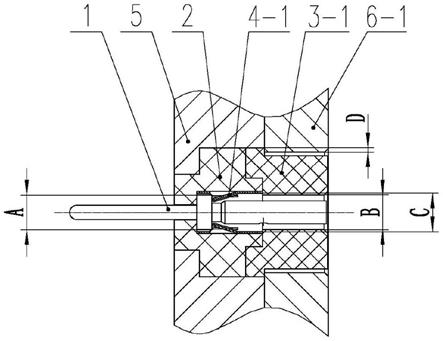
1.本实用新型涉及连接器技术领域,具体涉及一种固定可拆卸接触件的绝缘基座结构,主要用于实现同轴接触件与低频接触件的混装集成。
背景技术:2.基于电子设备小型化、轻量化、功能集成化发展的趋势下,在各类电子设备及通讯行业中,控制、通讯、数据等系统往往要求同时传输同轴信号和低频信号,传统的方案采用注塑成型的塑料基座进行集成混装,实现低频接触件的绝缘距离,需制作注塑模具,小批量加工,成本高,而且不易改型,一旦集成方案有所变化,原基座模具报废,需重新开发。
技术实现要素:3.针对现有技术存在的问题,本实用新型的目的在于提供一种固定可拆卸接触件的绝缘基座结构,实现了同轴、低频混装连接器的可拆卸低频接触件的固定,具有零件数量少、降低成本、通用性强、装配简单等特点。
4.为了达到上述目的,本实用新型采用以下技术方案予以实现。
5.一种固定可拆卸接触件的绝缘基座结构,包括插头绝缘基座结构和插座绝缘基座结构;所述插头绝缘基座结构包括针绝缘体2,与针绝缘体2凸台结合的插头绝缘体3
‑
1位于针绝缘体2之下,插头卡爪4
‑
1布置在针绝缘体2和插头绝缘体3
‑
1形成的台阶孔内,针绝缘体2和插头绝缘体3
‑
1组成的针端绝缘体组件布置在针安装板5与插头安装板6
‑
1形成的台阶孔内,可拆卸插针接触件1从插头绝缘体3
‑
1尾端孔位装入并通过插头卡爪4
‑
1的倒刺撑开后固定,实现可拆卸插针接触件1的固定;
6.所述插座绝缘基座结构包括孔绝缘体8,与孔绝缘体8凸台结合的插座绝缘体3
‑
2位于孔绝缘体8之下,插座卡爪4
‑
2布置在孔绝缘体8和插座绝缘体3
‑
2形成的台阶孔内,孔绝缘体8和插座绝缘体3
‑
2组成的孔端绝缘体组件布置在孔安装板9与插座安装板6
‑
2形成的台阶孔内,可拆卸插孔接触件7从插座绝缘体3
‑
2尾端孔位装入并通过插座卡爪4
‑
2的倒刺撑开后固定,实现可拆卸插孔接触件7的固定;
7.通过可拆卸插针接触件1插入可拆卸插孔接触件7中实现插头绝缘基座结构和插座绝缘基座结构的连接。
8.通过取送工具可实现可拆卸插针接触件1和可拆卸插孔7的嵌入和取出,实现可拆卸功能。
9.所述插头绝缘体3
‑
1尾端孔内径φb和插座绝缘体3
‑
2尾端孔内径φb要小于插头卡爪4
‑
1内径φc和插座卡爪4
‑
2内径φc,保证插头卡爪4
‑
1和可拆卸插针接触件1以及插座卡爪4
‑
2和可拆卸插孔接触件7的固定性,插头绝缘体3
‑
1尾端孔内径φb要大于可拆卸插针接触件1前端的台阶外径φa,插座绝缘体3
‑
2尾端孔内径φb要大于可拆卸插孔接触件7前端的台阶外径φa,φa、φb、φc之间的尺寸关系为:φb在φa和φc之间,即φa<φb<φc;插头安装板6
‑
1卡住针端绝缘体组件的台阶尺寸d和插座安装板6
‑
2卡住孔端绝缘体组件
的台阶尺寸d控制在0.3mm~0.5mm。
10.插头卡爪4
‑
1内径φc和插座卡爪4
‑
2内径φc比插头绝缘体3
‑
1尾端孔内径φb和插座绝缘体3
‑
2尾端孔内径φb至少大0.4mm。
11.插头绝缘体3
‑
1与插座绝缘体3
‑
2、插头安装板6
‑
1与插座安装板6
‑
2以及插头卡爪4
‑
1与插座卡爪4
‑
2在插头绝缘基座结构和插座绝缘基座结构中为通用件,零件通用性强。
12.所述的一种固定可拆卸接触件的绝缘基座结构,其特征在于:所述针安装板5、插头安装板6
‑
1与孔安装板9、插座安装板6
‑
2的材质为金属。
13.与现有技术相比,本实用新型具备如下优点:
14.1)该结构新颖,孔端和针端共用的零件多,降低了生产成本,提高了生产效率。
15.2)通用性强,该结构可借用到任何需要集成低频接触件的连接器中。
16.3)相对于原塑料安装板集成同轴接触件和低频接触件,该结构改型成本低,当混装方案改变时,只需重新加工金属安装板。
17.4)金属安装板集成同轴接触件比原塑料安装板可靠性提高。
18.5)该结构装配工序简单。
附图说明
19.图1为本实用新型插头绝缘基座结构视图。
20.图2为本实用新型插座绝缘基座结构视图。
具体实施方式
21.下面结合附图对本实用新型做进一步详细描述:
22.本实用新型一种固定可拆卸接触件的绝缘基座结构,包括插头绝缘基座结构和插座绝缘基座结构;如图1所示,所述插头绝缘基座结构包括针绝缘体2,与针绝缘体2凸台结合的插头绝缘体3
‑
1位于针绝缘体2之下,插头卡爪4
‑
1布置在针绝缘体2和插头绝缘体3
‑
1形成的台阶孔内,针绝缘体2和插头绝缘体3
‑
1组成的针端绝缘体组件布置在针安装板5与插头安装板6
‑
1形成的台阶孔内,可拆卸插针接触件1从插头绝缘体3
‑
1图示右端孔位装入并通过插头卡爪4
‑
1的倒刺撑开后固定,实现可拆卸插针接触件1的固定。
23.所述插头绝缘基座结构装配时分三步:第一步先将插头卡爪4
‑
1装入针绝缘体2,然后将针绝缘体2的凸台与插头绝缘体3
‑
1对应的孔对位,实现插头卡爪4
‑
1的固定,针绝缘体2和插头绝缘体3
‑
1组成针端绝缘体组件;第二步将针端绝缘体组件从针安装板5直径较大一边孔位装入卡在台阶孔内,然后将插头安装板6
‑
1穿过插头绝缘体3
‑
1靠在针安装板5图示右端面夹住针端绝缘体组件,实现针端绝缘体组件的固定;第三步将可拆卸插针接触件1从插头绝缘体3
‑
1尾部孔位装入,插头卡爪4
‑
1上倒刺被可拆卸插针接触件1上凸台弹开,当可拆卸插针接触件1装到位后,倒刺恢复,插头卡爪4
‑
1的倒刺将可拆卸插针接触件1牢牢地卡住,实现可拆卸插针接触件1的固定,完成插头绝缘基座结构的装配。
24.如图2所示,所述插座绝缘基座结构包括孔绝缘体8,与孔绝缘体8凸台结合的插座绝缘体3
‑
2位于孔绝缘体8之下,插座卡爪4
‑
2布置在孔绝缘体8和插座绝缘体3
‑
2形成的台阶孔内,孔绝缘体8和插座绝缘体3
‑
2组成的孔端绝缘体组件布置在孔安装板9与插座安装板6
‑
2形成的台阶孔内,可拆卸插孔接触件7从插座绝缘体3
‑
2图示右端孔位装入并通过插
座卡爪4
‑
2的倒刺撑开后固定,实现可拆卸插孔接触件7的固定。
25.所述插座绝缘基座结构与插头绝缘基座结构装配原理与步骤相同,也是分三步:第一步先将插座卡爪4
‑
2装入孔绝缘体8,然后将孔绝缘体8的凸台与插座绝缘体3
‑
2对应的孔对位,实现插座卡爪4
‑
2的固定,组成孔端绝缘体组件;第二步将孔端绝缘体组件从孔安装板9直径较大一边孔位装入卡在台阶孔内,然后将插座安装板6
‑
2穿过插座绝缘体3
‑
2靠在孔安装板9图示右端面夹住孔端绝缘体组件,实现孔端绝缘体组件的固定;第三步将可拆卸插孔接触件7从插座绝缘体3
‑
2尾部孔位装入,插座卡爪4
‑
2上倒刺被可拆卸插孔接触件7上凸台弹开,当可拆卸插孔接触件7装到位后,倒刺恢复,插座卡爪4
‑
2倒刺将可拆卸插孔接触件7牢牢地卡住,实现可拆卸插孔接触件7的固定,完成插座绝缘基座结构的装配。
26.通过可拆卸插针接触件1插入可拆卸插孔接触件7中实现插头绝缘基座结构和插座绝缘基座结构的连接。
27.如图1和图2所示,所述插头绝缘体3
‑
1尾端孔内径φb和插座绝缘体3
‑
2尾端孔内径φb要小于插头卡爪4
‑
1内径φc和插座卡爪4
‑
2内径φc,保证插头卡爪4
‑
1和可拆卸插针接触件1以及插座卡爪4
‑
2和可拆卸插孔接触件7的固定性,插头绝缘体3
‑
1尾端孔内径φb要大于可拆卸插针接触件1前端的台阶外径φa,插座绝缘体3
‑
2尾端孔内径φb要大于可拆卸插孔接触件7前端的台阶外径φa,φa、φb、φc之间的尺寸关系为:φb在φa和φc之间,即φa<φb<φc;插头安装板6
‑
1卡住针端绝缘体组件的台阶尺寸d和插座安装板6
‑
2卡住孔端绝缘体组件的台阶尺寸d控制在0.3mm~0.5mm。
28.如图1和图2所示,插头卡爪4
‑
1内径φc和插座卡爪4
‑
2内径φc比插头绝缘体3
‑
1尾端孔内径φb和插座绝缘体3
‑
2尾端孔内径φb至少大0.4mm。
29.如图1和图2所示,插头绝缘体3
‑
1与插座绝缘体3
‑
2、插头安装板6
‑
1与插座安装板6
‑
2以及插头卡爪4
‑
1与插座卡爪4
‑
2在插头绝缘基座结构和插座绝缘基座结构中为通用件,零件通用性强。
30.如图1和图2所示,针安装板5、插头安装板6
‑
1与孔安装板9、插座安装板6
‑
2的材质为金属。
31.如图1和图2所示,通过在针安装板5、插头安装板6
‑
1和孔安装板9、插座安装板6
‑
2内分别设置针绝缘体2、插头绝缘体3
‑
1和孔绝缘体8、插座绝缘体3
‑
2和插头卡爪4
‑
1、插座卡爪4
‑
2,实现可拆卸插针接触件1和可拆卸插孔接触件7的固定,并且通过取送工具可实现可拆卸插针接触件1和可拆卸插孔接触件7的嵌入和取出,实现可拆卸功能。借助取卸工具可将插头卡爪4
‑
1和插座卡爪4
‑
2倒刺撑开,用工具垂直拉出可拆卸插针接触件1和可拆卸插孔接触件7,完成可拆卸插针接触件1和可拆卸插孔接触件7的卸出。