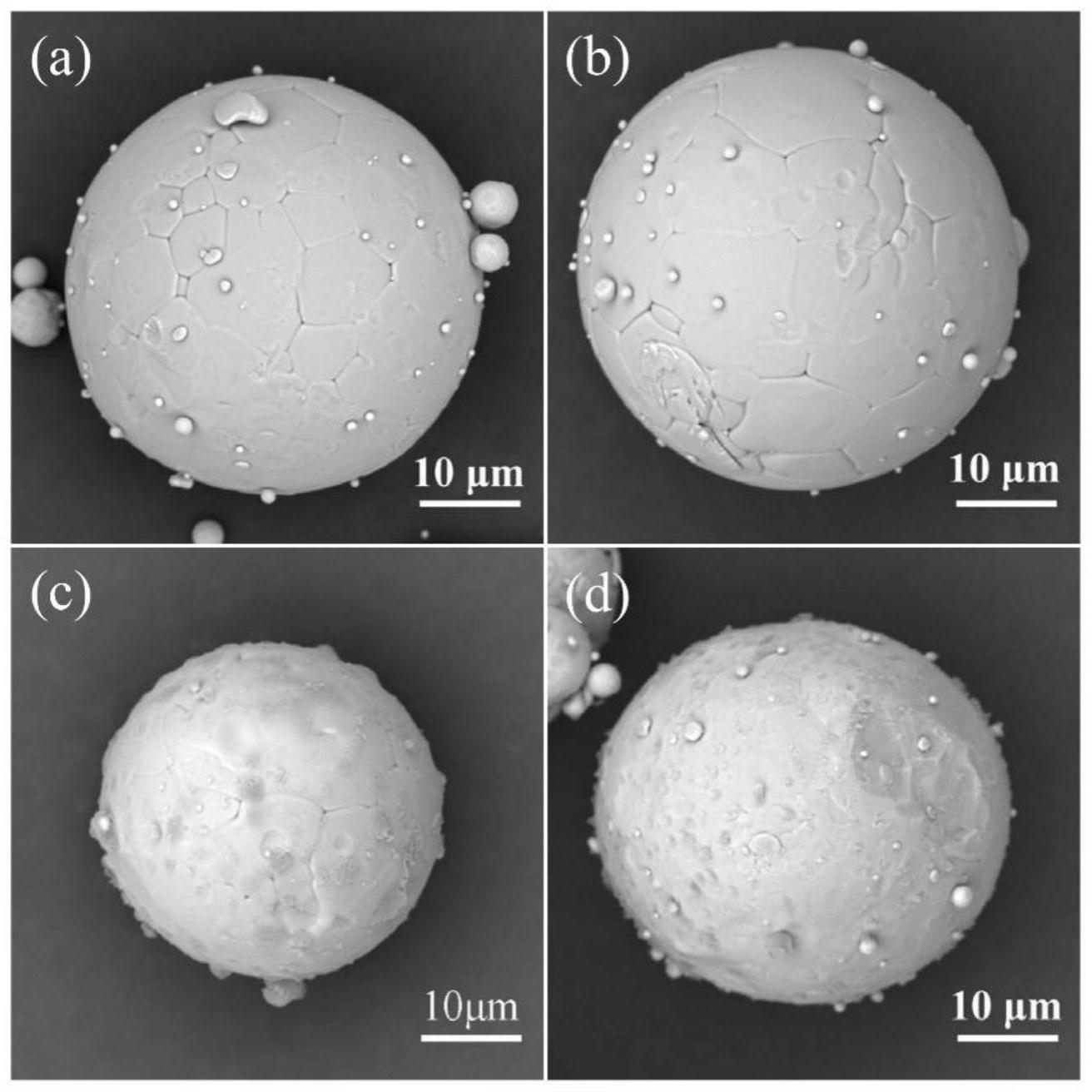
1.本发明属于磁性材料技术领域,特别涉及一种铁镍钼/二氧化硅软磁粉芯复合材料的制备。
背景技术:2.随着计算机、雷达、电动汽车及其他高端电力电子器件向高频化、微型化发展,迫切需要开发高响应、高效率密度和低损耗的软磁材料来实现器件的小型化和高效节能。由于软磁合金材料电阻率偏小,从而导致其在交变磁场中随频率上升,涡流损耗迅速增加,一定程度上限制了其在较高频率条件下的应用。提高金属软磁材料的电阻率能够显著降低交变磁场及高频环境中的涡流损耗,可以实现软磁合金的高饱和磁感应强度特性、高磁导率及低矫顽力特性的高效利用。目前使用最广泛的金属软磁粉芯材料主要有fe、fesi、fesial、feni和fenimo等。在这些材料中,fenimo相比于其他材料表现出更为优异的软磁性能;由于mo元素的加入,降低了磁晶各向异性常数,增加了相对磁导率,降低了涡流损耗,其磁致伸缩几乎为零,可以应用到更高的工作频率范围。在现有软磁粉芯材料中,由于纯的金属软磁粉芯材料均为金属,电阻率低,导致其涡流损耗较大,在高频情况下发热严重,因此限制了其在高频下的应用。软磁粉芯材料的电阻率与涡流损耗紧密相关,材料电阻率越大,同频率条件下的涡流损耗越小。因此,研究者们提出绝缘包覆工艺,在金属软磁材料表面包覆一层绝缘材料,获得了高电阻率,低涡流损耗的软磁复合材料(smcs),以达到其高频应用的目的。目前的绝缘材料主要有两种:有机材料和无机材料。相比于有机涂层,无机涂层具有更好的热稳定性和绝缘性能,其中sio2、al2o3应用最为广泛。sio2和al2o3颗粒通常采用溶胶-凝胶法和水热法制备而成。研究者们通过机械球磨法和溶胶凝胶法制备了fe/al2o3复合材料,al2o3的加入使得fe粉芯频率稳定性增强,损耗也显著降低。在已报到的研究中,金属软磁粉芯材料的包覆工艺大多集中于fe和fesial等软磁材料,而对于fenimo的绝缘包覆工艺的研究还较少。与此同时,软磁复合粉芯材料在推进商业化的进程中也面临着诸多难题,比如有效磁导率较低、损耗较高、高频稳定性较差以及制造成本过高。
技术实现要素:3.本发明的一个目的是解决至少上述问题和/或缺陷,并提供至少后面将说明的优点。
4.为了实现根据本发明的这些目的和其它优点,提供了一种铁镍钼/二氧化硅软磁粉芯复合材料的制备方法,包括以下步骤:
5.步骤一、将气雾化fenimo粉末放入真空管式炉中,通入h2/ar混合气体,升温进行烧结,得到烧结后的fenimo粉末;
6.步骤二、将烧结后的fenimo粉末通过溶胶-凝胶法进行sio2绝缘包覆,得到sio2包覆的fenimo复合粉末;
7.步骤三、将sio2包覆的fenimo复合粉末和环氧树脂、润滑剂混合,然后压制,得到
预压成型的复合粉芯;
8.步骤四、将预压成型的复合粉芯烧结,得到fenimo/sio2软磁粉芯复合材料。
9.优选的是,所述步骤一中,气雾化fenimo粉末的元素含量分别为81wt%ni、17wt%fe和2wt%mo,粒径尺寸为10-30μm。
10.优选的是,所述步骤一中,将气雾化fenimo粉末放入刚玉舟中,将刚玉舟放入真空管式炉中,使用机械泵抽真空10~30min;通入h2/ar混合气体,待气压表指针达到0mpa时,打开出气口,使之保持大气压状态;设置升温程序,处理温度设置为450~650℃,升温速率5~15℃/min,保温时间45~120min,之后开始自然降温;待管式炉温度降低至室温,关闭气体,得到烧结后的fenimo粉末。
11.优选的是,所述步骤二中,溶胶-凝胶法进行sio2绝缘包覆的过程为:将烧结后的fenimo粉末中加入无水乙醇、硅烷偶联剂和去离子水,搅拌45~90min,然后加入正硅酸乙酯,在45~60℃下搅拌2~4h,分离,固体使用无水乙醇清洗,然后经过抽滤后烘干,获得sio2包覆的fenimo复合粉末。
12.优选的是,所述烧结后的fenimo粉末与无水乙醇的质量体积比为1g:10~15ml;所述烧结后的fenimo粉末与硅烷偶联剂的质量体积比为1g:0.15~0.35ml;所述烧结后的fenimo粉末与去离子水的质量体积比为1g:1~2ml;所述烧结后的fenimo粉末与正硅酸乙酯的质量体积比为1g:0.03~0.07ml;所述搅拌的速度为400~600r/min。
13.优选的是,所述步骤三中,将环氧树脂溶解在丙酮中,然后加入sio2包覆的fenimo复合粉末,将丙酮挥发,添加润滑剂,然后压制;其中,环氧树脂的用量为sio2包覆的fenimo复合粉末质量的0.8~1.5wt%;润滑剂的用量为sio2包覆的fenimo复合粉末质量的0.3~0.7wt%;sio2包覆的fenimo复合粉末与丙酮的质量体积比为1g:4~6ml;压制的压力500~800mpa,保压10~20s。
14.优选的是,所述步骤四中,将预压成型的复合粉芯放入真空管式炉中,在氩气氛围中,在400~800℃下进行烧结,升温速率5~15℃/min,保温时间45~120min,自然降温,得到fenimo/sio2软磁粉芯复合材料。
15.优选的是,所述步骤二的过程替换为:将烧结后的fenimo粉末中加入无水乙醇a、硅烷偶联剂a和去离子水a,搅拌45~90min,然后加入正硅酸乙酯a,在45~60℃下搅拌2~4h,分离,固体使用无水乙醇清洗,然后经过抽滤后烘干,获得sio2包覆的fenimo复合粉末;将sio2包覆的fenimo复合粉末放入低温等离子处理仪腔体内,关闭腔体口,打开真空泵,抽真空至腔体内真空度降至50pa以下后,打开氧气和二氧化碳气体流量阀,控制通入氧气和二氧化碳气体的摩尔比为4:1,再打开高频电源,在100~200w条件下处理3~5min,得到预处理sio2包覆的fenimo复合粉末;将预处理sio2包覆的fenimo复合粉末加入无水乙醇b、硅烷偶联剂b和去离子水b,搅拌45~90min,然后加入微波超声波一体化反应器中,同时加入正硅酸乙酯b,同时开启微波和超声波进行协同处理60~90min,分离,固体使用无水乙醇清洗,然后经过抽滤后烘干,获得最终sio2包覆的fenimo复合粉末。
16.优选的是,所述烧结后的fenimo粉末与无水乙醇a的质量体积比为1g:5~7.5ml;所述烧结后的fenimo粉末与硅烷偶联剂a的质量体积比为1g:0.075~0.175ml;所述烧结后的fenimo粉末与去离子水a的质量体积比为1g:0.5~1ml;所述烧结后的fenimo粉末与正硅酸乙酯a的质量体积比为1g:0.015~0.035ml;所述搅拌的速度为400~600r/min;
17.所述预处理sio2包覆的fenimo复合粉末与无水乙醇b的质量体积比为1g:5~7.5ml;所述预处理sio2包覆的fenimo复合粉末与硅烷偶联剂b的质量体积比为1g:0.075~0.175ml;所述预处理sio2包覆的fenimo复合粉末与去离子水b的质量体积比为1g:0.5~1ml;所述预处理sio2包覆的fenimo复合粉末与正硅酸乙酯b的质量体积比为1g:0.015~0.035ml。
18.优选的是,所述微波功率为200~400w;超声功率为300~500w,超声频率为65~75khz;温度为45~60℃。
19.本发明至少包括以下有益效果:本发明选用软磁性能优秀的fenimo为基材,确保了粉芯材料的高频稳定性;同时,对fenimo进行sio2绝缘包覆,实现了fenimo软磁性能的显著提高。与其他同类软磁复合粉芯相比,通过h2/ar混合气体高温预处理工艺和绝缘包覆工艺的协同作用,本发明制备的fenimo/sio2复合粉芯具有优秀的软磁性能。经过还原性气氛高温预处理工艺后的绝缘包覆可以更大程度提升软磁粉芯复合材料的磁导率,降低其损耗,为软磁粉芯复合材料性能的提升提供了一种新的策略。本发明整个制备过程易调控、工艺简单、制备快速、可实现自动化大规模生产。
20.本发明的其它优点、目标和特征将部分通过下面的说明体现,部分还将通过对本发明的研究和实践而为本领域的技术人员所理解。
附图说明:
21.图1给出了气雾化fenimo粉末(a)、经h2/ar混合气体高温烧结后的fenimo粉末(b,实施例1~5步骤一)、气雾化fenimo粉末包覆sio2后的复合粉末(c,对比例1~5,步骤一)、经h2/ar混合气体高温烧结后的fenimo粉末包覆sio2后的复合粉末(d,实施例1~5,步骤一~二)的sem图;
22.图2(a)-(d)给出了对比例1~5步骤一得到的sio2包覆的fenimo复合粉末的sem图像(a)以及fe(b)、ni(c)和mo(d)元素的元素分布图;
23.图3(a)-(d)分别为气雾化fenimo粉末(未烧结)的xps全谱;图3(e)-(h)分别为对比例6烧结后的fenimo粉末的xps全谱;
24.图4给出了气雾化fenimo粉末(对比例11)以及气雾化fenimo粉末在h2/ar混合气体中经过不同温度处理后(对比例6~10)压制成型的软磁粉芯的有效磁导率和损耗,测试条件为b=100mt;
25.图5(a)对比例1~5制备的fenimo/sio2软磁粉芯复合材料(fs0)的有效磁导率;图5(b)对比例1~5制备的fenimo/sio2软磁粉芯复合材料的损耗;图5(c)实施例1~5制备的fenimo/sio2软磁粉芯复合材料(fs600)的有效磁导率;图5(d)实施例1~5制备的fenimo/sio2软磁粉芯复合材料的损耗;测试条件为b=100mt;
26.图6给出了h2/ar混合气体600℃处理后的粉末(对比例9)、未处理的fenimo原粉包覆sio2后的粉末(对比例3)和h2/ar混合气体600℃处理后的粉末包覆sio2后的粉末(实施例3)压制成粉芯,在600℃进行烧结后的有效磁导率和损耗;测试条件为b=100mt;
27.图7给出了实施例1和实施例6制备的fenimo/sio2软磁粉芯复合材料的和损耗;测试条件为b=100mt;
28.图8给出了实施例2和实施例7制备的fenimo/sio2软磁粉芯复合材料的和损耗;测
试条件为b=100mt;
29.图9给出了实施例3和实施例8制备的fenimo/sio2软磁粉芯复合材料的和损耗;测试条件为b=100mt。
具体实施方式:
30.下面结合附图对本发明做进一步的详细说明,以令本领域技术人员参照说明书文字能够据以实施。
31.应当理解,本文所使用的诸如“具有”、“包含”以及“包括”术语并不配出一个或多个其它元件或其组合的存在或添加。
32.实施例1~5:
33.一种铁镍钼/二氧化硅软磁粉芯复合材料的制备方法,包括以下步骤:
34.步骤一、将60g气雾化fenimo粉末放入刚玉舟中,将刚玉舟放入真空管式炉中,使用机械泵抽真空20min;通入h2/ar混合气体,待气压表指针达到0mpa时,打开出气口,使之保持大气压状态;设置升温程序,处理温度设置为600℃,升温速率10℃/min,保温时间60min,之后开始自然降温;待管式炉温度降低至室温,关闭气体,得到烧结后的fenimo粉末;气雾化fenimo粉末的元素含量分别为81wt%ni、17wt%fe和2wt%mo,粒径尺寸为10-30μm。
35.步骤二、将20g烧结后的fenimo粉末中加入170ml无水乙醇、5ml硅烷偶联剂(kh550)和30ml去离子水,以500r/min的速度搅拌60min,然后加入正1ml硅酸乙酯,水浴加热在50℃下搅拌反应3h,分离,固体使用无水乙醇清洗,然后经过抽滤后烘干,获得sio2包覆的fenimo复合粉末;
36.步骤三、将环氧树脂溶解在10ml丙酮中,然后加入2g sio2包覆的fenimo复合粉末,使丙酮挥发,添加润滑剂(硬脂酸锌),在600mpa(作用到样品上的压力)的压力下,保压10s,将混合粉末压制成外径10.2mm、内径5.08mm的环状样品;环氧树脂的用量为sio2包覆的fenimo复合粉末质量的1wt%;润滑剂(硬脂酸锌)的用量为sio2包覆的fenimo复合粉末质量的0.5wt%;
37.步骤四、将预压成型的复合粉芯放入真空管式炉中,在氩气氛围中,在高温(如表1所示,给出实施例1~5的烧结温度)下进行烧结,升温速率10℃/min,保温时间60min,自然降温,得到fenimo/sio2软磁粉芯复合材料。
38.表1
39.实施例实施例1实施例2实施例3实施例4实施例5烧结温度400℃500℃600℃700℃800℃
40.实施例6~8:
41.一种铁镍钼/二氧化硅软磁粉芯复合材料的制备方法,包括以下步骤:
42.步骤一、将60g气雾化fenimo粉末放入刚玉舟中,将刚玉舟放入真空管式炉中,使用机械泵抽真空20min;通入h2/ar混合气体,待气压表指针达到0mpa时,打开出气口,使之保持大气压状态;设置升温程序,处理温度设置为600℃,升温速率10℃/min,保温时间60min,之后开始自然降温;待管式炉温度降低至室温,关闭气体,得到烧结后的fenimo粉末;气雾化fenimo粉末的元素含量分别为81wt%ni、17wt%fe和2wt%mo,粒径尺寸为10-30
μm。
43.步骤二、将20g烧结后的fenimo粉末中加入85ml无水乙醇a、2.5ml硅烷偶联剂a(kh550)和15ml去离子水a,搅拌60min,然后加入0.5ml正硅酸乙酯a,水浴加热在50℃下搅拌反应3h,分离,固体使用无水乙醇清洗,然后经过抽滤后烘干,获得sio2包覆的fenimo复合粉末;将sio2包覆的fenimo复合粉末放入低温等离子处理仪腔体内,关闭腔体口,打开真空泵,抽真空至腔体内真空度降至50pa以下后,打开氧气和二氧化碳气体流量阀,控制通入氧气和二氧化碳气体的摩尔比为4:1,再打开高频电源,在150w条件下处理3min,得到预处理sio2包覆的fenimo复合粉末;将预处理sio2包覆的fenimo复合粉末加入85ml无水乙醇b、2.5ml硅烷偶联剂b和15ml去离子水b,搅拌60min,然后加入微波超声波一体化反应器中,同时加入0.5ml正硅酸乙酯b,同时开启微波和超声波进行协同处理90min,分离,固体使用无水乙醇清洗,然后经过抽滤后烘干,获得最终sio2包覆的fenimo复合粉末;所述微波功率为300w;超声功率为400w,超声频率为65khz;温度为50℃;通过低温等离子体和微波超声波一体化反应的处理,使sio2的包覆更均匀致密,并进一步降低制备的材料的损耗。
44.步骤三、将环氧树脂溶解在10ml丙酮中,然后加入2g最终sio2包覆的fenimo复合粉末,使丙酮挥发,添加润滑剂(硬脂酸锌),在600mpa(作用到样品上的压力)的压力下,保压10s,将混合粉末压制成外径10.2mm、内径5.08mm的环状样品;环氧树脂的用量为sio2包覆的fenimo复合粉末质量的1wt%;润滑剂(硬脂酸锌)的用量为sio2包覆的fenimo复合粉末质量的0.5wt%;
45.步骤四、将预压成型的复合粉芯放入真空管式炉中,在氩气氛围中,在高温(如表2所示,给出实施例6~8的烧结温度)下进行烧结,升温速率10℃/min,保温时间60min,自然降温,得到fenimo/sio2软磁粉芯复合材料。
46.表2
47.实施例实施例6实施例7实施例8烧结温度400℃500℃600℃
48.对比例1~5
49.一种铁镍钼/二氧化硅软磁粉芯复合材料的制备方法,包括以下步骤:
50.步骤一、将20g气雾化fenimo粉末中加入170ml无水乙醇、5ml硅烷偶联剂(kh550)和30ml去离子水,以500r/min的速度搅拌60min,然后加入正1ml硅酸乙酯,水浴加热在50℃下搅拌反应3h,分离,固体使用无水乙醇清洗,然后经过抽滤后烘干,获得sio2包覆的fenimo复合粉末;气雾化fenimo粉末的元素含量分别为81wt%ni、17wt%fe和2wt%mo,粒径尺寸为10-30μm;
51.步骤二、将环氧树脂溶解在10ml丙酮中,然后加入2g sio2包覆的fenimo复合粉末,使丙酮挥发,添加润滑剂(硬脂酸锌),在600mpa(作用到样品上的压力)的压力下,保压10s,将混合粉末压制成外径10.2mm、内径5.08mm的环状样品;环氧树脂的用量为sio2包覆的fenimo复合粉末质量的1wt%;润滑剂(硬脂酸锌)的用量为sio2包覆的fenimo复合粉末质量的0.5wt%;
52.步骤四、将预压成型的复合粉芯放入真空管式炉中,在氩气氛围中,在高温(如表3所示,给出对比例1~5的烧结温度)下进行烧结,升温速率10℃/min,保温时间60min,自然降温,得到fenimo/sio2软磁粉芯复合材料。
53.表3
54.对比例对比例1对比例2对比例3对比例4对比例5烧结温度400℃500℃600℃700℃800℃
55.对比例6~10:
56.一种铁镍钼软磁粉芯材料的制备方法,包括以下步骤:
57.步骤一、将60g气雾化fenimo粉末放入刚玉舟中,将刚玉舟放入真空管式炉中,使用机械泵抽真空20min;通入h2/ar混合气体,待气压表指针达到0mpa时,打开出气口,使之保持大气压状态;设置升温程序,处理温度设置为如表4所示,升温速率10℃/min,保温时间60min,之后开始自然降温;待管式炉温度降低至室温,关闭气体,得到烧结后的fenimo粉末;气雾化fenimo粉末的元素含量分别为81wt%ni、17wt%fe和2wt%mo,粒径尺寸为10-30μm。
58.步骤二、将环氧树脂溶解在10ml丙酮中,然后加入2g烧结后的fenimo粉末,使丙酮挥发,添加润滑剂(硬脂酸锌),在600mpa(作用到样品上的压力)的压力下,保压10s,将混合粉末压制成外径10.2mm、内径5.08mm的环状样品;环氧树脂的用量为烧结后的fenimo复合粉末质量的1wt%;润滑剂(硬脂酸锌)的用量为烧结后的fenimo复合粉末质量的0.5wt%;
59.步骤四、将预压成型的复合粉芯放入真空管式炉中,在氩气氛围中,在600℃下进行烧结,升温速率10℃/min,保温时间60min,自然降温,得到fenimo软磁粉芯材料。
60.表4
[0061][0062]
对比例11:
[0063]
一种铁镍钼软磁粉芯材料的制备方法,包括以下步骤:
[0064]
步骤一、将环氧树脂溶解在10ml丙酮中,然后加入2g气雾化fenimo粉末,使丙酮挥发,添加润滑剂(硬脂酸锌),在600mpa(作用到样品上的压力)的压力下,保压10s,将混合粉末压制成外径10.2mm、内径5.08mm的环状样品;环氧树脂的用量为fenimo粉末质量的1wt%;润滑剂(硬脂酸锌)的用量为fenimo粉末质量的0.5wt%;
[0065]
步骤二、将预压成型的粉芯放入真空管式炉中,在氩气氛围中,在600℃下进行烧结,升温速率10℃/min,保温时间60min,自然降温,得到fenimo软磁粉芯材料(f0)。
[0066]
图1给出了气雾化fenimo粉末(a)、经h2/ar混合气体高温烧结后的fenimo粉末(b,实施例1~5步骤一)、气雾化fenimo粉末包覆sio2后的复合粉末(c,对比例1~5,步骤一)、经h2/ar混合气体高温烧结后的fenimo粉末包覆sio2后的复合粉末(d,实施例1~5,步骤一~二)的sem图,从图中可看出粉末均为球状结构,表面存在一定的缺陷,如裂纹和凸起的小颗粒等。经过600℃处理后的fenimo粉末表面形貌几乎没有变化(图1b)。经过sio2绝缘包覆工艺后,可以明显看出样品表面具有一层带有绒状结构的涂层,并且涂层相对均匀的分布在颗粒表面,如图1(c)和(d)所示。
[0067]
图2(a)-(d)给出了对比例1~5步骤一得到的sio2包覆的fenimo复合粉末的sem图
像(a)以及fe(b)、ni(c)和mo(d)元素的元素分布图,可以看出fe、ni和mo元素分布较均匀。从图2(e)和(f)中的o和si的元素分布图可以看出大量的o和si元素均匀分布在fenimo粉末的表面上,证明通过溶胶-凝胶法可以在fenimo粉末表面形成均匀的sio2包覆层。
[0068]
为了验证还原性气氛(h2/ar混合气体)高温预处理工艺的去除氧化层效果,进一步对样品进行了xps测试,揭示其元素价态的变化过程。图3(a)-(d)分别为气雾化fenimo粉末(未烧结)的xps全谱;图3(e)-(h)分别为对比例6烧结后的fenimo粉末的xps全谱;
[0069]
在图3(a)的全谱中,主要显示了fe 2p、ni 2p、mo 3d和o1s特征峰,证明fenimo原粉主要由fe、ni、mo和o元素组成。图3(b)-(d)给出了fe 2p、ni 2p和mo 3d分峰拟合的结果。在图3(b)中,将fe 2p拟合为7个峰,分别是fe0峰(707.3ev,720.4ev)、fe
2+
峰(710.9ev,724.0ev)、fe
3+
峰(713.5ev,726.6ev)和卫星峰(718.8ev),证明样品中含有金属fe单质以及fe
2+
和fe
3+
氧化态阳离子。图3(c)中发现了三组峰,一组是位于852.5ev处的ni
0 2p
1/2
轨道和869.6ev处的ni
0 2p
3/2
轨道;另一组是位于855.7ev的ni
2+ 2p
1/2
轨道和873.5ev处的ni
2+ 2p
3/2
轨道,两组峰分别对应于金属ni单质和ni
2+
阳离子,另外一组为卫星峰(861.6ev,879.8ev)。在图3(d)中发现了6个峰,分别是mo0峰(228.2ev,231.5ev)、mo
4+
峰(230.4ev,233.7ev)和mo
5+
峰(232.2ev,235.4ev),证明样品中存在金属mo单质以及mo
4+
和mo
5+
阳离子。由于相关的灵敏度因子是已知的,所以在所分析的区域中每个元素的相对比例来自峰面积比例,结果表明:fe0的含量由8.16%增加到了23.73%,ni0的含量由18.26%增加到了77.28%,mo0的含量由3.91%增加到了23.1%(图3e-h)。因此经过h2/ar混合气体高温预处理后的fenimo粉末中单质态fe0、ni0和mo0含量均有明显增加,其余氧化态含量减少。fe0、ni0和mo0含量的增加归因于高价态金属氧化物被还原成金属单质,此外,fe0和ni0含量的增加还可归因于fe
3+
和ni
2+
离子在高温下被还原为fe
0.64
ni
0.36
。
[0070]
图4给出了气雾化fenimo粉末(对比例11)以及气雾化fenimo粉末在h2/ar混合气体中经过不同温度处理后(对比例6~10)压制成型的软磁粉芯的有效磁导率和损耗,测试条件为b=100mt。如图4(a)所示,随着处理温度升高到600℃,低频范围内有效磁导率逐渐增大,从101增加到152。随着温度继续升高,有效磁导率降低,高频范围内有效磁导率变得不稳定,这可能归因于ni3fe从大于600℃的温度冷却过程中,fe和ni原子在大范围内规则排列,形成长程有序的相结构,致使晶体磁各向异性常数增大,有效磁导率下降。图4(b)中的损耗呈现先增加后减小的趋势,原粉(气雾化fenimo粉末)的损耗最低,而在h2/ar混合气体中经过600℃处理后粉末(对比例9)的损耗最高,在50khz处的损耗分别为3283kw/m3和7038kw/m3,损耗的增加可归因于还原性气氛高温处理对软磁材料的还原提纯效果。进一步对样品电阻率进行了测试,原粉(气雾化fenimo粉末)和h2/ar混合气体600℃处理后粉末(对比例9)的电阻率分别为18.69ω
·
cm和5.05mω
·
cm,处理后的粉末电阻率明显减少,进一步证实了还原性气氛高温预处理对软磁粉芯材料表面氧化层的去除效果较好。因此,h2/ar混合气高温预处理工艺导致软磁粉芯材料电阻率降低,有效磁导率增加,损耗也相应的增加,由此证实还原性气氛(h2/ar混合气体)中高温处理对软磁粉芯材料性能起到明显的改善作用。
[0071]
对原粉(气雾化fenimo粉末)(对比例1~5)和经h2/ar混合气体600℃烧结后的fenimo粉末(实施例1~5)分别进行sio2绝缘包覆,压制成软磁粉芯后,在ar气中进行400-800℃烧结处理,测试其有效磁导率和损耗,得到的数据如图5所示。图5(a)对比例1~5制备
的fenimo/sio2软磁粉芯复合材料(fs0)的有效磁导率;在图5(a)中,随着测试频率增加,有效磁导率逐渐降低,其中400-600℃烧结后的样品在测试范围内高频有效磁导率基本趋于稳定状态,而700℃和800℃处理后的样品分别在20khz和1khz开始急剧下降,这可能是由于高温烧结导致结构不均匀所致。图5(b)对比例1~5制备的fenimo/sio2软磁粉芯复合材料的损耗;对于fenimo/sio2复合材料,600℃烧结后的损耗最低(图5b)。在保证样品的高频有效磁导率稳定性前提下,为了获得高有效磁导率和低损耗的软磁复合粉芯,样品fs0的最佳烧结温度为600℃,在50khz处的有效磁导率为39.7,损耗为1636kw/m3。
[0072]
图5(c)实施例1~5制备的fenimo/sio2软磁粉芯复合材料(fs600)的有效磁导率;还原性气氛600℃高温预处理后的fenimo经过sio2绝缘包覆所形成的软磁复合材料测试结果如图5(c-d)所示。图5(c)中400-600℃处理后样品高频有效磁导率较稳定,700℃和800℃处理后的样品高频有效磁导率急剧下降。图5(d)实施例1~5制备的fenimo/sio2软磁粉芯复合材料的损耗;相比于其余烧结温度,600℃烧结后的损耗最低(图5d)。温度超过600℃后,高频磁导率稳定性变差,损耗增加,这归因于温度高于600℃后绝缘包覆层可能被破坏所致。通过800℃烧结后的粉芯样品截面sem图像可以看出,sio2层在高温下确实被破坏,如图5(c)插图所示。这样绝缘包覆效果被削弱,进一步导致fenimo的电阻率降低,磁导率明显增加,如图5(a)和(c)所示。因此,样品fs600的最佳烧结温度也为600℃,在50khz处的有效磁导率为46.8,损耗为1026kw/m3。相比于未处理的fenimo原粉包覆sio2后的软磁复合材料,经过还原性气氛高温预处理后包覆sio2的软磁复合材料有效磁导率明显增大,损耗降低。
[0073]
图6给出了h2/ar混合气体600℃处理后的粉末(对比例9)、未处理的fenimo原粉包覆sio2后的粉末(对比例3)和h2/ar混合气体600℃处理后的粉末包覆sio2后的粉末(实施例3)压制成粉芯,在600℃进行烧结后的有效磁导率和损耗。对比对比例9和实施例3的有效磁导率和损耗可以看出,经过sio2绝缘包覆后,损耗明显降低,高频有效磁导率稳定性显著增加,因此绝缘包覆工艺可以降低损耗,提升高频有效磁导率稳定性。对比对比例3和实施例3,可以发现实施例3的样品损耗更低,有效磁导率更高,由此证实还原性气氛高温预处理工艺可以提高fenimo/sio2软磁复合材料的有效磁导率,降低损耗。因此经过还原性气氛(h2/ar混合气体)高温预处理工艺后的绝缘包覆可以更大程度提升软磁复合材料的软磁性能。
[0074]
图7给出了实施例1和实施例6制备的fenimo/sio2软磁粉芯复合材料的和损耗;对比实施例1和实施例6,可以发现实施例6的样品损耗更低,由此证实采用实施例6的技术方案可以降低损耗。同样图8给出了实施例2和实施例7制备的fenimo/sio2软磁粉芯复合材料的和损耗;对比实施例2和实施例7,可以发现实施例7的样品损耗更低,由此证实采用实施例6的技术方案可以降低损耗。图9给出了实施例3和实施例8制备的fenimo/sio2软磁粉芯复合材料的和损耗;对比实施例3和实施例8,可以发现实施例8的样品损耗更低,由此证实采用实施例8的技术方案可以降低损耗。
[0075]
尽管本发明的实施方案已公开如上,但其并不仅仅限于说明书和实施方式中所列运用,它完全可以被适用于各种适合本发明的领域,对于熟悉本领域的人员而言,可容易地实现另外的修改,因此在不背离权利要求及等同范围所限定的一般概念下,本发明并不限于特定的细节和这里示出与描述的图例。