以及包围外部壳体5040 的侧表面的散热片5042。盖体单元5060可安装在发光模块5010上,并且可具有凸透镜形状。驱动单元5020可安装在内部壳体5050中,并且可连接至诸如插座结构的外部连接单元5030以从外部提供功率。另外,驱动单元5020 可将功率转换为用于对发光模块5010的半导体器件5011进行驱动的合适的电流源,并且可提供经转换的电流源。此外,虽然未示出,但是照明设备5000 还可包括通信模块。
68.参照图23,可将照明设备6000 设计为条型灯,并且可包括发光模块6010、主体单元6020、盖体单元6030、端子单元6040。
69.发光模块6010可包括衬底6012和安装在衬底6012上的多个半导体器件6011。半导体器件6011可为图15或图17中所示的半导体器件1000或图18和图19所示的半导体器件封装件2000。
70.可利用凹进6021将发光模块6010安装并固定在主体单元6020 的一个表面上,并且可向外消散发光模块6010所产生的热。因此,主体单元6020可包括作为一种支承结构的散热器,并且可包括用于散热的多个散热鳍片6022,其提供在主体单元6020 的两个横向表面上同时从其上突出。
71.盖体单元6030可紧固至主体单元6020的紧固凹槽6023,并且可具有半圆形曲面,以允许光均匀地向外消散。与壳体6020的紧固凹槽6023接合的突出部分6031可沿着主体单元6020 的长度方向形成在盖体单元6030的底表面上。
72.可在主体单元6020的开口端部中沿着主体单元6020的长度方向提供端子单元6040,并且可以向发光模块6010提供功率。端子单元6040可包括向外突出的电极销6041。
73.上述实施方式只为说明本发明的技术构思及特点,其目的在于让熟悉此项技术的
人能够了解本发明的内容并据以实施,并不能以此限制本发明的保护范围。凡根据本发明精神实质所做的等效变换或修饰,都应涵盖在本发明的保护范围之内。