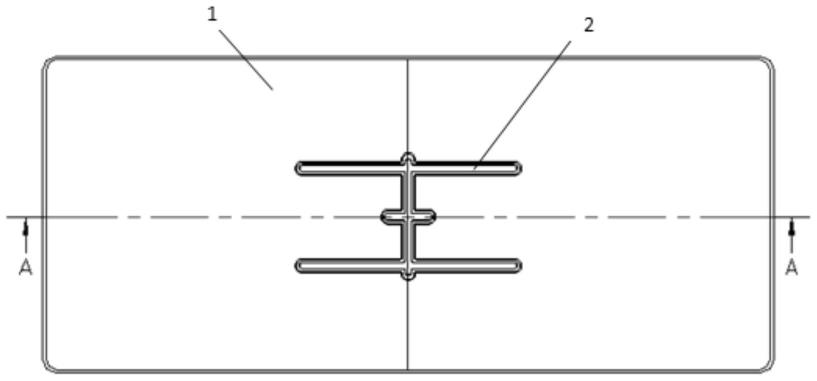
一种新能源防爆电池壳
[技术领域]
[0001]
本实用新型涉及电池壳防爆技术领域,具体地说是一种新能源防爆电池壳。
[
背景技术:]
[0002]
新能源车要求当电池壳内气体压力达到0.7mpa到2.3mpa时必须防爆打开。这是因为,新能源锂电池的铝材方壳在短路发生前电池会先爆炸或充电久了电解液等材料会分解产生气体而爆炸。所以,电池壳如果不能及时释放气体而防爆,这会对行驶中的汽车会产生不安全。
[0003]
目前,电池壳防爆的方法是:在铝壳盖上开孔后用日本进口的金属防爆材料,再采用激光焊接成一体。该种工艺材料成本很高,一套进口金属防爆材料再加激光焊接,成本需要1.6元以上。
[
技术实现要素:]
[0004]
本实用新型的目的就是要解决上述的不足而提供一种新能源防爆电池壳,不仅成本低廉,而且加工工艺简单,大大提高了生产效率,实现了汽车防爆脱险,安全行驶的目的。
[0005]
为实现上述目的设计一种新能源防爆电池壳,包括防爆电池壳体1,所述防爆电池壳体1采用铝材或钢材制成,所述防爆电池壳体1上局部经挤压形成有挤压层2,所述挤压层2上冲压有刻痕线3,所述刻痕线3的残留厚度为 0.10mm-0.22mm。
[0006]
进一步地,所述防爆电池壳体1上挤压层2的厚度为0.4mm-0.5mm。
[0007]
进一步地,所述防爆电池壳体1为方形盒状,所述挤压层2设于方形的防爆电池壳体1侧面。
[0008]
进一步地,所述刻痕线3由上下对称且相连接的两个半圆或两个矩形块构成,或者由左右对称且相连接的两个半圆或两个矩形块或两个三角形块构成,或者呈u字型、米字型或x型。
[0009]
进一步地,所述防爆电池壳体1为圆管状,所述挤压层2设于防爆电池壳体1的管壁上或/和管盖上。
[0010]
进一步地,所述防爆电池壳体1管壁上的刻痕线3沿周向均匀分布,且管壁上的刻痕线3为但不限于工字型、c字型、o字型、u字型、x型。
[0011]
进一步地,所述防爆电池壳体1管盖上的刻痕线3设置为笑脸状刻痕线。
[0012]
本实用新型同现有技术相比,提供了一种新能源防爆电池壳以及该新能源防爆电池壳的生产工艺,该新能源防爆电池壳采用铝材或钢材制成,并采用冲床多次挤压工艺使被挤压的材料缩孔压密压实,让材料形成较致密的组织结构,再在挤压部分材料上冲压刻痕线,刻痕后材料残留厚度仅为0.10mm到0.22mm 经试验表明,该刻痕后材料厚度在0.10mm到0.2mm之间时能达到防爆压力为 0.7mpa到2.3mpa的目的,当刻痕后材料厚度控制在0.15mm到0.2mm之间时爆破压力在0.9mpa到1.3mpa能成功产生爆破,当刻痕后材料厚度控制在0.18mm 到0.22mm之间时爆破压力在2.0
±
0.3mpa能成功产生爆破,可见,本实用新型
成本只有进口材料的十分之一不到,仅有一次性的设计和模具成本,不仅成本低廉,而且加工工艺简单,生产效率提高了原来的30多倍,实现了汽车防爆脱险,安全行驶的目的,值得推广应用。
[附图说明]
[0013]
图1是本实用新型防爆电池壳体上挤压层的结构示意图;
[0014]
图2是图1中a-a剖面图;
[0015]
图3是本实用新型挤压层上刻痕线的结构示意图;
[0016]
图4是图3中b-b剖面图;
[0017]
图5a、图5b、图5c、图5d、图5e、图5f是防爆电池壳体为方形盒状的结构示意图;
[0018]
图6a、图6b、图6c、图6d、图6e是防爆电池壳体为圆管状的管盖结构示意图;
[0019]
图7a、图7b、图7c、图7d、图7e、图7f、图7g是防爆电池壳体为圆管状的结构示意图;
[0020]
图8是本实用新型实施例2爆破试验数据图;
[0021]
图9a是本实用新型模具成型图(平面图);
[0022]
图9b是本实用新型模具成型图(立体图);
[0023]
图中:1、防爆电池壳体 2、挤压层 3、刻痕线。
[具体实施方式]
[0024]
如附图1至附图4所示,本实用新型提供了一种新能源防爆电池壳,包括防爆电池壳体1,防爆电池壳体1采用铝材或钢材制成,防爆电池壳体1上局部经挤压形成有挤压层2,防爆电池壳体1上挤压层2的厚度为0.4mm-0.5mm,挤压层2上冲压有刻痕线3,刻痕线3的残留厚度为0.10mm-0.22mm。
[0025]
如附图5a、图5b、图5c、图5d、图5e、图5f所示,防爆电池壳体1设置为方形盒状,挤压层2设于方形的防爆电池壳体1侧面,挤压层2与刻痕线3 轮廓线相同;刻痕线3由上下对称且相连接的两个半圆或两个矩形块构成,或者由左右对称且相连接的两个半圆或两个矩形块或两个三角形块构成,或者呈u 字型、米字型或x型。
[0026]
如附图6a、图6b、图6c、图6d、图6e以及附图7a、图7b、图7c、图7d、图7e、图7f、图7g所示,防爆电池壳体1还可设置为圆管状,挤压层2设于防爆电池壳体1的管壁上或/和管盖上。由附图7a、图7b、图7c、图7d、图7e、图7f、图7g可见,防爆电池壳体1管壁上的刻痕线3沿周向均匀分布,且管壁上的刻痕线3为但不限于工字型、c字型、o字型、u字型、x型,该刻痕线3 可设置在管壁一端,也可两端均设置。由图6a、图6b、图6c、图6d、图6e可见,防爆电池壳体1管盖上的刻痕线3可设置为笑脸状刻痕线,其嘴部的形状可根据材质或壳体尺寸需求进行设置,如圆形、椭圆形、弧形过渡的三角形、弧形过渡的等腰梯形或倒等腰梯形,等。
[0027]
下面结合具体实施例对本实用新型作以下进一步说明:
[0028]
实施例1
[0029]
采用铝材或钢材,不同材料的厚度和不同形状的圆管上,用冲床多次挤压工艺(冲床为300吨或400吨,行程450mm,精度0.05mm到0.08mm),使被挤压的材料缩孔压密压实,让材料形成较致密的组织结构,并使材料厚度达到 0.45mm左右,当挤压部分材料厚度在0.45mm左右时,再冲压刻痕线,该刻痕后材料残留厚度仅为0.10mm到0.2mm。试验表明:该刻
痕后材料厚度仅在0.10mm 到0.2mm之间,能达到防爆压力为0.7mpa到2.3mpa的目的。
[0030]
为什么刻痕后材料厚度要控制在0.10mm到0.2mm之间呢?其依据如下:新能源车要求当电池壳内气体达到0.7mpa到2.3mpa时必须防爆打开,为此,通过做了很多实验,先后购买了增压泵、比例阀、压力监控,设计并加工了压机机构的夹具等装置,并采用plc控制,当冲压刻痕线后,材料残余厚度控制在 0.10mm到0.2mm之间,爆破压力在0.7mpa到2.5mpa能成功产生爆破。经过前后13个月,做了400多个爆破试验,并用不同厚度的材料和不同形状的圆管做刻痕试验,也都得到了相应的爆破效果。试验证明,当刻痕后材料厚度控制在 0.10mm到0.20mm之间,爆破压力在0.7mpa到2.3mpaa能成功产生爆破。
[0031]
实施例2
[0032]
铝材厚度为1.8mm(或1.6mm均可),先通过铝壳三次拉伸挤压(冲床为“金丰”300吨,行程500mm,精度0.05mm到0.08mm),使局部被挤压的材料缩孔压密压实,使材料形成较致密的组织结构,并使材料厚度达到0.5mm左右;铝壳上部被多次拉伸后需要逐渐变薄,直至符合图纸尺寸;底部挤压部分材料厚度在0.5mm左右时,将再冲压刻痕线,该刻痕后材料厚度仅为0.15mm到0.2mm。试验表明:该刻痕后材料厚度仅在0.15mm到0.2mm之间,能符合防爆压力0.9mpa 到1.3mpa。其模具共10副,分别为:
①
落料、
②
拉伸、
③
拉伸挤压、
④
拉伸拉薄、
⑤
拉伸挤压、
⑥
拉伸拉薄、
⑦
拉方形、
⑧
方形整形、
⑨
冲刻痕、
⑩
旋切,其模具成型图如图9a和图9b。
[0033]
为什么刻痕后材料厚度仅控制在0.15mm到0.2mm呢?其依据如下:新能源车要求当电池壳内气体达到0.9mpa到1.3mpa时必须防爆打开,为此,通过做了很多实验,先后购买了增压泵、比例阀、压力监控,设计并加工了压机机构的夹具等装置,并采用plc控制,当刻痕后,材料厚度控制在0.15mm到0.2mm 之间,爆破压力在0.9mpa到1.3mpa能成功产生爆破。经过前后13个月,做了 400多个爆破试验,并用多种形状的刻痕线做了试验,如:图5a、图5b、图5c、图5d、图5e、图5f也都得到了相应的爆破效果。如附图8所示,为爆破效果数据,试验证明,当刻痕后材料厚度控制在0.15mm到0.2mm之间,爆破压力在 0.9mpa到1.3mpa能成功产生爆破。
[0034]
实施例3
[0035]
铝材厚度为1.6mm,先通过铝盖二次挤压(冲床为400吨,行程200mm),使局部被挤压的材料缩孔压密压实,使材料形成较致密的组织结构,并使材料厚度达到0.4mm左右,再冲压笑脸刻痕线,该刻痕后材料厚度仅为0.18mm到 0.22mm。试验表明:冲压刻痕后材料厚度仅在0.18mm到0.22mm之间,能符合防爆压力2.0
±
0.3mpa。
[0036]
为什么刻痕后材料厚度仅仅控制在0.18mm到0.22mm呢?其依据如下:新能源二轮电动车要求当圆柱电池内气体达到2.0
±
0.3mpa时必须防爆打开。为此,通过做了很多实验,先后购买了增压泵、比例阀、压力监控,设计并加工了压机机构的夹具等装置,并采用plc控制,当刻痕后材料厚度控制在0.18mm 到0.22mm之间,爆破压力在2.0
±
0.3mpa能成功产生爆破。经过前后5个月,做了100多个爆破试验,并用多种形状的刻痕做了试验,如:图6a、图6b、图 6c、图6d、图6e,也都得到了相应的爆破效果。试验证明:当材料厚度控制在 0.18mm到0.22mm之间,爆破压力在2.0
±
0.3mpa能成功产生爆破。
[0037]
本实用新型的精密冲压防爆笑脸刻痕工艺,成本只有进口材料的十分之一不到,仅有一次性的设计和模具成本,不仅成本低廉,而且加工工艺简单,生产效率提高了原来的
20多倍。
[0038]
本实用新型并不受上述实施方式的限制,其他的任何未背离本实用新型的精神实质与原理下所作的改变、修饰、替代、组合、简化,均应为等效的置换方式,都包含在本实用新型的保护范围之内。