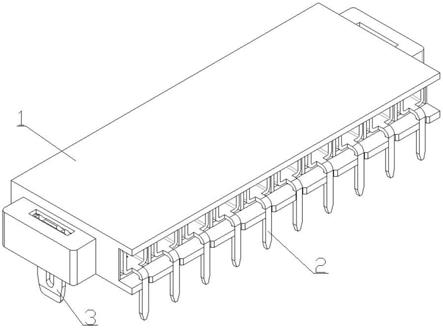
1.本实用新型涉及电连接器制造技术领域,尤其是一种排母连接器。
背景技术:2.排母连接器是一种广泛应用于电子、电器和仪表中的通用连接器件,主要起到电流或信号传输的作用,通常与插针连接器配套使用,构成板对板连接,其作用是在电路内被阻断处或孤立不通的电路之间,起到桥梁的功能,担负起电流或信号传输的任务。
3.排母连接器包括有绝缘塑胶体以及接触端子单元。接触端子单元由多个成排地插设于绝缘塑胶体内的接触端子构成。在实际应用中,排母连接器需要插装于pcb板上进行应用。在pcb板开设一系列与接触端子相对位的避让孔,以利于执行后续的信号导线施焊作业。然而,在实际工作过程中,排母连接器必不可免地会受到侧向力或拉扯力的作用,从而极易使得接触端子由避让孔中扯出,进而导致信号导线由接触端子上脱离,最终导致信号传输进行的中断。因而,亟待技术人员解决上述问题。
技术实现要素:4.故,本实用新型设计人员鉴于上述现有的问题以及缺陷,乃搜集相关资料,经由多方的评估及考量,并经过从事于此行业的多年研发经验技术人员的不断实验以及修改,最终导致该排母连接器的出现。
5.为了解决上述技术问题,本实用新型涉及了一种排母连接器,其与pcb板相插配,包括有绝缘塑胶体以及接触端子单元。接触端子单元由多个成排地插设于绝缘塑胶体内的接触端子构成,相对应地,在绝缘塑胶体上开设有多个供接触端子置入的安装孔。另外,排母连接器还包括有左置焊片、右置焊片。左置焊片、右置焊片均插设于绝缘塑胶体内,且对称地分布于接触端子单元的左、右侧,相对应地,由绝缘塑胶体的底壁向上延伸出有分别供左置焊片、右置焊片置入的左置插槽、右置插槽。左置焊片和右置焊片均穿过pcb板,且采用锡焊的方式实现与pcb板的固定。
6.作为本实用新型技术方案的进一步改进,在左置焊片上开设有储锡孔。当左置焊片相对于绝缘塑胶体插配完成后,储锡孔相对于绝缘塑胶体的下平面保持有设定距离。
7.作为本实用新型技术方案的进一步改进,在左置焊片上设有左置导向斜势或/和右置导向斜势。左置导向斜势由左置焊片的左侧壁斜切而成。右置导向斜势由左置焊片的右侧壁斜切而成。
8.作为本实用新型技术方案的进一步改进,由左置焊片的前侧壁继续向前延伸出有前置塑胶刺破凸起。由左置焊片的后侧壁继续向后延伸出有与前置塑胶刺破凸起相对而置的后置塑胶刺破凸起。
9.作为本实用新型技术方案的更进一步改进,位于前置塑胶刺破凸起的正上方,由左置焊片的前侧壁向后延伸出有前置容屑凹槽。位于后置塑胶刺破凸起的正上方,由左置焊片的后侧壁向前延伸出有后置容屑凹槽。
10.作为本实用新型技术方案的更进一步改进,位于前置塑胶刺破凸起的正下方,由左置焊片的前侧壁继续向前延伸出有前置扶正凸起。位于后置塑胶刺破凸起的正下方,由左置焊片的后侧壁继续向后延伸出有后置扶正凸起。
11.相较于传统设计结构的排母连接器,在本实用新型所公开的技术方案中,其增设有左置焊片、右置焊片。左置焊片、右置焊片均插设于绝缘塑胶体内,且采用锡焊的方式实现与pcb板的固定。如此一来,排母连接器所受到的侧向力或拉扯力全部由左置焊片和右置焊片进行分担,避免了因接触端子由受到侧向力或拉扯力作用而导致的其与信号导线相脱离现象的发生,即有效地确保了排母连接器与pcb板插配的可靠性、稳定性。
附图说明
12.为了更清楚地说明本实用新型实施例或现有技术中的技术方案,下面将对实施例或现有技术描述中所需要使用的附图作简单地介绍,显而易见地,下面描述中的附图仅仅是本实用新型的一些实施例,对于本领域普通技术人员来讲,在不付出创造性劳动的前提下,还可以根据这些附图获得其他的附图。
13.图1是本实用新型中排母连接器的立体示意图。
14.图2是本实用新型中排母连接器的爆炸示意图。
15.图3是本实用新型排母连接器中绝缘塑胶体的立体示意图。
16.图4是本实用新型排母连接器中左置焊片的立体示意图。
17.图5是图4的侧视图。
18.图6是本实用新型排母连接器中右置焊片的立体示意图。
19.图7是图1的正视图。
20.图8是图7的a
‑
a剖视图。
[0021]1‑
绝缘塑胶体;11
‑
安装孔;12
‑
左置插槽;13
‑
右置插槽;2
‑
接触端子单元;21
‑
接触端子;3
‑
左置焊片;31
‑
储锡孔;32
‑
左置导向斜势;33
‑
右置导向斜势;34
‑
前置塑胶刺破凸起;35
‑
后置塑胶刺破凸起;36
‑
前置容屑凹槽;37
‑
后置容屑凹槽;38
‑
前置扶正凸起;39
‑
后置扶正凸起;4
‑
右置焊片。
具体实施方式
[0022]
在本实用新型的描述中,需要理解的是,术语“左”、“右”、“上”、“下”、“前”、“后”等指示的方位或位置关系为基于附图所示的方位或位置关系,仅是为了便于描述本实用新型和简化描述,而不是指示或暗示所指的装置或元件必须具有特定的方位、以特定的方位构造和操作,因此不能理解为对本实用新型的限制。
[0023]
已知,在实际应用中,排母连接器需配套地插配于pcb板上,协同配合以实现信号的传输,因而,排母连接器相对于pcb板插配的稳定性、可靠性对信号传输进程的正常执行有着至关重要的影响。
[0024]
下面结合具体实施例,对本实用新型所公开的排母连接器做进一步的详细说明,图1、图2分别示出了本实用新型中排母连接器的立体示意图及其爆炸示意图,可知,其主要由绝缘塑胶体1、接触端子单元2左置焊片3、右置焊片4以及左置焊片3等几部分构成。其中,接触端子单元2由多个成排地插设于绝缘塑胶体1内的接触端子21构成,相对应地,在绝缘
塑胶体1上开设有多个供接触端子21置入的安装孔11(如图3中所示)。左置焊片3、右置焊片4均插设于绝缘塑胶体1内,且对称地分布于接触端子单元2的左、右侧,相对应地,由绝缘塑胶体1的底壁向上延伸出有分别供左置焊片3、右置焊片4置入的左置插槽12、右置插槽13(如图3中所示)。左置焊片3和右置焊片4均穿过pcb板,且采用锡焊的方式实现与pcb板的固定。如此一来,排母连接器所受到的侧向力或拉扯力全部由左置焊片3和右置焊片4进行分担,避免了因接触端子21由受到侧向力或拉扯力作用而导致的其与信号导线相脱离现象的发生,即有效地确保了排母连接器与pcb板插配的可靠性、稳定性,确保信号得以稳定的传输。
[0025]
然而,在排母连接器的前期小批量试制阶段,发现其成型工艺存在有以下问题:在执行左置焊片3、右置焊片4与pcb板的锡焊操作时,锡液会顺延着左置焊片3、右置焊片4自身而进入到绝缘塑胶体1与pcb板之间的装配缝隙中,而当锡液固化完成后必然会对绝缘塑胶体1造成“抬升”,从而更进一步地增加了绝缘塑胶体1和pcb板之间的装配间隙值。鉴于此,作为上排母连接器结构的进一步优化,如图4、5中所示,还可以在左置焊片3上开设有储锡孔31。当左置焊片3相对于绝缘塑胶体1插配完成后,储锡孔31相对于绝缘塑胶体1的下平面保持有设定距离。右置焊片4可完全参照左置焊片3的结构形式进行设计,即在其上亦开设有储锡孔(如图6中所示)。如此一来,在执行左置焊片3、右置焊片4的锡焊操作时,锡液顺延着左置焊片3、右置焊片4进行轴向“爬行”,最终全部流入到其上储锡孔31进行固化留置,最终有效地避免了因锡液固化而抬升绝缘塑胶体1现象的发生,确保绝缘塑胶体1相对于pcb板保持于紧密贴合状态。
[0026]
出于降低左置焊片3相对于左置插槽12的插配困难度,提高插配效率方面考虑,作为上述排母连接器结构的进一步优化,如图4、5中所示,还可以在左置焊片3上设有左置导向斜势32和右置导向斜势33。左置导向斜势32由左置焊片3的左侧壁斜切而成。而右置导向斜势33由左置焊片3的右侧壁斜切而成。当执行左置焊片3的插配操作时,左置导向斜势32或右置导向斜势33首先与左置插槽12的侧壁进行顶触,为后续的正式插入操作提供位移导向基准,即变相地放松了对左置焊片3插配对位精度的要求。
[0027]
出于实现上述相同的设计目的,右置焊片4可完全参照左置焊片3的结构形式进行设计,即在其上亦分别开设有导向斜势(如图6中所示)。
[0028]
另外,由图4、5中还可以看出,由左置焊片3的前侧壁继续向前延伸出有前置塑胶刺破凸起34。由左置焊片3的后侧壁继续向后延伸出有与上述前置塑胶刺破凸起34相对而置的后置塑胶刺破凸起35。当左置焊片3相对于左置插槽12插配完成后,左置插槽12的前、后顶壁由于分别受到前置塑胶刺破凸起34、后置塑胶刺破凸起35顶靠力的作用而发生自适应性弹性变形(如图7、8中所示),起到“铆固点”的作用,有效地提高了左置焊片3相对于绝缘塑胶体1的插配可靠性。
[0029]
出于实现上述相同的设计目的,右置焊片4可完全参照左置焊片3的结构形式进行设计,即在其上亦分别开设有塑胶刺破凸起(如图6中所示)。
[0030]
已知,在执行左置焊片3、右置焊片4的插配操作时以及排母连接器实际应用进程中,左置焊片3、右置焊片4相对于绝缘塑胶体1不可避免地会发生相对位移现象,加之绝缘塑胶体1的质地较软,从而导致左置插槽12、右置插槽13必然残存有大量的塑胶屑,最终影响到左置焊片3、右置焊片4相对于左置插槽12、右置插槽13的插配紧密度;另外,当左置插
槽12、右置插槽13被划伤后,必然会导致内应力的增大,进而极易在左置插槽12、右置插槽13的侧壁上产生裂纹,最终严重地降低了绝缘塑胶体1的额定寿命,鉴于此,作为上述左置焊片3结构的进一步优化,如图4、5中所示,还可以位于前置塑胶刺破凸起34的正上方,由左置焊片3的前侧壁向后延伸出有前置容屑凹槽36。位于后置塑胶刺破凸起35的正上方,由左置焊片3的后侧壁向前延伸出有后置容屑凹槽37。前置容屑凹槽36、后置容屑凹槽37不但可以对塑胶屑进行有效、及时地收集,亦可以在一定程度上优化左置插槽12侧壁的受力状态(如图7、8中所示)。
[0031]
出于实现上述相同的设计目的,右置焊片4可完全参照左置焊片3的结构形式进行设计,即在其前、后侧壁上亦分别开设有容屑凹槽(如图6中所示)。
[0032]
需要说明的是,如图4、5中所示,位于前置塑胶刺破凸起34的正下方,还可以由左置焊片3的前侧壁继续向前延伸出有前置扶正凸起38。位于后置塑胶刺破凸起35的正下方,还可以由左置焊片3的后侧壁继续向后延伸出有后置扶正凸起39。当执行左置焊片3的插配操作时,前置扶正凸起38、后置扶正凸起39的存在可以对左置焊片3的插配姿态进行自适应性调整,即变相地放松对左置焊片3插配姿态的要求,使其更为顺利至插入至左置插槽12内(如图7、8中所示)。
[0033]
最后,出于实现上述相同的设计目的,右置焊片4可完全参照左置焊片3的结构形式进行设计,即在其前、后侧壁上亦分别开设有扶正凸起(如图6中所示)。
[0034]
对所公开的实施例的上述说明,使本领域专业技术人员能够实现或使用本实用新型。对这些实施例的多种修改对本领域的专业技术人员来说将是显而易见的,本文中所定义的一般原理可以在不脱离本实用新型的精神或范围的情况下,在其它实施例中实现。因此,本实用新型将不会被限制于本文所示的这些实施例,而是要符合与本文所公开的原理和新颖特点相一致的最宽的范围。