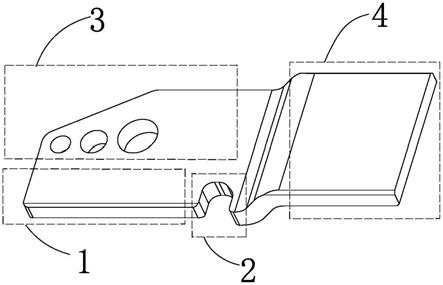
1.本实用新型属于连接器技术领域,具体涉及一种超声波焊接端子。
背景技术:2.超声波焊接是利用高频振动波传递到两个需焊接的线束工件表面,在加压的情况下,使两个线束工件表面相互摩擦而形成分子层之间的熔合。在进行超声波焊接时,既不施加电流也不施加高温热源,利用超声波频率(超过16khz)的机械振动能量,通过摩擦方式转换为热能。端子是用来进行传导大电流的部件。
3.由于要满足一些功能需求,如卡装需求、电镀捆绑需求等,一般端子上都有各种功能性开孔、缺口槽等薄弱结构。在端子和线束的超声波焊接过程中,端子不可避免的会跟随焊头产生振动,容易在薄弱位置产生裂纹,使端子失效或断裂。
技术实现要素:4.为解决上述问题,本实用新型提供一种新型结构的超声波焊接端子,使其通过在固定部设置减重区,通过减重区的减重处理来降低端子在焊接时的最大应力,避免薄弱位置裂纹的产生。
5.本实用新型的目的及解决其技术问题是采用以下技术方案来实现的。依据本实用新型提出的一种超声波焊接端子,其包括前端的固定部和后端的焊接部,所述焊接部表面具有用于与线束焊接的超声波焊接区,固定部包括用于与插孔配合的接触区和用于实现端子固定定位的固定区;所述固定部设有经过减重处理的减重区;所述接触区设置在固定部的一侧,所述减重区设置在固定部上远离接触区的另一侧。
6.本实用新型的目的及解决其技术问题还可采用以下技术措施进一步实现。
7.前述的超声波焊接端子,其中所述的固定区为一侧开口的开口槽结构。。
8.前述的超声波焊接端子,其中所述的固定区位于固定部设有接触区的一侧。
9.前述的超声波焊接端子,其中所述的接触区与固定区在固定部上沿前后方向分布,且该固定区的缺口槽为经倒圆角处理、内部平滑过渡的结构。
10.前述的超声波焊接端子,其中所述的缺口槽靠近超声波焊接区侧的壁体高度大于远离超声波焊接区侧的壁体高度,且超声波焊接区在靠近固定区处向外凸出形成一圆滑的凸部。
11.前述的超声波焊接端子,其中所述的减重区的减重处理包括倒角、圆孔、方孔以及缺口槽中一种或多种去除材料的工艺的组合。
12.前述的超声波焊接端子,其中所述的减重区在前端远离接触区侧设置倒角。
13.前述的超声波焊接端子,其中所述的减重区在远离接触区一侧开缺口槽。
14.前述的超声波焊接端子,其中所述的减重区沿前后方向开设多个由前到后直径逐渐增大的通孔。
15.前述的超声波焊接端子,其中所述的减重区在远离接触区一侧前端设置倒角,同
时沿前后方向开设多个由前到后直径逐渐增大的通孔。
16.前述的超声波焊接端子,其中所述的固定部和焊接部之间通过一弯折部过渡。
17.本实用新型与现有技术相比具有明显的优点和有益效果。借由上述技术方案,本实用新型超声波焊接端子可达到相当的技术进步性及实用性,并具有产业上的广泛利用价值,其至少具有下列优点:
18.本实用新型减重区域的设置可有效降低端子在焊接时的最大应力,由此可有效防止端子固定区在超声波焊接过程中裂纹的产生。
19.本实用新型通过在端子固定部一侧设置开口槽结构的固定区实现端子的可靠定位,且减小端子的体积。此外,本实用新型折弯部能够增强端子的对中。
20.最后,本实用新型还在端子固定部的减重区进行减重处理使得端子的一阶模态发生变化。在随机振动条件下,同时设置倒角和通孔时模型的最大应力由单独设置倒角时的770.85mpa降低为513.56mpa,降低了33.4%。由此可见,减重区域的设置可有效降低端子在焊接时的最大应力,由此可有效防止端子固定区在超声波焊接过程中裂纹的产生。
附图说明
21.图1为本实用新型实施例1超声波焊接端子的结构示意图;
22.图2为本实用新型实施例2超声波焊接端子的结构示意图;
23.图3为本实用新型实施例3超声波焊接端子的结构示意图;
24.图4为本实用新型实施例4超声波焊接端子的结构示意图;
25.图5为图4的主视图;
26.图6为图4的侧视图;
27.图7为本实用新型实施例1的模型一阶模态图;
28.图8为本实用新型实施例1的模型应力分布图;
29.图9为本实用新型实施例4的模型一阶模态图;
30.图10为本实用新型实施例4的模型应力分布图。
31.图11为连接器的结构示意图;
32.图12为图11的剖视图。
33.【主要元件符号说明】
34.1:接触区
35.2:固定区
36.3:减重区
37.4:超声波焊接区
38.5:弯折部
39.6:线束
具体实施方式
40.为更进一步阐述本实用新型为达成预定发明目的所采取的技术手段及功效,以下结合附图及较佳实施例,对依据本实用新型提出的超声波焊接端子其具体实施方式、结构、特征及其功效,详细说明如后。
41.请参阅图1-6,其为本实用新型超声波焊接端子的各部分结构示意图,该超声波焊接端子包括前端的固定部和后端的焊接部,其中所述固定部包括与插孔配合的接触区1和用于实现端子固定定位的固定区2,所述焊接部表面为与线束焊接的超声波焊接区4,所述固定部尾部和焊接部前端固接。
42.在本实用新型实施例中,所述接触区1和固定区2位于固定部的同一侧,较佳的所述接触区1和固定区2沿固定部前后方向分布,且固定区2位于接触区1后端位置。
43.为减小端子尺寸,本实用新型固定区2为凹槽结构。所述固定区2的凹槽结构为经过倒圆角处理、各部分平滑过渡的结构,以降低此处产生裂纹的可能性。
44.在本实用新型实施例中,所述固定区2的凹槽结构为位于固定部尾部一侧的缺口槽结构,但并不限定于此。
45.较佳的,所述固定区2为位于接触区尾部一侧的u型缺口槽,但并不限定于此。当固定区2为位于接触区尾部一侧的侧面敞开的u型缺口槽时,该u型槽靠近超声波焊接区4侧的壁体高度大于远离超声波焊接区4侧的壁体高度。超声波焊接区4在靠近固定区2处向外凸出形成一圆滑的凸部。
46.为防止在超声波焊接过程中的振动使固定区2处萌生裂纹从而造成端子失效,本实用新型固定部还设有对端子进行减重处理的减重区3,所述接触区和减重区并列分布在固定部表面的不同侧。该减重区3的减重方式包括且不限于倒角、圆孔、方孔等去除材料的工艺中的一种或多种的组合。
47.所述减重区3位于接触区1的一侧,该减重区3的设置既可满足焊接部的焊接尺寸需求,又能够减小固定部的重量,以防止固定区产生裂纹,且该减重区3的减重方式简单且减重效果好。
48.在本实用新型实施例1中,减重区3通过其前端远离接触区侧设置的倒角a实现减重目的。在本实用新型实施例2中,所述减重区3通过在远离接触区一侧开缺口槽的方式实现减重目的,较佳的,该缺口槽位于固定部一侧的中部。
49.在本实用新型实施例3中,所述减重区3通过在其上开设至少一个通孔b实现减重目的。具体的,本实用新型在减重区3沿前后方向开设3个由前到后直径逐渐增大的通孔b实现减重目的。较佳的,3个通孔b靠近接触区1侧布置。
50.在本实用新型实施例4中,所述减重区3同时通过倒角和通孔两种方式实现减重,具体的其通过在减重区远离接触区1一侧前端设置倒角a,同时在减重区3上开设3个由前到后直径逐渐增大的通孔b实现减重目的。较佳的,3个通孔b靠近减重区3前端布置。在本实用新型其它实施例中,所述通孔b的数量可增减。
51.图7至图10为模型的对比仿真结果,其表明在减重区域增加工艺孔并且对定位区域的凹槽进行倒圆角处理后,端子的一阶模态发生变化。在随机振动条件下,同时设置倒角和通孔时模型的最大应力由单独设置倒角时的770.85mpa降低为513.56mpa,降低了33.4%,而未做减重处理的超声波焊接端子的最大应力则在800mpa以上。由此可见,减重区域的设置可有效降低端子在焊接时的最大应力,由此可有效防止端子固定区在超声波焊接过程中裂纹的产生。
52.在本实用新型实施例中,所述固定部和焊接部为一体成型的结构,且所述固定部和焊接部之间还具有一弯折部5,该弯折部5使得固定部和焊接部之间呈由前到后上升或下
降的阶梯状。所述弯折部5的设置有利于超声波焊接后线缆与固定部的对中,进而保证装配时与所配合的绝缘体及壳体的对中。
53.本实用新型还提供一种使用上述超声波焊接端子的连接器。请参阅图11和图12,该连接器内的端子为超声波焊接端子,连接器尾部线缆的线束6通过超声波焊接在该超声波焊接端子的超声波焊接区4上,该超声波焊接端子通过国定区2实现在连接器壳体和绝缘体的定位。
54.以上所述,仅是本实用新型的较佳实施例而已,并非对本实用新型做任何形式上的限制,虽然本实用新型已以较佳实施例揭露如上,然而并非用以限定本实用新型,任何熟悉本专业的技术人员,在不脱离本实用新型技术方案范围内,当可利用上述揭示的技术内容做出些许更动或修饰为等同变化的等效实施例,但凡是未脱离本实用新型技术方案的内容,依据本实用新型的技术实质对以上实施例所做的任何简单修改、等同变化与修饰,均仍属于本实用新型技术方案的范围内。